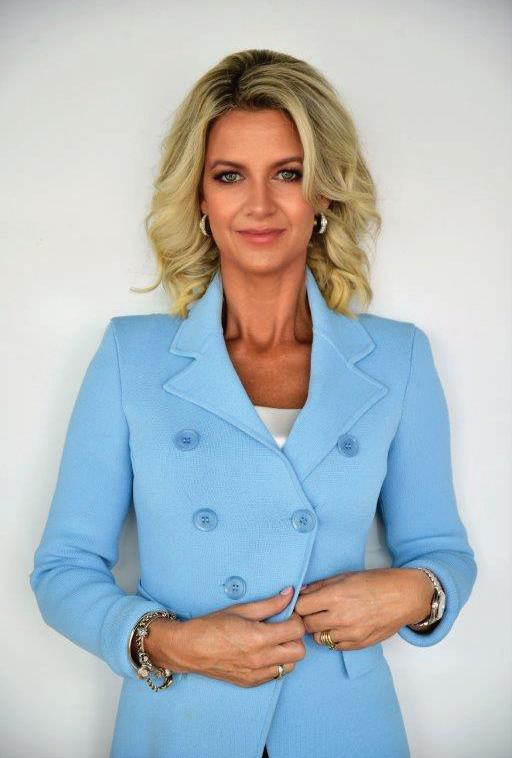
1 minute read
Developments Preventing a workplace safety crisis in New Zealand
Workplace incidents across New Zealand are all too common, with over 194,000 workplace injury claims lodged last year with ACC. A recent incident with the Alto Packaging breach in Wellington highlights how Kiwi businesses are at risk of complacency, opening themselves to reputational and financial damage by neglecting safety processes.
To prevent a workplace safety crisis in New Zealand, Kiwi businesses need to make workplace safety a priority - not a ‘ticking the box’ exercise. As a Kiwi-grown business specialising in personal protective equipment (PPE), safety is at the heart of what Eagle Protect do. They supply a range of industries across manufacturing, agricultural and construction sectors with disposable gloves and other PPE to prevent workplace incidents and reduce exposure to hazardous materials, cross-contamination and the spread of disease or illness.
Advertisement
From their experience (and from working with customers), here are three areas where Kiwi businesses should invest time and energy, to create a safer working environment for their staff and minimise risks in the workplace.
1. Using high-quality PPE
Companies looking to build a low-risk workplace should put high-quality PPE at the top of their shopping list.
Occupational skin disease (OSD) and injuries to the hand and upper limb (musculoskeletal disorders
- MSDS) are hazards for any worker. However, high-quality PPE, especially disposable gloves can reduce the impacts of these ailments. Quality PPE should protect employees from skin irritations, musculoskeletal injuries, and chemical hazards found at work sites.
Eagle Protect created the ‘Eagle Standard’ which goes a step further, ensuring durable PPE items are sourced from responsible, ethical, and traceable supply chains. Employees who know they are using quality PPE which is also socially responsible, tend to work more efficiently as they can trust they are safe, leaving more time to focus on work outputs.
2. Ongoing training and education
Training and education on the importance of safety should be an ongoing process, integrated with workplace culture. If you’re a workplace manager, you may be asking how you would do this effectively. Typically, this involves completing regular risk assessments; educating teams on how to spot wear and tear on PPE; and ensuring processes are clearly communicated and implemented to fix or avoid hazards in the workplace.
While these are the basic steps needed to ensure safety, every industry has different needs. It’s important to note a one size fits all approach will not suffice when it comes to protecting workers.
Eagle Protect, offer personalised, on-site audits of