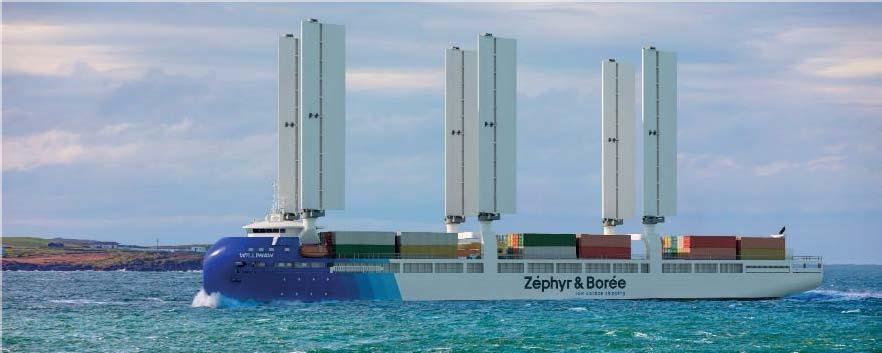
2 minute read
CCS SOLUTIONS SPRAWL AS MARINISATION PICKS UP
With carbon capture technology gaining traction in industry, more options are emerging for shipping
Nominees for the “Best CO2 Utilisation 2023” innovation award at this year’s Conference on CO2-based Fuels and Chemicals include the company On which has produced the first ever shoe made from a feedstock of carbon emissions. The shoe, and the award, demonstrate the wider innovation picture that shipping is being drawn in to, and it is one being backed by regulators.
In February 2023, the U.S. Department of Energy announced nearly $2.7 million for five R&D projects that will help to accelerate national and international deployment of carbon capture and storage (CCS) technologies for permanent geologic storage or for conversion to other valued uses. And in March 2023, the European Commission launched its Net-Zero Industry Act which in part aims to accelerate the use of CCS. This is expected to have a flow-on effect to shipping as the technology is developed and adapted, particularly to suit hard-to-abate sectors.
A project led by Windship Technology Limited which includes partner Leilac, a subsidiary of Calix focused on the decarbonisation of cement and lime, demonstrates the potential for cross-over from land-based industry. The project combines wind power and a lime-based carbon capture solution for the emissions from conventional diesel engines. It has been awarded £5m by Innovate UK.
Integration of the carbon capture system with the ship’s engines can enable waste heat recovery from the capture reaction, reducing fuel demand. Lime is a highly effective sorbent for the capture of CO2, but for this solution to provide a net reduction or elimination of emissions, the lime used for capture must be produced with low or zero carbon emissions, using shore-based decarbonisation of the lime. Leilac’s patented technology can produce low emissions lime by efficiently capturing the unavoidable process CO2 emissions released from limestone, without additional chemicals or processes.
Leilac’s technology is compatible with clean energy sources, such as hydrogen and electricity, and also alternative fuels, enabling flexible and economical pathways for the production of zero emissions lime and cement. It is proven at pilot scale, including through its pilot plant, Leilac-1, that has been in operation since 2019 with a capture capacity of 25,000 tonnes of CO2 per year. A demonstration plant, which aims to prove a low-cost module with a capture capacity of 100,000 tonnes of CO2 per year is due to open in 2024, paving the way for commercialisation of the technology at any scale.
This maritime version of the system is compatible with a wide range of ship types, including tankers, container ships and cruise liners. It is retrofittable, fuel agnostic, and can be scaled to meet the decarbonisation ambitions of each ship.
Noting the benefits of research and development already undertaken by the cement and lime industries, Leilac CEO, Daniel Rennie said, “This project marks a significant step in developing a potential route for the efficient and low-cost decarbonisation of the shipping industry. Marine shipping is a particularly hard-to-abate sector, and the very strong synergies that can be made from leveraging the large-scale industrial decarbonisation efforts in the lime and cement industries – combined with the innovative renewable approach by Windship – is an exciting development.”
The project aims to demonstrate the low-cost potential of the proposed decarbonisation solution for shipping and pave the way for zero emissions lime to be used for reducing or eliminating emissions from conventional diesel-powered vessels. The key objective of the project is to design, develop, build and demonstrate a novel drive train system consisting of a single powerful wind propulsion device, working together with a trial carbon capture system to pave the route to zero emission propulsion for bulkers and tankers. This will be installed and trialled on a 15,000dwt bulker.
Carbon capture technology company Ionada recently welcomed DNV to its carbon capture pilot installation at Halliburton Labs in Houston. The visit marked the beginning of a collaboration between Ionada and DNV aimed at supporting maritime CCS projects. Ionada says its unique Hollow Fiber Contactor Membrane technology requires half