
10 minute read
FORAGE PRODUCTION ON CATTLE FARMS
by Doug Ward Doug@ABPmag.com Forage production on cattle farms & ranches is one of the most essential elements needed for it to be profitable. The only reason the Beef cow was put on this earth was to convert lower quality forages that are inedible to humans and turn them into a very delicious protein for human consumption. The cow would graze the rough terrain, consuming forage not only to feed herself, but to also provide nutrition to her offspring. Ideally year round grazing of these forages would greatly reduce the need for equipment and in turn increase profitability of the ranch or farm. The climate that you live in dictates how much forage has to be mechanically harvested and stored to feed the herd during the winter months and during years of lower production due to weather. There are 100 different ways to put up hay. From the early days of putting up loose hay, to the invention of the small square baler. Then there‘s the now high capacity round and big square balers along with self-propelled forage harvesters. The modern-day equipment has come a long way to help reduce labor and time needed to harvest forages. Though it seems like we don’t have as many good harvesting hours in the day to put up quality forage as when we were younger. This might be due to the instant access to weather on our smart phones and the weatherman not being as correct in their forecasts that reduces our harvestable hours. Plus there are some of the more arid parts of the U.S. where baling is done at night when there is a dew on the hay to help prevent leaf loss.
What are companies providing and what are the farmer/ ranchers wanting these days in equipment?
Farmers/ranchers want equipment that is reliable, cost effective, and has the ability to do the job a fast, efficient way. Equipment has become bigger and faster due to less available labor. Another question one has to consider is to own your own equipment or to hire the job done? Machinery is not cheap to own. Most of the custom operators have newer equipment that might be more reliable than what you can afford on your own. Equipment dealers are providing more customer and technical service in recent years. When I was talking with one of my local dealers, he mentioned that within
their 4 stores, they were able to have a forage specialist amongst their employees to help producers with problems and breakdowns. This way communication between the dealer or service tech can be face to face or via cell phone while in the field. Wireless communication can reduce downtime if the problem can be diagnosed without bringing equipment in from the field to be repaired. Before a company turns out a new piece of equipment, they go through a couple years of research on it before selling it to the public. They research out in real situations in all parts of the country. One machine might be running over 20-30,000 acres to ensure that every possible scenario is covered.
Cutting hay and other for
ages: Many producers have gone to the Disc Mowers. These mowers range in sizes from 7 - 20 feet. They can be just a cutter bar or be equipped with conditioning rolls.
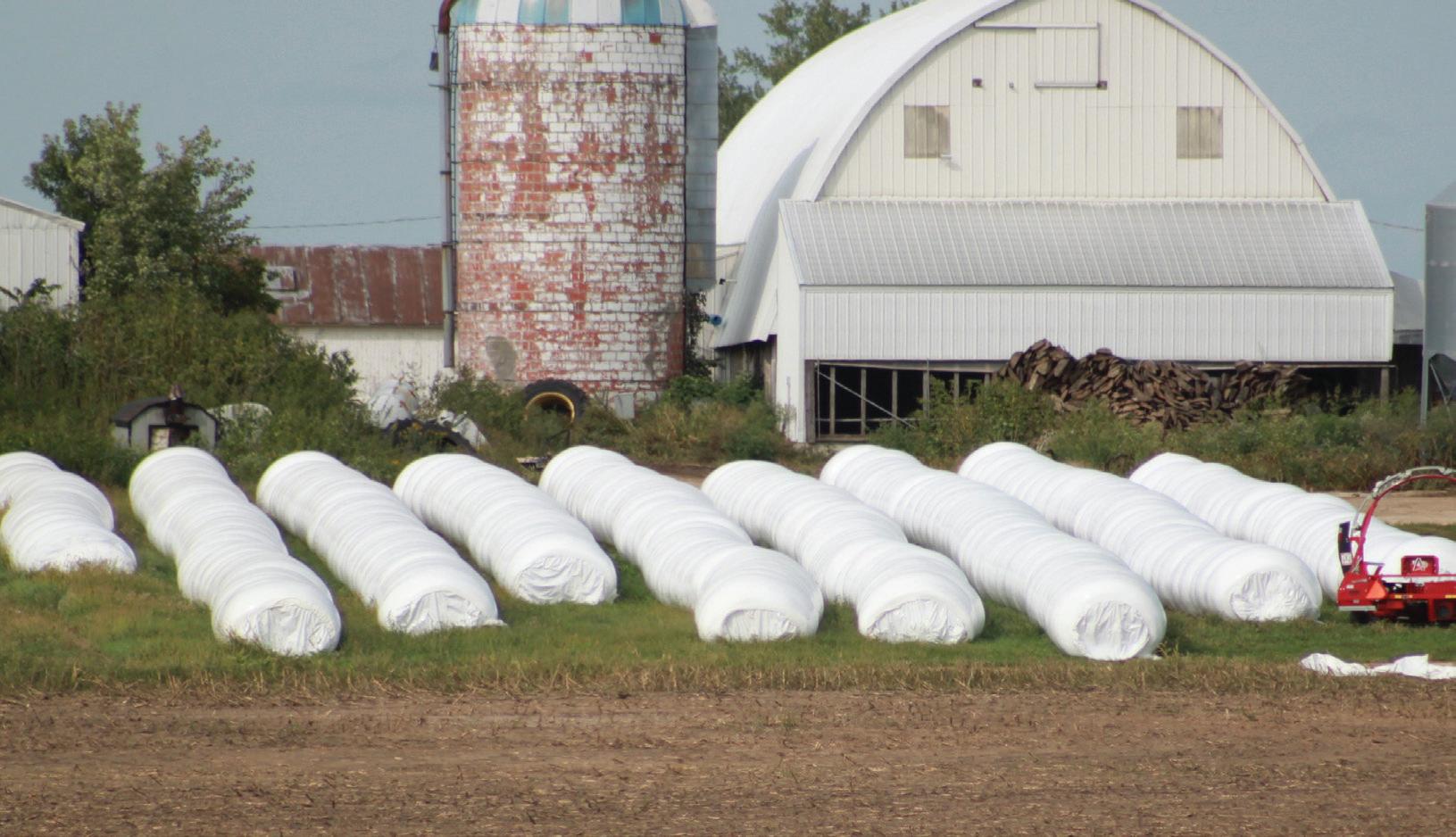
The principle of the machine is by having knives on a rotating disc which provide high speed, non-clogging cutting. Continuous non-stop mowing is accomplished. The smaller producer can use one that is 3 point mounted on smaller tractors. Pull behind models come in side draft, hydro-swing and self-propelled. Bigger machines require higher horse power to do the job. But there are disadvantages. Initial costs are higher and resale value can be lower. If you have rock in your fields, these are not the machines to use. Hay quality is also reduced as more ash (dirt) gets into your windrow. The Sickle Mowers can still do the job. They can be towed behind a sickle bar or can come equipped as a mower conditioner. High quality hay can be produced with this type of cutting. The mower conditioner has a reel to guide hay into the cutter and conditioner which can help in picking up downed hay. Although this machine has to run slower ground speeds, it has the advantage of being lower cost. In some parts of the country where higher humidity levels hinder the drying of hay, the Tedder has gained popularity. These machines fluff the windrow to allow more air movement to the forage. The rotary tedders take the forage and spread it out wide allowing more of the crop being exposed to the sun. These machines can reduce drying time by a day or two. Higher quality forage can be put up by using a tedder. Tedding dry hay can lead to high leaf loss and quality. Rakes have changed over the years. Raking was used to speed the drying process and to make a narrow windrow. October 2020 The Single Basket Bar Rake was the standard for years. It produced good quality hay as the tines did not touch the ground. Speed of raking is slow and only one windrow at a time could be turned. Most are hydraulically driven with one being left delivery and the other right in the same unit. Cost of this machine is higher. Rotary rakes both single and double can rake nice clean hay into a windrow without added dirt to the hay. The tines do not touch the ground, but are higher cost and higher maintenance with many moving parts. They work well when combing windrows of higher moisture hay. Can lead to leaf loss when used to rake dry alfalfa. The most common and cost effective rakes are the Wheel Rakes. The wheel rake has very few moving parts. One windrow with some models to many feet of cut hay with other models. The ground drives the wheels so there are fewer moving parts and they can handle high ground speeds resulting in high volumes of forage. The small Square Baler is still being used in most parts of the country. A person can put up some really high-quality hay in a small square bale which still has its place today. They come in handy when needed to feed a single or a small group of animals and can be hand fed. The big square balers have its place in forage production too. Continuous baling is an advantage for big squares. Basically, the baler does not have to stop in the field once you start to bale. They can bale up many acres in a day when the hay is dry.

A disadvantage of this type is the hay has to be drier than round baling and most of the time a preservative has to be used to prevent spoilage. Higher HP is needed to power the baler and baler cost is high. Round Baling has become the most go to way of baling hay. Tons per hour can be baled with most round balers. With the bales rounded tops they can shed most of the rainfall and do not necessarily need to be stored right of way. The standard size baler makes a 5x6 ft. bale. Other sizes include 4x5 and 4x6. Newer model round belt balers make a very tight, dense bale that is easy to handle and transport. Many options can be added to the baler, like moisture meters, preservative applicator, bale density gauge, bale accumulator, bale ¼ turn positioner to aid in picking up bales in the field. The monitors for the baler provide a lot of settings for aid in making the correct shaped bale. Twine can be used to wrap the bale but net wrap has become the norm. A mesh is wrapped around the bale while in the baler. It provides for a nice and neat looking bale that sheds more moisture and can be handled multiple times still keeping its shape. In the last couple of years, a Self-propelled Round Baler has come onto the market. This unit is gaining interest amongst larger and custom operators. It has the ability to replace possibly 2 pull type round balers due to its speed and efficiency which reduces the need for multiple balers and tractors. It has moisture sensing, cameras and even an auto mode. It is great when baling corn stalks. It can ¼ turn to position bale
more easily so it makes for more efficient mechanical pickup. The unit also has a higher highway speed to get to multiple places in one day. Operator comfort is another advantage with this unit since there‘s no need to look backwards at the machine while operating. Then there‘s Silage Bales. Both big square and round bales can be baled at 35-45% moisture and wrapped with plastic to prevent spoilage. A smaller diameter bale is used as the weight of the bale is increased due to higher moisture levels. Silage balers can handle the higher moisture hay and many times are equipped with knives to cut the hay for easier feeding. Bales can be feed free choice, rolled out or even further processed in a vertical feed wagon or bale processor. Although the cost of plastic can cost up to $4.00 per bale plus equipment costs, this method of harvesting and storage can take out the weather equation. Most of the cutting takes place on day 1 and day 2 consists of baling and wrapping. With so many different ways to put up high quality, a person has to decide what works on their operation. This was just an overview of what‘s available in terms of equipment. Ideally, we would like to graze all year long. ABP
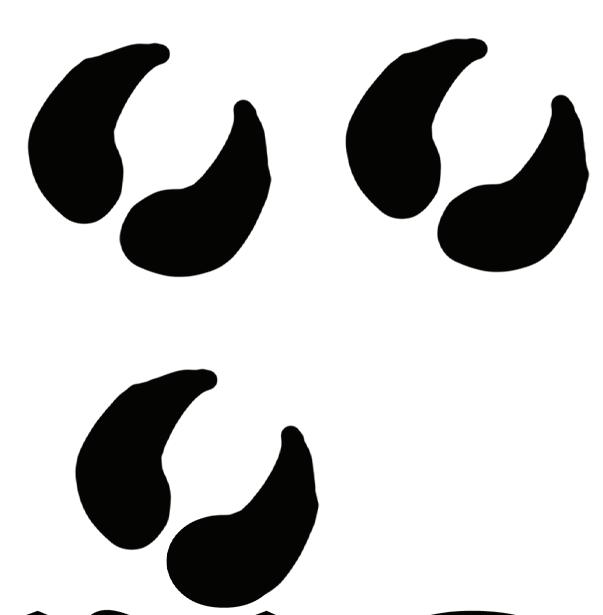
Artex SB Series Spreader
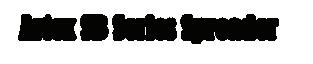

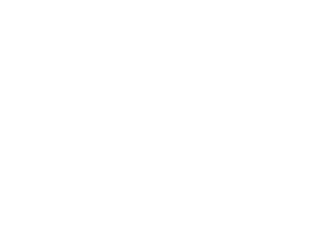
This is quite simply the most advanced, best built manure spreader you’re ever going to see. Now, do you want one this tough? Well, that all depends on how often you like to buy them. 900T Supreme TMR Mixer

The World’s Best TMR Processor. Supreme offers a full line of pull-type, stationary, and truck-mount mixers from 285 to 1,585 cu. Ft. with every unit custom designed and built.
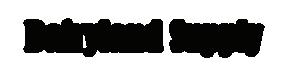
Off I-94 on the corner of Hwy. 28 & 71 So. Sauk Centre, MN 800-338-6455 or 320-352-3987 www.dairylandsupply.com Financing Available
5290 Hagedorn Hydra-Spread Spreader

Hydraulic push gate and end gate. Poly floor and side boards. Replaceable beater paddles. High ground clearance. Simple hydraulics. Infinite push gate speed adjustment. Sizes range from 285-550 Bu.
Ritchie Waterers
Most models on hand. Parts on hand.
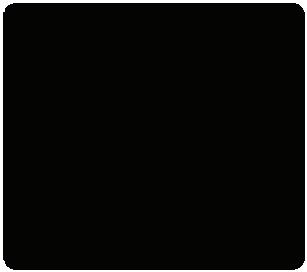
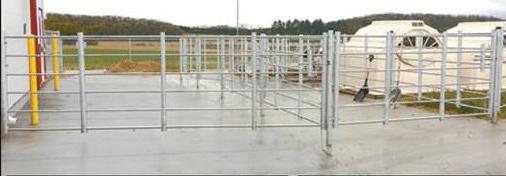
“We built our new ABS Global Calf Facility in the summer of 2016. This was the first time we utilized anything except steel at one of our facilities and it was a hard sell to the staff. However, after meeting with Travis at TJ’s Fencing in Harpers Ferry, and having him bring a gate home to show the staff, we were sold. We utilize more than 200 different sizes of gates, all purchased from TJ’s Fencing and installed by Cliff ’s Incorporated from Friesland, WI. The gating is holding up very well. We intend to expand our calf facility this summer and will definitely continue utilizing TJ’s Fencing for the gating.” - Jim Meronek, Health Assurance, Production and Supply Chain Director ABS Global, Inc DeForest, WI
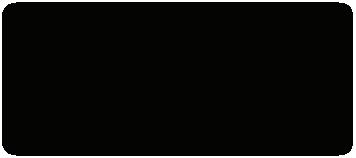
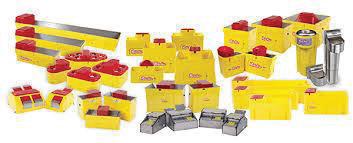