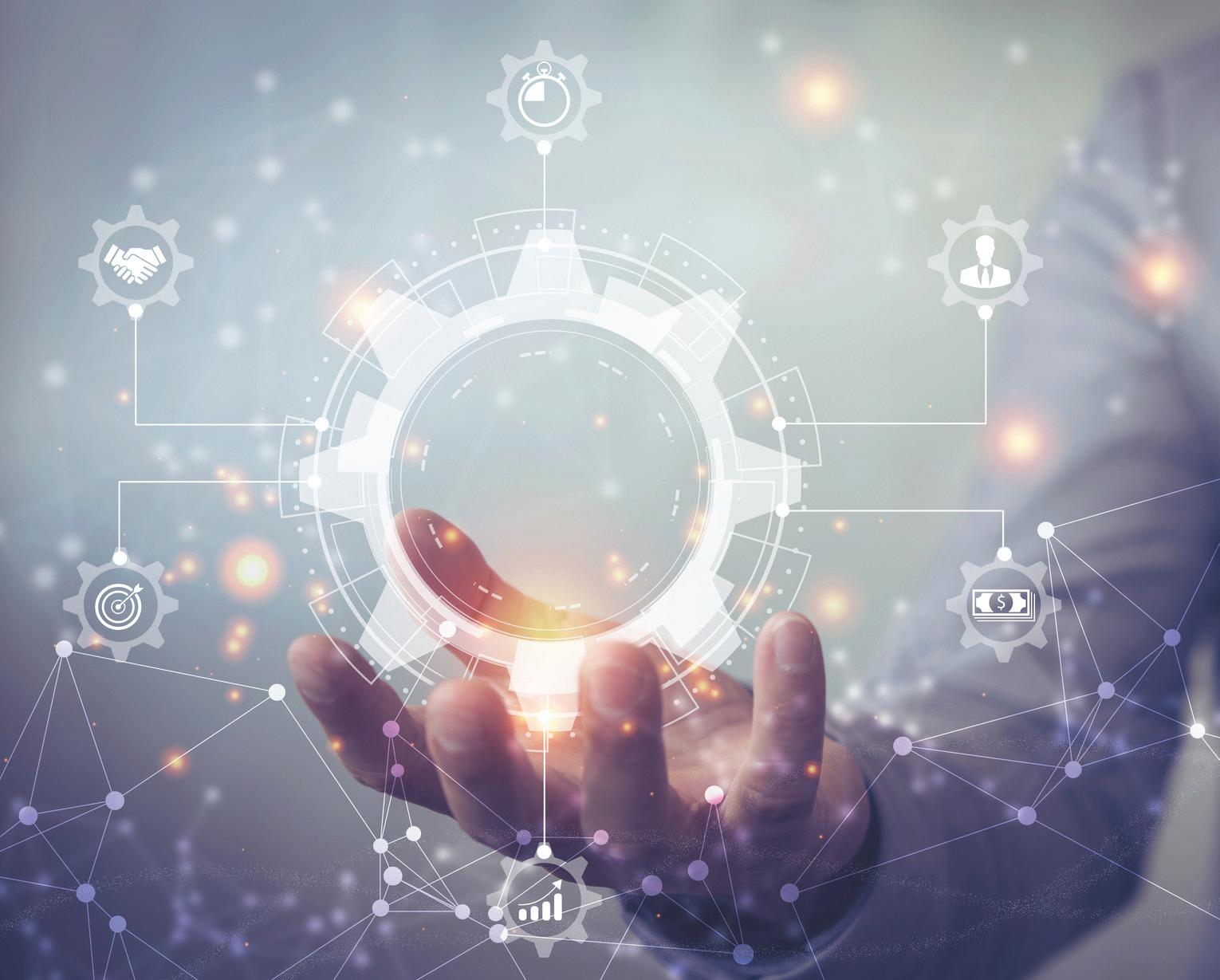
5 minute read
Sustainable Manufacturing Productivity Improvement Is A Holistic Endeavor
By John Abplanalp
Productivity is the key driver of sustainability, but for the last several decades, it has faced unrelenting headwinds. Here are some all-too-sobering data issued on May 4th by the U.S. Bureau of Labor Statistics (BLS) that underscores this chronic problem. According to the BLS, “Nonfarm business sector labor productivity decreased 2.7 percent in the first quarter of 2023, as output increased 0.2 percent and hours worked increased 3.0 percent. From the same quarter a year ago, nonfarm business sector labor productivity decreased by 0.9 percent, reflecting a 1.3 percent increase in output and a 2.3 percent increase in hours worked. The 0.9-percent productivity decline is the first time the four-quarter change series has remained negative for five consecutive quarters since the bureau first began recording these numbers in 1948.
With numbers like that in mind, sustainable productivity should be a top priority with every manufacturing leader and executive as a perpetual journey, not a destination. It’s a marathon run, and won, one step at a time. And it requires a workforce who are universally focused, motivated and engaged as valued, vital, and key contributors to the process. One noteworthy quote about productivity comes from William E. Simon, former U.S.
Secretary of the Treasury, who said, “Productivity and the growth of productivity must be the first two economic considerations at all times, not the last. It is through those two things that innovation, jobs, and wealth are created.” And this holds true both in a micro sense, the company itself, and, in a macro sense, the overall U.S. economy.
Improving productivity is a realworld, day-to-day effort that is also enabled and empowered by information. Foundational to the data-gathering efforts is instituting a holistic process from the outset that generates the most useful data. In my experience, that data-gathering mechanism can be best served through the contributions of an organization’s entire workforce. From the c-suite to the production floor, identifying the barriers to a company’s productivity is a real-world endeavor that frequently yields its best results through a unified effort, especially that of a manufacturer’s workforce.
If the goal is to eliminate the non-value-added work that roadblocks manufacturing productivity continuously (then let everything else start falling into place), who better to enlist in the process than the very people who are primarily responsible for that productivity? Their observations and experiences can prove invaluable in designing the same information-gathering systems from which they directly benefit.
But data, no matter how expansive or comprehensive, is still data. It is the human factor that makes the difference in bending the productivity curve. It is people, first and foremost, who evaluate, analyze, and put that data into action. They transform digital information into real-world results. The confluence of the virtual and real world has been well underway for some time now, with a dramatic B2C evolution in focus from customer-first to people-first. Howard Schultz, the former CEO and Chairman of Starbucks, noted, “We are not in the coffee business, serving people, but in the people business, serving coffee.”
In today’s world of B2B, empowering a workforce, from top to bottom, to provide opinions and recommenda- tions that contribute to success is a core tenet of sustainable productivity. Employees have found their voice, and they express it through their feet, moving towards or away from companies that do not value their roles and contributions. Employees are responsible for products, services, and solutions that attract and retain customers. If employees are not engaged, efficiency, productivity, profitability, competitive position, and revenue, along with enterprise value, all suffer.
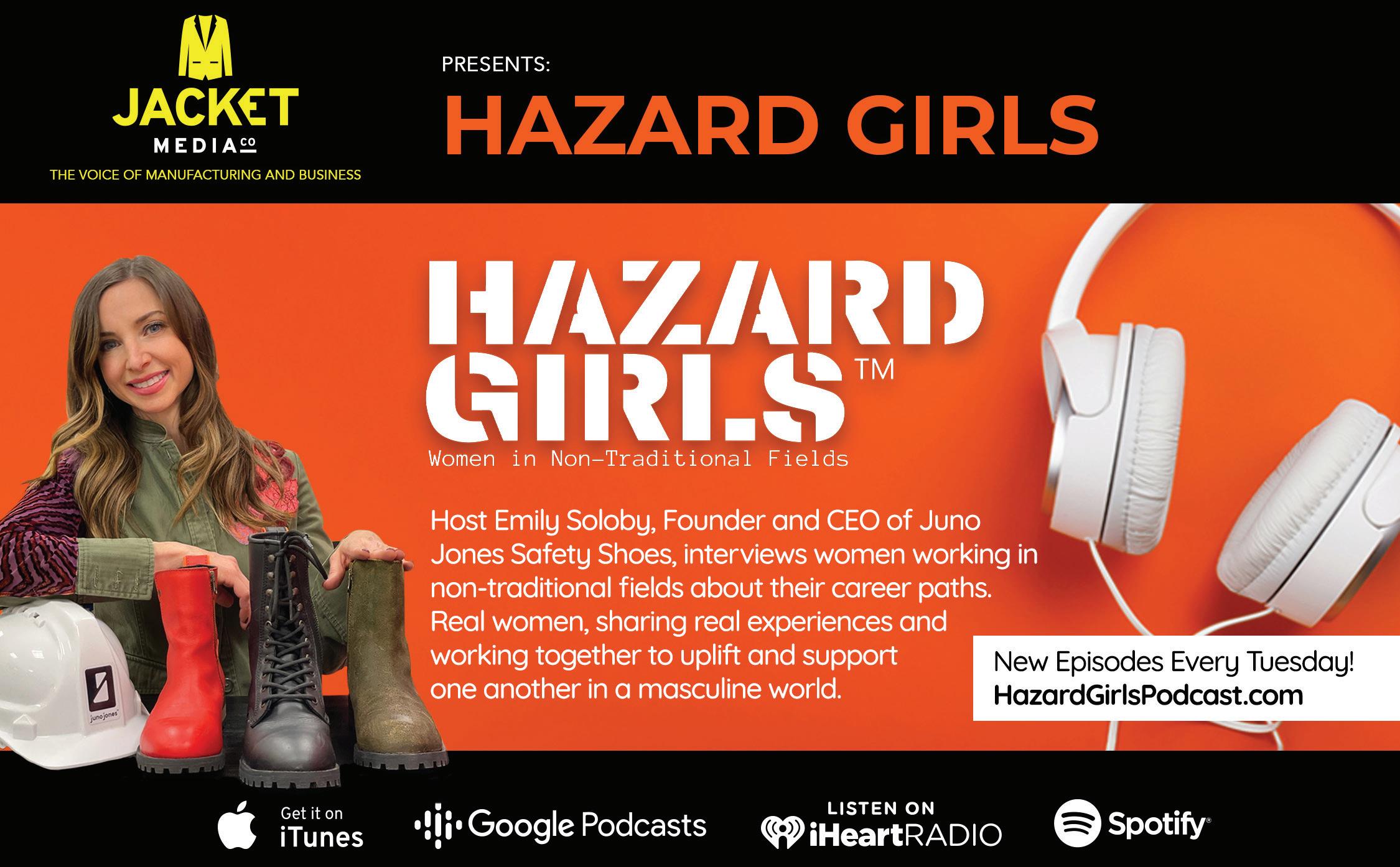
In the post-pandemic workplace, the employee value proposition must be a consideration in every strategy and company decision. That requires shifting from an “employee’s work for me” attitude to an “employee’s work with me” mindset. This transformation will inspire membership, not followership. Followers take on “accessory” roles, while membership is about having an “owner’s” mentality and spirit as contributors and co-builders of the vision.
Consistently soliciting employees as engaged contributors is an essential component that drives sustainable productivity. When employees become engaged contributors, the output is increased collaboration, execution, engagement, innovation, production, and revenues. As an example, real-time shop floor data collection enables warehouses to optimize productivity, gathering data from processes so that manufacturers can drive advancements for a broad variety of metrics. These include improving the quality of products, improved traceability and compliance, longer equipment life spans, more rapid cycle times, and highly precise control of inventory.
At the outset, it is important to identify and understand the underlying barriers and challenges to a company’s productivity. This step is critical because acquiring and implementing an organization-wide data collection and analytics platform can be both time-consuming and expensive. By performing this due diligence first, the process of selection becomes more efficient and effective across all metrics.
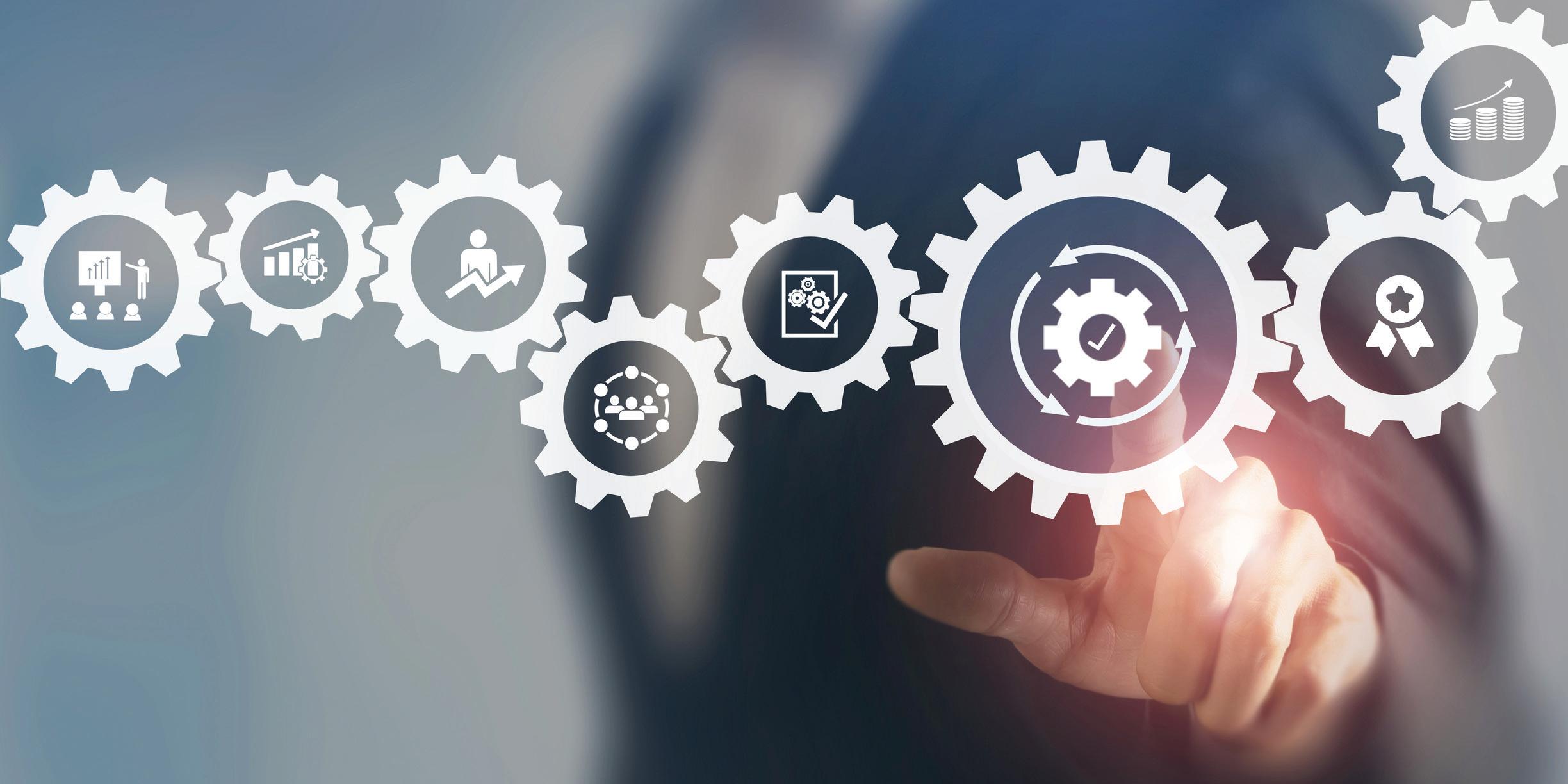
So, how do you manage the risks and opportunities in both the short and long term? Here are a few thoughts that I hope will help you as you seek to bend your productivity curve.
1. Establish a robust ecosystem of appropriate and meaningful data collection. Usually the obstacles to productivity, along with overall operating efficiency, give the organization the beginnings of the understanding of its relationship and overall effect on profitability, competitive position, and value creation within your organization and throughout your entire supply chain.
2. Invest in a data collection platform that provides a holistic and robust compilation of information.
3. From the executive offices to the manufacturing floor, arm your workforce with the type of copious real-time data that drives timely analysis and smart decisions.
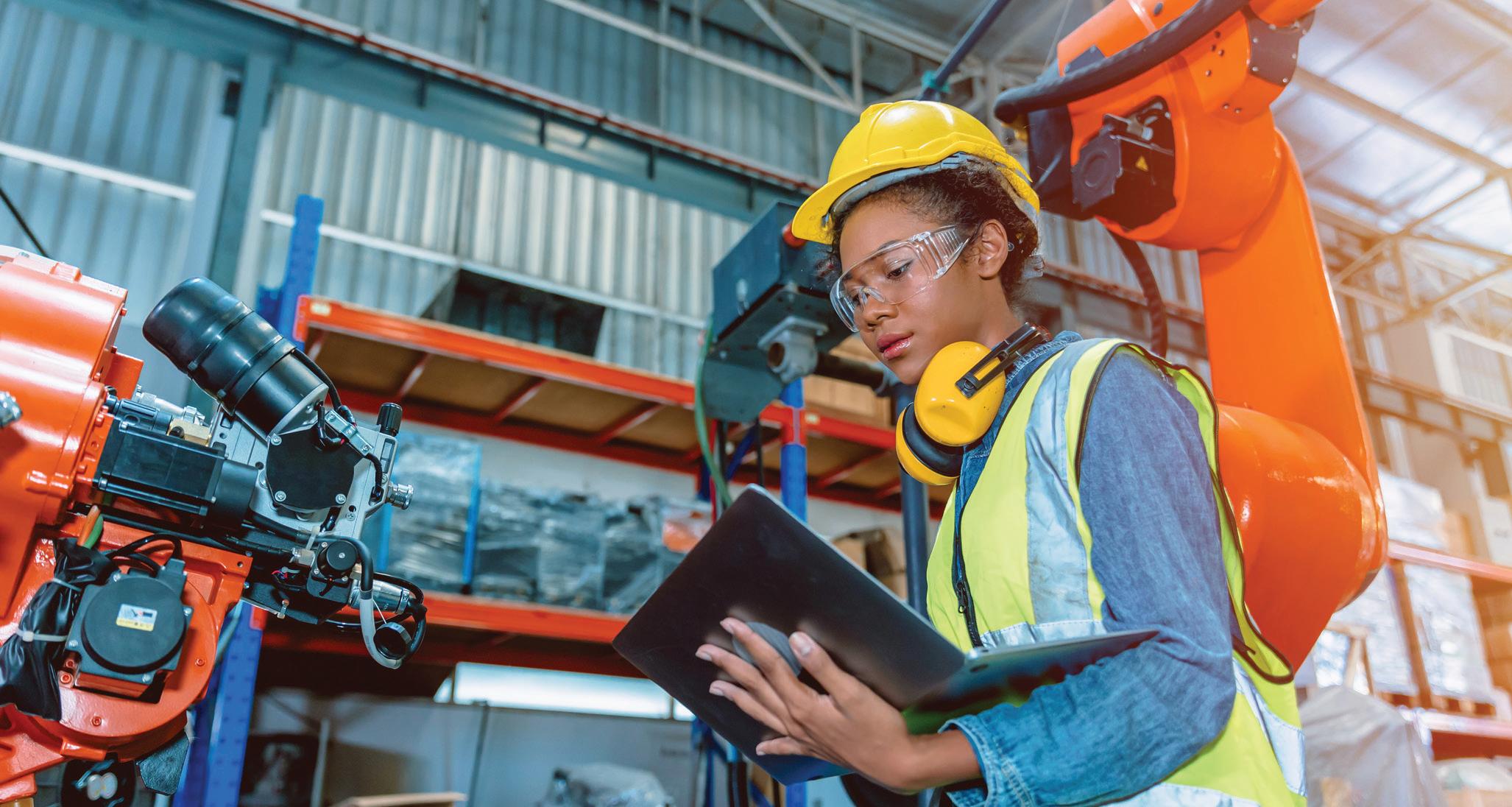
4. Train, develop, and empower the people/employee stakeholders throughout your organization to play a meaningful role in your company and its success. Their shared ownership in its growth and achievements will generate a plethora of benefits, from loyalty to efficiency and much, much more.
5. Encourage collaboration and the sharing of findings and insights that drive innovation and efficiencies for all involved.
While many challenges exist and more will inevitably emerge, now is the time to start driving productivity by taking advantage of opportunities whenever and wherever they appear. To capitalize, leaders must apply a purpose-driven process, keeping one eye on current conditions and the other squarely on reimagining their organization for whatever the future holds.
John Abplanalp has spent more than 35 years in manufacturing. He is an experienced, respected industry leader and innovator who has learned from the bottom up. John began as an assembly mechanic responsible for the setup and maintenance of the aerosol valve assembly lines, most recently serving as CEO and President of Precision Valve Corporation from 2003 to 2013 and Chairman of the Board from 2013 to 2015.
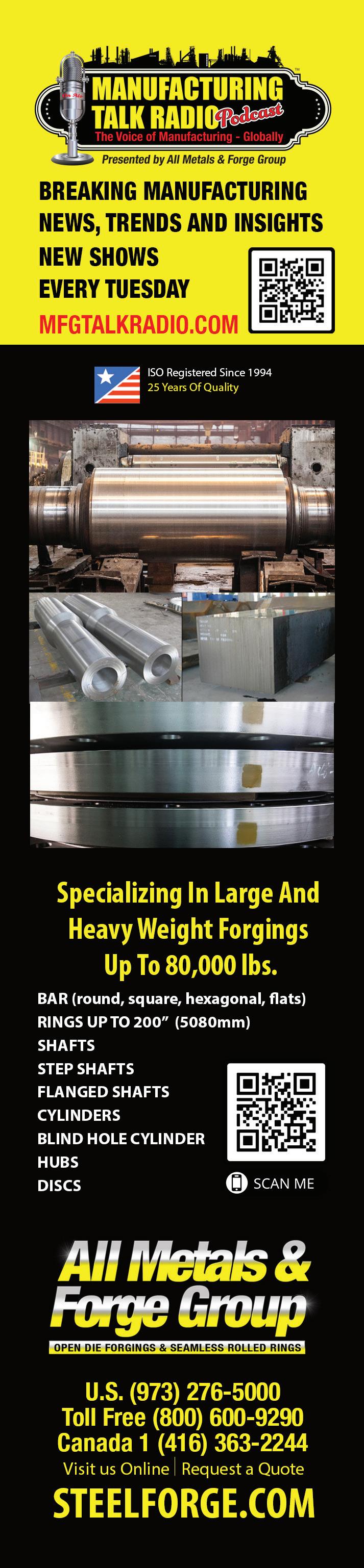
During the time in between, John attended college, receiving an undergraduate degree in mechanical engineering from Manhattan College and an MBA from Fordham University. Returning from college, he was awarded a position in the corporate offices as a business analyst reviewing various business ventures held by Precision. In 1989, he was promoted to Vice President of North American Operations and developed and implemented Total Quality Management programs throughout the Precision Valve Corporation. Through his leadership, the sales of Precision Valve Corporation increased from $250 million in 2003 to $343 million in 2008, a 37% increase in revenue over a brief five-year period.
John’s broad expertise and experience in strategic planning, management, OEE, operational improvement, plant facilities layout/design and international business provides an extensive knowledge base to assist clients in overcoming their challenges.n
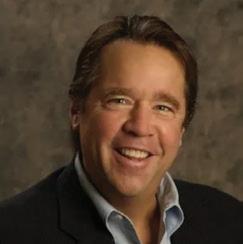