
10 minute read
Supply chain woes
OFFSHORE, THE WEAK LINK IS THE CHAIN
The ability to assemble successful supply chains will determine the future success of the floating offshore wind industry, says Mark Goalen, Director of Offshore Engineering at marine consultancy Houlder
In November, the news broke that Shell had cancelled the construction of a demonstrator floating wind farm offshore France. Shell cited supply chain issues among the key reasons for abandoning the project.
Despite its success and high ambitions, the industry is clearly still in its infancy. Barriers to full commercialisation exist, and key among them, as Shell and Equinor said, are supply chain constraints. Collaboration will be required to realise the industry’s full potential as it moves forward.
At the moment ScotWind - which leases the seabed around the northern UK - has 14 floating projects, and these too will face supply challenges. ScotWind had assumed it would mostly use 18-20MW turbines, but these are not yet available, so it’s a bold assumption on the developers’ part.
For a 10-year period (2029 – 2039) for manufacturing and installations, this requires approximately 125 units to be made each year. Critically, many Scottish ports do not have the required areas to deliver commercial-scale floating offshore wind without significant investment and infrastructure development. Decisions on floating foundation type are yet to be made, and until then the supply chain can’t form, and investment cannot be made in port infrastructure.
Disruptive technologies
There are many floating foundations to choose from, but they can typically be categorised in four main structure types: spar buoy, tension leg platform, semi-submersible platform, and square barge.
Most demonstrator projects have used a conventional wind turbine generator, which was originally designed for onshore or fixed wind. Given the number of known challenges associated with operating and maintaining these conventional turbines in a dynamic environment, it is expected that disruptive technology such as X1 Wind’s weather-vaning downwind concept, SeaTwirl’s vertical axis turbine and SENSEWind’s self-erecting nacelle system to gain traction and direct the evolution of the industry.
To date, demonstrators have mostly been driven by the floating structure designed by themselves to prove their technology, rather than to provide developers with an objective demonstration of each technology for a given site and environmental conditions.
As such, there is still a fundamental need to identify the best technical solutions for each planned floating site that will minimise costs, risk and inefficiency for developers.
There will not be a single definitive foundation type. A developer will select a foundation most suitable for the wind farm they are developing, and that will vary from site to site, especially since a developer’s portfolio is likely to be global.
Advanced floating foundation selection involves analysing a combination of technical and operational factors and, arguably, operation may have a bigger impact throughout the asset’s lifecycle.
Port infrastructure and O&M
For ports to support a new development, location, infrastructure, water depth, available space for fabrication and storage are all key. Taking the UK as an example, current options are limited. Individual ports do have plans to invest, but none will be sufficient to cover all options, which means there is a risk that significant parts of the manufacture could go to Europe or Asia. This lack of port infrastructure seems to be driving the choice of concrete over steel foundation, with concrete structures requiring a less skilled workforce. These structures only require the moulds and raw materials, not the specialised welding equipment or qualified welders. Steel can be prefabricated elsewhere and assembled, but that builds in additional fabrication risk and requires additional transport of large components, increasing costs. Operations and maintenance is an even bigger challenge facing the industry.
Floating foundations are currently towed back to port for maintenance and repairs – but this will not remain viable or economical as wind farms are placed further offshore and the distance to O&M ports increases.
It is vital that O&M on-location is developed, because the risk and costs associated with connection, disconnection and transport of the wind turbines will prove too high over time. A combination of modifying the turbine, as well as developing the tools and vessels required to support this O&M phase, will be crucial to the success of floating wind. Having the right expertise and advice available in the initial phase of the project ensures that developers gain a holistic understanding of the processes, equipment, vessels, and operations involved from the outset. Independent marine specialists can provide consultancy on the costs, timeframes, emissions and risks of each floating wind technology.
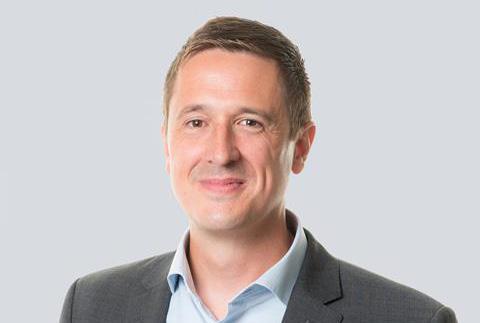
8 Mark Goalen
FIRST TURBINE INSTALLED WITH ‘REVOLUTIONARY’ METHOD
Three years after offshore wind firm Parkwind announced a turbine installation would be carried out using a floating method, the first one of 27 has been completed
Parkwind, Heerema and Vestas are working together on the Arcadis Ost 1 site, marking ‘an industry premiere’ in wind turbine installation on a commercial scale, the partners say.
“This innovative method has two main advantages: the first is zero seabed interaction, especially important in areas of significant water depth or challenging soil conditions; the second advantage is a shorter installation cycle,” says Parkwind.
Using Heerema’s crane vessel Thialf, the pre-assembled wind turbine tower was lifted to the foundation by one crane while the second crane simultaneously assembled the wind turbine generator (WTG). The assembly was done with a lift on a ‘support’ tower on the vessel itself, where a stable platform developed by Heerema allowed a fast, secure assembly of the nacelle and blades, Parkwind says.
“Once pre-assembled the complete RNA (Rotor Nacelle Assembly) is lifted as one piece onto the WTG tower in only one lift,” Parkwind said. ”The pre-assembly process on board Thialf ensures full control, thereby guaranteeing a safe and highly reliable installation environment.
“The reduced number of lifts between the vessel and the structure eliminates key risks of the floating installation.”
In total, 27 turbines by Vestas will be installed, with a total projected electricity generating capacity of 257MW. ”The floating installation method is the perfect example of what it takes to set new industry standards, and new standards mean new opportunities for offshore wind globally. Arcadis Ost 1 will soon be one of the world’s most advanced wind farms, thanks to its design, components,” said Parkwind CEO Eric Antoons.
In August, the first major step was taken when DEME, using its offshore installation vessel Orion, put the first monopile foundation in place, The Baltic Sea wind farm is due to be fully commissioned next year.
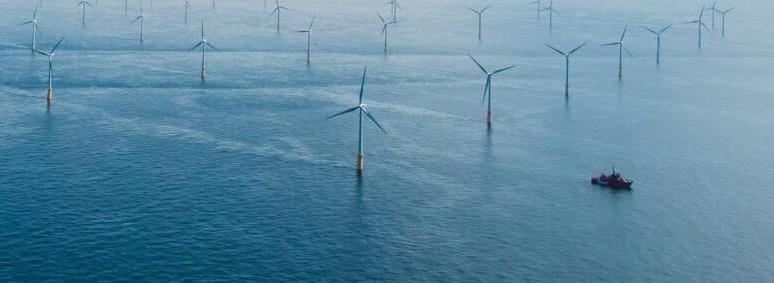
8 Parkwind
First power generated at Hywind Tampen
Power has now been delivered to the Gullfaks A platform in the North Sea from the first of 11 wind turbines.
Hywind Tampen, Norway’s first floating wind farm and so far the biggest in the world, is predicted to be able to meet about a third of the electricity needs of oil and gas operations owned by Gullfaks Snorre.
As well as being the largest, it is also the first floating farm to power oil and gas operations.
Equinor says that when fully operational, the 11 turbines will generate 88MW, which is half of the current total of floating wind generation in the world. ”This is an important contribution towards transforming the Norwegian continental shelf from an oil and gas province to a broad
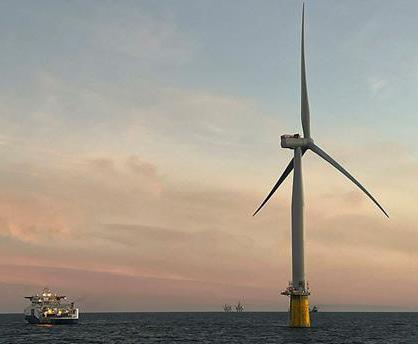
8 Hywind Tampen has begun generating power
energy province,” said Kjetil Hove, executive vice-president for Exploration and Production Norway with Equinor. ”Just a few years ago, no one would have believed that offshore platforms could be powered by electricity from floating wind turbines. Well, now we have started.”
The €272 million project has been funded by financial services multinational Enova (€218 million) and the Norwegian government’s Business Sector’s NoX Fund (54 million).
Hywind Tampen is 140km from shore in water depths of between 260 and 300 metres. Seven turbines should come online in the next few months, with the remaining four to be installed next year.
Earlier this month, Equinor said it was considering the Celtic Sea off Wales for floating wind as the Crown Estate will in 2023 launch another seabed leasing round around the British Isles.
NORTH STAR SECURES MILLIONS TO EXPAND SOV FLEET
Offshore infrastructure support services provider North Star has secured major financing to expand its renewables fleet as Scotland, where it is based, moves towards its net zero goal
The £140 million (€161 million) financing package includes commitments from RBC Capital Markets, BRIDGE (Edmond de Rothschild), IFM Investors and the Scottish National Investment Bank, which has pledged £50 million (€58 million).
The package has come soon after the firm entered the offshore wind market last year, when it won four long-term charter SOV (service operation vessel) contracts for Dogger Bank Wind Farm, which at the moment is set to be the world’s largest on completion in 2026. The SOVs, financed by a £127 million facility from Allianz Global, are due to be delivered from next year.
It also follows investment by the bank into the Port of Aberdeen, which it calls a ‘hub for North Sea offshore services and, increasingly, new offshore wind farms’. ”Raising this level of corporate funding from the bank and other investors, as well as the ongoing backing of Partners Group, provides us with the means to continue to add to our growing vessel fleet and supports our ambition to be a leading player in the European SOV market,” said chief strategy officer Fraser Dobbie with North Star, which is owned by private equity firm Partners Group.
“The £140 million secured today secures the capital required for us to continue our new-building programme in the year ahead, whilst providing us with the flexibility to continue to expand these facilities to meet our strategy of 40 new SOVs by 2040.”
Crown Estate Scotland, which leases the seabed around the country to offshore projects, said in its latest annual report in November that a record level of revenue had been generated for public spending ‘with the potential for billions of pounds to be invested in Scottish offshore wind’.
The number of seabed agreements has reached 20, it says, with a target of generating 27.6GW of electricity.
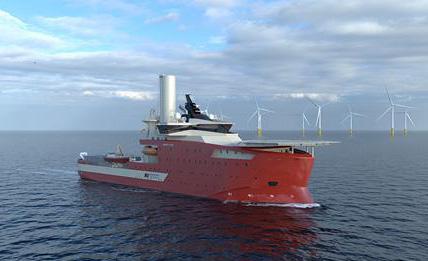
8 North Star has
secured £140m financing to progress its offshore wind fleet
Schottel steps into China’s massive wind market
As Schottel wins a deal to supply Chinese firm Ouyang with its thrusters, reports have come out about a wind farm being planned that could power Norway.
Schottel has announced a deal with Ouyang Offshore in Shanghai to install four wind turbine installation vessels (WTIVs) with its azimuth thrusters, with delivery beginning this year and finishing in June 2023.
Each vessel will be equipped with two electrically driven RudderPropellers (SRP) type 430 azimuth thrusters and two TransverseThrusters type STT 4.
“The 360o steerable SRP combines maximum manoeuvrability and bollard pull
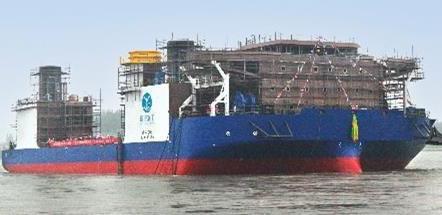
Credit:Schottel
8 Ouyang Wind transfer installation vessel with outstanding course stability during free sailing to provide powerful thrust in the chosen direction at all times,” says Schottel.
The WTIVs are 90m x 42m, can accommodate 100 people and can install turbines in depths of 60 metres.
As China’s offshore wind industry develops, opportunities for European firms like Schottel are bound to increase. The country already has the world’s most wind farms and plans revealed last month show it is set to grow massively in years to come.
A report by news agency Bloomberg and published by the Institute for Energy Economics and Financial Analysis (IEEFA) said an industry publication had revealed plans to build a wind farm off the southern coast that would be big enough to power Norway.
The 43.3GW project will be built off Chaozhou, in the Taiwan Strait, by 2025, the report said, quoting a copy of the city’s five-year plan.