
19 minute read
Brett O’Riley
3D printing and titanium — a life-changing combination
~ Additive manufacturing and titanium powder will disrupt medical implant production ~
Advertisement
3D printing is delivering customisation options that make it possible to create almost any shape using additive manufacturing (AM) technology. In fact, the possibilities of 3D printing are so game-changing, it is even possible to create carbon copies of our own skulls.
Sandvik’s additive manufacturing and metal powder specialists are exploring the potential of AM in the medical field, and are preparing for the future of medical implants.
Life-threatening accidents, vertebral damage, chronic osteopathic conditions and side-effects from medical treatment can all cause irreparable damage to patients. The consequences can be painful, debilitating and even fatal, so we must develop solutions to help the human body overcome challenges, enhance the healing process and improve patient prognosis. Medical implant technology has developed vastly over the years, and one of manufacturing’s most disruptive technologies is set to transform the way we treat patients. Medical implant developers require a manufacturing technology that delivers speed, individualisation and the ability to produce complex designs. 3D printing, paired with bio-compatible materials like titanium, is demonstrating its evident potential as the medical industry’s manufacturing technology of choice for life-changing solutions. In the past, surgeons used metal mesh to replace areas of the body such as skull bones, which tended to be weak and lacked precision. 3D printing eliminates these flaws because it uses medical imaging to create a customised implant, shaped exactly according to the individual’s anatomical data. This means that the patient can be fitted with an exact match to replace the lost or damaged area of the skull. In Sandviken, Sweden, lies one of the world’s most cutting-edge titanium powder plants. At the plant, Sandvik’s experts are unlocking the potential of 3D printed titanium devices for the medical industry. Titanium, 3D printing and the medical sector are the perfect match. Titanium has excellent properties and is one of few metals accepted by the human body, while 3D printing can rapidly deliver bespoke results for an industry where acting quickly could be the
Harald Kissel, one of Sandvik Additive’s R&D managers. difference between life and death. In addition to titanium’s material benefits, AM can help overcome some of the challenges when producing medical implants and prosthetics. Typically, the process of being fit for a prosthesis involves several visits to create a device that fits a patient and their needs. As a result, the time between a patient’s life-changing surgery and them receiving their device can be painstakingly slow. If a patient undergoes a serious accident, one that destroys areas such as the skull or spine beyond repair, they simply do not have time to spare to ensure their reconstructive devices fit correctly. Instead, they’re given solutions that work, but aren’t tailored to their bodies. Long waiting times and a lack of customisation can really impact how a patient feels after they’ve undergone a life-changing event or procedure. Even in 2020, there are still prosthetic patients using devices that do not move, or are simply just hooks. Using computer tomography, it is now possible to optimise designs that simply cannot be produced using other manufacturing methods. What’s more, we can make our designs lighter, with less material waste and in shorter lead times. Patients could receive a perfectly matching device, in less time and using a high-performing, lightweight material. In summer 2020, Sandvik’s specialist powder plant was awarded the ISO 13485:2016 medical certification for its Osprey titanium powders, positioning its highly automated production process at the forefront of medical device development. As AM disrupts many areas of manufacturing, it’s clear that its potential in the medical sector will be life changing. Sandvik is also part of one of the most ground-breaking research projects within the medical segment to date, contributing with its extensive material expertise. The Swiss M4M Center in Switzerland is a public-private partnership initiated by the Swiss government, aiming to evolve medical 3D printing to a level where patient-specific, innovative implants can be developed and manufactured quickly and cost-effectively. The Swiss M4M Center is intended to build up and certify a complete end-to-end production line for medical applications, like implants. Being able to facilitate this initiative through the unique material knowledge that is found within Sandvik is an empowering experience. Joining forces with an array of experts to reinvent the future of medical devices as well as the lives of thousands of people — is an experience out of the ordinary. Custom cranial implants and bespoke medical prosthesis are not for the distant future — the technology needed to develop and manufacture them already exists.

continued from Page 1 What we said when the PM came to visit
parts for industries such as medical, cinematography, marine and aerospace. Utilising the very latest in CNC, robotic and software technology available. But that investments into machine capacity will come to nought, if we don’t have the highly skilled people to run them. Of the seven qualified CNC machinists we have hired in the past 18 months, six have been from overseas. “Go hard & Go Early” – a motto often used by Prime Minister Jacinda Ardern can be applied here. We really need to look at developing interest in the trade at school. Let’s get kids excited about how stuff gets made. Our apprenticeship and university training simply isn’t fit for purpose for the trade’s careers of the future.
Apprentices lack experience with new technology, and University graduates aren’t designing to optimise for manufacturability – especially for NZ capabilities. As technology becomes more integrated and the ‘digital factory twin’ evolves, workshop roles are becoming a hybrid – with our CNC machinists upskilling to mechatronics, automation design, LEAN management concepts, programming and software for scheduling and production planning. Enough already with the obsession that to have a ‘real career’ you need to go to university. We’ve got guys in their mid to late 20s in management roles earning over $35 an hour….. instead of paying off student loans, they’re buying their first homes already. But building this workforce of the future is going to take at least a decade if we are starting from grass roots at school. And even with this future workforce, relying on labour alone is not going to lift production and improve our global competitiveness. It is critical for businesses like United to invest in automation to lift productivity. Not to replace jobs, but to increase machine utilisation to 24/7 and optimise production from the labour and asset base that we have.
Let the robots do the midnight shift and the low value work that isn’t sufficient in volume or margin to hire for.
This will allow for staff to focus on higher value work like prototyping, R&D and process improvement. Automation for us has never been a move to replace staff but rather to allow staff to flourish to their fullest potential while increasing productivity, team skills and ultimately profits that can be shared through better wages. And if we lift our productivity, then we can absolutely compete internationally. New Zealand is well positioned for niche hi-tech manufacturing on a global scale. With approximately 80% of United’s work destined for export markets, at a unit price ranging from $15k to $1m, we do not need to be high volume to create a high value and extremely productive industry. We simply need to ensure we’re building a supply chain to suit the high mix, low volume, high value precision work that our industry requires. Add to this the opportunity we’re presented with New Zealand’s global reputation post COVID, the “Made in New Zealand” brand value is only going to grow. Take for example in med-tech industry, in the last few months we have secured several new production projects for prosthetics and pathology companies whom are actively on-shoring their production back to New Zealand.
On the flip side we’ve heard that low volume NZ products have very little negotiating power with a global supply chain – they may get a better price, but they’re going to have little wiggle room on batch sizes and lead times. And if something doesn’t go to plan, well that’s often catastrophic. But for NZ to compete on a global scale we need to back up our technical expertise with business savvy to provide a reliable and comprehensive supply chain. We often hear that the difference in offshore manufacturers like China and Malaysia isn’t only in pricing, but also because they simply provide a better all-around consistent service to their clients and customers.
They collaborate with other manufacturers to provide an end-to-end solution. Plus, they’re ISO9001 accredited, provide immediate responsiveness to enquiries, and while it may take longer and have minimum run sizes – they’re pretty good at sticking to a schedule.
Given the fragmented SME nature of our industry, these are often skills and philosophies that aren’t within our companies. At United we’re on this path of continual improvement, putting our capital investment aside, most of the work has actually been behind the scenes on systems, processes and organisational design. It’s been into software that gives us the capability to feed live data to our customers, and team and culture development to systematically remove bottlenecks.
Not to mention a huge amount of time developing SOPs as we move towards ISO9001 compliance. We’re not there yet, but we’re pretty proud of how far we’ve come.

As for what Government can do. There is a step change that needs to take place for our contract manufacturing industry to raise the bar. In the last decade we’ve had significant incentives to invest in R&D through Callaghan Innovation, and to de-risk developing export markets through NZTE and the NZ Export Office. The strategy is to lift productivity (measured by average income per employee) through focusing on the development and export of IP. We believe this could gut the workforce, and whilst you’ll have a few on higher more ‘productive’ salaries, you’re also sacrificing the manufacturing backbone that underpins our communities – especially our regions. Isn’t it time to support the C, CAPABILITY – in the form of Skills and Capital. We need incentives recognise the importance of contract manufacturing in NZ’s hi-tech eco-system. That:
Make it easier to hire apprentices
Provide education and support to manufacturers undergoing digital transformations
Incentivise capital investment into productivity
Incentivise government procurement locally So just a few things, we don’t have the answers. But we did thank Jacinda for helping us buy our new Mazak Integrex through the Provincial Growth Fund Grant.
PGF was a pretty blunt instrument, however it was a step in the right direction for funding growth in the regions. And is it so different to Callaghan providing companies a 40% grant of up to $15m in R&D funding? What does Labours PGF 2.0 look like?

Breaking Barriers
How Boom Supersonic is Using 3D Printing to Challenge What’s Possible in Commercial Flight
Uncertainty is arguably what most business leaders fear most. But when you launch a new company aimed at building the first supersonic passenger jet since the Concorde, you need to embrace it, be agile and think big. That’s the story behind Boom Supersonic, an aerospace company located near Denver. Boom is a growing company with a big idea – to make supersonic air travel mainstream. Earlier attempts at commercial supersonic flight were unable to achieve sustainability, economically or environmentally. Technology advancements and the growing prevalence of global travel create a market opportunity for Overture, the company’s flagship airliner. Overture will be the world’s fastest airliner and will cut long-distance flight time almost in half, making it possible for more people to go more places more often. To bring it to life, Boom has embraced 3D printing in nearly every facet of the aircraft’s development. With 3D printing, we’ve been able to obtain parts very quickly and determine that they’re either going to work or that we need to make changes.” Mike Jagemann Director of XB-1 production, Boom Supersonic What Boom is trying to accomplish isn’t for the faint-hearted. The last time paying passengers flew supersonic it was a government-driven Cold War-era prestige project involving a consortium of large, established aerospace companies joining together and spending more than ten years and an enormous amount of development resources and risk to make it happen. This time around, Boom, as a private company, is working within a business context, in order to ensure that the end product, Overture, can be profitable for its customers
and the company itself. Fortunately, aircraft technology has advanced a lot in 50 years. Today’s aerodynamic design capability, material properties and engine performance have mostly overcome the issues that grounded the last supersonic aircraft. Combined with the manufacturing benefits of 3D printing, Boom is well positioned to meet its goal. Now, the company is ready to take its first major step toward its ultimate goal with the first flight of its one-third scale demonstrator aircraft, the XB-1, next year, following an unveiling event this October. From the start, the Boom team knew 3D printing was going to play a crucial role in the development of XB-1, and ultimately for Overture. Mike Jagemann, Director of XB-1 production, had previous experience with 3D printing and brought in two Stratasys 3D printers – an F370 and Fortus 450mc— right away to help with prototyping. Boom later added a Stratasys F900 3D printer to expand beyond prototyping to include the additive manufacturing of tooling and production parts, and the company has since 3D printed hundreds of parts and prototypes. One of 3D printing’s biggest benefits is time savings, and the company estimates it has saved hundreds of hours thanks to the technology. Boom uses 3D-printed parts to check for proper fit and alignment, saving valuable engineering time. “With 3D printing, we’ve been able to obtain parts very quickly and determine that they’re either going to work or that we need to make changes,” says Jagemann. “Rather than spend eight hours in CAD trying to check space constraints, the engineer can continue working on other things. When the part is printed, they can check the fit.” Manufacturing these parts using traditional methods would be more expensive and too slow. Being able to print parts like hydraulic line clamps that will fly on the XB-1 is another critical time saver. The advantage is the ability to optimize the engineering workflow, leaving these components to the very end of the design process because they can quickly be printed in-house. “That shortens the supply chain on certain components that are a good fit for 3D printing,” adds Jagemann.
Breaking Barriers
The biggest savings so far, both in cost and time, has been the ability to make custom drill blocks to accurately locate the many fastener holes that pepper the XB-1’s airframe. Initially, Boom developed tooling that relies on metrology to position one hole at time.
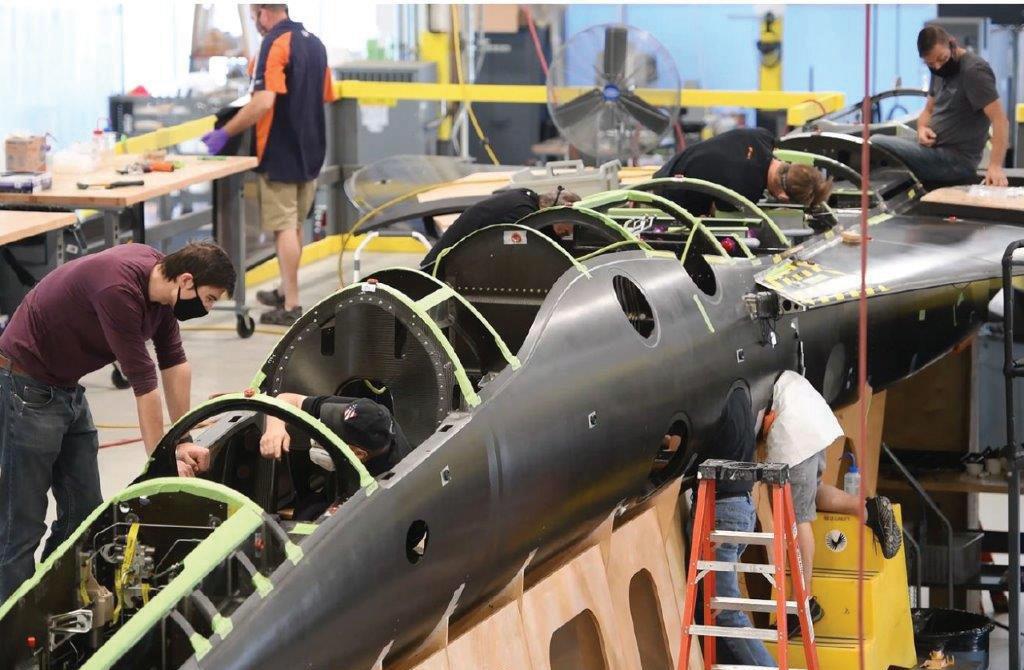
As the assembly progressed, however, it became clear that this approach was taking too much time. Instead, the team pivoted and 3D printed more drill blocks, each incorporating multiple holes. That allowed them to use metrology to accurately position twenty or more holes instead of just one at a time.
“Being able to locate a drill block with a large volume of holes has been a huge manufacturing time saver for us,” says Jagemann. One surprise with 3D printing Jagemann wasn’t expecting involved how it helps make Boom’s engineers more efficient, which in turn helps the team move faster.
“3D printing parts helps make the physical connection between what the engineer sees in CAD and how the part actually turns out,” Jagemann says. “If you don’t have a 3D printer to close that loop, you’ll use machined components instead, and that’s more expensive.”
Breaking the Biggest Barrier
Every business faces uncertainties from competition, economic instability and other factors out of its control. Boom is no different. But Boom concentrates on what it can control, and relies on technology like 3D printing to blunt risk. 3D printing lets Boom break down manufacturing, supply chain and workflow barriers through innovation, cost constraint and speed of execution. And based on the evidence so far, it’s a good bet the technology will continue to play a key role in helping Boom break the sound barrier too.
www.objective3d.com.au www.stratasys.com

title continued from Page 6 Manufacturing forum highlights key issues
Woodliffe points out industry landscapes have Depreciation counterparts who increased the threshold from changed irrevocably and many current policies Finally, a call for our depreciation rules to be $30,000 to $150,000. This will return to $30,000 on and structures have been exposed by Covid-19 reviewed was a constant theme discussed during the 31 December 2020. as outdated and need rethinking to fit the “new forum, according to Helen Down. ‘It would mean that if a manufacturing business normal”. An example being the Employment Relations Act which he says is 20 years old, outdated and not fit for purpose in these changing times. “If we want to stimulate private investment alongside Government investment, and take advantage of our virtually Covid-free status this is one simple thing Government could consider immediately,” bought a $100,000 piece of equipment, they would be able to expense that for tax purposes in the year that they buy it. Obviously that gives them a real incentive to do it – whereas at the moment they have to capitalise it and muck around with depreciation “The fallout from having to work with an Act that is she said. over a number of years. now seriously outmoded, is that it cripples everyone. Michael Markham, Director of Kendons Chartered “There is a massive compliance cost to capitalising Anecdotally we are aware that the Employment Accountants Ltd said the instant asset write-off assets, so an increased threshold would also be Relations Authority has a resultant backlog of at least threshold increased from $500 - $5,000 (on 17 March advantageous to businesses in terms of administration 12-18 months of cases that need to be considered as 2020 as a result of covid) in New Zealand for this and the timing of tax payments (getting a quicker a result of actions taken by companies because of year, and will end on 17 March 2021. After 17 March tax deduction),” said Markham. Covid-19. Is that not a clear indicator the Act is not 2021 this will decrease to a new level of $1,000. working?” He said this in comparison to our Australian
continued from Page 18
Industry 4.0 Adaption to NZ Industry
Lesser scale, thou not necessarily simpler projects, can often be handled by smaller integrators providing much better value and more hands-on support. Edge Robotics and Automation is also happy to help those undertaking projects predominately inhouse providing opportunities for significant cost reduction.
Machine Learning
Machine learning is one technology that often goes hand in hand with this wider discussion of Industry 4.0. Many “in-production” machine learning applications are more around the financial and operational space of companies such as production modelling and preventative maintenance. This pattern will increase into the future, but realistically, still quite a few steps away from transformational changes to a big portion of our industry. NZ and Australia have another opportunity since our industries are heavily towards the primary and secondary industries, and often even our later manufacturing has natural components. Key to applying automation in these industries is the capability of systems to move away from fixed numerical decision-making, and towards those that work with subjective or chaotic environments. In essence, the automation system needs a “feel” of a process or to reason as per an operator; and this is what machine learning can offer. Despite the recent hype, machine learning has been lurking in these industries for over a decade, it just has not been publicised and players have kept it under wraps for competitive reasons. Media often builds up the picture of some magical invention with Will Smith fighting a glowing white ball. In reality, machine-learning is “just” a field of mathematics based around the self-tuning of equations. Each application is typically a customised pattern with different base equations and tuning methods. The pattern technically referred to as a model, will be based around KPIs such as accuracy, stability, disturbance rejection, plus the practicalities on the amount of data collection and tuning (cka training) time. Various means of producing machine learning models exist from simple software wizards to full expert level development. Most in-production industrial machine learning systems work on cloud or server setups, however, recent products like new TwinCat features from Beckhoff allow expert level models to operate on standard automation controllers. As a nation we have the technical capability to gradually roll out the advantages, ideally from lowest hanging fruit and up. The difficulty is connecting the computer science trade with the wider range of industry groups and there are simply not many people who can cross that boundary.

Vision systems
Automation companies should these days have minimal trouble doing a basic integration of smart cameras and this works great in a carefully controlled manufacturing environment. Get closure to natural products and the mass market vision systems fall over. Machine learning has been a great aid to vision systems by allowing more subjective measurements. 3D systems are another vast range of technologies that get attention, and if you know the tricks, these can also simplify and reduce the overall cost of more conventional problems. As with many leading technologies it is important to looking beyond the marketing and get a better understanding of the limitations and challenges that are not immediately obvious. Beyond this we barely scratch the surface of what is possible with machine vision due to our own limited perception of the world. The road to truly mastering vision applications occurs once you go beyond the notion of human sight. In many cases difficult problems, or those that we think are random, become clear when we know where and how to look. Non-Visible UV or Infra-Red is not just one grey type but has variations like colour and this has many uses with sorting and quality control in natural products. Using UV light for example can lead to fluorescence of contaminants and bacteria, all normally invisible to our eyes and colour cameras. Using polarisation properties like your sunglasses, provides the chance to look at internal structural defects in transparent materials, packaging seal quality or microscopic surface details. Measuring these principles are no longer the domain of solely scientific equipment but available in off the shelf industrial components at reasonable prices.