
4 minute read
ABOVE THE WAVES: ECMA WINNER ARTEMIS TECHNOLOGIES
Last summer, Artemis Technologies unveiled the world’s first commercially-viable zero-emissions electric foiling workboat at Seawork, for which it scooped the Spirit of Innovation and Vessel Build & Design awards
Since then, company founder Dr Iain Percy OBE says the firm has doubled in size and the MCA has granted it a Cat 2 workboat licence – up to 60 miles from a safe haven – which means it has been tested in big seas and much harsher conditions, validating simulations and reassuring the company of its central principles. Debbie Mason spoke to Iain Percy – a double Olympic sailing gold medallist – about a busy few months for Artemis Technologies and what’s on the horizon.
Snowball effect
“We’ve validated a lot of the data with an identical sister ship, so we’ve come back and measured real flows of petrol on the test vessel, the control vessel, and the electricity of ours at sea,” says Percy. “On the second day of testing, our electric foiling workboat was using 6.5kWh per nautical mile whereas the sister ship was using more than 52kWh of petrol per nautical mile, at a speed of 17 knots. This is a proven 90% saving of fuel that’s been measured and tested rather than predicted.”
It’s because of what Percy calls the snowball effect – the hydrofoil reduces the drag, which means less battery capacity is required, which means the boat is lighter – and so on. This is the crucial difference between his hydrofoil and the Boeing Jetfoil of the seventies, he says.
“The challenge in the seventies to the nineties was that it didn’t save much fuel, because the effect of drag of a loaded surface-piercing hydrofoil is very high drag.
“Where Boeing spent 10 years developing one boat, we spent 10 years developing computational tools that allowed us to do it on our second, third and fourth class of vessel. Computational simulation and the years we’ve put into developing it has allowed us to bring new variants in of that inherently unstable foil, so we can produce lots of different shapes and sizes quickly.
“The other thing that’s changed since the jet foil and the passive V-shaped hydrofoils is materials – foils are much thinner now with composites that reduce the drag which is quite significant.”
In fact it was the aerospace industry that attracted Artemis Technologies to Belfast, along with its naval tradition: the companies and research institutes, including Queen’s University Belfast, form a cluster of knowledge known as the Belfast Maritime Consortium, which has been invaluable in researching composites, engineering and electronics.
In Belfast harbour, Artemis Technologies’ vessel can travel at over 25 knots compared with the other boats, which are restricted to six – because even at that speed there is minimal wake, thus no damage to the shoreline or other boats. The other major change, he says, is that the in-house Artemis Technologies drive train is submerged, thus passively water cooled, saving all moving parts and the cost, complexity and efficiency loss of the shaft.
Every key technology on the boat is Artemis Technologies owned, Percy says. All the sub systems have been designed in-house.
“The propulsion and drive train are Artemis Technologies, the battery system is an Artemis Technologies one – they are just a couple of the key components,” he says. “The hydrodynamics of the hull shape is less important because it’s not in the water, but it still has an interesting optimisation profile compared with a standard boat.”
Passenger ferry
One of the projects Artemis Technologies is working on, and is launching next year, is a 24m electric foiling ferry that can take up to 150 passengers. It will run a pilot scheme between Belfast and Bangor, have a top speed of 38 knots and a battery range of over 100 nm at cruise speed.
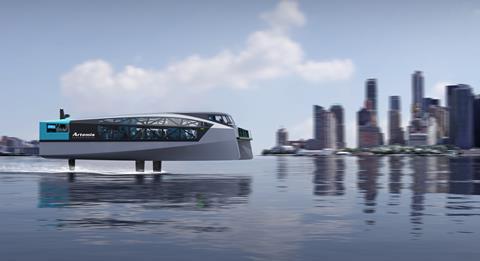
Artemis Technologies says the fuel savings on its passenger ferry are immense, estimating that operating at a 35 knot average speed for 200 nm a day, 350 days a year, could save £2.6 million (€3 million).
“There’s a physical limit on foiling because of the relationship between the wing span and the weight of the vessel,” says Percy. “If you tried to have a super tanker with wings they would have to be 10 miles long.
“Eventually you could have a 350-passenger vessel with some accommodation, but we went for the 150 passengers size because we did a lot of market research and reckoned we could achieve efficiencies in cost.”
Ferries also have an added benefit of much quicker payback period than the wind farm sector, he says.
Range anxiety
As more offshore wind farms are developed further out, servicing them becomes trickier, but the problem is halved, with the likes of MJR’s offshore charging system, which also won an award at Seawork last year.
“It’s an enabling technology and very important for us as we will be able to service every wind farm in the country whereas current vessels can service 80% of UK wind farms with battery storage,” Percy says.
“We’re doing a project on a hydrogen range extender. I understand why there’s a nervousness and a range fear about batteries, lack of lithium is also going to be a challenge, but we’re going to respect all of that.”
While the company is working on a hydrogen fuel cell range extender, Percy rules out fuelling the vessels on hydrogen alone for high-speed, close to shore applications: “All our business modelling at the moment shows that you can’t make Total Cost of Ownership with hydrogen cost effective compared with an electric solution,” he says.
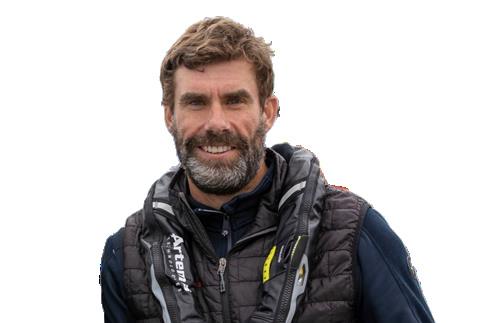
He rules out diesel, which he says is more expensive over greater distances and ten times more polluting.
“If you used a diesel CTV to go to a wind farm in Liverpool as opposed to ours you would be seriously hit in the pocket,” he says.
“This really works – you really can go 60 miles back and forth in comfort in 2m high seas. Unless it’s a wind farm very near to shore, there is no other solution than an Artemis eFoiler®.”