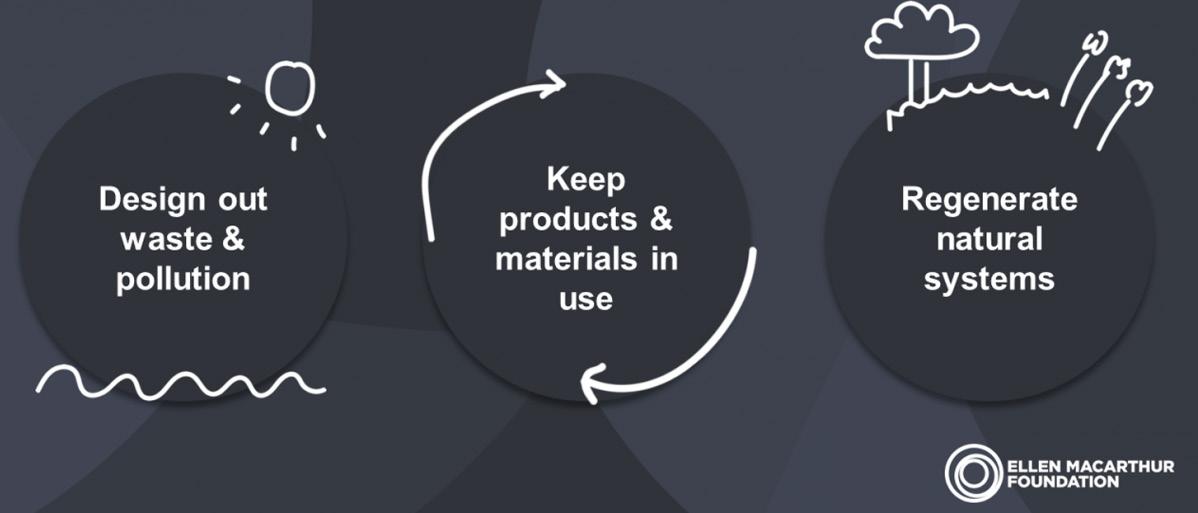
3 minute read
Kiwi moves towards a circular economy
The essential concept at the heart of the circular economy is to ensure we can unmake everything we make
The products we use for all aspects of life are often designed and manufactured with little thought for the resources consumed in making them or what happens to them at the end of their life.
Advertisement
Apart from the most expensive purchases we make, like a car or house, when something breaks in our modern world it is often more expensive to repair than to buy a new one, and usually it goes to the landfill. This take-make-dispose mindset has created a linear economy -- products are not designed for reuse, repair, refurbishment or to be remanufactured.
A circular economy is an alternative to the traditional linear economy in which we keep resources in use for as long as possible, extract the maximum value from them whilst in use, then recover and regenerate products and materials at the end of each service life. When a product is designed for the longest use possible, and can be easily repaired, remanufactured or recycled (or used, composted and nutrients returned) we consider it to have a circular life cycle.
A circular economy is fuelled by renewable energy (solar, hydro, wind and tidal power, and biofuels) while a linear economy works on the principle of natural resources>take>make>dispose>waste. Technical A circular economy is based on these three principles

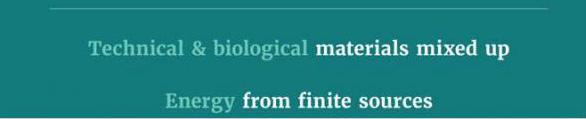

and biological materials are mixed together. Energy comes from finite sources. Growing international research and evidence shows numerous benefits over the traditional linear economy. These include: • long-term cost savings • increased local job opportunities
• encouragement of technical innovation
• reducing the amount of harmful waste produced • reversing our impacts on climate change
International research and strategies on the circular economy • What is a circular economy? • Circular economy pubications • London's circular economy route map • Finnish road map to a circular economy • Key findings from the forthcoming OECD report - Global Material Resources Outlook to 2060: Economic Drivers and Environmental Consequences
Waste Minimisation Fund
The Waste Minimisation Fund (WMF) is for initiatives that will accelerate New Zealand’s transition to a circular economy.
Flight Plastics is a great example of how circular economy business models can benefit New Zealanders with the support of WMF.
Flight Plastics has built New Zealand’s first integrated PET recycling and manufacturing facility. PET is commonly used in plastic bottles, punnets and other food containers.
Every year New Zealand imports millions of plastic bottles and food containers.
When these had been used they were either sent overseas for recycling or disposed of to landfill.
But since 2017 Flight Plastics in Lower Hutt, with the support of funding from the Waste Minimisation Fund, has been turning waste PET into new containers to supply distributors in New Zealand
In 2011 Flight Plastics received $30,000 from the Waste Minimisation Fund to assess the economic viability of installing a plant to recycle PET (number 1) plastic in Wellington.
The plant which makes PET food-safe packaging using recycled PET flakes went ahead. In 2013 the company was awarded further funding of $4 million from the Fund to build a wash plant to enable complete onshore recycling of PET.
Previously PET collected from recycling was shipped in bales to overseas markets for processing. Now, every tonne of PET plastic that is recycled at Flight Plastics prevents a tonne of plastic being imported and another tonne being shipped overseas for recycling. You can spot a recycled Flight Plastic container by the NZ RPET and Flight logo on the container's base. As well as creating local jobs, this initiative is reducing the amount of new plastic coming into the country and waste plastic being shipped offshore or sent to landfill. When a product’s component materials are reused rather than put in a landfill, not only is that material no longer waste but new raw materials are not required to be extracted, what Flight Plastics calls the “double whammy” effect.
Countdown uses Flight Plastics products in its bakery and delicatessen.
Credit: Ministry for the Environment
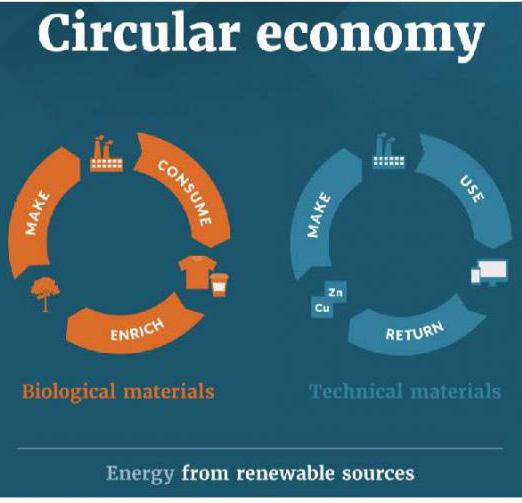
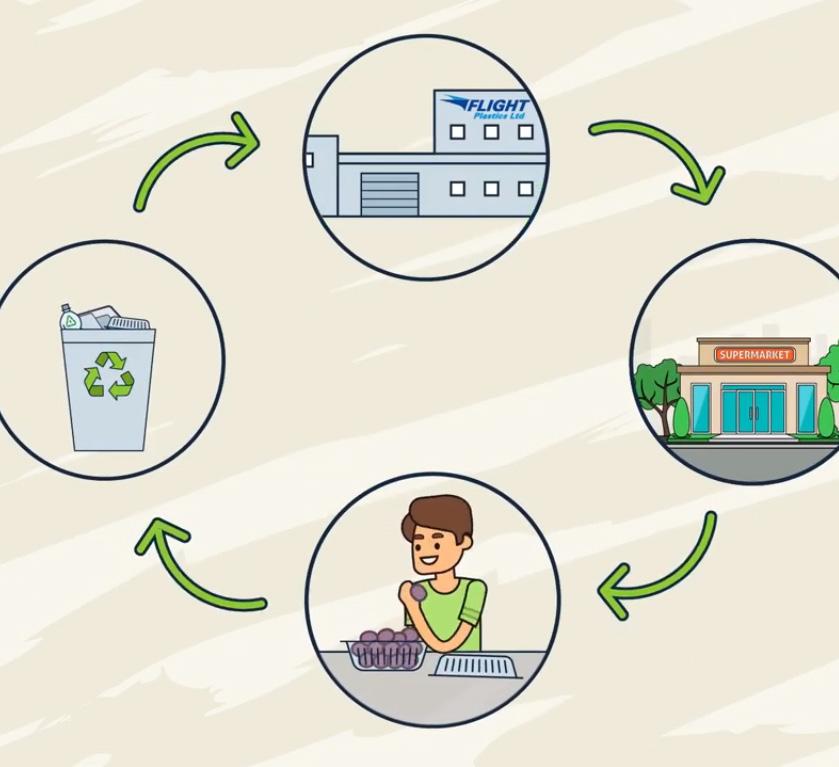