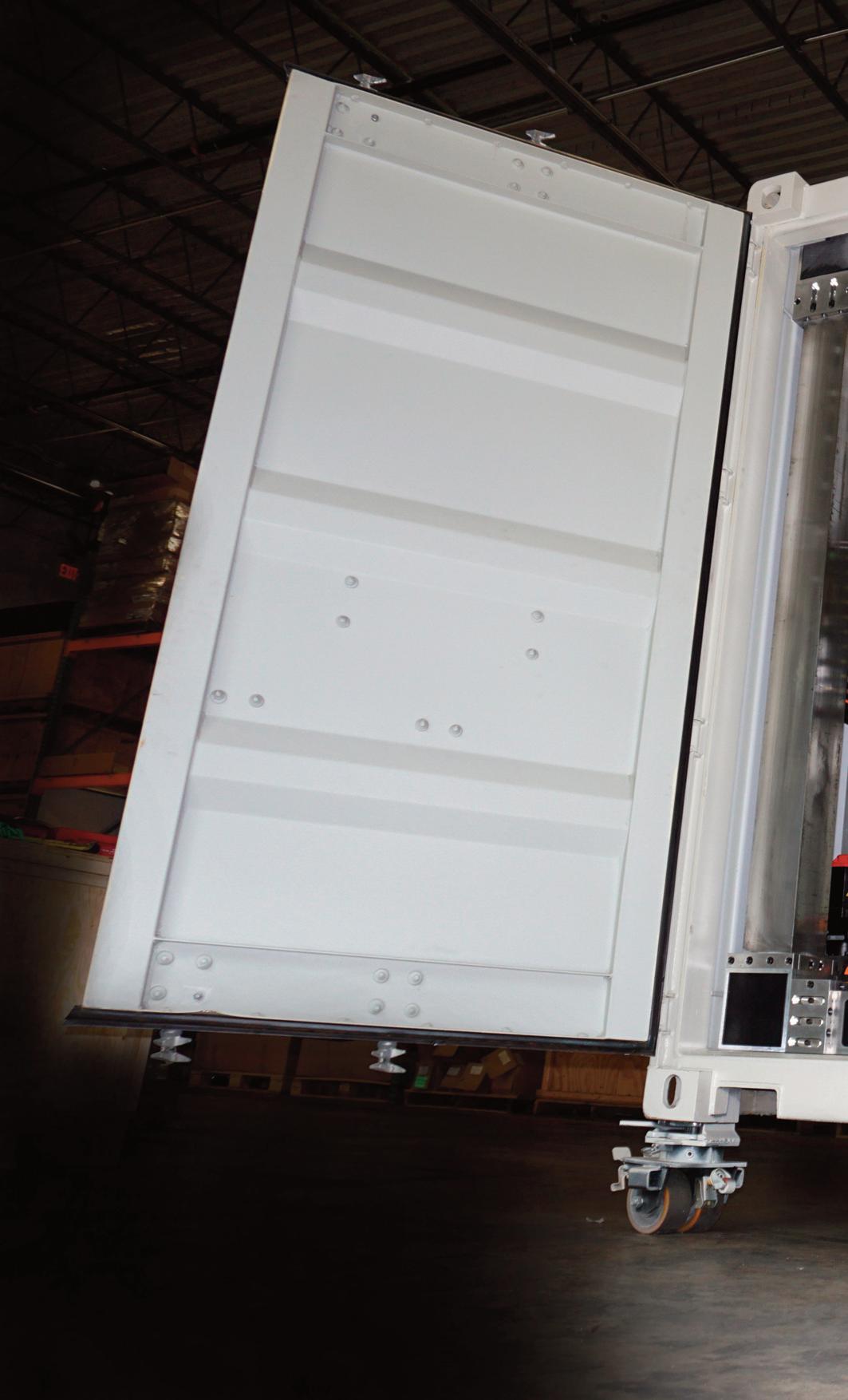
1 minute read
REVOLUTIONIZING READINESS
WARFIGHTERS FACE A MULTITUDE OF CHALLENGES AND OBSTACLES IN THE FIELD. SNOWBIRD TECHNOLOGIES IS ADDRESSING MISSIONREADINESS AND SUSTAINMENT WITH A PATENTED, MOBILE HYBRID MANUFACTURING SOLUTION.
Critical spare parts distribution is an immediate concern for defense forces around the globe. The fulfillment of repair or replacement parts for equipment remains a critical need in remote locations. As the global supply chain, shipping, and raw materials markets continue to fumble, fundamental entities such as defense forces are left vulnerable to operational downtime and security breaches when they aren’t able to efficiently maintain machinery. Long delays, wrong or missing parts, and inconsistency of material availability leave essential systems down or in need of repair, potentially weakening perimeters and leaving troops and operators in dangerous situations.
The Snowbird Additive Mobile Manufacturing platform (SAMM Tech) is a patented hybrid manufacturing system that revolutionizes parts procurement and logistics in the field. SAMM Tech provides an additive manufacturing system (3D printing) with subtractive manufacturing capabilities (milling and routing heads) to produce large format, metal or composite parts. The patented gantry platform is constructed inside a standard shipping container, allowing the platform to be shipped to any location in the world. This concept is patented by US Patent No. 10,434,712 B1.
Mobile, hybrid manufacturing allows for any component to be produced in any location. If a part needs to be replaced immediately, a new one can be printed and machined on location or nearby, avoiding the challenges of navigating supply chain and logistics shortcomings.
SAMM Tech differentiates itself from other additive manufacturing systems in several ways. First, it is designed for large format parts. The standard model features a 10-ft. x 5-ft. print bed, manufacturing parts as large as 250 cubic feet onsite. Second, SAMM Tech can produce in both metal and composite materials, while many systems focus on composites only. Lastly, the SAMM Tech system uses standard weld wire for metal production and inert gas to run the system, reducing an excess of consumable parts.
SAMM Tech challenges the way that parts make it to the operators in the field, minimizing downtime and optimizing fleet and troop readiness.
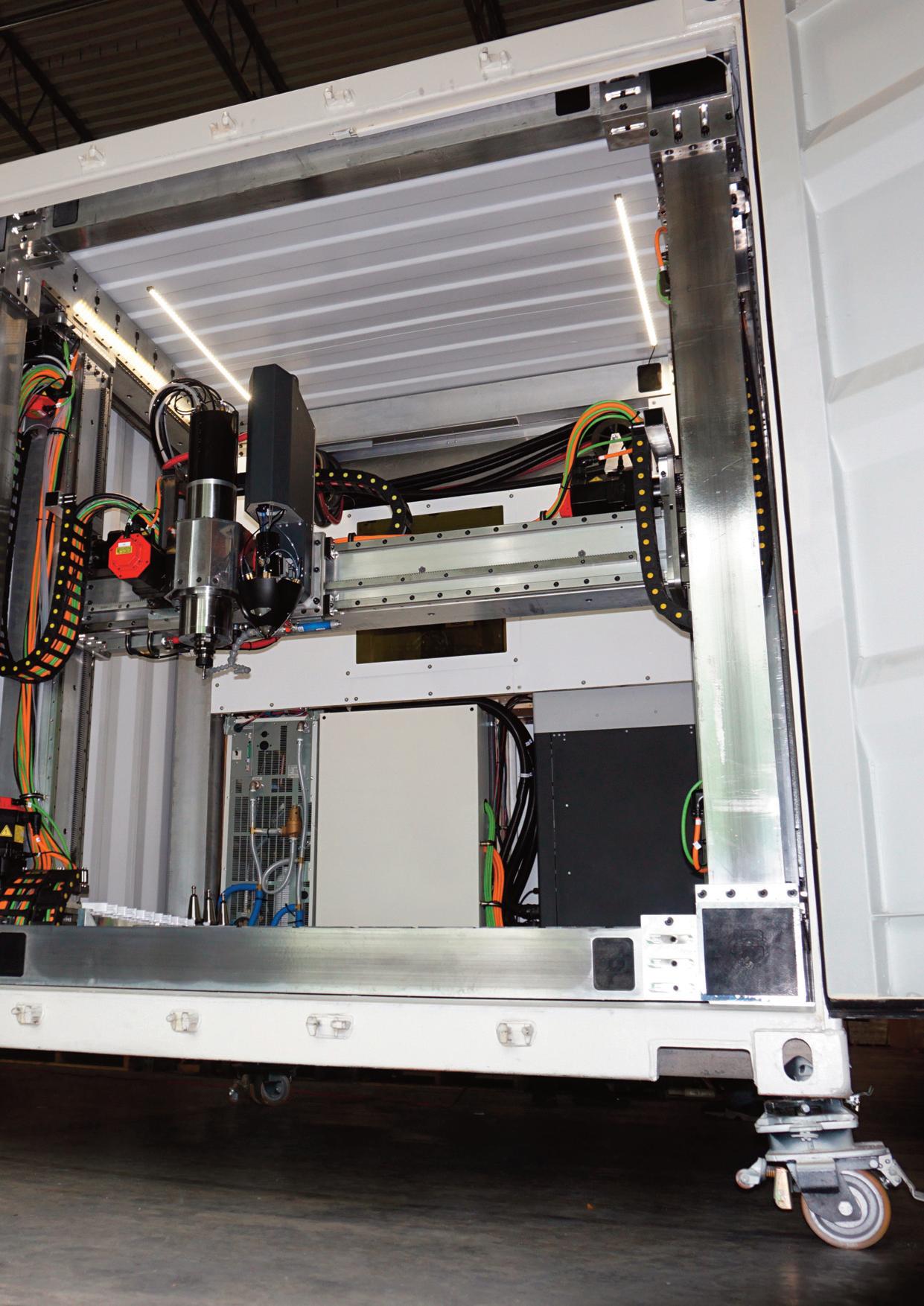