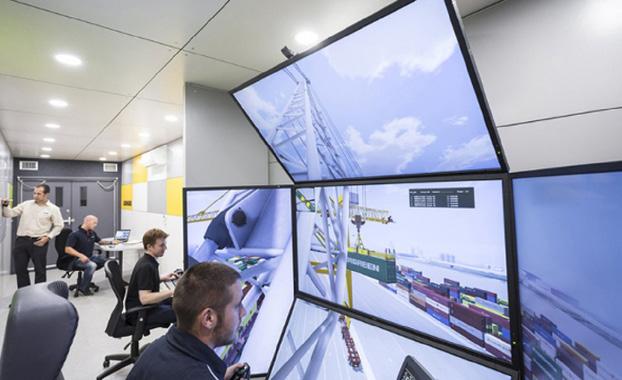
4 minute read
Kazakhstan Looks West
HELP WITH BENEFITS
The hi-tech’ pursuit of the next generation of equipment operators offers distinct advantages including, going forward, data generation complementary to wider goals*
Skilled workforces across all sectors are being hit hard by labour shortages: data from the 38 member countries of the Organisation for Economic Cooperation and Development (OECD) suggests that there were 14 million more people inactive in 2021 than in 2019.
The port industry has not been spared. The consequences range from delays in cargo processing to a more volatile climate in labour relations. The impact is further compounded by complexities that have long germinated around sector volatility and pressures on throughput levels.
As a result, port terminals are fighting the same war for talent as everyone else, but with higher stakes — and the sooner they can solve the recruitment challenge, the better their business outlook will be.
MATCHING TECH’ TO TARGETS
Anyone born since the turn of this century has grown up immersed in technology that works seamlessly to make information available instantly. In addition, today’s candidates are not likely to be actively applying for work. Instead, they expect to be persuaded — essentially marketed to — before they commit to so much as an interview.
Successful operator hiring, therefore, often depends on matching technology to expectations at all stages of the process. In fact, port terminals are already deploying advanced tools, including simulation, augmented reality, and other solutions that are transforming the nature of recruitment and training.
Traditional processes for evaluation are limited, with candidate qualification rates ranging from 10 per cent on complex cranes to 40 per cent on equipment such as straddle carriers. Terminal managers using realistic simulation tools report up to a 99 per cent success rate for candidates passing initial evaluations. Not only is that more efficient, it is an encouraging stroke of confidence for new recruits that you want to keep engaged.
WINNING PROPOSITION
It used to be that the only way of experiencing the highs of equipment operation was from the actual machine cab.
However, safety considerations and limited equipment availability have driven the development of simulation and visualisation tools that provide increasingly life-like operator experiences, ranging from the ability to conduct detailed inspections of operating environments, to the virtual sensation of lifting containers.
These tools are highly portable — even allowing for remote use in some cases — and provide safe hands-on environments that are conducive to effective candidate screening. Still, attracting candidates is only half the battle. The real challenge is keeping them, given their famously high mobility.
Demonstrating consistent commitment to technologydriven safety goes a long way towards answering that challenge. Terminal operations have begun to do just that. For instance, while using simulators to broaden their recruitment reach, they are also improving processes for evaluation and selection of the best suited operators for advancing their skills, or when introducing new equipment and processes.
*By David Clark CM Labs Simulations is the developer of Vortex® training simulators for the port industry. CM Labs clients include the Port of Tilbury, Flinders Adelaide Container Terminal, Indonesian Port Corporation, Napier Port, Ports of Auckland, multiple DP World sites, the Pacific Maritime Association (USA) and over 100 other world-class companies, OEMs, equipment operators, and trades training organisations.
THE ROAD AHEAD
Despite, or maybe as a result of, the growing use of simulation for a variety of port sector applications—from simulation of intermodal hubs, energy consumption, and traffic, the topic has become a hot one. It can be challenging to incorporate new technology into established business practices: recent research published in the Journal of Business Logistics suggests that “incremental innovative solutions produce a polarised port labour market.”
The key to resolving conflicting perceptions lies in the ability for training technology to gather relevant, accurate data, and display it transparently. There are new skill sets for incoming operators, and transitional learning is needed for existing, experienced operators, as port terminals transition to remote operations.
Hi-tech solution providers have taken note, and companies such as CM Labs Simulations have developed simulators that integrate with original equipment manufacturer control systems. The company’s Remote Operating Station training solution is designed for STS, RMG, and RTG operations and simulates all crane functions, camera displays, and automated safety functions, as well as the terminal’s container management system.
The next generation of training solutions will essentially be purpose-built to reward learning, as well as to “show the money,” transparently displaying insights to trainees, relating to the tangible impact of skills acquisition on productivity, safety, and possibly even earnings potential.
Terminal operations managers, on the other hand, will be able to leverage the insights produced during the same learning stream, to make accurate predictions about machine maintenance and longevity, and accelerate other decisions that directly impact the bottom line.
8 Simulation,