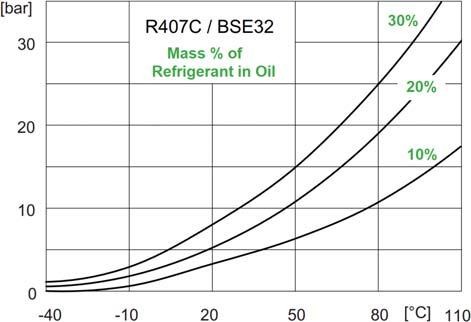
6 minute read
REFRIGERATION Monitoring the lubrication of reciprocating compressors
MONITORING THE LUBRICATION
OF RECIPROCATING COMPRESSORS
Reciprocating compressors utilize moving parts, which need to be protected by a dynamic oil film. Since the oil in the compressor is continuously exposed to refrigerant, it follows that the oil will also contain a certain amount of refrigerant. The amount of refrigerant contained within the oil depends on the type of refrigerant and oil used, the oil temperature and the refrigerant pressure.
The lower the oil temperature and/or the higher the refrigerant pressure, the higher the amount of refrigerant solution in the oil. A Daniel plot is typically used to indicate the percentage of refrigerant in the oil, for a given pressure and temperature.
Oil heaters are recommended for most refrigerating compressors, regardless of whether the compressor is installed in an indoor or outdoor unit. Of course, the viscosity of the oil must be high enough to support long-term, reliable operation. This is true for all modes of operation, including refrigeration and defrost. The only time it is possible to omit a crankcase heater is when the crankcase will not be exposed to temperatures below the minimum as stated in the compressor manufacturer’s operating instructions, and when the refrigerant charge does not exceed 1 1/2 to two times the oil charge. In systems that use a pump-down approach, the oil heater could be omitted if the crankcase temperature can’t drop below 10°C or 50°F. Omitting the crankcase heater is risky and it is good practice to install one in all cases.
As the piston moves towards the valve plate the oil film between the piston and wrist pin, along with the oil film between each crankshaft journal and connecting rod, are exposed to very high forces. It is extremely important this layer of oil is not squeezed out prior to the piston reaching the end of its compression stroke. Refrigerant always reduces the viscosity of oil. The refrigerant type, oil type and refrigerant pressure determine the viscosity of the oil.
For example, in Figure1 we can see BSE32 oil at 50°C (122°F) will contain 30 per cent refrigerant R407C when the pressure of the refrigerant is 15 bar or 218 psia.
The return gas superheat, and ultimately the discharge temperature, have a large influence on the oil viscosity in the crankcase. Therefore, compressor operating instructions include minimum discharge temperatures that must be present during all modes of operation.
There are two main lubrication methods used in reciprocating compressors. These methods are: positivedisplacement (using an oil pump) or dynamic, using a rotating oil disk (centrifugal lubrication). Some smaller
Figure 1 Refrigerant content

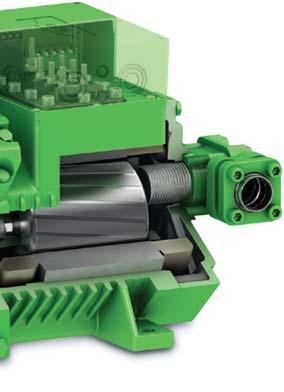

Phil Boudreau Phil is the Ontario sales manager for Bitzer Canada Inc. and provides training and technical support for Bitzer’s clientele. He can be contacted at: pboudreau@bitzer.ca.
compressors on the market utilize another method known as splash lubrication, where the oil is simply thrown around the crankcase to keep moving parts wetted with oil.
Oil pumps are generally required in larger reciprocating compressors since the oil has a longer distance to travel as it makes its way to the various bearing surfaces. For smaller reciprocating compressors, the dynamic disk may be used. In some cases, it is possible to choose the preferred method of lubrication for a given compressor size.

There is also the possibility of adding an oil level regulator to the compressor. This is a requirement for compressors that will be installed on a common refrigerant circuit with a single oil management system. Note that these oil level regulators actively feed oil to the crankcase whenever needed. Modern oil level regulators also provide monitoring functions and can indicate changes, including oil fill cycle timing, low oil level and dirty oil.
Note that the oil level regulator only maintains an oil level in the crankcase. It does not provide as much protection as the optical and differential pressure switches discussed here. Therefore, on parallel compressor systems it is recommended to use both an oil level monitoring switch at the oil cup or pressure switch, in addition to the crankcase oil level regulator in parallel compressor applications.
POSITIVE-DISPLACEMENT LUBRICATION
When an oil pump is used, a differential oil pressure monitoring switch is used. This differential oil pressure is referred to as the net oil pressure and represents the pump’s discharge pressure minus the crankcase pressure. Net oil pressure is typically 40 to 50 psid or so. The purpose of the control is to ensure the oil pump maintains a pressure difference that is high enough to support thorough lubrication of the compressor. During start-up, the oil pressure can be quite low. This can be due to low oil temperature and/or higher refrigerant content in the
Imagine a Refrigeration System that…
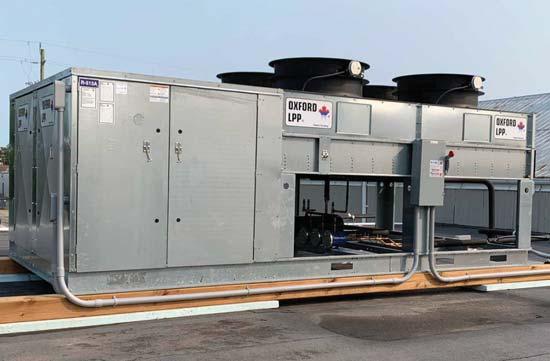
• uses 100% “plug & play” controls over secure connection • uses less than half the refrigerant charge of conventional platforms • incorporates Vapour Drive™ … oil free, magnetic drive, 0-100% modulation, semi hermetic scroll compressors
•
No need to imagine. Meet the Oxford LPP.
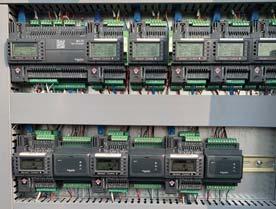

519-532-6373 • oxfordenergy.ca
oil. For this reason, the oil failure switch has a built-in time delay. Note that this time delay tends to vary by compressor manufacturer. For a 90-second delay, the compressor will be permitted to operate for a 90-second period as it builds oil pressure. If the minimum oil pressure is not established within this time delay period, the control must take the compressor offline to protect it. In this situation, the oil pressure differential switch contacts are wired in series with the compressor safety circuit (low-pressure, high-pressure, protection module, and so on). Note that this oil monitoring control will not reset. This is important because we do not want a situation where the compressor is able to continue to cycle with a low oil pressure condition present.
While the compressor is off, there is no need for the oil pressure differential switch to monitor the pressure. In this case, a run signal is removed from one of the control’s inputs. When the compressor starts up, the run signal is provided to the control to indicate that it is time to start checking the oil pressure.
Reciprocating compressors that use a rotating disk for lubrication have an optical oil level switch. This oil switch is installed into an oil collection pocket at the end of the crankshaft, on the crankcaseend. Like the oil pressure differential monitoring control, the optical oil level control has a built-in time delay. When the compressor starts, the optical oil level control receives a run signal and the timing delay is initiated. The control will take the compressor offline if the oil level in the pocket does not reach the minimum allowable level within the time delay period. Again, this will require the control circuit to be manually reset.
Oil pump model with differential pressure switch on the left and crankcase oil level regulator.
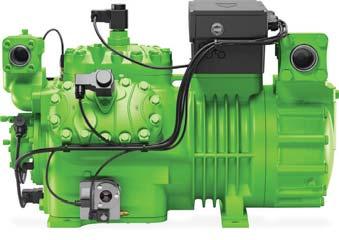
R-22 is best for R-22 equipment. If you need to change,
Arkema has your R-22 Retrofit Solution
DYNAMIC LUBRICATION
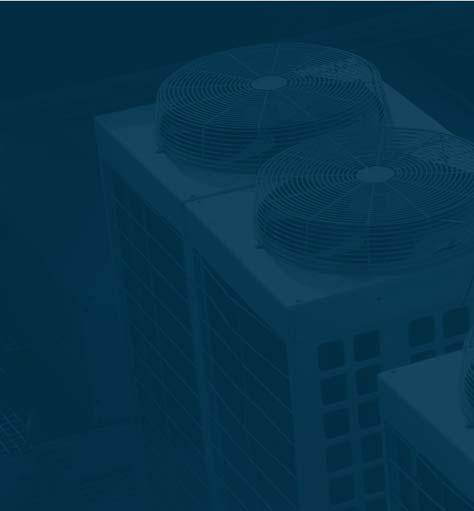
407C
427A
R-407C Air Conditioning R-427A All around solution for both A/C and refrigeration R-407A Refrigeration
Dynamic disk lubricated compressor with optical oil level monitoring switch.
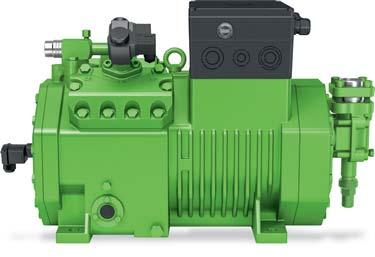

407A
For more information call 416-614-3610 or 1-800-567-5726 x 230 or visit us on the web at www.R22retrofits.com
