
8 minute read
CRE
Adaptive Reuse: Should Retrofitting Be the Future of Real Estate?
Adaptive reuse, or the process of reusing an existing building for a purpose other than that for which it was originally built or designed, is an important commercial real estate trend that our team predicts has long-term staying power. While new build construction has many benefits, adaptive reuse is moving on from being considered solely for historical buildings or revitalization. While it takes an experienced team and a targeted strategy to properly retrofit an asset, the benefits range from cost savings, sustainable construction, historical or cultural preservation to community building and repositioning properties left vacant from cultural or economic shifts.
As experienced in many industries, the events of the past year have caused a major shift. During any real estate upheaval, adaptive reuse becomes even more attractive. During the recession of 2008, many condo buildings were undersold or entirely empty. Across the U.S., adaptive reuse was used to convert condos to rental or hospitality properties. Forward thinking developers in Phoenix bought up decades-old, dilapidated apartment properties that still had good bones and repositioned them to provide affordable housing in prime urban areas of the Valley. Empty retail spaces were converted to offices and churches. While our market today is different, one commonality is the surplus of empty buildings due to cultural and economic shifts.
Two main factors are contributing to the low occupancy of existing office buildings: the urban to suburban migration and the rise in employee telecommuting. Current conditions have left landlords and companies scrambling to figure out what to do with buildings that are either now obsolete or in need of downsizing. And while we hope some of these buildings can be retained for their original use, the properties that can’t be make prime candidates for adaptive reuse projects. Converting office complexes into multifamily, mixed use or live/work properties is a direct response to the supply/demand issue that real estate is currently experiencing.
At Private Label, we are certainly not strangers to repositioning assets. From a design perspective, we like a good story and find inspiration in leaving a building better than we found it, thus affecting the community in a uniquely positive way. One project we are currently working on is converting three high-rise office buildings into live/work rental apartments. The lower levels of each building are being outfitted with state-ofthe-art super amenities, like a recording studio, fitness pods, a virtual reality lounge and duckpin bowling lanes, as well as conference rooms, teleconference rooms and an indoor/ outdoor amphitheater. The original office infrastructure lends itself well to providing the necessary building programming for multifamily units through necessary parking, existing restrooms and public to private square footage. On many projects, we’ve had the opportunity to uncover design features that deserve to be retained and not bulldozed. Adaptive reuse, when done correctly, gives us an opportunity to stay true to a building’s innate character, and that can only enhance the final product. We hope to see more developers in the future continue to look for ways to reuse and adapt where possible. —Christina Johnson, creative director of Phoenix- and San Francisco-based Private Label International (privatelabelintl.com), a full-service interior design studio that develops hospitality environments and lifestyle brand experiences for clients worldwide GET REAL
by Mike Hunter
Affordable Housing Breaks Ground in Central Phoenix
Construction on Mesquite Terrace, a multifamily affordable housing community in the Solano Neighborhood on 19th Avenue, one block north of Camelback Road near the light rail, broke ground earlier this summer.
When completed at the end of 2023, the three-building property on nearly four acres will offer 297 units: 129 one-bedroom, 78 two-bedroom and 90-three bedroom apartments ranging in size from 575 to 1,050 square feet. The first building is expected to be completed by the end of 2022.
The project is being co-developed by Catholic Charities, through its Housing for Hope, Inc. affiliate, and Trinity Development, LLC. housingforhopeaz.org • catholiccharitiesaz.org
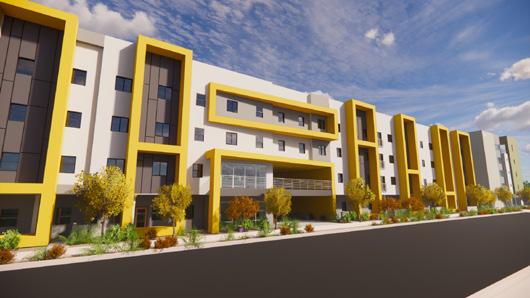
Attainable Housing Fills Gap between Affordable and Luxury
Scottsdale-based Greenlight Communities plans to start construction this summer on a 250-unit development called Cabana Southern just west of the southwest corner of Crismon and Southern Avenues in Mesa, and expects to welcome its first residents in fall of next year.
Greenlight Communities is the first company to focus solely on building attainable housing to fill the void between affordable and luxury apartments, using its leading-edge business and development model to create a one-of-a-kind housing alternative for middle-class residents working in fields such as teaching, healthcare and public safety.
Greenlight Communities is currently leasing at its Cabana Hayden property in Scottsdale and has two projects underway in the city of Goodyear, one in Glendale and second in Mesa. Projects are also under construction and in the development pipeline in additional cities, including Phoenix and Tucson. livegreenlight.com
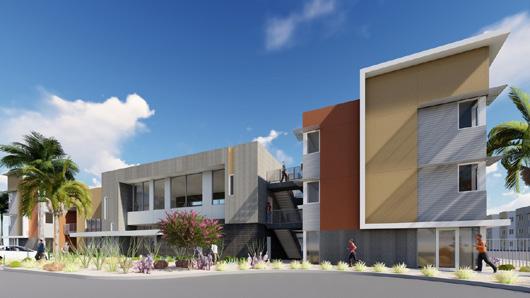
Not Yet in Phoenix
Businesses’ workforce needs span from high-level (and high-paying) jobs to entry-level and menial jobs. Businesses need workers, and all income levels need housing. Creative ideas have been emerging to address the affordable housing crisis. Gensler, for instance, is involved in a project in Los Angeles that is using prefabricated modular construction, which it predicts will be a game-changer for the industry, potentially cutting production time in half and reducing costs by 20% compared to conventionally built projects. Real Estate company Repvblik, under CEO Richard Rubin, has been delivering apartments through adaptive reuse of malls and stores.
Large-Scale Logistics Center Planned near Phoenix-Goodyear Airport
Data Centers: Increasing Speed to Market

Phoenix-based alternative investment and real estate development firm Creation, in partnership with CrossHarbor Capital Partners, recently closed on 170.25 acres at the southeast corner of Yuma Road and Bullard Avenue, adjacent to the Phoenix-Goodyear Airport in Goodyear, Ariz.
Plans call for a five-building, multi-phased 2.7 million square-foot logistics development called Airpark Logistics Center. The site is located on the northwest side of the 8,500-foot length runway — the third largest in Arizona — in a federally approved Foreign Trade Zone in Maricopa County, one of the fastest-growing counties in the United States. Goodyear is centrally located within Phoenix’s West Valley, which has evolved into a primary manufacturing and logistics hub serving both the Phoenix Metro area and the entire Southwestern U.S. over the past decade.
The strong demand for logistics and warehouse space has been accelerated by the surge in e-commerce direct-to-consumer retail sales in response to the COVID-19 pandemic, as well as a resurgence of inventories back to the U.S. as companies reduce their supply chain dependence on China.
Construction of the first phase of Airpark Logistics Center, which will consist of three buildings totaling approximately 1.4 million square feet, will commence in September 2021. Phase two will total approximately 1.3 million square feet and construction is anticipated in early 2023. While phase two is presently being offered on a traditional build-to-suit basis, Creation has engaged in preliminary discussions about the potential to
Construction teams across industries are faced with common challenges: shortened schedules, tight budgets and labor shortages — all while bringing facilities online faster to meet an uptick in demand, particularly in the mission critical sector. JE Dunn Construction has deployed creative solutions to increase speed to market for data centers at a time when the market needs them the most.
Modular construction: Modular construction involves prefabricating components — such as input and output switchboards, UPS modules and battery cabinets — in an off-site facility for quicker installation, either in modular containers or open skids. The modular containers and open skids contain all assembled equipment and are shipped directly to the site for installation of each component, as trade partners are ready for them. This cuts the time in the schedule that would be required to build these components onsite for a traditional stick-built project. When the client orders premade skids and has them onsite, that makes construction faster and reduces the overall schedule. One of the biggest risks to a data center schedule is getting the equipment onsite when it’s needed. Having premade skids available eliminates that risk.
Advanced work packaging: Advanced work packaging takes design down to the utmost level of detail to eliminate mistakes, improve quality, enhance safety, save time and increase efficiency through repeatability. It combines planning, prefabrication and modular components at not only a higher level of detail but also to a much larger scale that creates smaller, repeatable packages for installation that are easy to track and execute. By breaking project scopes into smaller packages, teams can reduce the amount of build-up of work-in-process, in turn decreasing the risk for project delays.
facilitate future aviation logistics by way of “through the gate” access to Phoenix, Arizona 2021 . 04 . 15AIRPARK Logistics Center CONCEPT RENDERING VIEW - NW CORNER - REAR LOAD BLDG ‘A’Phoenix-Goodyear Airport. This artist rendering is for conceptual design only and should not be referred to as a construction document. THESE DRAWINGS ARE AN INSTRUMENT OF SERVICE AND THE PROPERTY OF LGE DESIGN GROUP AND LGE DESIGN BUILD AND SHALL REMAIN THEIR PROPERTY. THE USE OF THIS DRAWING SHALL BE RESTRICTED TO THE ORIGINAL SITE FOR WHICH IT WAS PREPARED AND PUBLICATION THEREOF IS EXPRESSLY LIMITED TO SUCH. Creation and CrossHarbor have hired Phoenix-based LGE Design Build for full design-build construction and architectural services.
Throughout the country, there are a limited number of industrial logistics developments adjacent to runways where air cargo fleets have direct access into hangars located on fee simple land. —Mike Hunter
Creation creationequity.com CrossHarbor Capital Partners crossharborcapital.com
Shift the schedule left: Another way to shorten the schedule and reduce the risk for delays is a shift to commissioning to the “left” in the schedule, or beginning activities earlier in the process. This frees up time on the back end (or right side) of the timeline. Teams create fully functional systems off site ahead of typical project schedules to eliminate potential misalignments and delays. By having an offsite location to test equipment before the building is complete, project teams can work out any bugs with the owner/engineer, agreeing to the final product in a controlled environment.
Changing the model: Each owner and project is unique, but, by changing the approach and execution model, owners get back time, predictability and peace of mind throughout the construction process. —Brad Schenck, senior vice president and Southwest Division leader of JE Dunn Construction (www.jedunn.com), a domestic general building contractor in the United States founded in 1924, now with offices in 24 locations
