
28 minute read
Seacat on trial
Swedish boat builder Marell has won a contract to supply five fast patrolling and interceptor vessels to the Norwegian police.
The orders include Marell’s most recent model, the M12 RIB, which is based on the M15 platform that was awarded ’Interceptor of the Year’ by the Baird publication in 2019 and 2020.
As well as being in use as a sightseeing boat in the Arctic Ocean by Hurtigruten Svalbard, the MI5 was also chosen by Marine Police in Stockholm, and as a fire fighter craft in the Swedish capital.
The M12 combines a central helm station with an almost absent planing threshold, providing the helmsman with full control and 360o visibility at all speeds and in all conditions, says Marell.
The five boats will be deployed in different places in southern Norway for surveillance, search and rescue, boarding and control of recreational boats. They can carry up to 10 people plus equipment.
Two crew members can sit in the wheelhouse, and the low aft deck is suitable for divers, drones and life rafts as well as acting as a platform for hoisting and retrieving injured people. The boats have a wide beam, allowing easy passage on both sides of the wheelhouse, from bow to stern.
MARELL BOATS RECEIVES ORDER FOR FIVE RIBs
”The canopy is made of vacuum moulded GRP to reduce weight and noise, and to insulate the crew area from the effects from both cold and warm weather,” says Marell. ”The novelty of this design approach makes the craft suitable for both arctic and tropical conditions.”
The boats have a twin engine set-up, including the new Mercury 600hp V12 Verado engines with the ability to travel at speeds of more than 55 knots.
“Marell Boats has offered a robust boat, which in this procurement process best fulfilled the specifications published by NPSS,”
8 M12 NORPOL.534
says Marianne Haahjem, Department Director for Procurement and Legal in the Norwegian Police Shared Services. ”For example, the boat facilitates close cooperation between the helmsman and navigator during high-speed manoeuvering. It also delivers the best ratio of speed to load capacity. We expect this to be a solid addition to the Norwegian Police in the years to come.”
The boats should be delivered in the second half of this year and first half of next.
Steady at sea Steady at sea

Improve your working days

Install a powerful Humphree Stabilization system and working days on the sea will be steadier than ever. Our interceptor system lowers roll and slamming by up to 50%. And it feels like even more. It also reduces resistance. That means lower fuel consumption and less CO² emissions. Easy to install, easy to operate. Premium technology at affordable pricing. Help our planet and ensure a successful mission for you and your crew at humphree.com
For Humphree web page and international dealer network - visit commercial.humphree.com Scan QR code with your phone. We are just one click away.
FOR ALL BOATS, FAST FERRY, PILOT, POLICE, RESCUE, COAST GUARD, NAVY, MONOHULLS AND CATAMARANS.
A new 15m amphibious landing craft will be a size up from PDL’s existing 12m version.
Boat builder PDL Marine has received a request for a bigger, better amphibious landing craft to complement its existing 12m offering.
As well as its larger size, the new 15m vessel will carry a crane with a 2.5 tonne lift capability, a winch and capacity for 12 personnel plus two crew.
“Landing craft seem to be the ‘in’ thing at the moment,” said Business Manager David Rutter. ”Most clients want diesel outboard engines - they want more power, more torque, and with an outboard they can be unbolted and swapped, whereas with an inboard the vessel is out of action for a lot longer.
“We do get enquiries about hybrids but the problem is the cost - for a 24m transfer vessel you’re talking around £2.5 million for a conventional one, another million for a hybrid. New technology is always expensive, but it will come down.” Rutter could not say what the new vessel would be used for as discussions are still going on with the client, but he did say it can carry 11 tonnes on deck when in standard mode, seven tonnes when wheeled. ”The newer model can also be certified to MCA category 2 for operations up to 60 miles from a safe haven, so it is a ‘go anywhere’ type
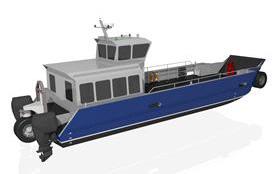
BIGGER AMPHIBIOUS BOAT ORDERED FROM PDL
Landing craft seem to be the ‘in’ thing at the moment. Most clients ‘‘ want diesel outboard engines - they want more power, more torque, and with an outboard they can be unbolted and swapped, whereas with an inboard the vessel is out of action for a lot longer
of vessel and has the option to change the wheelhouse layout to suit specific requirements,” he said.
“The Amphibian can be fitted with a wide array of engine choices, whether it be petrol or diesel outboards, IMO tier III inboard engines, and can sustain speeds up to 28 /30 knots.”
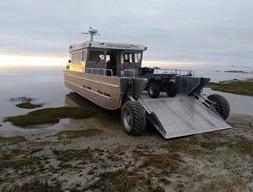
8 PDL Marine’s 12m landing craft Mandopigen
8 The new amphibian
will be 15m long and carry a crane

EFFICIENT ON BOARD MAINTENANCE
Jotamastic Smart Pack is the ideal brush and roller solution for smaller maintenance and repair jobs whilst on the go
OPTIMISED FOR:
Reduced paint consumption Brush and roller application Consistent coverage & Excellent flow Simple 1:1 mix ratio
Other products
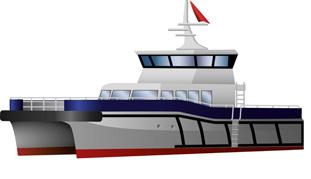
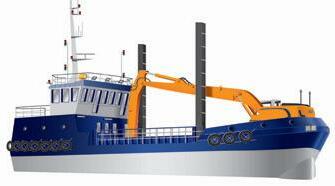

jotun.com
NEW HEAVYLIFT CRANE VESSEL UNVEILED
Dutch offshore equipment manufacturer GustoMSC has unveiled a new series of heavy lift crane vessels that it says are needed to address the needs of the rapidly growing offshore wind industry
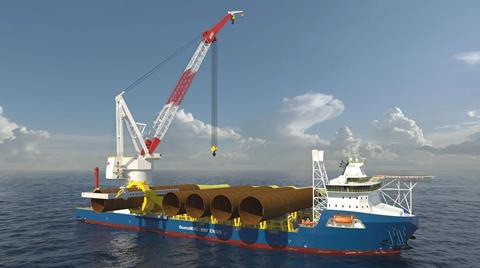
“With monopiles and jackets increasing in size and weight and the continuous need for efficiency in installation, a new generation of vessels is needed,” GustoMSC says.
The largest of the series so far is the ENSIS 5000 design, which is 220m long and 55m wide, with 9,500m2 of deck space, where it accommodates a 5,000t heavy lift crane with an increased load moment and lifting height in an optimised position to balance efficiency and flexibility.
“The vessel is designed around a combined upend hinge with a motion-compensated gripper that allows the ENSIS 5000 to take up to six XXXL monopiles in one trip,” says GustoMSC, which is owned by the American multinational engineering firm NOV. ”These capacities exceed present capabilities in the market. The draught is optimised to be able to operate from common marshalling yards, and a foldable A-frame allows mobilisation around the world.”
Two other designs - the ENSIS 3000 and 4000 - are based on the same principles but with different specifics: the 3000 is more compact, for installing smaller monopiles, pin piles or suction anchors; and the 4000 could work within an evolving US market as a Jones Act-compliant vessel.
8 ENSIS 5000 crane
vessel
Tetrahedron designs 130m crane
A consortium has been awarded cash to put together a prototype crane for use in installing rapidly growing wind turbines.
Tetrahedron is working with Jack-Up Barge BC, TNO, Shell and GE after a grant was awarded by the Dutch government along with a loan and investment from unnamed sources.
At the moment the company is not giving many details of its new crane, other than to say it will be a leg-encircling crane transported on a jack-up barge that can ’lift higher than a conventional luffing boom crane on the same foundation’.
“This will become apparent as a skyscraping structure when the prototype will be completed in 2024 in the Netherlands,” the company says. ”The prototype will be built to measure key aspects of the Tetrahedron crane’s structural behaviour, verify the design and test its resilience against hot-topic phenoma such as crane-deflection and a sudden loss of load. Moreover the full-scale Tetrahedron prototype crane is a proof to the wind industry of its potential of lifting higher than conventional cranes, without needing to build a completely new jack-up vessel.”
The world’s tallest crane vessel is still Heerema’s Sleipnir, which carries two Huisman tub-mounted cranes that each lift 10,000 tonnes and when fully extended rise up 220 metres.
Port Esbjerg orders 7th Liebherr crane
Denmark’s largest port, Port Esbjerg, has ordered a second LHM 800 crane, which will bring the total number to seven Liebherr cranes in the port.
It is already awaiting delivery of an LHM 600, and the pair together will provide a tandem lift of next-generation offshore wind turbines of up to 616 tonnes. The port will be the third port in the world to have two LHM cranes in its fleet.
Esbjerg port needs the extra lifting capacity as its current annual handling capacity of 500,000 tonnes of wind turbine components is bound to increase.
“The LHM 800 is the largest and most powerful mobile harbour crane in the Liebherr LHM portfolio,” says Liebherr. “The machine meets the ever increasing demand for mobile heavy-duty cranes in the maritime sector. A key driver of this development is clearly the wind industry.
“In a special heavy-lift version, the LHM 800 is capable of lifting weights of up to 308 tonnes and up to 616 tonnes in tandem mode with the intelligent Liebherr system Sycratonic.”
Sycratonic is a computerised assistance system for operating two cranes with one crane operator.
HYDREX REPLACES BOW THRUSTER ONSITE
Vessel repair firm Hydrex has reported a major repair to a ship at Rotterdam. The team of divers and technicians replaced a bow thruster for an OEM without using a drydock
The diver and technician team took all necessary equipment with them on one of their workboats, which are all fully equipped with hydraulic cranes, winches, nautical and communication equipment a well as a dive control room.
The team set up a monitoring station, then divers inspected the bow thruster and tunnel while initial preparations were made in the engine room to remove the unit. ”The divers’ first action was to take off the external thruster tunnel grids to provide access for removal of the old unit,” says Hydrex. ”Next, pad eyes were welded inside the tunnel to hoist the thruster unit up and down. ”The next step was to secure the gearbox with hoisting equipment. The team then disconnected the unit from the engine room, removed it from the thruster tunnel and brought it to the surface. ”We carried out the operation in close communication with the OEM involved. They provided a new thruster unit and prepared it for installation on-site. ”Because the thruster was fully assembled and prepared, it could be installed in its entirety without the need to create a dry environment in the tunnel as is required when the blades are installed separately. Our diver/technicians lowered it into the water and brought it into the thruster tunnel. The team secured the unit and connected it to the engine room. ”The operation ended with the removal of the pad eyes and the reinstallation of the thruster tunnel grids.”
Hydrex has stations in Antwerp and Rotterdam, which enables rapid deplpyment and increases flexibility, the firm says.
Because it performed the repair onsite, the owner was able to keep the vessel out of the drydock, reducing the time required for the repair to be carried out and allowing the ship to sail on schedule.
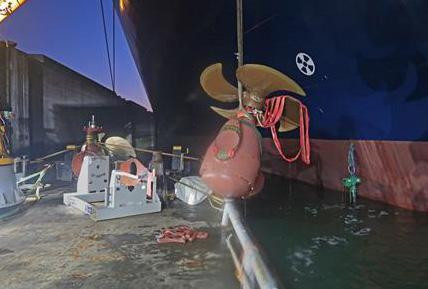
8 Hydrex
bow thruster replacement operation
HMS Lancaster upgraded for departure
BAE Systems has finished off required maintenance and repairs on one of the UK Navy’s frigates, the ’Queen’s frigate’.
HMS Lancaster has been sent back to work after a year’s upgrading and maintenance by BAE Systems, the multinational arms, security and aerospace giant based in London.
Work on the Royal Navy Type 23 Frigate included the swap-out of two diesel generators at the same time, which BAE says was ‘a rare and significant undertaking which was completed ahead of schedule’.
Upgrades were made to the bridge, messes and crew accommodation; new capabilities delivered across communications, navigation and defence systems; and planned maintenance of mechanical systems including valves and propellers, as well as hull maintenance and deck repairs.
”The hard work and expertise of the team throughout these major maintenance and upgrade periods alongside their agile responses to changing requirements and emergent work means HMS Lancaster will leave Portsmouth optimised for any role the Royal Navy should require of her,” said Dean Kimber, Head of Asset Management for BAE Systems’ Maritime Services business.
HMS Lancaster, which is the sixth so-named ship in the navy’s history, will now ‘spend a brief period on NATO tasking ahead of future deployments’, according to BAE Systems.
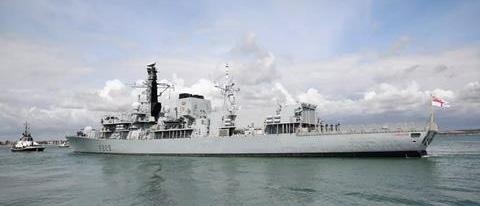
8 HMS Lancaster
NEW GUIDANCE ISSUED FOR NAVIGATING WIND TURBINES
As the number of wind farms increases around the UK coast, the government has launched guidelines to navigate around them safely
The UK government has published a new Marine Guidance Notice highlighting the issues to be considered when navigating in the vicinity of offshore renewable energy installations (OREIs) off the UK coast.
Most OREIs are of course wind farms, but wave or tidal power installations are also included under the term.
“Offshore renewable energy installations present new challenges to safe navigation, but proper voyage planning and access to relevant safety information should ensure that safety is not compromised,” the guidelines state.
Wind farms can affect the ocean in a myriad of ways, from obstructing tidal streams and creating eddies to changing the scouring of the seabed, which could result in unreliable depth information, thus affecting under-keel clearance.
“Some wind turbines have scour protection in the form of boulders and/or concrete mattresses placed around their base,” note 2.7.3 says.
They can also have an effect on communications and navigations systems, note 2.8 says, revealing that in trials in 2004 with the MCA and QinetiQ at North Hoyle, turbines produced strong radar echoes giving early warning of their presence, but at close range ’the trials showed that they may produce multiple reflected and side lobe echoes that can mask the real targets’. ”These develop at about 1.5 nautical miles, with progressive deterioration in the radar display as the range closes. Where a shipping lane passes within this range considerable interference may be expected along a line of turbines. Target size of the turbine echo increases close to the turbine with a consequent degradation of target definition and bearing discrimination. These effects were encountered on both 3cm and 10cm radars.”
The guidelines point out that mariners should be aware of the different navigational aids in place under particular circumstances, for instance during the construction phase, when special marks are used.
“Mariners should be aware of the likely presence of foundations without a yellow Transition piece, which present a significant navigation hazard and will be appropriately marked,” the guidelines, which can be accessed here, say.
One example of what is included in the guidelines are the Significant Peripheral Structures (SPSs), such as wind farm boundaries, which are marked with lights visible from all directions in the horizontal plane, and should be synchronised to display simultaneously an IALA ‘special mark’ characteristic, flashing yellow, with a range of at least five nautical miles.
“Aids to navigation on individual structures are placed below the arc of the rotor blades, typically at the top of the yellow section,” it says.
With tidal energy installations more complications arise due to the fact that they are invisible above water level.
The guidelines recommend that these are all marked by aids to navigation that must be visible to mariners from all relevant directions in the horizontal plane by day, and lit at night.

8 Navigating
around wind turbines
Buoys maximise wind potential
Two LiDAR buoys installed in the UK Celtic Sea will provide data to inform offshore wind developers about the best position to place wind turbines.
The LiDAR (Floating laser imaging, detection and range) systems, by French firm Akrocean, are about 60 miles offshore and will use laser technology to collect wind speed and direction, meteorological and oceanographic data.
The 5.1m x 2.4m buoys are part of Akrocean’s fleet of LiDAR and RADAR buoys, which are based on French firm GEPSTechno’s technology. The company says its systems provide several types of offshore measurement tools on stable and
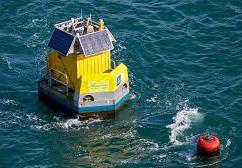
8 LiDAR buoys from Akrocean hybrid power platforms. Remote supervision is also a feature.
Celtic Sea Power, which is owned by the local authority, has been tasked with the development of a Celtic Sea for Floating Offshore Wind (FLOW) initiative to generate more offshore electricity. A number of agencies, including the European Union, are also involved in the project.
Neil Farrington, Strategic Offshore Development Manager at Celtic Sea Power, said: “The data from these Floating LiDAR systems will benefit Cornwall, South Wales and the wider South West by feeding into a bank grade regional wind resource model. This model will then be validated by external experts to support investment decisions for FLOW sites across the UK Celtic Sea region. It will also help reduce the time it takes to install floating offshore wind farms”.
AUTOMATION KEY TO BULK VESSEL EFFICIENCY
Norway’s Høglund Marine Solutions has been commissioned to supply advanced hybrid and automation systems to six hybrid bulk vessels
The contract has an option for six more sisterships, all on order for Finland’s AtoB@C Shipping.
AtoB@C and Høglund claim that these 1A ice class bulk vessels, due to start delivery next year, will reduce greenhouse gas emissions, including CO2, per cargo unit transported by almost 50% compared to AtoB@C Shipping existing ships. This would make the vessels the most efficient in the world in their class, with the monitoring and control systems acting as a major force multiplier in this achievement.
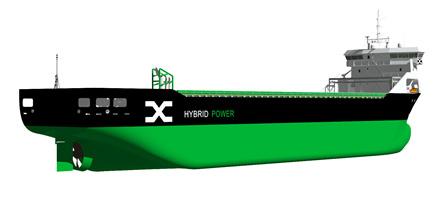
Emission free at port
The vessels will use batteries, shore-side electricity solutions and electric hybrid solutions to enable completely emissionfree and noise-free port calls, being able to arrive and leave port with electric power alone.
Høglund will supply both automation and hybrid systems for these vessels. Its Integrated Automation Systems (IAS) links alarm monitoring, control and power management systems, giving crew and shoreside teams supreme reliability and control over the vessel’s systems. The IAS will integrate with Høglund’s cloud-based ship performance monitor (SPM), using data from the automation systems to monitor performance in real time. Høglund’s hybrid systems include a 1000kWh battery for each vessel.
SPM is an adaptable monitoring software, designed to help manage and improve ship efficiency. Day and Mode Reports are automatically generated and sent to the Høglund Cloud Server together with LiveData from the vessel.
Mode reports are triggered according to operation mode (In Port, Transit, Operation). These reports contain important data such as fuel and power consumption, together with other ship relevant data such as vessel speed, wind, wave, draft and trim data. Høglund focuses throughout on lowering the installation cost, using existing sensors already available onboard.
For example, the SPM system can avoid the expense of flowmeters by calculating the fuel consumption with up to 98% accuracy.
Høglund’s expertise lies in gathering data from all types of systems onboard a vessel. All ships with Høglund solutions also have the company’s playback functions – making it possible for the crew to go back in time to troubleshoot historical events.
Additionally, with the LiveData solution Høglund makes
8 Høglund’s Ship Performance Monitor interface the playback function available onshore through its cloud portal, enabling: 5 Monitoring status of onboard systems through mirrored mimics 5 Remote troubleshooting of incidents with onshore playback functionality 5 BigData analysis and digital twin functionality 5 Calculations of customer-specific reports using historical data
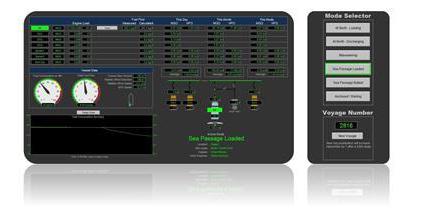
Recalculation
Data stored in the Høglund Cloud server is made available through a ‘Fleet Manager’ portal. Crew have write-access to reported data, making it possible to adjust Day- and Mode reports if incorrect data has been reported. With LiveData located on the Høglund server, new fuel and power consumption may be recalculated once date and time for the events have been manually adjusted.
Høglund CEO Børge Nogva said: “We are excited to be working on another hybrid project, which demonstrates how quickly the industry is embracing this technology. Our systems will not just be helping to drastically reduce emissions but will also give crew and shoreside teams far better insight into their vessel performance, as our SPM uses data from the automation system to give a clear picture of vessel operations and ensure reliability for the long term.”
AtoB@C Shipping Technical Director Janne Eklöf said: “We chose to work with Høglund because of their track record in delivering high-quality hybrid and automation systems, and their ability to work flexibly. We have worked closely with naval architects on the design of these vessels to create the most efficient ships of their type, and as such, we needed specialist expertise when it came to the systems that will make these vessels work.”
AtoB@C Shipping AB is specialist in carrying industrial products, project cargos and raw materials. Currently, the company operates 33 ice classed vessels in 3,000-6,000 dwt segment. The company operates several liner services from Scandinavia to UK and central Europe. Founded in 2000, AtoB@C Shipping is part of ESL Shipping Ltd.
The total investment value in the six ships is approximately 70 million euros.
8 Hoglund will
supply advanced automation systems to six hybrid bulk vessels
SEAGRASS MONITORED BY INVALUABLE USV SYSTEM
A new, non-invasive method to measure and monitor seagrass biomass on the seabed around England’s South West coast is being developed as part of an ongoing, collaborative project

The innovative technique is being trialled by HydroSurv and Valeport, working with the University of Plymouth and Natural England, and supported by a grant of more than £266,000 (€320,000) from Innovate UK’s Smart Grants programme.
It builds on the concept of the acoustic reflectivity of seagrass providing valuable information to characterise submerged aquatic vegetation. A full-stack solution consisting of a Valeport VA500 altimeter installed onto a HydroSurv REAV-28 Uncrewed Surface Vessel (USV), specifically developed for this project, provides a noninvasive, cost-effective platform to survey seagrass sites.
A large, validated signal library and deep learning algorithm, developed by the University of Plymouth, deciphers the survey data to predict seagrass distribution. The data is visualised and interpreted within a cloud application created by HydroSurv.
The USV platform facilitates accurate repeat surveys that can be compared to monitor temporal changes in seagrass coverage for the planning of protection and regeneration projects at biodiversity-rich worksites. The full solution, which was demonstrated successfully to project stakeholders for the first time in May this year, is set to change the way seagrass meadows are monitored in the future, complementing traditional diver surveys to cover much larger areas and enable rapid re-survey work as required.

Versatile 2.8m package
Launched in 2021, Hydrosurv’s REAV-28 aims to offer open water performance in a versatile 2.8m package. The USV is proving a popular choice for hydrographic, oceanographic and environmental data acquisition within inland navigation, ports and harbours or nearshore coastal worksites.
Built out of marine-grade aluminium alloy, the REAV-28 has proven stability and buoyancy combined with excellent seakeeping characteristics, which aim it squarely towards survey contractors and coastal scientists.
With twin Torqeedo Ultralight 1103 electric outboards, the REAV-28 may be configured with either two or four 915Wh propulsion batteries providing full dayworks endurance. The autopilot system supports steering in combined vectoring and rudder modes. It also provides monitoring of the outboard motor and battery status by integrating directly with Torqeedo’s TQ-Bus, providing alarms to notify operators when the batteries are low. A separate 1,280Wh general service battery offers uninterrupted power to the embedded survey PC and command, control and communications equipment.
Live monitoring and visualisation of the mission and sensor data quality control is performed from NaviSuite Kuda on a separate base control station PC. For docking, or when otherwise needed, it is possible to take control of the USV using a radio-controlled joystick.
Fiona Crouch, Natural England ReMEDIES Project Manager, said: “To effectively conserve and restore seagrass meadows we need innovative solutions to enable cost effective, repeatable surveys of established meadows, plus areas being restored through projects such as ReMEDIES, to monitor change. I’m really excited to see where this new technology will take us in supporting our seagrass conservation efforts.”
Emerging cluster
HydroSurv, Valeport and the University of Plymouth form part of a fast-emerging Southwest England maritime innovation cluster. The project partners are engaging with the Environment Agency and Natural England to develop the solution further, with a second phase of demonstrations planned for September.
Dr Tim Scott, Associate Professor of Ocean Exploration at the University of Plymouth, said: “When combined with the advantages of lightweight autonomous survey platforms, this new combined survey solution introduces a step-change in accurate and repeatable seagrass mapping.”
The UK has lost around half of its seagrass since the mid1930s due to factors ranging from seagrass wasting disease (SWD) and pollution to physical disturbance from the anchoring, launching and mooring of leisure boats. The £2.5 million LIFE Recreation ReMEDIES partnership ‘Save Our Seabed’, led by Natural England and funded by the EU LIFE Programme, was launched in July 2019 to protect and restore these sensitive habitats.
Seagrass meadows are a crucial part of the marine ecosystem and are increasingly being recognised for their essential carbon capture abilities. As well as being as effective at storing carbon as woodland, seagrass also provides vital habitat for young fish, seahorses and jellyfish. It also cleans surrounding seawater and helps to stabilise the seabed, thereby reducing coastal erosion.
8 HydroSurv
REAV-28 Uncrewed Surface Vessel (USV). Inset: HydroSurv REAV-28 Unmanned Surface Vessel (USV) surveying seagrass meadow
NEW RIG ANCHOR RELEASE DEVICE UNVEILED
A new device by Delmar Systems should save time, cut emissions and costs in moving oil rigs, the company says
Delmar’s mooring release device, the RAR Plus, has been installed and activated on the Diamond Offshore Drilling’s Ocean Endeavour rig.
The oil rig, around 290 nautical miles northeast of Aberdeen in Scotland, was moved between the Pan West and Tybalt well locations at Penguins Field, which is operated by Shell.
RAR Plus can disconnect a rig in one hour by acoustically releasing all mooring lines, saving hours of critical path operational time, compared to traditional methods, Delmar says. ”This allows the rig to move in shorter weather windows and maximises available weather windows to continue operating. The device also incorporates a mechanical back up release option, providing 100% (or full) redundancy. ”The RAR acoustic release needs fewer anchor handling vessels (AHVs) on hire and for less time, to move the rig, saving costs and CO2 emissions from the boats. Demand for AHVs is very high this summer, pushing hire prices up, so the use of RAR Plus could deliver even higher cost savings. As the rig is on critical path for less time, the operator further reduces costs and CO2 emissions from the rig.
The device was originally designed for avoiding cyclones or icebergs, until the company realised its function could be applied to quick-release for rigs and other applications. ”The Ocean Endeavour has completed drilling and testing operations at the Pan West well and has moved to the Tybalt well to carry out similar operations there,” says Delmar. “This is all part of a planned sequence of operations to be carried out before production starts next year.”
The release of the device coincides with a move to Aberdeen for the company.
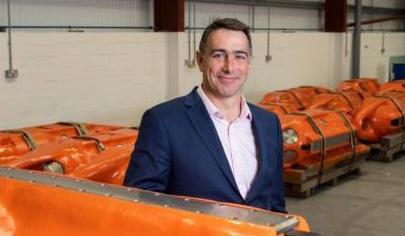
8 Delmar UK
General Manager Duncan Watson
Combatting underwater drug smuggling
A product development company is exploring novel ways to use autonomous underwater technology to help combat drug smuggling.
Bede O’Neil, strategic & international account director at UK-based Plextek, explains how submerged sensors can be used to monitor the increasingly innovative ways criminals are operating.
“The press recently reported that Spanish police had seized several underwater drones built to smuggle drugs across the sea from Morocco,” said Bede O’Neil.
“This seems to be the first capture of its kind and has increased international awareness of underwater crime. It is more technically difficult to monitor the sea than either land or air and is an obvious step for traffickers who are being pressured away from usual routes.”
The company, based in Essex, is no stranger to underwater technology, having worked in the sector for more than 20 years, designing a marine RF telemetry subsystem. However, the Spanish seizure signals a new, more covert threat, says O’Neil, who believes that autonomous sensors could be a low-cost, enduring way to tackle smuggling.
“There could be a discovered asset, like a haul of drugs, that is stored stationary under water for a period of time,” he said. “Police need to know the exact moment smugglers arrive back to collect the drugs. A sensor system provides the basis for a highly cost-effective covert surveillance capability.”
The concept involves the deployment of a low Size Weight Power and Cost (SWaP-C) node fitted to the drugs. If disturbed and brought to the surface, the beacon relays its position enabling tracking.
The technology is in its early stages, but with underwater smuggling becoming more prevalent, wider rollout is anticipated.
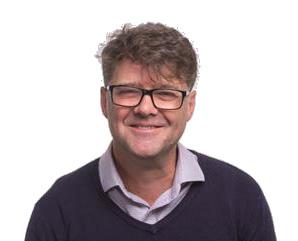
8 Bede O’Neil,
strategic & international account director at Plextek
GEOPHYSICAL SURVEY FIRST FOR FUGRO
Fugro’s new geotechnical system has successsfully completed its first offshore wind project
The Blue Snake geotechnical system was used at the IJmuiden Ver (Noord) V and VI windfarm sites as part of a geophysical survey package for the Netherlands Enterprise Agency (RVO).
“Supporting our partners to innovate is one of the ways to jointly improve our site characterisations for offshore wind. With the 21 GW planned on the Netherlands’ Offshore Wind Energy Roadmap 2030/31, offshore site investigations need to speed up as well,” said Michel Vrolijk, consultant offshore wind energy at RVO. ”RVO is pleased with the implementation of Fugro’s Blue Snake, because of the ability to perform a vibrocore in combination with a CPT in a single deployment. The short fixed distance between the CPT and vibrocore will also allow for better correlation between data, this could improve data interpretation.”
High-tech
Using a third party vessel, 25 co-located cone penetration tests (CPT), thermal cone penetration tests (T-CPT) and high performance corer (HPC) tests were taken using the Blue Snake system.
The system integrates CPT and sampling technology, achieving enhanced data quality, safety and efficiency. Tests are taken consecutively, at a fixed distance, enabling highquality data acquisition and improved data correlation.
With the integrated testing approach and the significant reduction of manual and crane handling, productivity is improved whilst health and safety risks are reduced.
“Having the support and commitment from a client such as RVO is highly appreciated. Their willingness to trial our new innovative equipment, resulted in the successful delivery of geo-data in a safe, sustainable and efficient manner.” said Sven Plasman, principal commercial manager, Fugro.
The IJmuiden Ver V and VI areas are in the northern part of the IJmuiden Ver windfarm zone and will be able to accommodate around 2 GW of offshore wind capacity, on top of the 4 GW of capacity already planned in the IJmuiden Ver zone.
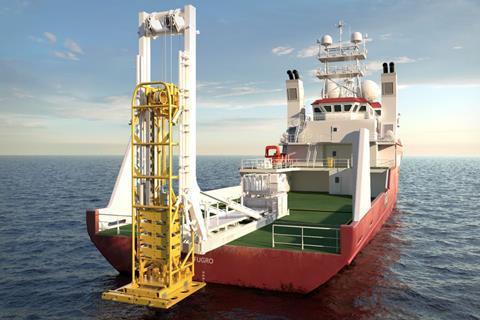
8 Fugro Blue
Snake integrates CPT and sampling technology, achieving enhanced data quality, safety and efficiency
UK seabed mapping centre opens
The new UK Centre for Seabed Mapping (UK CSM) should enable an increased coverage of seabed mapping data as well as access to it for working groups.
Members will be able to contribute to national and international data collection and collaboration ’to enable the diverse community of marine geospatial stakeholders to come together to deliver significant, sustained and strategic benefits to the UK’, according to a statement.
“Quality marine geospatial data is essential for almost every activity undertaken in the marine domain, including maritime trade, environmental and resource management, shipping operations, and national security and infrastructure,” said David Parker, Head of Hydrographic Programmes at the UK Hydrographic Office.
“Due to the UK’s role as a world leader in seabed mapping, there is a clear opportunity for us to establish a collaborative seabed mapping community which coordinates the collection, management, and access of publicly funded data. More interoperable and usable data will support more informed ocean governance and policy, which in turn will support greater innovation and prosperity.”
The UK CSM was created at the UN Ocean Conference in Lisbon last month. The aim of the conference was to propel science-based solutions ‘that focus on starting a new chapter of global ocean action’.
