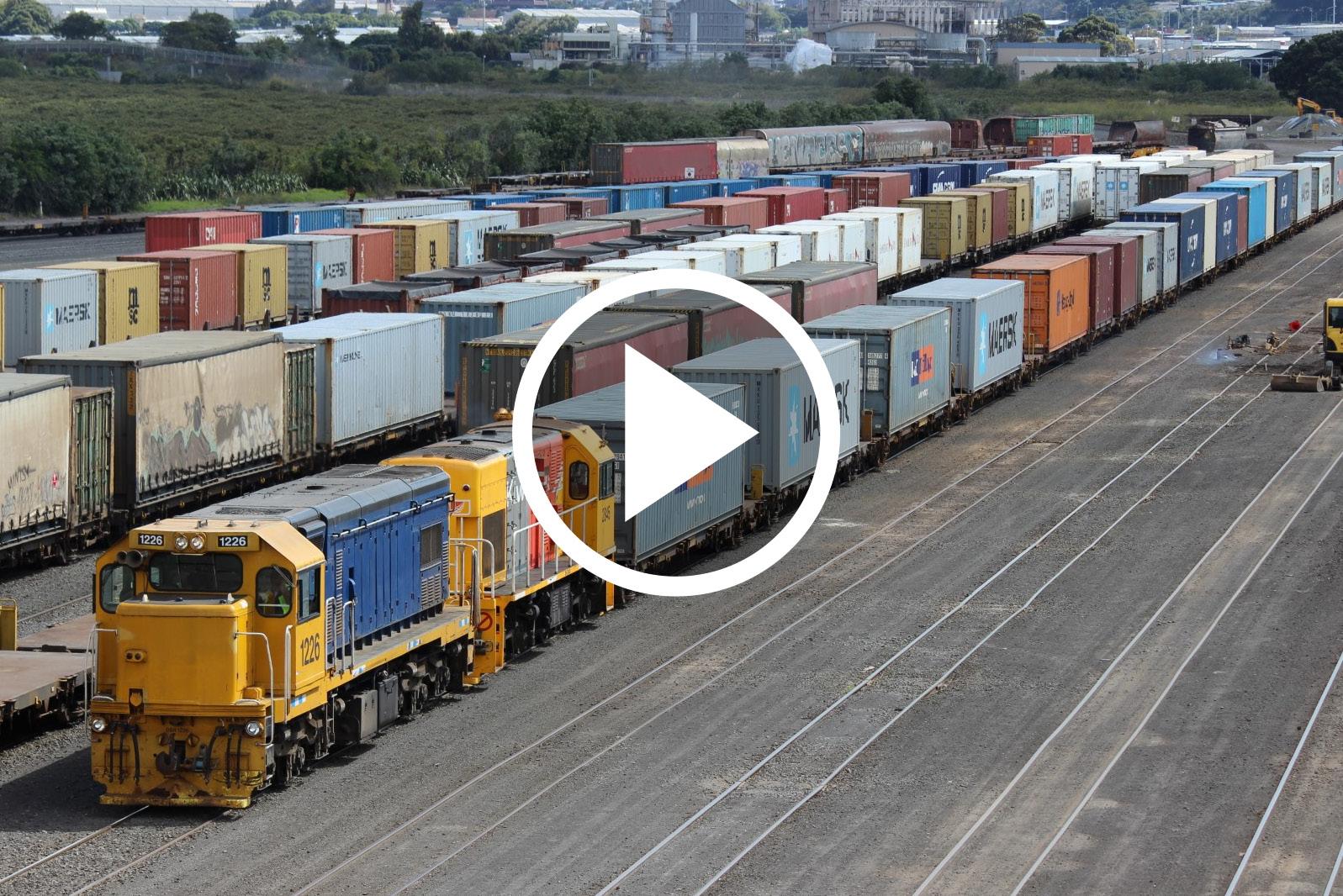
19 minute read
New national freight hub
August - September 2020 Regional Freight Hub unveiled
The preferred site for the 2.5 kilometre long inter-modal freight hub is between Palmerston North Airport and Bunnythorpe
Advertisement
The announcement of the preferred site for the Regional Freight Hub near Palmerston North is a significant milestone for this nationally important logistics project.
Palmerston North is a nationally strategic freight location, with domestic and export goods moving to the city from Auckland and the upper North Island, Taranaki, Hawkes Bay and Wellington.
Freight volumes are expected to increase

significantly in the coming decades and it is crucial that we have an integrated transport network to support this growth. Rail is an important part of this picture.
KiwiRail is progressing plans for a high-tech, intermodal freight hub which will help grow Palmerston North’s role as a critical freight distribution centre for the lower North Island.
It will support rail and road transport working together to meet the freight demand in the lower North Island, while boosting the regional economy.
The hub project is aligned with Horizon’s and Palmerston North City Council growth plans and it will tie in with other freight transport projects in the region.
KiwiRail has received investment through the Government’s Provincial Growth Fund to undertake the design (Master Plan) of the hub, have the land designated for rail use and commence purchasing the required land.
“The Regional Freight Hub will have huge longterm benefits for Palmerston North and the wider Manawatu – with the ability to attract two to four billion dollars of logistics investment into the area – while servicing the entire central and lower North Island.
It will be New Zealand’s first, truly world-class supply chain logistics precinct – including capacity for a log yard, bulk goods silo, container terminal (including free trade zone capability for exports), significant warehousing for freight partners, and KiwiRail’s operations.
Integrating all of these services, on this scale, creates efficiencies and cost savings that will set the standard for New Zealand
logistics and support the growth of Palmerston North as a distribution centre well into the future.
KiwiRail is a proud part of the Palmerston North community and he wants to ensure locals are involved as the design of the Hub is finalised.
The Hub is designed to enable our trains and heavy trucks to work efficiently together, while helping to get trucks out of already congested parts of Palmerston North city.
“I fully appreciate a project of this size represents a big change for the local community. That is why we want to work with the public as we finalise the design of the Hub to ensure we have the right mitigations in place and any environmental impacts are minimised.
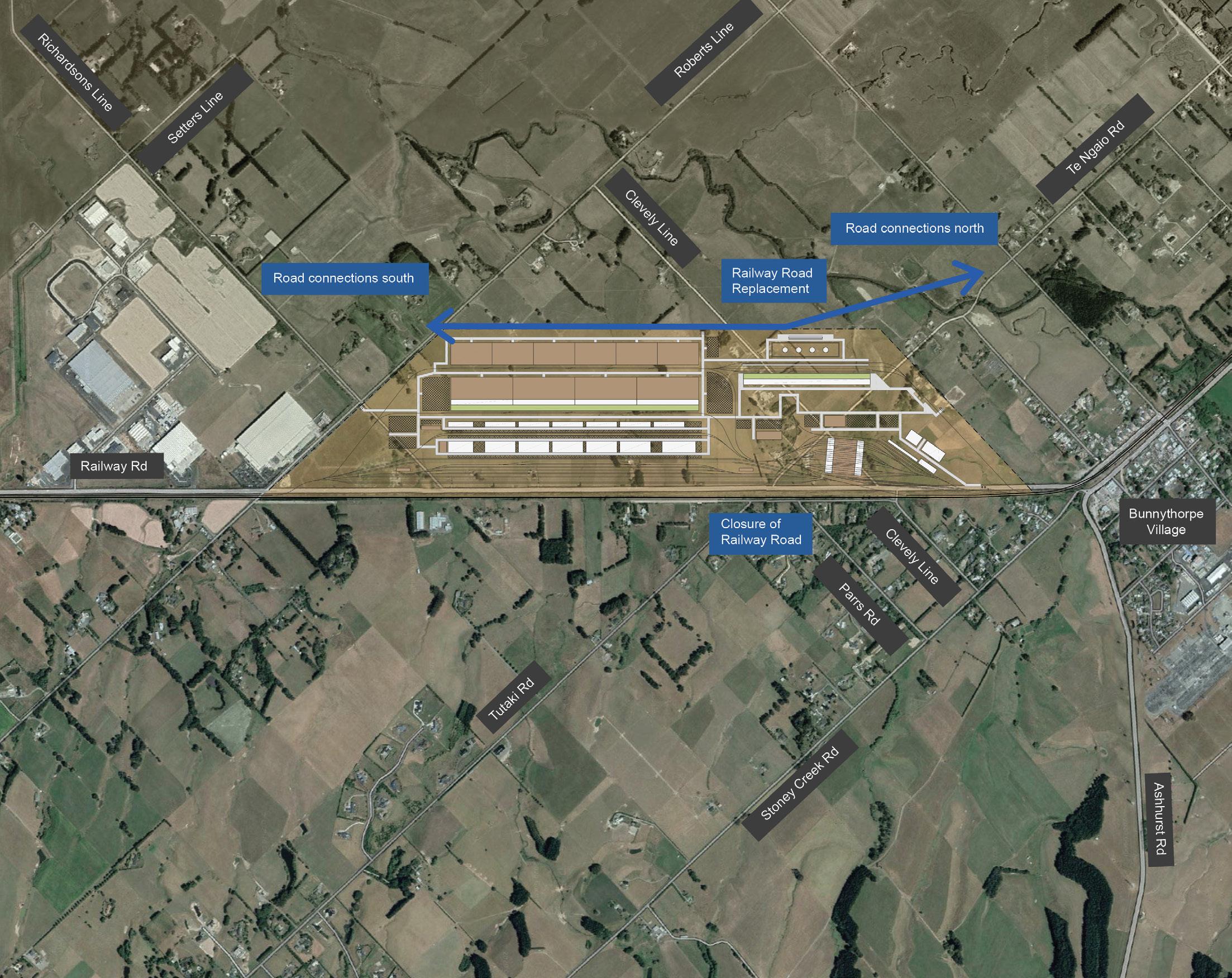
“KiwiRail has contacted affected landowners and today begins wider public consultation that will allow feedback on aspects of the Hub footprint, and the mitigations we will be developing. My team will also be holding public meetings in and around Palmerston North in the weeks ahead.
“The Regional Freight Hub is designed to meet the freight needs of the Manawatu and the surrounding regions for the next 100 years. Announcing the preferred site is a major milestone in this important regional project.”
Design, consenting, and acquisition of land for the Regional Freight Hub is funded through a $40 million investment from the Government’s Provincial Growth Fund.
Benefits
> Reducing transport emissions and road costs – every tonne of freight carried by rail has 66 per cent fewer carbon emissions than heavy road freight. Getting more freight on rail also reduces road maintenance costs and improves road safety.
> Taking pressure off city roads – situating the hub outside Palmerston North and integrating it with NZTA’s planned freight road and Manawatu Gorge road, will take freight traffic out of central Palmerston North and reduce congestion.
> Growing the logistics industry in Manawatu – KiwiRail will also work with key customers on major infrastructure requirements to encourage logistics and distribution businesses into the area, to help grow the sector and create more local jobs.
August - September 2020 Time to rethink our no compromise view of plastics
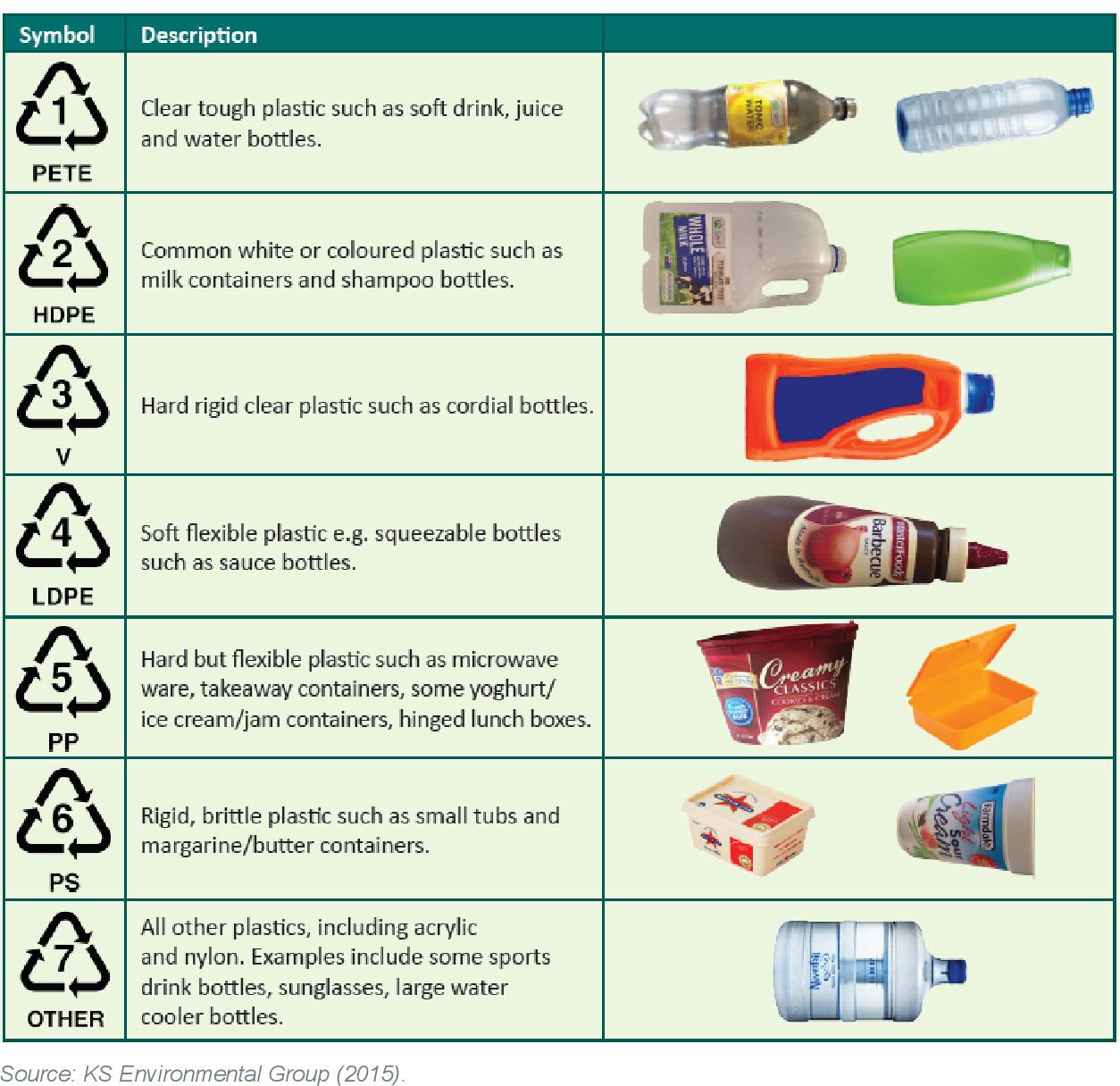
There is a future for plastic waste in road construction and maintenance among others
No doubt, waste plastic is a significant contributor to Australasian waste generation with way too much of it going to landfill.
But there is good argument also for including the use of plastics and composites in our circular economy ambitions.
For example, there is growing interest in exploring the viability of using recycled plastic in roads with advantages to the environmental and the development of sustainable
road making materials.
A report late last year by Austroads, a collective of Australian and New Zealand transport agencies, found that waste plastic can act as a partial aggregate replacement in bituminous mixes and a binder extender without having any significant influence on the properties of the asphalt mix.
While there may be environmental benefits associated with the use of recycled plastic, there are concerns regarding the potential health and safety hazards, mainly relating to the workers using the material.
Not all recycled plastics are suitable for bitumen modification at high temperatures. For example, heating poly-vinyl chloride (PVC) at high temperatures can result in dangerous chloride emissions. In addition, alternative In 2018, a series of road trials took place around Australia, mainly involving two proprietary products from suppliers MacRebur and Downer EDI. The report provides details and performance testing results reported by the manufacturers of these two products. It was found that soft plastics were the predominant material used in road trials in Australia. Soft plastics are those that can be scrunched into a ball such as plastic shopping bags, bread bags, cereal bags, bubble wrap, fruit and vegetable bags, packaging, netting.
materials such as reclaimed asphalt pavement, crumb rubber, glass and crushed concrete have been increasingly used for road pavement construction.
All of the commercial products available in the Australian and New Zealand market are made from different classes of plastics and little is known about the manufacturing process.
Since the Australian trials with recycled plastic only commenced in 2018, it is important that the performance of these pavements be monitored over the longer term, the report says
Still, if recycled plastic can be successfully incorporated into pavements it will enhance road-building material options and lessen the reliance on virgin non-renewable resources.
There will be environmental and, potentially, commercial benefits arising from reduced landfill and the benefits associated with a consistent and reliable source of recycled materials for the road building industry.
The use of recycled plastics will improve sustainability through climate and infrastructure resilience

benefits.
The most commonly recycled plastics are PET, HDPE, LDPE and PP which comprise more than 85 percent of all reprocessed Australian plastics.
The report suggests the use of HDPE, LDPE and polyethylene terephthalate (PET) are most prevalent for binder and asphalt modification. PET also has a high potential for reuse.
Some plastics are more difficult to reprocess owing to their chemical properties, resulting in increased proportions being sent to landfill.
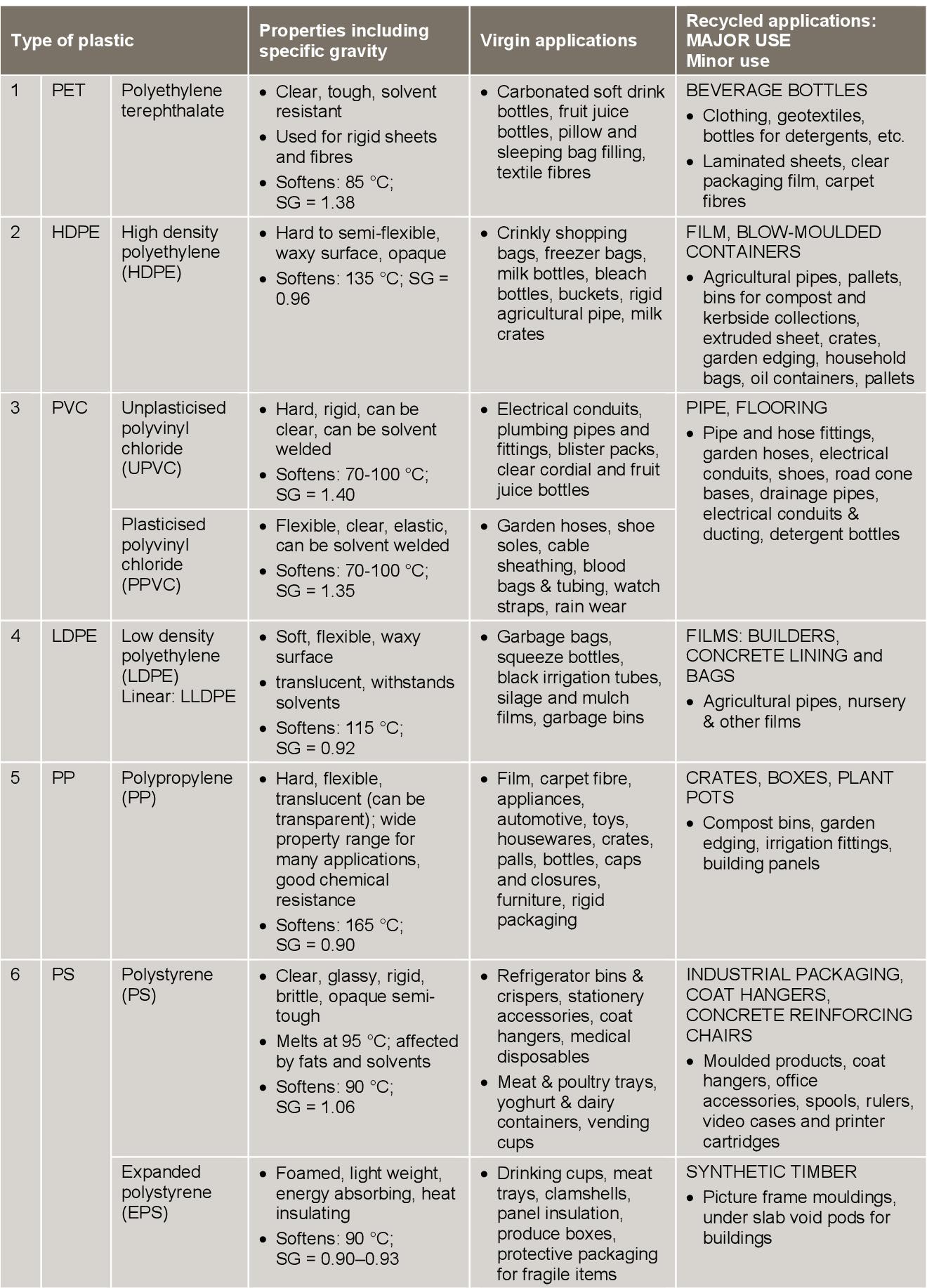
Three products developed and tested from simple ideas in India
In 2015, a commercial plastic waste recycling venture was released in Scotland.
The idea behind the product was inspired by practice in Southern India of retrieving waste plastic to fill up potholes.
Diesel was then poured over it and the mix set on fire until the plastic melted into the craters and formed a makeshift plastic pothole filler.
India has been using plastic in the construction of roads since the turn of the century, following a process developed by Rajagopalan Vasudevan, a chemistry professor at Thiagarajar College of Engineering in the South Indian state of Tamil Nadu.
Vasudevan's process involves scattering shredded plastic over hot stones

to form a thin, primer coat. This is then added to bitumen, resulting in a strong bond.
To date, this method has been used on an estimated 100,000 kilometers of roads across India.
In late 2015, the Indian road transport ministry made it mandatory to construct roads using waste plastic in most urban areas.
MacRebur has now produced three products (MR6, MR8 and MR10) made from domestic and industrial waste plastic.
These products have a melting point lower than that of typical asphalt and binder production temperatures, enabling it to melt into the binder to extend and modify it.
These three products come in a different colours and forms:
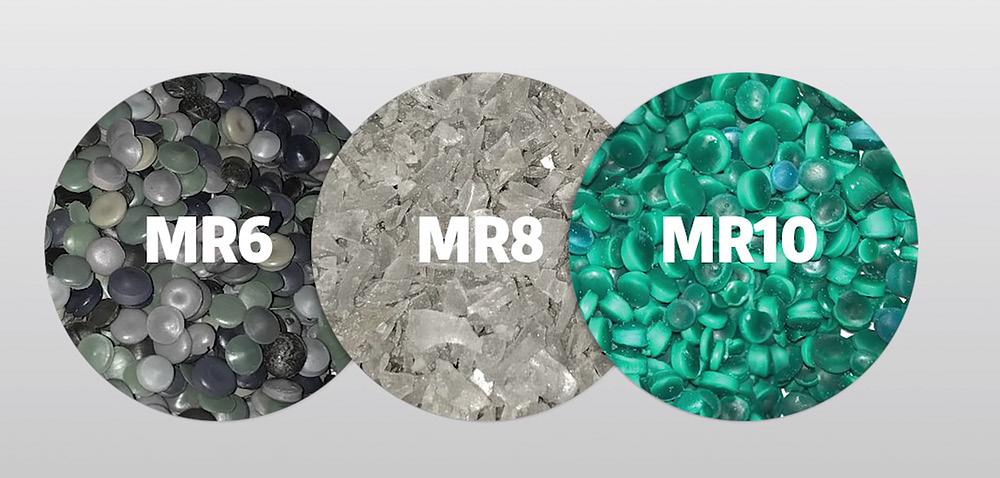
• MR6 – comes in pellet form and is intended to be incorporated directly into the asphalt production plant. It modifies the asphalt by increasing its tensile strength and the softening point. It is flexible but rigid and unbreakable.
It is reported to work well in hot conditions (like Australia) as it has a melting point of 110 °C. • MR8 – a shredded plastic. It was developed to be a more economical bitumen extender without any performance enhancement. It is a cheaper version of MR6. • MR10 – comes in pellet form (looks similar to MR6). It was developed to provide a more crack-resistant binder. In contrast to MR6, it is flexible in a solid form - it rebounds when flexed.
It was reported that it worked well in colder climates such as the UK, Canada and Russia.
In 2017, Cumbria County Council was the first highway authority in the UK to trial MacRebur’s plastic-based material.
An equivalent of 500,000 plastic bottles and over 800,000 one-time-use plastic bags were recycled for a 400m long by 20m wide strip of road.
MacRebur says the company aims to use a ratio of 50/50 domestic and commercial waste for local road applications.
In Australia, MacRebur performed a road trial for Brisbane in 2018.
There is limited information about this trial in the public domain although it is understood that a series of performance tests has been conducted by Brisbane City Council’s Pavement Division in association with the University of Sunshine Coast, Boral and Fulton Hogan.
The proof is in the plastic
Testing was undertaken to compare the behaviour of a binder that had been supplemented with the MacRebur products -- MR6, MR8 and MR10. When 4.5 percent of MR6 was added to the C170 binder, the properties were similar to a A35P bitumen with good torsional recovery and an increased softening point to about 78 degrees celsius. This was in line MacRebur’s claims that MR6 mimics a plastomeric polymer and MR10 an elastomeric polymer. However, the MR10 blend was much stiffer, which contradicted the claim. There was no significant difference in the properties when the MR8 was added to the C170 bitumen. Six per cent (by mass of bitumen) of MR6 and MR10 was added to the C320 bitumen through a batch plant. Another two batches of asphalt were prepared which were C320 and Multigrade M1000 control mixes. The deformation resistance of the MR6 mix was superior to the M1000 mix. However, the tensile strength of both the MR6 and MR10 mixes dropped drastically when the mix was exposed to moisture. The addition of MR6 to the C320 mix resulted in an increase in stiffness similar to the M1000 mix, but very little difference with the MR10 mix. However, the fatigue results for the MR6 were poor, suggesting no improvement to the life cycle of the asphalt. The fatigue life of the MR10 mix, on the other hand, was slightly higher but minimal compared to the results for the C320 and M1000 mixes. It was suggested that this behaviour could be due to the poor digestion of the waste plastic material in the samples, as some pellets were still visible. An asphalt mix containing British pen grade 40/60 bitumen (equivalent to C320) modified with 6 percent MR6, MR8 and MR10 was undertaken. Testing was conducted according to British Standard EN 13108-5:2016 and it was found that the addition of all three products resulted in an improvement in deformation resistance and overall structural contribution. MR10 had the highest stiffness modulus, whilst MR6 had the most significant effect on asphalt fracture resistance and deformation resistance. This contrasted with the original intention of MR6 to exhibit plastomeric properties rather than MR10. The tests also suggested that the addition of MR6 and MR10 resulted in improved fracture toughness and fatigue life.
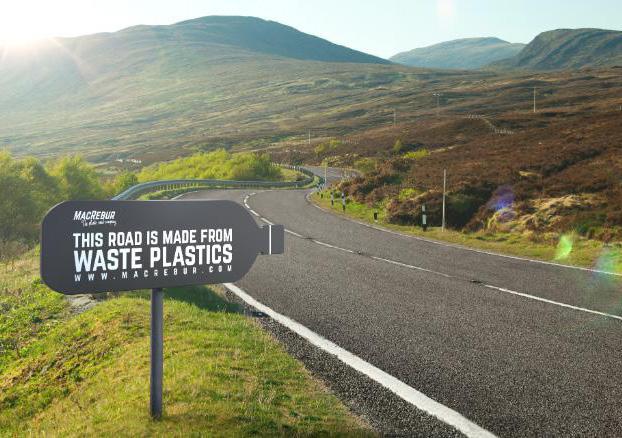
New ideas with soft plastics and glass

Downers launched its soft-plastic trial road using Reconophalt in Craigieburn, north of Melbourne in 2018
Downer, Hume City facilities combined with the It is not limited to only forms the soft plastics Council, Close the ability of recycling comusing recently banned collected by the REDcycle Loop, Sustainability panies such as Close the plastic bags. Sustainprogram along with waste Victoria and RED Group Loop allowed for the use ability Victoria estimates toner collected through worked in partnership to of materials such as glass that 170,000 tonnes of soft programs such as Cartridgbuild the first ever Austraand printer cartridge toner plastic waste is created in es 4 Planet Ark to develop lian road with soft plastics, to manufacture asphalt, Victoria each year, with only an asphalt additive called glass and toner. effectively keeping it out of 17,000 tonnes or 10 percent TonerPlas.
The same day, the project Australia’s waste stream. recovered TonerPlas is then mixed was the first to be funded Through the REDcycle The programme is not with glass and Reclaimed under the A$2.5 million program (hosted by the limited to only using reAsphalt Pavement (RAP) Resource Recovery Market RED Group), unwanted cently banned plastic bags. to produce the final proDevelopment Programme plastic shopping bags and Sustainability Victoria estiprietary product named of the Australian state to other soft plastics such mates that 170,000 tonnes Reconophalt. support market developas food packaging were of soft plastic waste is creDowner commissioned an ment for recovered resourccollected from bins placed ated in Victoria each year, internal research and develes materials. at major supermarkets to be with only 17,000 tonnes or opment program to assess
Downer’s expertise in re-used in an environmen10 percent recovered. product performance, occubuilding infrastructure and tally responsible manner. Close the Loop transpational health and safety
risks and scalability in a real-world application.
There is no risk of releasing microplastics into the environment. The asphalt is made up of 95 percent aggregate and five percent bituminous binder.
The bituminous binder is the ‘glue’ that bonds and waterproofs the aggregates. The soft plastics additive melts and becomes part of the bituminous binder.
Because of this process it is not possible for the additive to separate out creating microplastics.
This method involves returning plastic waste to its original polymer state which is used as a substitute for virgin petrochemical products which are normally mined for use in road construction.
The roads industry has used virgin polymers since the 1990s and this soft plastics initiative follows a similar vein; where asphalt manufactures modify a road construction material to improve long term performance.
The sustainable, cost-competitive road has a 65 per cent improvement in fatigue life and a superior resistance to deformation allowing it to better handle heavy vehicle traffic.
When scaled up from the Melbourne trial, every kilometre of two-lane road paved with plastic and glass modified asphalt would use about 530,000 recycled plastic bags and packaging, 170,000 recycled glass bottles, toner from 12,500 used printer cartridges, 130 tonnes of reclaimed road (asphalt) re-used with the inclusion of 20 percent RAP.
It is not limited to only using recently banned plastic bags. Sustainability Victoria estimates that 170,000 tonnes of soft plastic waste is created in
New Zealand Experience
Fulton Hogan, in partnership with Christchurch Airport, conducted a trial with recycled plastic modified asphalt mix. PlastiPhalt®, which was developed by Fulton Hogan and used to pave half of Christchurch Airport’s fire station. PlastiPhalt® is made from used oil containers collected through Fulton Hogan’s Recovering Oil Saves the Environment (ROSE) scheme. Previously, these containers could not be reused due to the residual oil left on the inner surface. In 2014, the company began its research program by shredding these plastic containers to an ideal size before incorporating them into an asphalt-grade bitumen. PlastiPhalt® is used to modify the asphalt mix required to meet the performance requirements of any given site. Once it is blended and ready to be used, it is sampled and laboratory tested to ensure the level of modification is achieved. Additional plastic material can be added to fine-tune the mix, if required.
Victoria each year, with only 17,000 tonnes or 10 percent recovered.
However, it costs 2-5 percent more than standard asphalt due to the additive production and transport costs. Despite this, it was claimed that it was still 25% cheaper than PMB-modified.
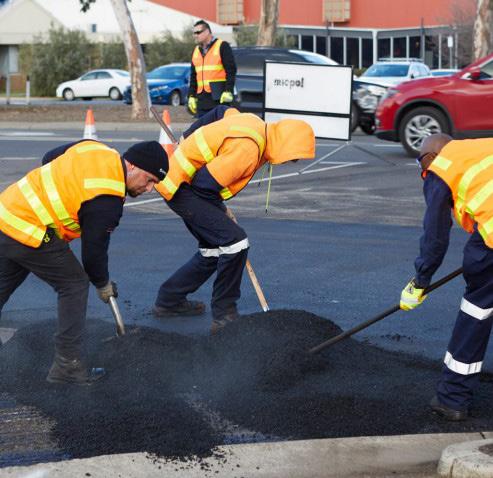
Alex Fraser has recently resurfaced two municipal streets in the City of Yarra, Victoria with its proprietary product, PolyPaveTM. The resurfacing of Stanley and Margaret Streets in Richmond was reported to contain recycled glass, asphalt and HDPE plastic (hard plastic/bottles), amounting to almost 100 tonnes of recycled waste. The city has re-engaged Alex Fraser to repair and repave several more streets.
August - September 2020 Place your order now for the recycled plastic modular road
Industrial manufacture of the PlasticRoad will start in the first quarter of 2021
In September 2018, a 30-metre-long bicycle path called PlasticRoad, composed of recycled plastics, was installed in Zwolle, Netherlands. The innovation was the result of collaboration between three companies, an engineering firm KWS (a VolkerWessels company), Wavin (a subsidiary of the plastic piping company Mexicham), and an energy company Total. The first pilot trial in Zwolle involved the use of 70 percent of recycled plastic, including plastic bottles, beer cups, cosmetic packaging, plastic furniture and the like. Besides the effective use of waste plastic that would otherwise have been incinerated or dumped into landfill, the construction of the path was fast and easy. This was because the road design incorporated prefabricated and lightweight modular pieces put together like Lego. The path was installed in a matter of days, thus reducing of the normal down

time and traffic obstruction often related to traditional road construction methods. The modular design also resulted in a reduction of in the levels of greenhouse gas emissions typically associated with conventional road construction methods. PlasticRoad is hollow. As a result, it offers many benefits, including the ability to cater for utility services such as pipelines and cables for high-speed internet, and the storage of rainwater to mitigate flooding. It was reported that this concept offers opportunities for further innovation such as solar roads, light poles and traffic loop sensors. A second pilot trial was established by the same partnership in November 2018 in the town of Giethoorn. Similar to the first trial, this was also a 30-metre long bicycle track but smaller and smaller and lighter equipment was used to ‘pick and drop’ the fabricated pieces. A fter more than 18 months of testing, learning and continued development into a design suited for industrial production, the circular economy technology known as PlasticRoad is now ready for commercial launch.
At the time of their installation in 2018, both test roads in the Netherlands were fitted with sensors that enabled 24/7 monitoring of their use and behaviour.
It has become clear from practical tests and data that the PlasticRoad is also a match for heavier loads like garbage trucks and maintenance vehicles.
Further improvements to the design mean that the definite version will be more rugged and 2.5 times stron
ger than the test sections.
This makes the PlasticRoad suited at this stage for applications like parking lots, and the first pilot project for this application is underway.
The eventual realisation of the first PlasticRoad for cars and other road traffic has become more likely than ever, the project team says.
“The PlasticRoad has proven able to handle heavy loads and offers an effective solution for water management with heavy precipitation and periods of drought.
It holds up under a wide range of conditions and the group behind the PlasticRoad initiative are “exceptionally satisfied with the results of the pilot project and look forward to seeing the first PlasticRoad element roll off the production line.”
Marcel Jager and Anne Koudstaal of the PlasticRoad project team say “ we have proven that our ground-breaking circular concept – a prefab road
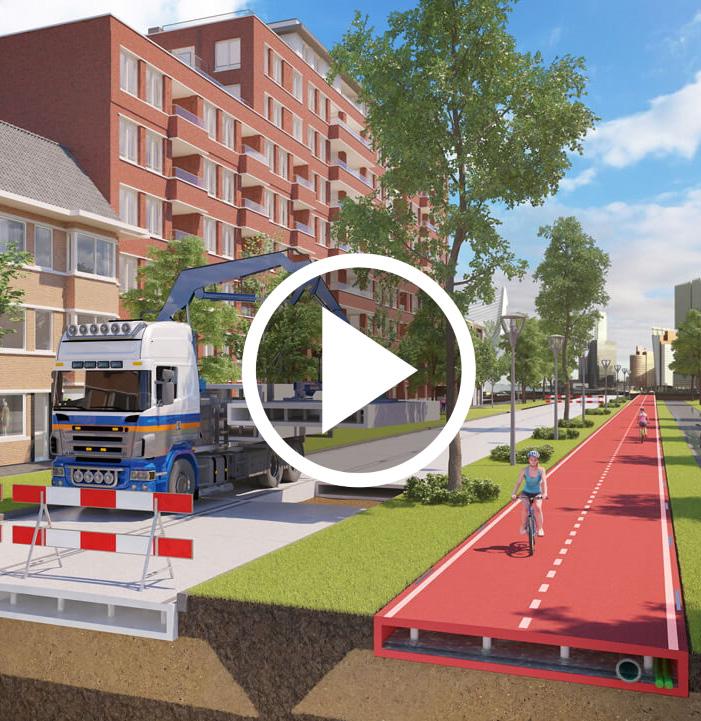
based on recycled plastic – is feasible in practice.
“An initiative that started in 2018 with two pilot projects is now ready for industrial production – a feat that we are incredibly proud of.”
Each pilot contained about 1000 kg of recycled plastics, the equivalent of 218,000 plastic cups.
The pilot version of the PlasticRoad has already cut carbon emissions by between some 50 percent and 70 percent compared to conventional bike paths made from asphalt or concrete.
The group says this percentage stands to increase even further when the finalised design is taken into industrial production in 2021.
The circular characteristics of the finalised product have been optimised by further developing the road’s structural design – an achievement that has been confirmed by an independent circular audit.
Climate-adaptive infrastructure
Extreme precipitation and heavy showers are becoming increasingly common as a consequence of climate change.
In many cases, current infrastructure struggles to accommodate all the excess water – with flooded streets as the result.
The hollow sections under the PlasticRoad’s surface are intended to quickly store this sudden precipitation and then gradually allow it to infiltrate the subsoil.
This climate-adaptive solution turns out to work very well in practice.
“Before the two test sections were installed, both locations used to be affected by water storage problems,” the group says.
“But with PlasticRoad, even the heaviest showers proved to have a minimal impact on local storage capacity.
“The highest water level measured within the PlasticRoad was only 48 percent of the available storage capacity at one test site.
The water subsequently infiltrates the subsoil within the next two days – exactly as predicted.

The project looks certain to encounter strong interest from the market. Based on the convincing results recorded in the pilot projects, the PlasticRoad team are taking he production line into operation. The PlasticRoad is available for orders immediately with initial deliveries in the first quarter of 2021. Working together with clients and contractors, PlasticRoad will be launching a variety of applications that can help make cities and towns climate-adaptive and carbon-neutral. For example, the PlasticRoad planning includes bike paths, parking lots, pavements and schoolyards. The team will initially be focusing on clients in the Netherlands and neighbouring countries, after which they expect to scale up to markets in other parts of the world.
www.plasticroad.eu
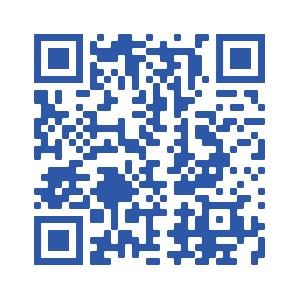