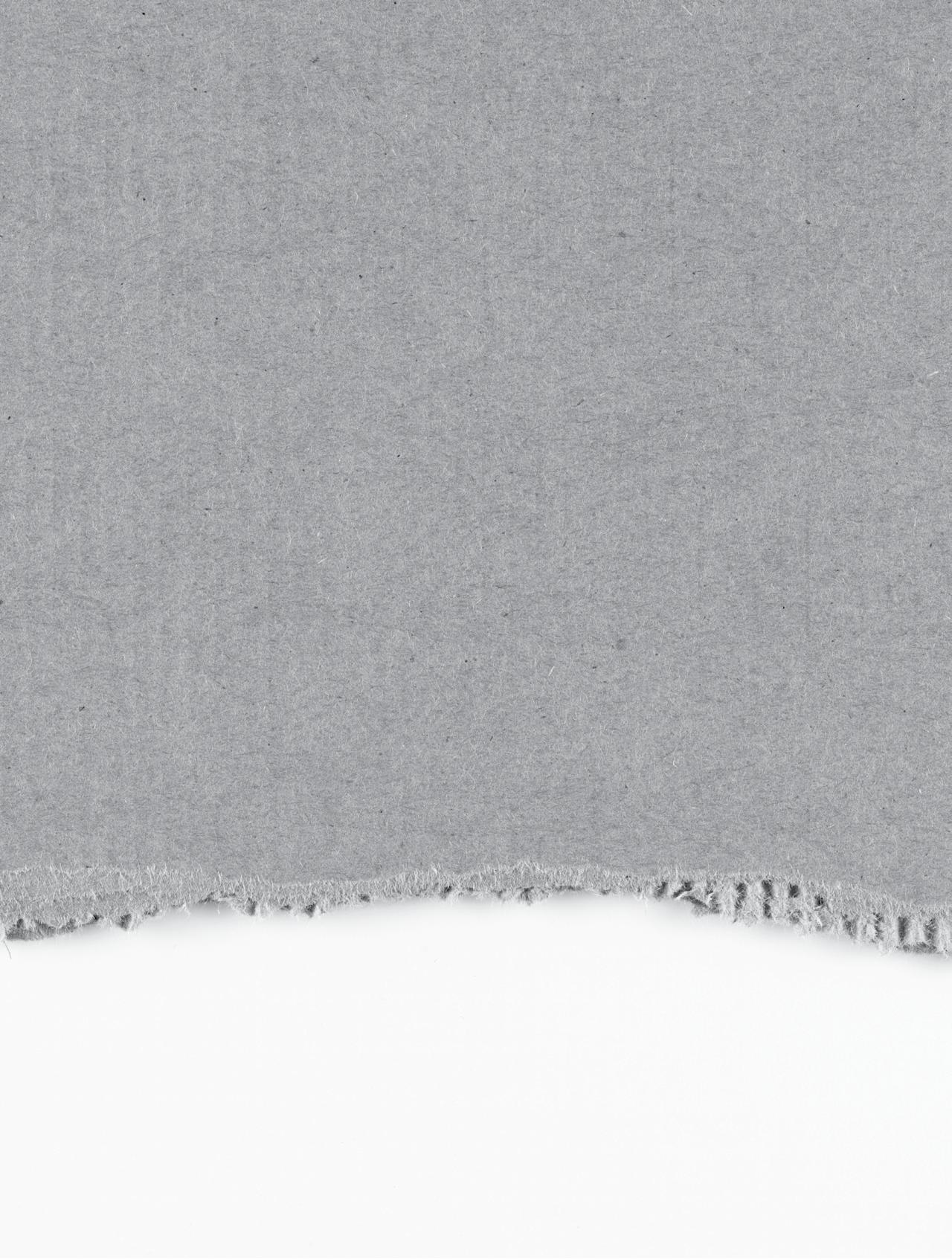
5 minute read
Taking Engineering to Heart Packaging Compliance Labs
BY CASSIE PETERSON, MARKETING, MANAGER, PACKAGING COMPLIANCE LABS
Packaging Compliance Labs has been through four major expansions in its history including, adding a lab, doubling its office space, and creating a mock surgical facility. Co-founders Matt Lapham and Ryan Erickson recognize the significance — and the seriousness — of their upward trajectory. Lapham noted, “We never want to lose sight of the people who need the medical products we work with.”
Advertisement
The medical device packaging engineering, validation lab, and contract manufacturing firm works hard to protect its small-business, customer-centric mindset from the pitfalls of big business. Lapham stated, “We are fortunate to work with global leaders and major corporations, but we also work with small startups and OEMs. Every one of those clients is in the business of bringing life-improving or life-saving products to people and families. We honor that reality with our clients. Internally, we have a continuous improvement culture that keeps us mindful.”
Taking Quality to Heart
When Ryan Erickson, Vice President of Engineering, attended an open-heart surgery at a northeast Ohio hospital, he had the opportunity to experience the full journey of a life-saving device, like those for which he designs packaging systems every day.
Scrubbed and gowned, Erickson had listened intently as the cardiovascular surgeon explained that the open-heart surgery would repair a congenital heart condition that had not only severely affected the patient’s quality of life but had also been a looming threat to her life altogether. The surgeon explained that the procedure would replace a defective aortic valve with a prosthetic valve. Seeing the heart lay on ice while the ECMO (Extracorporeal membrane oxygenation) machine sustained the patient’s life and the surgeon implanted the valve was sobering. Yet, it helped Erickson prepare for upcoming projects engineering packaging for emerging technology in prosthetic cardiac devices.
Within hours, the young patient, with a fully functioning heart, was wheeled to recovery with a new chance at a healthier, more active life.
Back in Michigan, Erickson reported that it had been meaningful to reflect on the young patient’s new hope for the future and how her family must have felt. He went on to tell his team that the experience had driven home the weight and significance of their work. After hearing the story, it was easy for the team to agree that every strict quality assurance measure they follow is worth the effort.

Additionally, Erickson’s experience observing that procedure cemented the importance of understanding real surgery situations, patient needs, provider expectations and more. Since that visit, PCL (Packaging Compliance Labs) has launched a new Usability Evaluation service and mock surgical facility to ensure its packaging and manufactured products meet the highest quality standards and maintain a patient- or end-user focus.
Even PCL’s in-house training programs emphasize the human side of the medical device equation, whether lab or engineering. Quality Manager and Senior Packaging Engineer Ryan Ott noted, “We hammer the message home that whether designing a joint replacement package or running a transit test, oversights could hurt someone—and that someone could be your mom, your grandma, your child or brother.”
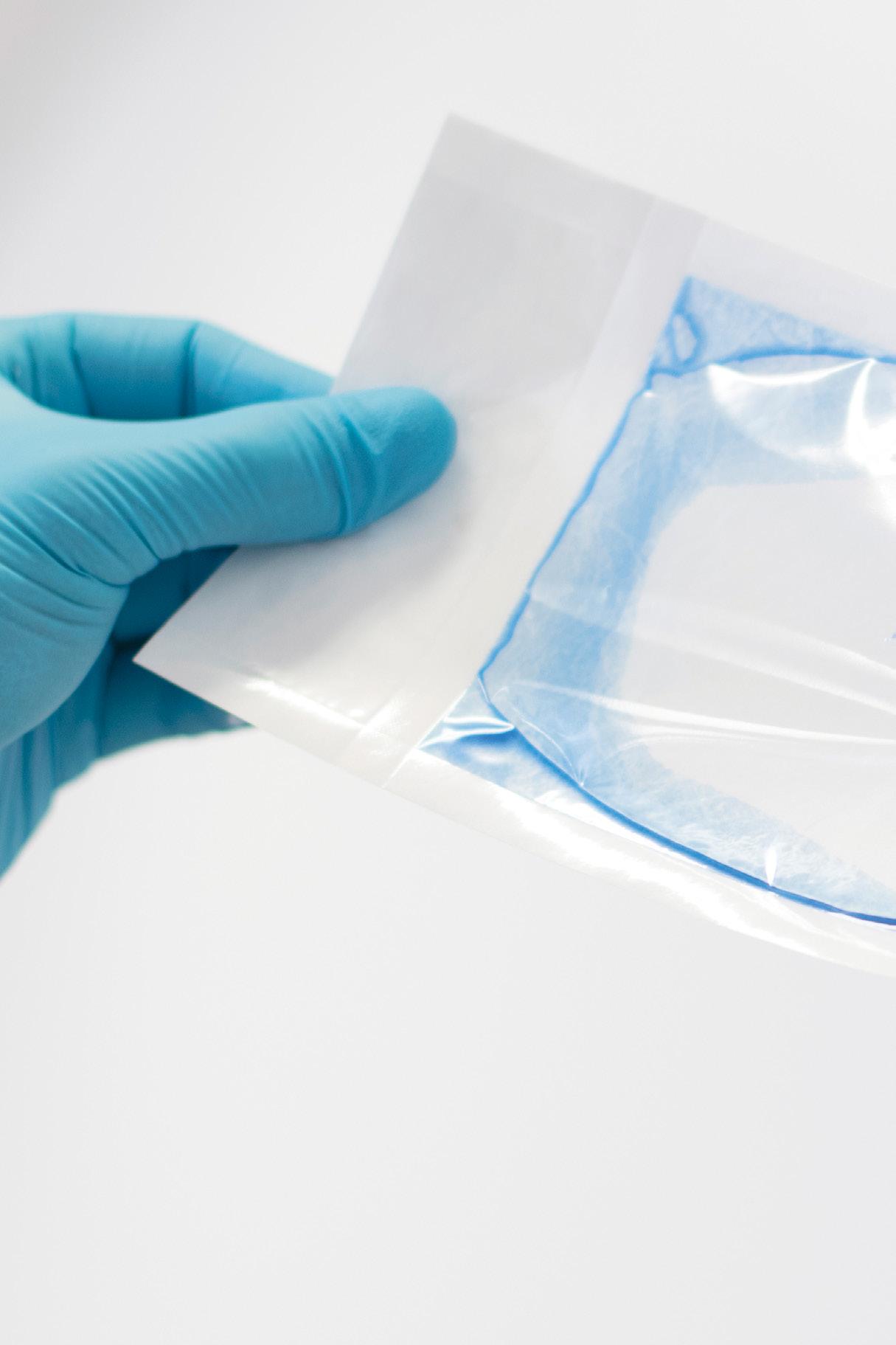
Coincidence and Consequence
Erickson added that just as his operating room visit was so inspiring, it brought to mind a past project that had hit close to home in the opposite way.
He recalled, “A client distributed a wide variety of popular health care products. That client was outsourcing the packaging of this product line, as happens all the time, and had received some negative reports. Those reports led them to enlist PCL to research and investigate the potential problems.”
“It just so happened that around that time, a PCL family member had cause to use these products and had ordered them online. When they arrived, the PCL employee saw the products and was alarmed to see multiple failures and defects in the ‘sterile’ packaging. Confiscating the products, our team member advised the family member to seek a substitute.”
Erickson continued, “Examining those products in the PCL lab, our findings showed a flagrant disregard for quality control - something that was confirmed upon visiting the outsourced facility. We don’t usually see the actual products we test. In this case, timing was everything and, unfortunately for the client, the concerns reported were valid.”
“We had product from the marketplace, we’d confirmed the failures, and our investigative visit to the outsourced facility fueled our report and recommendations to help our client restore their quality standards — starting with severing the relationship with the careless, non-compliant vendor.”
It is stories like these that make the day-to-day work feel worthwhile and exciting. Packaging Compliance Labs is proud to be part of the MI Bio community!

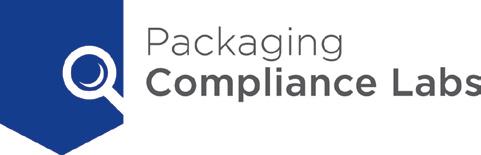