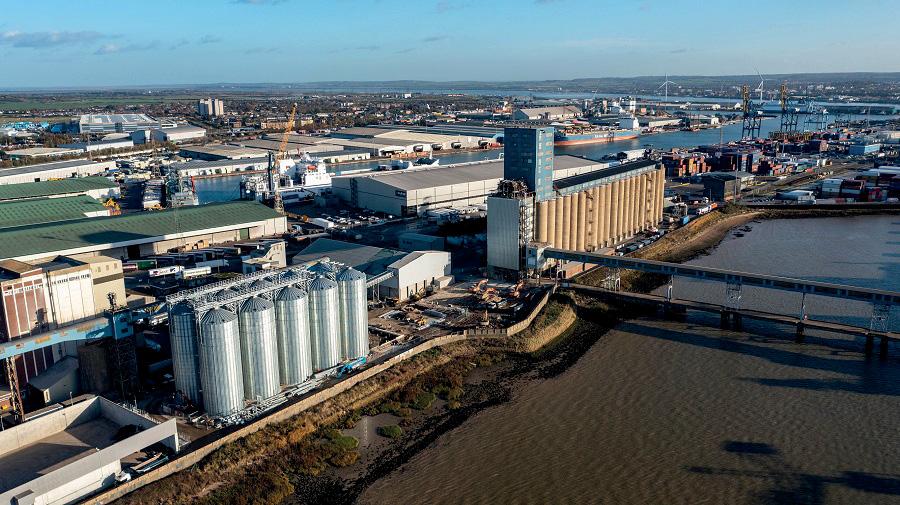
7 minute read
Grain: System Innovation
Grain handling and storage system innovation continues apace. John Bensalhia highlights recent developments in the supply sector
The international grain trades face a new challenging era as highlighted in the earlier article in this issue, Grain a Price to Pay for Confl ict. While, however, there are signifi cant structural changes underway at an international trading level, suppliers of grain handling and storage systems continue to innovate in order to meet the latest customer requirements in terms of performance, durability, operational cost and the new eco-conscious era.
The companies highlighted below have all recently made Port Strategy aware of advances in one or more of these respects and insight is provided into their recent activities by way of signposting the ‘direction of travel’ of the grain and allied products system supply sector. The range of products discussed is diverse as is the scope of recent project work.
BEDESCHI: BUSY WITH R&D AND ORDERS
Italy-based Bedeschi, a versatile supplier of bulk handling systems across a range of commodities, highlights the application of pipe conveyor technology to the grain handling business as a most beneficial development. Lodovico Bernardi, Sales Director Asia Pacific & Grain Key Account, Bedeschi, underlines:
“This kind of conveyor allows for dust free operations (the product completely sealed by the rubber belt) and also has the big advantage of being cost-effective as a result of requiring fewer sections and supporting steel structures resulting in a much lower weight compared to a standard belt conveyor. The technology also removes the need for transfer towers, not necessary to achieve changes of height or direction of the conveyor – another cost-effective measure.
Two other areas of design activity that Bernardi highlights are knowledge transfer from handling other bulk commodities into the grain sector and the automation of vessel loading and unloading operations. In the former respect he notes: “Our effort focuses on exploiting our experience with different materials and applying solutions developed for other Industries to grains & oilseeds and vice versa.”
On the automation of vessel loading and unloading he states that this is an area of great potential effectively unlocked due to the new generation of sensors and 3D scanning systems. “The technology is ready,” he stresses, “but the challenge is to ,create a system at the same time which is reliable and cost effective: Artificial Intelligence (AI),” he suggests, “may play a crucial role in reaching this target.”
In project terms Bernardi cites a busy order book. “In the last six months,” he explains, “we have commissioned a shiploader project for a major grain terminal on the Mississippi River in Louisiana (USA), and are currently working on another one in the same area. We are also completing two shipunloader projects able to operate with both grains or meals, one is in the UK and the other in Israel.”
The latter project also included the supply of three ecohoppers to Ashdod Port.
At Renova Plant, Rosario, Argentina Bedeschi installed what it claims is the largest pipe conveyor ever commissioned for grains and oilseed, with a capacity of 1500 t/h and 700m length for soya beans. Additionally, at Westwego, a New Orleans area grain terminal, the company has installed a ship loading system.
BRUKS SIWERTELL: R&D PROGRAMME
Siwertell has undertaken a research and development programme with the aim of improving the lifetime of the vertical screw conveyor. Per Hansson, Sales Director, Bruks Siwertell, explains that as well as delivering performance enhancing product improvements, the purpose of the programme was to make the process of producing the
8 The Tilbury
Grain Terminal facilities are in the fi nal stages of a comprehensive upgrade
systems more environmentally friendly (in accordance with the company’s sustainability goals).
The results of the programme, according to Hanson, have generated lower wear component parts with a commensurate reduction in costs for its ship loaders/unloaders and conveyors in general. “We are delighted that the results of this programme will offer our dry bulk handling customers some of the most substantial owner benefits available on the market,” states Hansson. “The vertical screw conveyor’s longer lifetime will result in fewer exchanges of worn components and deliver significantly lower total maintenance costs for operators that use our technology. These customerdriven advances are extraordinary and set an extremely high industry standard for this type of wear part.”
Hansson further points out that the sector is one that demands an incredible amount from its dry bulk handling equipment, in terms of intensity, value, and a competitive, expectant market. “We have grain, soya bean and soya meal handling systems operating in Brazil that run up to 4000 hours/year, working to some of the agribulk industry’s tightest seasonal schedules. There is no capacity in these operations for any unplanned downtime; longer screw conveyor lifetimes ensure that we will continue to meet this target in a more effective way.
“Very high use conditions naturally have an inevitable impact on wear parts, and, arguably the vertical screw is one of the most critical. By focusing our R&D efforts on this, we could see great potential; by dramatically improving the service life of wear parts, we can offer customers significant through-life maintenance savings, without increasing investment costs, and benefit the environment through a more sustainable approach.”
BUHLER: EXTRA PROTECTION
The Buhler Portalink unloader was selected by Krakatau Bandar Samudera (KBS), the operator of the largest dry bulk port in Indonesia. KBS typically handles commodities such as maize, wheat and soybeans. Facing the challenges of maintaining its customer base and boosting income in a stagnant market, KBS chose the Portalink on account of its throughput capabilities. It has a maximum unloading throughput of 1300 tons per hour. This Portalink installation marks a first for Indonesia, being its first continuous ship unloader.
Despite the challenges posed by the COVID-19 pandemic, Buhler reports it was still able to fully install the unloader at KBS in two weeks, with the commissioning and training handled by a local Buhler team, backed up by remote support.
Other advantages of the Portalink system highlighted by Buhler include its closed-system technology, which reduces commodity losses and broken grains, and the overall reduction of dust emissions.
CLEVELAND CASCADES: ABRASION RESISTANCE
The CC896, CC897 and CC898 ship loading chutes have been popular sellers for Cleveland Cascades.
ADM Ama Louisiana is one example, using three identical shiploader systems for grain handling, as well as a drum winch sourced by Cleveland to extend and retract the system. The systems also use a series of 1700 GRP cones as a means of directing the flow of the cargo and to reduce its velocity and impact. Due to the abrasive properties of grain, the cones are designed to withstand wear and tear, so that they can hold out during the fast conveyance of the grains.
The system reportedly also offers a high degree of flexibility in terms of accommodating the variation in grain densities.
In 2021, Cleveland Cascades won a contract to supply two identical cascade systems to Ashdod Port, Israel. The systems are used for grain loading (attached to a grab fed eco-hopper used for vehicle loading) and, in order to withstand the abrasion from the grains, are lined with stainless steel.
TH WHITE: UPGRADING TILBURY
The rebuilding of Tilbury Grain Terminal has been ongoing since 2018. Matters weren’t helped by a dust explosion and fire in its concrete silos in 2020 – however, with the help of TH White Storage Solutions, the rebuilding project is well on track, with a completion date due for the middle of this year.
Work is presently underway on Tilbury’s Steel Silo 3 (the 2020 explosion occurred in Silo Block 4). All of the silo bases have been modified with a concrete slab so as to accommodate the new corrugated 11m wide x 30m high steel silos. The silos themselves have been built with 3m wide overhead gantries which will accommodate the 700tph high capacity 800mm wide chain conveyor belts.
While Silo 4 is being worked on, TH White has also been commissioned to work on a transfer reclaim conveying and elevating system. This is to transfer cereals from the main terminal headhouse to the new silos, the 17,000 tonne bulk store and the two local customer flour milling operations of ADM & Allied Mills – doing so at a rate of 500tph.
Knowledge transfer from other bulk handling sectors and automation drawing on AI are two prominent drivers ‘‘ of system innovation
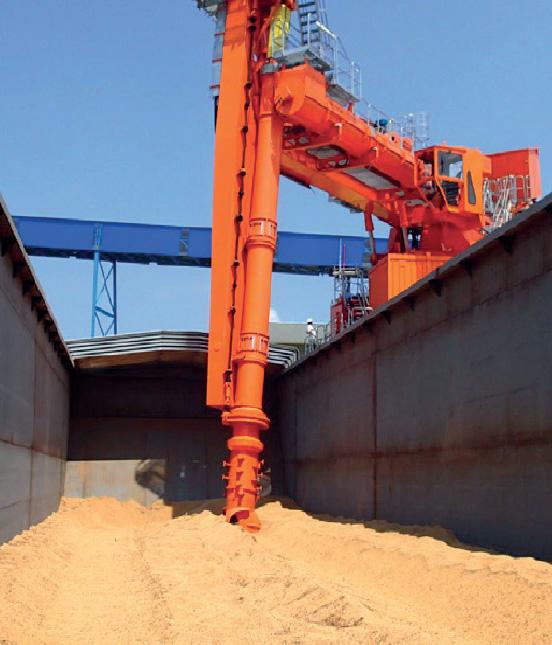
8 Reducing