

Future of Manufacturing
“The
Court Edmondson, Director of

Page
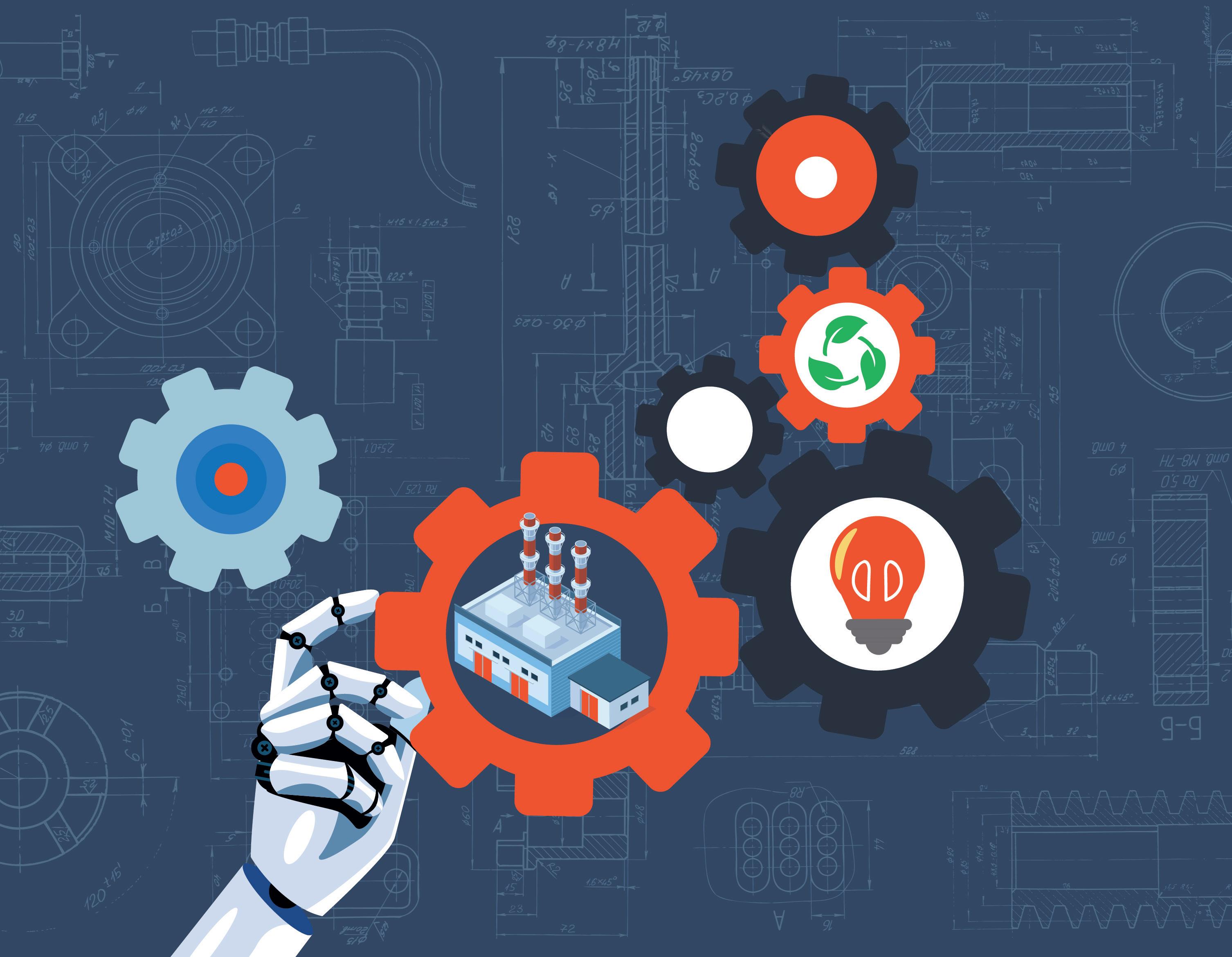
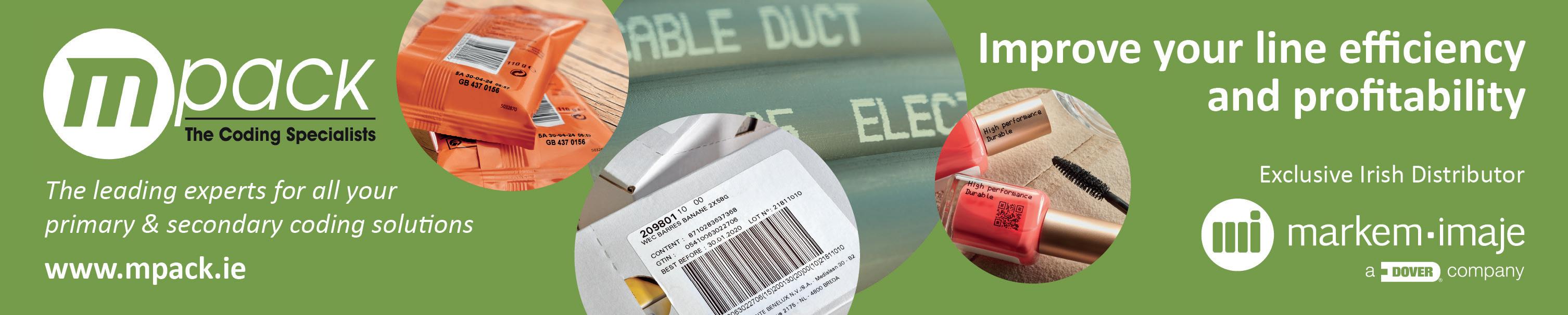
Sinead Keogh, Director, BPCI and Ibec Head of Sectors
How solar panels can give manufacturers a competitive edge
Manufacturers of all sizes can make significant savings on energy and operational costs with a transition to renewable energy sources such as solar power.
Atransition to renewable energy has the potential to support businesses in achieving sustainable manufacturing goals and bring them into line with supply chain partners that may already be reducing greenhouse gases (GHGs).
Reduce carbon emissions
Martin Mulholland, Commercial Operations Director with Activ8 Energies, says companies that adopt solar PV (photovoltaic) solutions can lower energy costs and make operational savings. “Reducing manufacturing costs additionally gives companies a competitive edge in the market,” he adds. Such a switch will also see businesses play a role in meeting Ireland’s Climate Action plan target of 80% renewable electricity by 2030. Activ8 Energies employs 270 people and provides large-scale solar installations for SMEs and industrial clients across Ireland, the UK and Continental Europe.
Bespoke system
The company provides end-to-end solar PV solutions, including energy audits, operational monitoring and identifying efficiency improvements to help companies reduce manufacturing costs and optimise energy usage. Solar design engineers, acquired globally and through their own graduate programme, then design bespoke systems from their headquarters in Co Monaghan.
Typically, he adds, an organisation can expect to see the project pay for itself in two to three years. “With improvements in technology and the cost of PV modules coming down, we are seeing significant reductions in the capital cost of these installations,” Mulholland says.
Government grants
They also advise on planning permission and government grants, which range from €2,400 to €162,600, depending on system size. “We pride ourselves on a full process and have an in-house team to design the system from start to finish and then project manage it,” adds Mulholland.
Once installed, the company offers a full operations and management service with site visits, remote monitoring and thermal imaging drone reports.
Rather than capital outlay, an alternative option for companies is a Power Purchase Agreement (PPA) where Activ8 and its partner SSE Airtricity fully fund and maintain the project over a specific timescale with agreed kilowatt hour rates to provide an organisation with “energy resilience.”
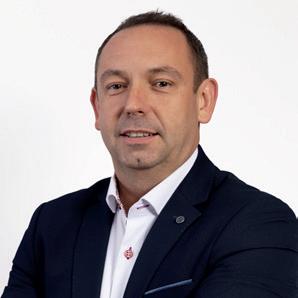
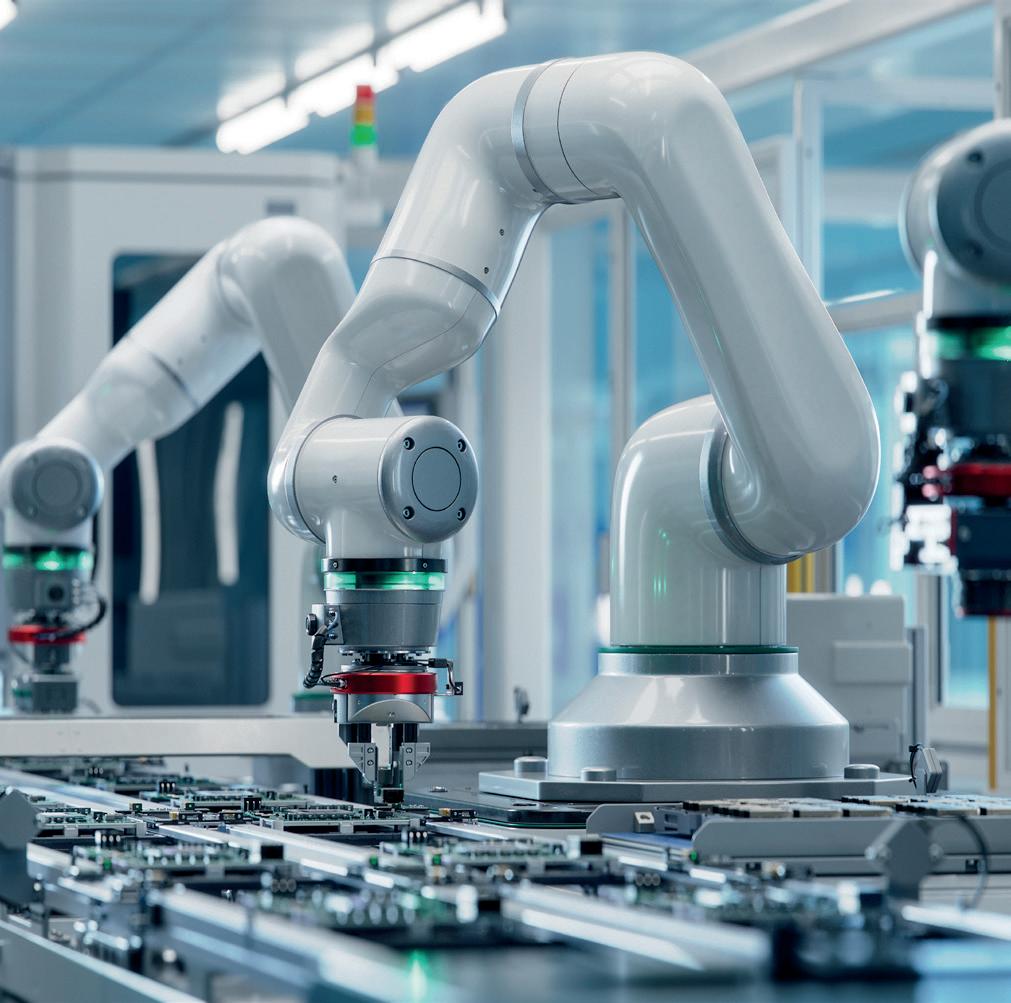
The circular economy propels the next wave of robotics
For many, the ultimate robotic system is one capable of tackling nearly any task at any time. This goal has propelled our recent push in humanoid robotic systems. We are now finally able to realise these dreams as well.

Court Edmondson Director of Robotics and Automation, Irish Manufacturing Research
With new computing hardware, we can finally get the response times we have been dreaming of for decades to process our sensor our data.
Enablers of step change in advanced robotics
Streamlined software ecosystems are making robotic deployment faster and more accessible. Crucially, a new generation of engineering talent is coming into the workforce with skills that once was only available with a PhD and years of experience. Access to these new tools and talent means one thing: the robotics field is finally ready to step up and answer many delayed challenges in our vast manufacturing ecosystem. The agile robotic systems we will create with them will surpass the wave of industrial robots seen in the final decades of the 1900s.
Opportunities for robotics in today’s circular economy
The circular economy, nearly untapped by the robotics field, is full of worthy challenges for our new agile robotic systems too. For decades, robotics has been guided by dull, dirty and dangerous tasks. The circular economy, with its R-Strategies presents a wealth of opportunities that fit into the ‘Three Ds.’ Robotic systems deployed into these labour-intensive
tasks will need to disassemble varied products, sort potentially hazardous materials and refurbish goods for a second life. The circular economy represents a goldmine of opportunities for the robotics community to tackle.
Robotics for the R-Strategies
Like canaries in the coal mine, there are some signals that our industry is mobilising. Robotic sorters, using the latest machine vision and AI, identify and sort our recyclable waste — an ability once dependent on human perception. Automated systems for dismantling solar photovoltaic (PV) panels or electronics exist too and are pushing robotics and automation into the supply chain of the circular economy. This proves that we are no longer limited by past limitations. We are finally capable of developing solutions to navigate scores of tasks, enabling return on investment (ROI) faster than ever.
This quest for versatile robotic systems in the circular economy sounds like the ‘holy grail’ that our first generation of roboticists have been pursuing. I’m certainly excited to help us push our industry, purely for the joy of building some awesome robots. However, if we end up helping the planet in the process, I can still feel good about what I have done for the next generation, too.
WRITTEN BY Mark Nicholls
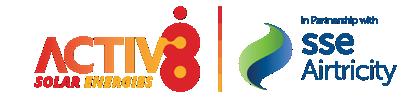
Martin Mulholland Commercial Operations Director, Activ8 Energies
Why making a rare disease medicine is more complex than you may think
For the 300 million people worldwide living with a rare disease, having effective treatment could be the difference between life and death. That’s why advancing access to treatment is crucial.
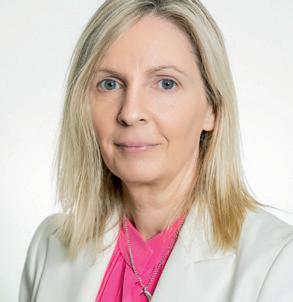
Making these critical medicines demands a unique understanding of patient needs, intricate biological processes and an unwavering commitment to reliable supply.
At Alexion, AstraZeneca Rare Disease, we recognise this profound responsibility and are leading the way in sustainable manufacturing of cutting-edge therapies for rare diseases, from Ireland.
Precision-driven, life-saving manufacturing Manufacturing for rare diseases isn’t simply about producing medicine; it is about giving people options. We understand the serious consequences of any delay in getting medicine to an individual who urgently needs it.
The manufacturing of these therapies is complex. We work with living cells, meticulously nurturing them through an intricate production process. We constantly monitor the cells, interpreting their needs and adjusting the environment accordingly. Whether it is providing additional nutrients, adjusting oxygen levels or managing CO2, this intricate dance of data analysis and biological response requires advanced technology and a deep understanding of cellular dynamics.

Personalised medicines will redefine how we operate Looking ahead, we must advance our processes and ways of working — following the science is key. Personalised medicines present a unique opportunity for patients and a challenge for manufacturers, requiring highly specialised treatments tailored to an individual’s genetic makeup. At
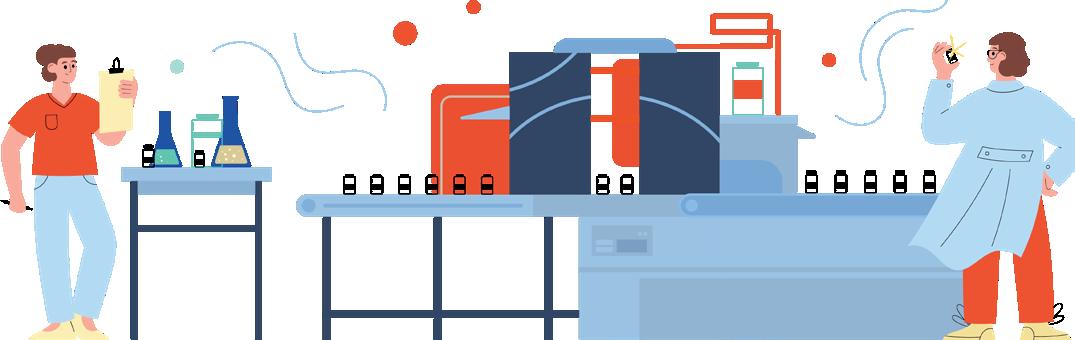
Alexion, we are exploring how we can introduce innovative solutions, including automation, artificial intelligence and advanced biological methods, as we evolve how to develop these highly specialised therapies.
Collaboration and diverse thinking unlock potential
People who can collaborate and offer diverse thinking are critical to success. Ireland’s close-knit pharmaceutical network fosters valuable collaboration. At Alexion, our crosssite multidisciplinary approach between Dublin and Athlone is a strength we leverage. We work seamlessly across sites to ensure the development, scalability and timely delivery of our therapies.
Another tenet of how we are advancing our manufacturing business is through enhanced diversity and inclusion. Better representation of women in manufacturing is proven to deliver improved innovation and a wider range of perspectives. We run several programmes to increase representation of women and other under-represented groups in the workplace, encouraging them to consider technical roles early in their career journey.
Bold leadership will bring positive change
Bold decision-makers, courageous future leaders and a determination to continuously advance how we operate can ensure that we continue to not only manufacture medicines, but to help build a world where people living with a rare disease have options.
Date of Prep: December 2024 M/IE/UNB-U/0012
Why manufacturers must minimise waste in the face of critical materials shortages
Constant supply of key materials used in the manufacture of essential products is no longer a given. Saving waste in the fabrication process is therefore more vital than ever.
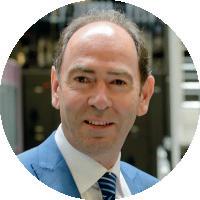
Critical raw materials including lithium and tungsten — defined by the EU as ‘economically and strategically important for the European economy’ — are used to make a range of essential products. However, there is a growing threat to the continuous supply of these and other raw materials.
Critical materials supply challenges
WRITTEN BY Tony Greenway
To maintain and establish a secure and sustainable supply, the EU’s Critical Raw Materials Act came into force in May, listing 34 critical materials and including raw materials recycling targets. Massive demand from a growing middle class, particularly in India and China, is one reason for this disruption in supply.
The rare earth element neodymium is now in
big demand.
“Geopolitics is another,” says Professor Denis Dowling, Director of I-Form, the Advanced Manufacturing Research Centre funded by Taighde Éireann – Research Ireland. Headquartered at University College Dublin, the Centre is a partnership between nine academic institutes across Ireland, working with industry to achieve a step change in manufacturing process efficiency and sustainability.
“For example, the rare earth element neodymium is now in big demand as it’s used in production of magnets found in electric vehicles and wind turbine motors. Yet, approximately 87% of the world’s rare earths are produced in China, which recently applied sweeping restrictions on their export.”
Consequently, prices have increased in global markets. China is also the world’s biggest producer of titanium, which is used in many manufacturing areas, including aircraft and lifesaving medical devices, such as stents. “A question over its supply
will dictate where products like these are manufactured,” says Professor Dowling. “It leaves Europe quite exposed.”
Developing academic and research talent for manufacturing I-Form works with a broad range of manufacturing companies, including those in the clean energy and medical device sectors, on research that aims to minimise critical raw material waste during fabrication. Research areas include materials modelling and AIbased process feedback tools for realtime defect identification. Adoption of these tools has yielded impressive results. One industry partner reported a 90% reduction in experiments needed to achieve optimum product performance, with associated material and energy savings.
Another focus for I-Form is the development of the academic and research talent that will be crucial for Ireland’s manufacturing sustainability. “During our first sixyear period, approximately 130 PhD and postdoc researchers were working within the Centre,” says Professor Dowling. “Those researchers have gained a combination of materials and digital skills and, for the most part, will go directly into industry. Along with the work we’re doing to help companies better use materials and minimise waste, we’re having a significant impact on the talent pipeline.”

Maureen Larkin Executive Director and Site Lead (College Park) Alexion, AstraZeneca Rare Disease
Sponsored by Alexion, AstraZeneca Rare Disease
Professor Denis Dowling
Contributing to Ireland’s growing pharma economy and global health solutions
A major biologics manufacturing plant in Ireland combining stateof-the-art facilities and environmentally conscious practices is playing a pivotal role in the global biopharma supply chain.

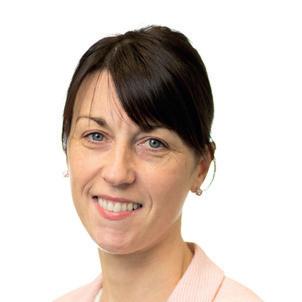
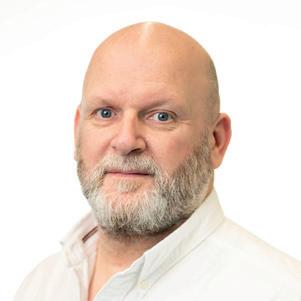
The pharmaceutical sector has emerged as a critical component of the Irish economy in recent years. Supported by leading global manufacturers, it provides employment opportunities for local talent and fosters a supply chain spanning production, technology and administrative support. Additionally, it strengthens Ireland’s position as a global hub for life sciences and biopharma innovation. One of the newer companies in Ireland’s pharma sector is WuXi Biologics, which began operations at its commercial-scale biologics manufacturing hub at Dundalk in 2022.
Shortening supply chains
From seeing some 1,800 construction personnel build the plant, it now employs 770 full-time equivalent personnel in an operation that works closely with the world’s biggest pharma companies. The arrival of WuXi Biologics also highlights the importance of Ireland’s position geographically and economically in the global drug arena, shortening supply chains to Europe and the United States sustainably.
Brendan McGrath, Ireland Site Head and VP of Manufacturing, points to the site’s role in supporting global biopharmaceutical innovation and ensuring a reliable supply. “We established the facility at the request of clients who were looking for geographical closeness in relation to reducing pressure on supply chains,” he explains.
That was graphically illustrated when the Covid-19 pandemic gripped the planet and supply chains were severely disrupted when a container shipped blocked the Suez Canal for several weeks in 2021. “That showed the importance of reducing reliance on long supply chains and trying to bring partners closer to point of use,” adds McGrath.
“An added benefit is the positive impact on the environment by not having to ship materials and products around the world.”
Single-use technology
WuXi Biologics is a global contract research, development and manufacturing organisation

(CRDMO). Its Ireland greenfield site specialises in large-scale, single-use bioreactor facilities for commercial biologics manufacturing. It provides end-to-end solutions to support the discovery, development and production of biologics. With a production capacity of 54,000 litres, the Dundalk facility’s capabilities include its 48,000L fed-batch and 6,000L perfusion suites.
“Single-use technology in our bioreactors allows us to provide a more flexible manufacturing opportunity, particularly where there is a product that is going to be new to market,” says McGrath.
The single-use capability — an alternative to traditional stainless-steel systems used in bioprocessing — offers significant operational efficiencies, including better cost of goods (COGS).
It also reduces resource consumption, such as water and energy, making it a more sustainable and economical option for bringing a product from discovery to commercialisation. In that way, the site contributes to the production of breakthrough therapies, especially in addressing global health challenges for rare diseases that may have an unmet therapy with the production of so-called orphan drugs made in smaller amounts.
Quality standards
Dr Eimear McCarron, Senior Director of Quality, underlines how quality is maintained within the processes both at development and commercial production. The company’s quality compliance record is rooted in the strong quality culture at the Dundalk facility, which has consistently demonstrated control through effective execution.
Blending the synergies of scientific knowledge with regulated quality policies and engineering practices has resulted in the plant receiving the prestigious 2023 ISPE Facility of the Year Award for Operations shortly after achieving initial GMP (Good Manufacturing Practice) certification in 2022 from the Health Products Regulatory Authority (HPRA) in Ireland.
The site’s Quality Risk Management programme led by Dr McCarron points out that the site’s Quality by Design (QbD) approach allows data to flow

Sponsored by WuXi Biologics
Brendan McGrath
Ireland Site Head and VP of Manufacturing, WuXi Biologics
Dr Eimear McCarron Senior Director of Quality, WuXi Biologics
Gene Russell
Senior Director of Engineering, WuXi Biologics
WRITTEN BY
Mark Nicholls
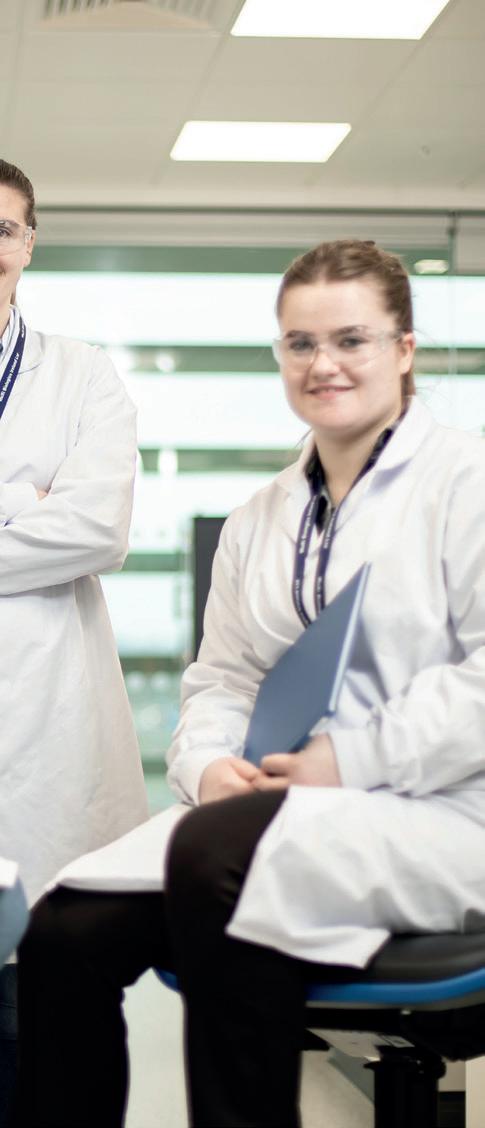
smoothly, supporting the foundations for a strong endto-end model for product release. “A strong compliance culture has led to the successful commercialisation of the site’s ability to manufacture clinical and commercial drug substance of small and large molecule and biologic treatments for multiple clients serving the needs of patients,” she adds. “The Dundalk operation has a clear approach to continuous improvement in operational efficiency and quality control, leveraging the most current technology and innovation to minimise risks.”
Supporting businesses and talent
From construction to becoming operational, the plant has supported an ecosystem of local businesses, suppliers and research collaborations. McGrath says the world’s top 10 pharma companies have a presence in Ireland, and the support of that ecosystem of construction, equipment, technical expertise and supply chain vendors has been pivotal.
An additional contribution has been in nurturing local talent through partnerships with Irish universities and training programmes aimed at building a skilled workforce. “To grow our workforce, we have a mix of employees: attracting existing employees from other companies that may have many years of experience; attracting graduates to a state-of-the-art facility and also some employees new to the sector and want to join our industry,” says McGrath.
That has seen close liaison with Dundalk Institute of Technology (DkIT) and liaison with universities and students on biopharma and science courses, attending college fairs, holding on-site recruitment days and using technical services such as those provided by the National Institute for Bioprocessing Research and Training (NIBRT).
Attractive environment
The company has a STEM strategy and works with schools and colleges to help potential recruits understand the roles of scientists, microbiologists, manufacturing technologists and data analysts to link the pathway from classroom subjects to a successful career in the biopharma sector. That additionally includes being industry partners of the Virtual Labs Project, Women in STEM initiative and core members of leading industry biopharma bodies.
Single-use technology in our bioreactors allows us to provide a more flexible manufacturing opportunity.
There are advancement opportunities within the company, which has sites in the United States, Germany, China and Singapore, providing services to 600 partners globally, including the top 20 pharmaceutical companies. Ireland’s established reputation as a life sciences and biopharma innovation hub is further enhanced by the presence of companies such as WuXi Biologics, particularly as the first large-scale CRDMO in the country.
“It is a very attractive environment for people who are seeking new opportunities in a dynamic and fast-paced environment, the types of technology platforms and products are cutting edge and represent the industry’s future. It is a different pace to big pharma and takes different skills and mindsets,” says McGrath. With 22 different nationalities in the workforce, the aim over the next decade is to become a ‘partner of choice’ for the major pharmaceutical players and see additional products come to the site, potentially leading to expansion. “We want to become a trusted partner and have an impact on patients’ lives in a positive way through the products we manufacture,” adds McGrath.
Achieving net zero through sustainability and science-based targets
With a commitment to environmentally responsible practices, while driving biopharma innovation, WuXi Biologics Ireland’s Senior Director of Engineering Gene Russell explains the company’s focus on sustainability.
How does the company follow sustainable practices in its overall business?
Gene Russell (GR): In 2023, WuXi Biologics committed to the Science Based Targets initiative (SBTi) and has made strong progress in tackling climate change and reducing carbon emissions. Since 2020, the company has achieved a 29% intensity reduction of its Scope 1 and Scope 2 greenhouse emissions through carbon and energy-saving measures with further projects planned to achieve the group’s — and Ireland’s — longterm targets of 50% reduction by 2030 and net-zero emissions by 2050.
How does the site follow sustainable practices in line with group strategy and Ireland regulations?
GR: The company has integrated sustainability into its operations, aligning with Ireland’s Climate Action Plan and the United Nations’ Sustainable Development Goals (SDGs). Company efforts include reducing energy consumption, promoting sustainable resource use throughout the manufacturing process and implementing sustainable supply chain practices. These are core to our company priorities both short and long-term, which are championed by engineering SMEs, supported by initiatives throughout the site and progress routinely cascaded through the organisation.
What are the major sustainable practices at the Dundalk site?
GR: We have launched several initiatives to address energy efficiency, waste management and carbon neutrality. High-efficiency energy systems, including advanced building management technologies, have been installed to optimise electricity and heating usage. Projects for energy consumption/carbon emission include the identification and implementation of feasible energy to reduce dependency on natural gas; use of renewable electricity sources and biofuels; implementation of waste segregation and recycling programmes to divert waste from landfills; and carbon offset programmes.
Green transportation policies encourage electric vehicle use (with on-site EV charger installations and newly launched car share scheme) and reduce travel-related emissions. Single-use technology (SUT) in manufacturing has led to 70% water savings versus comparable stainlesssteel technology. Waste reduction achievements include 100% recovery of solid hazardous and non-hazardous waste; 0% waste sent to the landfills; and rainwater harvesting savings of over 16x million litres. Further works around the areas of solar power, wind energy, WWPT (wastewater pretreatment plant) and reforestation are currently in consideration and evaluation.
How do you measure and ensure impactful sustainability efforts?
GR: We ensure sustainability initiatives are measurable and effective by adopting international environmental frameworks. The site has been on the journey since 2022/2023 and achieved energy/environmentrelated ISO 14001 and ISO 50001 certifications. Through energy-saving technologies and waste-reduction strategies, WuXi Biologics Ireland is paving the way for a greener future in biopharma.

Cutting-edge research and innovation shaping the future of manufacturing
One of the most significant global challenges facing the manufacturing sector today is sustainability. Ireland’s manufacturing sector is crucial, contributing to almost 37% of the country's GDP and 11% of total employment.
Digital transformation and the green transition are key to driving both competitiveness and sustainability across the manufacturing sector. The integration and adoption of emerging and advanced digital technologies have a transformative potential to address both technological and societal challenges relating to the sustainability of manufacturing and supply chain resilience.
Sustainability and resilience through collaboration Sustainable industrial development faces challenges that demand technological innovation and strong, coordinated collaboration across diverse stakeholders. Investment in research and innovation is crucial for the manufacturing sector to develop solutions to these challenges that will lead to sustainable manufacturing processes. Involvement of stakeholders who understand the needs of end users ensures that digital technologies are integrated in a responsible way that reflects values such as safety, fairness, inclusion and privacy.
Value of a solution-focused approach
One novel approach being employed is called ‘Challenge-Based Funding’. This solutionfocused approach fosters cross-disciplinary and cross-sector collaboration among academic researchers, industry experts, government regulators, end-users and other stakeholders. It ensures close cooperation to develop innovative, practical solutions to wellarticulated problems.
Research Ireland’s National Challenge Fund, a €65 million research fund established under the Government of Ireland’s National Recovery and Resilience Plan, and funded by the EU Commission Recovery and Resilience Facility, supports researchers in creating disruptive digital technologies that will lead to new digital products, processes and services that will unlock transformational societal and economic impact for Ireland.
Teams of researchers working with industry stakeholders are developing a range of innovative industry-focused solutions — from deployable collaborative robotic systems and additive manufacturing (3D printing) with integrated computer vision to sustainable green hydrogen production.
Engage Ireland’s research ecosystem
With the ever-growing need to deliver solutions to specific industrial challenges, there has never been a better time to engage with Ireland’s leading research ecosystem and discover the benefits collaborative research and innovation can and do deliver for industry and society as a whole.
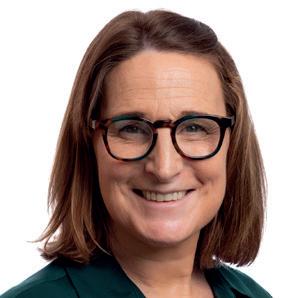
Ireland’s manufacturing hub generates billions in exports and attracts global investments
Manufacturing contributes 39% of Ireland's GDP and €208 billion in exports. Industry 5.0 capabilities are key for attracting high-value investments and driving innovation in future manufacturing pipelines.
IDA Ireland partners with over 1,800 leading multinational companies across various sectors including biopharmaceuticals, medical technologies, engineering, technology and financial services. From their operations in Ireland, these leading international companies develop and deliver products and services globally.
Strategy for Ireland to win new manufacturing investment
Ireland’s stable, business-friendly environment, EU membership, skilled workforce and strong manufacturing heritage, particularly in medical technologies and biopharmaceuticals, position it as a top manufacturing investment location.
IDA’s 2021–2024 strategy, aligned with the Government’s White Paper on Enterprise 2022–2030, focuses on five pillars (growth; transformation; regional development; sustainability; and impact) and continues to drive both existing and new manufacturing investments. The transformation pillar focuses on increasing the competitiveness, agility and resilience of Irish operations through RD&I, digitalisation and sustainability. All this is underpinned by a relentless focus on talent development.
In medical technologies, companies like Abbott and Dexcom, have announced and constructed large-scale greenfield advanced manufacturing facilities to produce nextgeneration blood glucose monitoring devices for patients living with diabetes. Other leading manufacturers have leveraged the transformation opportunity to build out highvalue manufacturing operations.
Irish manufacturing: digital growth supported by skills
The twin digital and green transition is bringing challenges and opportunities that require an agile and resilient workforce. Ireland remains a stable, reliable partner for organisations pursuing agile, flexible, digitally enabled and sustainable manufacturing, supported by a strong ecosystem and a focus on future skills to drive this transformation.
Future-proofing life sciences workforce
IDA Ireland, through its transformation, talent and innovation team, recently facilitated an event on ‘Future-Proofing Ireland's Life Sciences Workforce: Strategies for Talent Transformation’ hosted by the National Institute for Bioprocessing Research and Training (NIBRT). The event featured workshops from Digital Manufacturing Ireland and included speakers from the Future of Work Institute and the Skillnet Climate Ready Academy, plus leaders from life sciences companies. Through collaboration with the ecosystem and our partnership on upskilling, Ireland is building the strategic workforce for the future of life sciences manufacturing.
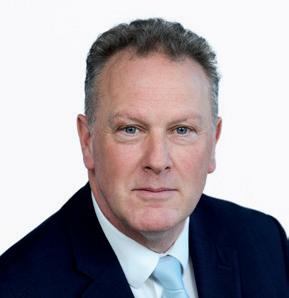
A strategic
vision for growth in Ireland’s manufacturing future
Ireland's biopharmachem industry, employing nearly 50,000 across 90+ sites, drives economic growth with over €100 billion in annual exports, highlighting the nation's resilience and adaptability.
Recently, BioPharmaChem Ireland (BPCI) convened 80 senior leaders for its annual ‘think-in’ to discuss shifts in the global landscape. The recent pandemic underscored the importance of local supply chains and health sovereignty, prompting nations to prioritise domestic manufacturing. As global competitors increase investment incentives, it is crucial for Ireland to adopt transformative policies to maintain its competitive edge.
Life sciences and healthtech strategy
The need for a robust life sciences and health technology strategy led by the Department of Enterprise, Trade and Employment is urgent. This strategy should provide a clear roadmap for the sectors, effectively coordinating state resources to foster the sustainable development of the sector. Ireland must keep pace and lead in attracting investments to strengthen its life sciences manufacturing base.
Emphasising lifelong learning for all Talent acquisition and skills development are essential to this strategy. The Expert Group on Future Skills Needs report, ‘Skills for BioPharma’ published in 2024, identified a potential 21,000 additional jobs in the sector over the next three years. Achieving this growth depends on cultivating a science, technology and digital workforce. Emphasising lifelong learning and increasing female participation in STEM fields will be vital for nurturing this talent. While we welcome the recent Budget 25 investment in the Department of Further and Higher Education, Research, Innovation and Science, it is critical that these funds target fundamental and applied research within Higher Education Institutes. Promoting collaborative R&D can strengthen the link between academia and industry, fostering innovation that enhances competitiveness. With 25% of all PhDs in Ireland employed in this sector, support for doctoral programmes aligned with industry needs is essential.
Infrastructure and sustainable growth
Ireland's infrastructure must also adapt. Addressing constraints hindering growth, particularly in planning, EPA licencing and more broadly childcare, housing and health services require significant investment. Improving quality of life is essential for attracting and retaining international talent.
Increasing productivity remains the sector's priority, driving substantial investments in digitisation and sustainability. In March, we will launch our sustainability strategy alongside our annual BPCI Responsible Care report, assessing the sustainability performance of the sector from 2021 to 2023 with insights from over 45 sites. Additionally, we are introducing a new AI programme for the life sciences manufacturing ecosystem, fostering collaboration on use cases through our Connected Health Skillnet.
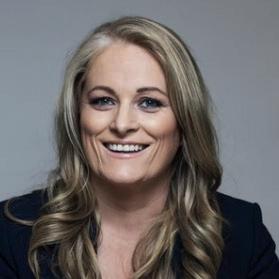
Lisa Higgins Head of Challenge Research, Education & Public Engagement, Research Ireland
John Nugent Manager Medical Technologies & Healthcare Services, IDA Ireland
Sinead Keogh Director, BPCI and Ibec Head of Sectors
Unlocking factory floor data: challenges and opportunities
The highest-performing companies in the world run on data. Many manufacturing organisations are still facing challenges in data integration across their systems, inhibiting their competitiveness in the quickly evolving era of Industry 4.0.
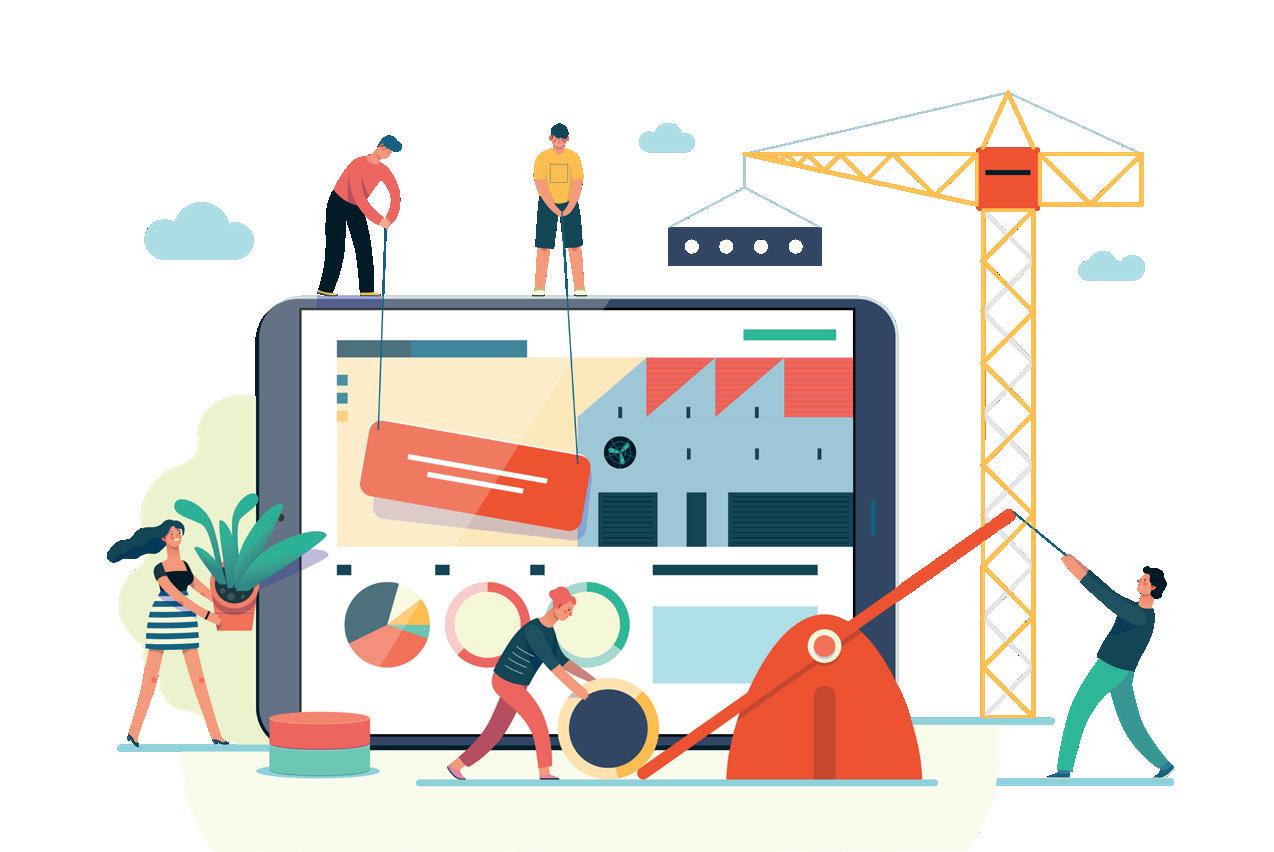

Data generated from manufacturing operational technology (OT) systems — industrial equipment, sensors, production systems etc. — are some of the fastestgrowing data subsets in the world. The opportunity to drive transformational change by refining this data into actionable information, particularly utilising AI, is significant. The challenge faced by manufacturers is how they collect and prepare their data, at scale, to fuel the coming wave of AI innovation.
Architecting data pipelines
No two factories are the same, particularly when it comes to data. A typical factory digital footprint is made up of a fragmented mix of equipment, vendors, software platforms, communication protocols and more. Traditional approaches to connecting assets
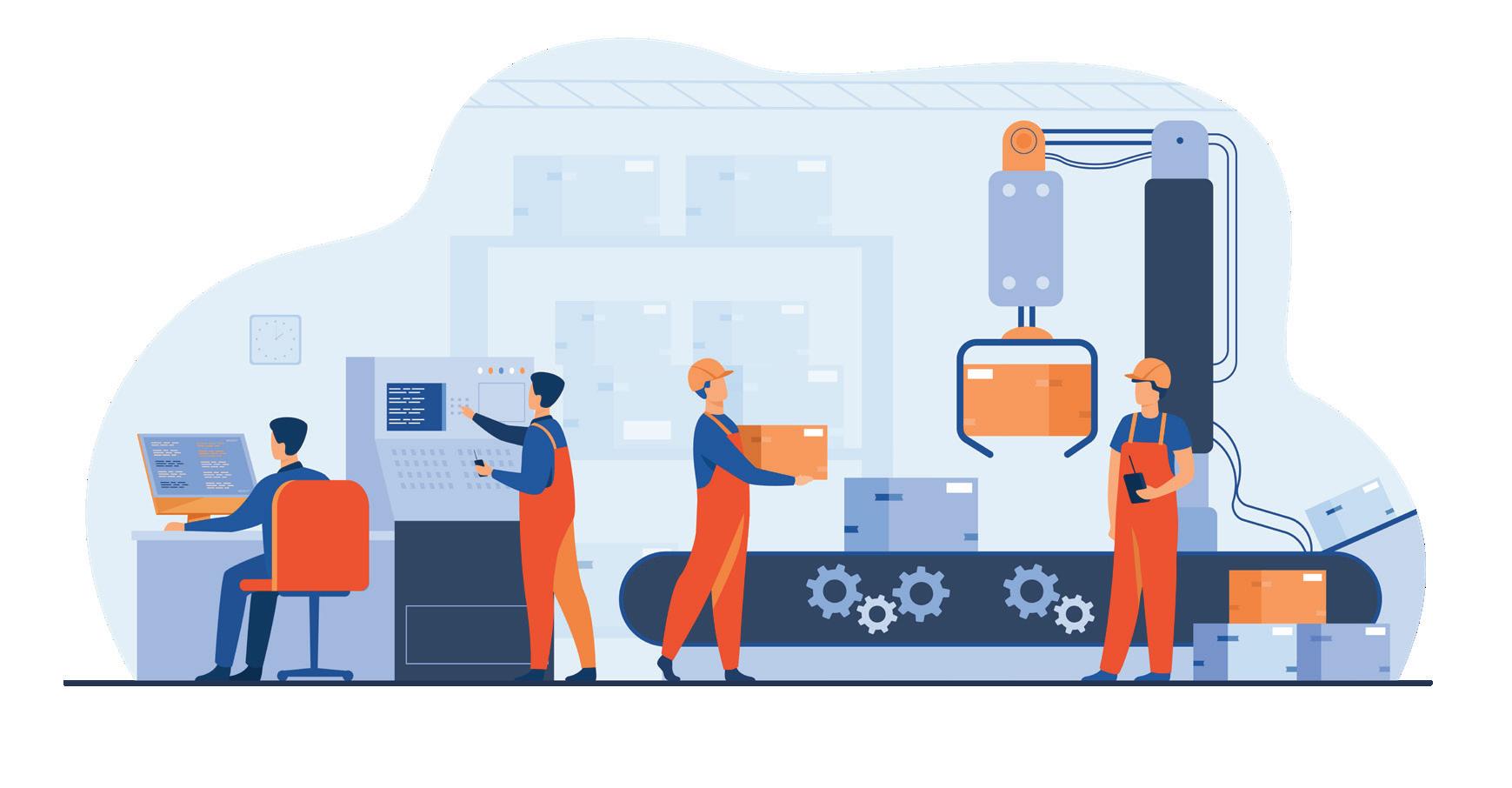
Emerging OT systems and security challenges
and collecting data from OT and IT systems have required mostly monolithic, proprietary stacks of software, often with closed architectures from specialist service providers. These ‘pointto-point' linear integration approaches, transferring data from the shop floor through OT/IT layers to enterprise or cloud solutions, have been the foundation of manufacturing IT and OT systems for decades. This proven approach has advantages in security and reliability but can often lack flexibility and ability to scale. Moreover, it can be costly to develop and alter. Seeking change, industry innovators and disruptors are pioneering other approaches. Functionally driven, open factory data architectures are now becoming an important foundation for successful digital transformation.
Among the trending OT architectures, decoupled messaging-based systems are gaining popularity. These architectures allow for all equipment, people and systems (nodes) in the factory to become data ‘publishers’ and ‘subscribers,’ creating massive flexibility and scalability.
No
two factories are the same, particularly when it comes to data.
New architectures offer advantages but face challenges in widespread adoption, especially in addressing cyber security risks and ensuring compliance with strict regulatory standards. Irish Manufacturing Research (IMR), along with its ecosystem of partners, is enhancing its digital factory capabilities to showcase the art of the possible in this critical area for Irish manufacturing.
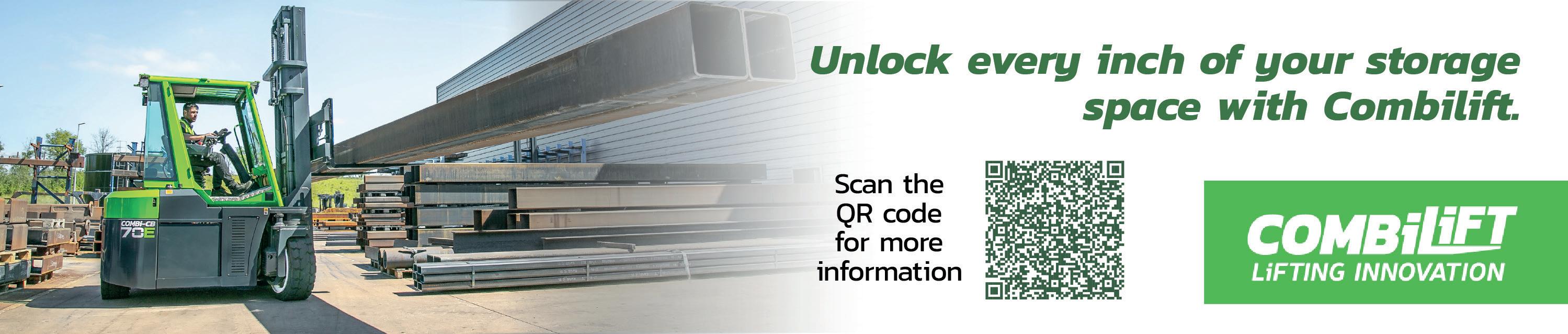
Alan Kavanagh Senior Digitalisation Programme Manager, Irish Manufacturing Research
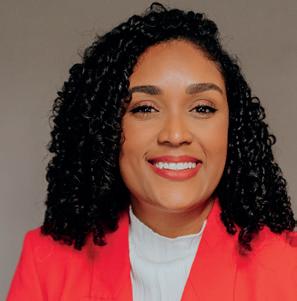

Addressing the manufacturing skills gap by giving schools access to tools
Ireland’s manufacturing sector faces a talent gap, threatening its future. Learn about the initiative bringing advanced manufacturing tools to schools, inspiring students to explore careers in this vital industry.
Ireland’s manufacturing industry is facing a critical challenge: a shortage of reliable, qualified staff. This growing gap threatens the sector’s future, but we believe the solution starts with the next generation.
Inspiring youth to bridge manufacturing skills gap
To help address the skills shortage, the Precision Tooling and Machining Association (PTMA) is introducing Alpha Mill CNC machines into schools. This initiative aims to inspire and educate young minds about manufacturing through hands-on experience.
One of the most effective ways to address this challenge is by engaging the younger generation early.
The lack of skilled staff has become a pressing issue for many companies in Ireland’s manufacturing sector. A recent survey among industry leaders confirmed that this talent shortage is the biggest hurdle they face.
As an association dedicated to supporting the sector, we understand that action is needed now to secure a thriving future for manufacturing in Ireland.
Learning through access to CNC machinery
One of the most effective ways to address this challenge is by engaging the younger generation early, sparking their interest in the manufacturing world. With support from our member companies, we have developed a new initiative that puts this idea into action.
The recently launched Alpha Mill CNC Machines in Schools programme brings state-of-the-art CNC (computer numerical control) machinery directly into schools, allowing students to explore manufacturing in a hands-on, interactive way. The feedback has been incredible, demonstrating the powerful impact of introducing students to the practical side of manufacturing.
Empowering the future of Ireland’s manufacturing
As the PTMA, we are fully committed to fostering a brighter future for the next generation by giving them the tools and inspiration to pursue careers in the sector. Together, we can tackle today’s challenges by shaping the future of Ireland’s manufacturing industry. It is another initiative from us to the future of the manufacturing sector in Ireland.
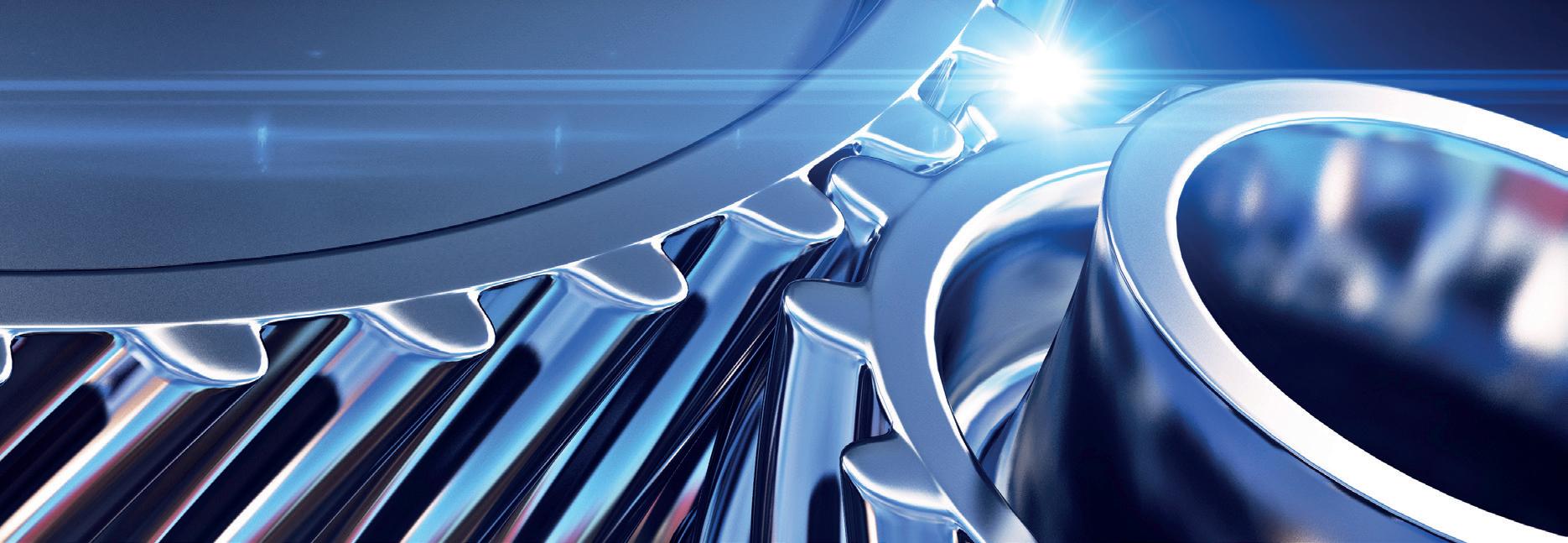
Leticia Bastos Marketing Coordinator, PTMA Ireland