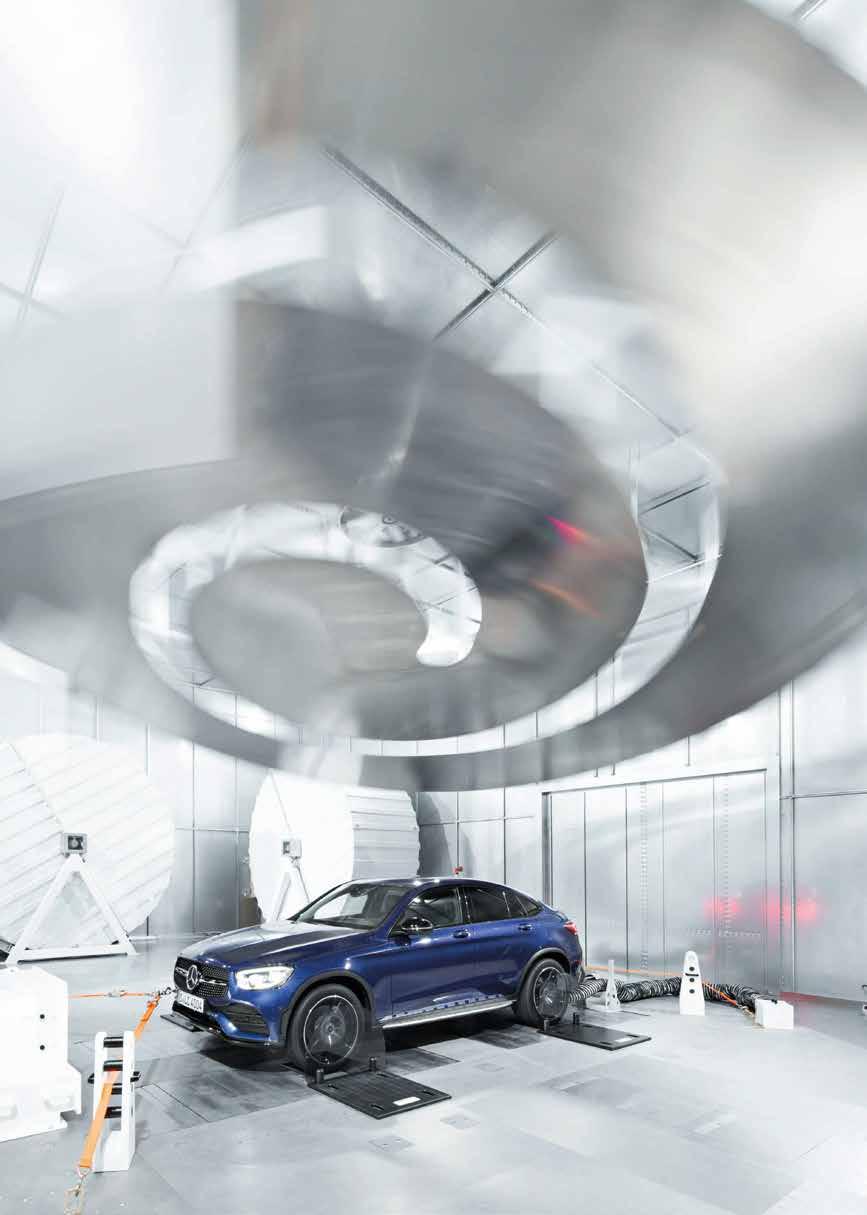
10 minute read
TECH TALK
The Wave Riders – The Technology within
By Sven Sattle
Advertisement
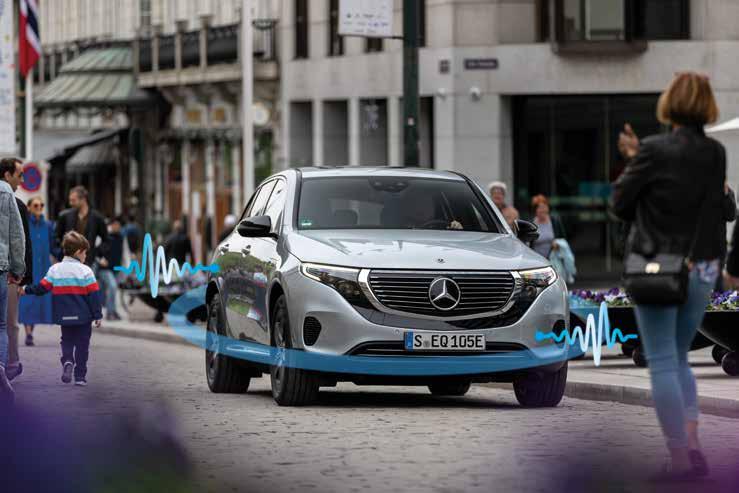
Technological progress has greatly changed the way we drive. The electronics and electrical system on board a Mercedes-Benz makes driving safer and more comfortable than ever before. However, the new technologies have to be incorporated into cars somehow – and that’s why today’s vehicles contain numerous high-tech components. Jürgen Schwarz and his team make sure that all of this technology works flawlessly even in the event of electromagnetic interference. And they ensure that the technology is harmless to those travelling inside the vehicle. I have vivid memories of some adventurous trips in our family car: My father sat at the wheel of his dearly beloved Mercedes-Benz 190D, while my mother sat in the front passenger seat, where she struggled with the road map. The two debated whether it would be better to turn le or right. I vividly remember a scene in which they unsuccessfully tried to find the venue of a wedding. We were so frustrated that we almost turned around and drove 200 kilometres back home – without having seen the newly married couple. With regard to the 190D, I also vividly remember a two-hour ride in that car during which I spent almost the whole time watching the radio antenna sway in the wind with such force that I childishly feared it might snap off and fly away. It didn’t fly away. It remained steadfastly on the old. Its successor had an onboard navigation system, of course. This made it harder to get lost. And if my father managed it somehow, it always started with him claiming to know a shortcut. Ten years later, Live Traffic Information enables my navigation system to predict fairly precisely where I will encounter stop-and-go traffic on my route and whether it would be worth it to take the supposed shortcut. Telescopic antennas are also long gone. Today’s Mercedes-Benz cars don’t have a visible antenna at all. Nothing should interfere with the design’s clear lines. “People oen don’t know how many antennas they are driving around in their cars” Jürgen Schwarz Head of the Testing Facility for EMC and Antenna Systems Still, you need an effective infrastructure so that the digital systems and services in cars can work. It’s necessary so that my navigation system knows where I am as I drive around. Ideally, it will also be able to predict where traffic jams will be so that it can route me around them. “Today’s customers naturally want mobile communications, Bluetooth, and WiFi inside their cars. To make this possible, we need many different transmission frequencies so that the various radio signals don’t interfere with one another. People oen don’t know how many antennas they are driving around in their cars,” says electrical engineer Jürgen Schwarz, 55. He knows the number, of course: “A modern Mercedes can have as many as 20 antennas. Although you don’t see them, they are there. The rear window, for example, contains antennas for AM and FM Radio, Digital Radio and TV. Various WiFi/Bluetooth antennas are built into the interior. Additional antennas for GPS and mobile communications can be installed in the exterior mirrors and will also be available in a roof module in the future. Antennas are also
needed for unlocking the doors and for parking functions. But that’s by no means all.” Electromagnetic waves provide the basis for today’s cars There is a reason why Jürgen Schwarz knows exactly where each type of antenna is located: He is, in a sense, Daimler’s (electromagnetic) wave guy. He heads the testing centre for electromagnetic compatibility (EMC) and radio-frequency (RF) antenna systems at Mercedes-Benz Research & Development in Sindelfingen. His team tests the specific infrastructure that makes this wonderful new world of driving possible. In this way, it ensures that this wonderful new world is also safe. It is almost in the nature of things that the number of components that Schwarz and his team have to test has tended to increase in recent years rather than decrease. That’s because all of the major future-oriented topics in the automotive industry are pretty much directly related to data transmission. Highly and fully automated driving will only be reasonable for large numbers of vehicles if they are connected with one another and with the infrastructure. Digital services can only work if cars and service providers share data. Electromagnetic waves are the physical basis of this data transfer. “All in all, a new S-Class contains around 260 electrical or electronic components. That’s benchmark for a modern car, of course,” says Schwarz. “Each of these components can be a potential source of interference. Depending on the wiring, the effects of an antenna can cause even a small signal to have a huge impact. That’s why we inspect each and every electrical and electronic component that is installed anywhere in a Mercedes-Benz car. We can’t test all of the theoretically possible equipment and engine variants, of course, because that would be a 24-digit number.”
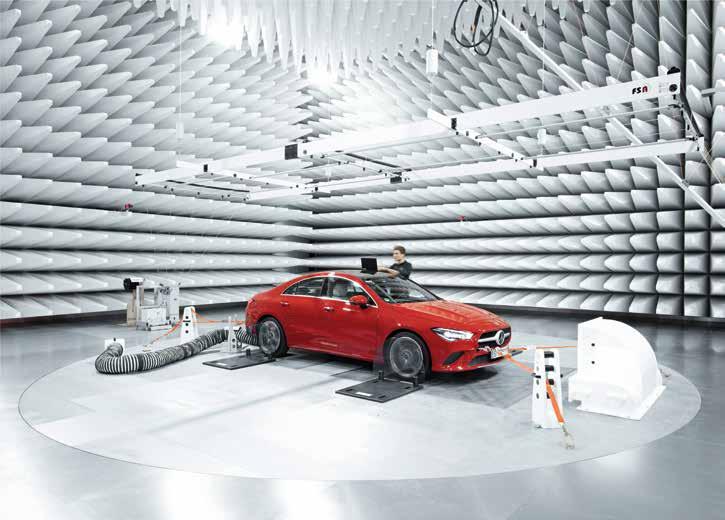
Performance and compatibility must go hand in hand In this regard, Schwarz’s team mainly focuses on four aspects. First, the electrical or electronic (E/E) components in cars generate electromagnetic fields. The colleagues therefore conduct tests to make sure that these fields don’t interfere with other systems inside or outside a car. The second aim is to make sure that the magnetic fields and radio waves have as little effect as possible on passengers inside the vehicle. Third, the tests should guarantee that vehicle functions are so protected that they cannot be affected by external magnetic fields or electromagnetic waves. The fourth aspect involves optimizing the quality of reception as well as the performance of the antennas built into a vehicle. Schwarz has been working on waves and frequencies throughout his career. “My doctorate was in the field of high-frequency applications, and while working on it I developed antennas that were three meters tall and this much around,” he says as he forms a big ring with his hands. In a sense, Schwarz’s current work in the EMC/HF centre is taking him back to his roots aer he devoted decades of his life to functional reliability. Schwarz joined Daimler’s development department in 1995 as a young engineer working on the validation of complex functions, including those in a SL-based research vehicle that was operated by a joystick instead of a steering wheel and pedals. In 2008 he became the Head of the department for Functional Reliability and E/E Processes. The waves from the test centre don’t get outside Schwarz has directed the EMC/RF test centre since 2017. In the first two years of his work there, he spent less time on antennas, vehicles, and radio waves than on statics and architecture. That was because the decision to add such a
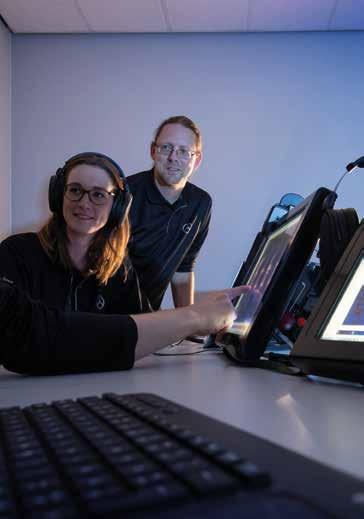
centre to the Sindelfingen development location was first made in the fall of 2016. So, Schwarz also became a construction manager — and had to regularly wear a hard hat — when he started work at the test centre. Now, a little more than two years later, he no longer wears a hard hat or a safety vest as he sits in his office in the administrative wing of the new building bearing the house number 20/4. This building is almost impossible to miss when you drive past the plant on Calwer Strasse. However, you can’t see what’s inside, of course. The building contains three halls for EMC tests as well as one especially big hall in which high-frequency antenna measurements are carried out. In any case, nobody outside the building could measure what goes on inside. The halls are completely screened with metal, preventing any signal from getting outside. Conversely, no signals from the outside can interfere with the measurements inside the building. “During construction, we had to deal with some challenges that had nothing to do with our core business,” recalls Schwarz. “For example, we decided to build the antenna hall for radio-frequency measurements on top of the EMC halls. We therefore needed test rigs on the fih floor. I should mention here that one normally sets up test rigs on the ground floor so that you can simply dig a pit for all of the parts that have to go underground.” says Schwarz with a laugh. “It therefore turned out to be somewhat more complicated for us.” And don’t forget: Measurements were still regularly made while the new building was under construction. These measurements were conducted on the two existing test rigs in Sindelfingen as well as in EMC halls that we had rented outside the plant. “The entire team put in a top performance,” says Schwarz. Unparalleled in size: the electromagnetic reverberation chamber The halls of the new test centre have been in operation since July 2019. The first time you walk through these halls, you can sense why all of this effort was worth it. You can also see why the team had a good feeling as it invested many hours and much effort in its new home. The colleagues are especially proud of a hall that bears the rather cumbersome designation “electromagnetic reverberation chamber.” Insiders refer to it as the reverb hall. When you stand in this hall, you feel as though you’re inside an oversized kitchen mixer. From the ceiling hangs a spiral metal disc 10 meters in diameter that rotates on its axis. This disc is called the stirrer. The disc’s continuous rotation changes the distribution of the electromagnetic waves in the room. “It has raised EMC measurement to a new level. Before we had it, we used to direct antennas at cars from a variety of angles and different distances,” explains Schwarz. The brain behind the reverb hall is Martin Aidam, who is responsible for new EMC technologies in the test centre team. When Aidam still worked in the research and advanced engineering departments, he built a small reverb test rig as part of his research activities. For the new facility, he drew on his experience and knowledge to think bigger. The team not only came up with the chamber’s design in-house, “We also developed the soware that’s used in the reverb hall,” says Aidam. The wave experts get involved in vehicle development when it’s still in the digital phase The team continues to tinker and test in the EMC/HF test centre. Moreover, it doesn’t just study a vehicle’s electrical and electronic systems when the automobile is almost ready for series production. On the contrary, the wave riders’ expertise is now more in demand than ever before. The more technology is contained in cars, the more intelligently the individual components have to be arranged to keep the impact of electromagnetic fields in the interior as low as possible. “That’s not a problem as such,” says Schwarz: “The magnetic field of a straight conductor is the strength of the current divided by two pi times the radius. We can therefore achieve a lot by simply increasing the distance between the component and the vehicle interior. Every additional centimetre greatly reduces the field strength.” If that isn’t feasible, Schwarz also knows of a second possibility: “As an alternative, we can, of course, work with the direction of the current. This means that we channel the currents inside the vehicle in such a way that the resulting magnetic fields cancel each other out,” he says. No matter which variant is ultimately chosen, it’s clear that the resulting electromagnetic fields have to be taken into consideration early on. This has to be done at a time when the vehicle doesn’t yet consist of metal and rubber, but only of design data. “Our team is now involved in the vehicle development process from the very start. As early as the digital phase we keep an eye on the new model’s design so that the wires are arranged in such a way that magnetic fields in the interior are kept to a minimum. This assessment is now one of the quality gates on a vehicle’s path to series production,” says Schwarz. Electric mobility creates new challenges But that’s not the only reason why Schwarz can be certain that his team will continue to play a key role in product creation. There is, in fact, another important reason called electric mobility. Aer some reflection, Schwarz says, “The challenges we will face are of course huge, not least because the drivetrain will contain much more powerful electrical components than those in a conventional combustion engine.” The new EMC/RF test centre is ready to tackle these challenges, as are the experts who work there. They work to ensure safety. Because aer all, driving nowadays is more than just moving the steering wheel and letting the front passenger read the map. And that’s why safety in this wonderful new automotive world has to be so much more than just seat belts and airbags.