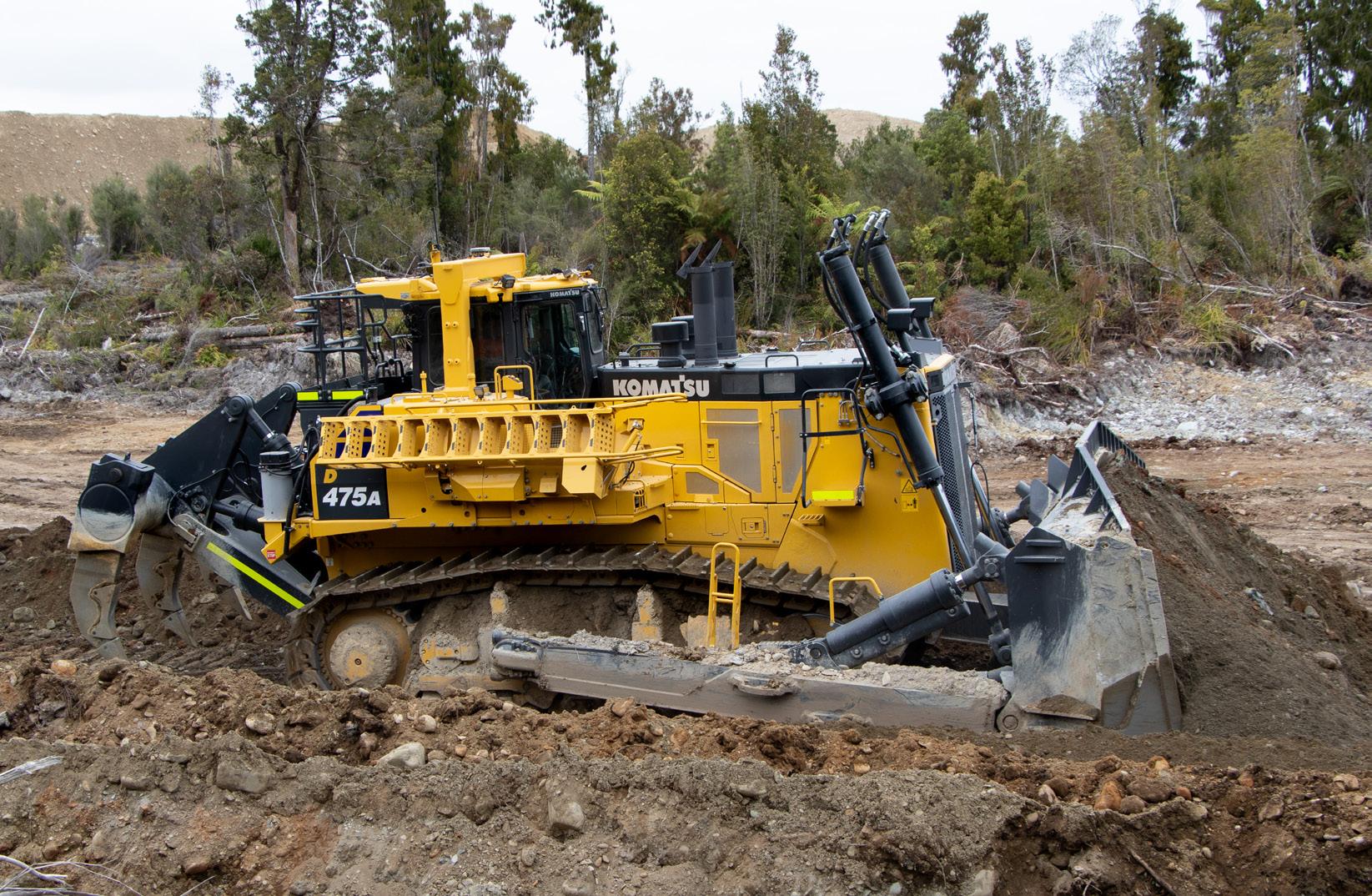
13 minute read
Komatsu's new standards in performance
Sponsored Article Greymouth miner gears up for new challenge
West coast miner Whyte Gold has recently taken delivery of the largest and most sophisticated bulldozer in New Zealand, to service its new claim in the glacier region behind Greymouth
Advertisement
Afive-truck convoy carrying the 115-tonne machine, broken down into transportable capsules, made the 500km journey from Lyttleton to its new base at Rimu.
Komatsu positioned technicians at Whyte Gold's purpose-built hard stand to assist with the final construction of the massive machine. "It was fully built up and tested in Japan before it was shipped to New Zealand, Len Higgins, Territory Sales Manager, West Coast/Marlborough/Nelson says. "We had to semi-knock it down at Lyttleton in order to be able to transport it across Arthur's Pass.
The rebuild commenced within hours of the 75 tonne main frame arriving at Whyte Gold on one low loader accompanied by another four trucks of essential components.
The machine marks the start of a new phase in the development of the veteran gold mining company on a long-established site, until recently believed to have been worked out.
Company principal Iain Whyte conducted tests which have convinced him that there is plentiful new material lying deeper into the substructure.
Whyte believes the claim can be worked for at least another eight years, using techniques he has developed to access the site under increasingly stringent ecological controls.
The Komatsu D475A-8 he purchased is one of the first delivered by the Japanese specialist in the Southern Hemisphere, to anchor his operations.
It is the largest in Komatsu's range with levels of emission control at the leading edge of heavy machine capability.
It is fitted with electronic controls so sophisticated that its essential operations are monitored by telemetry flowing constantly to Japan and Australia.
The new bulldozer is capable of extracting and crushing material with unmatched efficiency of time and materials which will limit and manage impact on the land.
Operation is made easier with electronic control of the work equipment, including blade auto pitch and ripper auto return.
There's the potential for future expansion to Intelligent Machine Control, incorporating remote control and automation. "Some say I would be better served with a smaller machine, but this bulldozer can extract substantial material with a single-pass, so it is actually in use far less than any alternative method," Whyte says.
Whyte Gold had wound back its operations on a nearby site at Dungaville to comply with directions of the Department of Conservation and the Crown Minerals act, and had sold its first D475 bulldozer, a previous model, to a local coal mining company. "I was left with enough to keep ticking over - but I've worked with a lot of good local people and I felt I owed it to them, and to their future, to keep prospecting," Whyte says. "I tested a lot of claims, mainly on old workings - I figured the old guys didn't tunnel for nothing."
Whyte Gold's new site was believed to have been mined out. "But the previous miners worked only the top level," Mr. Whyte says.. "Further down there's a wash with strong content."
Whyte Gold will use its new Komatsu to open cut between 25 and 35 metres into the site to reach the new level.
Komatsu’s advanced Tier 4 engine and hydraulic control technology improves operational efficiency and lowers fuel consumption by up to seven percent, according to Garth Dixon, Komatsu New Zealand’s Sales Manager.
“As with all our products, it has been designed in line with Komatsu Harmony principles, resulting in a fully integrated machine to produce an efficient, reliable system,” he says.
“Komatsu designs and manufactures all major components, including engines, pumps, valves, motors and cylinders. This optimises machine performance, and maximise production while minimising fuel consumption.”
As with others in Komatsu’s Dash 11 range, the PC210LC-11 is fitted with a number of unique features that contribute to reduced fuel consumption and allow the engine to operate at the most efficient speed.
These include: • Low speed matching, which provides higher flow output at a lower engine RPM through the use of larger displacement hydraulic pumps. This feature also provides better pick up and response to hydraulic flow demand and provides fuel savings in all duty cycles. • Variable speed matching, an engine-pump matching control that matches engine speed to hydraulic flow requirements. It keeps engine speed high when large pump delivery is required and reduces engine speed in light duty operations to save fuel. • Six working modes including a Fine Control mode, Breaker mode and Economy and Power modes for Attachments. • A reduction in auto deceleration speed to low idle

New standards in performance
Komatsu has released the 23-tonne class PC210LC-11 excavator, delivering increased performance, operating efficiency and productivity, while significantly reducing fuel consumption compared with predecessor models
speed.
The PC210-11’s advanced Tier 4 engine technology delivers reductions in NOx and PM emissions by up to 90 percent compared with the Tier 3 engines in the previous Dash 8 range, says Dixon.
Additional improvements that contribute to fuel efficiency – and which are standard across Komatsu’s Dash 11 excavator range – include an economy working mode for attachments, an “ECO-guidance” function which provides data and recommendations to the operator for fuel saving operations, and auto idle shutdown to reduce excessive idle time.
Safety and operator comfort have also been upgraded. “As with all our Dash 11 excavators, it has an upgraded, fully compliant ROPS cab and includes a new high back air suspension operator seat with lumbar support,” Dixon says..
“The new cab also incorporates console mounted arm rests with a tool-less height adjustment so that operators can easily change the arm rest position in relation to both the seat and the joysticks for better ergonomics.”
Safety is further improved with the lock lever auto lock function to prevent unintentional movement. “If the operator has accidentally activated a control during start-up, the machine recognises this and automatically applies the hydraulic lock so that no uncontrolled movement occurs,” Dixon says. Quick hitch and hammer piping is standard on the PC210LC-11, as is an additional service valve for easy set-up of a proportionally controlled second auxiliary line.
Attachment tool management is also available through the monitor panel, enabling an operator to name and set the flows for up to 10 attachments for easy selection when changing out attachments on the jobsite.
“The PC210LC-11 also includes the latest developments in our KOMTRAX telematics-based remote monitoring system, ensuring unrivalled visibility into all critical machine and operational parameters,” Dixon says.
Sponsored Article The Swiss army knife
Brandon Whiddetts has designed or modified 10 attachments for his Komatsu PC220 excavator, all interchangeable in the space of just five minutes
Treescape has been at the forefront of innovation in green management in New Zealand. The Komatsu partnership, according to Whiddetts has brought exceptional efficiency to every facet of the business, to the benefit of his company, his customers and the environment.
Komatsu New Zealand's product support manager Brent Hepple has worked with Brandon for almost 20 years, to help turn his ideas into reality.
Each innovation has been made to work within Komatsu's operational guidelines to maintain product integrity and retain Treescape's machinery investment.
Komatsu has helped devise a can bus system with easily identifiable graphics which allow an operator to switch hydraulic flow from within the cockpit "It is the most extraordinary sight," Hepple says. "You can arrive on a Treescape job and find a multitude of attachments all neatly laid out waiting to be used in sequence, with minimal change-over time between them.
Whiddetts ideas include the design of a high-speed mulching head, a vertical tree grab sheer, a chain saw felling head, a high-speed hydraulic stump grinder, a hydraulic tree transplanting spade, rotating grapple with pusher bar, and a winch bucket.
He is co-founder of Treescape, a green asset management company with branches throughout New Zealand and on the eastern coastline of Australia. He and his business partner Ed Chignell started Treescape as a teenagers almost 40 years ago.
Whiddetts has spent his working lifetime seeking out new ways of making machines work smarter in the service of his clients. "There isn't a machine built yet that is so perfect it can't be made to work better,"Whiddetts says.
His title in the 660 strong person business is CEO, but it stands for Chief Engineering Officer. He works from a small office in a workshop of 14 people whose task it is to make their equipment more efficient.
Co-Founder and Chief Executive Officer of Treescape Ed Chignell pioneered the concept of ecologically sustainable arbo-culture more than 35 years ago, while Whiddetts concentrated on mechanical improvements to support the concept.
Treescape uses 45 Komatsu excavators and wheel loaders across its network. It is one of several exclusive long-term supply arrangements he has with key business partners. "The benefits to us and our partners are intertwined - if we don't live, they don't live," he says. "Practically, the ability to train operators on the systems of one brand has substantial benefits in terms of safety and machine servicing."
But beyond that, Brandon has sought from his business partners a shared belief in maximising productivity through improvement and innovation. "I come up with the ideas and Komatsu does the design to my request," he says. "I'm not an engineer, just someone who thinks about practical improvements," he says.
Treescape's purchase of its first Komatsu, a PC130 excavator, more than two decades ago was unusual in the arboriculture industry which was employing manual labour, according to Hepple.
The tipping point was Brandon's innovative use of attachments which turned the excavator into a machine purpose-fit for the task. "The attachments work so well with the machines that they are imposing minimal stress - on both machine and operator," he says.
The company has recently purchased two new Komatsu PC220 excavators and these too are performing above and beyond expectations.

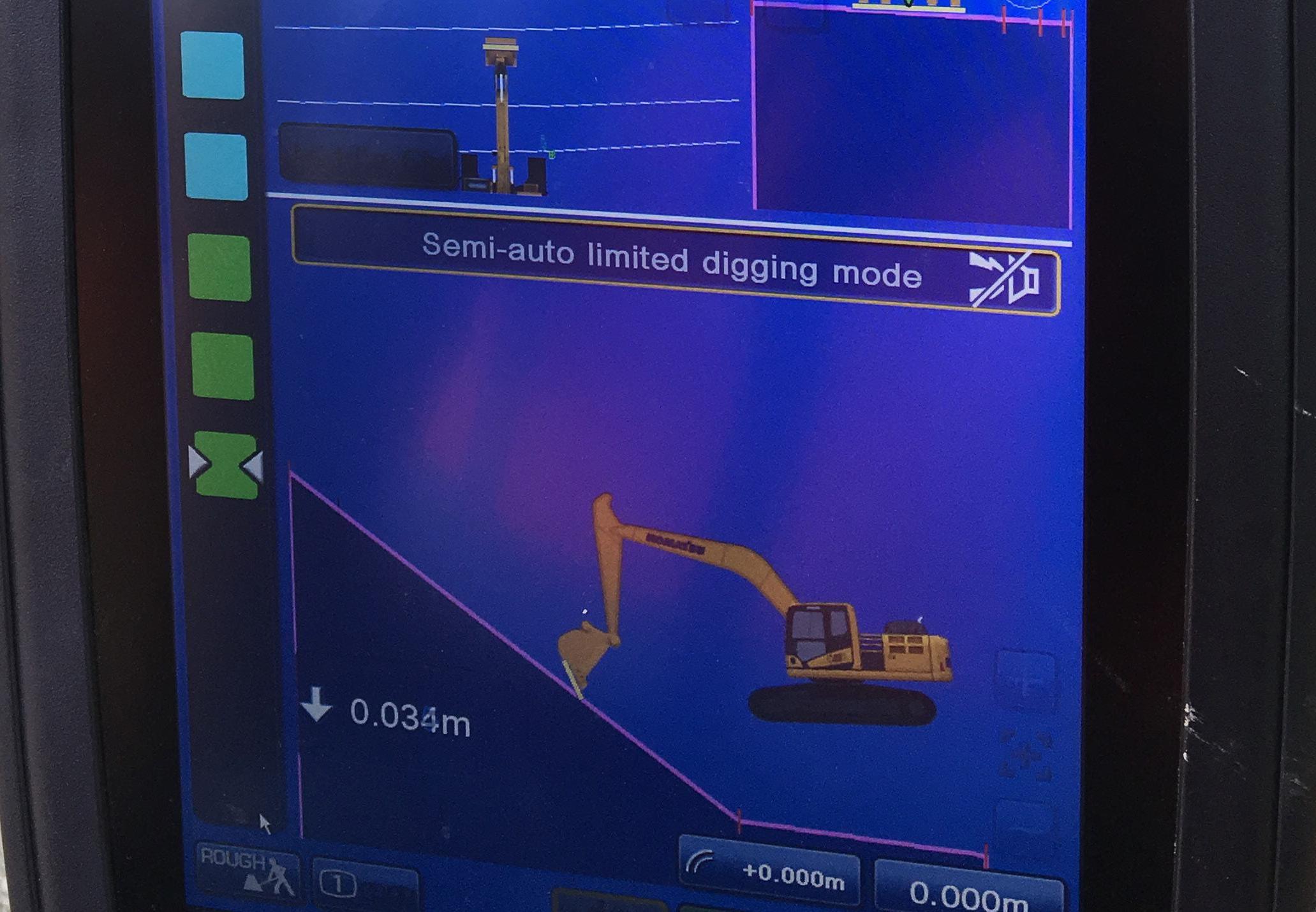
Innovative technology stabilises rock face
When Fulton Hogan was awarded a contract to remediate a steep unstable rock face overlooking the Port of Otago, it faced with a number of challenges
Reclamation of areas of the port during the 1990s had resulted in an unstable rock face at Flagstaff Hill (Observation Point) with several slips and rocks and boulders all-to-often falling to the road below.
For more than 20 years half the roadway at the foot of the face has been battered off with safety fencing to protect public roads and walkways. The unstable nature of the face meant daily inspections of the road.
Port Otago installed a shipping container wall across half of the road about the turn of the century, along with additional safety catch fencing to protect the public.
An adjacent log yard storage and handling area was reduced, to allow the public road to use part of the Port’s land for access.
Fulton Hogan purchased a Komatsu PC210LCi-10 intelligent Machine Control (iMC) excavator specifically for the project. iMC allows earthworks to be carried out to millimetre-level accuracy and is based around Topcon’s precision machine control capabilities, fully factory integrated within the machines.,
Consulting engineers WSP Opus were awarded a design contract to assess the underlying geology and develop a design for a cut slope with benches to remove the risk of further slips and rock falls in the area.
According to Grant Sime, Fulton Hogan’s senior project delivery manager in Dunedin, the contract scope was to work at height on an unstable rock face and strip off over 47,000m3 of clay and rock, and safely remove all the material from site.
“Before we work out where and how to start the physical work, the entire site needed to be accurately surveyed,” says Sime.
“With existing gradients of 70 percent and greater, combined with the instability of the ground, putting people on the slope face would have been extremely dangerous.
“Using our in-house surveying team, and external subcontractor Jared Reeves of Overview Surveying, we carried out a point cloud survey using a drone to understand what we were
Why Fulton Hogan chose the Komatsu iMC
Fulton Hogan looked at a number of different makes when considering which excavator machine control system to use on the project, says Senior Project Delivery Manager Grant Sime “With the Komatsu system, what really impressed me was the simplicity of the cab layout. In terms of the operator interface, it’s spot on,” he says. Operator Ray Te Huna says Komatsu iMC excavator takes a lot more people off the ground, so it’s much safer and easier not having to work around them. “I’m probably 50-60 percent quicker doing my work because I don’t need people to check it all the time. Now we just need the surveyors to come in and check the calibration a couple of times a week.” Fulton Hogan’s Otago-based surveyor Craig Kenneally also finds the Komatsu iMC concept makes his job much easier. “I like the Topcon operating system because you can put your drawing files straight into it, rather than having to use third party software. That’s one less step, and it’s easier than loading up terrain models,” he says. “We also had very good support from Komatsu’s Smart Construction crew. There’s a feature where they can log into the excavator’s system remotely and help us out where there’s any issues. Kenneally worked closely with operator Ta Huna setting up project protocols and loading the data. “It’s really nice that it’s got that feature where I can load the data externally whenever we get a new set of plans from which to work. “At the Port of Otago, we were using the excavator to quality assure all the time. Ray would go to a known point to check it was calibrated, and it was always consistent, always good. It was always very close to what we were getting off the drone and our other surveying systems,” says Kenneally.
up against.”
The pre-start drone survey was mapped against the required finished batter of 35 percent, along with three, five-metre wide benches at the top of the slope, so that the exact quantities of material to be excavated were known.
Given the safety and operational challenges of excavating on such a steep, unstable slope, Fulton Hogan sought input from excavator operators Ray Ta Huna and Kevin Patrick, described as two of the best operators in the region.
“It’s simple,” says Ta Huna. “When you are loading out from a digger, you sit on top of the material and load out while your mound comes down gradually.”
Sime says this response gave Fulton Hogan the basis for how to proceed, knowing the company had full engagement of its expert operators.
With the drone survey providing a highly accurate 3D overview of the existing site, and WSP Opus providing a 3D model of the required final design, making use of an excavator fitted with precision GPS-based machine control was the solution to this challenge.
“Having integrated Machine Control on Komatsu PC210LCi-10 was magic,” says Sime.
“Not having to set out pegs using manual survey methods improved efficiency ten-fold. And because we didn’t have to have a surveyor on the ground, it was much safer.
“In that type of environment, we had no option but to start at the top and work down, and there was no going back.
“The end result was without a doubt the best batter slope I have ever been associated with,” he says. “It wasn’t just a simple slope either; it was benched at the top, then battered and curved around to follow the line of the point.”
The designs for the batter were provided to Fulton Hogan electronically, then downloaded to the iMC excavator, so at all times it was working to the client’s designs.
“In addition, the client accepted the as-builts coming out of the machine,” says Sime.
“Then, when we completed the 47,000 m3 material removal, we were between 80 to 100m3 different compared with the original design -- it was so close. We are very proud of how close we got."
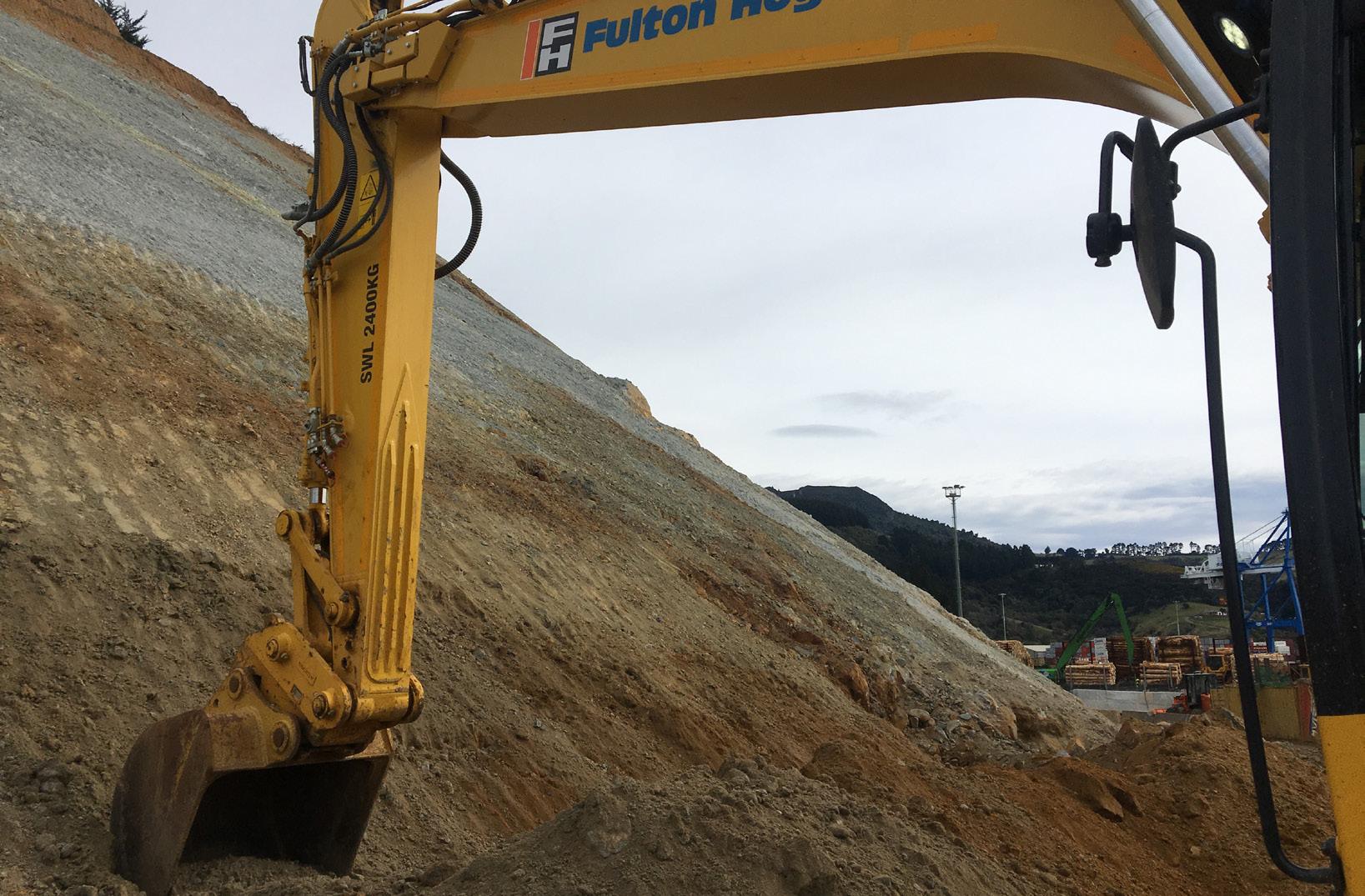