
34 minute read
Cherished News
by MG Car Club
Pete Barrett MG Car Club Insurance Manager Cherished.vehicle@aplan.co.uk
Welcome to my first Safety Fast! column. Firstly, let me introduce myself… My name is Peter Barrett and I manage Cherished Vehicle Insurance Services.
Advertisement
Both the Team and I are extremely proud and very excited that we have been appointed as the recommended insurance scheme for the MG Car Club.
My Team and I are all very passionate about cars and are for the most dedicated “petrol heads”. Between us we have three MGs: my TF160, a ZT190 and a ZR160. I have also got access to an MGC that I use regularly when the weather is fine.
Cherished Vehicle Insurance are one of the Specialist arms of A-Plan insurance brokers and we have set up a scheme to suit the needs of the members along with organising further discount for products like home insurance when organised by ourselves at the Worcester branch.
I am looking forward to writing this section every month to let you know the answer to any questions that may regularly arise when we speak to members and also give you an update on what we have been up to with our cars.
Personally, I got into MGs at a young age (six) when I used to be picked up after school by my friend’s mum who had a chrome bumpered MGB GT – I remember the back-bench seat being very hard – but the smell, noise and feel impassioned me forever and after this experience I was forever hooked on classic cars. Over the years, my family have had a few MGs, including an Abingdon MGF, and a TF cool blue. I then went on to purchase a TF160 which I sold to my uncle shortly after my second daughter was born. In December 2019 I bought “Emma” a 102K mile 2002 TF160 as I missed my previous one. This car, it seemed, was in great condition and I really enjoyed putting another 1,500 miles or so on her. As with most cars, I have had a few problems including the airbag light coming on, an easy fix under the driver’s seat connection, then the alternator packed up which I dutifully changed. When I purchased “Emma” I was under the impression that the cambelt had been changed. This unfortunately turned out to be untrue and it decided to snap on my birthday in September 2020. Hopefully she will be back with me soon, as it’s currently having the head rebuilt after I bent most of the valves, and some remedial rust replaced with metal. I will keep you updated with what we get up to with her.
As part of the launch of the insurance scheme I am currently offering to do Zoom PowerPoint presentations covering the scheme benefits, including a Q&A session. So if any of the regional Centres or Registers would like this please email me at peter.barrett@aplan. co.uk. Also I would like to thank the MGB Register for being my guinea pigs and for listening to what I had to say!
This is administered as part of the A-Plan Holdings who have a whole panel of insurers and can give you independent advice for your Private Car, Buildings and Contents, Commercial, HGV, Life and Travel Insurance. Please note that the MG Insurance scheme powered by Cherished Vehicle Insurance uses one insurance provider only, KGM Underwriting Services whom we have selected due to their experience in the classic car market.
Please note there is a promotion specifically designed to reduce MGCC members’ Home Insurance. This gives a £25 discount off the standard administration charge for new policies if you are an existing MGCC member. Just call 01905 930747 and let the team know you are a MGCC member.
And that is it for this month! If you’d like any more information on any of the above feel free to give any of us a call here at Cherished Vehicle Insurance on 0345 250 8282 – we’d all really love to hear from you.
MG Car Club Limited is an Introducer Appointed Representative of A-Plan Holdings. The MG Classic Car Insurance Scheme is managed and administered by A-Plan Holdings Ltd. Cherished Vehicle Insurance Services is a trading name of A-Plan Holdings who are authorised and regulated by the Financial Conduct Authority.
The Benefits of the policy include:
• Free and simple Agreed Value service - Completed in house
by our specialists
• Member to member cover
• Reinstatement cover available
• Salvage Retention – Subject to qualifying Criteria
• Modification cover
• 90 Days European Cover – included as standard
• Multi-Vehicle Cover – we can look to put all your vehicles,
even non MGs, on the same policy
• Laid Up Cover – if it’s not on the road it can still be insured
• Spare parts cover – up to £1,000 cover for your spares
• Occasional Wedding Hire – can be arranged on application
• Business Use – can be arranged on application
• Limited Mileage discounts
• Young Accompanied Driver cover from age 18
• Track day Cover– can be arranged on application
New event marks historic
collaboration between Triumph clubs, TR Register and TSSC and the MG Car Club to create the Triumph and MG Weekend at the Three Counties Showground, Malvern August 13-15 2021.
It was one of the great rivalries of the British Motor Industry. The automotive equivalent, if you like, of City vs United – it was Triumph vs MG!
But, whilst fans of these historic marques have traditionally existed as friendly acquaintances ever since, the global Coronavirus pandemic has brought all sorts of communities together closer than ever before and the Triumph and MG clubs are no different.
It is with great excitement that the TR Register, Triumph Sports Six Club (TSSC) and MG Car Club announce that they have created an equal partnership to create a memorable, jointly run, inter-club weekend at the Three Counties Showground, Malvern, Worcestershire, over the weekend of August 13-15 2021.
The TR Register and Triumph Sports Six Club (TSSC) had already combined their annual international festivals into an inter-club collaboration with the Triumph Weekend in 2019. But, following the news that MGLive! at Silverstone had been forced to be postponed until 2022, the hand of friendship from Triumph was extended to the “marque of friendship” in MG and the partnership has added the MG Car Club, joining as the event’s third organising partner.
The weekend will feature specialist traders, an extensive Auto-jumble, Autosolo including the MG Car Club’s historic California Cup, technical seminars, plus inter-club challenges, evening entertainment, live music, live action arena show and Concours d’Elegance competition, anniversary displays – plus much more to be confirmed during the coming weeks. The collaboration between clubs isn’t limited to those organising the event either, as all marque car clubs are invited to come and display their vehicles and join in with this historic collaboration.
The three-day event will also celebrate a number of historic milestones and anniversaries for each marque, including 60 years of the MG Midget, 60 years of the Triumph TR4 and Herald 1200, 20 years of the MG Zeds, and 40 years of the Triumph Acclaim and special display areas will be a focal point of what promises to be an event you will not want to miss!
Lauran Gallacher, Assistant General Manager of the MG Car Club says: “Whilst we were sad that MGLive! was not possible this year, we have turned the challenges of COVID around into an opportunity to offer a new, fun and landmark event for members of the MG Car Club. We need to come together more as a classic car community and this collaboration shows just what we can achieve when we do so.”
Allan Westbury, Chairman of the TR Register, says: “It is important for the future of the classic car scene that clubs come together and collaborate and the challenges we all face as a result of COVID have made this even more crucial. Combining our events and resources in this way, means that we can bring Triumph and MG fans together for a really memorable and enjoyable weekend.”
Chris Gunby, Chairman of the TSSC, says: “We are excited by the added interest this will bring to the show. We are all classic car fans at the end of the day and we think this will spark some lifelong collaborations and friendships across fans of these two marques, which have always enjoyed a bit of friendly rivalry. We can’t wait to meet our new friends from the MG Car Club and celebrate our love of classic British cars in the wake of what has been a challenging twelve months for everyone. ”
Weekend entry packages, day tickets and other passes all go on sale from March 1 2021. You can find full details and purchase online via: www. triumphandmgweekend.com
NEW TRIUMPH AND MG WEEKEND IN 2021

MG PRODUCTION IN AUSTRALIA
By Tom Aczel
Tom Aczel from Australia, who is a keen MG enthusiast owning an MGB and MGA, gives a history of the production of MGs in Australia.

BACKGROUND PREAMBLE:
Successive Australian Federal Governments from the early 1900s pursued protectionist tariff policies to encourage the development of local industries and infrastructure. (In fact, favourable rates applied for Commonwealth countries, especially the UK, or at least until Britain “turned its back” on Commonwealth member nations and joined the EEC in 1973.)
Following the Second World War, the then Labor Federal Government’s advice was that a further world war within 20 years was probable, and that, without a substantial increase in the country’s population and its industrial base, Australia was likely to face an Asian invasion from the north. In the jingoism of the late 1940s this was commonly referred to as “The Yellow Peril”.
“Populate or Perish” became the guiding political motto. Consequently a massive immigration policy was instituted, predominantly from the UK, Ireland and Europe.
Simultaneously, major encouragement was given to overseas motor vehicle manufacturers to establish production facilities in Australia.
General Motors and BMC were the earliest to proceed with local manufacturing. General Motors-Holden released their first Holden in 1948.
VICTORIA PARK, WILLIAM MORRIS AND THE NUFFIELD GROUP
The Nuffield facilties (later BMC (Australia), and later still, BLMC and then Leyland Australia) were located at Victoria Park, just 5.8 km from the centre of Sydney. The adjoining suburbs here were Zetland and Waterloo, (and hence the business address changed, depending which frontage the administrative offices occupied!). The area was originally a swamp, and then from 1900 a horse racetrack. A speedway track also occupied the site from 1908 to 1920.
Interestingly, the first powered flight in Australia was made from this site, in 1909.
William Morris had come across the Victoria Park site in 1945 on one of his visits to Australia. (He enjoyed spending the English winters in warmer climes!) As a patriotic British subject, Morris was eager to see the Australian market remain substantially British. He recommended to the Nuffield Group board that they purchase the Victoria Park site for an Australian factory. The board considered and rejected this proposal, whereupon Morris purchased the site himself.
Morris subsequently sold the property to Nuffield a matter of months later, and what’s more, at a considerable profit!
However, Morris only sold about half of the approximately 115-acre site to the Nuffield Group for their Australian factory.
Morris then sold off parts of the rest of the site to support industries and feeder companies, such as to James N Kirby, Joseph Lucas Ltd, Champion Spark Plugs, Olympic tyres, etc.
Clearly William Morris was an extraordinarily astute and successful entrepreneur.
Nuffield Australia commenced operations in 1950. The first factory was completed in 1952. By 1957 BMC in Melbourne had been shut down, and all assembly moved to Sydney.
The factory site was later named BMC (Australia) after the merger in 1952 of Nuffield and Austin. From 1968, it became The British Leyland Motor Corporation of Australia and Leyland Australia in 1971.
MGB Mk I cars on the line at Zetland, circa January-February 1968. The BMC (Australia) factory from the air. The MGB and the MG Midget were assembled in the left side of the building at the top of the photo.

BMC (AUSTRALIA)
Most people overseas were and remain quite unaware of just how large a venture BMC (Australia) was. The factory employed about 5,000 people, and by the late 1950s was producing a car every four minutes.
Apart from extensive and progressively expanded factory floor area for assembly, the factory, on its 57-acre site, was equipped with its own panel pressing facilities, (the largest presses in the Southern Hemisphere).
Engines, transmissions, axles and bodies were all cast, assembled and/ or pressed locally. (Major castings were supplied by “Australian Forge and Engineering” and others in NSW, Victoria and South Australia).
Heat treating of components for hardening, and metallurgical control was in-house. (*)
The “Unit Plant” was where engine, transmission, axle and suspension components were manufactured, ready for vehicle installation. The transfer machines in the unit plant machined cylinder heads, engine blocks and gearbox casings. These transfer machines could index the part automatically from station to station, allowing 30 sets of operations to be performed on three faces without any human intervention. (*)
The Paint Shop included a “Rotodip” where all assembled vehicle bodies were located onto a frame and rotated through a series of baths and ovens.
All trim was locally sourced and fabricated on site.
There were production engineering offices, drawing and design facilities, a service department and research laboratories, and a department termed “Experimental”.
There was an active apprentice training programme with related facilities.
As a result of the highly developed engineering facilities and capabilities available, in addition to the various mainstream vehicles produced by the parent company in the UK, suitably modified for Australian conditions, a number of vehicles unique to the Australian market were constructed here.
The original prototype MGC, incidentally, as conceived by Sydney Enever, employed an Australian-produced 2.4 litre 6-cylinder engine based on “one and a half” 1622cc ‘B’ series engines, named the “Blue Streak 6”. This was a much lighter and much more compact engine than the Morris C-series engine ultimately used. This engine could potentially have been manufactured as a relatively small lightweight 2.7 litre 6-cylinder engine.
Even the 1622cc version of the B-series engine for that matter was conceived and produced in Australia, long before its UK counterpart; the parent company engineers initially claimed that 1500cc was the practical limit of the B-series engine.

The production lines at the Pressed Metal Corporation factory in Enfield Sydney. The middle line carries MGAs being assembled.
MG ASSEMBLY IN AUSTRALIA
Despite the highly developed significant local manufacturing facilities available to Nuffield-BMC, because of the smaller production volumes of MG models, prior to 1957, MG cars were shipped to Australia completely built up, (CBU) but partly disassembled. Wheels/tyres and bumpers, for example, were removed and stowed in or under the cars.


MGB body in finishing, BMC (Australia). Unlike at Abingdon, where the bodies were received assembled and painted, the MGB body was assembled from the very smallest of panel sections

THE MGA IN AUSTRALIA
As the MGA, which had been introduced in 1955 was proving to be in significant demand, and there remained encouragement through tariffs to assemble motor vehicles in Australia, a decision was made to commence local assembly in Australia of the MGA.
Due at this stage to having insufficient spare capacity at the Zetland facility, this task was subcontracted by BMC (Australia) to Pressed Metal Corporation, which like BMC was based in Sydney, in the suburb of Enfield.
Consequently shipments of batches of Completely Knocked Down (CKD) MGA cars commenced to Australia in 1957. Until the later part of 1962 these were assembled at Pressed Metal, with ever greater local content.
Indeed, the degree of assembly of these cars here in Australia was very much greater than at the MG factory in the UK, where in contrast to Australia, MGA bodies were received at Abingdon already fully built up and already painted.
Ultimately 2,040 MGA roadsters were built in Australia. (The Coupes and the Twin Cam models remained fully imported due to their lower numbers.) Again because of the production volumes, major mechanical components such as engines, transmissions and chassis were imported (though in the case of the MGA 1500, the engines were built here, from imported components).
PRESSED METAL CORPORATION
Pressed Metal Corporation was a joint venture established in1930 between the Larke Hoskins group, the Austin agents for NSW and Larke, Neave and Carter, the Chrysler distributor. The PMC factory after WW II occupied a 22-acre site, and had extensive capability for the complete assembly of motor vehicles. A number of the factory buildings were redundant aircraft construction hangars, imported into Australia from the UK after WW II.
Apart from assembling a range of sedans, light commercial vehicles (“utes” and panel vans), trucks and buses, Pressed Metal Corporation also assembled a very significant number of sports cars on behalf of BMC.
Between the years of 1957 and 1967, inclusive Pressed Metal Corporation assembled: MGA roadster (1500, 1600, 1600 MkII): 2040 vehicles. Austin Healey Sprite: MkI (Bugeye) through to the Austin Healey Mk 3A: (approx) 3,600 vehicles. MGB roadster: MkI (approx) 4,625 vehicles. (Based on VIN plate images, somewhere between 4,600 and 4,650) TOTAL: Around 10,265 sports cars, in a little over 10 years.

THE MG MIDGET IN AUSTRALIA
In the latter part of 1967 Austin Healey Sprite production ceased at Pressed Metal Corporation. The model was replaced by the MG Midget. Unlike the UK and world markets, the Australian market was not deemed large enough to run the two similar models in parallel.
The MG Midgets were assembled at the BMC (Australia) plant, again from CKD packs.
Building the MG Midget commenced at Zetland in November 1967, with the vehicles offered for sale from early in 1968. Features and changes in the series generally reflected those in their UKassembled brethren, but again with a significant inclusion of locally produced components, including electrics, paint and of course local labour, which constituted a significant proportion of the overall vehicle production costs.
Approximately 788 MG Midgets of the series YGGN4 and YGN4 were assembled in Australia. (As with all Australian BMC vehicles, “Y” indicated Australian assembly. It has been said that the “Y” was meant to represent an upside down “A”, A for Australia. Some with factory first hand knowledge dispute this as the

MGB bodyline production.
reason for the choice of Y in the series nomenclatures).
October 1969 saw the introduction of the (ahem) “Facelift” model; GAN5 for the Abingdon assembled MG Midgets, and typed YGN5 for the Australian cars. These cars reached the market about 6 months earlier than the similarly revised black recessed grille MGB models.
A total of 788 MG Midgets were assembled prior to the final Facelift model, of which 396 were built; 1,184 Australianbuilt MG Midgets in total, until production was wound up in December 1971.
THE MGB IN AUSTRALIA
The MGB was assembled in Australia from 1963 to 1972. A total of something in excess of 9,000 examples were built over this period. The Australian content was ultimately 45% of the car’s value.
As with the MGA, the Mk1 MGBs were constructed at “Pressed Metal Corporation” in Enfield, commencing in April 1963. At the time, the BMC plant at Zetland was fully occupied with the production of the Mini and preparations were under way for the upcoming introduction of the other FWD models, the Morris 1100 and later the Austin 1800.
The MGB engines and gearboxes were received already mated at the BMC Zetland works. They were hot run tested, and then transported to Pressed Metal. Suspensions were assembled and painted at Zetland, and similarly transported to Pressed Metal.
Springs, electrics, paint and a rapidly larger proportion of the trim were locally sourced. As a result, and as had occurred with the MGA, local body colours, though similar to their UK counterparts, were unique to Australia. Early colours included colours such as ‘Sky Blue”, ‘Monza Red’, ‘Nurburg White’, Katoomba Grey, and of course, British Racing Green. (The last had been also available on locally assembled MGAs, unlike their UK counterparts.)
Because of the relatively small production numbers compared to more mainstream BMC models, all Australian MGBs were similarly specified. Only roadsters were ever built locally. All cars had wire wheels and (until 1970) packaway style tops only. Oil coolers, front sway bars, front overriders and ash trays were standard fittings. Like the preceding MGA, the interior trim was, for both cost reasons and because of the harsh local climate, always in vinyl. Contrasting piping disappeared after 1964, and progressively thereafter ever more of the interior trim became black only. The only options were (an initially rarely fitted) heater, and the dealer-fitted radio. Overdrive was not available in Australia, even as an option, until the last of the MGB Mk1 vehicles were assembled, between late 1967 and August 1968.
As with the MGA, and in contrast to the MG cars emerging from the MG factory in Abingdon, the Australian-built MGB bodies were locally built up from their most basic pressed components on locally created jigs, whereas the Abingdon factory received the MGB bodies completely painted and assembled.
Rust proofing on these earlier Enfieldassembled cars was unfortunately rudimentary at best, with the bodies just “slipper dipped” in primer. (The author’s own Mk1 MGB was already visibly rusting by the time it was five years old!)

MG ASSEMBLY AT BMC ZETLAND
BMC ultimately purchased Pressed Metal Corporation, and, as with the MG Midget, production of the MGB was transferred from the PMC factory to a dedicated production facility in the CAB 3 building (Car Assembly Building 3) at the Zetland facility.
New jigs were commissioned from Dorman’s in Victoria.
Bodies were here far more elaborately rust proofed, going through the “RotoDip” process, as described earlier.
Even though the MGB MkII had been introduced in the UK from November 1967, between January and August 1968 it was still the MGB MkI being assembled at Zetland. The MGB MkII was finally built and introduced in Australia 9 months after its UK debut.
It is difficult not to draw the conclusion that left over redundant superseded

Mock furneral being performed on the last MGB built in Australia Mock funeral procession

stock of MGB MkI car components was offloaded by the British parent company for sale to their less important colonial Australian customers to make way for the MGB MkII in the UK for the home and other export markets.
A very similar situation had occurred in 1961, immediately prior to the introduction of the MGA MkII in the UK, when suddenly a large volume of MGA 1600 cars for assembly arrived on these shores, far in excess of the volume needed to fulfill immediate Australian market demand. As a result, the MGA MkII was first assembled in Australia from February 1962, nearly a year after its arrival in the UK. The intervening period was required to build and sell the excess volume of already shipped MGA 1600 cars. The MGA MkII consequently had a short run in Australia of just a few months prior to the arrival of the MGB, with a mere 148 MGA MkII roadsters assembled in Australia.
From August 1968 onwards, the models and changes were again more in line with their UK counterparts, although these running changes always generally arrived three to four months later than in the Abingdon cars because of the time needed for shipping and the sourcing of components.
The “automatic” option was also offered in Australia, from 1969, and though well received by the press, it was, as in other countries, not especially popular, though sales continued right through to 1972.
Unlike their British counterparts, the Australian-assembled MGB vehicles carried ‘MkII’, ‘Overdrive’ and ‘Automatic’ badges whenever applicable.
The Australian version of the (debatably termed) “Facelift” model was assembled from April 1970, and reaching the dealer showrooms from about June 1970.
Unique to Australia, this series of the MGB was ascribed the model description of MGB BL (for British Leyland). Unlike the Abingdon MGB, these black recessed grille models in Australia also had the area forward of the radiator diaphragm painted black to hide this area as seen through the grille in the lighter coloured cars.
Australian assembly of the MGB ceased late in 1972. The Federal Government had announced a restructuring of the tariff arrangements, whereby an 85% local content was to be required for a favourable import duty. In any case, by this time sales of the MGB had dropped to a trickle. The buying public’s interest in small, responsive but relatively low-powered sports cars was waning, with a growing interest in high-powered sedan derivatives (the local equivalent of the American ‘Muscle cars’). Cars such as the Holden Monaro and Torana XU1, the Ford Falcon GT/HO and Chrysler Valiant Charger were extremely fast cars. (The Ford Falcon GT HO was, in its time, the fastest four-door sedan produced anywhere in the world.) These locally built power-houses could be seen competing most weekends on the various circuits around the country (most famously at Bathurst) and it was these cars that now fired the imagination of the young (and young-at-heart). These two factors, along with the impending P76 large sedan’s introduction requiring freeing up of production space, led Leyland Australia to take the decision to wind up local assembly of the MGB.
* “Building Cars in Australia” BMC-Leyland Australia Heritage Group Published 2007 The author would like to acknowledge input from John Lindsay, Garry Kemm, John Clarke and Roger Sharpe

THINGS THAT GO BUMP IN THE NIGHT

By Ian Pogson
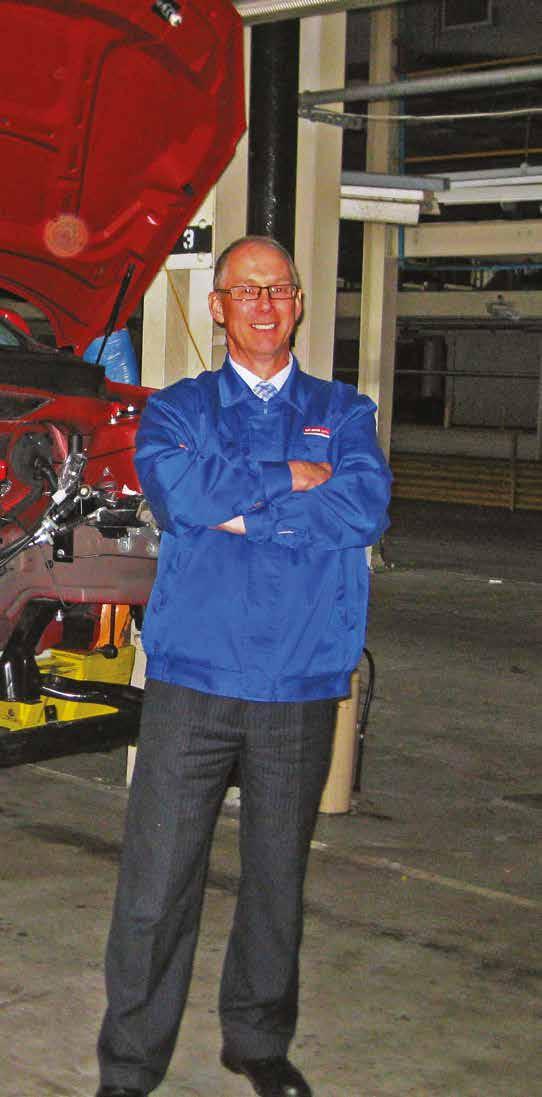
As a seasoned veteran of corporate wrangles, take-overs, give-aways and site closures, I and others were expecting MG Rover to run out of money as we beavered away in Shanghai trying to teach young Chinese engineers fresh out of University. This was January 2005 to the end in April. When a typically sensitive Patricia Hewitt announced (before the Company seniors were briefed) that MG Rover was going into Administration, I was asleep. My wife called me with the news, understandably frightened and concerned. A stop-gap loan gave us another week’s work, which saw me and others removing confidential information and data sources from the SAIC offices where we were based in Pudong. During that last week, Gan Pin, one of the senior Chinese directors, had asked me if I would consider staying on and carrying on with the work to localise K-Series parts manufacture in China. I said I would love to but could not work directly for a Chinese company. He asked if I would were something “joint” set up.
Colleagues and I lounged around the pool at our apartment block until everyone’s tickets home became valid, as any chance of swapping them for earlier ones was expensive or just not possible. The BBC, looking for the usual media angle, tried to infiltrate our ranks and bought drinks at the local bar “The Maudesley” to try and loosen tongues, but soon got as bored as we did. The flight home was a blessed relief and I arrived to an emotional welcome.
The weeks passed and with 6,000 people fresh on the dole, local jobs were hard to secure back home. Then the call came from an ex-colleague asking if I would like to join a new company, Ricardo 2010, who were 50/50 SAIC and Ricardo owned in the latter’s offices at Radford Semele. It was August before I was sent back out again to Shanghai, to restart our original work.
In the interim, NAC (Nanjing Automotive Corp.), which had been successfully working with Fiat-Iveco building Daily vans, had bought the equipment and (they thought) the IPR for the MG vehicles. SAIC had stolen a
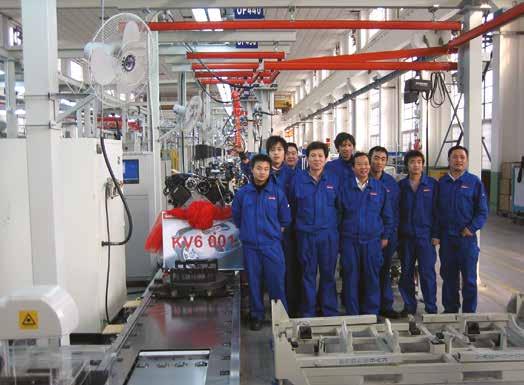
The local Shanghai team in the new KV6 assembly facility. Photo: Eddie Harris
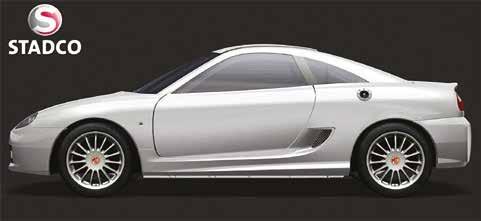
The MGTF Coupe. Photo: Stadco
march on NAC as they had been evident in the offices at Longbridge for some time from at least mid- to late-2004 and consequently thought that they knew more about the products. Incidentally, SAIC had been preceded by China Brilliance (who were allied to BMW), who had tried and failed to negotiate a JV (Joint Venture) with MGR. I had been tasked in 2003 to pick, pack and despatch 75 engines-worth of parts, so they could assemble K4s and KV6s in their facility. The idea died on the vine, after I had sent the parts, which were beautifully packed. I have no idea if they were ever built up.
NAC had drafted in a complete workforce to clear the CABs, East, North, South and West Works as well as the LPS (Low Pressure Sand) foundry that made K4 heads and blocks. They slept on Z-beds in the old Purchasing Block and elsewhere around the site, supported by ex-Rover employees advising upon facility removal and later re-installation in China. It was a masterful piece of lift and shift, similar to that conducted in record time by the Cowley and Longbridge teams when MINI went south and Rover 75 ventured north, except this time there were several thousand miles and the odd ocean to cross.
SAIC’s plan had been to create their “own” first car – a Rover 75 update, for which they had the BoM (Bill of Material) and in parallel, NAC were to create a ZT variant, the MG7. SAIC had finally been enlightened over the use of the Rover name at the 59th minute of the 11th hour by Ford ‘suits’ from Detroit HQ, then owners of Land Rover. The badge tooling had already been made and so a hastily rehashed Roewe badge in the familiar shape was to adorn the front and rear.
As this was going on, a number of us were tasked with sifting through the hard copy drawings and database to decide which documents were Rover and which MG, to suit the plans already outlined. The job was to be conducted in the offices of a Birmingham solicitor, who were later to be our poorly prepared adversaries in an Employment Tribunal. (Warning: do not take on a bunch of disillusioned Engineers who are up for a fight – we are very skilled at assembling data and drawing conclusions!) Of course as we all know, this was a nonsense job, as so much was shared, e.g. core engine as well as base body and suspension components. SAIC and NAC slugged it out for some time via UK-based legal firms, paying UK rates (ouch!) until the Central Government said “Stop!” SAIC then absorbed/ assimilated NAC.
In what was later to appear a little silly, SAIC (my team) set about creating a new line to machine the KV6 and K4 engines whilst NAC re-installed the exLongbridge facilities in Nanjing. It was strange to me to be able to walk around the old familiar line 6,000 miles away from its original location. To their very great credit, the good ole’ boys in the ancient capital (Nanking) were hard-bitten, proper grey-haired manufacturing types who recreated a first-class facility which in many ways was superior to that which had been in East Works, especially in the late and post-BMW days. Both companies are to be commended, as they implemented all the design and process improvements that we had been asking for but had been denied by parsimonious and short-sighted top management (MLS gasket, PRT, etc. – although in place on Freelander engines – and a much cleaner assembly track).
Attempts were made to manufacture the PG1 gearbox, but the difficulties of annotated ex-Honda drawings and a lack of the right UK personnel hampered

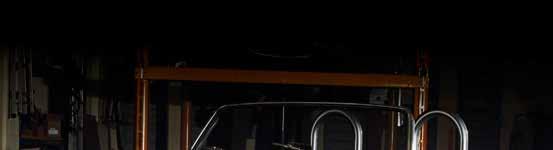








West works body repair Photo: MG Rover The first KV6 engine off SAIC line. Photo: Eddie Harris

production and it was this and (some would say) lacklustre Sales and Marketing that caused the cessation of TF production.
What amused me greatly when I visited the Pukou plant in Nanjing, was the product line-up display area, which plainly and without embarrassment showed the 1.8L ‘N’ series engine (check!), a PG1 box (hmmmm?), an L series diesel (what? In China?) and a lovely, but very Ford-looking V8 (Ha!) Dreams of mice and (Chinese) men.
When the Central Government finally caused SAIC to absorb NAC, as their UK legal battle was perhaps embarrassing, it was not long before I was sent from Radford back to Longbridge to seek out the MGTF Engineering team and see what they had been up to. While we had been supporting SAIC to build up their own production facilities for the Roewe 750, the NAC team had been building TF test cars and proving out the parts supply chain from China. Also, the bodies for the MG Rover TFs were latterly built by Coventry-
The NAC factory at Pukou, Nanjing. Photo: NAC



K4 engines on a very clean assembly track at Pukou. Photo: Author’s Collection SMTCUK team build first RHD car at Lingang. Photo: Author’s Collection
based Mayflower, now known as Stadco. The latter had a facility on site in CAB2 to make bodies, but disagreements with NAC caused manufacture to be taken to China as well. All in all, it had been a busy time for the small NAC team, who were not only proving out massive changes to the engine (now N-Series) manufacturing process (such as removing the electromagnetic pump in the LPS), but were also using parts from suppliers with no previous TF or often any car-component experience.
I set about reporting to Ricardo 2010 seniors what I had seen at Longbridge, having audited the Paint Shop and GA (General Assembly) processes. I was keen to have these gents view the impressive progress themselves and become involved. There were issues that I had uncovered for sure, but the small team had worked hard and diligently. As is often the case, an adversarial air existed between both companies, with the SAIC team wanting to concentrate on their trips to Shanghai for Roewe products and the NAC team desperate to show they were capable of resurrecting the TF. It has to be said that plenty of advice was given by the UK team not to restart TF manufacture, as the weakest car in the MG line-up, and to bring the evergreen ZR back, but for good reason, the Chinese have become wary of Western advice!
And so, as TF production ended (see my previous article in the December magazine), the first Roewe 550 body arrived at the plant, part-built, trimmed but without running gear or powertrain. It was packed in a sea container and six weeks later dragged out, loaded on to the System and began its lonely, slow journey down the back line of the old Rover 75 line and around the bend towards the ‘stuff-up’ area. This is nothing to do with poultry preparation, but manufacturing speak for the way the powertrain subassembly is ‘stuffed up’ into the engine bay, as the body makes its way along the line, barely stopping in its progress. And so began a new chapter for Lord Austin’s old factory complex. No BIW in West Works, indeed, no West Works at all, as in the usual premature haste the landscape was cleared of anything to remind genteel
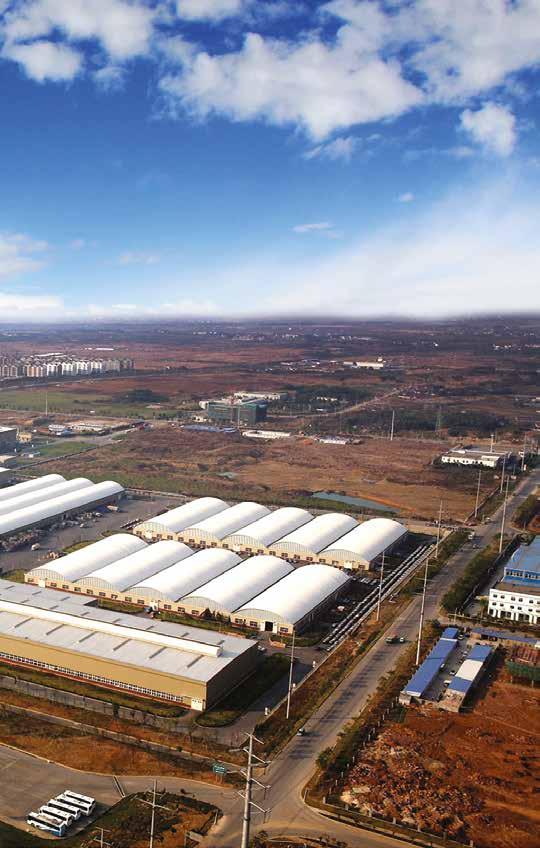
Trial Roewe 550 body on Longbridge System Photo: Author’s Collection

Conservative voters that such dirty things ever went on in England’s green and pleasant land. How is it that old office blocks can be left intact, or even new ones erected, when there is no call for such space? How does that work economically?
Sorry about that; the ruminations of a Manufacturing Man. No East Works either, that’s houses now, no Trentham or Trim Shop with its hoard of somewhat dangerous women, no suspension manufacture in Dalmuir, no block line in North Works, no Toolroom over the railway tracks; all gone. The powertrain arrived with the body, the steering, cooling and associated ancillaries were in the container with wheels, exhaust and all the other bits. This was a new dawn for Longbridge: a screwdriver operation.
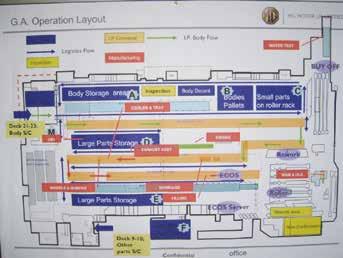
MAGNETTE

SUMMIT MEETING
In the adversity of the pandemic in 2020, we were still fortunate enough to hold a Magnette Gathering. The meeting point was the area around Salzburg in Austria. Fortunately the local authorities saw no problems and the first official meeting of the MG Car Club Germany in 2020 could be held, albeit not in Germany but perfectly organised by our Austrian friends Vroni and Jörg Wiefler and Christina and Thomas Nebauer, who even ordered beautiful weather for the weekend, Thank you so much!
The basis of the weekend was the rebuilt and just opened Erentrudisalm,
By Dietrich Krahn
1,000m above sea level with magnificent views of the city of Salzburg.
We travelled from Kassel with a stopover in Regensburg to the Salzburg area. The steep approach to the lovely guesthouse was a first adventure for our ZA‘s mighty 60 hp. Ms Adler had to struggle with some really fast E-bike riders.
Everything went well. All the 15 cars arrived without any major problems, with only two of Gerald Palmer‘s masterpieces needing some fettling before their journeys.
The Magnette Day was an international meeting with participants from Austria, Switzerland, Luxemburg and Germany, all in all 30 enthusiasts and four dogs.
Worth mentioning was the fact that four actual presidents of Classic car clubs were aboard, representing the MG Owners Club Austria, the RR Enthusiasts Club Sektion Austria (driving an unrestored ZA), the MG Car Club Luxembourg and the MG Car Club Germany – such an honour to have them with us.
The Friday was a very relaxed day, meeting and greeting new and old friends, the initial tenseness due to the virus vanished fast. Our southern neighbours manged to establish a very nice
atmosphere, as we had the Erentrudisalm Gasthaus and Restaurant exclusively for our group.
On Saturday we made our way to a salt-mine in Hallein. It was really too hot for the dogs – a short walk and then a siesta under some trees was enough, the Golling waterfall cooling our four-legged participants and their human counterparts at the opposite ends of the leads.
Meals and drinking are very important for every family life, the team at the Erentrudisalm was very helpful, and the Saturday barbecue was excellent!
Sunday was the day for the Ray Cairn Trophy. This year the trophy was handed over to Vreni and Joe Keller from Switzerland and then came the tearful farewell as we all parted to head home.
Conny and I had some spare days so we headed to the Berchtesgaden area to relax and then we made our way to Kassel via Bayreuth. The only problem was a nonworking windscreen wiper; fortunately I found a loose contact and after fixing it everything went well.
Whatever the Coronavirus has in mind, the planning of the Magnette Day in 2021 is well on its way.
Pictures taken by: Erentrudisalm, Günter Graskamp, Conny and Dietrich Krahn
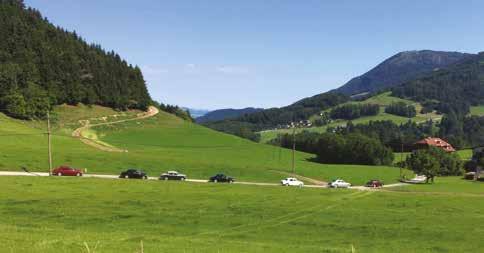

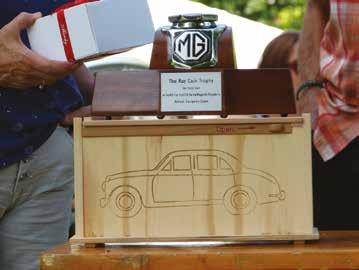
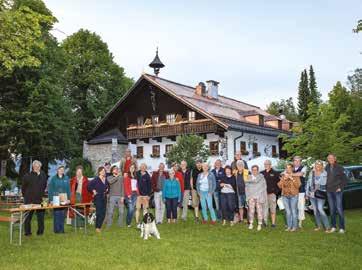
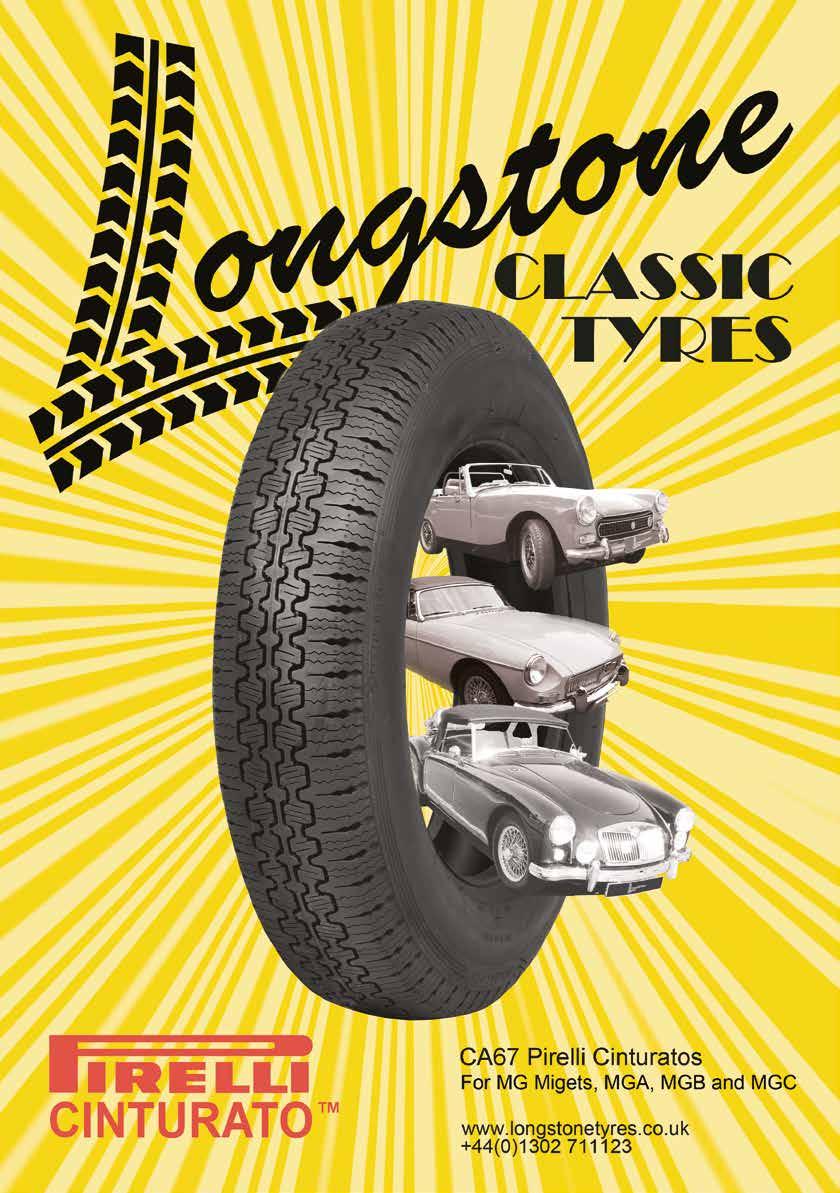