
5 minute read
SORTEX
Data equipping companies with essential information to combat sorting challenges
Companies using Bühler Insights are finding access to advanced data tracking in optical sorting is “nourishing” machinery with health and high performance in the same way that fruit and vegetables can nourish the body with nutrients for health.
The Internet of Things has brought with it an understanding of the many ways data can be used to increase productivity, identify faults, and earn higher revenue. Today, data has become a vital lifeline in the production of high-quality and sustainable fruits, vegetables and potatoes.
According to Bühler, to understand the value of data in optical sorters, it is important to understand the monetary value of a company’s time. For example, if a company is producing €10,000 of vegetable products an hour and there is a fault that is not discovered until two hours later, then the company has potentially lost €20,000 of revenue. This is just scratching the surface of the value of data in fruit, vegetable and potato sorting, but it gives an idea of the cost of not connecting and utilising data. The world needs to adapt to survive, and that includes the agriculture sector. Simply, data provides us with statistics that show behaviours, human behaviours, and machine behaviours. The more we understand behaviour, the more we can optimise, patch up the leaks, react speedily, and create a leaner, healthier business.
By way of example, Bühler dives into the three problems facing the fruit, veg and potato sector, and explains why how data is the “hero” we need. The data integrated into Bühler Sortex machines easily and instantly recognise blockages, reporting them on the dashboard and triggering an alarm.
processing will involve frozen products. A common problem is when a product clump or ice chunk gets stuck and causes a blockage. This becomes a larger problem when the blockage obstructs the camera view which is detecting the product. In this scenario, perfectly good product can end up in the rejected stream, wasting resources and money.
THE SOLUTION:
The data integrated into Bühler Sortex machines easily and instantly recognise blockages, reporting them on the dashboard and triggering an alarm. This means the issue can get sorted quickly with minimal contamination or loss of good material.
PROBLEM 2: VARIATIONS IN PRODUCT QUALITY
Two differently farmed potatoes may both be nutritious, but they’re not always equal when it comes to processing costs and quality. Fruit and vegetable processors will often receive their raw materials from multiple suppliers. The problem? One supplier’s quality may be better than another despite both farmers being paid the same. This could go unnoticed without the ability to measure and analyse the wasted material.
THE SOLUTION:
Data can effortlessly show which supplier has a greater rejected percentage. Appearing in the dashboard, the data will visually show problem areas, allowing customers to identify and act to reduce costs and become leaner. This could mean negotiating with the supplier for a better deal, and if they ask for proof, they can always be shown the data.
PROBLEM 3: HUMAN ERROR
Companies will often process more than one type of product, and Sortex is highly skilled at sorting different products, the problem is when operators forget to switch the mode accordingly to the product.
THE SOLUTION:
Data outperforms human reliability. Bühler Insights provides a timeline of the mode selected, making it easy to track the issue and resolve it before too much good product is wasted.
While the agricultural world is still rooted on the ground, the digitalisation of agriculture is increasingly being seen as an ally in keeping fruits, vegetables, and potatoes high quality, clean and sustainably produced.
Find Bühler at Interpom 2022
ARTIFICAL INTELLIGENCE FOR HYPERSPECTRAL SEAL INSPECTION OF RIGID FOOD TRAYS
The new HyperScope® uses Artifical Intelligence for smart seal detection of rigid packages, even with printed foils Contamination in the seal of rigid plastic packages causes important issues for food producers as it may lead to leakage and consequently reduced shelf life, health issues and even expensive recalls with potential brand damage. As such automatic detection of contaminated seals is important for both food safety and packaging production automation. Engilico, specialist in in-line seal inspection for flexible packaging, introduces a seal inspection solution for rigid trays, pots and thermoforms sealed with plastic or thin paper film.
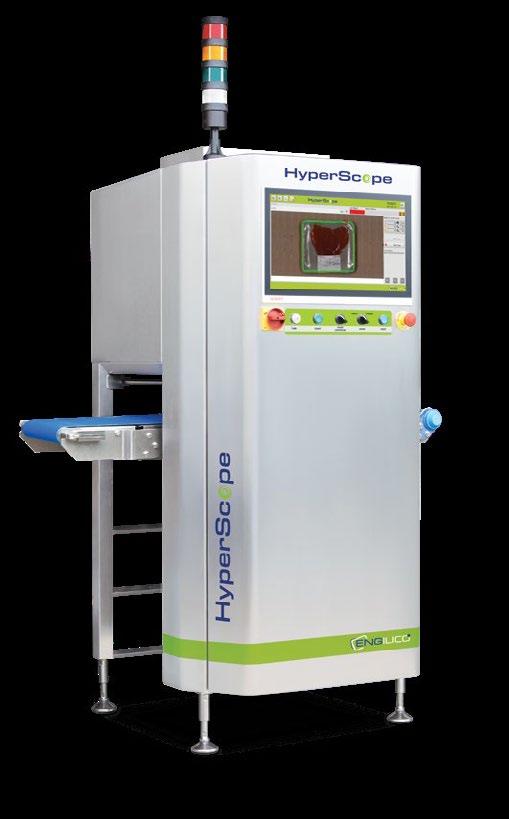
The HyperScope® solution is based on hyperspectral imaging (HSI). This technology enables to obtain images with much higher contrast than traditional vision systems and can even detect contamination through printed films. The inspection system features GPU-accelerated artificial intelligence, which enables high-precision seal area detection in real-time, regardless of the package orientation, packaging material, layout or size. Typical applications are the in-line inspection of trays with meat, cheese, seafood and vegetables.
In-line, 100% inspection
In an industrial food production environment, a hyperspectral system is implemented as an in-line, 100% seal inspection system that can check up to 160 packages per minute. Every package is inspected and the system issues a signal to an ejector to reject packages with seal issues.
The “core” of the HyperScope® system is situated in the software controller that uses artificial intelligence to instantly recognize the orientation of the package, and to analyze the seal quality. All information is displayed in an operator-friendly user interface to provide feedback on every package. All production related data, such as product type, number of good/ bad packages, date, time is saved to monitor the production quality.
In general, in-line seal inspection enables customers to realize better packaging quality, higher packaging productivity, end-of-line automation and reduction of manual inspection.
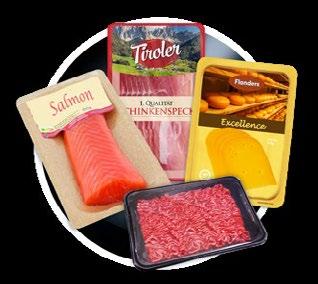
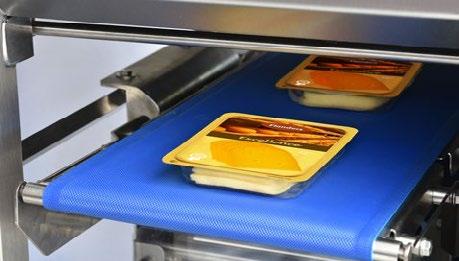
Visual image When product and film have similar colors (yellow-on-yellow), contamination in the seal is not visible
Hyperspectral image
The higher contrast reveals contamination (red) in the seal (green mask) CONTACT ENGILICO | Wingepark 55b 3110 Rotselaar | Belgium www.engilico.com