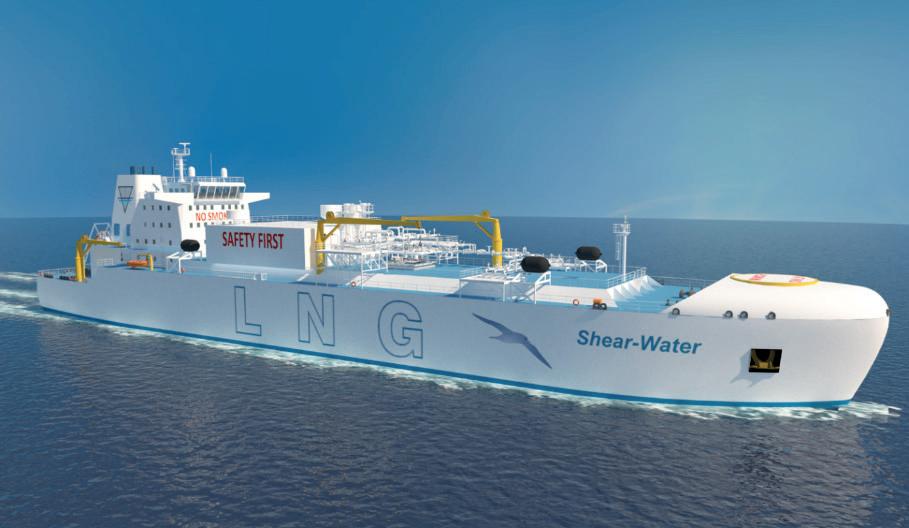
11 minute read
Ballast-free bunker vessel design
BALLAST-FREE LNG BUNKER VESSEL DESIGN LOWERS CapEx
GTT has developed a new ballast-free LNG bunker and feeder vessel which reduces both Capex and Opex compared to traditional designs.
The ballast-free Shear-Water design eliminates the risk of invasive species transfer and also reduces the CO2 footprint of the vessel by negating the need for operating a ballast water treatment system.
Typically, LNG carriers have standard square shaped midship sections. The V shape of the Shear-Water reduces the vessel’s block-coefficient and that leads to an increased design draft (loaded draft) compared to a conventional vessel. The aim is to keep a sufficient draft when the ship is empty to maintain propeller immersion and to ensure sufficient forward draft for safe navigation.
The vessel design is based on the currently proven 18,700 m3 capacity vessel. The propulsion system includes twin azimuth propulsors and dual-fuel electric power for the 141 metres vessel, leading to a service speed of 14 knots.
The design features two identical Mark III Flex membrane tanks and takes full advantage of the membrane tank shape with its 45-degree chamfers. The lower chamfers are significantly increased compared to a standard design and perfectly matched to the vessel’s V shape hull.
An exhaustive testing campaign has been carried out at the HSVA Hamburg tank test facility to ensure manoeuvrability and sea keeping. The model used was 7.75 metres in length and weighed 2.75 tonnes. A sloshing test campaign was also carried out by GTT to ensure the technical feasibility of the project: the excellent results obtained helped prove the concept. In total, more than 150 tests were carried out, including seakeeping tests in sea state 7 conditions.
There is no loading limit for the two tanks, in any navigation condition. Sloshing motions within the tanks are not specifically different from other vessels, as the tests proved that the large lower chamfers of the tank shape are efficient at mitigating sloshing motion.
One rule to be respected is the visibility line, meaning the trim has to be within acceptable limits, says a spokesperson for GTT. A trim-water system is provided to assist the operator with this, and a roll damping tank forward of the LNG tanks has been central to ensuring the performance of the design. Its performance was confirmed during testing even in transverse waves at zero speed and at most severe wave period. A roll reduction of up to 60% was achieved.
The vessel will be able to bunker in the same conditions as any other bunker vessel, i.e. calm conditions, with low relative motions between both ships. “Operators will gain experience over time and may admit somewhat higher conditions in accordance with all involved participants in such operations.”
The vessel is available for order already. GTT says that capex can be expected to be around 5%, lower than a conventional vessel. There are also substantial opex saving: 10-15% lower fuel costs, less maintenance, less paint and less corrosion due to the lack of ballast water tanks. The amount of steel used can also be reduced as the void spaces are no longer ballast tanks. The boil off rate is guaranteed to be low, and the vessel is designed for worldwide service without any filling limits.
The design is highly flexible and can be built in various sizes (including 7,500m3, 12,000m3, 17,500m3 and 25,000m3) and used on regional trades as a feeder vessel. GTT says operation is simple, with a lower environmental footprint than traditional vessels leading to a better company image for shipowners.
Following Approval in Principle from China Classification Society and DNV last year, GTT has now been awarded AiP for the design from Bureau Veritas (BV). Mathieu De Tugny, Vice-president of BV, said: “Bureau Veritas has given approval in principle to this new design, which has clear performance and environmental benefits: elimination of the need for ballast water treatment systems and equipment; easier maintenance of the void spaces surrounding the cargo, and reduced propulsion power requirements. Bureau Veritas has monitored and reviewed all the test results performed to support its Approval in Principle.”
Philippe Berterottière, Chairman and CEO of GTT, said: “We are proud to have developed Shear-Water, an innovative ballast-free design for LNG bunker and feeder vessels. This new technological solution allows a reduction in investment and operating costs, simpler operations as well as a reduction in corrosion supporting a longer service life. Obtaining this approval by Bureau Veritas constitutes recognition of the ecological relevance and performance of our technological solution.”
8 The new ballast-
free Shear-Water bunker vessel design is expected to offer significant capex and opex savings compared with conventional vessels

8 A sloshing test
campaign was also carried out by GTT to ensure the technical feasibility of the project
ALL EYES TURN TO CCUS: LR’s VAN DER POST
The emergence of a new trade in carbon transportation is likely to depend upon regulatory developments to support investments, Lloyd’s Register’s Sean van der Post tells The Motorship in an exclusive interview
Sean van der Post, LR’s Global Offshore Business Director, opened the interview by refusing to accept arbitrary distinctions between on-board and stationary carbon capture schemes. A recurring theme was the importance of joined up thinking – both with LR’s project teams, within the maritime industry as a whole, and among regulators who need to create supportive conditions for the introduction of carbon capture at scale.
“We’re trying to do something at scale quickly, with many developments happening concurrently. Creating an [arbitrary] separation between the subsea storage of carbon dioxide and how its captured at source or transported is a gap we do not need in the industry.”
Van der Post noted that drawing on the experience of both the marine and [oil and gas] teams would help with the challenge of developing cost effective standardised solutions that would bring new innovations to market at scale, while meeting challenging timescales.
Technical challenges
Van der Post noted that while the development of CO₂ handling solutions for offshore marine storage was interesting from a technical perspective, the basics of managing CO₂, are well understood. “LR has been managing CO₂ for decades in its oil and gas team injecting it into wells for enhanced oil recovery. We have a lot of expertise within the process side around CO₂ [extraction] from whatever the waste stream is, and the chemical process most often associated.”
LR’s gas specialists in Korea also had experience working on the technical requirements of transporting Liquid CO₂ (LCO₂) on a vessel. Van der Post noted that creating multidisciplinary teams drawing on the skills of various experts within LR was a key part of the knowledge sharing within the various projects LR is involved in.
However, LR expected commercial LCO₂ transportation to have very different operational requirements, partly reflecting operations at a much greater scale, as well as the very different level of expertise and understanding of managing CO₂ that commercial marine crew typically have, compared with oilfield engineers and technicians.
That said, the marine industry is becoming increasingly aware of the specific technical challenges posed by the transportation of carbon dioxide. “People and the industry as a whole are starting to understand better that [CO₂] is different, and that it needs to be managed differently.”
LCO₂’s specific properties include a higher density than other liquefied gases, with a density of 800-900kg/m3 , compared with 500kg/m3 for LNG or LPG. Meanwhile, other challenges including the need to minimise pressure variations within containment vessels, specific sloshing related effects, as well as the need to prevent the formation of hydrates (dry ice).
The Motorship notes that while some CCS solutions are seeking to minimise variations in pressure, temperature and state between capture and final injection, others are employing compressors between different stages.
Van der Post noted that the development of tailored solutions designed to manage specific issues, rather than applying established gaseous handling solutions, was likely to impact the speed of developments.
“We’ve set ourselves [timescales] trying to find standardised solutions and build on them and have optimised solutions when we actually haven’t even got enough pilots in the ground yet.”
“It’s like trying to run before you can walk, because there are things that are going to come out in operation that are going to be different – we need to learn from operational experience to optimise the solutions.”

8 Sean van der
Post, LR’s Global Offshore Business Director
Commercial considerations
Van der Post noted that technical obstacles would not prevent the introduction of carbon capture into the industry. “I think the challenge for the shipping industry is not the technology, but the cost.”
Assessing the commercial outlook for the carbon capture was not a simple matter of assessing returns on investment – “this technological transition is the first that is not being driven by the adoption of a superior technology, but by moving to cleaner technologies”.
However, leaving aside potential CII compliance advantages, Van der Post noted that the very term “transition
fuel” was unhelpful for potential investors examining the business case for carbon capture. “Uncertainty about the duration of that transition is one of the things that have been holding [investment in CCUS] back.” These considerations affect investment because carbon capture is going to be expensive. The longer the payback period, the longer the amortisation period, Van der Post said simply, which will “make it easier to implement CCUS at its various scales, and across various industries.”
This in turn depends upon society recognising that we are likely to continue to choose to use fossil fuels over the longer term while incorporating clean fuels into the mix. “Which is where carbon capture comes in, as part of that sustainable integrated energy system of the future.”
A second closely related issue related to the economics of carbon capture. Taking on board carbon capture as an example, van der Post noted that aside from the cost of installing such a system aboard a vessel, a ship operator faced increase fuel consumption, arising from both the additional weight from the system, as well as the additional power consumption required by the system itself. This might equate to a 25%+ potential increase in fuel consumption. “Your net benefit is unlikely to exceed a 40-50% reduction in CO2 emissions, even if you’re utilising a very efficient system that can capture over 80% of a vessel’s CO₂ exhaust.”
Regulatory environment
This is turn meant that carbon capture would not become commercially viable without the creation of a regulatory environment that encouraged its implementation.
The passage of the London Protocol amendment had eliminated the regulatory impediments to the marine transportation of CO₂, even if the amendment was yet to be fully ratified.
Van der Post noted that while significant attention was focusing on the potential introduction of market-based measures such as a carbon levy in the commercial shipping industry, other regulatory changes were also required. These included the broader introduction of carbon capture into land-based hard-to-abate industries, which would help to create a broader carbon capture market.
When asked by The Motorship whether this meant the introduction of regionally-focused carbon border adjustment mechanisms, as are currently under discussion in the EU and in the UK, Van der Post responded that such a mechanism would create an environment in which the industry within the country would invest in CCUS, without fear of being undercut by competitors from locations with less stringent standards.
Reverse supply chains
The development of reverse supply chains at ports and in the hinterlands around ports has also been identified as a potential barrier to the wider adoption of on-board carbon capture by sceptics.
While recognising that safety risks around the discharge of carbon dioxide from vessels at scale would need to be carefully managed, van der Post noted “the industry has extensive experience of offloading other materials from vessels. “The main focus will need to be on updating regulations rather than practical material handling. And that is not just a carbon capture problem, this is an entire energy transition challenge.”
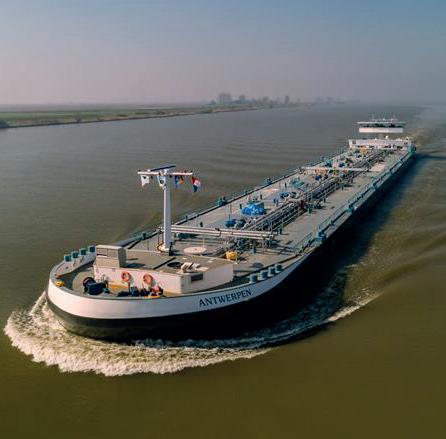
A solution for hard-to-abate industries
While the maritime sector was focusing on the emergence of CCUS within the marine segment, van der Post added that it represented a potential solution for hard to abate industries, such as steelmaking, cement manufacturing or other energy intensive manufacturers. This was also contributing to demand for onshore CCUS projects, an area in which LR is also active.
Returning to the offshore market, van der Post noted that the lack of cost-effective alternatives for hard to abate industries was likely to create a market of a certain size globally for carbon capture and storage.
8 The Motorship
has reported on plans by European shippers to develop barge-based carbon dioxide transportation links connecting hard to abate industries with ports such as Rotterdam or Antwerp
Carbon as a commodity
Van der Post noted that interest was increasing in the development of market tools focused on the development of liquid carbon as a commodity to be transported and stored.
Carbon will have a number of particularities, beyond the simple fact that negative pricing will introduce complications for pricing mechanisms, although carbon will not be the first material to have a negative price.
Van der Post was more sceptical about the emergence of global carbon commodity networks. Liquid carbon transportation requirements were likely to remain local, which will lead to smaller capacity cargo vessels designed to serve local routes. With the planned network of CO₂ storage sites, “There should not be any need for 20,000 cbm capacity LCO₂ carriers, as carriers will not need move carbon from Asia to the Americas before injection… ideally you [just] want [the carrier] to be the right size so you can dispose of [the carbon] quickly and easily via the shortest journey possible.”
As far as spot price predictions are concerned, van der Post noted that without long distance transportation, carbon would remain a largely local material, if carbon could even be described as a commodity at all.