
24 minute read
Your responsibilities as a PCBU
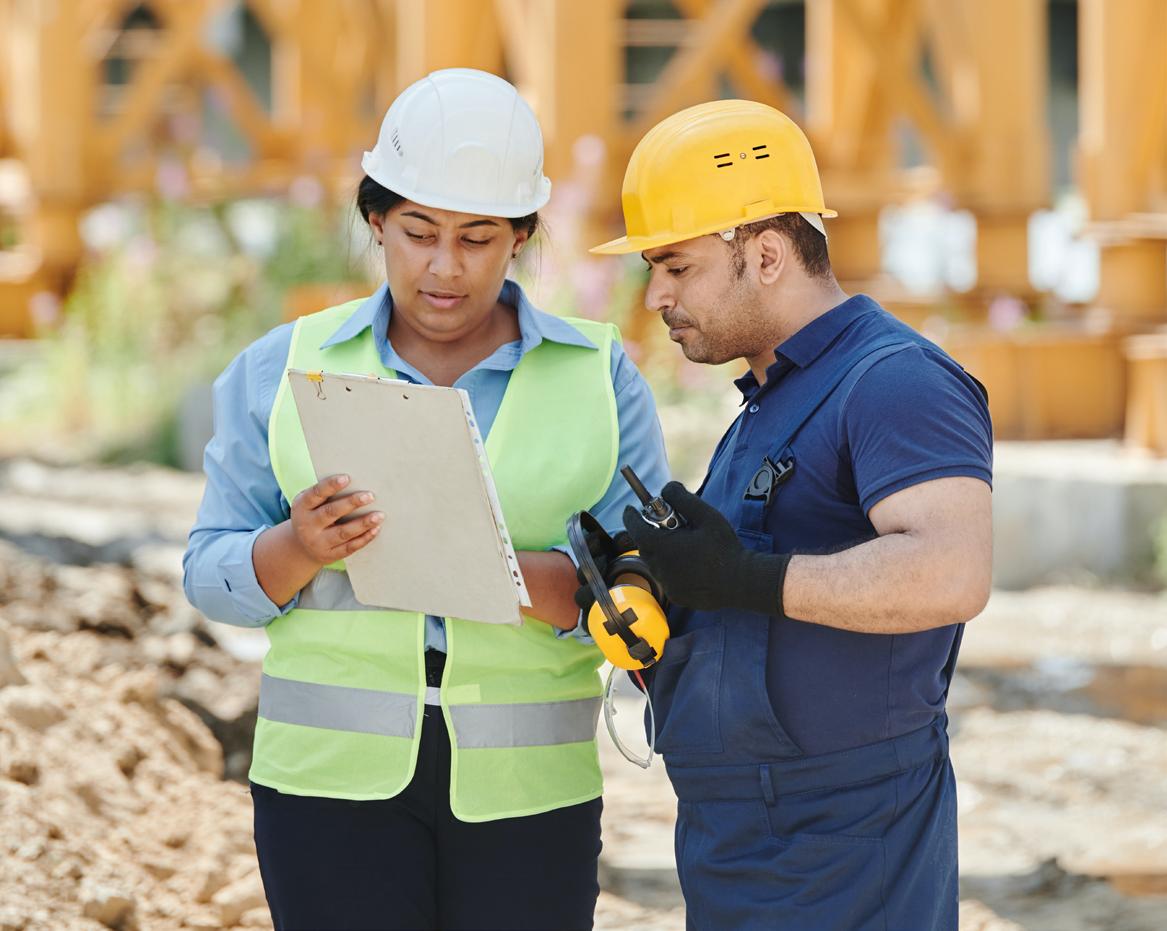
A PCBU means a Person Conducting a Business or Undertaking. Most New Zealand businesses, whether large corporates, sole traders, or self-employed, are classed as PCBUs.
Advertisement

A PCBU must, so far as is reasonably practicable, provide and maintain a work environment that is without health and safety risks. The work environment includes:
• the physical work environment, including lighting, ventilation, dust, heat and noise • the psychological work environment, including overcrowding, deadlines, work arrangements (eg the effects of shift-work and overtime arrangements) and impairments that affect a person’s behaviour, such as work-related stress and fatigue, and drugs and alcohol.
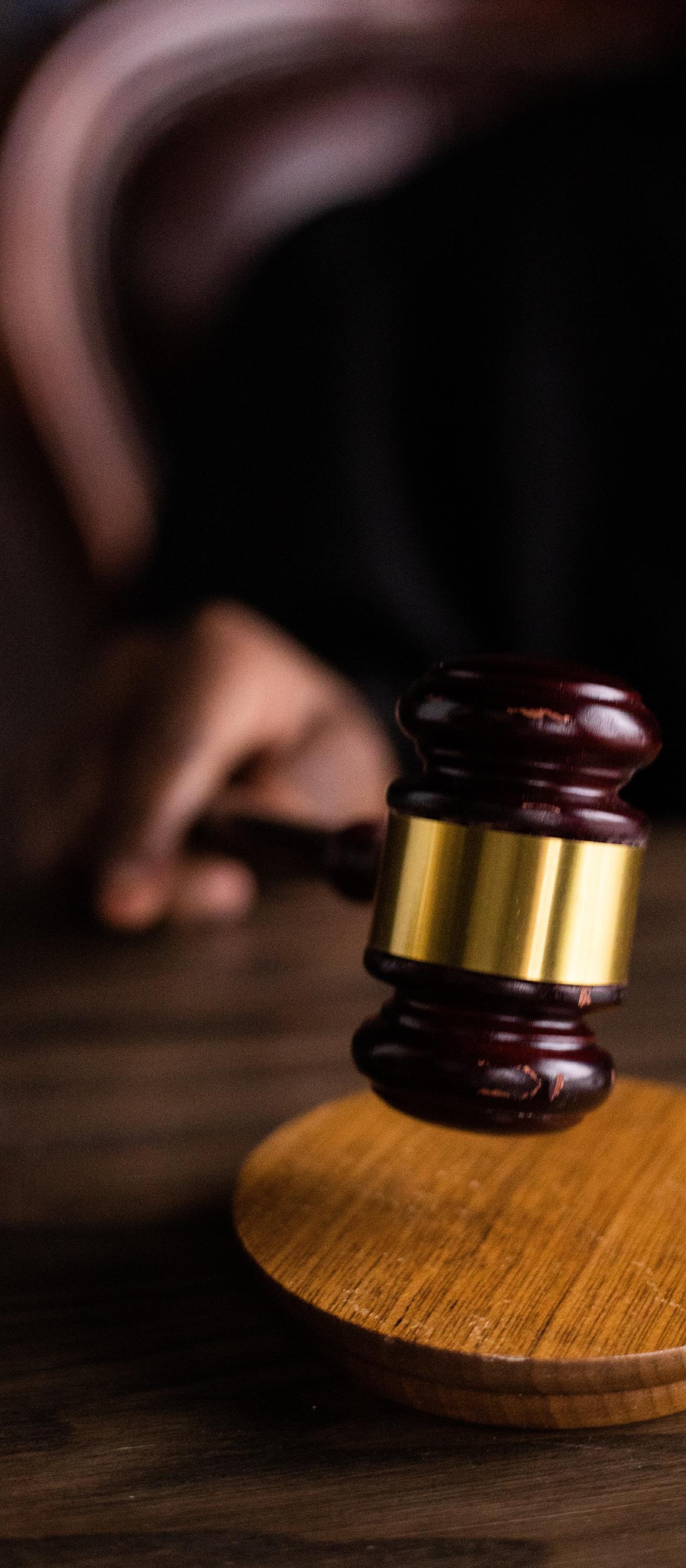
PCBUs are responsible for providing and maintaining safe plant and structures. This includes machinery, vehicles, vessels, aircraft, equipment (including personal protective equipment), appliances, containers, implements, tools, buildings, masts, towers, frameworks, pipelines, quarries, bridges, underground works (including shafts and tunnels) and any component of one of these items or anything fitted or connected to one of these items. PCBUs must also ensure the safe use, handling and storage of plant, structures and substances.
Providing safe systems of work is also a PCBU’s responsibility, as is providing any information, training, instruction or supervision that is necessary to protect all persons from risks to their health and safety which may arise from the work of the business.
It is also a PCBU’s job to monitor the health of workers and the conditions of the workplace.

Another responsibility of a PCBU is to provide adequate facilities for the welfare of workers when doing work for the business, including ensuring access to those facilities. This also applies to providing healthy and safe worker accommodation when appropriate.
Click here for more information.
PCBUs that fail to meet their health and safety obligations are putting people at risk and can face prosecution. The following are recent examples of health and safety failures by PCBUs and the resulting consequences.
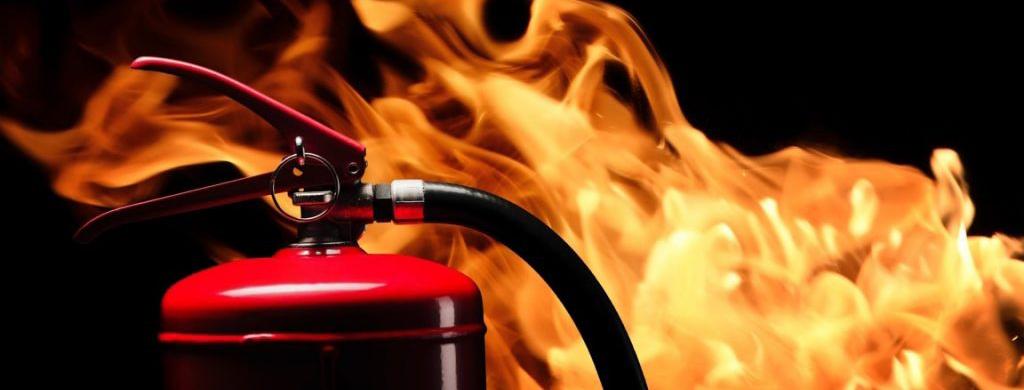
Three injured after training goes up in smoke
Fine: $355k | Reparation: $100k | Max Fine: $1.5m
Lack of proper training and instruction is always a recipe for disaster, no matter what the situation, WorkSafe National Investigations Manager Hayden Mander says
NZDF has been sentenced in the Palmerston North District Court under the Health and Safety at Work Act 2015 and must pay out over $450,000 after a training exercise went wrong.
In August 2020 a mock operation was carried out at the Linton Urban Training Facility as part of an annual training exercise. During an exercise an incendiary device ignited, and three Service Persons were harmed.
In the NZDF Risk Management Plan for the exercise it stated that controls would be in place to ensure the health and safety of those involved, including full flame-retardant PPE gear including overalls and a fire-resistant hood.
A WorkSafe investigation found that the appropriate PPE had not been provided to the Service Persons on the night of the incident. The provision of sufficient flame retardant PPE should have been ensured by NZDF, as specifically outlined in the Risk Management Plan.
WorkSafe found that a limited safety briefing had occurred, and insufficient instructions were given prior to the training exercises commencement, with some new participants on the second night not receiving any at all.
WorkSafe also found that the petrol and diesel used to make the incendiary devices was not appropriately stored and participants in the mock exercise had access to and used the fuel during the mock exercise.
Appropriate safety precautions must be taken in highrisk settings such as this, including the bare minimum of providing the right equipment to keep people safe.
Three Service Persons will have to live with physical and mental injuries for the rest of their lives. It was reasonably practicable for NZDF to keep these people safe, but a lack of oversight means their lives will be altered forever.
Management pleads ignorance over severed thumb
Fine: $200k | Reparations: $30k | Max Fine: $1.5m
Though management were unaware of their machine’s health and safety risks, the company was fined $200,000 over the incident
Mainland Poultry Limited was sentenced in the Papakura District Court after a worker’s thumb was severed in October 2020. The south Auckland egg processing company has been fined $200,000 and ordered to pay reparations of $30,000 to the victim.
While cleaning machinery, her thumb got caught between the edge of an opened access latch and the rotating blade of a screw conveyor, which had inadequate guarding.
WorkSafe’s investigation found workers were aware of the open latch to the blade but management was not, due to its obscured location. Health and safety matters at the site were raised in an ad-hoc way, and staff were using workarounds which managers were also unaware of.
“This injury could have been avoided if the machinery was properly guarded to industry standard,” says WorkSafe’s national manager of investigations, Hayden Mander.
“Although a business might have standard operating procedures for machinery while it’s in use, it’s critical to think about how that extends to cleaning and maintenance too. Those uses can’t be dismissed as out of sight and out of mind.
“Mainland Poultry has now improved its health and safety procedures, but their experience provides a timely warning for other businesses. Clear guidance and standards have been in place for many years, and the wider manufacturing industry needs to take notice to stop injuring and killing its workers,” says Mander.
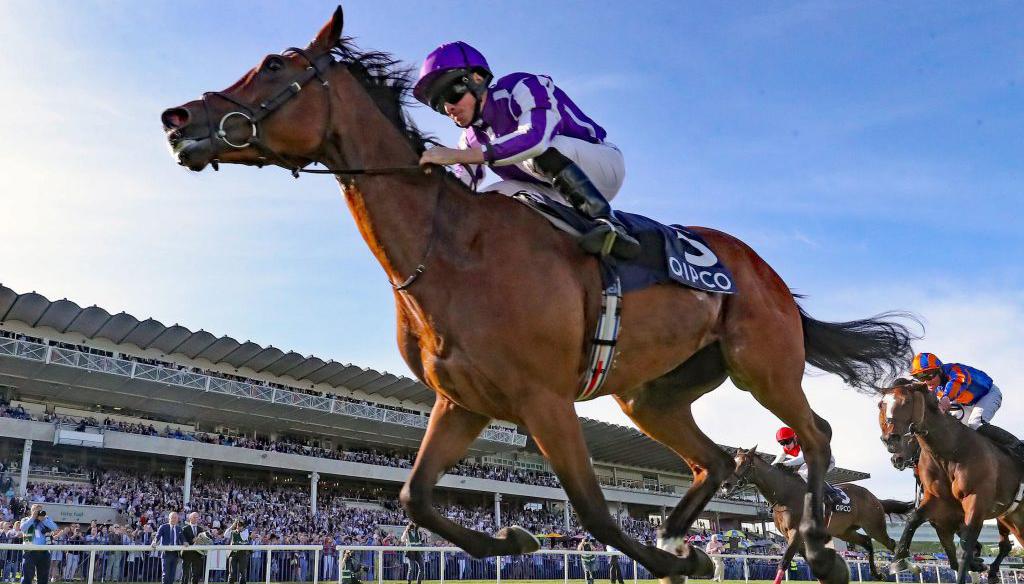
Horse race incident a lesson to all employers
WorkSafe New Zealand is reminding businesses they must assess the capabilities of their workers in a safe and controlled environment after a life-altering incident left a teenage girl paraplegic
On her first day working for Blackadder Racing in January 2019 the victim was asked to ride a thoroughbred racehorse.
While the 16-year-old had some experience riding horses she had no experience and was not capable of riding a racing-fit racehorse. She wasn’t expecting to ride a horse on the day of the incident and wasn’t dressed in riding attire.
The victim was not able to control the horse, and it bolted. The horse jumped over a fence, failing to clear it, and the victim was thrown from the horse causing serious injuries.
A WorkSafe investigation found while the business owner had intended to, no induction was done the morning of the incident. No competency assessment was undertaken, including no assessment of the victim’s riding abilities in a safe and controlled environment before she mounted the horse.
Blackadder Racing also failed to have in place a safe system of work that ensured the use of approved personal protective equipment (PPE) for the riding of a thoroughbred racehorse, including helmets and rider safety vests.
“If Blackadder Racing had taken reasonably practicable steps to ensure that qualified and competent individuals had assessed the capability and competency of the rider and ensured the rider was correctly fitted with appropriate PPE, this may never have happened,” says WorkSafe Area Investigation Manager Steve Kelly.
“There has clearly been a lack of planning and forethought given to the hazards and risks of a new worker undertaking track work riding, which has led to an incredibly tragic, and incredibly preventable incident.”
In the year prior to the incident, the victim been studying at the National Equestrian Academy in Rangiora and had recently completed a National Certificate in Equine Skills Level 3, specialising as a “Sporthorse Stable Assistant”. The sporthorse specialisation did not include any assessment of riding in-work thoroughbred racehorses.
The New Zealand Thoroughbred Racing Inc requires any licensed rider (such as the victim) riding a thoroughbred racing horse at a training facility to wear appropriate PPE including an approved helmet, body protector (safety vest), and footwear.
Blackadder Racing’s Health and Safety Policy stated they would provide appropriate PPE gear to any person riding at the facility and only experienced riders were permitted to ride the horses.
WorkSafe’s investigation found the victim wasn’t supplied appropriate PPE. The victim wasn’t wearing a helmet approved for riding a thoroughbred racehorse nor was she wearing a safety vest.
No steps were taken to ensure the victims’ PPE was fit for standard nor that she was competent and capable to ride a racing thoroughbred horse.
“It’s the duty of a business to ensure their staff have the appropriate PPE and are competent and capable of performing the tasks asked of them.”
“Worker competency assessments must be done in a safe environment where controls are in place to prevent serious harm.”

Business facing liquidation after double fatality
Fine: $595k | Reparation: $100k | Max Fine: $1.5m
A company has been fined $595,000 after a court found it responsible for the death of two of its customers due to multiple health and safety failures
What was supposed to be a 50th birthday celebration turned to tragedy, when two British tourists lost their lives in March 2019 while on a bespoke tour operated by Prestige Adventure.
As part of the tour, the group were set to undertake a coast-to-coast offroad driving component, led by company director John William Neil Thomssen.
The victims were travelling second in a convoy of five vehicles, led by Thomssen, along a track on the Kakanui Ranges that had a steep drop off the righthand side.
The wheels on the righthand side of their second vehicle (a side-by-side offroad machine) crossed the tracks causing the vehicle to over-balance and the two men to fall more than 80 meters. They died instantly.
A WorkSafe investigation found multiple health and safety failings by Prestige Adventure and Thomssen. The business had no documented training processes and no operations manual in relation to the tour.
While the tour group had undertaken basic training before commencing the trip with Thomssen, WorkSafe’s investigation found that this training had only lasted around 15 minutes and the practice terrain in no way resembled the hazards that the group would face while on the tour.
While the adventure operator had assessed the terrain for the tour by helicopter, nobody had travelled the actual route in the off-road vehicles the group would be using.
The off-road driving element of the tour was set to pass through a several high-country stations and Department of Conservation land. Mr Thomssen had been explicitly denied access to the farmland that the fatal incident occurred on.
WorkSafe also found that Prestige Adventure was not a registered Adventure Activity operator, even after knowing that this was a necessary legal requirement under the Health and Safety at Work (Adventure Activities) Regulations 2016.
“There is no excuse for Adventure Activity operators not to register with WorkSafe New Zealand”, says WorkSafe Area Investigation Manager Steve Kelly.
“When operators are registered, that is an assurance to members of the public that the business’ health and safety practices are appropriate.”
“Two men lost their lives as a result of Prestige and Thomssen’s failure to keep them safe. The impact on their families and friends will last forever and would have been avoided had the company and Thomssen not failed in the very basic duties required when people put their lives in their hands.”
Prestige Adventure was fined $595,000. Although it should be noted the company was no longer trading and was expected to go into liquidation.
While the judge would have ordered reparation in the vicinity of $230,000 due to the financial position of the company and Mr Thomssen the only reparation ordered was $100,000. That figure being the amount that Mr Thomssen had been able to set aside from his personal finances Thomssen would have faced a fine of $30,000 but due to his financial position and the priority to ensure that reparation was to be paid no fine was imposed on him.
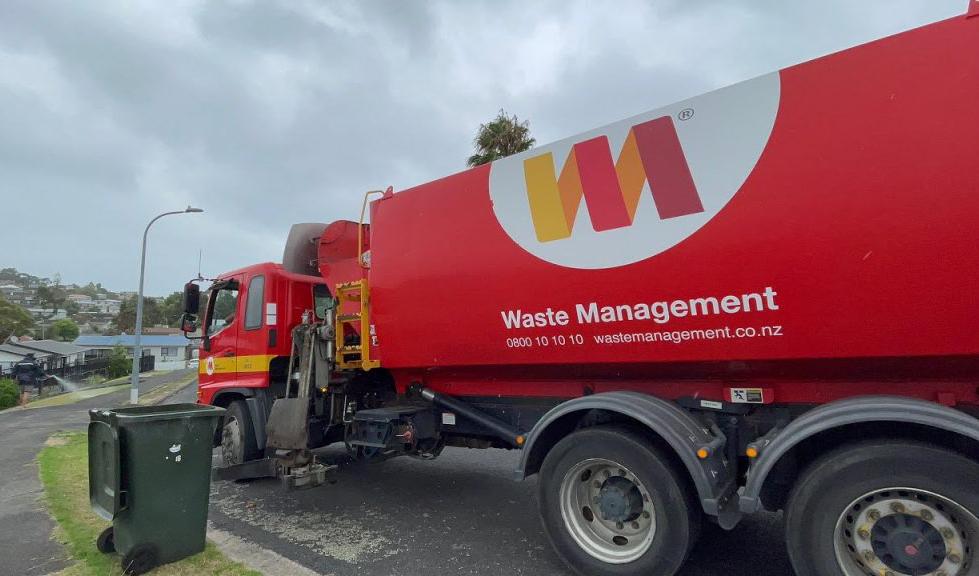
Gross negligence caused toxic gas death
A litany of health and safety failings has been laid bare in the Wellington District Court, where Waste Management has been sentenced to pay over $800,000 for the chemical poisoning of a worker
Jim Gideon died in August 2017, after being overcome by hydrogen sulphide gas from a treatment pit at Waste Management’s facility in Seaview, Lower Hutt.
Gideon had been directed to carry out a dangerous mixing of reactive chemicals to treat hazardous waste from the Haywards substation.
The waste had sat unmarked at the site for six months before being dealt with. During this time, the waste was never officially recorded, nor tested or labelled by the site chemist. A destruction certificate was issued despite the waste having not actually been destroyed.
On the day of the fatal poisoning, the hydrogen sulphide alarm repeatedly rang at the site, but work continued regardless. Gideon collapsed mid-afternoon, after exposure to at least 500 parts per million of hydrogen sulphide. The maximum workplace exposure allowed is 10 parts per million over an eight hour period.
WorkSafe’s investigation uncovered a breakdown of systems at the site, with health and safety failures at every level. These included improper storage and hazard identification, a lack of personal protective equipment (PPE) for workers, and inadequate risk assessment.
“Jim Gideon’s death was completely unnecessary and avoidable. It’s only by luck that there were not multiple fatalities at Seaview that day,” says WorkSafe’s national manager of investigations, Hayden Mander.
“Exposing workers to this degree of danger is unacceptable to WorkSafe, and negligent in the extreme. Waste Management’s failure on so many levels is appalling.”
In sentencing, Judge Davidson said a “wholesale systemic failure” had led to the creation of a “fatal gas chamber” at the facility. He imposed a fine of $450,000 and ordered reparations of $360,000.
Read more about hydrogen sulphide Read more about WorkSafe prosecutions
‘I’m not their mother’ no excuse for lax health and safety
A Kaikoura employer who failed to provide appropriate eye protection has been sentenced for failings that cost a young worker his vision in one eye
Daniel Anderson, an agricultural fencing sole trader, had a 17-year-old worker who was chiselling when a piece of metal flew into his right eye in March 2020. Despite multiple surgeries, the teenager lost sight in the eye.
Anderson did not notify WorkSafe of the injury, as required by the Health and
Safety at Work Act 2015. Several months later the victim’s mother did so, triggering an investigation.
When a WorkSafe inspector asked Anderson whether he told workers to use protective gear, his response was: “I’m not their mother and going to dress them every morning”.
Anderson confirmed that he had not provided full instruction to the victim on the use of personal protective equipment (PPE), such as safety glasses, because in his words “it was common sense”.
Anderson also indicated to WorkSafe he felt it was too expensive to buy PPE, saying: “I’m too small for that sort of… carry on”.
WorkSafe’s national manager of investigations, Hayden Mander says the employer’s comments reflect an outdated, unacceptable, and cavalier attitude.
“A young man at the start of his working life now has seriously impaired vision. It’s astounding for an employer to not understand the seriousness of the situation.
“The cost of health and safety is part of the cost of doing business. The worker should have been provided with appropriate PPE, including eye protection, and required to wear it when using a chisel and hammer or any other task where there is a risk of an eye injury.”
Workers who are vulnerable because of age, inexperience, or conditions of employment may be less likely to question health and safety practices or to speak up if they are unsure.
“Beyond the obvious health and safety gaps in this case, it’s both illegal and morally wrong for an employer of any size to not notify WorkSafe of an incident like this. No employer is exempt,” says Mander.
Judge Raoul Neave ordered $22,500 be paid for emotional harm and consequential loss, given Daniel Anderson’s lack of insurance and inability to pay a fine.
Read WorkSafe’s guidance on protecting your workers’ eyes
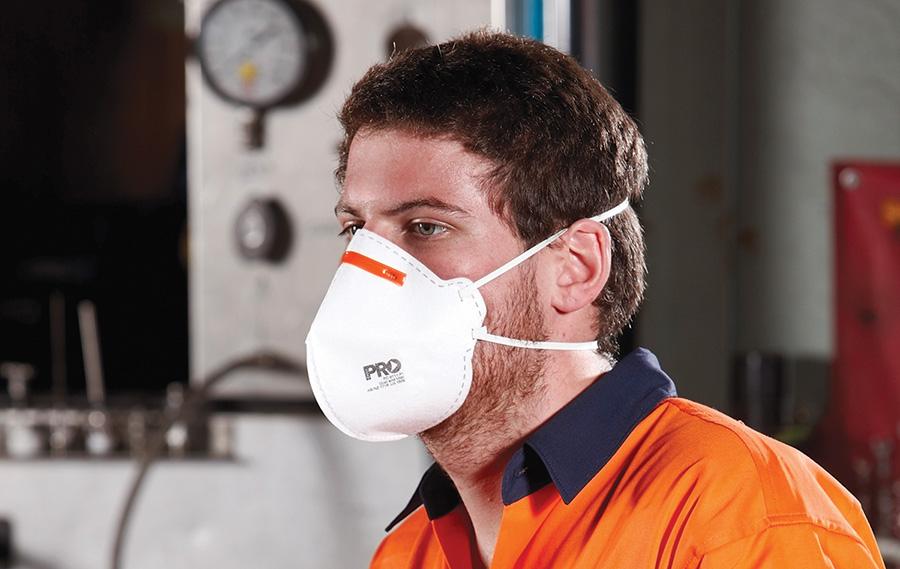
Employer’s advice gets workers poisoned
Fine: $250k | Reparations: N/A | Max Fine: $1.5m
A business was fined $250,000 after workers were exposed to methyl bromide, a WorkSafe New Zealand investigation found
The investigation began after workers at Flick Anticimex Limited, a pest control fumigation service, suffered acute methyl bromide poisoning as a result of ongoing exposure to the hazardous substance.
“Our investigation found problems with fitting Respiratory Protective Equipment (RPE), and that some workers were not using it at all. Practices around RPE were seriously below what they needed to be,” says Api Poutasi, Manager Health, Health & Technical Services at WorkSafe.
“Businesses shouldn’t rely on RPE as the main way to look after the health of their workers. They need to consider the hierarchy of controls. This is a requirement under the Health and Safety at Work (General Risk and Workplace Management) Regulations 2016.
“In this case workers were exposed due to the way the work was carried out, or due to ineffective respiratory protective equipment.
“Flick Anticimex was advising workers with facial
hair to use Vaseline to help the mask fit on their face. This is a myth which is deeply concerning in how widespread it is. Businesses and organisations must stop propagating this myth.
“Workers wearing RPE should be clean shaven. Even a small amount of stubble can prevent a proper seal from forming. Vaseline does nothing to help this, and workers will still be wearing RPE which hasn’t formed a seal based on incorrect information from their employer.”
WorkSafe’s investigation also found the business standard was workers didn’t use RPE when undertaking formaldehyde fumigations and no staff had been adequately trained to clean and maintain the RPE equipment that they did have. There was also no coherent system in place that monitored employee exposure to toxic fumigants.
The business had been advised by an Occupational Health Consultant in 2019 that given the lethal nature of the fumigants involved, and the potential concentrations that workers would be exposed to, it was essential that RPE was provided and properly fitted.
Flick Anticimex Limited was sentenced on 7 December 2021 at the Auckland District Court, under the Health and Safety at Work Act 2015 for exposing employees to toxic fumigants such as methyl bromide, hydrogen cyanide and formaldehyde.
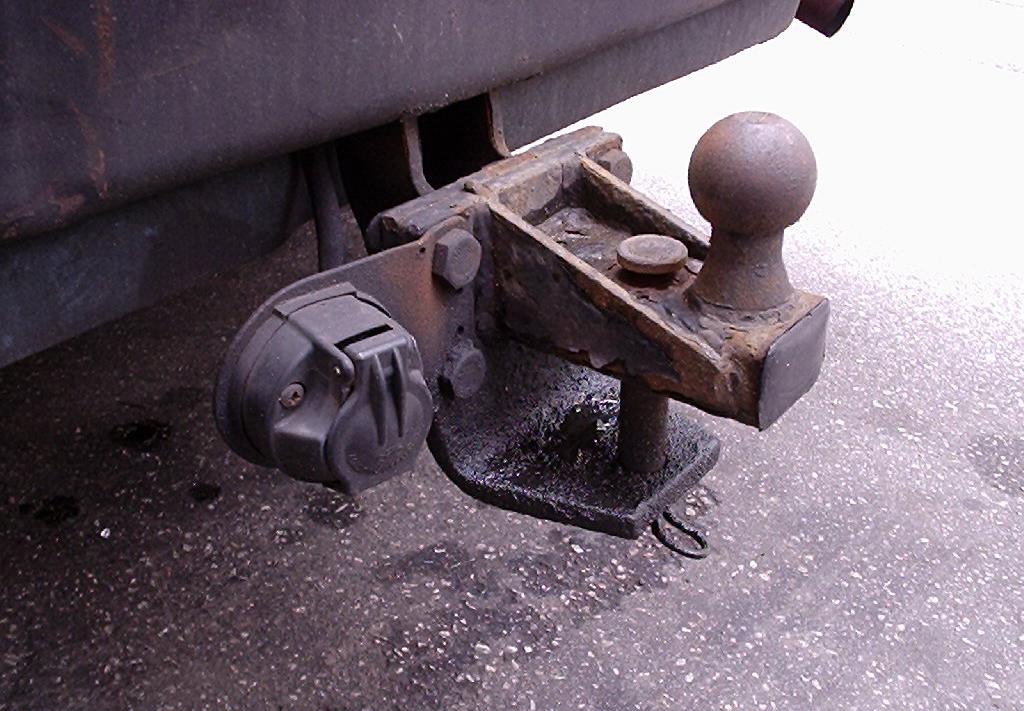
Decoupled trailer fatality results in $50k fine
Fine: $50k | Reparations: $145k | Max Fine: $1.5m
The death of a nine-year-old girl in a Northland traffic crash has been traced back to a badly worn down towball and coupling on a trailer used by a local trucking business
The trailer’s safety chain failed, disconnecting it from the truck towing it in October 2020. The trailer collided with an oncoming car the young girl was travelling in near Mata, south of Whangārei. The owner-operators of the trailer, Johnston’s Direct Logistics Ltd, have been sentenced in the Whangārei District Court for health and safety failings. Expert analysis commissioned by WorkSafe found the condition of the towball and tow coupling was of “significant concern”. There was very extensive wearing on both, which meant a small bump in the road, or change of incline, could allow the trailer to easily decouple. As well, the trailer’s certificate of fitness had expired, and its tyres had uneven pressure. WorkSafe alleged Johnston’s Direct Logistics failed to undertake regular and effective inspections of its vehicles, and failed to identify the deterioration of the towball and coupling. “The company had a duty to ensure the health and safety of other people was not adversely affected by its work. Johnston’s should have been doing regular inspections of all its vehicles including the trailers
couplings and towballs to ensure they were safe and roadworthy,” says WorkSafe’s area manager, Danielle Henry. The company should also have ensured its vehicles had current warrants or certificates of fitness. As well, Johnston’s should have identified and logged the maximum weight every towing vehicle and trailer could manage, to ensure that towing componentry was rated safe for use. “This tragedy should serve as a warning to other businesses to keep a much closer eye on basic maintenance. A young girl’s life has been lost through no fault of her own, and her whānau is forever impacted,” says Henry.
Read more about WorkSafe prosecutions
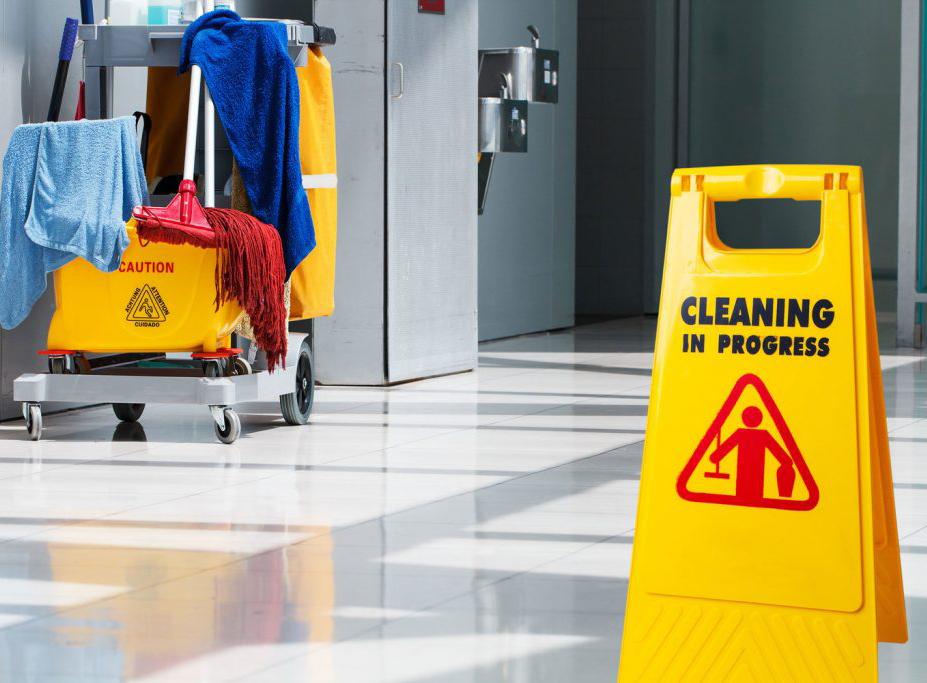
Cleaner’s death a reminder to think around the clock
You may have very competent staff and thorough procedures onsite in daylight hours, but many businesses have cleaners or other contractors coming in after hours for maintenance, WorkSafe area investigation manager Paul West says
The early morning death of a Taranaki cleaner is a lesson in 24-hour health and safety. 74-year-old Robin Killeen died doing cleaning work in December 2019 at ANZCO in Eltham. The company and its subsidiary, Riverlands Eltham Limited (REL), have been sentenced in the Hāwera District Court for health and safety failings. Killeen’s employer, Kia Ma Limited, has pleaded not guilty and is still before the courts.
Killeen became trapped after climbing into a bin lifter to clean it. The evidence indicates he operated the controls from inside but was unable to stop the machine.
A WorkSafe investigation found ANZCO should have developed a safe operating procedure for cleaning of the machine, and REL should have had better hazard identification and risk assessment about the cleaning process.
Commercial cleaning is a high-pressure industry that works on tight timeframes. Safety must come ahead of whatever appears to be the quickest and easiest way to do the job.
You may have very competent staff and thorough procedures onsite in daylight hours. But many businesses have cleaners or other contractors coming in after hours for maintenance, so it’s critical to consider these people in health and safety planning and assessment of risks.
Robin Killeen’s death is also a warning for other interlinked companies to ensure their health and safety practices align. Front-foot the discussion, agree your procedures and document them clearly to avoid catastrophic consequences.
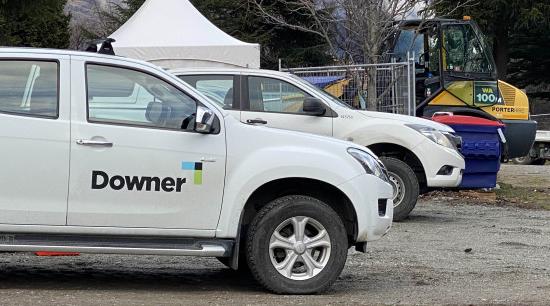
Detoured cyclist killed by construction vehicle
ENFORCEABLE UNDERTAKING
Two companies have avoided prosecution after traffic management health and safety failures caused the death of a cyclist, but have committed to an enforceable undertaking to ensure it does not happen again
On 30 October 2019 Fyfa Campbell Dawson was cycling to work with her route taking her past a construction site on a temporary section of Springs Road associated with work on the new Christchurch Southern Motorway extension.
Due to the nature of the site, a temporary route was set out for pedestrians, cyclists and others by those in charge. Dawson was following this route when she collided with a truck as it entered the site.
A subsequent WorkSafe investigation alleged Downer New Zealand and McConnell Dowell failed to ensure the health and safety of members of the public as a safe and effective temporary traffic management system wasn’t in place. WorkSafe laid charges against both, and as an alternative to prosecution Downer New Zealand and McConnell Dowell each offered an enforceable undertaking, which was accepted.
WorkSafe considered the following mitigations were reasonably practicable and could have reduced risk of harm: • A minimum one metre shoulder for cyclists • Providing Traffic Management Operations with effective information, instruction and supervision, specifically relating to provision for cyclists and clear and consistent information • Instruction and supervision should have been provided to Traffic Management Operations in relation to the frequency and numbers of expected deliveries to allow for the consideration of effective controls relating to the risk of vehicle entry and egress on site.
“Enforceable undertakings require a commitment from the businesses and organisations involved to improve health and safety within their business, industry and community,” says WorkSafe’s Head of Specialist Interventions Dr Catherine Gardner.
“Both companies in this instance have expressed a desire to improve health and safety and especially to protect cyclists and other vulnerable road users.”
Downer and McConnell Dowell have worked together, as joint venture partners, to coordinate the activities they are undertaking.
The two enforceable undertakings comprise: • Reparations to the victim’s family • A fleet training programme focusing on the potential impact of driver’s actions on vulnerable road users • Supporting a scoping study and pilot to
establish options to mitigate the risks to vulnerable road users with CHASANZ • Supporting the establishment of a Good Practice Guideline for the treatment of vulnerable road users in temporary traffic management • Development of an NZQA qualification for Temporary Traffic Management Risk Assessment • Investment in a virtual reality training programme • Facilitating a cyclist awareness programme across roading sites • Contributions to Waka Kotahi’s BikeReady programme
“An enforceable undertaking requires the business or organisation to be directly involved in improving health and safety for the betterment of all. Today is where
the commitment really begins and WorkSafe will regularly monitor progress on the conditions which have been agreed,” says Gardner.
“This doesn’t take away from the fact this was a preventable death. Cyclists and other vulnerable road users have a more than reasonable expectation they will be safe when they travel – and those in charge of sites like this one need to meet that.”
Downer Chief Executive Steve Killeen says his company has strived to ensure the activities set out in its enforceable undertaking will benefit not only its workers and industry, but also will have a wide reach within cycling communities across New Zealand.
“We are always seeking improvement in the Temporary Traffic Management space and we strongly believe that the work undertaken as part of this enforceable undertaking will move the industry beyond mere compliance with existing requirements and have a significant step change effect that benefits the construction industry and the broader community.”
McConnell Dowell Managing Director Fraser Wyllie says he embraces the enforceable undertaking as a platform to improve temporary traffic management delivery and build capability of workers and our industry to make roads safer for our entire community.
“The emphasis will be educating and training initiatives to improve awareness and to reduce the risk exposure for all road users. We are creating a digital engineering visualisation tool and partnering with industry bodies when construction work is carried out.”
Read more about the accepted enforceable undertakings:
Downer New Zealand Limited
McConnell Dowell Constructors Limited
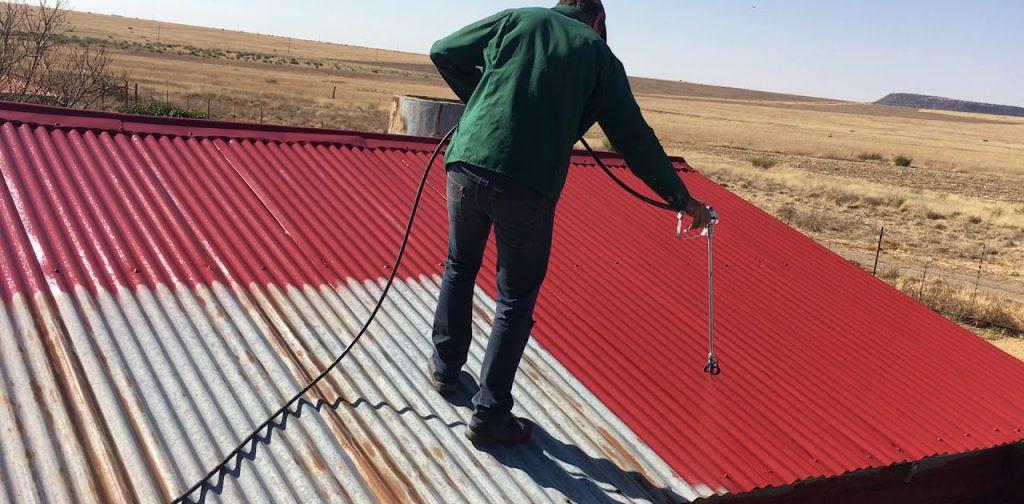
Liquidation no escape from health and safety accountability
Fine: None | Reparations: $100k | Max Fine: $300k
An Auckland businessman is being held liable for failures that led to the death of a subcontractor, who fell from the roof of a house while spray painting
Hon Sang Cheuk was the sole director of DMJ Painters Limited, which hired the painter for the job at Bucklands Beach in June 2020. No scaffolding was in place at the house, nor did Cheuk check if the worker used the harness he was given for the job, or was trained and competent to use one.
DMJ Painters Limited was put into liquidation 49 days after the fall occurred, so Cheuk himself was prosecuted for his failings as a company director under the Health and Safety at Work Act 2015. He has now been sentenced in the Manukau District Court.
“Individuals and directors have a range of health and safety responsibilities and liquidating your company does not absolve you of them,” says WorkSafe’s area investigation manager, Danielle Henry.
A WorkSafe investigation found inadequate risk assessment at the site, where no measures were in place to prevent the victim falling from the roof onto a concrete patio.
“Some form of edge protection should have been in place as a basic safeguard. It was easily foreseeable that a fall could occur, resulting in serious injury or death.
“The victim of this fall leaves behind a wife and son, whose lives are forever changed by a simple failure to put safety first,” says Henry.
Hon Sang Cheuk was sentenced at Manukau District Court on 27 July 2022. Judge Forrest ordered reparations of $100,000 to be paid to the victim’s family. Judge Forrest did not impose a fine due to Mr Cheuk’s financial circumstances.