
30 minute read
Articles
Image for representation
Guwahati Metro
Advertisement
Copyright: Alstom Transport
The Guwahati Metro is a 61.40 km long Mass Rapid Transit System (MRTS) system proposed for the city of Guwahati, Assam, India. The proposed system consists of 4 corridors and 54 stations.
In January 2016, The Detailed Project Report (DPR) and Feasibility Report of Guwahati Metro Phase 1 were prepared by RITES. On February 26, 2016, The DPR and the formation of Guwahati Metro Rail Corporation Limited (GMRCL) to execute the project were approved byAssam’s state government.
Subsequently, State Cabinet in January 2017 has reviewed the project and suggested to modify the DPR with additional lines connecting Dharapur with Guwahati Airport and North Guwahati with AIIMS in Phase 1 itself.
As of March 2020, RITES has been tasked with preparing a Comprehensive Mobility Plan (CMP) & Alternative Analysis (AA) Report for Guwahati. Afterthe approval ofthese reports, Guwahati Metro’s DPR will be modified and finalized accordingly.
Guwahati Metro Phase 1 Routes (Proposed) RITES prepared Feasibility report of total corridor length of 200 km and DPR (PhaseI) for the total length of 61.4 Km in January 2016. The Phase-I have 4 corridors:
Corridor-1: Dharapur– Narangi (Elevated) Corridor-2: M. G. Road to Khanapara (Underground) Corridor-3:Jalukbari to Khanapara (Elevated) Corridor-4: ISBTto Paltanbazar(Elevated)
Corridor-1: Dharapur – Narangi (Elevated) Length: 22.6 km Type: Elevated Number of Stations: 22 Corridor-2: MG Road – Khanapara (Underground)
Length: 10 km Type: Underground Number of Stations: 10 Corridor-3:: Jalukbari – Khanapara (Elevated)
Length: 19.4 km Type: Elevated Number of Stations: 14 Corridor-4: ISBT– Paltan Bazar (Elevated)
Length: 9.4 km Type: Elevated Number of Stations: 8 Additional potential lines being explored: • Dharapur – Guwahati Airport • North Guwahati – AIIMS
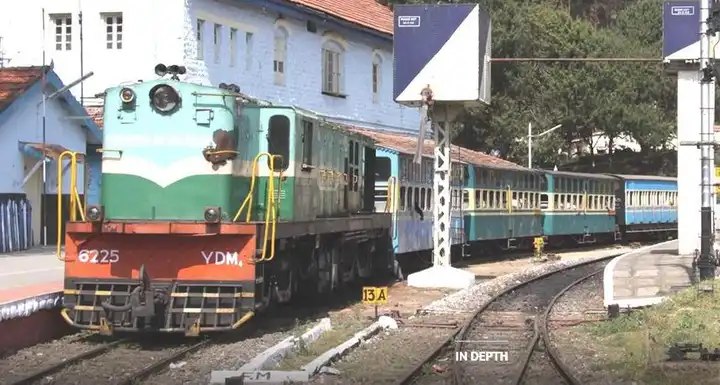
India to trial Hydrogen Fuel Cell Trainset
Indian Railways expects to roll-out a four-car hydrogen fuel cell multiple-unit by the end of 2021, as the country looks to alternative fuels as a way of reducing greenhouse gas emissions from the transport sector.
* Bharti Jain is an electronics and communication engineer, who began her career in the telecommunications sector before joining Rites as a project manager for signalling & telecommunication projects. She is currentlyworking on Indian Railways’ alternative energy initiatives and semi high speed rail projects. Next year will see the development of India’s first hydrogen-powered train, with a four-car demonstrator due to be rolled out of the Diesel Loco Modernisation Works in Patiala before the end of 2021. Mirroring initiatives in other parts of the world, the fuel cell powered multipleunit will be used to investigate the potential for decarbonising the rail sector, building on government plans to accelerate the use of hydrogen across the national economy.
India has one of the fastest growing economies in the world, with the rapid expansion of heavy industries and other production. This has resulted in a significant increase in greenhouse gas emissions from both the industrial and transport sectors, notably carbon dioxide and carbon monoxide. According to a report by the Potsdam Institute for Climate Impact Research, India’s GHG emissions in 2015 stood at 3.6 million gigatonnes of CO2 equivalent, or about 7% of global emissions. That makes it the world’s third largest emitter of greenhouse gases. Climate change due to GHG emissions has been recognised as an increasingly important issue in recent years, with CO2 a major contributor. At present, roughly one-third of global CO2 emissions come from industries and a quarter from the transport sector. If current trends continue, by 2050 there would be a 55% increase in transport emissions, and 38% of global CO2 emissions would come from just seven industrial and transport sectors.
Bharti Jain
PMP and ISO 9001:2015 Certified Project manager working in RITES Ltd, Ministry of Railways
According to the International Transport Forum, global freight and passenger transport volumes are projected to grow three-fold by 2050. Demand is being driven by multiple factors such as economic globalisation, increasing population, urbanisation, tourism, rising international trade and the diversification of product value chains. More and more industries are moving away from manufacturing products at a single location, and expanding technology-specific production units which require the integration of components sourced from factories around the world.
Hence the need to move both industry and transport to more sustainable forms of energy. To this end, rapid technological development and falling costs are helping to stimulate greater use of renewable energy sources. As part of its contribution to international efforts to limit the global temperature rise to 1·5°C, India is looking to achieve zero emissions from its heavy industry and transport sectors by around 2060. It has been working to reduce emissions from the transport sector through a range of initiatives. These include encouraging a shift from two-stroke to four-stroke internal combustion engines for road vehicles, the adoption of alternative fuels such as CNG or biofuels and the takeup of electric vehicles.
In the rail sector, there are multiple alternatives for reducing carbon emissions, including biofuels, synthetic fuels, electrification and hydrogen. India has committed significant investment to accelerate the electrification of its national rail network, while the advent of a hydrogen-propelled train will provide a further weapon in the armoury for the fight against climate change.
WhyHydrogen?
The Covid-19 pandemic has helped to underline more than ever the need to take sustainability seriously, and this has manifested into widespread enthusiasm for hydrogen as a commercial energy source. Between November 2019 and September 2020, India’s project pipeline for green hydrogen production has grown from 3·5 GW to just over 15 GW, signalling the emergence of a growing hydrogen economy.
The Indian government is driving a number of initiatives to increase hydrogen production. The Ministry of New & Renewable Energy and major power generation players such as Indian Oil Corp Ltd and National Thermal Power Corp have committed to the establishment of hydrogen production units across the country and the implementation of fuel cell technology. Significant investment is envisaged by both public and private firms and the use of hydrogen is expected to expand between three- and 10-fold by 2050.
In keeping with this trend, Indian Railways has begun to investigate the potential for hydrogen traction, as a cleaner fuel which is both convenient and cheap to obtain.
Both battery and hydrogen trains have been considered as an alternative to diesel traction for operation on non-electrified routes. Conventional locomotives would need large and heavy batteries to operate over long distances or haul heavy payloads. Fuel cells offer a lower weight, better payload and a longer range. The consumption rate of hydrogen is less than diesel fuel, while the trains are quieter in operation. Unlike conventional diesel engines, hydrogen-fuelled trains emit only water vapour at the point of use. This results in minimum heat and low well-to-wheel . Given the right infrastructure, hydrogen is safe to handle and vehicles can be refuelled quickly, resulting in minimal downtime. Amongst the fuel variants, green hydrogen is considered to be the best alternative, being extracted from water using renewable energy such as solar or hydro power. This is preferable to ‘ grey’ hydrogen produced by reforming fossil fuels or ‘blue’ hydrogen generated from natural gas.
Given the rapidly expanding production pipeline and investment in renewable energy generation, the cost of green hydrogen is expected to fall by up to 65% between 2030 and 2040. This would make hydrogen more economic than fossil fuels, where prices are predicted to rise as a result of restricted supply and government policies. Fuel cell manufacturing costs are also expected to fall, given that they are assembled from stacks of standard components.
Hence, IR considers that hydrogen is likely to be the most promising technology for achieving a zero-emission railway network by 2030.
Article continues below ↓
Fuel Cell Basics
Various types of fuel cell are now available, which are typically classified by the type of electrolyte used. They include Proton Exchange Membrane, Alkaline, Phosphoric Acid, Solid Oxide and Molten Carbonate fuel cells. Indian Railways has opted to use PEM technology in its hybrid trainset, because of the low operating temperature (50 to 100°C), short starting time and the ease of using ambient air as the oxidant.
Each fuel cell transforms the chemical energy of hydrogen and oxygen to produce power. The electrodes (anode for hydrogen and cathode for oxygen) are separated by an electrolyte, which prevents the reactants from mixing directly and controls the charged ions created during the partial cell reactions.
Hydrogen molecules enter the anode and react with a catalytic coating on the anode, releasing electrons to form a positively charged hydrogen ion. While the free electrons cannot pass through the electrolyte, the ions reach the cathode and flow into an electrical circuit, generating power. The cathode causes the hydrogen ions and free electrons to react with oxygen from the air to form watervapour.
A single fuel cell under load produces between 0·6 V and 0·8 V, so multiple cells are stacked togetherto produce highervoltages.
Global Development

Internationally, countries such as Germany, Netherlands, France, South Korea, Japan and the UK are investing in the development of trains powered by hydrogen fuel cells as a part of their route to a carbon-neutral future.
when Alstom selected Hydrogenics as a key partner to develop the fuel cell technologies for its Coradia iLint project. The world’s first production fuel cell train has roof-mounted power modules and hydrogen storage tanks. During operation hydrogen is combined with oxygen drawn from the ambient air, in order to charge underfloor batteries which in turn powerthe electric traction motors.
Unveiled at the InnoTrans 2016 trade fair in Berlin, Coradia iLint demonstrated a range of up to 1000 km between refuelling, and a similar performance to conventional diesel multiple-units, with lower noise and environmental impact. Two prototype units entered service in September 2018 for an 18 month trial on the Buxtehude – Bremervörde – Bremerhaven – Cuxhaven line in northern Germany. The units have also been demonstrated in other countries including Austria and the Netherlands, where tests were successfully conducted in March 2020.
Alstom has so far received orders for 41 Coradia iLint trainsets. The first 14 are due to enter service in Niedersachsen during 2021, and the other 27 will be used in the Rhein-Main region from the end of 2022.
In June 2019, the UK launched its HydroFlex demonstrator, developed by Porterbrook and the University of Birmingham, and this undertook its first main line trials in October 2020. HydroFlex has been created by fitting a fuel cell power pack to an existing Class 319 EMU, enabling it to run on electrified or non-electrified routes without modifying driver’s controls.
Rolling stock leasing company Eversholt Rail is working with Alstom to develop a hydrogen multiple-unit to fit the restricted UK loading gauge; again using converted EMUs, the first Breeze trainset is expected to take to the rails in 2024. And in France, SNCF hopes to have its first fuel cell train in operation by 2022, with a viewto eliminating diesel traction by 2035.
Having been early in the field with its New EnergyTrain, East Japan Railway is looking to start testing its second hydrogen-powered trainset in 2021 at up to 100 km/h, with the first commercial version to be released by 2024. Korea Railroad Research Institute is also developing a fuel cell powered train for completion in 2022. This has been specified to achieve a range of 600 km on a single charge at a maximum speed of 110 kmph.
Electrification is likely to remain the most effective strategy for reducing carbon emissions from heavy freight haulage. India’s Hydrogen Prototype Indian Railways has completed the design for a 300 kW fuel-cell-hybrid trainset rebuilt from an existing diesel-electric suburban multiple-unit. This will be assembled by the Diesel Loco Modernisation Works at Patiala in Punjab and is expected to be completed by the end of 2021. Modification of an existing train for hybrid operation is intended to speed development and minimise the manufacturing cost.
According to IR, this will be the most powerful fuel cell trainset yet developed. As with many of the other hydrogen trains, it will have a maximum speed of 140 km/h. While the actual fuel cell power plant will be imported, the hydrogen storage system and lead acid battery packs will be supplied by Indian manufacturers. The gas will be fed to the PEM fuel cells (left), which will be mounted on the roof.

To avoid any loss of energy generated bythe fuel cells, the train will be fitted with lead-acid batteries to store electricity produced during non-operational periods. The batteries will also capture regenerated braking energy, and help to smooth out the power demand under real-life driving conditions. DC-DC converters in the powervehicle will balance the voltage difference between the fuel cells and batteries. While the long-term intention is to use green hydrogen, the current plans envisage that the hybrid demonstrator would initially be powered using hydrogen obtained from industries which generate it as a by-product.
In-House Hydrogen Production
As well as investigating the use of fuel cells to power trains, IR is looking at the scope for developing its own hydrogen production systems, using water electrolysis powered by energy from renewable sources. There are currently two areas of investigation: nano materials and metal-oxide catalysts.
The first would see nanoparticles fitted on existing solar cells, to mimic photosynthesis and separate hydrogen from water in the presence of sunlight. This approach has two key benefits. Firstly, it is a low-cost technology, and secondly it can work with seawater orwastewater, avoiding the potential wastage of clean water.
The metal oxide method combines electrolysis with low-cost catalysts such as Spinel oxides to improve performance. Electrolysis is an established way to extract from water. Electricity is passed through water in an electrolyser, triggering two chemical reactions which produce hydrogen and oxygen. These two gases are then kept separate by a membrane. However, the oxygen revolution reaction is relatively sluggish, lowering the energy efficiency of the overall conversion. Spinel oxides are typically made of cheap transition metals and have been demonstrated as a stable, low-cost catalyst that could speed up the process and overcome the energy loss.

IR is also experimenting with the production of ‘blue’ and ‘ grey’ hydrogen from biogas or oil feedstock.
Other Indian conglomerates now delving into green hydrogen production include NTPC and Tata Motors. Reliance Industries Ltd recently announced its intention to become a net carbon zero firm by 2030 by getting into green hydrogen production and replacing its transport fuels with clean electricity and hydrogen. Indian companies are working to build a full-stack electrolyser and indigenous fuel cell solutions, combining the powers of digital, power electronics, advanced materials and electrochemistry.

Recently, FTI Consulting entered into an agreement with The Energy & Resources Institute to develop an India Hydrogen Economy Roadmap. This includes the deployment of grey, blue and green hydrogen, carbon capture and renewable energy technologies, as well as research programmes to test the viability of hydrogen as the sustainable fuel choice in an Indian context.
Flash-Butt welded Long Rolled Rails, LRR, of Prime Steel Quality help to lower the Risk of fatal Train Accidents in India
Rolling of Rail at British Steel

Synopsis:
Long Rolled Rails, LRR, of prime steel quality, already tested in the manufacturing plant, and with Flash-Butt Welds of higher strength than that of Alumino Thermic, AT, welds, provide far better alignment and continuity parameters for far smoother train runs, that lower the risk of in-service rail failures, which had led in past decades to nasty, unwanted and fatal train derailment accidents. The mutual impacts of rail and running wheel governed by Newton`s Laws of Motion are on tracks consisting of flash-butt welded long rolled rail panels far lower than on a track consisting ofATwelded short 13 m rails. Long rolled and flash-butt welded rails are a prerequisite for 160 kmph Semi-High Speed Lines in India.
CORRELATION BETWEEN FATAL TRAIN ACCIDENTS AND RAIL TRACKS CONSISTING OFATWELDED SHORT13 m RAILPANELS
There is no other country around the globe than India, from where in the last decades so many nasty and unwanted fatal train accidents could be reported; see contributions in http://www.drwingler.com. Mahakaushal Express Derailment near Kulpahar, 30.03.2017

In India, one thought, one could not keep rails longer than 13 m, otherwise the expansion gaps at the joints, hold together in position by bolted fish-plates, might become too wide; see J.S. Mundrey, Railway Track Engineering, 5th print edition, 2017, page 49, 103 ff and 329, McGraw Hill Education (India) Private Limited, Chennai, ISBN (13): 978- 93-5260-648-1 / ISBN (10): 93 -5260648-5. It had been considered that the gap between the rail ends should be proportional to the length of the rails to allow free expansion during hot weather.
The gaps between rail ends were generally thought to be the prime cause of impact at joints. Although the provision of longer rails would lead to a reduced number of joints, it was dis-favoured due to the increase of impact-density, if proportionately wider gaps were to be provided at the ends.
To weld rails in long lengths was therefore technically disinteresting. It was realized later that the intensity of impact is not directly proportional to the width of the gap, and the gap itself must not be exactly proportional to the length of the rail because the rail does not really behave as a free rail when laid in track. With this realization any reduction in the number of joints was welcome, as it had the prospect to minimize, if not completely eliminate, the problems connected with the jointed track.
With this background the welding of rails into 3 rails, 5 rails and 10 rails was started on Indian Railways. The welded panels have been named “Short Welded Rails” (SWR) as distinct from “ Long Welded Rails” (LWR). The experience with short welded rails has been that joints with panels of length more than 3 rails cause more damage to track than the proportional advantages derived from the elimination of joints. Welded rails panels longer than 3 rails are therefore no longer in use on the Indian rail tracks.
Rails, welded into long strings of 200 m or more, denominated as LWR/CWR, behave differently at the joints and are governed by their own inbuilt system. On LWR/CWR track the expansion and shrinking forces get arrested over the frictions at the rail-seats, the rail-fastenings and sleepers in the track-bed.
With the introduction of concrete sleepers and strongertrack-bed structures efforts are made to have continuously welded track to the extent possible, as jointed track on concrete sleepers is beset with many maintenance problems including the structural failures of concrete sleepers at joints. Step by step the short 13 m panels, jointed by bolted fishplates, have been welded Alumino Thermic (AT) to LWR/CWR tracks.
AT Welding on Kashmir Valley Railway Line; source: Northern Railway; India ModernDigitalcontrolledAT“SmartWeld”
HighQuality RailWelding by Th. Goldschmidt`s Digital controlled Process AT welding is the common conventional welding method, which enables rail to be manually welded in a relatively short time with simple devices at site. However, it is necessary to carefully control its quality at point of installation, in terms of both track component condition, assembly, rand the welding proceedure itself bywell trained work forces.
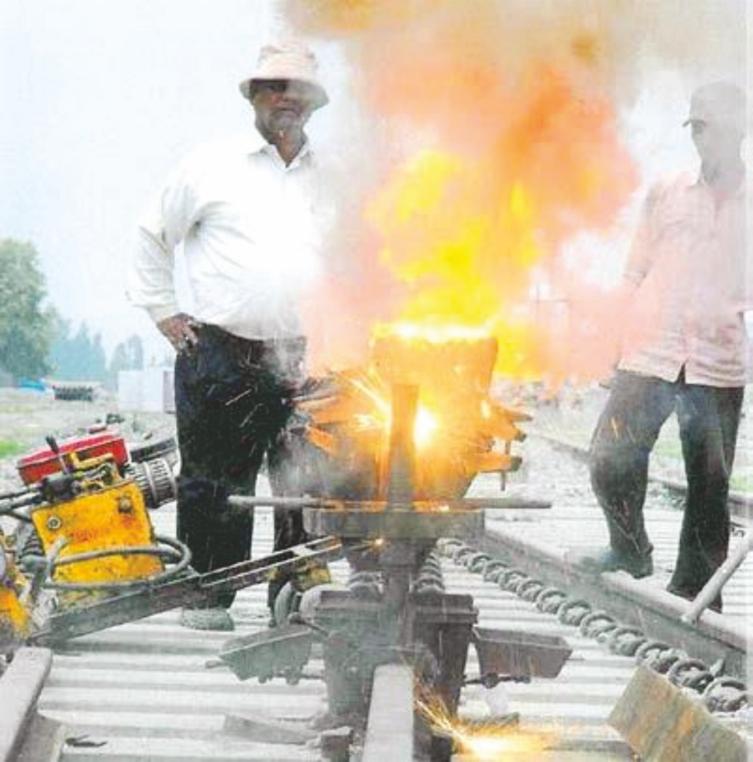
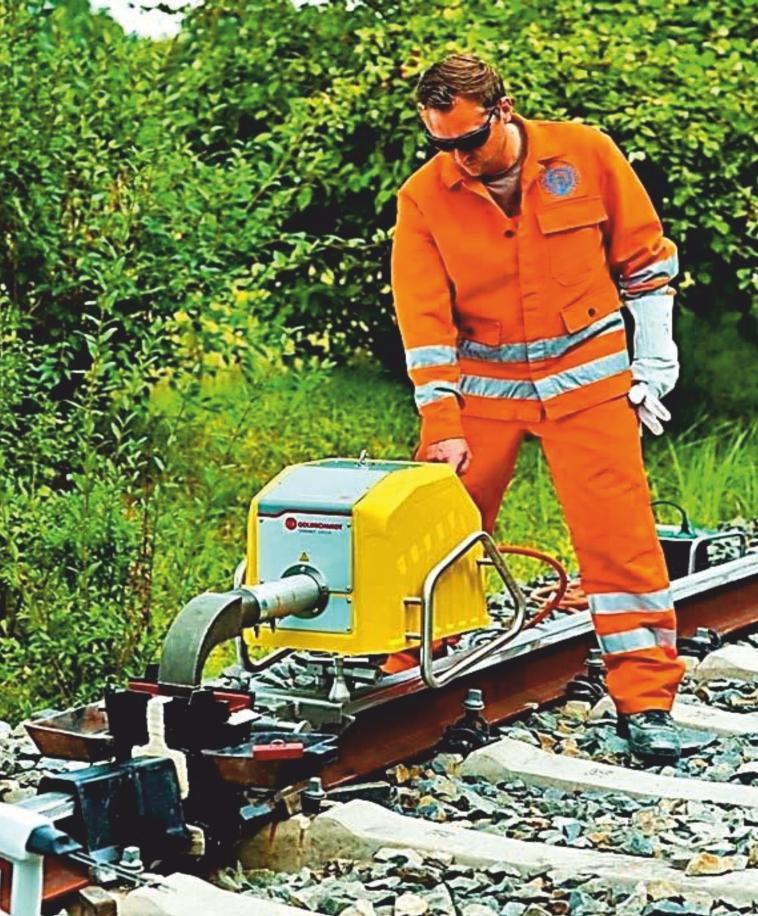
An good quality AT weld has a Fatigue Life of only about 56 % as compared to the parent rail, whereas a Flash-Butt Weld has a Fatigue Life of about 90 %. Japanese Gas Pressure Welds reach a Fatigue Life of 96%, however Gas Pressure Welding needs skilled work-forces and is only best suitable for stationary welding in factory or at site. See M.M. Agarwal, INDIAN RAILWAY TRACK ,twentieth edition, 2017,p.384, Prabha & Co. Delhi, India, ISBN 81900613-1-3.
Often the AT welds on INR tracks are below standard and the Fatigue Life mostly below 56 %. This means, on an Indian LWR/CWR tracks consisting of AT welded 13 m rail panels, there are every 13 m weak spots and discontinuity/disturbance in rail strength and alignment parameters. INR tries to secure those weak spots with Joggle Fish Plates.
The numerous Joggle Fish Plates on INR tracks reveal that INR is aware of the Risks ofATWeld Failures. To mitigate the impact of AT Weld Failures, which may lead to nasty fatal railway accidents, INR therefore tries to secure the AT welds with Joggle Fish Plates:
Finishing, Stripping and Grinding of AT Rail Weld Joggle Fishplate edge, got stipulated. Poor alignments with discontinuities increase the lateral and vertical stress between running Mechanics: NEWTON`S LAWS OF MECHANICS, THE DYNAMICS OF TRACKTRAIN INTERACTIONS AND RELATED PROBLEMS See: A.D. Kerr FUNDAMENTALS OF RAILWAY TRACK ENGINEERING, Simmons Boardman Book, USA, ISBN: 0-911 382-40- 2, 2003, p. 252.

Newton`s FIRST LAW suggests that any change of velocity of a body under consideration must be associated with the counteraction of a resultant force, which acts on his body. This in turn suggests a relationship between the resultant force and the acceleration ofthe body.
Newton assumed by his SECOND LAW the very simple relation that the resultant force, which acts on the body and causes acceleration, is linear related.
every ACTION there is an equal and opposite REACTION”. This is probably the most famous law of motion. This means that if one object 1 acts a force out on another object 2 then object 2 will act the same size force in the opposite direction on object 1; F21 = F12. Here are diagrammes to visually showthis:

Joggle Fishplate Rail Joint for INR from Chandra Industrial Works to secure AT Welds
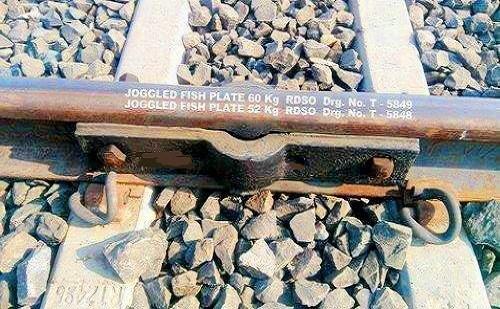
Securing Rail Fracture with temporary
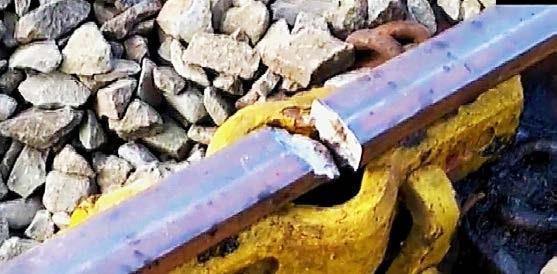
In addition, the alignment of the welds are often inferior. On INR bends in the vertical and horizontal plane ofATwelds are tolerated up to 0.7 mm, measured with a 1.5 m straight edge. For flash-butt welds a tolerance of max. 0.3 mm, measured with a 1.0 m straight wheel/rail-vehicle and rail, governed by the Newton`s Law of The THIRD LAW is the "LAW OF ACTION AND REACTION": “For “Action equals opposite Reaction”; F12 equals F21.
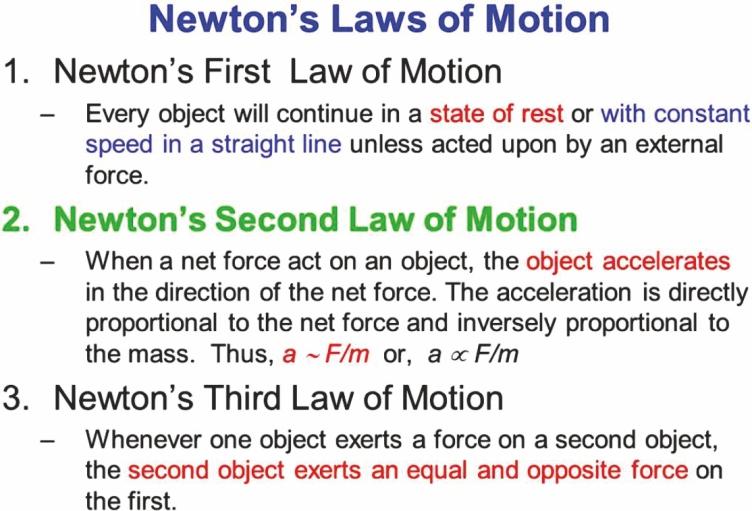
To every Action or Force there is an equal and opposite Reaction or Force.
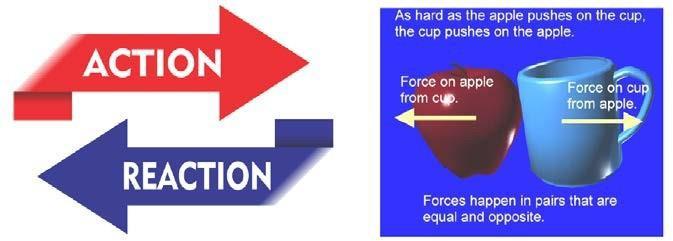
In otherwords, when a body (rail-track) exerts a force on a second body (rail-vehicle), in consequence the second body (rail-vehicle) exerts a numerically equal but opposite force on the first body (rail-track).
The force acted on the rail-vehicle causes acceleration in vertical and/or lateral direction and/or causes rotation movements. The extend of the acceleration and rotation is linear related to the force acted by the railtrack on the rail-vehicle and can be used to detect and measure railtrack defects by means of instruments/devices on board of the railvehicle (Instrumented Revenue Vehicle; IRV). The “IRV” can be a commercial and scheduled running Locomotive, Passenger Coach or Freight Wagon. See: F.A. Wingler: MONITORING INSTRUMENTS MOUNTED ON SCHEDULED RUNNING COMMERCIAL TRAINS (INSTRUMENTED REVENUE VEHICLES, IRV) MAKE USE OF NEWTON`S LAWS OF MECHANICS FOR TRAIN BASED AND INSERVICE TRACK-CONDITION MONITORING IN TARGET PLANING OF MAINTENANCE; published on: May 18, 2018; capacity with tract defects like, kinks, dips, undulations, twists, track components/constituents, poor bearing sub-structure components and poor drainage), rail-table defects and http://www.drwingler.com .
The Railway is a system, where steel-wheels run on steel-rails with a non-elastic contact area of less than 3 cm². This means that track and train interact over a contact area of less than 3 cm², and wheels exert the forces over this small contact area following Newton`s Laws of Mechanics: Oscillating rail-vehicle movements, self-exited or exited by track alignment defects, like Shuttling, Lurching, Bouncing, Rolling, Pitching, Nosing and Hunting, increase further the deterioration rate of an already deteriorated track.

At misaligned and un-straight rail-joints and rail-welds as well by wheels running with flat spots, high impacts are caused. Latter produce high rail and rail-weld bending stress, causing degradation of rail-welds, rails, rail-fastening systems, sleepers, ballast and track substructure components.
The geometrically perfect production of welded rail-joints and the correct alignment and rail-surface profiling of the jointed rails are therefore essential parameters for the durability of the welded joints. Rail-straightness and even rail-surfaces of welded joints are decisive factors for the durability of welds. A passenger travelling in a coach on Indian Railway`s tracks can detect nearly each and every rail-weld by the “tack-tack ” sound, caused by the response of the wheels, when running over un-straight and/or uneven railwelds. In countries of advanced railways with perfected welded rail-joints, such sound is not audible.
corresponding vehicle dynamics, which can be monitored by IRV.
In-service rail- and weld failures are in India frequent and have caused many derailment-disasters with high mortality rates:
Wheel-on-Rail Contact Area of new Wheel-Treat and RailHead Profile on straight Run When running on a straight rail-track, on a perfect aligned and smooth rail-table without any roughness and with only little raildeflection under the wheel load (optimum in the range of 1.5 mm), there are only little additional vertical and lateral inter-acting forces causing acceleration, deceleration and rotation on the railvehicle with equal corresponding forces acting on the rails. That is, why a high quality rail-track experience only little additional corresponding forces of the running railvehicles acting on the rails. Therefore, a high quality rail-track keeps its properties under given traffic load, volume and velocity over a longer period and loses its properties over the time with a slower deterioration rate. The deterioration rate under given traffic load and train speed is an index fortrack quality.
On poor quality rail-tracks of bad alignment and poor bearing high raildeflections under wheel load (related to deteriorated There is a clear correlation between weld-shape and the
roughness (corrugation, rail-headburns, RCF), running vehicles experience high additional vertical, lateral and rotation forces exerting equal opposite forces on the rail-track damaging the track components. With increased speed and accumulation of traffic, through this mutual “ SELF-DESTROYING SYSTEM” the situation can deteriorate rapidly. In-Service Rail- and Weld Failure; Central Railway, near Kalyan (left), near Badlapur (right)
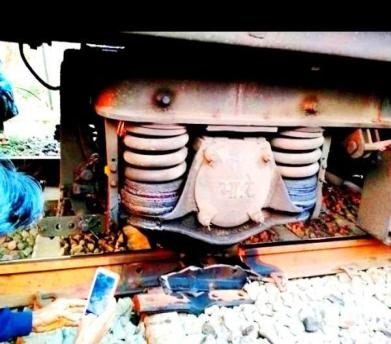

Rail-Weld and Rail-Head Defects leading to fatal and nasty Derailment Disasters on IR

Fatal Kalinka-Utkal Express Derailment near Khatauli on 19th August 2017

Poor qualitytracks deteriorate faster, the service life is shorter, and more frequent monitoring and maintenance is needed, and in consequence the expenditures or overall life-cycle costs keeping a train service on a poor quality track can be 8-fold higher than on a high qualitytrack.
The Picture Gallery of typical Weld- and Rail-Defects with the Figures 31 – 56 on page 112 – 125 of the RDSO MANUAL: ULTRASONIC TESTING OF RAILS AND WELDS, revised 2012, gives in a terrifying way evidence on what has ailed INR in the past decades causing so many nasty and fatal RAILWAYACCIDENTS.
LONG ROLLED RAILS, LRR, “MAKE IN INDIA” – A MILESTONE FOR TRACKIMPROVEMENTS; MANUFACTURE OFLRR
At present there are two Rail Rolling Mills in India.They are:
Bhilai Rail Rolling Mill, SAIL is a public sector plant, which has been producing rails for the last six decades, located at Bhilai, in the Indian State of Chhattisgarh. Originally set up with USSR assistance, it has recently been upgraded to roll long rails up to 130 m each. It has further facilities for welding rolled rails into longer panels in an integrated stationary Flash-Butt Welding Plant

Rail Production at Bhilai Steel Plant, SAIL; India Bhilai SAIL`s Success Story with Long Rolled R-260 Grade Prime Quality Rails for INR, that found Approval by RDSO

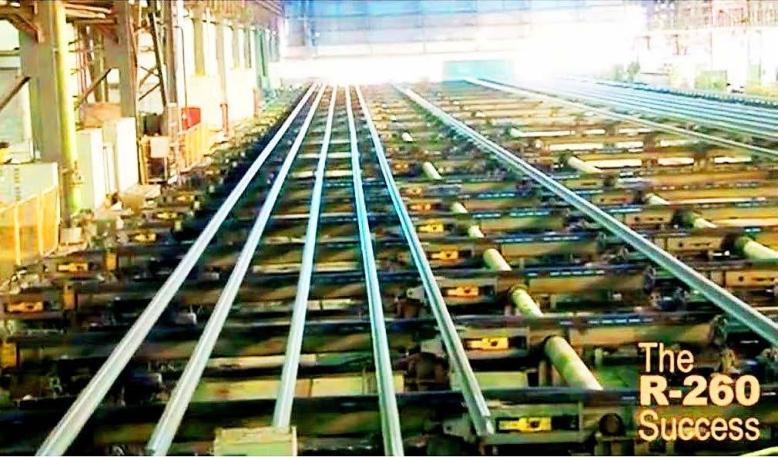
Schlatter stationary Flash-Butt Welding Plant GHA S 80
The other Rail Rolling Mill has been put up byJindal Steel & Power Limited (JSPL) at Raigarh. This Mill, a relatively new one, was setup in the years 2003-5 and can produce long rails of about 121 m length with the facility to make longer panels up to 480 m long in an integrated Flash-Butt Welding Plant. Jindal Steel & Power Limited (JSPL) has become India’s first private company to get “Regular Supplier” status from Indian Railways to supply 60 kg 880 grade (90 UTS) Rails.
JSPL produced 1080 HH rails and 880 Grade rails has already been approved by RDSO for use into Indian Railways on regular basis. JSPL’s 1080 Head Hardened Rails are already being supplied to the Metro Rail Corporations and High-Speed Corridors byJSPL.
JSPL is the first and only Indian manufacturer to successfully develop 60E1 1175 Heat Treated (HT) Rails suitable for High-Speed and High Axle-Load applications. Indian Railways have projected a requirement of 1.8 Lac t per annum of this high-grade 60E1 1175 Heat Treated (HT) Rails.
JSPL produced 1080 HH rails & 880 Grade rails has already been approved by RDSO for use into Indian Railways on regular basis. JSPL’s 1080 Head Hardened Rails are already being supplied to the Metro Rail Corporations and High-Speed Corridors byJSPL.
Indian Railways has embarked upon upgrading the Indian Railway Track system to carry 25 t axle-load and up to 200 kmph. Research Designs & Standards Organisation (RDSO) has approved the newly developed 60E1 1175 Heat Treated (HT) Rails of Jindal Steel and Power Limited. 60E1 1175 Heat Treated (HT) Rails is a superior grade to 1080 HH and will be used by Indian Railways for heavier loads and high-speed application; by M. K. Rai; 20/10/2020; Metro Rail News.

Long Rolled Rails made in India by Jindal Steel
Jindal Steel Rail Rolling Plant

Both the plants are located in the rich iron ore/coal mining belts of the State of Chhattisgarh, and they are well connected with the rail and road network.
Metro Rail Projects are predominantly designed on Head Hardened Rails. Under the Government of India ambitious “Make in India” scheme, the two large steel manufacturers took up the initiative to develop “Head Hardened Rails” to meet the growing demand of Metro Rail Corporations and High-Speed corridor projects in India.
J.S. Mundrey reports in his article “India becomes Atmnirbhar* in Head Hardened Rail Production” , 06/01/2021; Metro Rail News - Daily Round Up from Metro & Rail Industry (*:'self-reliant India'): Rail making technology in India has undergone a great change. Rails steel is coming now through Concast Route with RH Degassing, completely eliminating the piping in the rails, before a major cause of rail fractures.
The rail chemistry is nowadays well controlled. The Hydrogen Content in the rails produced by Indian Rail Mill is now less than 1.6 ppm, much belowthe international standards.
Modern cooling methods and the sophisticated rail straightening machines bring down theResidual Stresses to the bare minimum. Ultrasonic Testing of full rails and Eddy Current Testing do not allow any defective rails to pass undetected.
CAREFULHANDLING AND TRANSPORTOFLRR
For the careful handling of long rail panels, special rail transport trains and unloading shutes are deployed. These trains will transport long rolled rail panels to the rail laying sites at a speed of over 80 kmph cutting out zonal flash-butt welding plants from the transport circuit. This will not only save considerable cost but will also reduce damage, presently occurring in handling and transport of rails:

Rail Trailer with long rolled stationary Flash-Butt welded Bhilai, SAIL, Rail Panels (Londa, India); pict. by F. Wingler
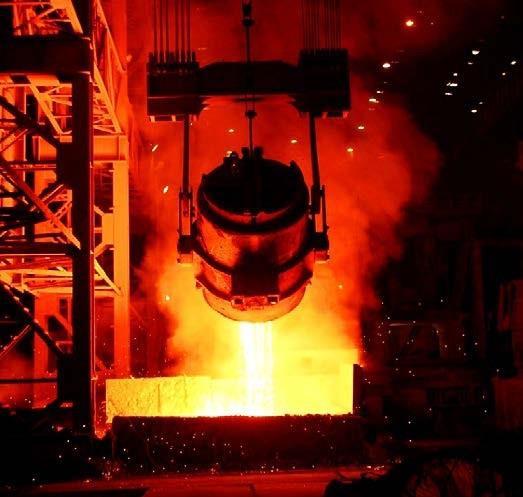
JSPL Steel Manufacture at Raigarh
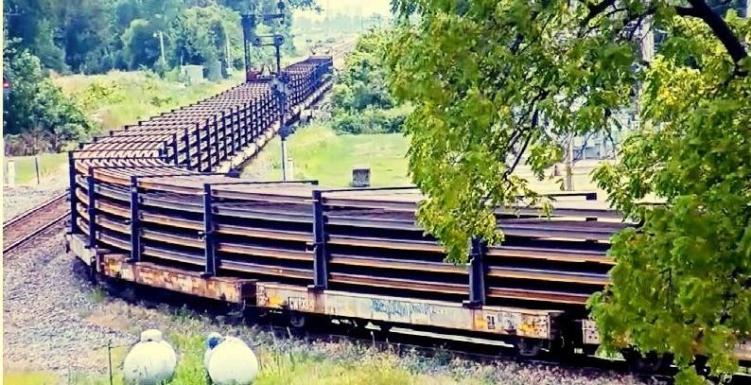
Robel Long Rail Transport Trailer, up to 500 m long RAUN Rail Unloading Train with Rail Shute; USA


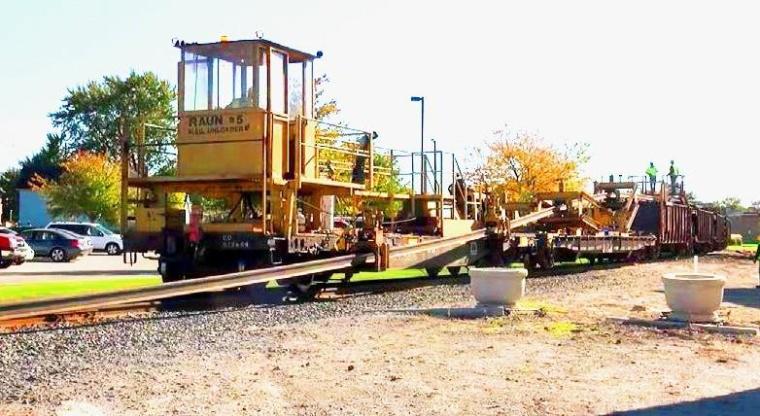

Robel “Spaghetti” Trailer for Long Rails

Picking-up of Long Rolled 60 kg Rails, LRR, for Dedicated Freight Corridor, DFC, with synchronised Cranes; India
LRR ON DEDICATED FREIGHT CORRIDOR, DFC, AND ON SEMIHIGH SPEED LINES
For the new Indian Heavy Haul DFC lines, designed for 32.5 t axleload, Long Rolled UIC 60 and 90 kg UTS rails, and 60 kg/m HH (Head Hardened) rails on curves of less than 2 degrees (875 m radius) have been introduced for the Continuous Welded Rail Tracks (CWR).
Unloading with Robel 40.30 Rail Putler Shute; pict. by DVV Media Group
Ongoing Construction Works on India's Eastern Dedicated Freight Corridor with LRR-CWR Track; photo: Joe Qian/World Bank


Mobile Flash-Butt Welding on Dedicated Freight Corridor with Holland RRV Mobile Flash Butt Welding Machine; Image: DFCCIL

Mobile Flash-Butt Rail Weld after Stripping and before Finishing Grinding; source: Plasser & Theurer
Mobile Flash-Butt Welding on Kashmir Valley Railway Line with Holland, USA, Flash-Butt Welding Unit; source: Northern Railway; India

Long rolled and flash-butt welded rails are a prerequisite for 160 kmph Semi-High Speed Lines in India; see F.A. Wingler SEMIHIGH SPEED (SHS) ON CURRENT INDIAN RAIL-TRACKS WITH CURRENT INFRASTRUCTURE – WILL IT BE SAFE? Published on February 24, 2019 on http://www.drwingler.com .
CHALLENGE TO IMPROVE EXISTING RAIL TRACKS CONSISTING OF SHORT 13 m AT WELDED WITH LRR RAILS OF PRIME STEEL QUALITY The challenge is to replace on old lines all rails consisting of short 13 m rails of insufficient rail steel quality and poor quality AT welds, which are in need of joggle fish-plates, by Flash-Butt welded long rolled rail panels of prime steel quality. Another challenge is the proactive and corrective Rail Management Strategy under a comprehensive Friction Management by ultra sound testing and by frequent rail grinding and milling, to prevent surface cracks to penetrate into the rail head leading to rail fractures.
Long Rolled Rails, LRR, of prime steel quality, already tested in the manufacturing plant, and with Flash-Butt Welds of higher strength than that of AT welds, provide far better alignment and continuity parameters for far smoother train runs, that lower the risk of in-service rail failures, which had led in past decades to nasty, unwanted and fatal train derailment accidents. The mutual impacts of rail and running wheel governed by Newton`s Laws of Motion are on tracks consisting of flash-butt welded long rolled rail panels far lower than on tracks consisting of AT welded short 13 m rails. Long rolled and flash-butt welded rails are a prerequisite for 160 kmph SemiHigh Speed Lines in India.
Better knowledge about rails in INR will help for better information based planning, actions and decisions at the right place and at the right time in order to bring down the frequency and prevalence of in-service Failures of Rails and Rail Welds, one of the root courses of so many unwanted, nasty and fatal train accidents in India. Authored By F. A. Wingler