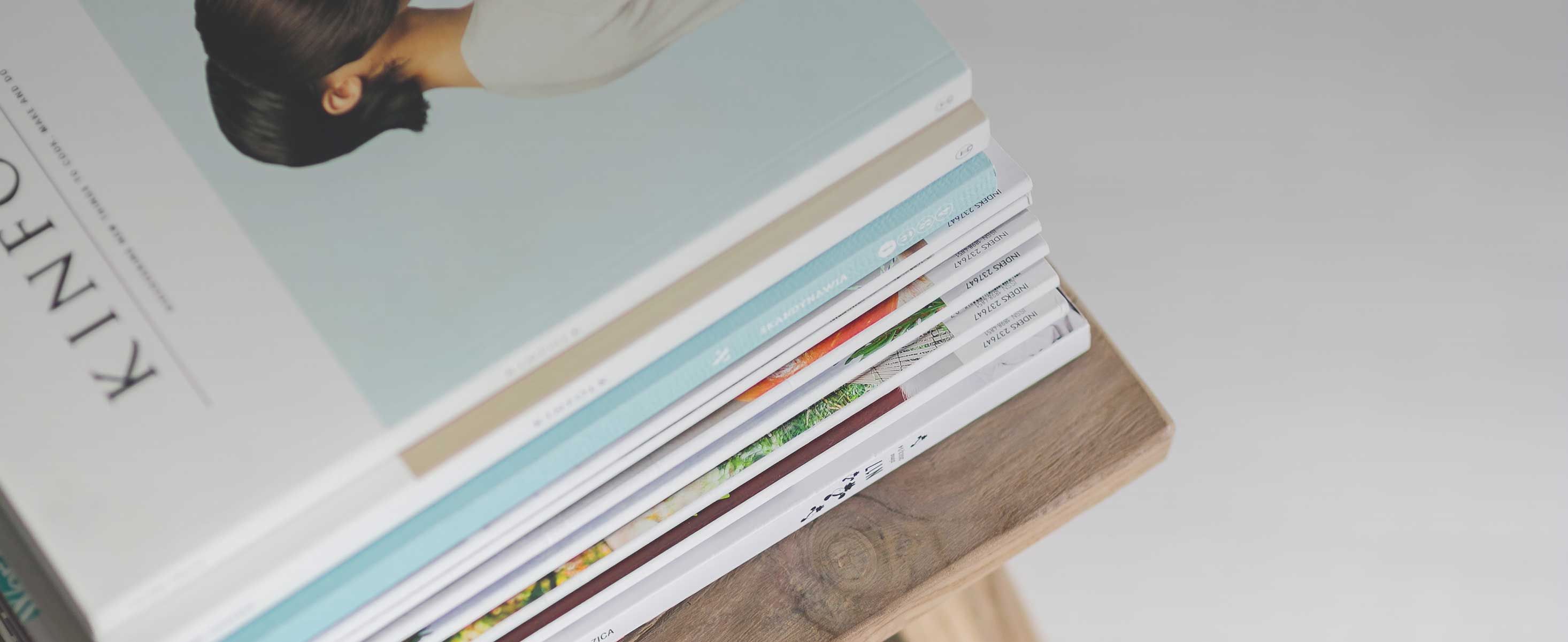
1 minute read
Controlled Fluidics reverse-engineers its way into the PPE market
When it comes to shifting gears, Controlled Fluidics, a Milford-based plastics manufacturer, certainly knows how to do it.
The company, which specializes in manufacturing precision manifolds and plastic components, was recently recruited by the Elliot Hospital in Manchester to help it meet a pressing need for face shields for its healthcare workers.
“I received a call from a surgeon from Elliot Hospital in Manchester,” said Tom Rohlfs, president and principal engineer of Controlled Fluidics. “He desperately needed face shields and wanted to know if we could manufacture them.”
The shields are part of positive pressure face masks which are used by healthcare workers primarily when intubating a patient when placing them on a respirator. The intubation procedure presents one of the greatest risks of infection for any procedure that healthcare workers routinely perform, Rohlfs was told.
The face mask assembly has a removable shield that can be discarded after every patient, preventing contamination and protecting healthcare workers’ well-being.
The emergency room physician told Rohlfs he was down to his last two face shields and had been unable to obtain replacements because of a nationwide shortage of personal protective equipment.
“I drove to his house and picked up one of his two face shields,” Rohlfs says. “My team and I examined it and reverse-engineered it. Within 24 hours, we had a prototype face mask for him. He approved the prototype and ordered 300 of them for the hospital.”
But, after fulfilling the order, Rohlfs discovered that he had a lot of extra material left over, so he advertised more shields for sale to medical workers. The response was tremendous, he said.
Controlled Fluidics was soon receiving calls from all over the U.S. Orders ranged from one shield for an individual nurse or doctor to 10 shields for a clinic to 2,000 for the HMO giant Kaiser Permanente.
In the meantime, the company is also busy making parts for respirator machines.
Rohlfs said Controlled Fluidics has been making parts for medical equipment for a long time, but the company has never experienced such demand.
“One client just placed an order that is five times larger than the biggest order we’ve ever gotten, and they keep calling because they need the parts right away. We’re making them as fast as we can.”