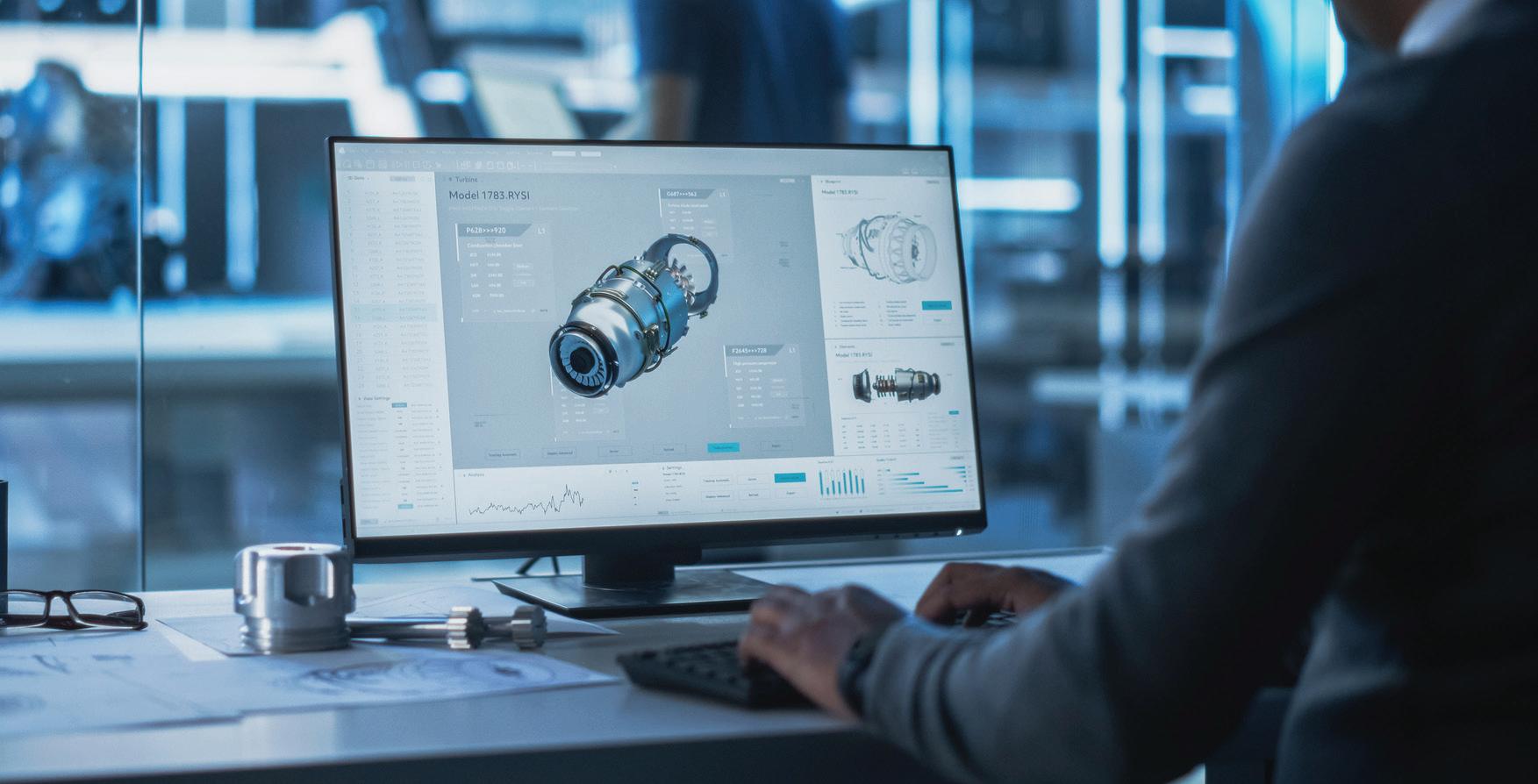
4 minute read
Product Scalability Depends On Design For Manufacturing
By Mark Dohnalek
The days of C-suites supporting new product development without showing specificity on scalability are over.
With the speed that technology advances and rapidly moving consumer trends, scalability has shifted in R&D planning from only a nice-to-have to a critical must-have. Innovations that improve scalability will only be considered when designers, engineers, and strategies can clearly demonstrate scalability and prove how the design can quickly, easily, and affordably be enhanced and integrated to keep up with changes in technology and consumer trends.
But without a crystal ball, how can we predict and prepare for what will come next? That requires approaching product development through the lens of “Design For Manufacturing,” commonly known as DFM. Here’s what it is, what it does, and why it matters.
What DFM Can Do
Ultimately, the DFM process optimizes production by merging the product’s design requirements with its production method, reducing the cost and time to bring a product to market. DFM considers the most important factors—from material selection to part design and assembly processes to quality control—and creates a framework for the rest of the manufacturing process.
Since effective DFM relies on analysis from various stages, the process takes on a more critical role in ensur- ing manufacturability and product quality while keeping manufacturing costs in line throughout the product development life cycle.
Why DFM For Scalability Matters
The ability to design scalable products and scale up production quickly is pivotal for efficiently dealing with increased product demand due to sudden sales surges. From idea to execution, it is essential for scalability to enhance performance, quality, and reliability. Without it, a business may struggle to keep up with demand or face high costs and inefficiencies in expanding production. By designing products with scalability in mind, businesses can optimize their production processes, resulting in increased profitability and competitiveness.
DFM has become a vital component in product development. When applied efficiently and cost-effectively, even at high volumes, DFM strategies help products have staying power, durability, and integration potential as consumer demands shift and technology advances. Here are four aspects of DFM to follow:
1. Material Selection
The right (or wrong) materials can significantly impact a product’s scalability. The wrong materials can postpone production for months or even years—a big no-no when trying to streamline manufacturing rates. Difficult or expensive materials introduce limitations to a product’s scalability as they may not be available in the quantities needed to meet increased demand. This is inevitable with the global supply chain issues that have plagued the world over the past few years. Additionally, using materials prone to defects or inconsistent properties can negatively affect a product’s reliability and performance, making it difficult to scale and impacting trust in the brand. DFM identifies and resolves potential issues with the product design that could impact the quality of the final product. Materials that are easy to work with, readily available, and affordable are typically the best choice for scalable products. By choosing the right materials, businesses can ensure that their products can scale without sacrificing quality or performance.
2. Actual Design
How the product is ultimately designed is fundamental in terms of scalability. How each piece works together to create the final product—every minute detail—is key to ease of manufacturing and assembly. A lot can go wrong when designers don’t understand how design impacts manufacturing. This is why designers need DFM tools to analyze the effects of their design choices on production. Parts that are overly complex or too difficult to manufacture can limit a product’s scalability, as they may be time-consuming or expensive to produce at high volumes. Using DFM, designers can compare design alternatives to understand which has the fewest manufacturability issues and is the least costly to produce, shortening production and distribution timelines.
3. Assembly Ease
Just as the design and number of pieces play a role in ease of manufacturing, ease of assembly is also a major concern. If assembly becomes overly complicated or time-consuming, that reduces efficiency and, as a result, scalability. Products that require human touch to assemble often take valuable minutes to produce and require hiring and paying more staff, increasing overhead production costs. Multiplying these minutes by the number of units produced will extend the time to market by months. The design must be optimized for assembly to reduce manpower and time constraints. Some strong assembly strategies include using modular design, snap-fit components, and incorporating features that enable quick and easy assembly.
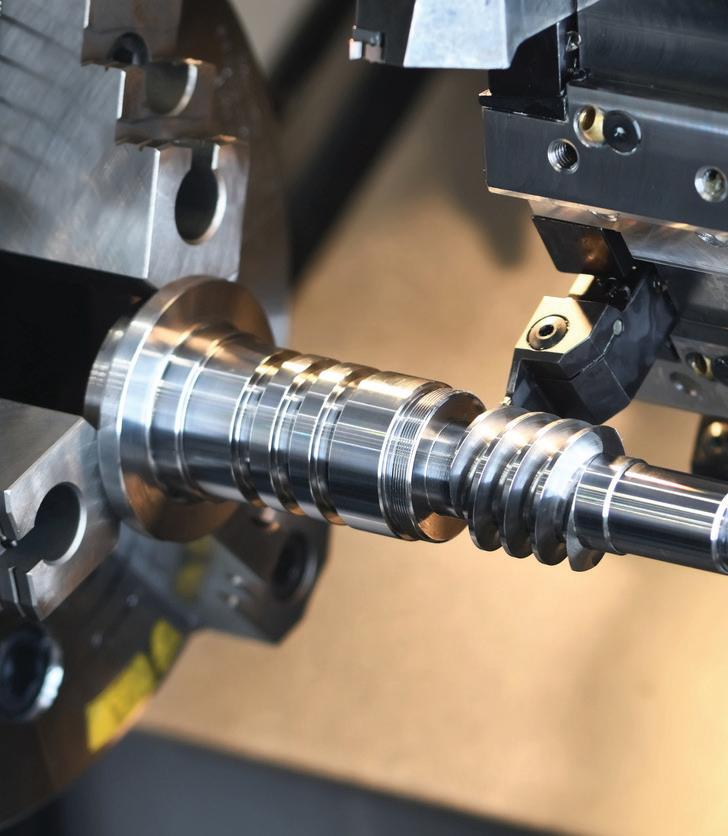
4. Quality Control
Last but not least, quality control is a crucial aspect of product development that is often overlooked. As a product scales, maintaining quality control becomes increasingly challenging, as there are more opportunities for defects and errors to occur. DFM sets quality standards for manufacturability early on to ensure better decisions throughout the design process, fewer redesigns and supply chain disruptions, a high-quality product, and significant savings. By designing products with quality control in mind, businesses can implement processes and procedures that ensure consistent quality even as demand increases.
Products that can scale efficiently are able to meet the demands of their customers and adapt to changing market conditions. With DFM, designers and manufacturers can ensure that products are designed and manufactured in a manner that is time- and cost-efficient, helping businesses bring products to market faster and ensuring their scalability long term. If you don’t have the expertise to use DFM internally, find a partner who can; because when scalability is achieved, it ensures that a product can grow with demand, making it more successful in the market. Good luck!
Mark Dohnalek is President & CEO of Pivot
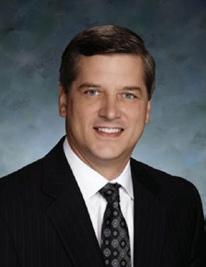
International
(www.pivotint.com), an award-winning US-based global manufacturing, engineering, technology, and product development company with 17 offices across three continents. He can be reached at mdohnalek@pivotint.com and on LinkedIn. n