
9 minute read
quality? You should know if the supplier
Quality
Solutions Lifecycle workflow
innovate Quality
innovate patients plan throughput consulting repair plan design
strategy quality management patients throughput webinars management manufacturing
consulting engineering
cost reduction manufacturing management
Solutions service Quality strategy end-user training technical support consulting field service







Could you improve service to your customers if....
• Your repair provider was also an FDA registered medical device manufacturer? • They utilized the same expertise and methodologies in repair as they do in manufacturing? • You had immediate access to complementary technical support when you needed it? • Your customers could receive end-user training proven to reduce costs and frequency of equipment failures?
At Innovatus Imaging, we call this Lifecycle Management and it’s what we do each and every day. Combining expertise in device manufacturing and data from over 200,000+ repairs performed with longevity and sustainability at the core, we’re able to offer up to a 1-year warranty.
Visit us at Booth 502 at MDExpo April 20-22 in Irvine, CA

It’s easy to think that a repair is a repair and so price matters most. Time to think again.
The success of a repair needs to be measured by the sustainability of the repair, the testing that proves its validity, and the documentation showing where
SPONSORED BY INNOVATUS IMAGING the parts came from and the processes executed to get the device back to its original form, fit and function.
Mike LaBree, CTO for Innovatus Imaging, and a seasoned imaging device engineer and manufacturer, explains what happens at a Center of Excellence for Ultrasound design and manufacturing and why protocols and processes rooted in ISO 13485:2016 matter for imaging departments, large and small. Learn what a Center of Excellence for device repair can mean for your inventory by watching this brief 3-minute video.
WHY ACCREDITATION FOR IMAGING DEPARTMENTS MATTERS
Accreditation such as ISO 13485:2016 should not stop with engineering and operations. Quality assurance processes are important for all aspects of a facility.
The American College of Radiology (ACR), the American Institute of Ultrasound in Medicine (AIUM), and the Intersocietal Accreditation Commission (IAC) offer accreditation processes and certification for radiologists and cardiologists to help increase clinical knowledge, and quality outcomes. Accreditation for clinicians requires demonstrating adherence to established standards for image quality testing, equipment maintenance, quality systems, and showing that medical personnel meet standards for interpretation of diagnostic examinations. It also signifies that facilities have audited their strengths and weaknesses and have taken any needed corrective actions to streamline efficiencies and operations to better serve patients. Why this matters: Patients are highly informed consumers and review performance studies on hospitals and caregivers provided by reporting organizations such as Health Grades and other sites which allow consumers to compare hospitals on many factors such as patient experience, timely and effective care, overall value, AND the use of medical imaging. Hospitals that don’t follow best practices for imaging services could be flagged as conducting unnecessary services or missing vital diagnoses.
Clinical engineers play a vital role in quality assurance and accountability for several processes and outcomes, including: • Providing full-service histories, repair documentation, and other activities associated with a device. • Performing frequent image quality assessments in much greater detail than the OEM • Assessing and documenting performance on accessory devices such as ultrasound probes, MRI coils and hard copy devices • Acquiring and assembling Quality Control data for the department applying for accreditation.
Even if your imaging departments are not currently accredited, aligning your teams’ activities with accreditation requirements can help avoid costly mistakes, downtime and other issues that can impact clinicians, diagnostic efficiencies, and patient satisfaction, all of which can impact your hospital’s quality ratings and potential insurance reimbursements.
An additional step you can take to protect your team and patients is to always work with repair providers that have proven their commitment to

quality by becoming and maintaining ISO 13485:2016 certification. Companies maintaining this level of certification provide many added values non-certified providers cannot such as: • Confidence that medical device repairs are being performed according to well-defined processes, that their partners and suppliers are routinely reviewed and qualified, that a system of continuous quality improvement based upon risk analysis is in-place and that the organization is open to external bodies assessing their entire operations. • Assurance that all aspects of the device are addressed during repair to ensure longevity and safe and effective performance. • Knowledge that short-cuts are not being taken during the repair process, which although may be cheaper, could lead to premature or latent failures or more importantly compromised safety or performance.
For more information about certification from ACR, AIUM, IAC, and ISO, download our summary of various accreditation programs, a PDF of our Webinar Wednesday on this topic at www.innovatusimaging.com/resources.
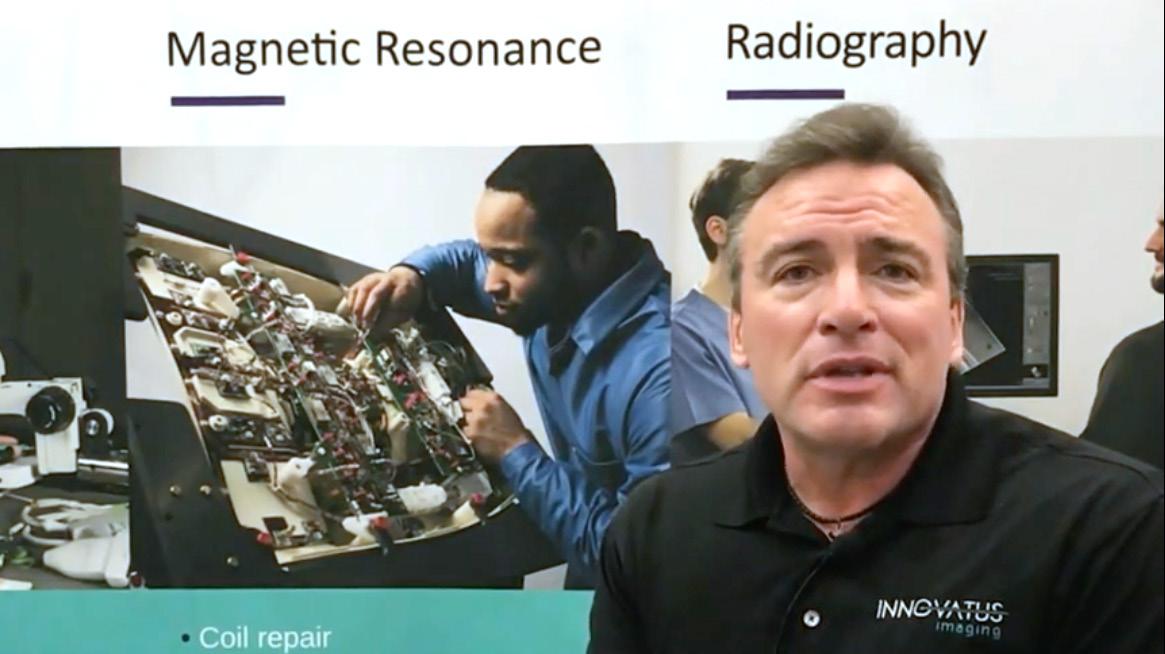
KEEPING UP WITH TECHNICAL ADVANCEMENTS WITHIN ULTRASOUND TECHNOLOGY
Significant advancements have occurred in transducer technology in the past few years, including single-crystal technology, CMUT, matrix array technology and wireless probes. Even though the causes of probe failure remain mostly unchanged, the components within probes and the methods to address the failures have become increasingly challenging. Healthcare organizations have been struggling to find true repair solutions for live 3D volumetric probes, such as the Philips X8-2t, X7-2t, X5-1,
GE 6VT-D, and that most solutions result in replacement versus traditional repair.
Take a few minutes to learn how Innovatus focuses on new technology and how we can help to reduce your overall cost of ownership.
3-STRATEGIES FOR ADDRESSING MRI FAILURES
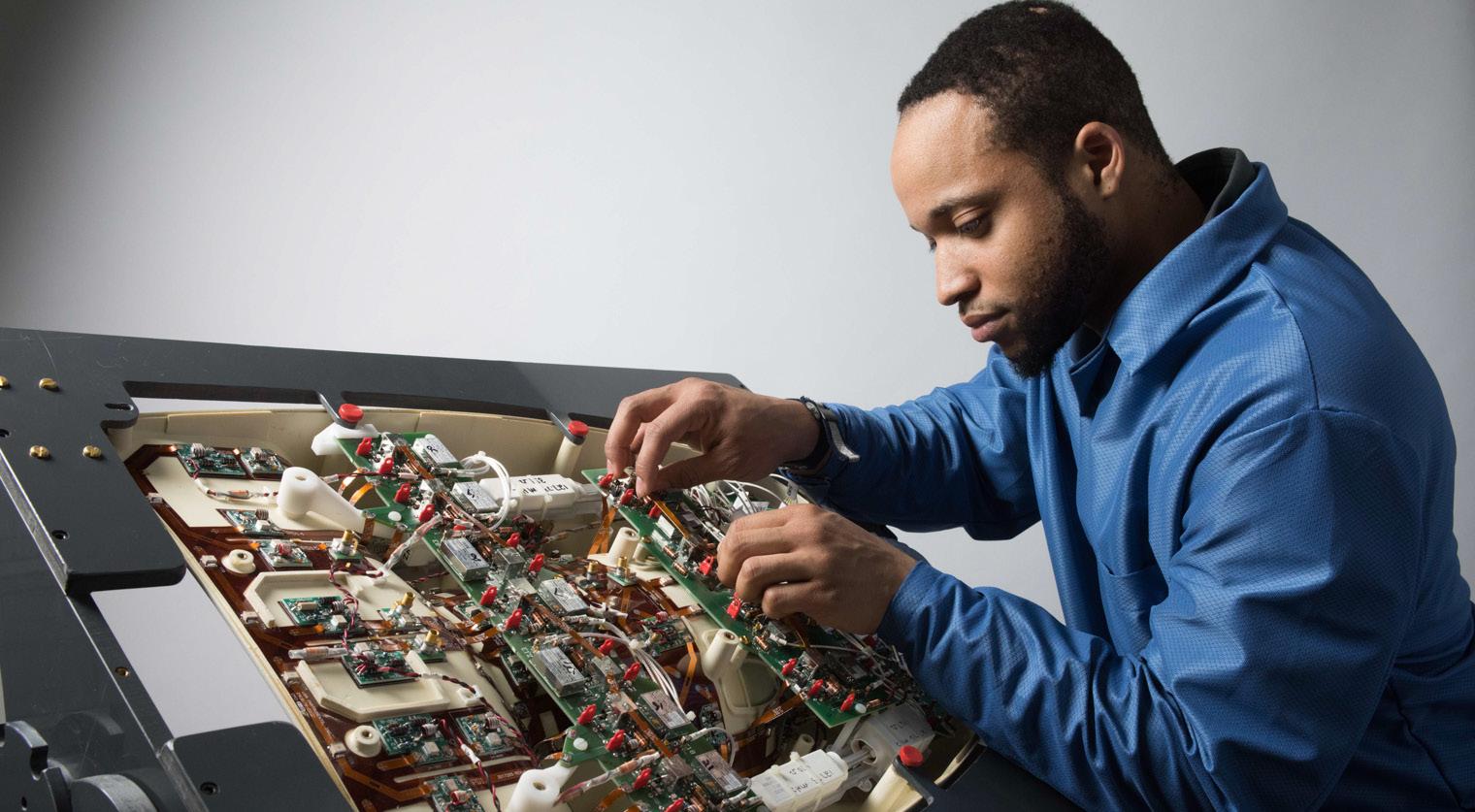
Do you know what's NOT covered under warranty and contract on your MRI? More importantly, do you know how you'll address it?
Warranties and service contracts provide us with a sense of security that sometimes can be misleading. It’s easy to think that because we have a warranty or contract in place, our MRI’s are covered no matter what happens, and we’ll be back up and running in short order. However, what many of us might not know is that warranties and contracts are very different from insurance. You’re only protected under certain circumstances and you’re not covered under others. Like with your car, warranties cover manufacturing defects or failures, not user error or slip ups.
Scenarios involving user error or human slip ups occur every day in healthcare facilities. For instance, while prepping for an MRI, a technologist drops a large body coil. While performing a scan, the patient loses bladder control. The magnet is quenched because a ferrous object is pulled into the field. While lowering the patient table, an MRI coil's cable becomes trapped and is partially severed. Whether a new MRI, covered under warranty, or an older model, covered under OEM contract, addressing the failures described above are, most times, the responsibility of the facility.
It's not new. Failures considered preventable, avoidable or attributed to trauma and/or misuse are often not covered by an OEM service contract. In the chance that a single, preventable, event IS covered, it most likely won't be a second time. Understanding how and why out-of-pocket expenses occur and developing contingency plans for when preventable failures occur can have a huge impact on service budgets. For example, MRI coils.
With a core team that once manufactured MRI coils, and a major repair provider for all makes and models for more than 25 years, Innovatus Imaging has amassed a large amount of failure analysis data. Data shows that most MRI coil failures are a direct result of or related to mechanical damage or trauma. Over 35% of all
coils present with mechanical damage due to trauma and an additional 18% are RELATED to trauma and/or improper use.
Typically, when a coil fails, the OEM sends a replacement next day. It may take days or weeks before an invoice is received highlighting preventable damage and the out-of-pocket expense. You may be surprised to learn that some OEM's install shock sensors within their coils to determine if the coil has been dropped or exposed to an unusual amount of force. So, even though there are no outward signs or trauma or mechanical damage, coverage may be denied.
The tough reality we must face with most contracts we buy is that 50% of your coil failures may not be covered. Having to absorb an out-of-pocket expense of $35,000 - $100,000+ for a single coil failure can ruin any budget. At one point or another, we've all been asked, "Did you read the fine print?" Analyze your options when considering a service contract on your MRI. 1. Insure that, if you have a service contract, that ANY and ALL
failures are covered in the final cost. Costs will be high, but this option can ensure maximum uptime and continued workflow while eliminating out-of-pocket expenses. 2. If a standard OEM service contract is in-place, use an ISO 13485:2016 certified repair provider, such as Innovatus Imaging, to address any coil that shows evidence of preventable or avoidable damage. And, if there is ANY mechanical damage, do not assume that a replacement coil, through the OEM, will be covered. Address the failure via repair or non-OEM replacement using a qualified provider. 3. If magnets are not supported in-house, service contracts are a must to insure uptime and continued workflow. Knowing that over 50% of coil failures may not be covered provides some powerful information. Consider removing MRI coils from the service contract altogether. It is possible and there is a huge cost savings to be realized. Coil repairs start as low as $500 and some repair providers offer loaners and/or expedited repairs.
Why this matters: The bottom line for any facility, large or small, is simple: When selecting a repair provider, be sure that repairs are performed with longevity in-mind. Ask about their length of time in the industry and quantity of repairs performed. Both matters. For example, the team at Innovatus Imaging is applying experience from over 25 years and 30,000 plus repairs to define best-inclass coil repair processes and even help predict potential future failures. Ultimately, providers should demonstrate a dedication to quality by having ISO 13485:2016 certifications specific to the medical device(s) they support.
For more information on how Innovatus Imaging can help to reduce your service budget with quality, sustainable repairs for MRI coils and US probes, please contact info@innovatusimaging.com.

Our Repairs Are Priceless Too
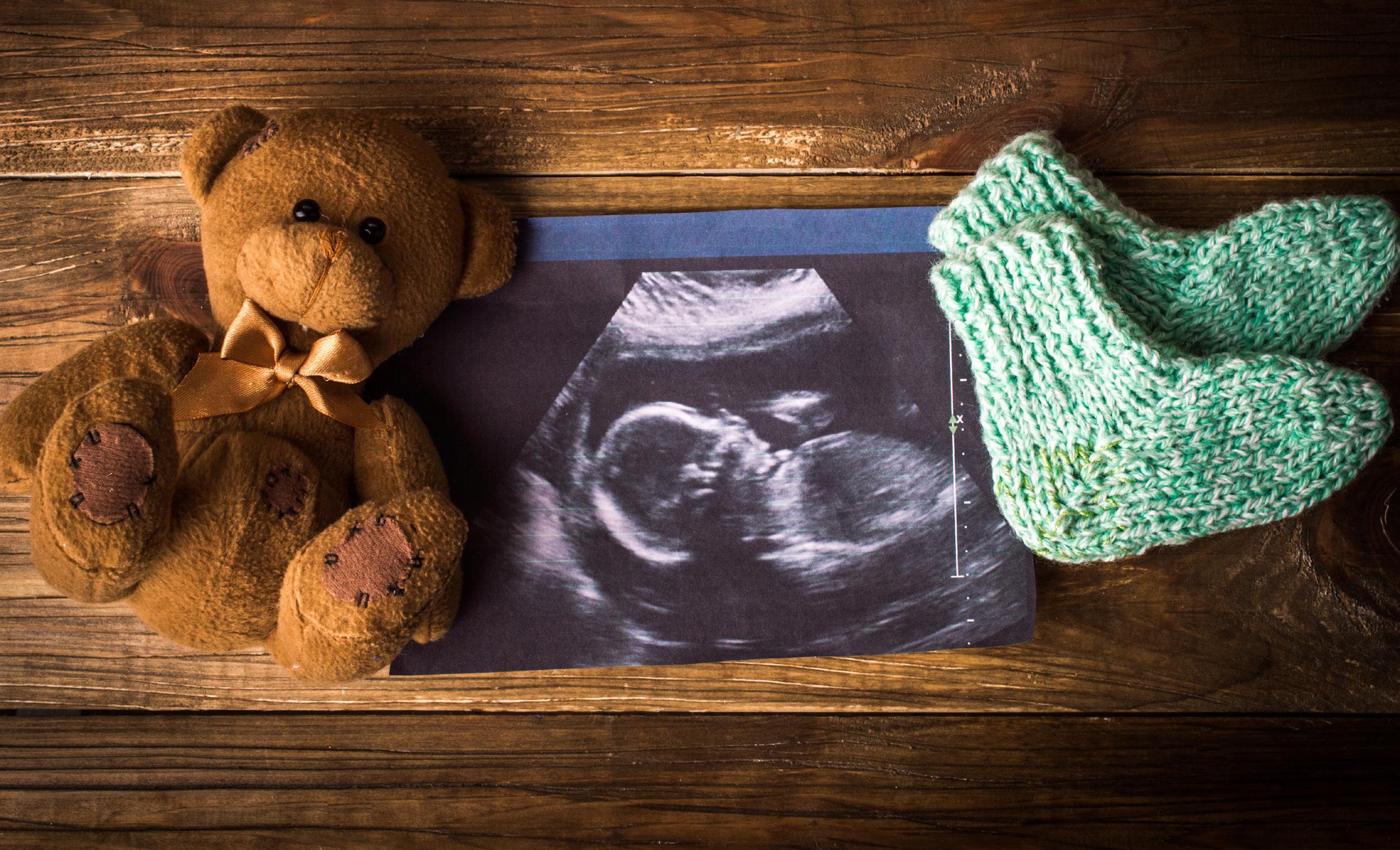
The process behind every repair is what ensures your probes will be reliable for your patients in critical moments.
Our Denver facility is FDA-registered as an ultrasound probe manufacturer and we apply some of the same processes, technology and testing to our repairs as we do in manufacturing.
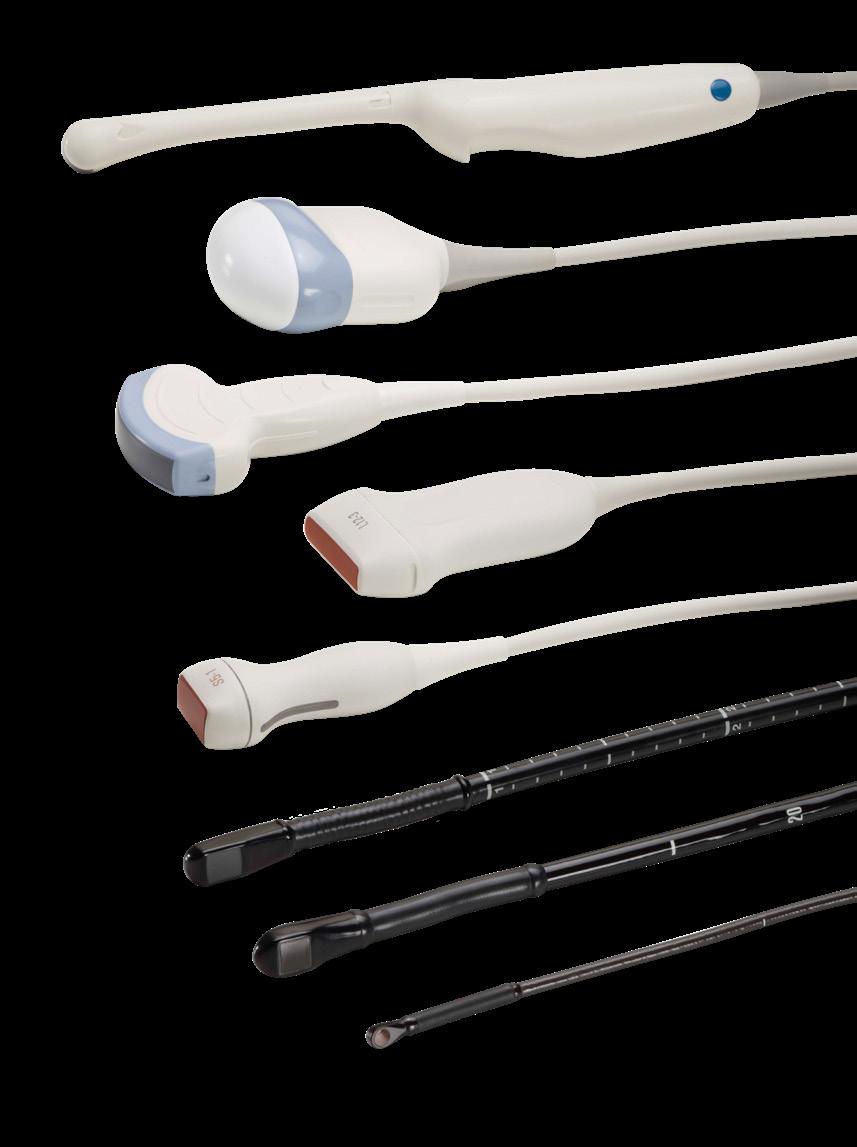
With over 40 years of research & testing, 150,000+ completed repairs and some of the broadest probe repair capabilities on the market, you can trust your probe with us.