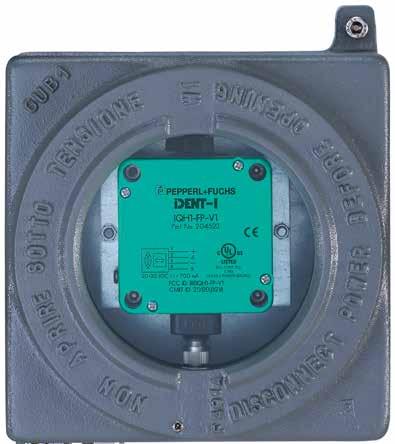
4 minute read
PEPPERL+FUCHS (INDIA) PRIVATE LIMITED
Product News | PEPPERL+FUCHS (INDIA) PRIVATE LIMITED
Automate. Apply. Optimize
Advertisement
Innovative system solutions for process automation
Finding solutions to complex problems requires considerable expertise, particularly where hazardous areas are concerned. Whether using sensor technology from industrial applications or highly flexible enclosures for explosion protection— only those with the requisite knowledge of the relevant subject area can offer the ideal customer solution. Pepperl+Fuchs's many years of experience in factory automation and process automation enable the company to adapt to customer requirements and bring the right products on the market.
Using sensors for factory automation in hazardous areas
The rising level of automation in the process industry is increasing demand for solutions that use sensor technology—and hazardous areas are no exception. Pepperl+Fuchs is now offering its customers more and more customized solutions for Zones 1 and 21 that feature sensor technology from factory automation and can be used in a huge range of applications. From monitoring warehouses Key Highlight:
Our main objective is combining state-of-theart technologies and comprehensive services to optimize our customers´ processes and applications.
New GR Series GRP Enclosures and rooms to use in areas focusing on personal and environmental protection, huge developments are being made in the automation of explosion protection. Sensors from Pepperl+Fuchs are housed in pressure-resistant enclosures, allowing processes to be further automated even under harsh conditions. For example, the latest pilot project involves using the R2000 photoelectric scanner in Zone 1 to safely fill up tankers with chemical substances.
Highly flexible GRP Enclosure Series
The GR series of GRP enclosures caters perfectly to the needs of electrical installation in process plants. The products in this series are designed to offer maximum flexibility for a wide range of applications. Many small details make it easier to plan for specific customer demands. The sophisticated mounting grid makes the additional mounting base obsolete, while also enabling terminals and switching elements to be planned and installed quickly and easily. It also means that any DIN mounting rails can be mounted using self-tapping screws. An innovative spacer system allows components to be installed at different levels within the enclosure. Different enclosure sizes and depths ensure that the enclosure series with IP66 expanded silicone seal offers unlimited flexibility. The series of enclosures can be used in environments up to -60 °C in Zones 1/21 and Zones 2/22.
The legacy
A willingness to take entrepreneurial risks, a pioneering spirit, and a firm belief in their own inventive powers - these were the assets that Walter Pepperl and Ludwig Fuchs started out with when they opened their Mannheim radio repair shop in 1945. Their invention of the proximity switch a few years later proved their strength. It was also the starting point in a successful history defined by close customer relationships as well as innovative automation technologies and procedures. Then as now, our focus is directed squarely on the individual requirements of each customer. Whether as a pioneer in electrical explosion protection, or as a leading innovator of highly efficient sensors - the close communication with our customers is what allowed us to become the leader in automation technology. Our main objective is combining state-of-the-art technologies and comprehensive services to optimize our customers´ processes and applications.
Success Story | RENISHAW C’mon Tiger!
Automated workpiece set-up boosts forestry equipment manufacture
Overview
To meet the rising demand for its marketleading range of forestry equipment, Tigercat Industries Inc. aimed to boost production efficiency and output at its manufacturing facility in Cambridge, Ontario, Canada.
By automating workpiece set-up using Renishaw machine tool probing systems and software, the company achieved 75% reduction in set-up times and a 40% increase in available time.
Background
A manufacturer of premium quality forestry equipment, Tigercat prides itself on providing the lowest cost per tonne timber harvesting solutions. From its base in Ontario, Canada, the company exports its products to busy logging operations throughout the world.
With a strong engineering culture, Tigercat thrives on the design and continuous improvement of all kinds of forestry machinery.
Its broad product range features both treelength and cut-to-length machines and includes feller bunchers, skidders, loaders, harvesters and fellers. They are big, strong, robust machines, typically weighing in at 25 tonnes.
Since logging crews often need to rely for example on a single drive-to-tree feller buncher for continuous operation, machine reliability is always a paramount concern. Just one machine down can cause a whole felling operation to stop. For Tigercat this means that robust construction, high uptime and a long useful lifespan are key product design requirements.
At its Southern Ontario, Cambridge site, Tigercat manufactures the larger steel components for its wheel-based forestry equipment, most notably its feller bunchers, a gold standard in the logging sector since 1992. Busy production line operations include laser cutting, machining, manual and robotic welding and assembly.
Challenge
In the face of increasing global demand,
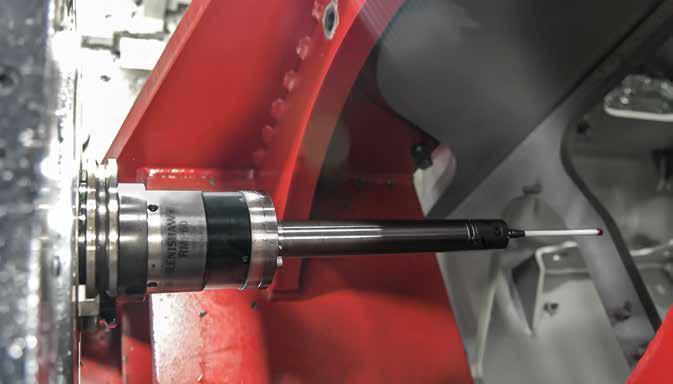
Renishaw RMP60M machine tool probe