
4 minute read
Fonterra construction culture change bears fruit in safety and productivity
april-may 2021 Components of an effective project culture
Following two construction site fatalities in 2009, Fonterra wanted to understand how it could avoid future incidents and develop cultural model to achieve success
Advertisement
Components of the Manuka Project
- A daily joint meeting involving all trades to review the day's activities, risks, dependencies and opportunities for collaborative working - Providing meal options on site to encourage shared lunches and increase cross-trade communication - Specialist health services onsite, including a nurse providing regular health checks and workplace support services to assist with mental health or other employee issues (eg. specialists providing support for family or financial issues)
- Onsite training opportunities, including specialist supervisor training on conflict resolution and communication - Reinforcing cultural values around the site (for example Project Manuka branding and information) and promoting rewards and recognitions (for example:. free lunch to reinforce positive or exemplary behaviour) - The introduction of simple measures, including regular cleaning of site toilets, to make staff feel more valued. To improve health and safety at its worksites, the company needed to create an environment that was both physically and psychologically safe. Central to this was changing the culture at its construction sites.
The company developed a robust, yet innovative, approach to site culture, worker welfare and project efficiency.
To find out the cause of health and safety incidents on its sites, Fonterra embedded a researcher with different working crews in 2009.
The company discovered that its leadership decisions were having a direct impact on site safety. The researcher observed staff taking risks and cutting corners.
Although construction typically requires a linear way of thinking, Fonterra discovered that cultural change requires a trial-and-error approach.
For this method to work, Fonterra needed to become an environment where people feel safe to talk about what's not working.
Leaders listened and learned from their staff to understand their needs and what approaches might work on future projects.
Improving site culture is based on the theory that a quarter of a project's success is driven by the effectiveness of the design, another quarter by the effectiveness of systems and processes and the remaining 50 percent driven by the effectiveness of the project's culture.
To help track its progress to transformational change Fonterra developed a cultural model: - Generative: positive behaviour and safe culture is reinforced by all staff - Proactive: senior leaders
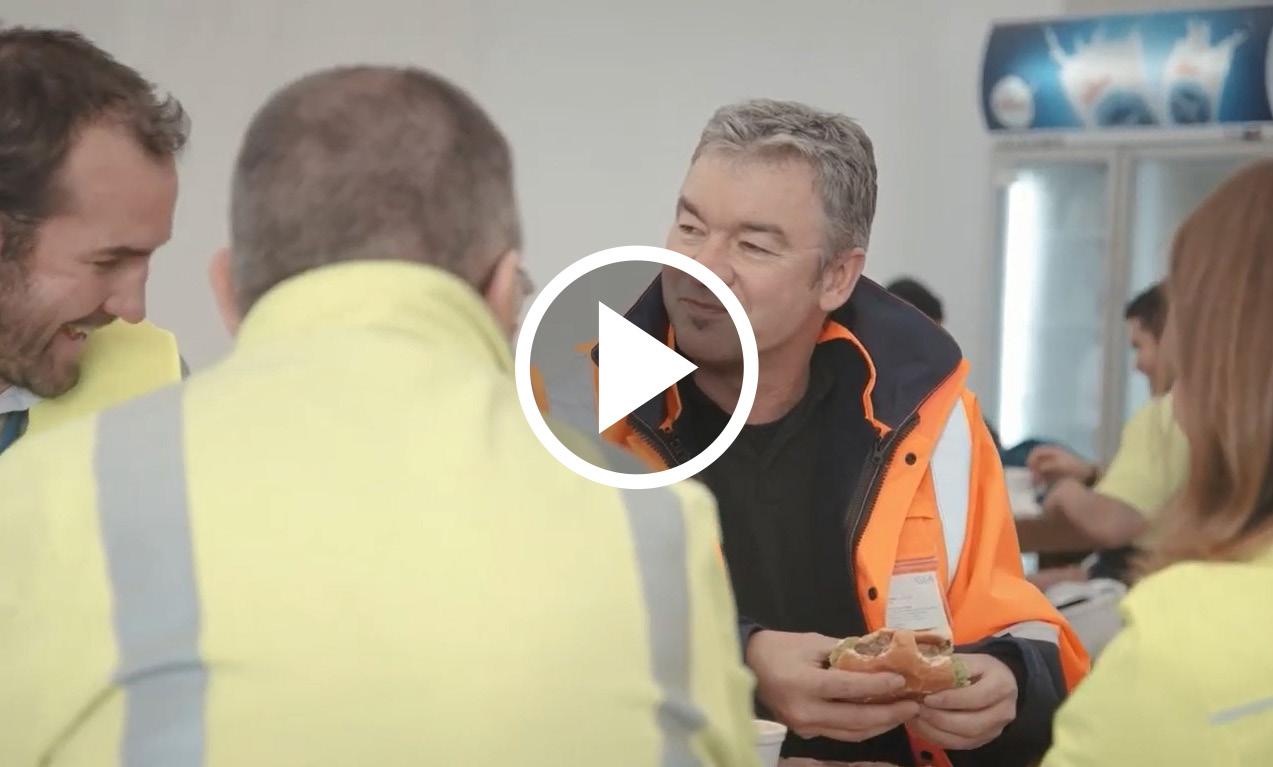
look to actively address culture issues - Calculative: rules and compliance procedures are put in place to minimise risk - Reactive: measures are taken to address issues as they arise - Pathological: little care or effort is taken to address issues
Project Manuka’s Community of People
Fonterra launched its Community of People programme at the Project Manuka site with an investment of $500,000 – half a percent of its $100m site upgrade to two Hawera milk processing plants.
While the approach was developed with improved health and safety in mind, Fonterra achieved better project outcomes as a by-product of improving its culture. By focusing on worker well-being and creating an environment where employees from different trades can meet and socialise, the team became more collaborative and efficient.
These changes not only made Fonterra’s employees and contractors safer and healthier, but also made its projects more successful. "Health and Safety was promoted by Fonterra by turning it into a Trojan horse for improving productivity through better planning and collaboration, " says Juergen Link, General Manager Assets and Capital Projects.
This transformational change has benefitted clients, contractors, and employees.
Since launching its approach in 2009, Fonterra has experienced a 93 percent decrease in injuries and incidents on its major construction sites, which would have previously resulted in lost time on projects. "Absolutely without a doubt, the village/family environment is a big success in creating culture change, attitudes towards health and safety and that management do actually care," - says Fonterra Health and Safety Coordinator Mike Longstaff.
Toolbox meetings, involving detailed planning between different trades, has allowed Fonterra to move from a slower, sequential method of working to a faster and more dynamic approach.
Contractors have developed positive relationships with Fonterra and see the benefits of the training their supervisors and front-line staff have received. "Project Manuka's Community of People Programme made it possible for the team to work through the incredible stressors of a pandemic.
“Resources had been implemented to support the mental health and wellbeing of the staff, which gave the team the tools and motivation to continue during even the most stressful times and conditions," says Craig Waghorn, Apollo Projects Director and Chief Executive.
Project outcomes are better, more successful and more consistent, according to Andrew Grafas, Tetra Pak Processing Key Account Manager. "We still have the usual challenges, but we collaborate better, solve complex problems, work across boundaries and are more respectful of each other. "It has enabled us to develop better eco-systems for our projects, pushed us into new ways of thinking and made it easier for us to listen to each other."
As a result of the many benefits available to staff – including improvements to their health, social and cultural wellbeing – workers are incentivised to work harder and ensure they remain on the project.
The work site, "is like Disneyland" says one scaffolding supervisor. His team works harder and takes more pride in their work, he says, because they enjoy where they're working.
Learn more about the Fonterra approach: read the how-to guide.