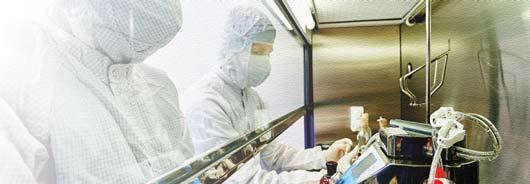
4 minute read
Pharmacy Relies on IV Robots, Batch Compounding to Cope
By Karen Blum, Bruce Buckley and Gina Shaw
As the COVID-19 pandemic surged in spring 2020, the pharmacy at the University of Maryland Medical Center, in Baltimore, faced several challenges affecting inventory management and pharmacy operations. By tweaking its in-house IV robot compounding process and transitioning to making some highly used products in batches instead of patient-specific doses, the pharmacy team quickly accommodated emerging inventory needs.
The main challenge was to come up with solutions that worked for both under- and overstocked medications—both of which occurred, paradoxically, as a result of the panemic. For example, inventory for many normally used medications such as succinylcholine and phenylephrine accumulated because of a fall-off in patient admissions and surgical procedures, Yevgeniya Kogan, PharmD, the hospital’s sterile compounding operations manager, said during the ASHP annual meeting. Other drugs, such as hydromorphone IV bags, went into critical shortages because they were being purchase from 503B vendors, many of which had supply chain issues. The pandemic itself both increased demand for critical care products and generated staffing problems, as some employees stayed home to provide child care or because of a need to quarantine after potential exposure to the SARS-CoV-2 virus.
To overcome these challenges, Dr. Kogan and her colleagues quickly learned to adapt, turning to systems already in place for in-house IV compounding processing by robots, an inventory batch management analysis strategy and a prescribing trends review.
First, Dr. Kogan reviewed the pharmacy’s production schedule to make sure all compounds were still needed, flagging neostigmine for potential removal. The medical center typically used 700 syringes of the drug per month, but only 243 syringes were being used at the height of the pandemic. As COVID-19 evolved, the medical center was seeing a high demand for IV infusions of azithromycin 500 mg, cefepime 6 g, epinephrine 8 mg, furosemide 200 mg, hydromorphone 20 mg, pantoprazole 80 mg and rocuronium 400 mg. She and her colleagues determined they needed an estimated 600 weekly doses of these drugs combined and created a new schedule to batch the medications, in which hydromorphone and epinephrine would be produced by the IV robots while the remaining five products would be made manually by pharmacy technicians. They produced more than 20,000 doses of these medications over three months.
During this period, the pharmacy team continued to carefully monitor inventory of these and other needed medications produced by the robots, such as heparin and vancomycin, including what was on hand and what was expected to be released from their quarantine process each week. They tried to keep three weeks’ worth of extended-dated IV robot products available at all times to account for any increase in demand or production issues.
From June through July, the pharmacy had steady use of azithromycin, pantoprazole and furosemide, and decreases in the need for cefepime as the number of COVID-19 patients began to fall, and in rocuronium as the preferred paralytic agent shortage resolved. Among the robotic compounded products, hydromorphone remained in high use. In contrast, the team temporarily stopped production of hydromorphone because one vendor shipped four weeks’ worth of back-ordered product that had been on shortage.
Among other robotically made products, rocuronium syringes also experienced a significant shortage due to insufficient vial supply, so the pharmacy had to be wise in managing inventory, Dr. Kogan said. They were able to get one of their vendors to outsource the product to stay ahead of the need, she noted. When the vial shortage stabilized, the pharmacy quickly resumed production.
By using these strategies, the pharmacy estimated a cost savings of more than $95,000 over four months from producing drugs as needed and not having them sit on the shelf and expire. “It’s important to develop a dynamic inventory review to adjust quickly to whatever is thrown your way,” Dr. Kogan advised. “And an IV robot compounding program may help buffer the pharmacy department from 503B vendor product shortages.”
It’s also important to be adaptable. During one of the surges in COVID-19 cases, she noted, the Maryland team had to take another careful look at all of their compounding and inventory management strategies and make the necessary adjustments to ensure proper stocks. “It hasn’t been easy to balance that with surging patient care needs, but at least we have tools in place from our experiences in the spring,” Dr. Kogan said. “So far, we are managing to stay about one step ahead of the flood.”
The sources reported no relevant financial disclosures.
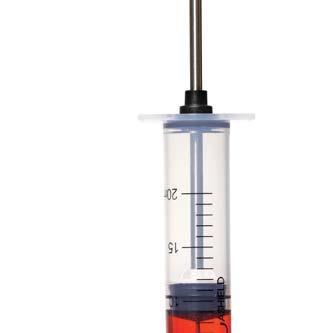
Equashield A Proven Closed System
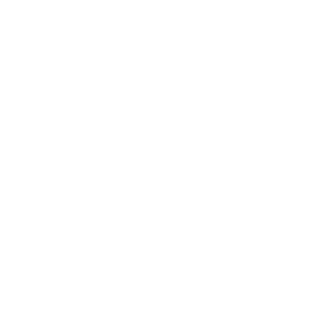
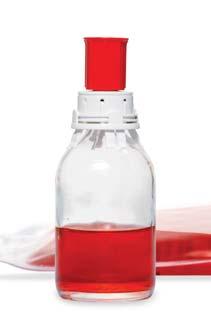
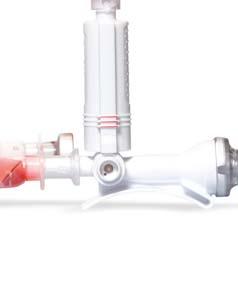
Snapping Vial Adaptor CLOSED Swiveling Connectors CLOSED

Double Membrane Locking System CLOSED Syringe Plunger and Barrel CLOSED
PROVEN as the only closed system to prevent syringe plunger contamination – standard syringe plungers accept contamination with almost every use*. STOPS the escape of hazardous drugs and vapor due to an internal sterile air chamber with a closed pressure equalization system. ADHERES to NIOSH, ISOPP, USP <800> and ONS definitions of a CSTD. PREVENTS disconnection of connector due to a welded connection point and prevents pulling out of plunger by encapsulating lid. NEEDLESAFE: fully encased needle eliminates exposure through needle residue and needle sticks. Prevents residuals of hazardous drugs on connectors and prevents microbial ingress for up to 7 days**.
Welded Connector CLOSED
Snug Fitting Bag Spike CLOSED
+1-855-378-2744 | www.equashield.com