
10 minute read
THE PERFECT FIT FLAWLESS FILTRATION
a high-quality product, but it also reduces the likelihood of returns or spoilage-related losses for the brewery.
There are several different types of liquid filtration methods that are commonly used in brewing processes, each of which offers a unique set of advantages and disadvantages.
It is efective for removing particles of all sizes and can be used over longer periods of time than other methods.
Since the early 1970’s, ultraflter has been providing the food and beverage industry with best in class, validated sterile air, clean steam, and liquid fltration products. From the beginning of the brewing process, through to the fnished product and packaging, ultraflter has you covered to ensure ultimate consistency, and purity to deliver the highest quality product possible.
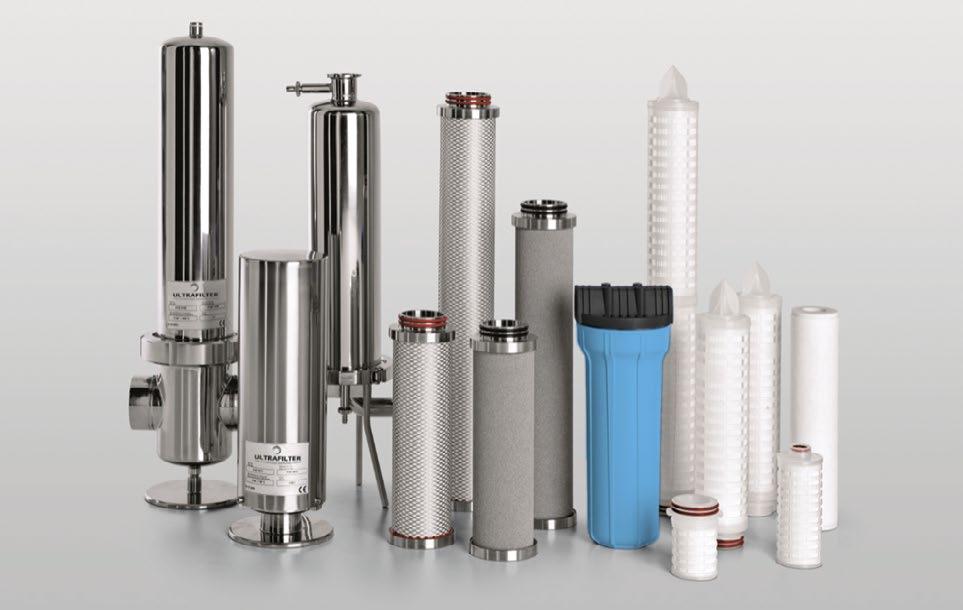
Let’s begin with Liquid Filtration . An essential step in the brewing process, as it helps to remove unwanted particles from the beer and ensure that it is clear and visually appealing to consumers. Suspended solids, such as yeast, grains, and other contaminants, can negatively afect the overall taste and appearance of the beer. ultraflters range of cartridges and housings provide solutions for any brewing application.
Filtration is also important for maintaining consistency in the brewing process. By utilizing fltration, brewers can ensure that their beer meets a specifc, and consistent standard every time it is produced. This is crucial for large-scale operations and for beer brands that are looking to establish a consistent taste and quality across their portfolio.
Utilizing the correct type and grade of fltration can also help to extend the shelf life of beer by removing impurities that can lead to spoilage or undesirable favors. This not only ensures that consumers are receiving
The most common style of flter, is depth fltration: This type of fltration is often used to capture and prevent larger particles and suspended solids, such as Diatomaceous Earth (DE), from entering the Bright Tank.
Surface fltration: In this type of fltration, the liquid is passed over a flter membrane, which traps particles on its surface. It is efective for removing smaller particles but can be costly and may require additional processing steps to remove trapped particles from the membrane.
Centrifugal fltration: This method uses centrifugal force to separate solids from liquids. It is efective for removing heavy particles but may not be as effective for very fne particulates.
Crossfow fltration: This technique uses a flter media that allows the liquid to pass through, while particles are trapped and removed from the system.
Overall, the choice of fltration method will depend on the specifc needs of the brewery and the goals of the brewing process. Our team ofer no charge discovery calls to assess what will suit your brewery the best. From our experience, the biggest liquid fltration challenges facing a master brewer today are related to process efciency, consistency, and quality control. Here are some of the specifc challenges that brewers face. How do these compare to your own challenges?
Efciency: Liquid fltration can be a time and resource-intensive process that slows down the overall brewing process. Brewers need to strike a balance between the speed of fltration and the efectiveness of the purifcation process. Solutions to improve fltration efciency include optimizing conditions, streamlining fltration protocols, and using the right type and size of flter technology for specifc application(s).
Consistency: We often receive feedback from brewers stating that they struggle to ensure that the quality and taste profle of the beer remains consistent from batch to batch. Filtration is an important part of this consistency process, but at the same time we need to be cognisant that fltration does not inadvertently alter the favor and aroma of the beer.
Quality control: Another challenge is ensuring that the beer is free from contaminants, such as bacteria and yeast, as these can negatively impact the quality of the fnished product. Brewers need to have robust quality control programs in place to ensure that fltration is removing unwanted particles and that the fnal product meets their quality specifcations on a consistent basis.
With ultraflters validated, and DOP tested range of cartridges, we ensure and guarantee a repeatable, measured consistency of performance.
Cost: Filtration can be an expensive consumable for breweries, especially if they are processing large volumes of liquid. A balance between the benefts of fltration and the cost of the setup and operation of the purifcation process are essential. Some fltration methods, such as depth fltration, can be carried out with relatively low capital and operating costs, while other methods, such as carbon fltration, require signifcant capital investment. The ultraflter team consult with you to ensure that the housings and cartridges are correctly sized, while selecting satisfactory micron ratings. Factory direct pricing enables us to drive your fltration costs down, while always retaining fltration integrity and efciency.
Lead time challenges: These are a major issue for brewers, “and purchasers alike when it comes to liquid flter cartridges.
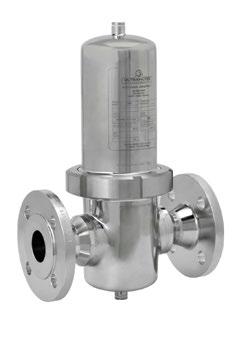
Common ones include:
• Limited availability: Some flter cartridge types may only be available from a few suppliers, and those suppliers may have limited stock of the flter cartridges. This can lead to longer lead times, especially if the cartridges need to be shipped from overseas or made to order.
• Unpredictable demand and consumption: Brewers may experience sudden spikes in demand for their beer, which can put a strain on their production and subsequently the fltration supply chain. If they do not have enough flter cartridges on hand to meet demand, they may experience production downtime or delays.
• Customization needs: Some brewers may require custom flter car- tridge designs to meet their specifc fltration needs. This can increase lead times, and costs, as the cartridges may need to be manufactured to order.

• Shipping delays: Transportation delays became the # 1 complaint during the recent pandemic. In addition, moving products can be afected by weather conditions, labour strikes, transportation, and logistical issues.
At ultraflter we have invested in a “Double Order Program”, whereby we process exactly what you order and then duplicate the quantities you ordered for our own inventory purposes. This ensures that we have the cartridges you consume in stock the next time you need them. We call it ultraplanning. It’s a Value Added Program we ofer to assist you in over- coming supply chain challenges.
The ultraplanning process begins with ultraflter performing a no charge discovery call to identify the fltration you are currently using. We list each housing, its point of use and the cartridge or element details associated to each one.
Next, we survey the stores area, or inventory crib, to take stock of the on-site filter inventory.
Together we discuss and agree on min/ max levels, and our objective is to guarantee zero outages
Note: We often identify duplicated inventory, where person X purchased part # 1234, and person Y used a diferent supplier to purchase a similar product but with a diferent nomenclature/part #.
Everything is catalogued to ensure that we achieve:
CFIA and other industry related audits are a breeze when it comes to demonstrating flter change out times, dates, and completion, as ultraplanning documents everything, within the program.
A consistent and reliable supply chain of flter cartridges, from a single source.
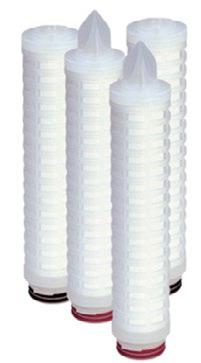
Forecasted demand, with recommended change out dates. Replacement flters can be ordered, and delivered well in advance to ensure an adequate supply is always maintained and available.
Optimized cartridge usage and on-site inventory, to eliminate inventory duplicates, and reduce the need for unnecessary replacements. This will also negate against lead time delays.
Explore and consider alternative filtration methods, to lower filtration costs and multiple inventory filter types and styles.
Fixed pricing, over a term to be agreed upon, so as price increases and market volatility don’t afect the agreed ultraplanning program prices.
Sterile compressed air is an important input in the brewing process as it ensures the elimination of contaminants, such as bacteria and mold, which can negatively impact the quality of the beer. The use of sterile compressed air is critical for maintaining consistency and reliability in the brewing process. Here are some of the ways that sterile compressed air is used in brewing:
Carbonation: Compressed air is used for carbonation of beer and other beverages. Sterilized compressed air is used to force carbon dioxide into the beer in order to give it the characteristic efervescence and head.
Fermentation: Sterile compressed air is used during the fermentation process to introduce oxygen and circulate the wort. This helps to encourage the growth of healthy yeast and other microorganisms, which play a critical role in the fermentation process.
Bottling and kegging: Sterile compressed air is used during the bottling and kegging process to ensure that no contaminants, such as bacteria or fungi, are introduced into the beer. This helps to ensure that the beer maintains its integrity and favor profle, which is critical for maintaining customer satisfaction.
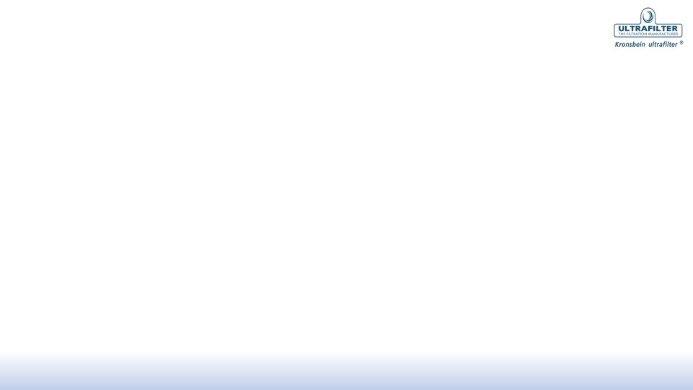
To ensure that compressed air is sterile, brewers use ultraflters P-SRF range of 0.2µ, steam sterilizable flters. The P-SRF should be protected by pre flters to remove contaminants such as moisture, oil, and particulate The P-SRF can be steam sterilized 100 times, guaranteed, or autoclaved.
Brewery bottle washing involves a cleaning process that typically uses a combination of mechanical and chemical methods to remove impurities and contaminants from bottles prior to flling them with beer. One common method of fltration used in brewery bottle washing is a multi-stage fltration process that includes the following steps:
Pre-fltration: The frst stage involves coarse pre-fltration to remove large particles and debris such as labels and bottle caps. This step is crucial to protect downstream fltration stages from clogging.
Carbon fltration: The next stage involves carbon fltration to remove organic matter and other impurities, such as odors, that could afect the favor and aroma of the beer.
Fine fltration: This fnal stage involves fne fltration, where a flter cartridge with smaller micron pore sizes is used to capture any remaining particles and bacteria that could be harmful to the beer.
Overall, the combination of these diferent types of fltration is efective at providing a thorough cleaning process that removes impurities and ensures that the bottles are clean and ready for beer flling. Each brewery may use slightly diferent approaches to bottle cleaning depending on their specifc needs and preferences.
Brewery Filtration Applications: Want a guide to application specifc flter data base and info? Then read on....
Sterilizing in Place (SIP Skid) To avoid contamination, equipment downtime and ensure process safety it is critical to flter steam. Ultraflters P-EG housing and our P-SWM 25 and 5 micron steam elements ensure purifed steam for your SIP system.
Boiler Feed Water
Only with clean water can brewers produce and ensure purifed steam, therefore it is prudent to flter the boiler feed water. Feed water con- sists of returned condensate and fresh make-up water. Contamination in this water can be introduced into the steam system and compromise the boiler efciency. ultraflter PF-EG housings and P-SM flter elements are designed to handle the high temperatures and solids associated with feed water fltration.
Steam Heated Mash and Lauter Tun When producing beer, a production step known as mash out separates the mash into a clear liquid Wort. The frst step of the process is referred to as mash out in which the mash is heated to a temperature of 171°F, (77 C°) . This is achieved through direct steam contact or with a Lauter Tun. To ensure that the heat transfer equipment is operating efectively and reliably, it is essential to flter the steam. ultraflter P-EG housings and P-SWM, and P-GS 5 micron flter elements remove contaminants that could reduce heating efciencies over time.
Yeast Propagation Systems and Wort Aeration
To start the fermentation process, breweries utilize Wort Aeration and Yeast Propagation systems which require ultraflters P-SRF Sterile air and oxygen flters to kick start the fermen- tation process. ultraflters P-GS Steam flters are used to sterilize the equipment between production batches. Using ultraflter’s P-GS Culinary Steam and P-SRF Sterile Air Filtration ensures that yeast growth is done effectively and consistently each time.
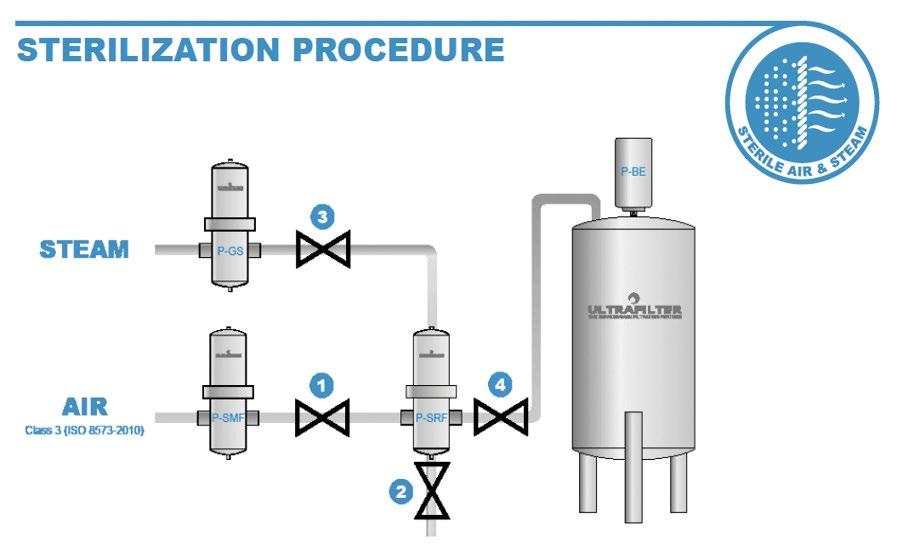
Product Push Out
In some productions CO2 may be used to push out the product and clean processing lines. ultraflter’s P-EG housing and P-SRF flter element ensures that the CO2 is sterile and will not contaminate the fnished beer or equipment.
Counterbalance Filter
Counterbalancing is used as an alternative to tank ventilation. ultraflter’s P-EG housing and P-BE sterile air flter, placed in the balance line, will prevent cross-contamination.
In-line Carbonation
When carbonating beer venturi pipe aeration systems are utilized. To ensure that quality standards are maintained, it is essential that all CO2 gas is fltered. ultraflter’s P-EG housing and P-SRF flter element ensures that the CO2 is sterile and will not contaminate the fnished beer or equipment.
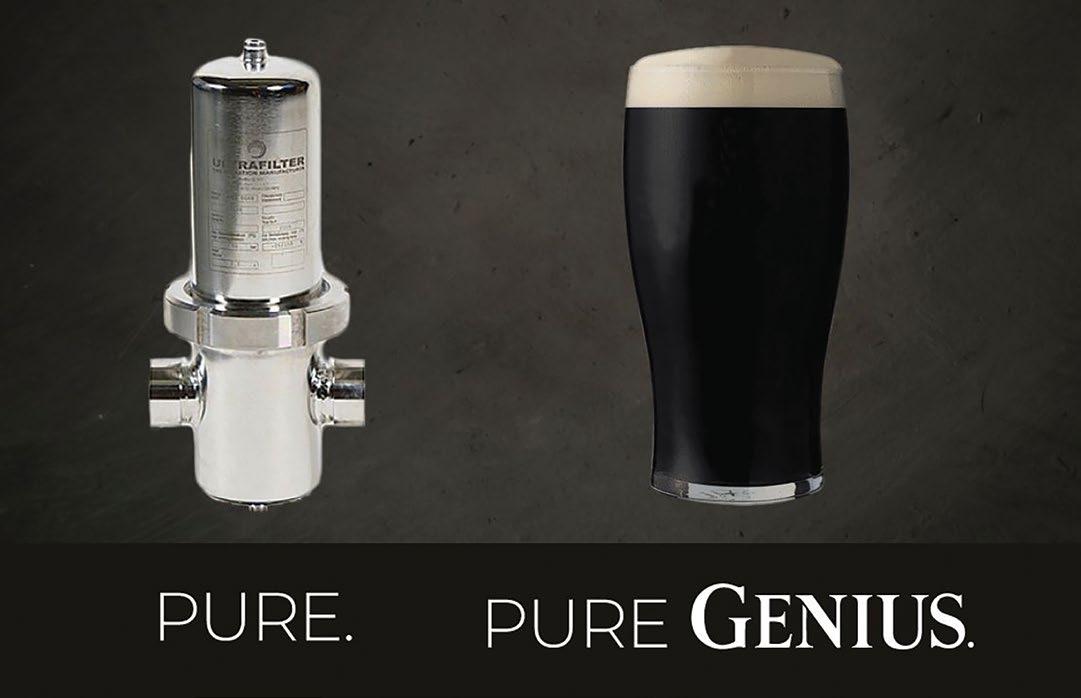
Trap Filter / Blank Filter
During Beer production Diatomaceous Earth is utilised to turn the beer into a clear substance. The DE must be fltered with a blank flter. To ensure a bright and clear product, the Trub must be fltered out. For both fltration steps, ultraflter’s PP100 & PP elements with our sanitary PF-EG flter housings are a recommended flter combination.
Keg
Washing / Sterilization Equipment
The rinse water used in the cleaning and sterilising of Kegs must be fltered to ensure contaminant free storage of the fnished product. Filtration at this step is critical and serves to protect customer investment. ultraflter’s PFEG housing and PP100 flter element can provide the necessary point of use fltration.
Cold Sterilization and Filling Machine
Ultraflter’s PF-PES flter range removes beer spoiling microorganisms and ensures a long shelf life. ultraflter’s P-EG housing and sterile gas flter is used to clean bottles and purge oxygen before flling. The sterile air flter P-SRF ensures that the counter pressure gas used during the flling process is free of any microbiological contamination. ultraflter’s fltration helps support the integrity of these processes and to produce a consistent quality product.
Clean steam is a vital component for many brewing processes as it is used to sterilize equipment and provide sanitary conditions for the brewing process. Filtration plays an important role in en- suring that the clean steam is free from impurities that could afect the quality and safety of the fnal product.
Here are some of the reasons why clean steam fltration is important in brewing:
Quality control: Impurities can negatively impact the taste, aroma, and overall quality of the beer. Filtration of the clean steam can remove contaminants such as particulates and microorganisms, ensuring that the steam is sterile and free from impurities that could negatively impact the quality and safety of the fnal product.
Safety: The presence of certain impurities such as bacteria and viruses can be a safety hazard, causing infections or illnesses. Filtration of the clean steam helps to ensure the safety of the brewing process by eliminating these hazardous microorganisms.
Equipment protection: Impurities in the steam can accumulate in the system and cause scale build-up, corrosion, or fouling, which can damage the equipment or cause inefciencies. Filtration can remove these impurities and protect the system from these potential problems.
Compliance: In the brewing industry, there are strict regulations and standards for the quality of the beer. Filtration of clean steam helps brewers to meet these compliance requirements, ensuring that their beer is safe and of high quality.
Overall, clean steam fltration is an essential step in ensuring the safety, quality, and consistency of the brewing process. It helps brewers to maintain high standards of quality and safety, control costs, and improve
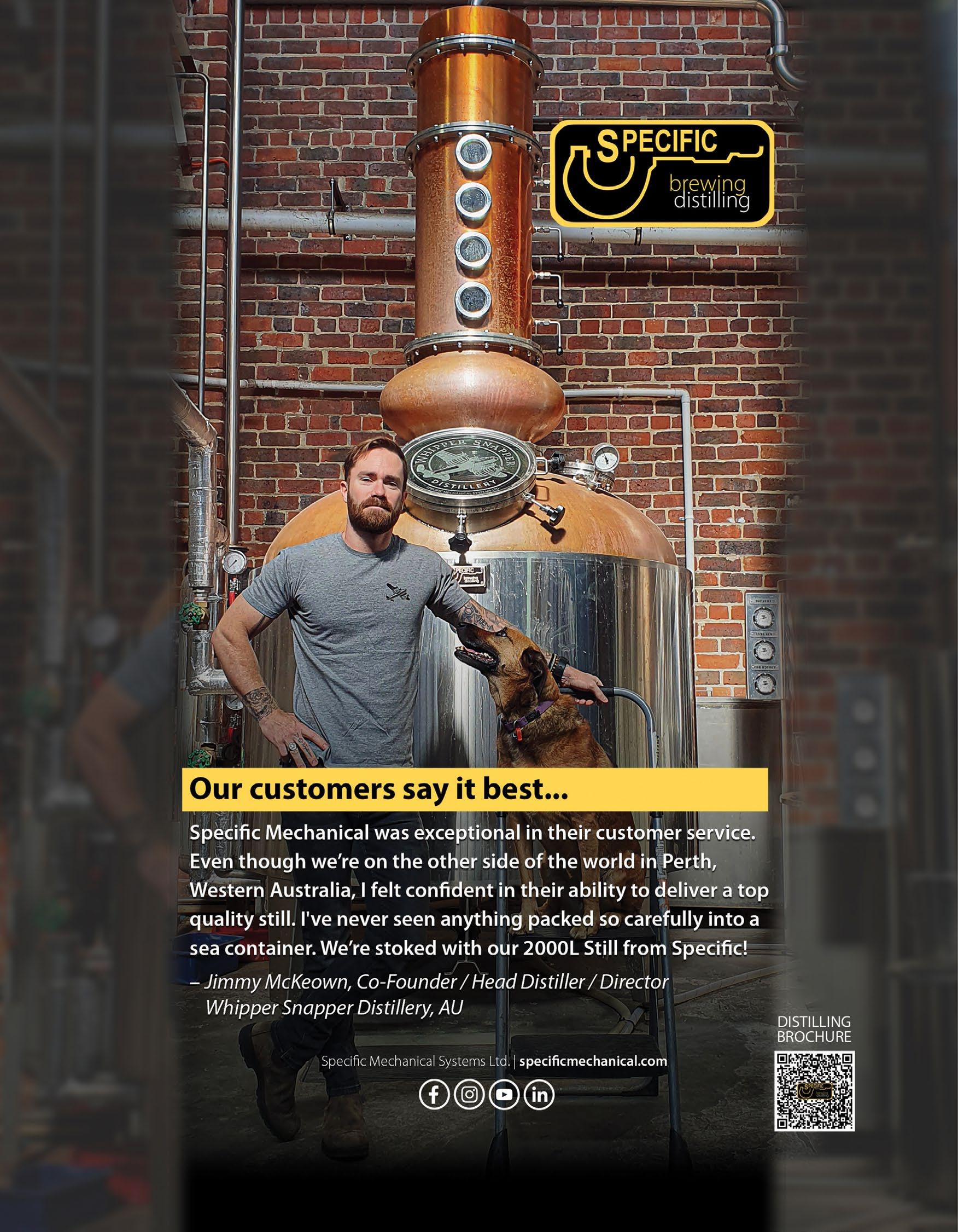