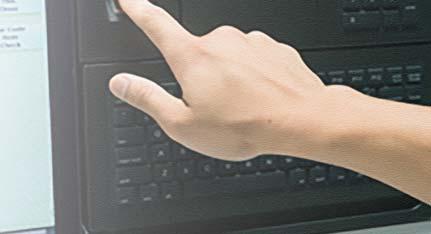
3 minute read
Replacing and upgrading ADCs: lessons learned
Automated dispensing cabinets (ADCs) provide critical support to hospital staff, but they have a finite life span. Two case studies presented at Omnicell Illuminate 2021 provide examples of how to transition to new ADCs at new and existing facilities with minimal disruptions to patient care.
In the first presentation, pharmacy manager James L. Besier, PhD, MS, RPh, of Shriners Children’s Ohio, in Dayton, described how his hospital transitioned from a stand-alone facility to a “hospital within a hospital” with nearby Dayton Children’s Hospital and used six ADCs to compensate for an 82% reduction in the pharmacy’s physical floor space, from 1,608 to 310 square feet.
Shriners specializes in pediatric burn injuries, wound care and pediatric plastic surgery, Dr. Besier noted. “The pharmacy space was reduced [because] fewer burn injuries occur now than in previous years, and health care is more efficient and requires less space,” he explained during his session.
Before the move to Dayton, Shriners had only one working two-cell Omnicell ADC to support 15 acute care beds. After the move, Shriners installed six working Omnicell ADCs to maximize the reduced pharmacy space in the new facility. “Financial resources are better utilized in direct patient care than in brick-andmortar maintenance,” Dr. Besier said. The six ADCs include one within the central pharmacy for Dayton Children’s Hospital, which compounds sterile products for Shiners (as Shiners no longer has its own cleanroom); a controlled substance manager; an anesthesia workstation; two tabletop cabinets in the same-day surgery and post-anesthesia care units; and an inpatient unit cabinet.
Overall, Dr. Besier said feedback from nursing and pharmacy staff has been positive. “The quality of patient care has been maintained because nursing staff particularly are not as confined to manual processes but rely on the improved technology that the Omnicell cabinets provide,” he said. Storage space, however, is still an issue for Shriners seven months after the move, he noted.
Duke’s Approach
In the second case study, Tyler Vest, PharmD, BCPS, BCSCP, the pharmacy manager of automation, medication, distribution and controlled substances at Duke University Hospital, in Durham, N.C., and an assistant professor of clinical education at UNC Eshelman School of Pharmacy, in Chapel Hill, N.C., discussed the process of replacing and updating 250 ADCs at Duke’s main hospital site and 375 cabinets across the entire system over three years. “We are completed with our process now,” Dr. Vest said. “It almost took that full three-year cycle, starting with the evaluation, to [finish the ADC] replacement.”
Aware that the system’s existing cabinets were nearing the end of their lives and running on a soon-to-be obsolete operating system (Windows 7), Dr. Vest and his colleagues started the evaluation and planning process for the replacement in fall 2018. They submitted a business plan to the institution in fall 2019 and started replacing the physical cabinets in spring 2020, a process that lasted until fall 2021.
To minimize disruptions to patient care while swapping out the cabinets, the Duke team developed an eight-day replacement process. The pharmacy team worked with suppliers to receive the cabinets, stocked the new cabinets in the pharmacy, connected the cabinets to the network and configured the settings, and then spent 20 to 30 minutes on the hospital floor swapping old for new. Then the old cabinets went to the pharmacy for destocking before being sent back to be recycled or destroyed.
In a few cases, the pharmacy team just did a “brain swap,” upgrading some of the newer cabinets. The goal was to swap up to four to nine cabinets each week, depending on size.
A project of this magnitude and complexity required considerable cooperation and communication among pharmacy technicians, nursing staff, suppliers, information technology staff and the electronic health care team, Dr. Vest said. Doing a project walkthrough at the start of planning and really understanding the construction needs, where applicable, were crucial for the execution of this project, he told the audience. “You want to understand what are those things that must happen prior to the cabinet being replaced.” —Jillian Mock
—Tyler Vest, PharmD
Helping you deliver better medicine to more people.
Leiters is an FDA registered and inspected 503B outsourcing provider of high-quality compounded sterile preparations and services including: Pre-filled syringes, IV bags and vials Opioid-free surgical pain services medications ON-Q* Pain Relief System fill services Ophthalmology medications including FDA-compliant repackaged Avastin®
The sources reported no relevant fi nancial disclosures.