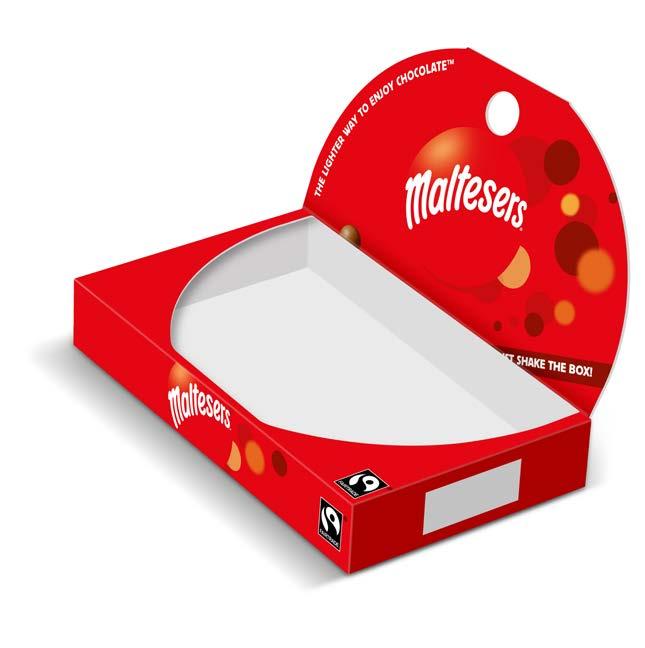
3 minute read
Product and service development
Our R&D work considers the entire life cycle of a package
As the amount of packaging grows, we need resource-efficient and easily recyclable solutions. It is the common goal of customers and Metsä Board to make packaging lighter and to reduce plastic with renewable raw materials and reduce emissions.
Thanks to long-term focused development work, Metsä Board has a leading position in the quality and performance of paperboard materials. Both our folding boxboards and white kraftliners receive the highest quality assessments. In cooperation with our customers and partners, we invest strongly in innovative solutions to optimise performance throughout the life cycle of packages.
The development work centres on the paperboard’s good printing and conversion properties as well as on reducing its weight, without compromising its strength. Lightweight paperboards are resource-efficient and help to reduce the carbon footprint of packaging throughout the chain.
The market has a strong need for recyclable solutions that can replace plastic
The dispersion-coated barrier paperboard we launched two years ago helps brand owners to reduce the use of plastic and make their packaging recyclable. The growth in the sales of this product was strong in 2021 in food industry end uses, including the packaging of confectionary, pastries and takeaway foods. The growth is also expected to continue.
Metsä Board has launched a biobarrier programme. The starting point for the solutions and polymers to be developed is that they will be based on fossil free raw materials, according to our 2030 sustainability targets. Development work is done in collaboration with partners.
Deeper customer cooperation
We invest in service development which helps our customers to make the most of our paperboard and optimise the performance of packaging throughout its life cycle. Our new 360 Services cover five areas: Sustainability Service, Packaging Design Service, Technical Service, R&D Service as well as the Supply Chain and Digital Service.
Mars Wrigley UK’s Maltesers boxes now fully recyclable
Mars Wrigley UK has replaced the old multi-layer box design, where the PE plastic liner covered the box, with a dispersion coated barrier paperboard. The company says the new design will reduce its annual plastic usage by 82 tonnes. The new Maltesers box uses Metsä Board’s dispersion coated barrier board, which is fully recyclable, biodegradable and compostable.
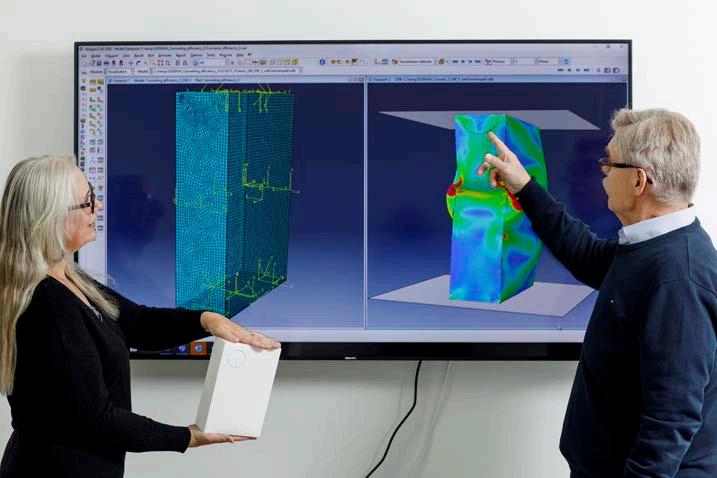
We minimise the environmental impact of packaging with Dassault’s simulation platform
The state-of-the-art 3D technology enables the simulation of the performance of materials and packaging under different conditions. Optimum material selections and packaging designs help to reduce carbon footprints. Compared to a physical prototype, 3D simulation allows us to come up with material and packaging design recommendations for customers 85% faster.
Examples of the above-mentioned services include carbon footprint calculations for packaging materials and computer-based packaging simulation, which enables the digital modelling of prototype packages as well as the optimisation of material and structural choices.
For over a year now, we have held development workshops at Metsä Board’s Excellence Centre in Äänekoski, in which our teams of experts have developed new packaging solutions in cooperation with customers. The virtual workshops have brought together both Metsä Board’s and customers’ multi-skilled specialists on product development, sustainability and packaging design, for example. In 2021, we held 25 of these workshops.
ExpandFibre is progressing
Metsä Group and Fortum’s ExpandFibre programme, which promotes the circular bioeconomy, moved forward in the form of concrete projects. The construction work of the 3D demo plant of Metsä Group’s innovation company Metsä Spring and Valmet has progressed, and production is expected to start up during the first half of 2022. Metsä Board was actively involved in new research consortiums and projects focused on innovative packaging solutions. Three projects were kicked off in 2021, with topics ranging from the reuse of packaging to fossil free polymers for coating and a new paperboard folding technique intended for the implementation of novel applications. These projects involve a total of 44 partners – business enterprises, research institutions and public sector organisations.
AI facilitating improvements in production efficiency and process control
We employ artificial intelligence in production at our Kemi, Kyro and Simpele mills, and its use is also being tested at our other mills. AI allows us to anticipate process deviations, which improves a mill’s efficiency and reduces quality deviations and idle time. It also allows operators to develop their own competence at the same time. At the Tako mill, we have tested the integration of our paperboard machine into our customer’s production line. When the production lines interact with each other, the parameters can be optimised at both ends.