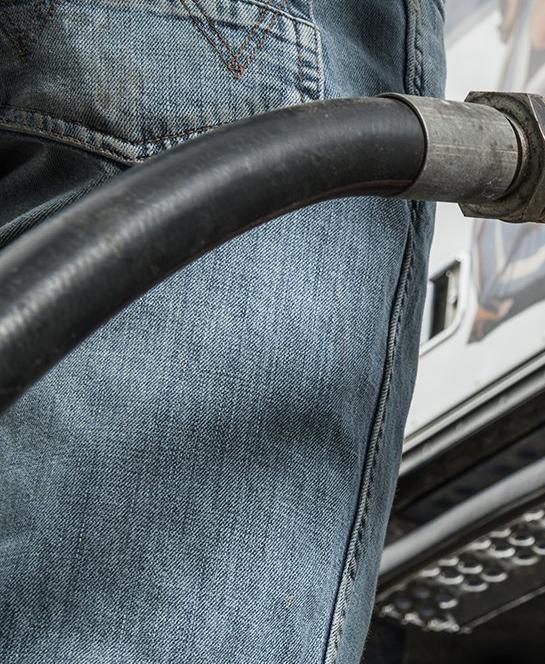
7 minute read
Has your fuel gone off?
october 2021 - January 2022 Is your fuel bugged?
Diesel is an organic compound, and like a slice of bread, it can go mouldy, which can pose some serious safety risks, says David Armitage from Conidia Bioscience
Advertisement
Mould, a form of fungus, yeasts and bacteria can grow in fuel over time. Termed ‘microbiological contamination’, this threat is greater now as the global pandemic has created a reduction in fuel turnover. As fuel is stored and backed up in the supply chain for longer, road haulage and commercial forecourt operations need to take extra care to keep this contamination in check.
While consuming mouldy bread may not be an appealing option, it will not actually do you any harm. Microbiological contamination in fuel supplies, on the other hand, has much more serious consequences on fuel systems and storage tanks.
As microbes multiply in the fuel, they can form a biomass layer consisting of billions of organisms. This biomass can block filters, increase injector wear, and even corrode tanks with the organic acid it produces.
Worst of all, microbiological contamination can be passed along the fuel supply chain, whether from pipeline to storage tank or fuelling truck to retail forecourt. This means that even if a depot is experiencing high fuel turnover, delivering food, Amazon boxes or other supplies, the overall slump in global fuel consumption across all modes of transport means contamination from the fuel supply chain could still be an issue.
Rachel Harrison at Fueltek Ltd says the ‘diesel bug’ is something that anyone storing fuel in bulk is generally aware of, but maybe not of the increasing risks it poses.
What does this mean for managers?
No one wants to add unnecessary activity or cost to operations, but managers need a smart way to make smart decisions to help prevent the potential of significant remedial costs due to damage caused by microbiological contamination. But why does microbiological contamination occur?
Fuel inherently contains water in some form as soon making it impossible to keep it completely out of the supply chain.
Many companies will have sophisticated wet stock management with water sensory equipment, but even the smallest amount of water (far from the levels these mechanisms can detect) can do damage.
Couple the presence of even a small amount of water with the use of more
While there is no regulation to test fuel supplies at garage forecourts or refuelling hubs, the risks contamination poses, especially at a time when overall throughput in the supply chain is lower, are significant
as it leaves the sterile environment of the refinery. Water can be picked up at any point in the supply chain; in pipelines, storage tanks and fuelling trucks. It can also naturally enter storage tanks due to condensation, sustainable and environmentally friendly fuels, which has led to a reduction in sulphur and addition of biofuels, and the microbiological problem gets worse.
While steps can be taken, such as cleaning fuel tanks or dosing them with biocides if the tank is not contaminated, this adds a significant cost to operations. A regular, on-site testing regime using lateral flow devices, however, offers a quick, easy, and low-cost way to ascertain whether action needs to be taken.
Immunoassay antibody test kits are a proven technology to give accurate levels of microorganism activity in a fuel source. Testing can be carried out on site without the need for in-depth training or investment in sophisticated test readers or other high-tech equipment.
The kits require no special handling, storage or disposal and are safe and easy to use, providing quick results without the need to send samples away for testing. The very nature of how the test works means that there is minimal risk of cross-contamination (unlike if sam-
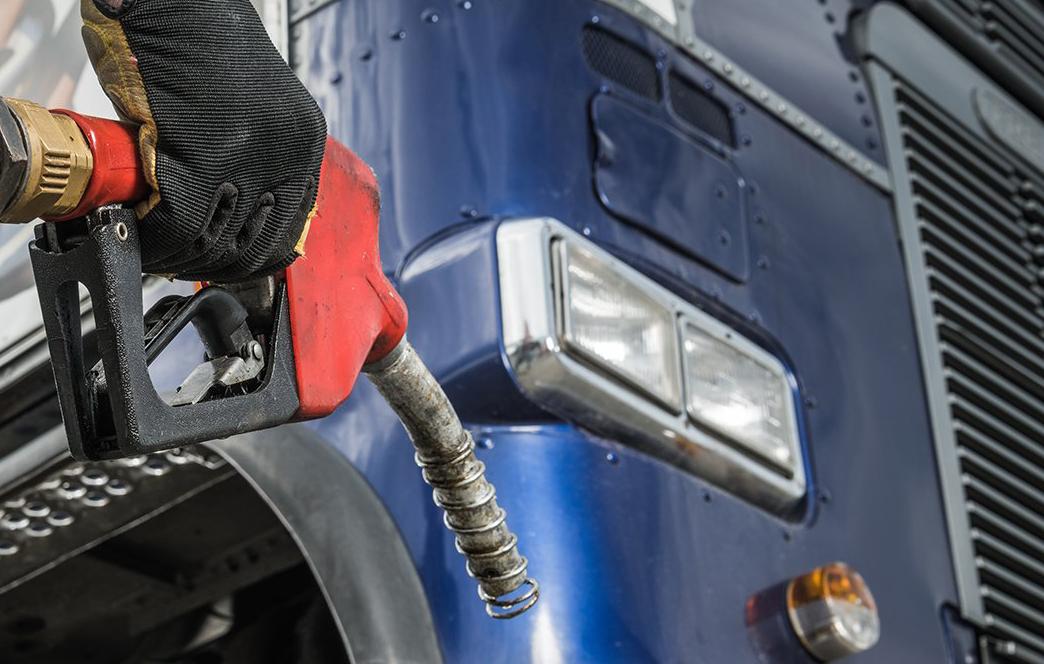
ples are sent away to a lab), results are accurate and completely reliable, and site managers can take control in ensuring they will not be caught out by undetected contamination.
Compared with other testing methods or technology to prevent a build-up of microbes, antibody test kits are one of the lowest cost options. With no initial capital investment required, the cost of a kit provides an almost immediate return on investment if it prevents just one unnecessary storage tank clean or biocide dosing or averts an incident where an engine is damaged by the microbiological contamination.
Antibody fuel test kits have been used for many years in the aviation industry, where fuel testing has long been a standard procedure, and other bulk users of diesel fuels, such as marine and power generation have followed suit.
Most people are aware of the technology, which is widely used in the medical industry, as it is the principal test for the COVID-19 infection. While there is no regulation or mandate to test fuel supplies at garage forecourts or at road haulage refuelling hubs, the risks contamination poses, especially at a time when overall throughput in the supply chain is lower, are significant.
A good testing regime
Microbiological contamination can occur at any stage in the fuel supply chain. In any testing process, some important procedures should be followed: Sampling points should be wiped clean with at least 70% alcohol solution or wipe; sampling equipment should be cleaned after each sample is taken, and, ideally, a new sampling container should be used for each sample.
If a site begins to use antibody test kits to periodically test fuel supplies, the frequency of this testing can be adjusted as historical results are catalogued.
For companies that employ fuel maintenance contractors, fuel testing is not assured and the number of cases in the road transport sector of equipment being damaged because of contaminated fuel is increasing.
Fueltek’s Rachel Harrison says a regime of good fuel husbandry and management should be in place, and antibody test kits are a useful, inexpensive tool to support this.
If left unchecked, microbiological contamination can have serious impact on machinery and drivers. Indeed, the damage it can cause to diesel engines, fuel tanks, pumps and other machinery should not be underestimated.
The contamination can be transferred to most middle distillate fuels and will grow if left undetected. Water is the fuel’s worst enemy, and it is good practice to periodically remove as much water as possible from supplies, but testing is the only way to be sure that contamination is not being left unchecked and machinery is not being damaged. This testing can be carried out by a single person and does not need to be an onerous or expensive task.
Antibody test kits offer a simple, quick, cost-effective way of checking fuel supplies on site without the need for specialised skills or procedures. For facility or fleet managers, these kits could lower maintenance costs and reduce risks to day-to-day operations. For all drivers, the cost of avoiding catastrophic engine failure on our highways certainly goes way beyond the cost of a lateral flow test kit.
3 No better investment than chemical safety training 4 Has your fuel gone off? 8 Toxic fumigant banned 10 Bastion NZ launch Industrial glove range 12 Remote working putting organisations at risk 13 Critical infrastructure vulnerable to hackers 15 Industry leader in soft fall protection on construction sites 16 Unlearning misguided muscle training 18 Radio technology keeps workers safe and compliant 19 Safety app a crucial element in building site safety 20 Tips and myths around dogs 22 Priming your business for post-lockdown recovery 24 Six strategies to manage cash flow during Covid 26 Surviving as a modern business 28 Chemical safety relies on meaningful cooperation 30 Homebrew 1080 poison hospitalises worker 31 Is standardised training the way forward? 32 The SME business dilemma 39 Latest lockdown puts ongoing strain on construction 41 AC Filter - an engineered solution protecting worker health 42 Multi-purpose, safer, faster telehandlers increase productivity 44 Australian construction industry cries out for reform 46 In search of the perfect surface - contractor invents new earth compactor 48 Immigration policies hindering construction sector 51 How scalable data centres help Mainfreight’s vision 52 Transmission Gully - what went wrong? 56 The New Zealand Upgrade Programme cost blowout 60 The fight for common sense and a reasoned debate 65 Site Safe Awards finalists announced 66 Facilities management with personal service 68 Where is housing most affordable in New Zealand? 70 Tax changes threaten rental market 72 New Zealand's housing crisis a breach of human rights 76 3D-printed housing 79 China builds apartment block in a day 80 Kiwi Property kick starts build-to-rent in New Zealand 82 Wrong name, right product why build-to-rent is struggling
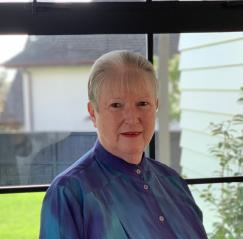
Published by Media Solutions Ltd PO Box 503, Whangaparaoa Auckland 0943 09 428 7456
Original material published online and in this magazine is copyright, but may be reproduced providing permission is obtained from the editor and acknowledgement given to Media Solutions. Opinions expressed are those of the authors and may not necessarily be those of Media Solutions Ltd. Sales Manager Margie Lindsay +64 22 317 8170 margie@infrastructurebuild.com Editor Michael Curreen +64 21 029 20234 michael@infrastructurebuild.com Get our FREE newsletter emailed to you each week
eepurl.com/dp33ez

