
5 minute read
Automation on the rise as labour shortage bites
The number of enquiries about automation have increased significantly across both our New Zealand and Australian businesses as organisations look for solutions to staff shortages.
Businesses are facing inflation, high wage costs, closed borders and now, the reality that staff may have to isolate for long periods of time over the next few months. Automation is increasingly being seen as a way to reduce the impact of these external factors.
Advertisement
More businesses see automation as a way to increase efficiency and reduce their reliance on a shaky labour market – that trend is accelerating in a Covid environment.
Businesses are recognising that incorporating automation can also help protect their people and customers by freeing up space and reducing staff contact in warehouses.
While traditionally automation was the domain of large corporates, there is now increased interest from small to medium sized businesses who are able to access automation at a lower price point.
Small to medium
With work shortages forecast to continue and predictions that up to 30% of the workforce may have to isolate, businesses big and small are looking to automation, TMX New Zealand General Manager Caleb Nicolson says
businesses are also the ones who are hit hardest by labour shortages and increased labour costs, so for them, an investment in automation is one which can pay dividends long term.
Automation doesn’t always have to be on a grand scale. There are a range of solutions available, from simple technology such as leveraging your existing WMS with pick and put wall processes, to vertical and horizonal carousels to more advanced solutions such as automated storage and retrieval (ASRS) at the pallet, carton or unit level.
There are a lot more automation providers and local partners in New Zealand compared to 10 years ago. While steel and shipping challenges are causing challenges around pricing, we are definitely seeing an uptick in interest in automation.
The warehouse automation sector is a rapidly growing market, with Reports and Data last year reporting that the global logistics automation market will reach $120 billion USD by 2026.
Planning and implementation can take time and is dependent on the capacity and timelines of automation suppliers.
New Zealand organisations also need to consider the incredible volume of automation demand in North America and Europe.
Identifying what kind of automation solution would best fit your business can seem complex so I’d encourage anyone interested in automating to seek independent advice to help them navigate the process.

Changes to our Global Harmonisation System (GHS) chemical regime applying from 30 April 2021 require accurate and timely advice - non-compliance could prove costly.
Competent staff avoid expensive and sometimes confusing compliance advice, while enabling an effective response to chemical incidents, often without requiring emergency services.
Inspectors and certifiers with years of expertise warn of a declining national workplace chemical safety performance.
A crucial factor is the continuing loss of onsite chemical safety advice, primarily due to replacing flawed but effective mandatory Approved Handlers with whatever employers now deem sufficient.
A second major chemical incident in the same public facility is a timely reminder that safe chemical management is not receiving the attention it deserves. Competent staff are essential.
Onsite Responsible Care NZ (RCNZ) Competent Chemical Handler Certification courses are tailored to reflect your chemical inventory and enable compliance.
Upskill the last of your HSNO Approved Handlers, update Certified Handler requirements and successfully implement the updated Global Harmonisation System (GHS).
For struggling, noncompliant business operators who are attracting attention from enforcement agencies, practical onsite advice from Competent Chemical Handlers helps lessen the load on a diminishing number of Compliance Certifiers. It helps to ensure site chemical safety measures remain effective.
RCNZ Competent Chemical Handlers (CCH) are increasingly in demand, resulting from our popular ‘Walk and Talk’ site visit to assess actual chemical management performance, identifying the need for specialist training, throughout the product life cycle.
Chemical incidents now guarantee media attention, often sensationalising the incident by highlighting persons adversely affected by unwanted exposure to chemicals.
This can irretrievably damage reputations to both customers and suppliers, particularly if employers have not taken all practicable steps to safely manage their chemical inventory throughout their operations.
When chemicals do cause problems, employees, customers, WorkSafe inspectors, local authorities, health protection officers and emergency response organisations all benefit from the expertise and product safety information available 24/7 from 0800 CHEMCALL®, our industry’s unique, subscription based chemical emergency advisory service.
Supported by thousands of compliant Safety Data
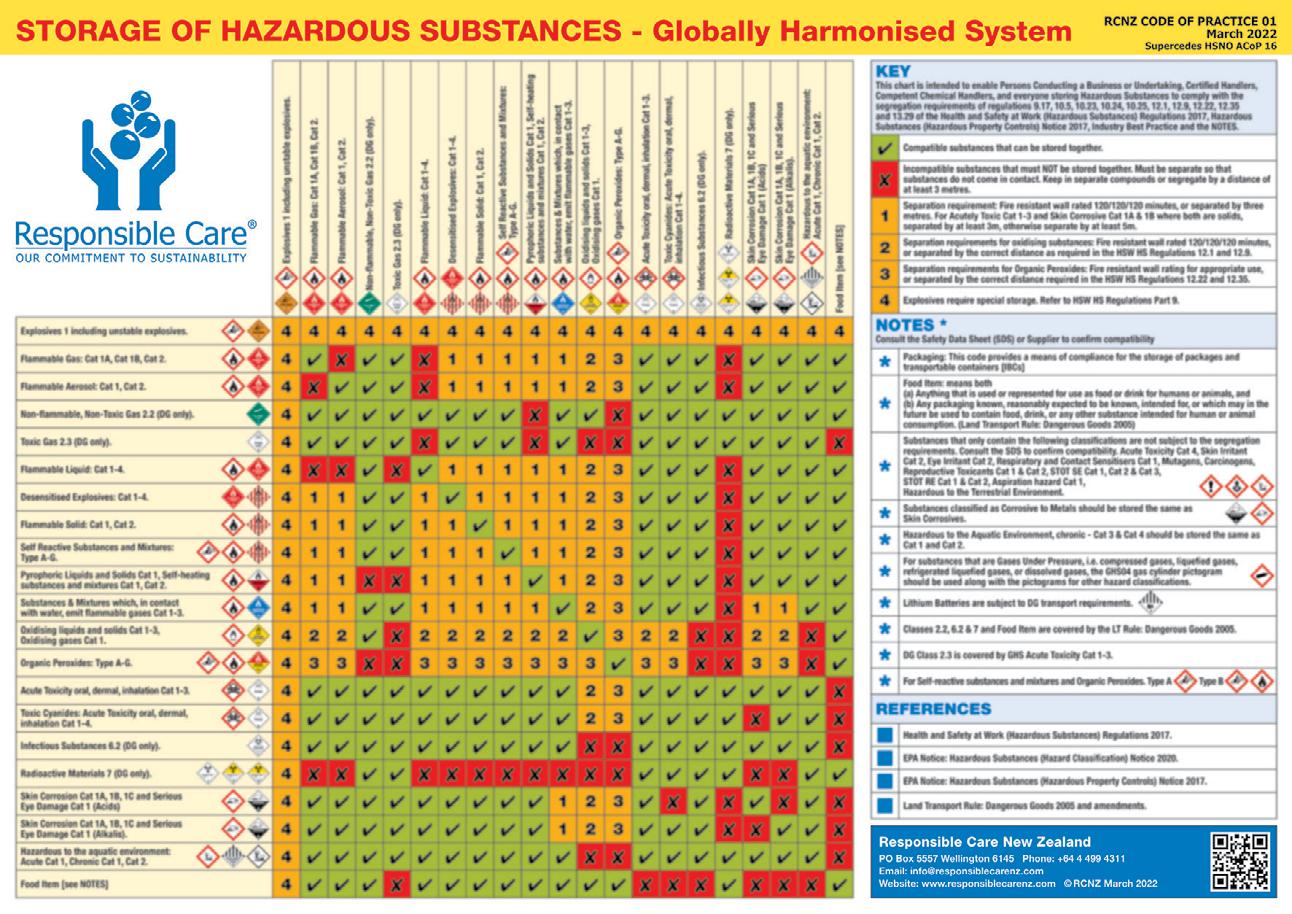
No better investment than chemical safety training DO YOU KNOW HOW Now is the time to schedule your customised Responsible Care NZ Competent Chemical Handler course, conveniently delivered on your own site TO SAFELY STORE
Essential compliance tools Chemicals Ensuring staff are competent to safely manage the harmful chemicals essential to your business includes your effective response to a chemical incident. To enable a smooth, cost-effective transition to and beyond compliance, you need compliance tools: - the updated RCNZ industry Codes of Practice reflecting our revised GHS chemical management system - your 24/7 CHEMCALL® emergency response subscription; and the all-important ‘how to’ advice arising from our popular site ‘walk and talk’ assessments
ORDER - replacing your Approved Handler with our Compe tent Chemical Handler -
THIS NEW certification
VERSON FROM OUR These are all cost-effective measures which add
WEBSITE value to your business. BULK DISCOUNTS Talk to us today about compliance tools, which conAVAILABLE firm you are a good employer, committed to safeguarding employees and our environment by safely managing your chemical inventory. OUR UPDATED WALLCHART HELPS EVERYONE
STORING OR HANDLING HAZARDOUS SUBSTANCES
Responsible Care NZ 04 499 4311 www.responsiblecarenz.com AND DANGEROUS GOODS. ENSURE YOU COMPLY WITH THE GHS SEGREGATION REQUIREMENTS
AND REGULATIONS, IN ACCORDANCE WITH
INDUSTRY BEST PRACTICE.
Sheets (SDS) combined with their collective industry expertise and local knowledge, CHEMCALL® WE HAVE YOU COVERED! BE COMPETENT, STAY COMPLIANT responders provide callers with comprehensive advice about how to safely manage Call 04 499 4311 the incident, safeguarding people and often avoiding business disruption.
www.responsiblecarenz.com
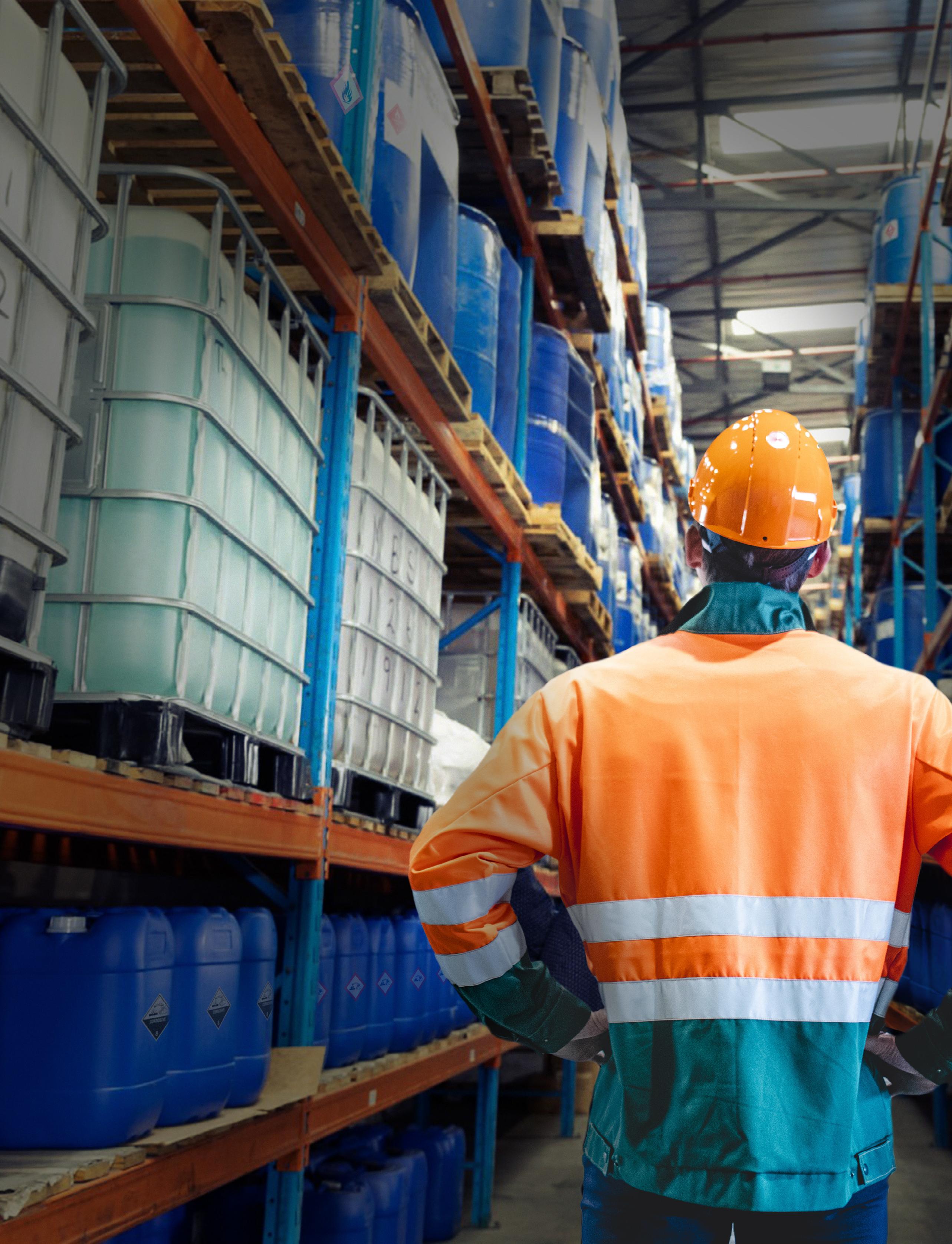