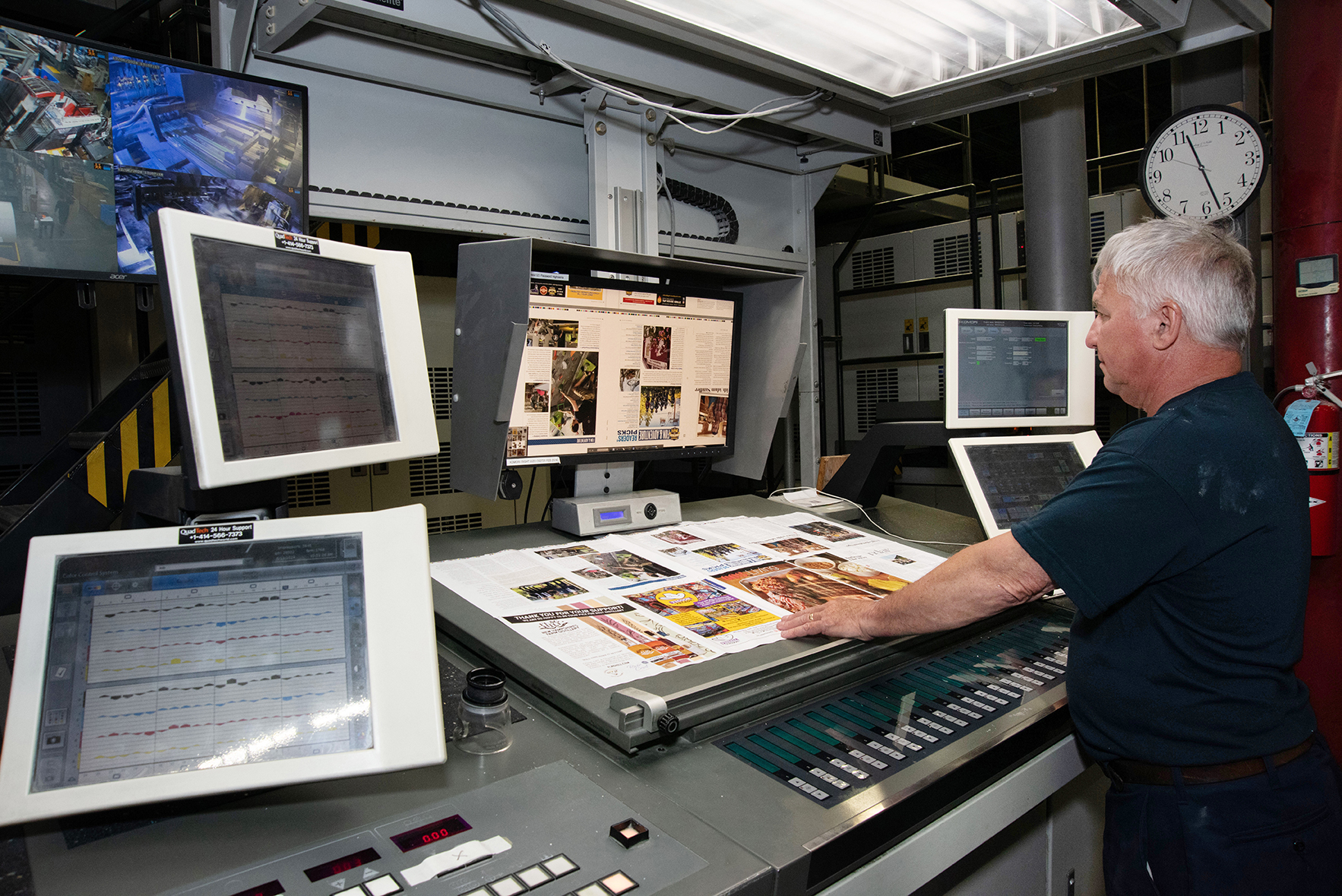
7 minute read
A Perfect Finish
Cummings Printing brings content to life
BY SARAH PEARSON PHOTOGRAPHY BY KAREN BACHELDER
The press thunders along with a rhythm twice as fast as a heartbeat. Thousands of feet of paper inked in repeating images weave through rollers until they’re folded, separated and stacked into “logs.” The run finishes and, for a moment, this press quiets, though the warehouse is still full of the cacophony of the other humming presses, rolling conveyors, stacking bindery machines and slicing trim equipment.
Over the din, the sound of Indiana Jones’ “Raider’s March,” played by a tinkling carousel organ, is heard. Jobs are running smoothly today, and the song is an indication that plates for the next job are being loaded on to the press.
It’s time to print the July issue of New Hampshire Magazine.
After the staff have written stories, taken photos, designed pages, read everything and then edited again and again, they send over the files to Cummings Printing, who complete the monthly relay race of getting the publication into your hands.
Digital files are received from clients, like New Hampshire Magazine, by the pre-press department. The Cummings team checks everything from the resolution of graphics images to the sizing of the spine.
New Hampshire Magazine Art Director John Goodwin says the attention to detail is impeccable, with staff even spotting a newt — the tiny amphibian that has driven a long-time readership promotion — that had fallen off an advertisement in between drafts.
When the pre-flight files are greenlit, it’s off to the press room.
Sheets of coated aluminum are fed through the plate setter. An array of pages is cut into the coating. Four plates are needed for each set of pages, one for each ink used: black, cyan, magenta and yellow.
When the plates are done, they’re loaded onto carts and head out to the presses.
Cummings operates two main web-based presses, a Komori 38D 32-page press and a Toshiba. It also has a smaller single-feed press used for covers that have specialized coatings, like UV, soft touch and course texture.
The 110-year-old company has been offering web-based printing for about three decades from their 100,000-square-foot facility in Hooksett.
“Cummings stays on top of technology,” says Mark Hamel, the chief operating officer. That’s despite the immense cost of production, like the $9 million for their Komori 38D press, which prints New Hampshire Magazine.
The main presses feed paper off rolls
weighing more than 3,000 pounds through a series of rollers. The page is printed — top and bottom — with the black plates, then the cyan, then magenta, and at last, yellow.
Hamel says they run the larger Komori at about 32,000 impressions per hour (iph), while the smaller press runs about 22,000 to 25,000 iph.
Then the paper continues to be fed through a dryer system to set the water-based ink. From there, on the larger presses, the paper is folded, and then the individual signatures are sliced apart. If the magazine is going to be perfect-bound, the inside edge is perforated. The signatures of folded pages are stacked into logs and brought to the binding machine, where they are collated with the other signatures.
With the pages stacked, they head down a bindery conveyor. For perfect-bound magazines, like New Hampshire Magazine, the inside pages are carried along a track. The fold is sliced off the spine. Then, the spine of the pages and about an 1/8-inch of the front and back pages are coated with glue. The cover sheet is pressed on to the spine and clamped around the sides.
While taking the time to travel on a spiral conveyor belt, the glue sets. The top, bottom and outer edges of the magazine are still oversized, so the magazines are stacked, a few at a time and trimmed to the final size.
Alternatively, for magazines getting a saddle-stitch finish, like our sister publication 603 Diversity, signatures are splayed open on a conveyor, collated and stapled.
The cut-offs of the saddle-stitched magazines, which don’t have glue, are baled and sent for recycling.
“Pretty much everything we do is recycled,” Hamel says.
Cummings ships out about two trucks a week of baled paper scraps. The aluminum plates from the press are also recycled.
After they are bound, the magazines may get a label if they’re being mailed, or are boxed for bulk delivery, or they may travel down a polybagging line where multiple publications are packaged together in a plastic seal.
This process is repeated for some 500 publications produced by Cummings each quarter.
Jobs range from a few thousand copies to as many as 400,000. The majority are runs similar in size to New Hampshire Magazine, about 20,000 to 30,000.
“That’s our sweet spot,” Hamel says.
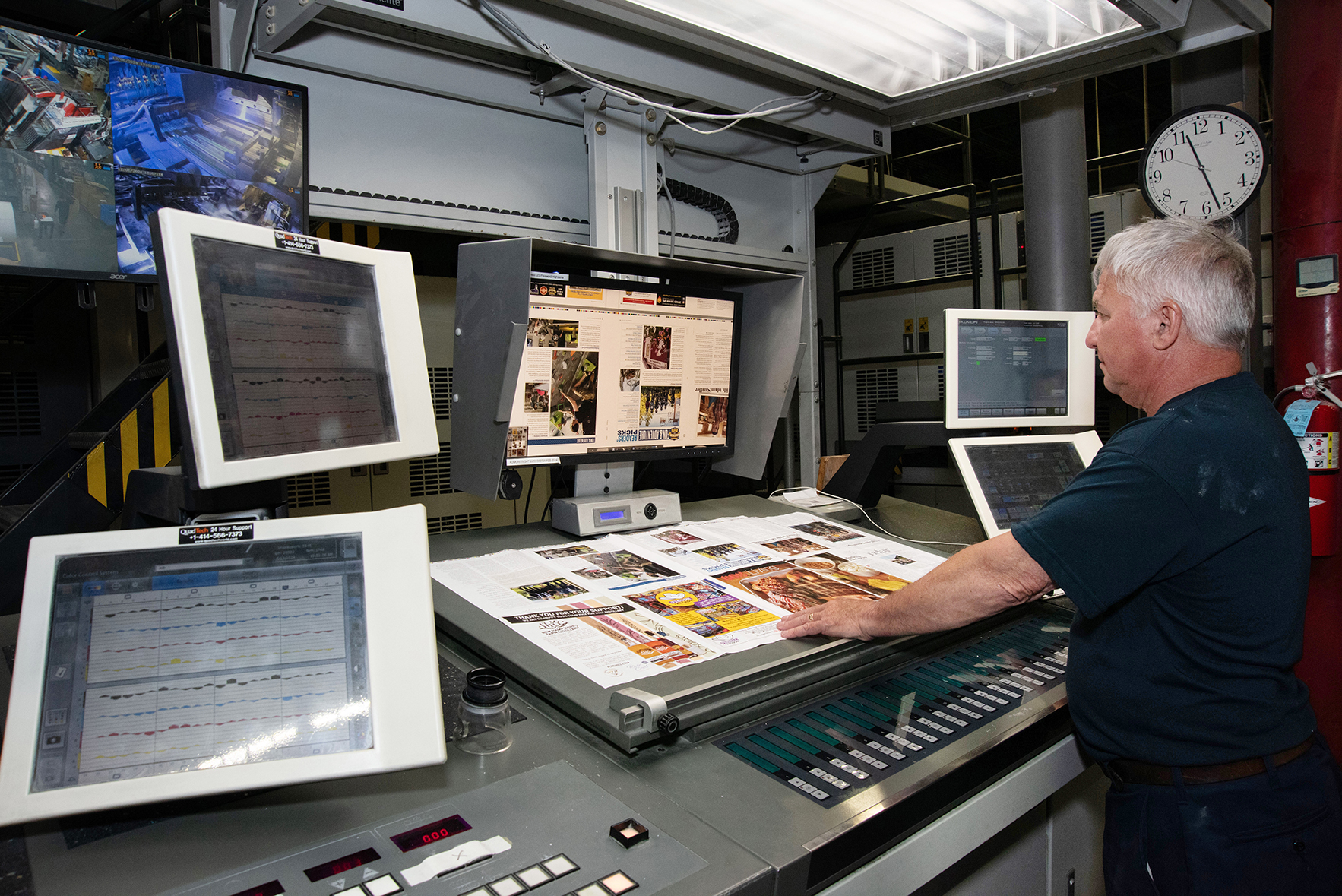



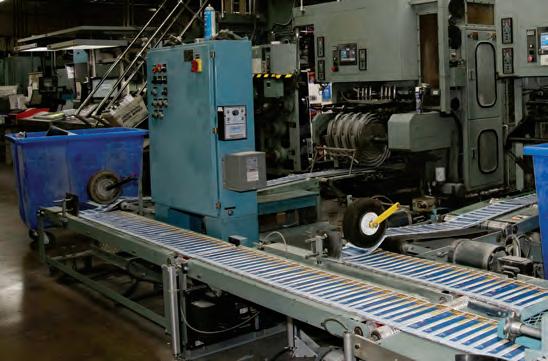


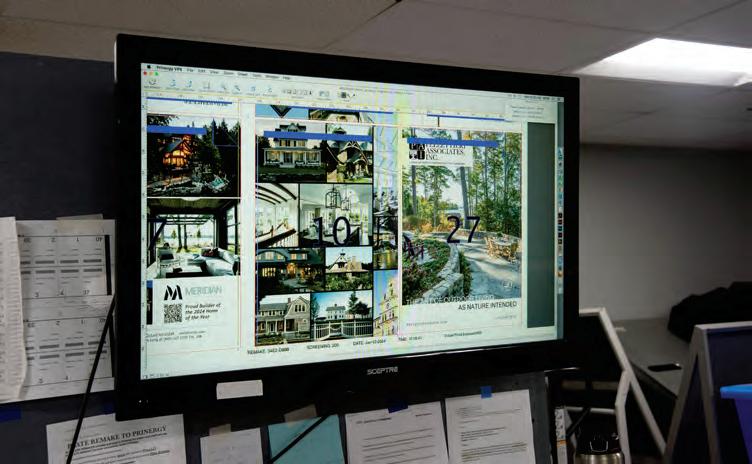
Cummings: Printing Through the Years

Cummings Publication Printing has been operating in New Hampshire for more than a century and is now run by the third and fourth generations of the Cummings family.
It was founded in 1914 by Lew A. Cummings out of a building in Concord and later relocated to Manchester after a fire destroyed the original building.
Printing in Manchester was a lucrative move, and by 1954, the company outgrew its Central Street home, so Cummings built a larger facility on Canal Street. That move came with a shift from letter press printing to a sheet-fed offset press.
Four years later, Lew Cummings died, and his son John Cummings took the helm.
The next generation saw the transition from hot type to four-color offset technology.
As the 1990s neared, magazines were transitioning to web printing technology. But there was no room for that new equipment at the Canal Street print shop.
Jack Cummings became president of the company in 1988 and led a five-year project to build the current plant in Hooksett, a then-65,000 (now 100,000) square-foot facility with new technology and streamlined processes.
The upgrades allowed Cummings to increase sales and complete projects more efficiently, contributing to its growth.
Cummings remains a family company, with Jack Cummings as president and owner. His sons Sam and Chris Cummings are co-chief executive officers, and both started working for the company as teens. But a family focus is not exclusive to its ownership. Chief Operating Officer Mark Hamel, who has been with the company since 1986, now works with his son Jacob, an account executive. Printer Steve Meisel has introduced his son Jeff to working on the presses.
The company has weathered some hard times: two world wars, the Great Depression, near-bankruptcy, and more recently, the COVID-19 pandemic.
During the pandemic, there were immense bidding wars over paper, as supply chains were disrupted and magazines folded or ceased printing.
Cummings was able to pivot to printing health materials for the government like millions of copies of instructions for rapid test kits and perforated health booklets.
“That kept a lot of people employed,” Hamel says. “We got through it, and we’re a better company because of it.”
With family and history behind it and an eye on evolving technology, Cummings is looking forward to a future of printing more high-quality publications.