W rkplace Safet
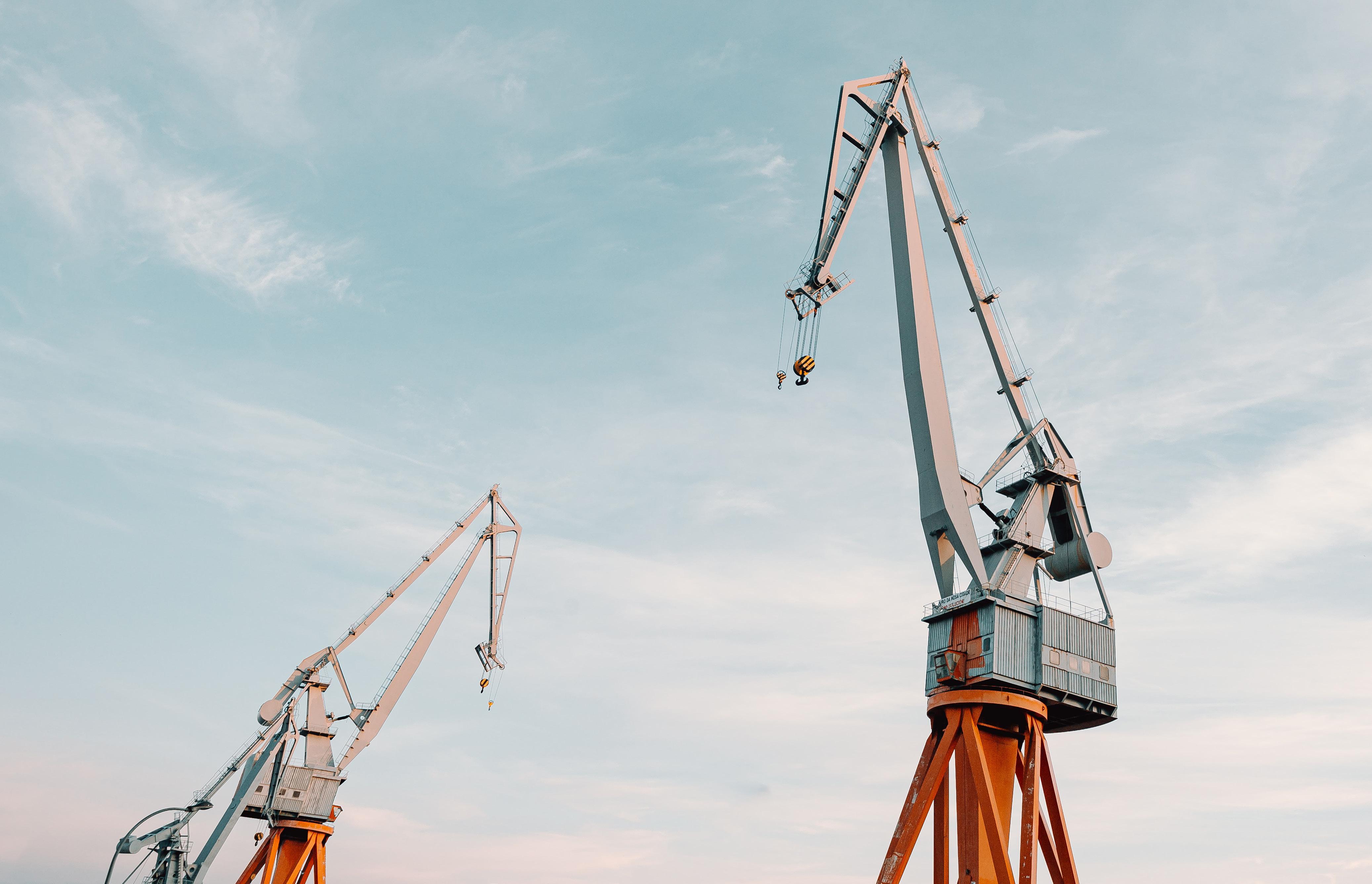
Q&A with the Inspirational Curtis Weber, Workplace Safety Advocate and Consultant
Can you tell us about your story?
I had just graduated from high school and took a summer job building steel grain bins, buying time, and anxiously waiting to begin playing Junior hockey in Western Canada. But, instead, on the third day of my first real job, my life as I knew it would change forever.
After a long, frustrating morning that saw our small construction team setting up a large steel structure, only to tear it down as the wrong material was delivered to the site, our day changed.
Employers have the opportunity to create work environments where people like me and my crew would've felt okay taking more time to discuss the best options for that move, no matter how bad our day was going. That opportunity lies within a system which puts culture ahead of anything else — even safety.
cycle of 14.4 kV passed through me, the energy ejected into another part of the steel structure. My co-workers immediately turned into first responders. They tried to revive me on site until the paramedics arrived.
Following the incident, my family was informed that I wouldn't survive, that my kidneys had failed, and the burns were just too significant to make a recovery. I spent six weeks in a coma with third/fourth-degree burns covering 65 percent of my body.
Without a proper discussion about the risk, we attempted to move a steel structure under an overhead powerline with our picker truck. Fifteen minutes before the move, we had a brief chat about the hazard but didn't spend any time on how to control it. Like so many times, we thought it would be fine for all of us. Instead, I became the ground point as three separate cycles of 14,400 volts passed through my body in a split second. I was surrounded by steel, and as each

TI spent over six months in the hospital and with over 30 surgeries, including amputating my arm and left leg. After those six months where they saved my life, I would spend the next six years travelling for 15 reconstructive and plastic surgeries, with recovery times lasting months before returning to physio to prepare for the following procedure.
What's the most important takeaway from your story that workers and employers should take with them?
I've always said that no matter
how good or bad your safety program or organizational culture is, there's always one constant in how we as workers can prevent going through what my family, friends, and co-workers have endured. That one constant is your voice. So speak up, speak out, and speak loud — voice those questions and those concerns.
Employers have the opportunity to create work environments where people like me and my crew would've felt okay taking more time to discuss the best options for that move, no matter how bad our day was going. Unfortunately, that opportunity lies within a system which puts culture ahead of anything else — even safety. We can have the best safety program in the world and spend a million dollars on it. But, still, if it's not communicated correctly, implemented properly, and we have a culture where people are afraid to follow it, then, unfortunately, it's money not well spent.
Instead, create a culture, don't implement one. The best organizational cultures that have created successful safety programs are by the craft, the crews, and the people on the front lines doing the work, while management and leadership play a supporting role, investing time and resources in the ideas brought to them.
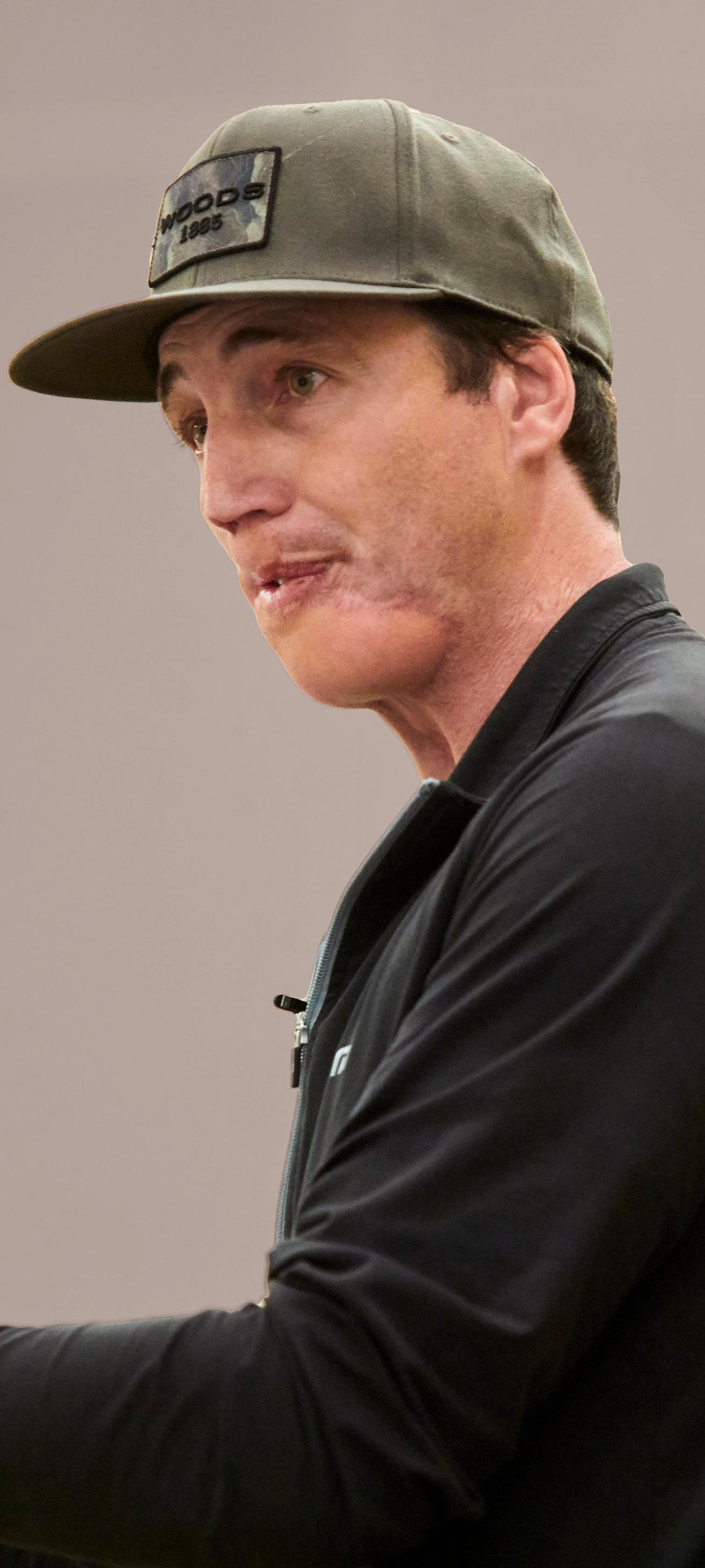
Keeping Temp Workers Safe on the Job
emporary employment takes a wide variety of forms: term, contract, seasonal, casual, and placement through a staffing company. It is common in construction, resource industries such as fishing and agriculture, public administration, personal services and community services. Canadians of all ages and all walks of life take temporary jobs — some by preference, and others because they cannot find permanent positions.
Tips for employers By law, Canadian employers must ensure that their workplaces are safe, train employees regarding any potential hazards, supply the necessary personal protective equipment and make sure workers know how to use them. These responsibilities apply to all workers, whether permanent or temporary.
Regardless of a worker’s qualifications, employers must never leave a new temp to work unsupervised before ensuring he or she can safely perform the required tasks. Job orientation and safety training are extremely important
Temps tend to suffer more injuries than permanent employees, and those injuries tend to be more serious. According to a study conducted by the Workplace Safety and Insurance Board, temporary workers are up to two times more likely to suffer an on-the-job injury relative to their full-time counterparts. Both the employer and the employee need to be on their guard for safety in temporary work situations.
for temporary workers, yet temporary workers commonly report that these important considerations were never provided. While injury claims for temporary workers will often see the costs ascribed to the worker’s temp agency, be sure you are aware of your province’s legislation. In the event of serious injury or fatality, you and your workplace may also be held liable.
Tips for temporary employees
As a temporary employee, you have some protections under your province’s Occupational Health and Safety Act. As far as safety is concerned, these rights include but are not limited to the right to safety training, information on personal protective equipment and procedures, and
notice of potential dangers you may encounter on the job.
It's important that any injury be immediately reported to your supervisor and to your provincial workplace compensation board. Your employer may encourage you not to report an injury — if this happens, document the situation as much as you can and contact your local workers’ action centre. In certain industries such as agriculture, logging and forestry, and construction, seasonal workers predominate. The rates of injury in those sectors are relatively high, due in large part to the nature of the work. With inexperienced seasonal workers, the risks increase. Again, both the employer and the worker must be aware of all hazards. Proper training, equipment and other safety measures are essential.
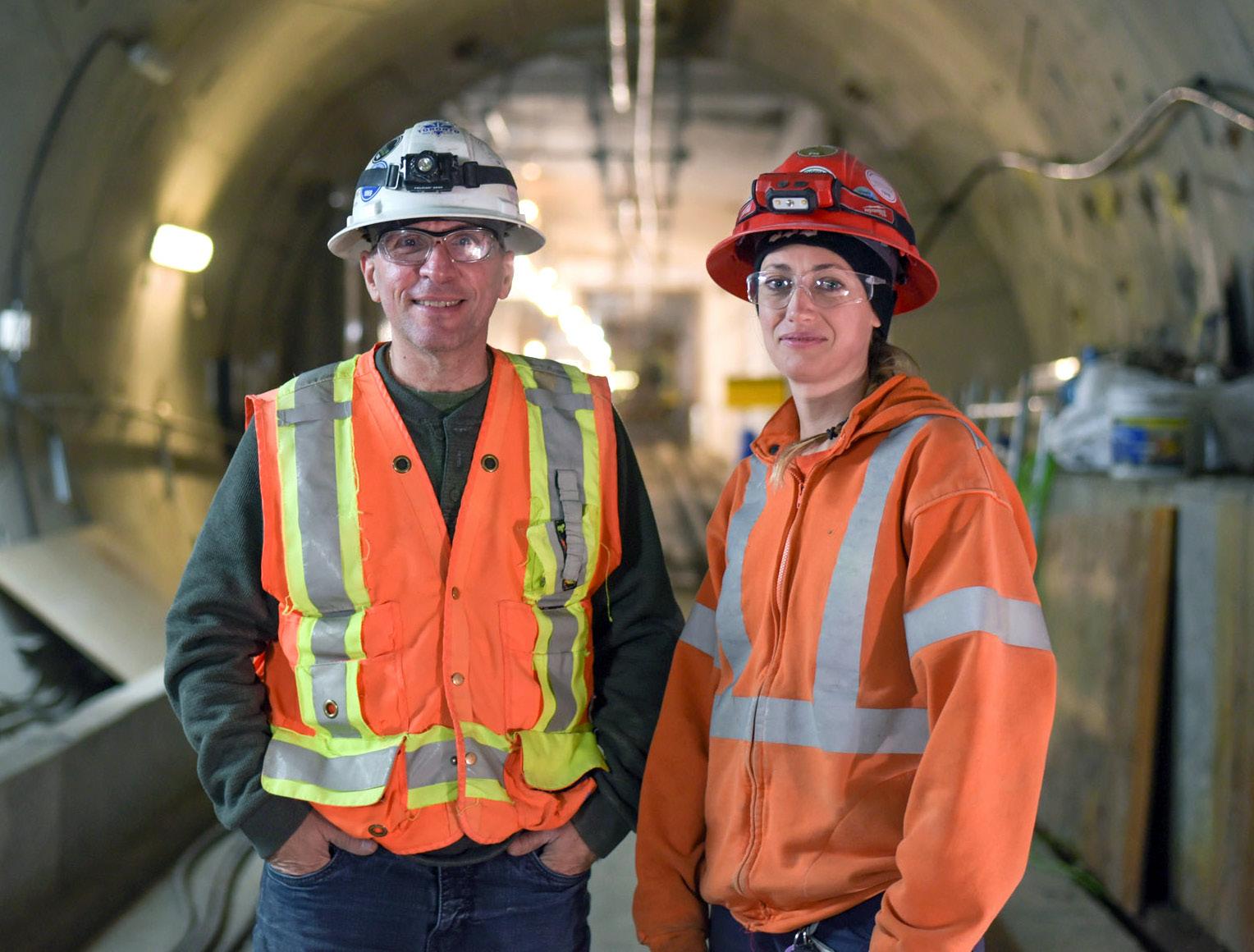
Seeking a Lucrative, Satisfying, and Safe Career? Consider the Skilled Trades
A
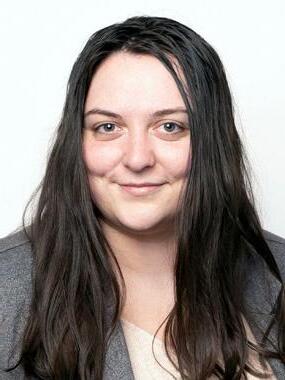
Many Canadians have preconceived ideas about careers in the skilled trades that are frankly out of date. Do you think, for example, that working in the trades is “beneath” white collar work or that pursuing a university education is always preferable to a trade apprenticeship? Or do you imagine that a career in the trades isn’t creative or intellectually stimulating? How about that working with your hands isn’t desirable or that you couldn’t possibly pursue a career in construction while also pursuing your passion?
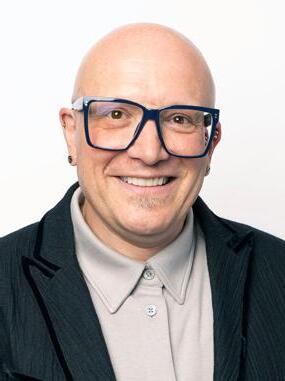
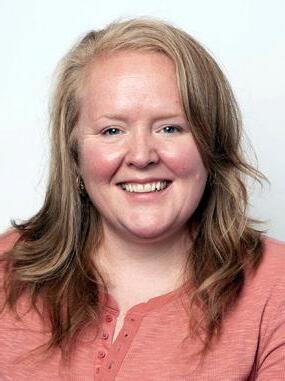
The women pursuing skilled trade careers would beg to differ. And with exceptional compensation, excellent opportunities for advancement, and a workplace culture that’s steadily improving, the trades clearly have a lot to offer.
Understanding the “union effect”
A safe work environment is one of the base requirements for satisfying work, and Ontario’s various building trades unions place a huge amount of emphasis on workers’ safety.
“Evidence shows that the unionized construction sector is safer,” says Carmine Tiano, Director of Occupational Services, Provincial Building and Construction Trades Council of Ontario (PBCTCO), an umbrella organization of 13 affiliated construction craft unions that acts as the collective voice of Ontario construction workers. “The Institute for Work and Health published a study on the effect of unionization on the incidence of workers’ compensation claims and found that union jobs were 23 percent safer when it comes to lost-time claims related to injuries. This is known as the ‘union effect.’”
Thanks to trade unions’ leadership and structured approach to ongoing, job-specific training, tradespeople are assured a safe working environment.
Supporting tradespeople
The PBCTCO is also undertaking various projects and initiatives designed to support its workers, including women in the trades, those struggling with mental health challenges, and anyone dealing with substance use issues.
The Ontario Building and Construction Tradeswomen (OBCT) was established by
Tania Amardeil
the PBCTCO to support, retain, and recruit women into skilled trade apprenticeships and careers. “We’re a committee of over 700 tradeswomen from across the province,” says Kayla Bailey, Program Director, OBCT. “We represent every trade, every sector, and every level of representation.”
The OBCT supports tradeswomen through a one-on-one mentorship program, as well as peer support and education on topics like leadership, mental health, substance use, and opioid poisoning emergency training. “As a tradeswoman, you’re often the only woman on a job site,” says Bailey. “That can be very isolating, especially when you’re facing challenges.
The OBCT provides a muchneeded support network.”
Promoting ongoing education
Skilled
tion industry is undergoing a cultural shift.
“It’s not perfect, but the days of an exclusively homogenized workforce are over,” says Bailey. “I think the industry is really starting to understand that having a workforce that’s mostly middle-aged white males isn’t sustainable or healthy, and it’s not what’s best for the project. It’s valuable to have a diverse workforce because it brings so many different perspectives.”
trades apprenticeships
Construction Training and Apprenticeship Ontario (CTAO), meanwhile, provides a one-stop shop of educational tools and materials for applicants pursuing pre-apprenticeship and apprenticeship opportunities in the skilled trades. “We build awareness of skilled trade careers with the intention of recruiting job-seekers into quality registered apprenticeship agreements with trades unions,” says Gillian Olohan, Program Manager, CTAO. “We also provide access to situational, job-specific education and training that’s vetted through industry partners.”
Bailey — a Journeyperson Steamfitter and Apprentice Welder — and Olohan — a Master Electrician — have both experienced sexism on the job, but they both note that it’s infrequent. They also credit their careers in the trades with growing their confidence and helping them to find material success and job satisfaction.
are a valuable post-secondary pathway. The trades allow people to learn in a hands-on manner and get paid while doing so, so you're not going into debt learning your new career.
“CTAO is so important because it connects people to topics they may not have realized were so powerful,” says Bailey. “For example, when I was in high school, I didn’t connect with the curriculum. I didn’t see the real-world application of math and theorems. But when I got into the trades, I began to love math. I suddenly understood how to use it and how it was going to make my job easier.”
A cultural shift
Tradeswomen often experience challenges in the industry, but they’re quick to point out their love for the work and that the construc-
“Working in the trades has done great things for me in terms of my independence and confidence,” says Olohan.
A valuable post-secondary pathway
Bailey and Olohan both point to skilled trade apprenticeships as an excellent opportunity for women looking to find a fulfilling and well-compensated career with ample opportunity for advancement.
“Skilled trade apprenticeships are a valuable post-secondary pathway,” says Olohan. “The trades allow people to learn in a hands-on manner and get paid while doing so, so you're not going into debt learning your new career.”
“Skilled trades are essential, in demand, and well-compensated, especially if you’re in the unionized sector,” adds Bailey. “And as a woman, when you’re in a union, there’s no pay gap. Every brother and every sister is getting paid the same wage. Also, there’s really no substitute for the satisfaction and sense of ownership that comes from helping to build and craft your community every day.
That’s my favourite part of the trades.”
If you’re considering a trade apprenticeship, Olohan and Bailey share the same advice: “Just jump in!”
