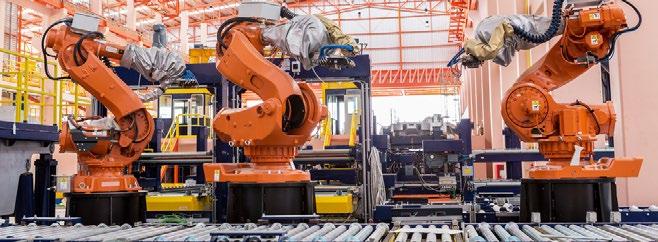
8 minute read
ABB
Are robotics set to play a starring role in the next ten years of British manufacturing?
Technology is constantly changing our day-to-day lives and has had a particular impact on the working world. Automation is fast becoming a key conversation within multiple industries in Great Britain, including manufacturing with robotics emerging as the solution.
Over the past few years, a need to move towards more automation in the manufacturing industry has been seen. In fact, a survey done by ABB Robotics found that of 250 SME and manufacturing companies, 81.2% were considering incorporating robotics into their processes to combat issues with workforce shortages and supply chain disruptions.
In this article, we’ll look at how, in order to keep up with the demand British manufacturing faces, more businesses are adopting robotics as a solution. We’ll also dive into what they can do for your business.
WHAT CAN ROBOTS DO FOR YOU?
A big question from businesses still on the fence about bringing in robots is what can they do to improve processes. By automating sections of your manufacturing processes with robots, you’re given an opportunity to stay competitive within a constantly evolving industry.
Substituting traditional labour with robots within your processes can help to provide added efficiency. Robots don’t require breaks, and they’re programmed to carry out specific practices with much smaller margins for error than humans. This results in a more cost-effective output from your business, which could see greater revenue for less paid labour.
Robotics can also be useful when it comes to tasks that require a steadiness that can’t always reliably come from humans. Whether it’s handling or removing materials that can be harmful or dangerous, welding, or separating materials from one another, robotics makes those tasks much easier to carry out.
THEY WORK AMONG US…
The UK’s manufacturing industry has leant into a ‘quality over quantity’ mentality, focusing on top value from each product made, and robotics are now being incorporated into processes.
Between 2020 and 2021, the UK became one of the top 15 for sales of industrial robots globally. The International Federation of Robotics (IFR) found that 2,205 industrial robots were installed throughout 2020, which brought the total in the country to around 23,000.
These robots are primarily found in the automotive manufacturing industry in the UK with around 875, making up 16% of those that were installed in 2020. Several sectors are seeing a benefit in robot application due to a lack of workers, including the food and beverage sector, which already uses industrial machinery and hydraulic cylinders, has seen an increase to 304 robots in 2020. This is a 96% increase in volume since the previous year.
LOOKING TO THE FUTURE
Though these numbers continue to rise, the IFR still ranked the UK outside of the top 20 countries with robot density within manufacturing. We can take from this that there is still room for robotics presence in manufacturing to grow on our shores.
The government itself outlined how much growth was possible in a Business, Energy and Industrial Strategy (BEIS), estimating that there was a potential 40% annual growth for robotics and autonomous systems in the UK between 2020 and 2030. This could in turn mean an extra £6.4 billion in value for the UK economy by 2035. And if our creation and sale of autonomous robots is set to increase, our use of them across a number of industries may be set to increase alongside it.
Automating your business process with robotics is not something to be scared of. The myth that robotics steals jobs has long since been debunked, and there is plenty of room for improvements within the manufacturing industry that they can help solve. Implementing robotics can help keep your business competitive in the global market, as well as provide an efficiency that is impossible to achieve with manual labour. There are currently a record number of robots installed; however, there is still room for growth, and the amount of revenue that could stimulate the UK economy if more is installed is staggering.
Good Practice Guidance for Electrical, Control and Cyber Security in Industrial Engineering
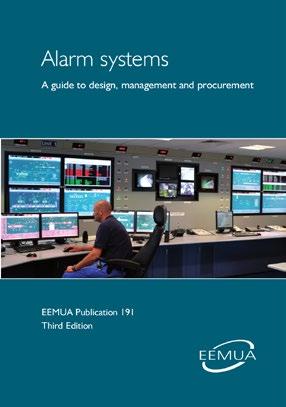
• Practical guidance for everyday and irregular situations and tasks • Verified and developed from contributions by the industry, for the industry • Readily accessible for all in the industry – wherever they are, whatever time they have • FREE task and procedure checklists • E-learning for professional development
Management of ageing electrical assets
Publication 227
Edition 1
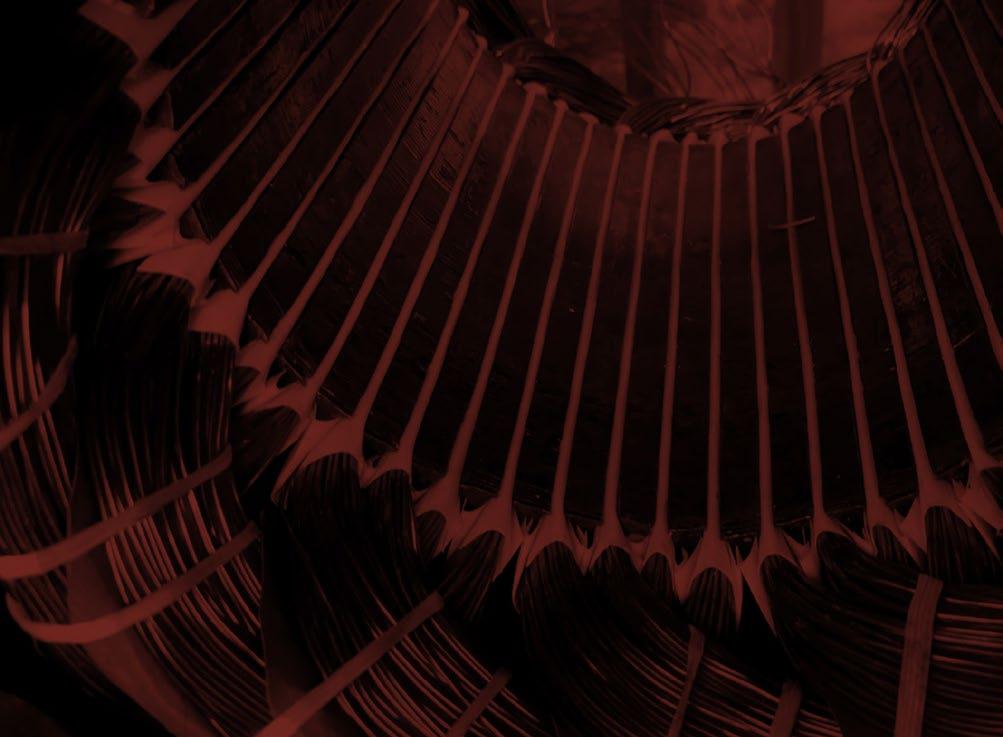
To purchase or for more information, please visit www.eemua.org
Innovative packaging machinery
Cap Coder are an established family-owned engineering company that is based in Chalgrove near Oxford, UK. The company was established over 40 years ago as a designer and manufacturer of equipment for the packaging industry – and has since grown to be a leading supplier of liquid filling and bottle capping machinery.
We are a dedicated engineering company, designing and manufacturing both standard and bespoke solutions to a range of filling, capping, labelling and coding applications for a strong customer base, both in the UK and Worldwide.
The Cap Coder range of equipment includes simple semi-automatic units designed for low-production and start-up companies, right up to fully-automatic monobloc systems producing products 24/7, 365 days a year.
Our in-house design team respond to an array of packaging challenges, and bespoke turnkey lines (including the integration of labelling, coding and vision checking systems) are tackled on a regular basis. Cap Coder has a network of experienced service engineers that install our machinery and offer the highest level of support to existing customers in the provision of change parts, spares and technical advice.
Cap Coder will strive to continue to innovate, meeting the changing needs of its customers with the development of new products.

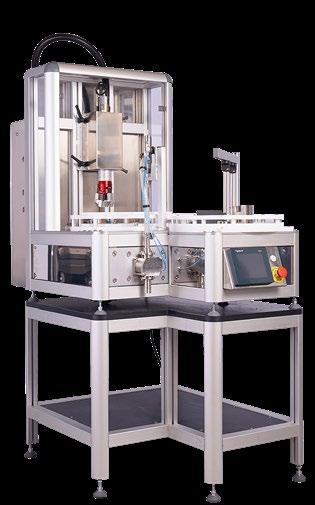
www.capcoder.com Tel: +44(0)1865-891466

PhoenixTM solution to HACCP Cook & Chill CCP Validation
As part of any Food processors HACCP program, validation of cook and chill processes is a critical and significant task, taking time, effort, and resources.
PhoenixTM have developed a thruprocess temperature monitoring technology specifically for this task, designed to meet the challenges of the food processing market. Ideal for the validation process for any new cook regime, new product, or annual process certification. Whether performing an oven survey “oven mapping to identify cold spots” or validating the cook under production conditions, the thru-process profiling solution gives you the accuracy, efficiency, and reliability you need to satisfy your HACCP demands.
As its name suggests, thru-process profiling is the method by which product and or process temperature is monitored throughout the complete cook / chill process. The data logger making the physical temperature measurement, with multiple thermocouples, travels safely with the product through the process. Protection from process conditions such as heat, steam, water, and oil is provided by a suitably designed thermal barrier. The thermal barrier provides robust protection to the data logger to prevent damage but also ensure that it maintains a safe operating temperature to give accurate temperature readings. Monitoring of continuous conveyorised linear and spiral ovens and semi-continuous or rotational batch cooks is feasible where the use of external recorders with trailing thermocouples is tedious, completely impractical, and possibly unsafe . Employing the thru-process principal, process monitoring can be performed under true production conditions without compromising line productivity . At the heart of the thru-process monitoring system is the PhoenixTM data logger. The PhoenixTM NT data logger range has been designed specifically for the challenges of monitoring food processing applications with an IP67 case design protecting from moisture. Type K or Type T data logger options allow accurate measurement of both cook and chill processes (Type T measurement range -200 °C to 400 °C). Data logger and thermocouple correction factors can be applied to the recorded data logger data to maximise measurement accuracy. PhoenixTM offer a range of thermal barriers to suit the process type, duration, and temperatures. Even if a standard thermal barrier cannot meet the process requirements, PhoenixTM can often custom design a unique solution to suit.
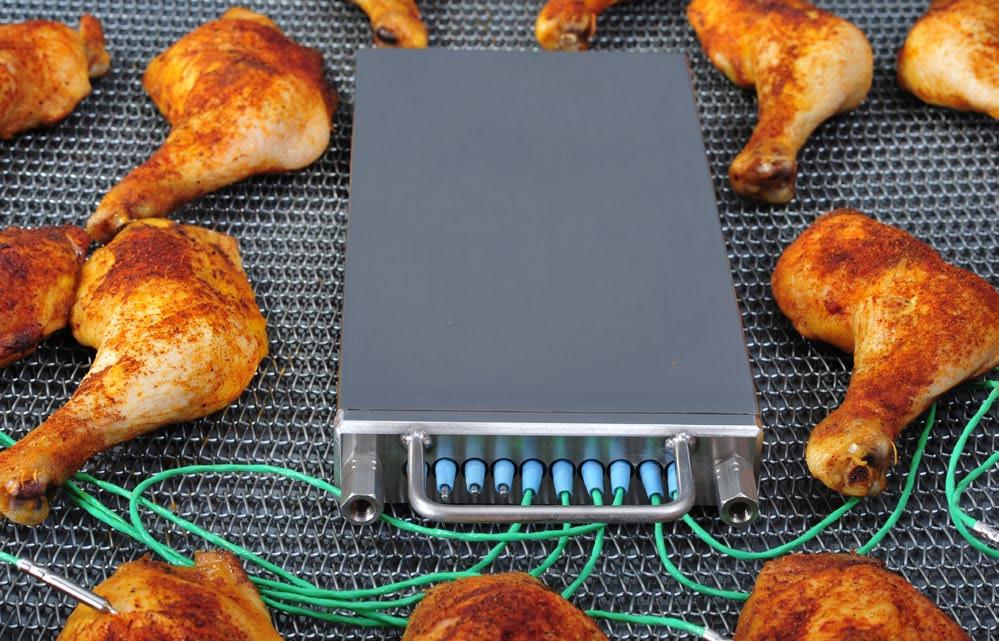
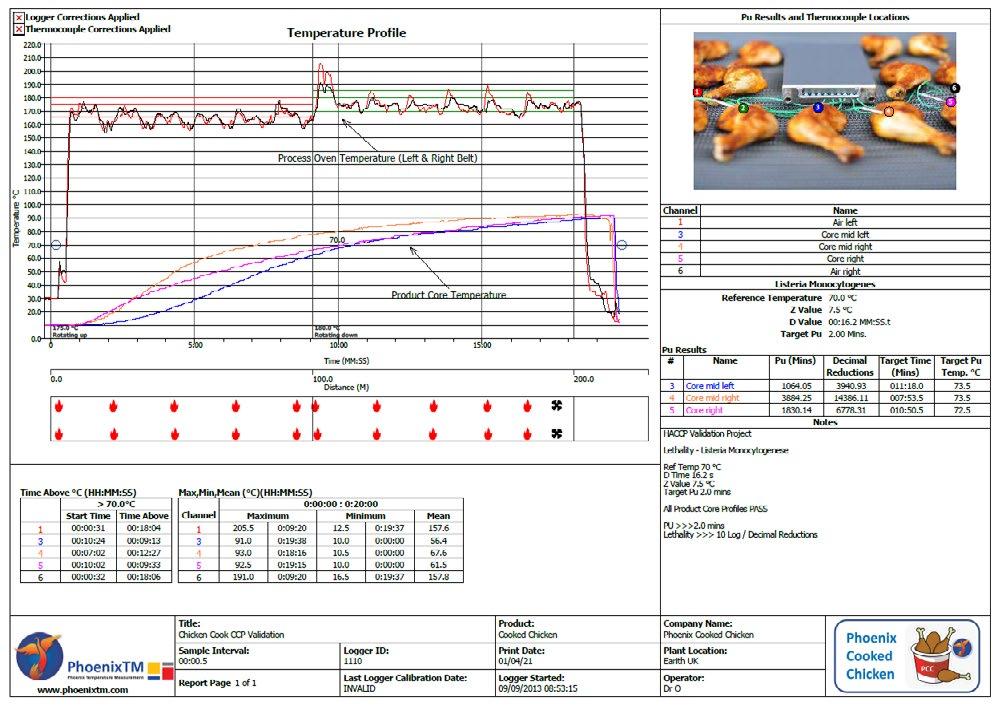
Monitoring core temperatures of food products can be a challenge and getting it right or wrong can have a significant influence on the data collected and therefore any decisions or conclusions made. PhoenixTM offer a range of different designs of thermocouple to suit different product types and sizes. The needle thermocouples ensure you can measure the true core/cold spot of the product accurately and repeatably. Fitted with standard miniature thermocouple sockets, the data logger is also compatible with other generic commercially available thermocouple designs.
Employing the thru-process temperature monitoring principle provides the food technologist with a complete temperature profile of the cook process from start to finish. This information is like the Cook DNA giving full details of the product and or process temperature which is invaluable to allowing validation of the Cook CCP. From a temperature profile it is possible to accurately quantify product safety (pasteurisation) knowing both the temperature, and time at temperature, of the product. Employing the thruprocess temperature monitoring principle provides the food technologist with a complete temperature profile of the cook process from start to finish.
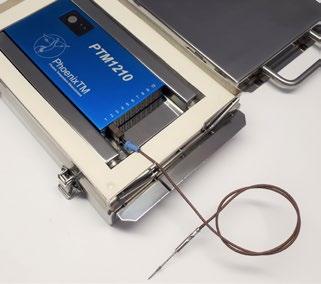
From the profile graph you can see instantaneously the variation in product temperature at any point in the process either at different locations on the product (whole chicken) or different product positions within the cooker, cooking rack or across a mesh belt. The PhoenixTM Thermal View Food Software provides a comprehensive suite of analysis tools to convert the raw profile temperature data into useful process information. The analysis tools include the ability to calculate Fo/Pu values for the process against target micro-organisms. For a typical chicken cook process the lethality parameters for Listeria Monocytogenes (Tref 70 °C, Dt 16.2 s and Z value 7.5 °C) can be input to automatically and accurately calculate for each monitoring point the number of decimal reductions of the pathogen achieved during cook to meet CCP limits.
The information gathered, further to process validation, can be used to allow informed process problem solving and optimisation to maximise product quality, yield, process productivity and efficiency.
Contact PhoenixTM to help Find, Fix and Forget your Food Cook Problems!