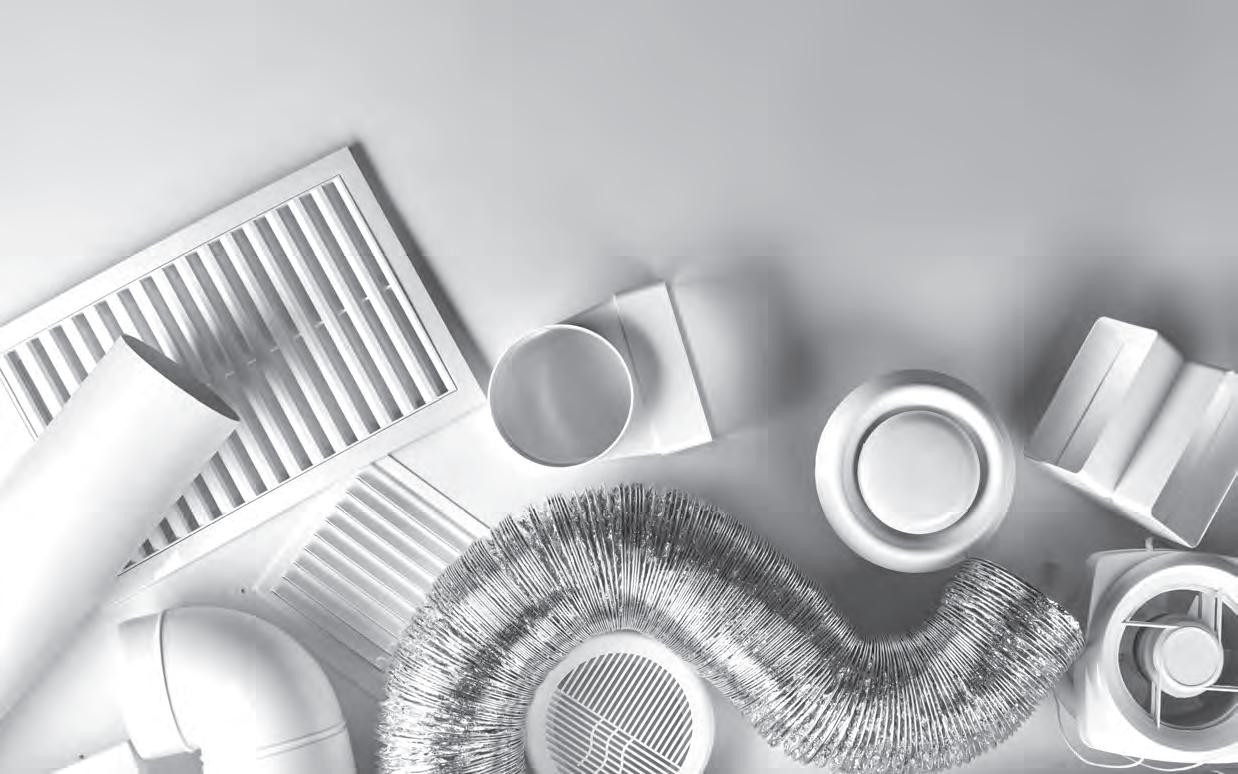
18 minute read
HIGH-PERFORMANCE HVAC
UPDATED RESOURCE IS A VALUABLE TOOL
Manual offers the latest information on ducted forced air distribution systems
The new sixth edition of the Residential Air System Design Manual (RASD) from the Heating Refrigeration and Air Conditioning Institute (HRAI) is the culmination of a collaborative task group, which included nation-wide input from HVAC contractors, HVAC designers, manufacturers of both equipment and duct systems, building officials, energy advisors, utilities, researchers, government representatives and HRAI instructors. The edition is a consensus documentation of the latest information with respect to ducted forced air distribution systems in residential applications. I am reporting on some of the changes and additions I feel will be of help to the residential HVAC industry. The task group members who contributed to the sixth edition of the Residential Air System Design Manual have recognized and responded to the compelling changes in ever more efficient but complex new houses and the challenges that may present to effective air distribution. Special recognition is due to Tom Cates, a long-time HRAI trainer, who took on the task of doing the technical writing.
Scope reflects important advancements
RASD was reorganized, starting with a concise Section One defining the scope of the document and clearly laying out the minimum requirements of residential forced air systems compiled from the National Building Code of Canada, provincial building codes, and standards that are referenced in those codes. This Section will be helpful to HVAC system designers and HVAC contractors working specifically in the new construction market as it ensures quick access to code requirements for consistency and clarity in preparing building permit applications. Indeed, this section identifies that while the manual may be helpful to contractors in renovation projects, its primary focus is on systems designed for new home construction. In this regard, the manual has updated the scope to reflect important advancements in equipment, ducting systems, and house construction. For example, the scope identifies a “Total Available Duct Pressure” range of 0.100” w.c. to 0.800” w.c. (25 Pa to 199 Pa). Identifying this specific, and I would say expanded range, recognizes the capabilities of electronically commutated fan motors, and equivalent technologies, to operate at higher system static pressures. The lower range similarly acknowledges the capabilities of smaller capacity, “mini-split” systems that may offer some limited ducting options. The expanded system pressure range offers important flexibility in ever more efficient houses with much smaller overall heating and cooling loads, but which still have the need to distribute air effectively. The extra system pressure available at the “end of the line” can allow for diffusers with better throw and spread characteristics to ensure comfortable living spaces.
Gord Cooke Gord is a professional engineer who has spent 35 years helping builders and HVAC contractors implement innovative technologies into high-performance homes. He has particular expertise in IAQ and airflow management in houses, and can be contacted at gordc@buildingknowledge.ca.
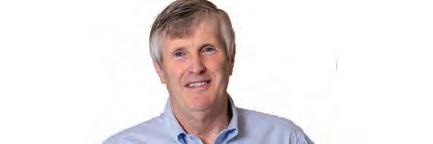
A range of options Reinforcing the importance of duct sealing Basements as livable spaces
Section Two of the Sixth Edition is titled “Optimizing Performance Through Design” and the introductory remarks clearly indicate this section provides good engineering practice information from industry resources such as the ASHRAE Handbooks and the ACCA Manuals. The remarks go on to say that the information in Section Two goes beyond the minimum requirements of Canadian building codes. RASD helps separate or delineate the code obligations of builders and their HVAC trade partners from approaches offered as enhancement or upgrades for optimized performance. I trust that professional contractors will use this important delineation when asked for opinions, specifically in new homes, to help resolve disputes between homeowners and their builders rather than escalate them.
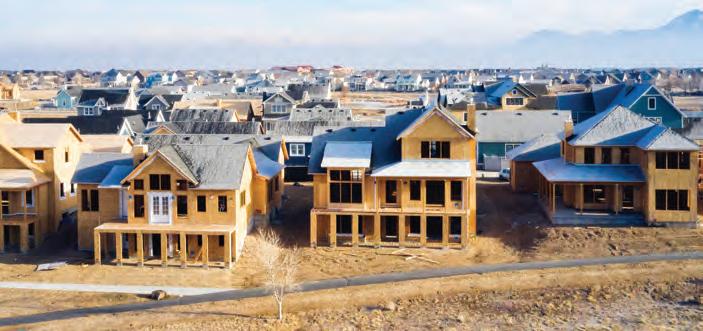
There are two specific topics in Section Two that can be helpful in both new and existing homes. There is good discussion of return air design systems that starts with the concept of return air “pathways.” Recognizing that if conditioned air (warm or cool) is to be effectively distributed to a room or space, there must be an adequate path for air to be returned to the central air handling device. The revised manual provides a wider range of options for contractors to provide return air pathways. Certainly, fully ducted returns offer the most direct path while avoiding potential air quality concerns when using wall or floor cavities. The manual, though, offers more alternatives for central than just the commonly used door undercut technique. Transfer grilles in doors or walls or “jump ducts” between rooms and central hallways have been used successfully throughout the U.S. for two decades. In new construction they can be more cost effective than fully ducted returns and more acceptable from a noise mitigation perspective than large door undercuts. These options can be very useful in existing homes in cases where the effective distribution of supply air is affected by the back pressure in a room with a closed door and an inadequate return pathway. The expanded discussion of duct leakage in the Sixth Edition is also helpful in new and existing projects. There is a note to designers regarding how new or recently installed duct systems in some jurisdictions such as Ontario are required to be sealed to the SMACNA Class 3 level – transverse joints sealed. The manual ascribes a duct leakage range of up to 15 per cent in these systems and suggests designers account for this loss in at least long duct runs. These notes provide a good hint in jurisdictions that don’t require duct sealing or in older homes that duct leakage rates much higher than 15 per cent may be affecting proper distribution of air. Expanded information on duct sealing methods and techniques, including the aerosolized sealant method applied under pressure, is provided. Specifically in new low load homes with lower airflow requirements, the need for precision in distributing those smaller flows implies the need for much better duct sealing. In over 25 U.S. states duct leakage testing down to rates in the three per cent to six per cent range are now a code requirement. The objective of lower duct leakage is also highlighted in an expanded section about the use of flexible ducts. References from the Air Diffusion Council design guide for the effective use of flexible duct have been added to take advantage of the inherent air tightness of these ducts while avoiding the challenge of increased resistance due to improper installation. A much-needed enhancement of effectively conditioning finished or habitable basements is a welcome discussion in the manual. Fortunately, advancing codes and energy programs are addressing the heat loss through basement walls, floor slabs and air infiltration. Thus, HVAC designers and contractors have more options in ensuring warm, dry, healthy lower living areas. In previous editions limited options for dropping supply ducts and return air runs near the floor or adding supplemental heat sources were provided. The supplemental heat option was often problematic because electric heaters, although very cost effective, prompted code requirements for higher insulation levels. The new edition provides a better discussion on the challenges in keeping these spaces warm and offers more specifics on conditioning alternatives. For example, there is recognition that the higher total system static pressures, noted above, provide designers with alternatives. Those include using the higher allowable duct pressures to select diffusers with the specific ability to “throw” air across larger spaces and create supply air distribution patterns that effectively bathe exterior walls and slabs on-ground with proper amounts of warm air.
Rather than opening up walls or ceilings to try and directly connect return ducts, installation of noise attenuated transfer grilles is a very effective option.
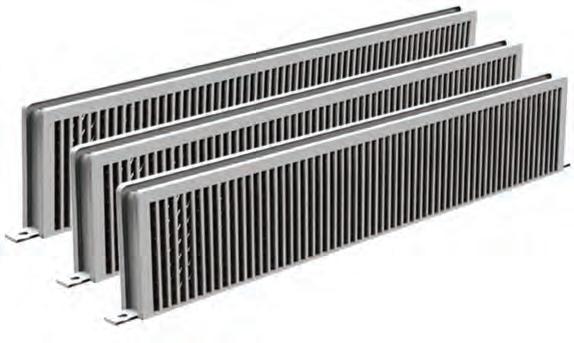
The move towards mass timber buildings − Part II
HVAC and plumbing challenges and the state of mass timber in Canada
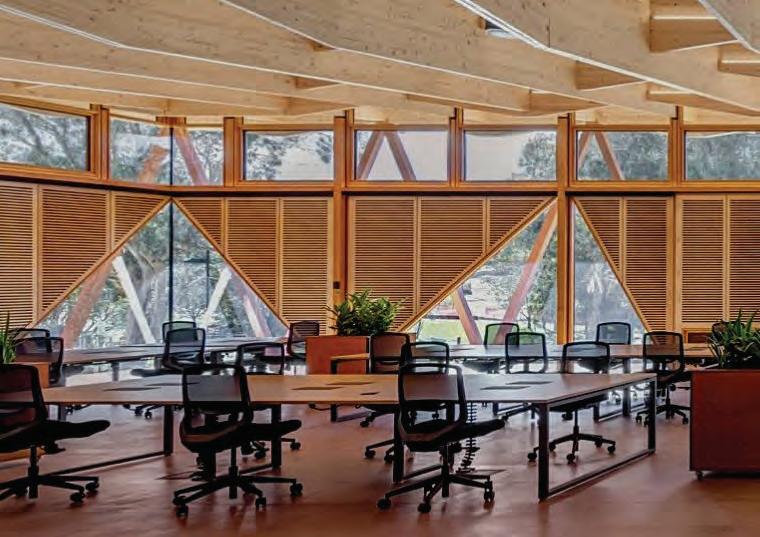
Photos: Cook’s Construction, Rocky View, AB
This is the second in a two-part series about how builders are starting to embrace mass timber construction as a desirable option for residential and commercial buildings. In this second part, we look at the challenges designers and contractors encounter when installing HVAC and plumbing systems in mass timber structures, as well as a review of the state of the mass timber industry in Canada.
The move towards mass timber buildings is underway and gaining momentum each year. Contractors need to stay abreast of this new construction sector and how it will change the way mechanical systems are designed and installed. For more information, go to the International Association for Mass Timber Construction (iamtc.org) and the Mass Timber Institute (academic.daniels. utoronto.ca/masstimberinstitute/).
WHERE TO PUT THE MECHANICAL SYSTEMS?
Experts point to the HVAC and plumbing system design as one of the most important construction processes builders and mechanical trades have to address for mass timber structures. These systems can have a profound effect on the aesthetic appeal of the interior of the structure with its large open spaces, high ceilings and attractive wooden beams. From the outset, the designer has to determine how the installation of these systems will mesh with the architectural look of the interior of the building. These design decisions will have a
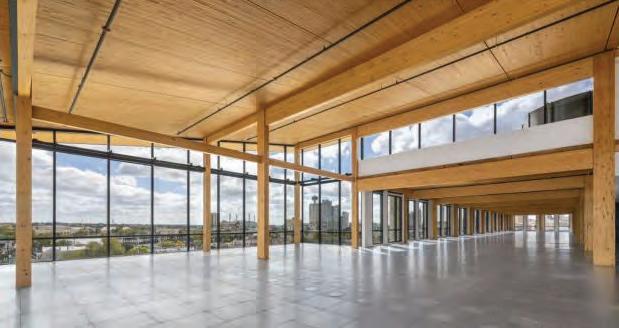
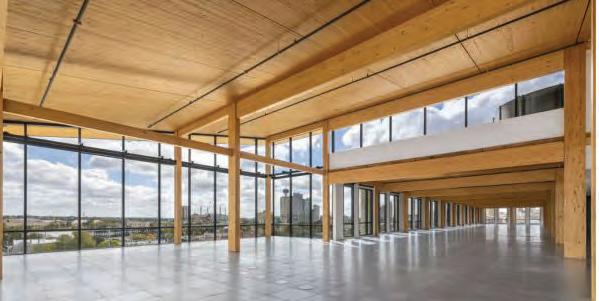
significant effect on the way mechanical systems are installed. In essence, the decisions will determine what components of the systems will be visible versus hidden to create the interior look desired by the architect and builder. If the architectural design for the structure uses the mechanical systems as a part of the interior look, ductwork, piping and other mechanical components can simply be left uncovered and blend into the architecture. If hiding some or all of the system components is determined, a number of options are available to the designer for the trades to use. Two such options are building “light frame walls or soffits” and “furring out” mass timber walls. The light-frame wall option can be located on one or both sides of the mass timber wall panels to house HVAC and plumbing system components. The “furred out” option involves expanding a portion of the lower half of the mass timber wall (similar to wainscoting) to house mechanical system components. Where the design calls for retention of as much of the “wood look” as possible, other solutions need to be used to hide the systems for aesthetics and retain good system performance. One such option used in mass timber buildings is an “underfloor air distribution system” (UFAD). This system manages the balance between efficiency and aesthetics without requiring the extensive ductwork systems used in traditional HVAC systems. The “underfloor” aspect of the system is actually a raised access floor installed above the air distribution system. UFADs can also be used to run piping and other mechanical components. One option used in mass timber Logistically, the raised buildings is an underfloor air access floor is built after the mass timber construction distribution system. is complete and in a configuration that will house the complete HVAC system including ducts and diffusers. The result is a system that is completely hidden and maintains the majority of the building’s aesthetic value. Another benefit of the UFAD system is the mass timber construction process for the building is completed before the mechanical system’s work is started, which makes the whole construction process move quickly and more efficiently. UFAD systems provide a wide range of improved performance aspects compared to traditional systems, including less time for installation, reduced loss of useable space, less energy use through more efficient air circulation and better ventilation. The bottom line is design and installation of HVAC and plumbing systems in mass timber buildings take careful preparation and participation by contractors in the design process to ensure trade concerns are taken into account as the design unfolds. There are many options to meet the design expectations and contractors need to have their say on what is needed to “get the job done properly.” And don’t forget, local energy and building codes need to be reviewed to ensure the options used meet local and provincial requirements.
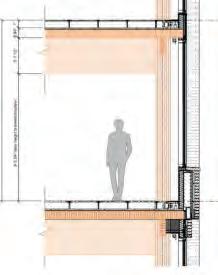
Photo: Cook’s Construction, Rocky View, AB
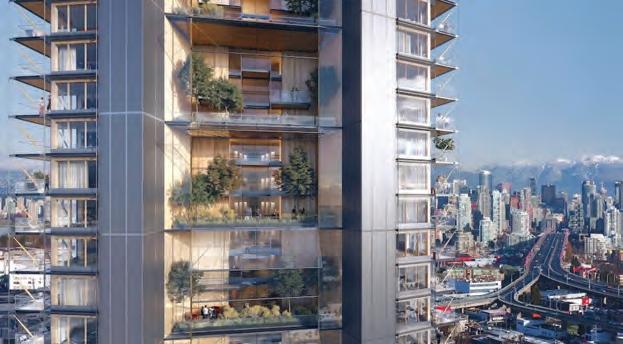
As conceptualized, the Canada Earth Tower in Vancouver will be the world’s tallest hybrid mass timber building.
MASS TIMBER IN CANADA
In 2021, Natural Resources Canada (NRCan) in partnership with the Green Construction through Wood program released The State of Mass Timber in Canada 2021, an inaugural report on mass timber construction. Seamus O’Regan, minister of Natural Resources at the time the report was released, stated “Canada is a world leader in building with wood, and we’re building bigger and taller buildings. Mass timber buildings are highly resistant to earthquakes, offer natural thermal insulation, are inherently fire-resistant, and can be rapidly installed. They’re also a critical nature-based solution to climate change, and an important part of getting to net-zero.” The report covers the progress of manufacturing and building with mass timber. There is an increasing demand in Canada for sustainable building materials and “sophisticated design and production systems.” The report indicates that mass timber will play a key role “in low carbon construction and developing the bio-economy.” Canada has completed or has under construction 702 mass timber projects with institutional (283), commercial (173) and residential (58) being the leading sectors. The report contains background on these projects, which represent more than 1.5 million square metres of gross floor space. There are also 21 mass timber manufacturing facilities across Canada. One of the more prominent Canadian projects is Brock Commons Tallwood House, a student residence at UBC. The Commons is a test project of 18 storeys in height. When it was opened in July 2019, the building was “the tallest mass timber structure in the world” according to Wikipedia. The structure is 53 metres tall with a capacity of 404 students, a floor area of 15,120 square metres and is considered a “hybrid” in that it uses some concrete and steel in the construction. Two other projects of note that are in the works are the Academic Tallwood Tower (ATT) at the University of Toronto and the Earth Tower to be constructed in downtown Vancouver. The ATT will be a 14-storey hybrid made of mass timber and concrete. The Earth Tower will be 37 storeys in height and could be the tallest mass timber structure in the world when completed.
James Hobson:
PUTTING THE COOL IN ENGINEERING
James Hobson, a.k.a. the Hacksmith, created his YouTube channel as a record of his inventions, innovations and gadgets that he has designed. Today it has almost 13 million subscribers. Hobson, who is never short of ideas, just the time to implement them, has taken that built-in customer base and expanded Hacksmith Industries’ ventures to include a retail store where shoppers can purchase miniature versions of his inventions and Hacksmith branded apparel. Hacksmith Industries specializes in taking fictional items from comics, video games and movies and making real working prototypes in order to share them with the world on its YouTube channel. Using this relatable medium, Hobson has taken the boring out of engineering and that gives him incredible satisfaction. “I’d say that’s the biggest benefit of the YouTube channel − basically, inspiring youth around the world to go into science, technology, engineering and maths by showing how cool it is to be an engineer. Kids say they didn’t know that was what engineering could be, thinking it was some boring thing. I feel we’re kind of doing the same thing for today’s generation as MythBusters did for my generation. “I like keeping this idea of an industry that is the cool place to work. A lot of fans say ‘my dream is to work for you’ and that’s really great. I never imagined that when I started.” Hobson has long been fascinated with engineering and as a teenager he knew it was the right career for him. “When I took tech class in high school, I learned that that’s engineering and then it was a pretty easy choice.” Ian Hillier, who would later join him at Hacksmith as co-founder and COO, was also in that tech class. “We went to high school together, college together, and worked on projects. When I started this business, he joined me very quickly after I quit my job,” says Hobson. The engineering bug stuck and Hobson went on to Conestoga College where there were lots of opportunities for hands-on projects. He graduated with a Bachelor of Engineering - Mechanical Systems Engineering. It’s been an adventure ever since.
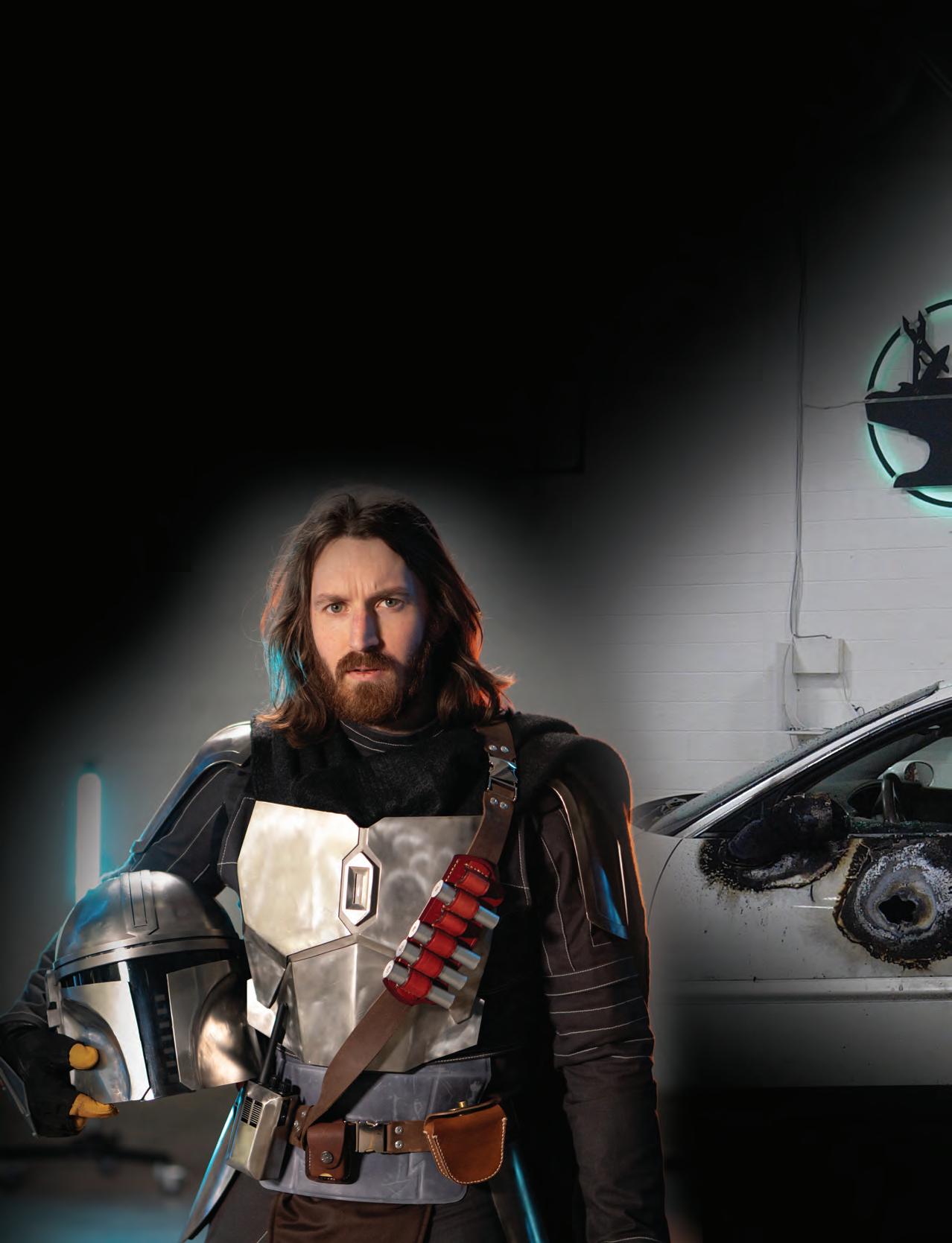
Best-selling butane BBQ starter fashioned after the light saber.
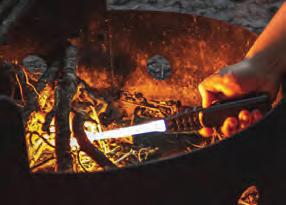
Editor’s note:
MythBusters was a television show in the early 2000s where the hosts used elements of the scientific method to test the validity of rumours, myths, movie scenes, adages, Internet videos, and news stories.
At the end of 2020 Hobson decided to do a full series on making all of the Mandalorian’s (a Star Wars Disney Plus television character) different gadgets and armour. “We did, I think an eight-part video series building all the parts such as the flamethrower, the blaster, the sphere, the armour, the helmet and the jetpack.”
Between operating a successful Etsy account, writing for Hackaday and working full-time in an engineering position, Hobson’s plate was stacked after graduating. The Etsy business selling laser engraved cutting boards was one of the side hustles he continued when he started the YouTube channel.
“It paid the bills while the YouTube channel grew,” recounts Hobson. “That was part of the reason I quit my job, because basically between trying to do YouTube, working full-time as an engineer, doing the laser engraving business on the side and doing the academic writing, I was burning the candle at both ends. I had about six months maybe of savings, so I had six months to make it or to crawl back to an engineering job. Luckily, between Hackaday and the laser engraving business on Etsy, I was able to make enough money to survive.” Hobson attributes some of Hacksmith’s success to his approach to running the channel as a business. “Lots of big YouTubers have lots of followers, but they never really built up a team or reinvested as much back into the channel. And because of the nature of what we do, which is engineering, we built it more like an engineering business. We’ve built up a team and are invested in building up the spec facility and having all the tools and resources. We have basically become a skunk works − being able to make anything under one roof.”
Hacksmith Entertainment is in the process of moving from its current site in Waterloo, ON to a 15,000-sq. ft. site with 18 acres in Cambridge, ON where they plan to grow the business. “The new property has lots of outside outdoor space for projects and whatnot. And we’re planning a 30,000-sq. ft. expansion,” says Hobson. “The acreage will allow for some more MythBusters-level projects. You can go out to the field to test a cannon or something. We can’t do that right now because we’re in the middle of an industrial district. Having that space, I think, is going to be the next paradigm shift for the business, which will be the second big shift because the first shift was moving out of my garage into a real facility 10 times the size. “The property is called HERC and it stands for Hacksmith Engineering Research Campus. The nature of even having an acronym as your business name adds curiosity. When you make it look cool and you have an acronym, people ask: ‘What is that?’” Ideas for the new location include large art installations, creating a collaboration hub, operating summer camps, and building a soundstage, a priority for Hobson. “Once we have that soundstage built, I wouldn’t mind looking into buying a decommissioned fighter jet and modifying it a bit and just parking it on the roof. Because if you park a plane on a roof, suddenly people are asking: ‘What’s that building? Why is there a plane on the roof?’ It is an easy way to make your building cooler than your neighbours’.” At the end of 2020 Hobson decided to do a full series on making all of the Mandalorian’s (a Star Wars Disney Plus television character) different gadgets and armour. “We did, I think, an eight-part video series building all the parts such as the flamethrower, the blaster, the sphere, the armour, the helmet and the jetpack.” Hacksmith followed that up with The Bounty, a 25-minute short film it did in collaboration with a local production company. “The Bounty is pretty cool because to me it feels like almost the same quality as the Disney Plus Series, which obviously has a lot more money and production quality. But it was a fun experiment. It didn’t get that many views on YouTube because it was kind of out of left field for us. People weren’t expecting a short film, but it still has over 1.6 million views, which is good,” says Hobson.
On the Move
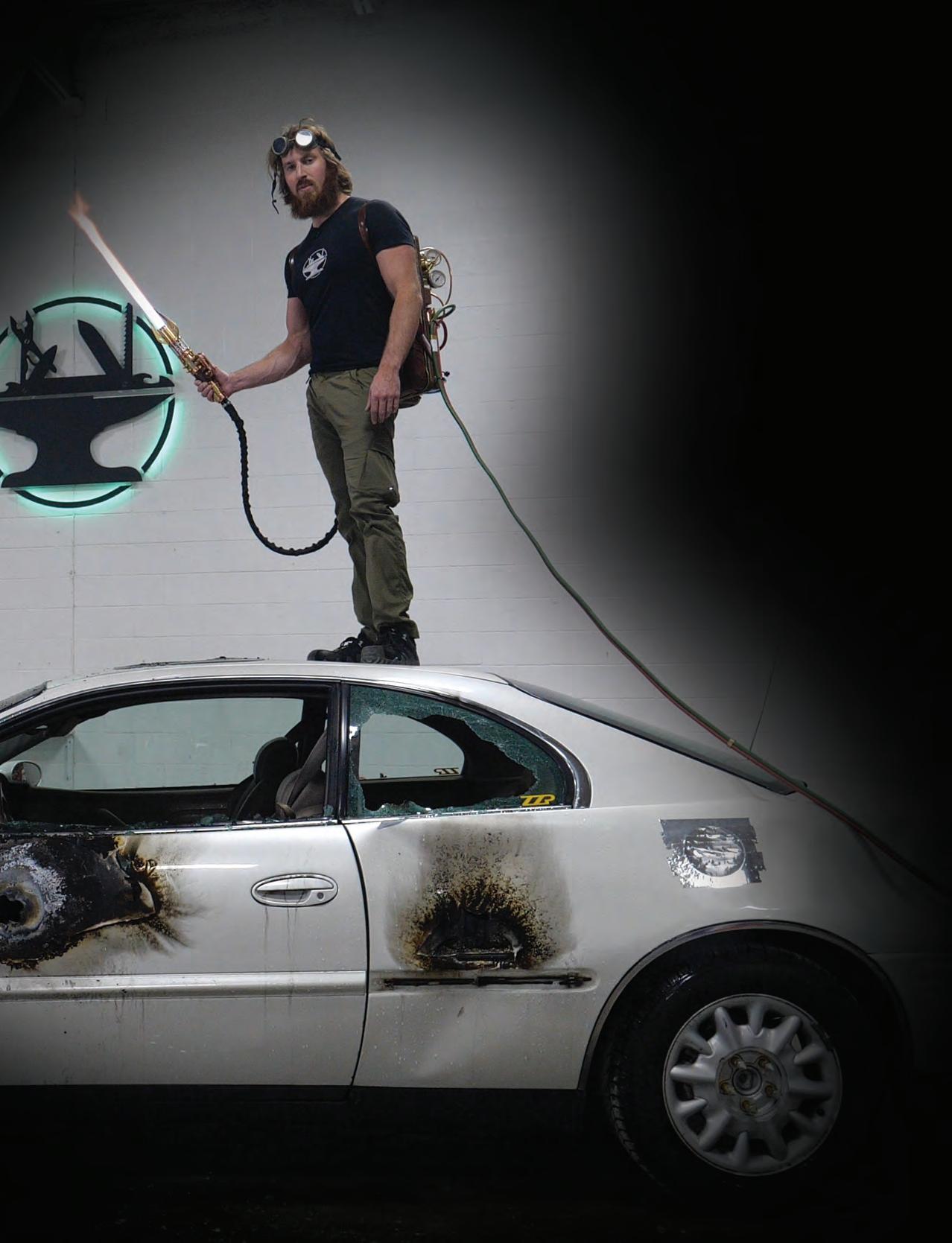
At the end of 2020 Hobson decided to do a full series on making all of the Mandalorian’s (a Star Wars Disney Plus television character) different gadgets and armour. “We did, I think an eight-part video series building all the parts such as the flamethrower, the blaster, the sphere, the armour, the helmet and the jetpack.”