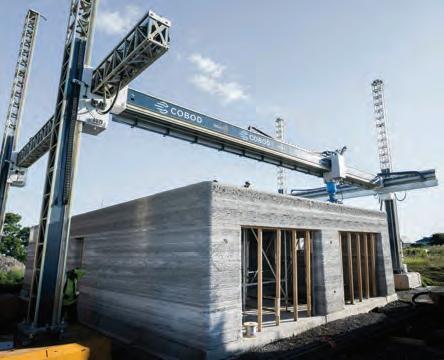
4 minute read
Construction 3D printing building technology – Part I First North American two-storey 3D building fabricated in Kingston
3d
printing is being used to fabricate small- to medium-sized items such as automotive parts, medical body parts and furniture. Did you know 3D printing is also constructing buildings? According to Ian Arthur, co-founder of Nidus3D, a 3D builder in Kingston, ON, “The building industry is ripe for change. Building materials have been the same for a long time and frankly there are too many components and process steps in current construction methods. It’s time for a change and construction 3D printing (C3Dp) is a good alternative.”
The skilled construction worker shortage and increasing demand for housing across the country highlight the need for new building construction methods. C3Dp provides an option for more affordable commercial buildings and housing that can be constructed in a shorter timeframe.
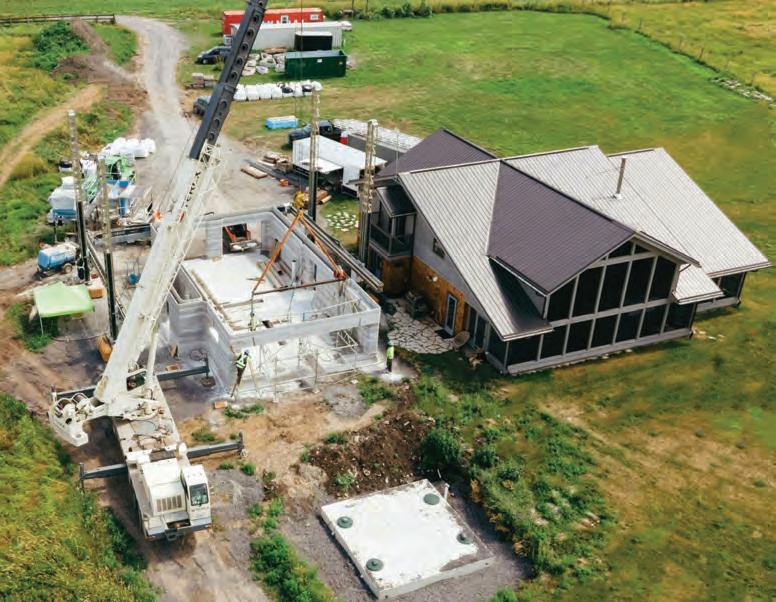
Nidus3D completed North America’s first C3Dp two-storey building near Kingston in September 2022. It has 2,300 sq. ft. with a studio on the main floor and a residence on the second floor. One interesting aspect to the build was the on-site 3D “printing” of a concrete beam.
Nidus3D constructed two two-storey buildings, with the first taking 200 hours to finish, and the second one taking only 80 hours. Future buildings will take even less time to construct according to Arthur. North American C3Dp buildings are typically singlestorey as compared to Europe where they fabricate two- and three-storey buildings. Nidus3D uses a Denmarkbased 3D technology called BOD2 provided by Cobod International.
HOW DOES IT WORK?
The 3D printing technology used to make a small object is the same for a large object. Digital code directs a printer arm as it extrudes a liquid substance such as plastic, metal, or concrete into layers to form the object. Because of this commonality, the same process is used for all sizes of items right up to large structures.
The most interesting use of C3Dp is with concrete. Any concrete structure, including buildings, bridges and parking garages, can be created with C3Dp. Once the digital code is loaded into the printer, quick solidifying liquid concrete is pumped into the moving arm and hardens as it is layered into the desired form.
The maximum concrete stream size at present is 25 mm to allow good flow through the supply system. Rebar cavities are programmed into the design because rebar would interfere with the printing process if it were placed in advance. Rebar is added after the printing phase is completed.
C3Dp applications also provide flexibility compared to other typical wood or concrete construction methods. One example is C3Dp concrete can vary in thickness and spaces can be created for a multitude of uses such as insulation, air ducts, and plumbing and electrical chases. Concern has been expressed about the exterior look of C3Dp concrete. However, experts in the field note that “there are a number of ways to finish the exterior including using the raw concrete look as a novelty in the design or creating a more traditional building look with materials such as cladding.”
Another advantage of C3Dp is the ability to basically program the computer generating the printing “to do what ever you want it to do.” This feature can assist with current building requirements such as energy efficiency and decarbonization. As an example, the programming can reduce heat loss in the wall makeup and use other techniques to move toward the desired environmental goal of net zero emissions.
Progress In Canada
Probably the most compelling aspect to C3Dp buildings is the opportunity to apply this technology to tackle the overwhelming need for homes in Canada at a reasonable cost to the buyer.
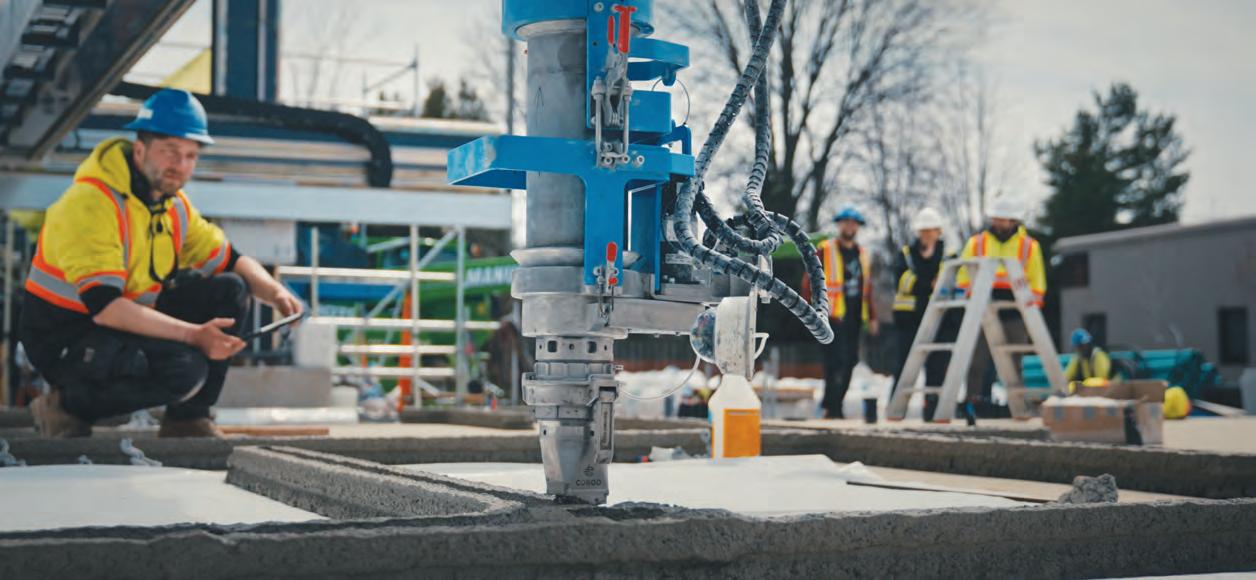
C3Dp has the capability to print whole subdivisions in a very short period at a cost that is more palatable to most Canadians. In addition to Nidus3D, there are other construction companies in Canada looking at C3Dp buildings such as 3D Printed Homes Corporation (3DPHC) in Calgary, AB.
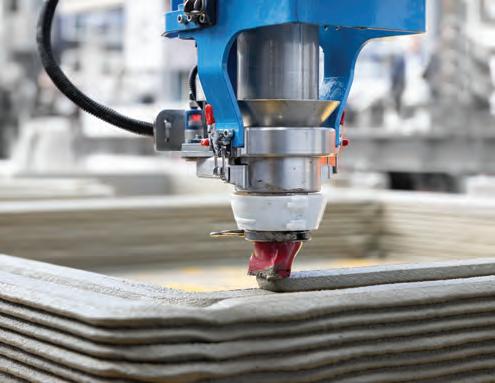
“3DPHC is in the start-up phase,” said Ed Macnab CEO of 3DPHC. “We constructed our first 3D structure at the SMART
Manufacturing Technology Exposition in Red Deer. This display provided people with a firsthand view of how 3D printing is used to fabricate buildings.” He went on to explain that the partners in the company saw a business opportunity with C3Dp, particularly in the housing sector. In his mind, Canada needs more housing across the country that is affordable for new home buyers. The reality is C3Dp is coming along very slowly in Canada as compared to other countries or regions of the world. As an example, Europe, the U.S. and Mexico are further along in adopting C3Dp fabrication and currently have a multitude of buildings in use or in planning including a community of 150 C3Dp homes in the U.S. In Canada, there are currently only four C3Dp buildings that have been fabricated: three in Ontario and one in BC.
Macnab feels one of the hurdles that C3Dp buildings must clear is the provincial and municipal building codes and inspectors who are not familiar with 3D buildings.
“The technology of 3D and the rounded look of some of these structures is not the typical rectangular shape of conventional buildings. Local inspectors have difficulty understanding how these structures should be dealt with under the Code,” says Macnab. “This means C3Dp buildings have to provide technical documentation to show the structure meets the intent of the Code.”
Arthur feels the building codes are not necessarily a problem. However, he agrees time must be spent with local authorities before a C3Dp build commences. “Early discussions with the municipality that focus on the engineering of the 3D building is needed,” says Arthur. “You want to have the municipality well informed about the building before you start the fabrication process.”
C3Dp building technology is now starting to have impact in Canada on engineering and architecture and it can integrate with Building Information Modelling (BIM) software. Some construction companies are using C3Dp to create miniatures of sections or entire buildings as part of their work plans. More and more technical schools in Canada are offering programs in 3D technology and graduates are entering the workforce trained to bring 3D into the mainstream of business.
C3Dp is also expected to result in subtrades that will supply specific parts of buildings including foundations, staircases, retaining walls, and even outdoor furniture. According to some experts, the technology will also be attractive to Indigenous communities, and rural construction where tradespeople are sometimes hard to find. Laneway homes are also seen as a target market for C3Dp houses. One expert noted that “it’s going to revolutionize the building industry.”
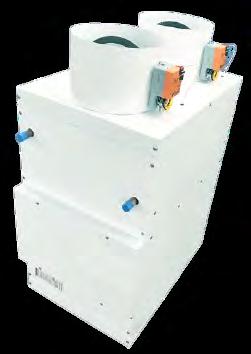
As both Macnab and Arthur point out, Canada has been slow to embrace C3Dp building technology. However, there are signs that this alternative is beginning to take hold in the country. “Europe and the Middle East are leaders in 3D building construction with the United States catching up very quickly,” says Arthur. “Canada has been slow to move on 3D. However, there is increasing pressure to make 3D a viable option for buildings in Canada and when it takes hold, it will expand exponentially.”
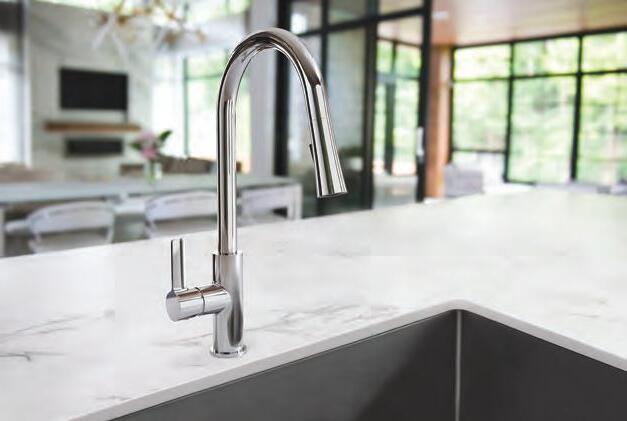
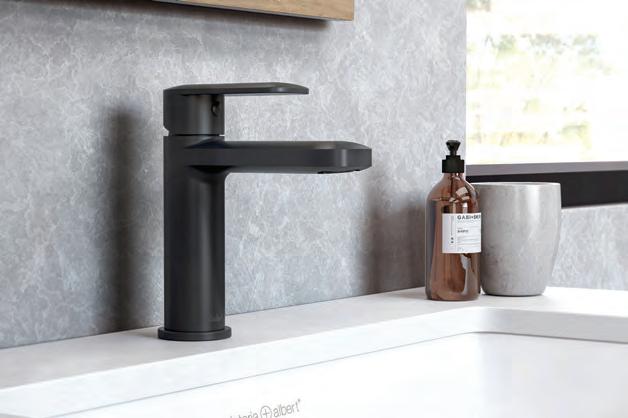
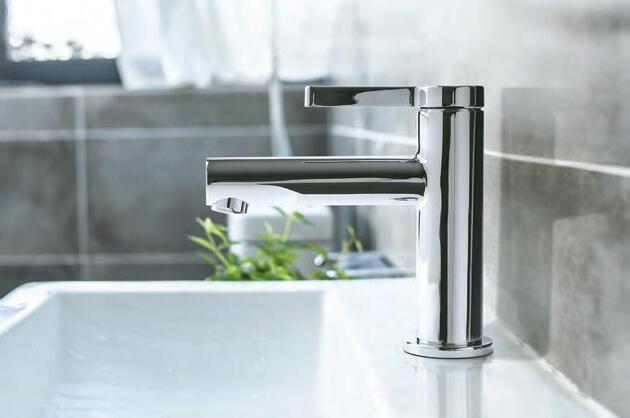
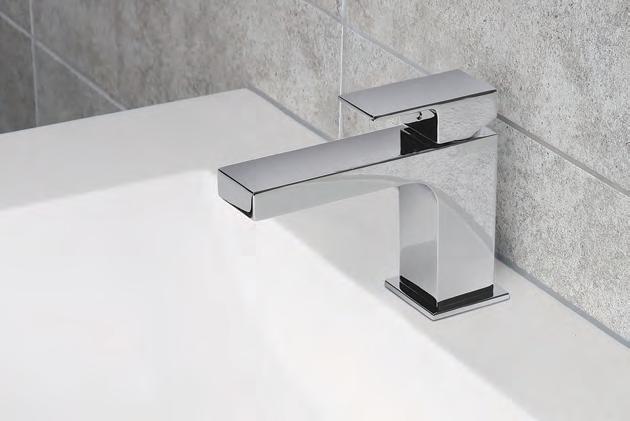
By Kerry Turner