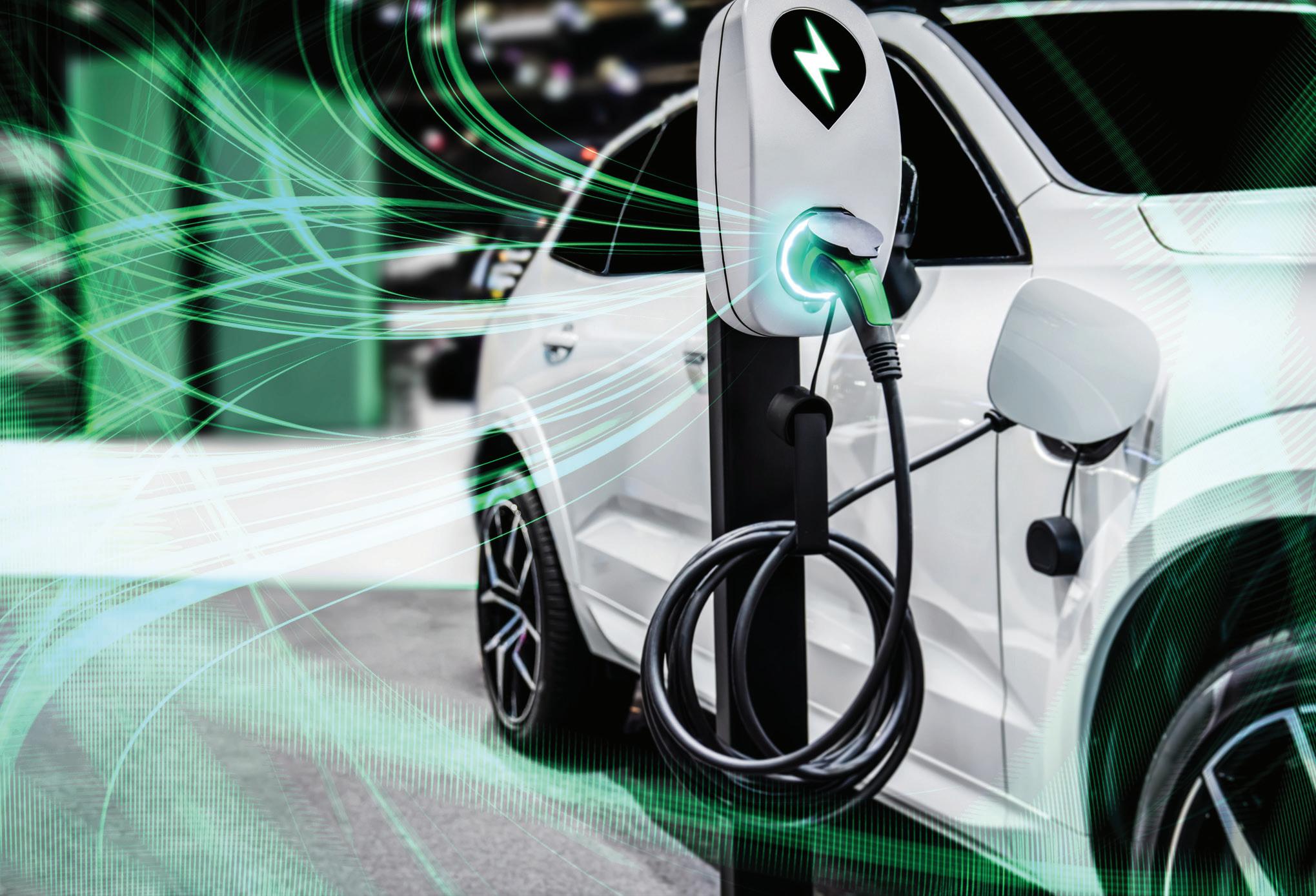
2 minute read
ENERGY OUTLOOK
Keeping Down E.V. Energy Costs
by Royce Lowe
to reduce reliance on rare earths. Model 3 and Model Y powertrains have already reduced consumption of heavy rare earths by a quarter, and Tesla’s next drive unit will include a permanent magnet motor that doesn’t use any of the materials, according to Colin Campbell, VicePresident of Powertrain Engineering. The automaker is looking to keep driving down costs, stay away from environmental and health risks, and reduce reliance on commodities that may be susceptible to wide price swings.
Tesla recently decided to tell the world that it wants to remove rare earths from future models. This caused quite a reaction, and shares of Chinese rare-earth miners were heavily sold off at the news. At the same time, it is hoped that the announcement will spur global efforts to come up with alternatives for electric car motors that currently rely on the materials. Other carmakers, including BMW, Toyota, and General Motors, have also sought continued
China has long had control of the rare earth supply chain. This has led to unpredictable prices. Rare earths are used in magnets in everything from phones to wind turbines and fighter aircraft, and the unpredictable prices have long been a problem for the auto and the clean-energy sectors. China accounts for around two-thirds of mining and 85% of refining of the materials. The risks of relying on Beijing were highlighted in 2010 when prices spiked on China’s decision to cut exports and in 2019 and 2020 amid speculation that shipments might be limited again amid trade tensions with the U.S.
The lack of diversity in rare earth permanent magnet supply chains is “a key concern for the industry within the geopolitics of critical materials,” said Nils Backeberg, founder of Londonbased consultancy Project Blue. “Use of cheaper - though less performanceand efficiency-focused - technologies is likely to become more widespread.”
One potential alternative is ferrite magnets, a mix of iron and such materials as barium and strontium, which are more widely available and cheaper, according to William Roberts, a senior research analyst at Londonbased consultancy Rho Motion. G.M. has previously used these, and Japanbased Proterial said in December it had developed motors using ferrite magnets that performed as well as components using rare earths. Minneapolis-based Niron Magnetics, which has partnered with Volvo Car, last year won a $17.5 million U.S. Energy Department grant to help scale up work on rare-earth free magnets that use iron nitride-based technology.
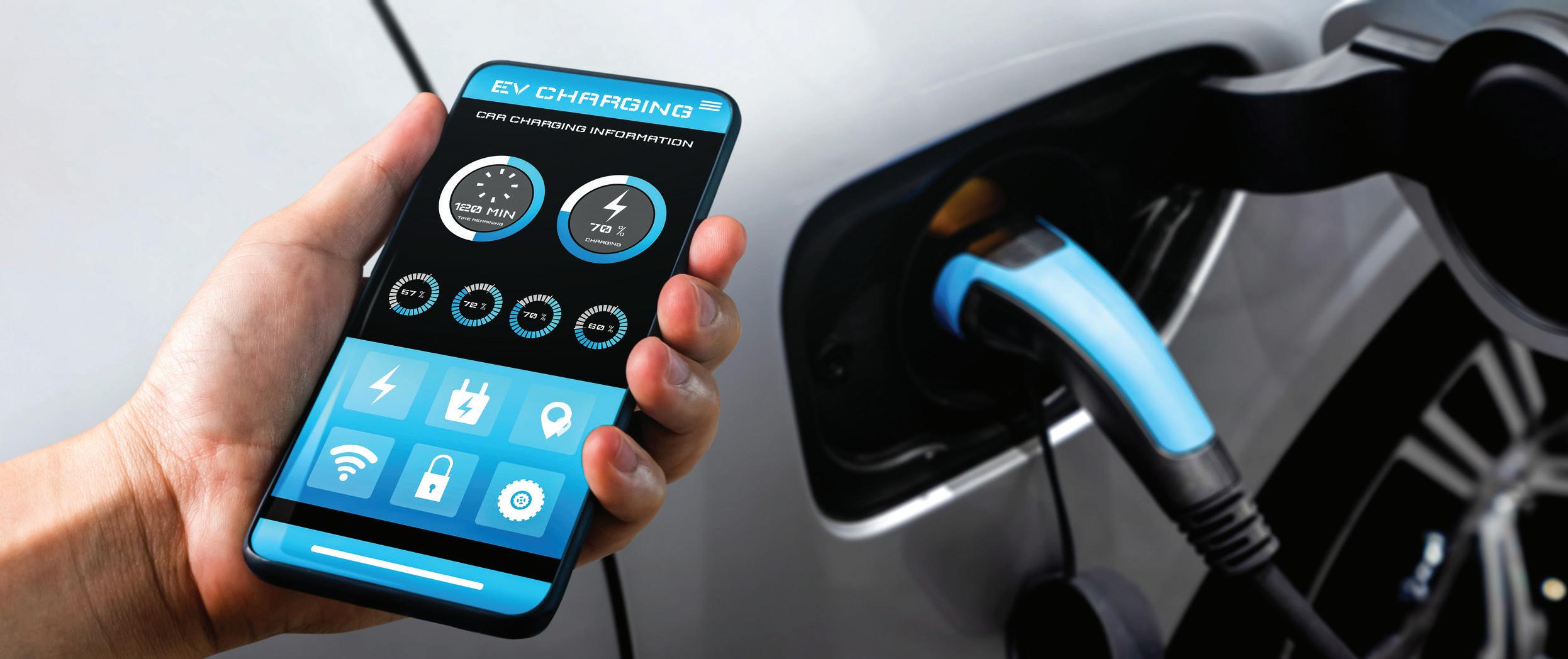
A team from the University of Cambridge and colleagues from Austria announced a new method to make tetrataenite, a possible replacement for rare-earth magnets, in a research paper published last year. It may be possible to produce tetrataenite, an iron-nickel alloy, at scale by adding phosphorus, the researchers found. Previously, making tetrataenite, whose magnetic properties approach those of rareearth magnets, in the laboratory, relied on impractical methods, they said. The researchers are hoping to work with major magnet manufacturers to determine whether tetrataenite might be suitable for highperformance magnets.
Ferrite magnets are the most likely candidate for Tesla’s innovation, according to research firm Adamas Intelligence, though the technology faces a challenge as it has traditionally come with a “significant weight or efficiency penalty.” Existing rare earth-based motor systems also have a track record of efficiency, and demand for the materials in electric vehicles and renewable energy is forecast to surge. About $3.8 billion of magnet rare earth oxides were consumed in energy-transition-related applications in 2022, and the figure will reach more than $36 billion in 2035, Adamas forecasts.
The Outlook - As alternatives are developed by creative minds with unique approaches to problem materials or critical components, manufacturers in the U.S. (and other countries) will reduce or remove rare earths and other conflict components, defined as any element or component that is reliant upon a supply source subject to current or ongoing geopolitical, socioeconomic, strategic, or extreme cost volatility.
Author profile: Royce Lowe, Manufacturing Talk Radio, UK and EU International Correspondent, Contributing Writer, Manufacturing Outlook n