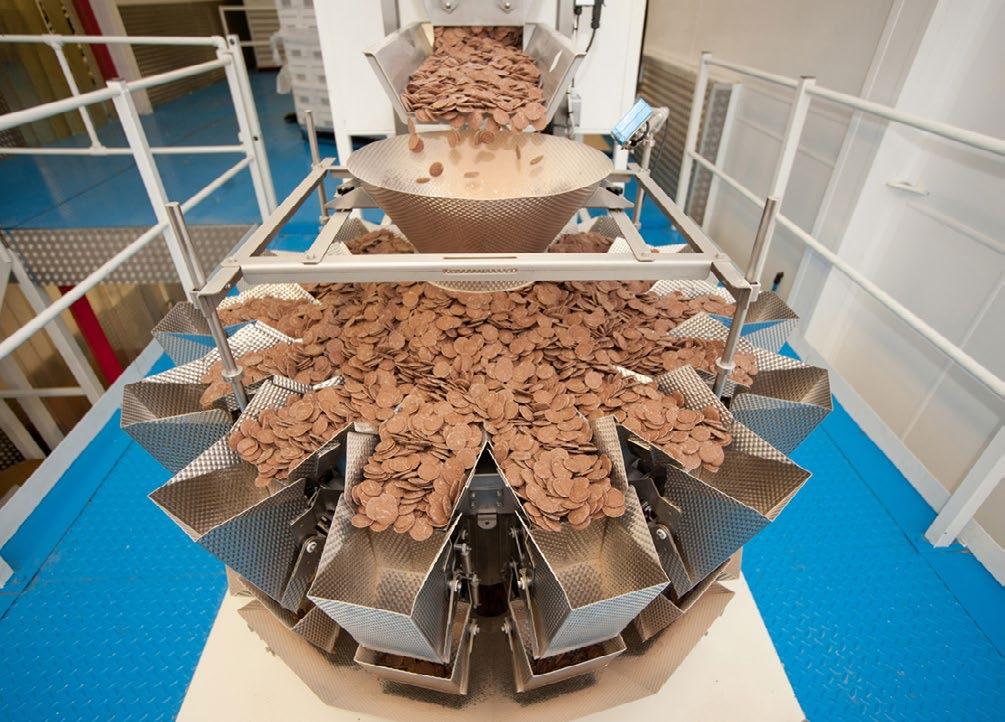
6 minute read
BCMPA
BCMPA exhibits for the first time at IFE manufacturing as outsourcing flourishes in the food and drink sector
The BCMPA - The Association for Contract Manufacturing, Packing, Fulfilment & Logistics – is excited to exhibit for the first time, at this year’s International Food & Drink Event (IFE), the UK’s largest food and drink show, which takes place at London’s ExCeL on the 21st-23rd March. The show is colocated with IFE Manufacturing, and the BCMPA will be representing its members in the food and drink industry, several of whom will also be exhibiting.
With just under four weeks to go, this is the first IFE event in three years, due to pandemic lockdowns, and the BCMPA believes that there will be much demand within the industry for a face-to-face event that brings together so many disciplines involved in food and drink production. The event will reflect the significant growth in demand for these services.
The BCMPA will be promoting the huge benefits that brands, entrepreneurs and retailers can gain from the outsourcing of their contract manufacturing, packing, fulfilment and logistics projects to 3rd party suppliers.
More than 30,000 visitors are expected at IFE 2022, which provides businesses with the perfect opportunity to discover what’s new, source innovative products, understand the latest consumer trends, and build face-to-face relationships to keep ahead of the competition.

Visitors to the BCMPA stand will learn about the extensive range of services offered by its members, from new product development, formulation and manufacture, to filling, packing and distribution. BCMPA members are now playing a key role across the supply chain for many of today’s leading food and drink brands.
In addition, the BCMPA will highlight its unique search facility available on its website, which helps retailers, wholesalers and foodservice professionals in finding the ‘perfect fit’ for their 3rd party outsourcing requirements.
Emma Verkaik, Membership & Marketing Director of the BCMPA, sees this as an ideal event for both its members and the wider food and drink sector; “At a time when the value of outsourcing has never been more important in the supply chain, the IFE Manufacturing show could not be more timely.
“It provides all the elements required to help businesses grow successfully, as well as giving brand owners and retailers an opportunity to talk to the BCMPA about their outsourcing needs and to find potential manufacturing solutions.”
Exhibiting BCMPA members include Imperial Food Packing, Place UK, Storefast Solutions & Universal Flexible Packaging. The BCMPA is also sponsoring a panel session on Monday 21st March at 13.00 with members The Alexir Partnership, Sauce Shed and independent Food Product Development Consultant, Nick Henson, to discuss the effectiveness of scaling up of production services with contract manufacturers.
Verkaik added; “IFE provides the perfect environment for our contract manufacturing, packing, fulfilment & logistics members to showcase their solutions to retailers and brand owners from the UK and abroad. We are delighted to be back supporting both our members and their customers in person again.”
Tickets for IFE can be secured online here.

Jam manufacturer cuts 20% of pectin from formulation using the Silverson Flashmix
A jam and marmalade producer has been able to reduce the amount of pectin in their formulation by 20% and reduce their process times and wastage with the use of a Silverson Flashmix powder/liquid mixer.
The company had previously been using basic agitators to mix the pectin in a 400 litre vessel at temperatures in excess of 55°C. They were incorporating around 20% more pectin than they actually needed for their formulation to account for what they were losing due to agglomerates and partially hydrated pectin sticking to the agitator shaft, blades and the walls of the mixing vessel. After around 40 minutes they were left with a low quality 5% pectin solution, wasting 20% of the material they had added as the agitator was unable to break down the agglomerates. This wastage was costing a considerable amount of money and after the mixing process they had to put the mixture through a filtration stage to remove the agglomerates, further lengthening the process time. cleaning was minimised and the mixture no longer needed to be filtered after mixing.
Using the FMX50 the consistency and quality of the mix was much better and the process time was dramatically reduced. The company would be saving a huge amount of money on pectin by being able to use 20% less pectin for each batch and by not having to heat the water before adding the pectin. The trials were so successful they company purchased the FMX50 for their factory.
And now the advantages of high shear powder/liquid mixing can be achieved at Laboratory scale with the introduction of the FMX5 mixer to the Silverson Product range.
The FMX5 is a laboratory scale version of the Flashmix and provides a simple, effective and hygienic means of powder/liquid mixing suitable for small scale manufacturing and R&D work with a typical batch size of up to 10 litres, depending on viscosity.
Trials were arranged at Silverson using a Flashmix FMX50 production scale powder/liquid mixer to incorporate the pectin. The trials were run at ambient temperature and it took around 10 minutes to incorporate and fully hydrate the 5% of pectin that had been added. With the FMX50 there were no agglomerates and no partially hydrated powder sticking to the vessel wall, so
If you’d like to find out more, visit the Silverson website: www.silverson.co.uk
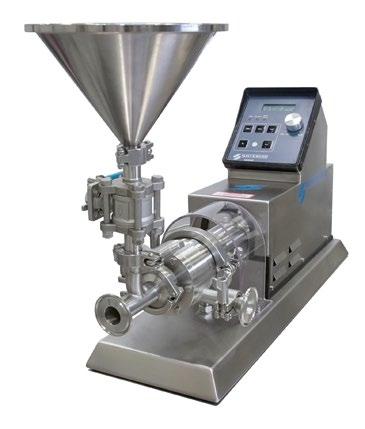

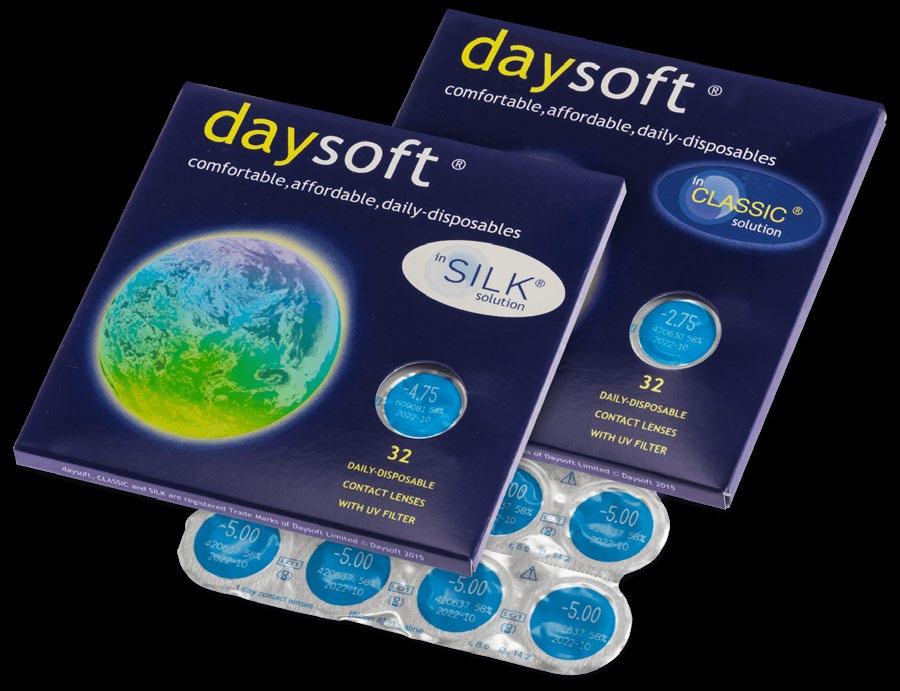
Which consumer-product relies most heavily on precision engineering? The first product to come to mind should be
daysoft daily-disposable contact lenses
Let me explain; daysoft relies on the skilful application of the most advanced manufacturing processes in the world to produce millions of identical contact lenses, time after time. Our unique process produces lenses at half the cost whilst only using half the plastic compared to any other daily-disposable contact lens manufacturer.
All this has been made possible by the development of a unique process of manufacture based on incredibly advanced precision engineering where the lens is made entirely inside a concave mould of exceptionally high precision.
INPAC TECHNOLOGY
The mould precision relies on the absolute accuracy of metal formers which have been cut to give outstanding accuracy and a ‘mirror’ finish using diamond tipped tools in air-bearing lathes to eliminate all polishing.
The highest level of precision is not just to ensure the lenses provide great vision but so that they sit comfortably and safely on the human eye making … every day a comfortable daysoft day
Kind regards Ron Hamilton CBE, Engineer, Contact Lens Inventor and Daysoft Founder © Fergus H Yard 2021. Used with permission.
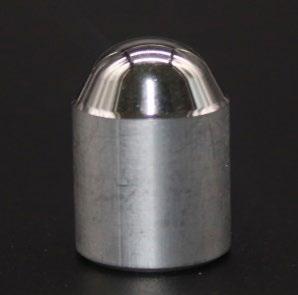