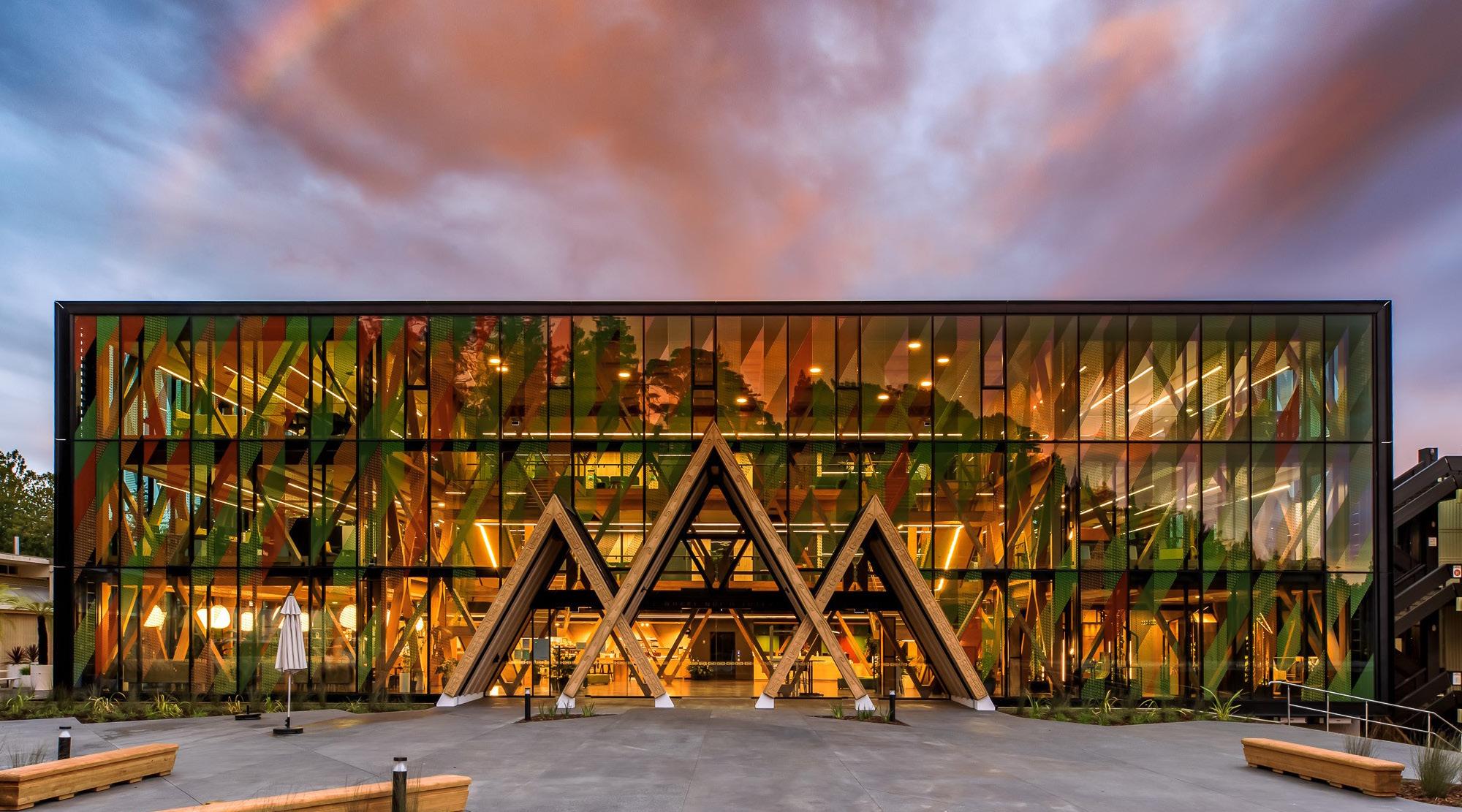
5 minute read
Government advances forestry agenda at expense of steel
Let science lead the way
Forestry Minister Stuart Nash is well qualified to advance the cause for wood but 20 years in the sector does not qualify him to close one eye when it comes to complementary options, says publisher Mike Bishara
Advertisement
Scion Innovation Hub - Rotorua
Practical visions for the future – a case for steel
The Heavy Engineering Research Association (HERA) maintains that design should dictate material, advocating for the right material based on design that has been tested, consented and peer-reviewed where appropriate.
Chief executive Troy Coyle says these decisions should not be dictated by government or industry bodies but by architects and engineers – “those at the coalface who are walking the line of design, performance, and seismic, sustainability and other standards every day.
Some of the conversation suggests that a ‘wood first’ policy would help New Zealand do better against emissions targets.
In fact, both the steel and concrete industries are aggressively decarbonising while delivering resilient buildings.
While both materials have significant embodied carbon footprints, their life cycle carbon emissions improve due to their resilience, ability to enable lower operational carbon emissions, and in the case of steel, its infinite recyclability.
Further, steel offers extremely long lifetimes, which means that the carbon is amortised over a longer period.
If our goal is to meet our emission targets, move to a low carbon economy and a circular economy, we need to stop focusing on embodied carbon and focus on lifecycle carbon.
Steel is surprisingly low-carbon over its lives, is 100 percent recyclable and can be infinitely recycled without loss of quality.
In New Zealand, 72 percent of steel is currently recycled. Lower-value steel scrap can be converted into high-value steels by using appropriate processing and metallurgy, and there are emerging technologies (locally and internationally) that have the potential to significantly reduce the carbon footprint of both materials.
The New Zealand steel industry also strongly delivers to the Living Standards Framework.
As for HERA’s own work, we are launching a zero carbon, steel-offsetting programme, which will also include steel reinforcing used in concrete; and a carbon emissions calculator, independently developed and based on verifiable data, which allows companies to offset embodied carbon emissions and offer zero-carbon steel.
We hope that this will refocus the conversation away from embodied carbon comparisons and more to what matters – net carbon emissions of the life of a building or structure.
While wood is absolutely right for many jobs and applications, mandating its use for all projects could create economic and other problems.
Yes, our future buildings must have a low-carbon footprint, but it is just as essential that they are resilient to our changing climate, and steel and concrete offer resilient buildings.
Steel and concrete are essential for supporting high-value jobs, community investment and economic growth. In fact, MBIE’s own Manufacturing Report shows that there are 30 percent more jobs in metals manufacturing than there are in wood and paper processing, and that the bulk of the growth is regional.
Based on this and other economic factors, Minister Nash’s expressed concerns about supporting regional development, national employment, sustainability and emissions reductions goals are more achievable with a practical, combined approach than with one which prioritises a single material.
Few would argue with the necessity of moving New Zealand to a climate-resilient, low-emission and circular economy while building resilience in our supply chain and maintaining manufacturing levels.
But this is not an either/ or scenario or a zero-sum game says the Heavy Engineering Research Association (HERA).
“Any suggestion that New Zealand construction and infrastructure has to choose between wood, steel and concrete would be akin to choosing between land, water and air, says HERA’s chief executive Dr Troy Coyle.
“We need all elements to survive and create the best outcomes for communities and the economy. If we allow our development programmes to be led by design and data, we will succeed, but if politics, money or special interests overtake science and evidence, collective failure lies ahead.”
There is no doubt that forestry will be a key part of our climate change response.
“In areas like biofuels, forestry can support our move away from fossil fuels. Innovative building products made from local wood will replace products such as concrete and steel,” Nash says.
Coyle suggests that we do not rush headlong into single material choices that are not grounded in good science.
“Rather, we need the research and evidence to guide decision-making and the journey to a circular, low-emission economy.
“New Zealand needs a mix of materials: concrete relies on steel; light timber and steel-framed houses sit on concrete floors; mass timber structures rely on steel and concrete cores and foundations.
“Materials are complementary, not competitive – together, we can enable a wider range of sustainable choices.”
And there, Nash is on somewhat safer ground and despite political rhetoric, real progress is being made in the forestry field by Scion, a world leading research crown entity. “The future for forestry is not only bright from an economic perspective, it holds the key to a more sustainable future,” Nash says in his vision for Future of Forestry Booklet.
Scion is combining science and forestry to effect truly innovative and practical change. From mixing plastics in with wood for strength levels the equivalent of steel, its current work on bio-coal from renewable resources is truly ground-breaking.
It has the potential to remove the greenhouse gas equivalent of up to 20 percent of light vehicles from our roads.
The largest source of biomass for biofuels in New Zealand comes directly or indirectly from forestry.
In cases like Red Stag Timber, wood waste is used to generate electricity and heat to kiln dry timber, with any excess power being fed into the national grid.
Forestry and mill residues could fuel boilers in other industries, but their low bulk density, high moisture content and low energy content in comparison to coal means in many cases they cannot directly replace coal in existing boilers. However, heat and pressure can transform wood waste into high energy, high density bio-coal.
The process of heating biomass to temperatures of up to 300°C in the absence of oxygen is called torrefaction. When woody biomass is torrefied, bound water is removed, which increases the energy density, and makes it less likely to reabsorb water.
The wood cell walls are also weakened, making it easier to compress the torrefied wood into dense pellets or briquettes.
Scion researchers are optimising the torrefaction and densification of woody biomass to produce solid biofuels that are durable, moisture resistant and have an energy density close to that of sub-bituminous coal (20 to 21 GJ per tonne and 17 GJ per cubic metre).
The investment needed is large but necessary to reduce the country’s dependence on fossil fuels, reduce our greenhouse gas emissions and help rejuvenate regional economic and employment growth as we head to a more sustainable future.
And that’s where you come in Mr Nash.
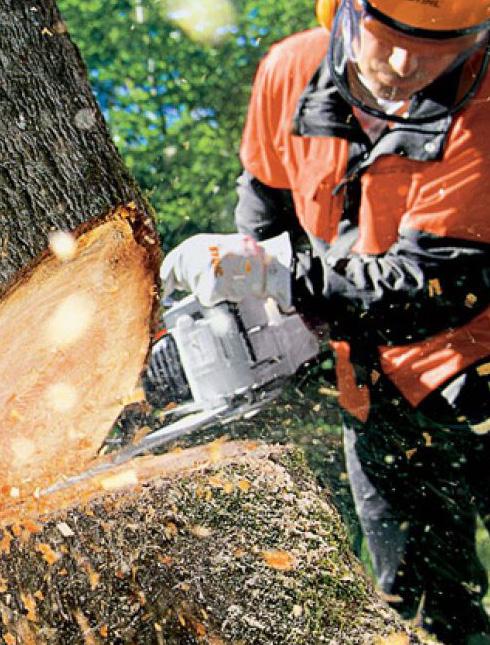