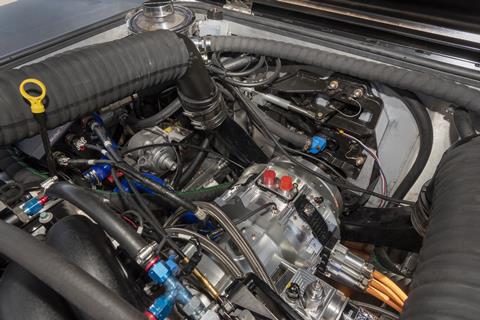
14 minute read
Ground-breaking
NEW-CONCEPT RIB RUNS ON BATTERIES, PETROL OR METHANOL
A fascinating concept in marine methanol hybrid propulsion could redefine the way vessels, particularly small commercial high-speed craft, are powered, writes Jake Frith
UK company and Seawork 2022 exhibitor Mathwall has a strong background in motor racing up to Formula 1 level, and is especially involved in historic racing engines, particularly Ford engines.
Genesis
A lot of racing engines run on methanol, which acts as a carrier for hydrogen, but from a marine decarbonisation standpoint it also has roughly double the energy density of pressurised liquid hydrogen, so it will allow boats to have an acceptable power-to-weight ratio and high-speed range that hydrogen boats struggle with and full electric boats are many decades away from providing. Mathwall Marine, and related consulting company PurpleSector, with their extensive methanol and hybrid experience, have found themselves in a good position to develop a hybrid marine propulsion system that can run on methanol, petrol, battery electric or a combination of these.
The technology of both an internal combustion engine and a pure electric drive gives the benefit of both technologies to achieve power, lower CO2 emissions and range of use that could not be achieved by any of the technologies on their own.
The venture is the brainchild of boat owner, Mathwall CEO and former Maclaren Chief Powertrain Engineer Mark Mathieson MBE.
This combination of internal combustion and electric to get the best of both worlds is well trodden ground for Mathieson, as he led the development of the Maclaren P1 supercar’s epoch-defining and multi award-winning hybrid drivetrain, which in concept is not a million miles away from this one.
Mathieson and the team’s racecar backgrounds also meant that, with some financial assistance from Innovate UK, and with the help of project partners, the prototype RIB shown here went from drawing board to high performing onwater test bed in just seven months.
This test bed, called the CHAMP Project (Clean Hybrid Alternative Marine Powertrains) was funded by Innovate UK as part of the government’s Clean Marine Demonstration Competition. The project aims to demonstrate the potential performance that can be achieved with the introduction of hybrid technology in recreational, defence and small to medium-sized commercial vessels.
Halfboard™
Fundamental to the success of the project so far has been a new, trademarked and patent-pending technology that Mathwall is calling the Halfboard, which gets its name from being halfway between an inboard and an outboard.
The Halfboard places the weight of the drivetrain in a continued watertight, buoyant planing surface bolted onto the boat’s existing transom. It is another racecar technology, as drivetrains are often mounted in a similar way in the rear of racing cars for strength, lightness, rapid swapping out for faster development.
The system means that existing boats can be repowered easily: it’s just a hoist and a number of bolts – not much more work than changing an outboard. In the case of RIBs, the tubes are extended further rearwards to accommodate and stabilise the unit.
Of course, different RIBs have different deadrise angles at the transom and different transom angles, arrangements of planing rails etc., so to get a fair hull continuation on all hulls, some degree of custom fabrication work will be required.
For the CHAMP project’s single boat prototype, Mathwall has partnered with Ballistic RIBS and Portsmouth’s Trafalgar Boat Club, and Mathieson believes that partnering with boatbuilders to ensure Halfboards exactly fit certain hulls could be one route to market.
Another could be to provide less bespoke halfboard units that are slightly shallower than the transom and mounted a little higher, thus adding the further high-speed efficiency benefit of an aft planing step.
As it is, the halfboard prototype with its LS3 engine (a V8 monster that most commonly lives under the bonnets of Chevrolet Corvettes) has been a great success.
It’s a big engine and hence the longest possible halfboard that will ever likely be made. Production models will all, most
8 LS3 V8 runs
on gasoline and methanol
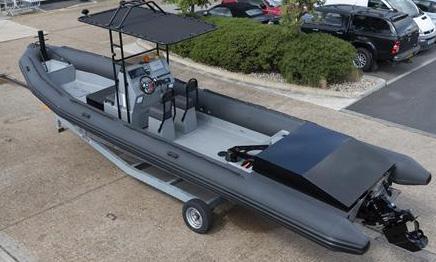
8 RIBs require
tube extension to accommodate Halfboard
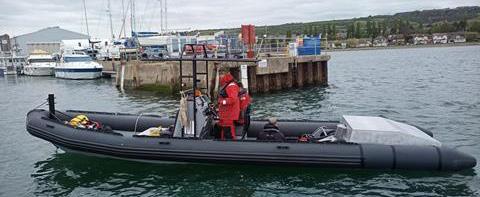
likely, be shorter. This long construction, and the high power, tests the loadings in the worst possible scenario, so according to Mark, it’s the best end of the spectrum to start from, development-wise.
What it brings to the party that an outboard does not is an increase in waterline length for better sub-planing trim and economy; plus the weight that is added to the boat through the hybrid system is more than supported by the added buoyancy of the increased hull and tubes, so increasing the weight of the boat does not drag it down further in the water, creating a greater hull inefficiency. A full hybrid system like this could also simply not be built into anything as compact as an outboard motor. Mathwall quotes a possible drag reduction of 28% with the halfboard concept compared with adding the extra weight of a similar hybrid system to an unchanged hull.
What it brings to the party that an inboard does not is easier adding as a retrofit or upgrade to an existing boat.
Mathwall believes that as well as retaining an element of fossil fuel, or ‘Flex Fuel’ use for certain parts of the duty cycle, an effective marine energy transition also has to consider how new technologies can most easily be integrated into existing hulls.
Complex control
A complex control system allows for the optimum use of battery power and methanol, based on how an operator intends to use the boat using real-time data and feeding back to allow for offline monitoring and future improvements.
Using a 63kWh battery, the boat has a range of up to 30 nautical miles in full electric mode and with a 420 litre methanol fuel capacity, 230 nautical miles range is easily achievable with a sustainable fuel source and up to 360 nautical miles in eco mode.
In the CHAMP project prototype, the internal combustion engine provided circa 450 horsepower with the hybrid drive motor adding an additional 150 BHP (and up to 200 BHP for limited periods), either for additional top end power, or more likely, quiet zero carbon operation at harbour speeds.
Methanol is an environmentally sustainable fuel source identified on the Government’s Maritime Plan, but at present has limited supply dockside. By calibrating the engine to be able to run on pure methanol or gasoline or any blend of the two, Mathwall has reduced the issue of methanol not being available dockside. This means the technology can be rolled out immediately, even though access to methanol dockside is still limited at this time.
There are some elegant engineering touches that Mathwall has been able to demonstrate with the CHAMP project.
One is the closed freshwater cooling circuit for the hybrid drive motor, which is shared with the engine’s cooling circuit. This means if the electric motor is used, as will be likely, to get the vessel off its berth and within a harbour for some minutes, the internal combustion engine has been gently warmed up by the spent heat from the motor and is already at operating temperature.
It can be used at wide open throttle if necessary from the moment it kicks in without worry of increased wear or damage.
Engaging
Speaking further to Mark Mathieson, it’s clear that engaging with marine industry stakeholders, particularly at events such as Seawork, has been a key part of the project.
“We learn things and get to hear of opportunities when we get closer to potential end users of the technology,” he said. “For instance, it was recently pointed out to us that ecotourism could be a great use of boats powered with this system. The energy density and grunt to get out to a location can be provided by internal combustion, then the vessel can switch effortlessly to silent battery power when close to sensitive wildlife.
“We have also had the opportunity to successfully show our abilities when it comes to getting concepts built. Out of 55 projects funded by the Clean Marine Demonstration Competition, we were one of two that actually got a vessel on the water by the end of the funding period.
“Now Innovate UK would like us to find companies we can partner with to take things further with multiple prototypes for multiple sectors with different duty cycles.
“We’d like to look at the leisure and superyacht tender markets, but it’s clear that commercial marine will most likely provide our first customers, with the RNLI, the defence sector and harbourmasters showing early interest. We’re keen to talk to any potential partners who are interested in the concept, from boatbuilders to potential future end users.”
8 CHAMP prototype in on-water testing
PEEL PORTS ISSUES £17m TENDER
Scotland’s most important west-facing freight port is to get its biggest investment in cranes to date.
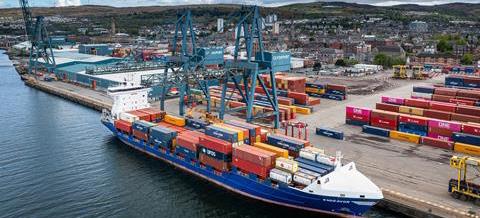
Greenock Ocean Terminal is to get a £17 million (€19.8 million) boost with two new cranes courtesy of owner Peel Ports.
It is the largest single investment in the container terminal since it opened in 1969 and comes amid ongoing construction of a multi-agency Border Control Post, which has been put in place to accommodate all commodities in the face of changing legislative requirements following Brexit, Peel Ports says.
The terminal has also increased its storage capacity for containers, and as part of the changes will later decommission one crane and replace it in the short term with a multi-docker crane that specialises in handling forest products.
Once the two new cranes are completed and on site - which could take up to 18 months once the contract is awarded - two other cranes will be decommissioned.
“Throughout the last two years, we have seen some significant changes in the supply chain and trading patterns due to COVID-19 and Brexit and by investing in our infrastructure, we are ensuring the future of the terminal,” said Peel Ports Clyde Port Director Jim McSporran.
“Greenock Ocean Terminal is a mainstay of the local community and it’s important that we look towards the future and continue to provide job prospects and economic opportunities for local businesses.”
8 Greenock Ocean Terminal is to get two new cranes
Leg encircling crane contract
Huisman has announced a contract award from COSCO Shipping (Qidong) Offshore Co Ltd for the design and construction of a Leg Encircling Crane (LEC).
The crane will be installed on the new build F-class jack-up vessel of Cadeler, a key supplier within the offshore wind industry for installation services, operations and maintenance works.
“We are thankful and proud that, with this third order, we are able to make a significant contribution to Cadeler’s fleet expansion. We look forward to delivering the cranes in the coming years and, as a committed partner helping Cadeler to boost installed offshore wind capacity around the world,” said David Roodenburg, CEO of Huisman.
The contract award follows last year’s
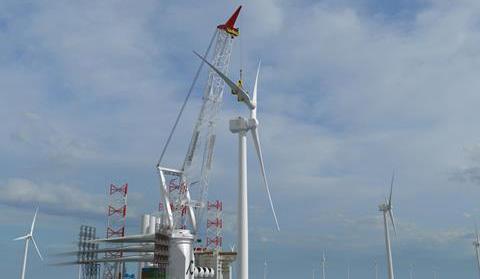
8 With this crane, Cadeler will be capable of
installing foundations and wind turbines for next generation offshore wind projects worldwide
contracts for two identical 2,600mt Leg Encircling Cranes for Cadeler’s X-class vessels.
With this crane, Cadeler will be capable of installing foundations and wind turbines for next generation offshore wind projects worldwide.
The F-class vessel features a unique design, allowing the vessel to convert from being a foundation installation unit to a wind turbine generator installation vessel within a short period of time.
Huisman has designed its LECs to meet the requirements of the continually developing offshore renewables sector. The cranes are lightweight yet robust, have high positioning accuracy and are energy efficient, contributing to a reduced emissions footprint during the installation of increasingly large turbines.
Scope of work for Huisman consists of the design, engineering and construction of the LEC at its production facility in Zhangzhou, China.
The cranes will be commissioned in 2025 at COSCO’s shipyard in Qidong, China, where the F-class vessel will be built.
STEAMSHIP BACK TO WORK AFTER TWO YEARS
The UK’s largest working steamship has returned to service after its annual drydocking, writes Graeme Ewens
After languishing alongside its Southampton mooring for two years during the pandemic lockdown, the 1955-built SS Shieldhall was drydocked at A&P Falmouth for maintenance and repair but needed extra work in patching some 10m2 of the keel plating that ultrasound scanning had shown to had corroded.
Built in 1955 by Lobnitz in Renfrew, the vessel was constructed to an obsolete design based on 19th century technology and using many features similar to the ill-fated Titanic.
Shieldhall was built to replace a vessel of the same name operated by the Glasgow Corporation to carry treated sewage sludge from the city to be dumped in the Clyde estuary. For economic reasons the design used old plans from the original 1910 vessel it replaced, and the boilers are smaller versions of those used in the Titanic. The steamdriven emergency steering engine and bridge binnacle are of the same era.
The ship is twin engined with one rudder, with loa of 268ft, 45ft beam and 13’4” draft. Its original tonnage was 1792 gross, 998.9 registered and 1840dwt. The 5/8th (15mm) hull plating was rivetted above the waterline and welded beneath.
The reciprocating steam engines were built to run on Heavy Fuel Oil but she now runs on diesel, which means a lot more leakages to be kept under observation. The 450bhp engines run with 120 psi pressure at 104 degrees F (42oC). Maintenance usually includes cleaning out the boilers and taking valves apart to clean them.
Shieldhall was designed to carry 80 passengers on day trips, most of them on the open decks with limited space in the saloon.
Today it carries 200 day-trippers, who are invited to visit the engine room and wheelhouse, each with a fine array of brass telegraphs, dials and gauges.
Annual inspections include renewing the passenger certificate and every five years a lightship survey is carried out to verify any changes in lightship displacement and longitudinal centre of gravity.
The cargo tanks, which take up most of the hull, are now used for ballast in midships with a workshop, general storage and sewage plant.
Drydocking used to be a simple matter of regular repaint, certificate renewals and safety checks, but as MCA controls have become more demanding the list of tasks has increased.
This year some of the porthole glasses and the shutter seals needed to be replaced. The sewage plant was removed, while its base was strengthened to allow better access; and the aft mast needed rewiring, but the major works, including the keel plating and painting, with five coats of anti-corrosive primer and antifoul, which is now blue rather than red, were below the waterline.
It is guaranteed for 10 years and requires only the occasional washdown.
After being transferred to the Southern Water Authority in 1977 the ship was decommissioned in 1985 and is now owned by the Solent Steam Packet Company, a charity whose president is Sir Robin Knox Johnson and chair John Rose, a younger Brother at Trinity House.
The costs of maintaining and running the ship are met by bequests and grants. A recent award of £196,000 (€226.5 million) from the Heritage Lottery Fund covered 70% of the costs incurred at Falmouth A&P dock, where the total bill, including bunker charges, came to around £250,000 (€289,000). The ship has a permanent berth in Southampton docks provided by ABP.
The vessel takes passengers on short cruises around the Solent from May through to September and has been as far as Glasgow, Bristol and the Netherlands.
The volunteer crew includes two chief engineers who hold steam tickets, some railway firemen, metal workers and exMerchant Navy masters and mariners. The dedicated deck crew tackle regular chipping and painting through the winter. There is a programme of training for Sea Scouts and local schools. Fire and rescue and ambulance crews also train in enclosed spaces exercises, while police and Coastguard carry out anti-terrorism exercises, sometimes landing helicopter winch crew on the deck.
This year’s annual visit to Falmouth was not trouble free. While entering the inner harbour a commercial-sized drone dropped out of the sky onto the deck, fortunately without hitting any person or sensitive equipment.
Work was further set back a few days before scheduled undocking when a storm blew away the protective sheeting, causing debris and litter to stick to the wet undercoat while the top coat required another 48 hours’ drying time.
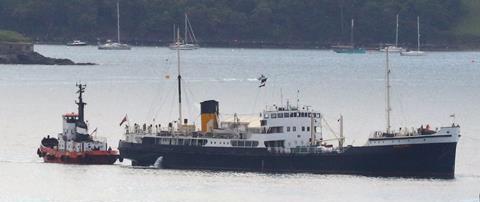
8 Shieldhall arriving
at Falmouth
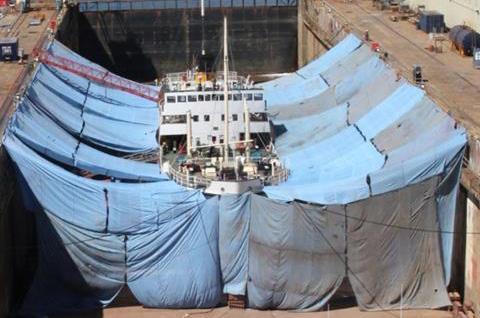
8 Under repair - SS Shieldhall, before returning to work