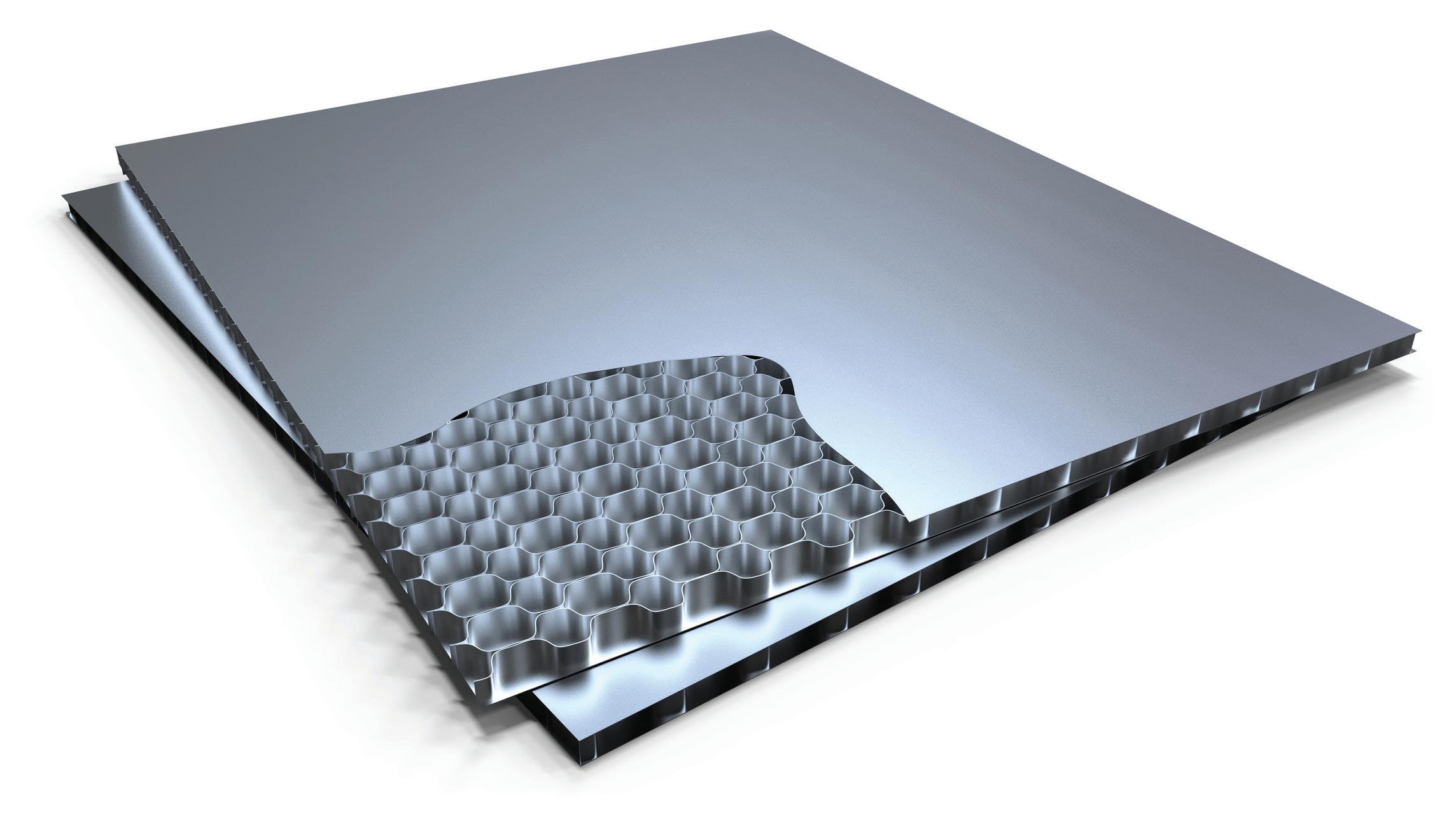
3 minute read
AEROSPACE OUTLOOK
By Royce Lowe
Composites in Aerospace
What are composites, and how are they used in aerospace engineering? These great beasts that we see in the sky, that carry us thousands of miles, evolved from very early models whose fuselages were often made of wood, which had to be replaced by metals for the structural strength of larger airplanes, particularly aluminum and steel. Aluminum is light and corrosion-resistant, and can be alloyed for strength. It is also relatively inexpensive. Steel can be used where strength is the major factor. Titanium is the best of all but hugely expensive. But materials that can be substituted for metals in many applications are carbon fiber reinforced plastics, or CFRPs, and other materials known as composites.
In these times, where carbon emission reduction is on every aircraft manufacturer’s agenda, the aim is fuel efficiency, which can, of course, be related to an aircraft’s weight. Airbus states on its website, “In CFRP production, thousands of mi- croscopically thin carbon threads are bundled together to make each fiber, which joins others in a matrix held together by a robust resin to achieve the required level of rigidity. The composite component is produced in precisely shaped sheets laid atop each other and then bonded, typically using heat and pressure in an oven, called an autoclave, resulting in a high-quality composite.”
“Parts such as fuselage and wings can make extensive use of composites as the required fiber loading, the way continued the fibers are laid up and cured in the autoclave, is simple. However, parts requiring complex loading will, for the foreseeable future, continue to use metal.”
Much of the credit for the move to composites is due to Boeing. It chose to follow the success of the 777, the best-selling widebody, with a new aircraft design in the 787. This design was lower capacity than the 777 and moved Boeing into the unproven market for a composite airframe. Airlines reacted positively, though. So much so that Airbus chose to revise its plans for the A350 and also design a new composite widebody with the A350XWB.
Aluminum-based, Magnesium-based, Titanium-based alloys, ceramic-based, and polymer-based composites have been developed for the aerospace industry with outstanding properties. However, these materials still display insufficient mechanical properties and are liable to stress corrosion cracking, fretting wear, and corrosion. Thus extensive studies have been conducted to develop aerospace materials with superior mechanical performance and are corrosion-resistant. Such materials can improve the performance as well as the life cycle cost.
The main advantage of composites is weight reduction, leading to lower fuel consumption, emissions, and ultimately cost per seat for airlines. Such materials are also less susceptible to corrosion and fatigue, reducing maintenance time and cost for airlines. Composite structures can be molded into any shape. This has allowed separate entire fuselage ‘barrel’ sections to be made in different locations, rather than using aluminum sheets that needed to be bolted together. Boeing has used this extensively in its construction of the 787. Fuselage sections are fully assembled in different locations (including Italy and Japan) and then flown to Boeing’s US factories for final assembly using a specially designed aircraft to carry the fuselages inside.
Composites can allow larger windows since the fuselage is more resistant to fatigue. The 787 has the largest passenger windows of any passenger jet, and as composite use advances, bigger ones could appear.
The move to composites for passenger jets is now well underway and may bring with it certain drawbacks. Cost is one. CFRP components are more costly to produce than standard metallic parts, but this could change with increased volume. A reduction in maintenance costs could help here. There have also been concerns raised about the detection of damage to the fuselage. Impact damage is not as visible or easy to detect as it is on a metal airframe. Proposals from regulators to mitigate this include better training and more monitoring and reporting of potential airframe contacts. Other tests (including optical, electrical, and acoustic) can check for airframe damage. Another challenge that might crop up is aircraft modification. This has been raised as an issue with freighter conversions, where cutting a cargo access door in a composite fuselage is more challenging than in an aluminum one. It may be easier if a fuselage is constructed from composite panels rather than complete barrel sections.
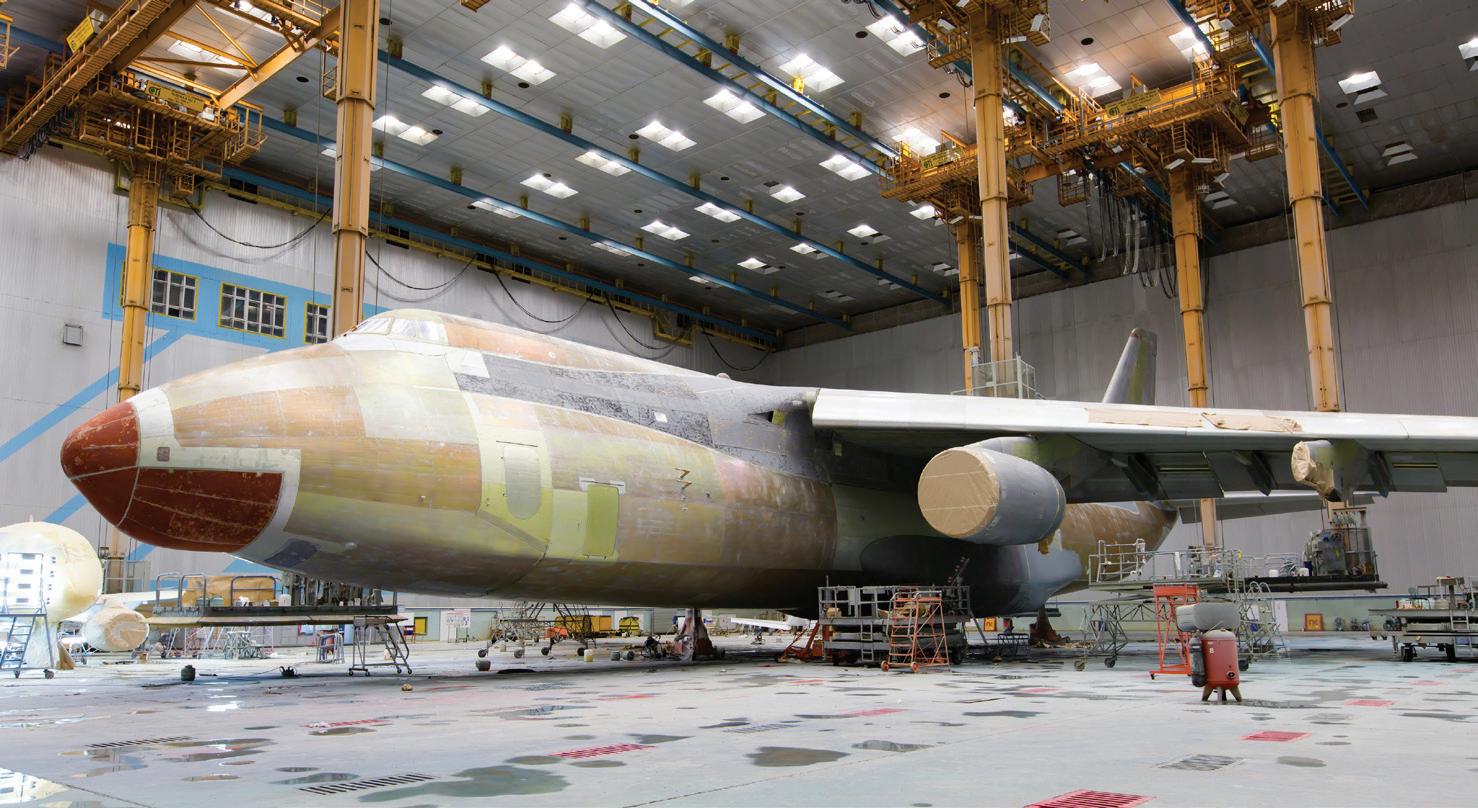
But with the savings in weight and improvements in efficiency, these drawbacks are likely ones that operators will be happy to live with, at least temporarily.
A relevant report published in MarketsandMarkets estimates the global market for aerospace composites at USD 29.7 billion in 2022, which is anticipated to reach USD 51.6 billion by 2027, expanding at a CAGR of 11.7% from 2022 to 2027. The market is expanding based on the advantageous performance and resistance characteristics of aerospace composites. Plus, there is a rising demand for fuel efficiency.
The Outlook: Global development of composites will result in materials that will ensure superior strength and performance. The creation and development of new base materials, such as graphene, could favorably alter the weight and strength of future composites and accelerate the change from metal as the primary component to metal as a tertiary component.
AUGUST 2023