
3 minute read
Increasing interest in ZLD driven by costs and environment
By Matt Hale, International Sales & Marketing Director, HRS Heat Exchangers
In 2021 the global market for zero liquid discharge (ZLD) technology was estimated at US$1 billion and is forecast to grow at almost 12% over the next ten years1. The rise is being driven in particular by an increase in adoption of the technology by the food and drink and textile industries as a growing world population puts greater pressure on fresh water supplies.
Advertisement
What is ZLD?
Zero liquid discharge (ZLD) is a liquid waste stream treatment which involves transforming liquid waste streams into clean water (which can be reused) and a minimum volume of solid residues.
One of the advantages of ZLD over other treatment techniques is its theoretical ability to separate unwanted materials from water, whether they are benign, hazardous or toxic. The resulting solid residue is often more stable, making it suitable for recycling or landfill.
However, poor management or handling of the remaining residue can result in unintended environmental consequences. For example, storage ponds may leak or affect local wildlife while there is the potential for toxic chemicals to leach into groundwater from landfill.
It is therefore important that when implementing a ZLD system, full consideration is given to the entire process, including the ultimate fate of liquid and (semi-)solid waste streams. A well-designed ZLD system should minimise or even eliminate liquid waste streams, resulting in clean water for reuse or environmentally-friendly discharge, and a solid residue suitable for further processing (often to recover valuable components for use elsewhere) or for safe disposal.
The factors driving ZLD uptake up its waste processing systems. ZLD methods are already widely used in industrial wastewater treatment to recover useable and profitable minerals and by-products from waste streams, and the success of such systems is encouraging their take up by other businesses. In 2015 the Indian government issued a draft policy requiring all textile plants generating more than 25 cu. m. of wastewater effluent a day to install ZLD facilities2.
According to Transparency Market Research1, ZLD is being implemented across a wide range of industries, including chemical and petrochemical production, food and drink production, textiles, energy and power, and pharmaceutical manufacturing.
These industries are being driven to adopt the technology due to growing environmental awareness of the hazards of toxic wastewater and increasing environmental regulation. In turn this has increased the costs of handling and disposing of such waste streams, and in some cases has made such disposal impossible. As a result, companies are looking for more sustainable alternatives, and ZLD is one of the leading technologies in this area.
ZLD technology has been utilised in various markets around the world, including Europe, Australia, Canada, the Middle East and Mexico, but the biggest markets, and the biggest potential for expansion, can be found in the United States, China and India2.
The benefits and challenges of ZLD
In general terms, the use of ZLD reduces water pollution and augments water supply, but this is sometimes offset by high costs and energy consumption and in the past these factors have limited the uptake of the technology.
Wastewater reuse minimises the volume and environmental risk of discharged wastewater, but also alleviates the pressures associated with the abstraction of freshwater, but these benefits have to be balanced against the economic and energy costs of implementing ZLD systems.
As water scarcity and environmental pollution around the world intensifies, ZLD becomes more feasible and widespread, and the relative costs of ZLD technology versus the alternatives (assuming alternatives even exist) are lowered.
Increasing the efficiency of ZLD
Diary
Profiles www.nzmanufacturer.co.nz
The specific factors driving uptake are different for each industry. For example, in the energy and power sector (historically the largest user of ZLD technologies), access to clean water suppliers is an increasing concern.
Pollution control is also a major driver, and the US EPA considers zero discharge as the preferred treatment option for fly ash and bottom ash transport water, and wastewater from flue gas mercury control systems2.
Elsewhere, growing awareness of the toxic effects of petrochemicals and petrochemical waste products is driving efforts by the industry to clean
Separating all of the water out of the product requires large amounts of energy. It takes roughly 6 times more energy to evaporate water (latent heat) at its boiling point then the energy needed to actually bring it to that boiling point (sensible heat).
continued on Page 29
In nursing, in dispensing machines, in the field or in factories, collaborative lightweight robots can help automate monotonous tasks. To enable interactive service robotics concepts to be implemented quickly and inexpensively, igus has developed the new generation of the ReBeL. The lightweight plastic robot has a fully integrated tribo strain wave gear with motor, encoder, force control and controller. Electronic components in the fully integrated strain wave gear allow human-robot collaboration to be possible (HRC). This is because the encoder technology enables forces and torque to be determined and limited via the motor current in combination with the angle measurement. For this, igus relies on a double encoder, in which a measurement is carried out in front of and behind the joint. This detects forces and torque levels and responds accordingly.
Plastics is a game changer in automation
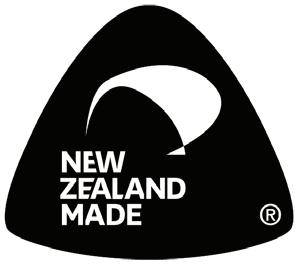
The use of plastic in the ReBeL results in an extremely compact, lightweight design. With a net weight of