
29 minute read
Green Logistics and the Food Chain
The staff is knowledgable and “ accessible by email and by phone. Lansdale has helped us to grow our local business, with excellent shipping and delivery Our inventory of merchandise is maintained at the highest standards. ” -- Importer and Distributor of Tomato Products procedures. The staff is knowledgable and accessible by email and by phone. Our inventory of merchandise is maintained at the highest standards. -- Importer and Distributor of Tomato Products ” Lansdale has helped us to grow our local business, with excellent shipping and delivery procedures. The staff is knowledgable and accessible by email and by phone. Our inventory of merchandise is maintained at the highest standards. ” “ for the industry to have confidence in fully automated designs, which in turn makes automation as a whole a harder sell. He says, “I believe that our industry needs to continue to focus on automating point A to point B and avoid the point A to point Z tasks.”
Transitioning Food Companies To Warehouses of the Future Butterfield says cost and timing are two of the biggest challenges food companies face when considering a transition of traditional operations to include more robotics and automation. He says depending on the scope of the automation, projects can be three to five times the cost of traditional warehouse construction. And, those projects can take 20 or more months to complete. He says hiring and training offer a lot of new skill sets and positions in a warehouse, but far fewer positions than required in a conventional warehouse.” He says when pitching to company leadership, promote sustainability in servicing customers long term as a major benefit from making the transition. “Labor has been and continues to be a challenge to fill traditional positions in frozen environments,” Butterfield says. “Automated solutions offer the ability to ship and receive product with 60+ percent less labor. Power savings, less land needed to purchase due to building height…the ability to put 2-3 times more pallet positions on the same footprint, reduction of injuries, and faster more reliable carrier turn times all aid in making the industry better and sustainable for the future.” According to Kukal, companies no longer have a choice but to make the transition to more automated warehouse operations. “The move to automation is going to be a make-orbreak decision for multitudes of companies operating in our industry today,” Kukal says. “Most company leadership knows this and getting buy-in from Senior/C suite leadership is not difficult…as long as your ROI makes sense.” Kukal and Butterfield both want to see more reliable solutions get to the market quicker. Kukal says he looks forward to mobile case picking, lumping, unloading, and loading technology catching up to the rest of the warehouse technologies that exist today.
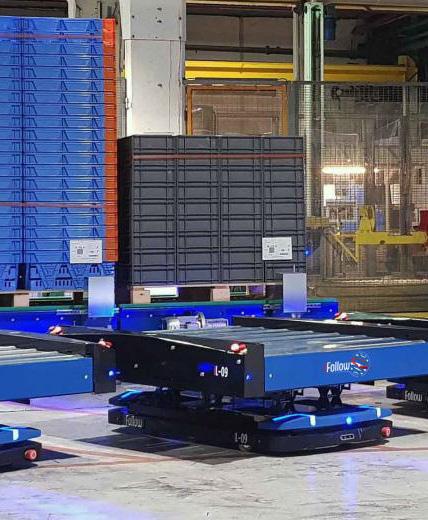
Located within the northeast -- Importer and Distributor of Tomato Products
MegalopolIs that runs from Located within the northeast MegalopolIs that runs from Located within the northeast
Washington to Boston
- Rail Served Daily by CSX and PNR - Diverse Material Handling Equipment - AIB Certification “ - Rail Served Daily by CSX and PNR - Diverse Material Handling Equipment - AIB Certification - ISO 9001:2018 and ISO 200005 - An Asset Based Corporation Lansdale has helped us to grow our local business, with excellent shipping and delivery procedures. The staff is knowledgable and accessible by email and by - Rail Served Daily by CSX and PNR - Diverse Material Handling Equipment - AIB Certification - ISO 9001:2018 and ISO 200005 - An Asset Based Corporation - - Five Locations between Allentown phone.Five Locations between Allentown - ISO 9001:2018 and ISO 200005 & PhiladelphiaOur inventory of merchandise & Philadelphia ”- An Asset Based Corporation - Five Locations between Allentown - WMS and RF Technology - Licensed to Store and Transport Alcoholic Beverages is maintained at the highest standards. -- Importer and Distributor of Tomato Products - WMS and RF Technology - Licensed to Store and Transport Alcoholic Beverages & Philadelphia Located within the northeast
MegalopolIs that runs from
- WMS and RF TechnologyWashington to Boston - Rail Served Daily by CSX and PNR - Licensed to Store and Transport - Diverse Material Handling Equipment Alcoholic Beverages Dave Emery 215 855 8460 ext. 205 dave.emery@lansdalewarehouse.com - AIB Certification - ISO 9001:2018 and ISO 200005 www.lansdalewarehouse.com Dave Emery 215 855 8460 ext. 205 - An Asset Based Corporation dave.emery@lansdalewarehouse.com - Five Locations between Allentown www.lansdalewarehouse.com & Philadelphia - WMS and RF Technology - Licensed to Store and Transport Alcoholic Beverages 44 | FOOD CHAIN DIGEST • EDITION 3 • 2022

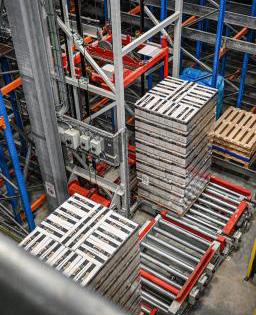
TRUCKING • WORTHINGTON, MN

Refrigeration SPECIALISTS
Redefining your refrigerated shipment experience.
Our fleet of refrigerated trailers can handle your frozen and refrigerated freight at the temperature you need. State-of-the-art refrigerated trailers. Rest assured your load will be delivered by the safest, best maintained and modern equipment in the industry.
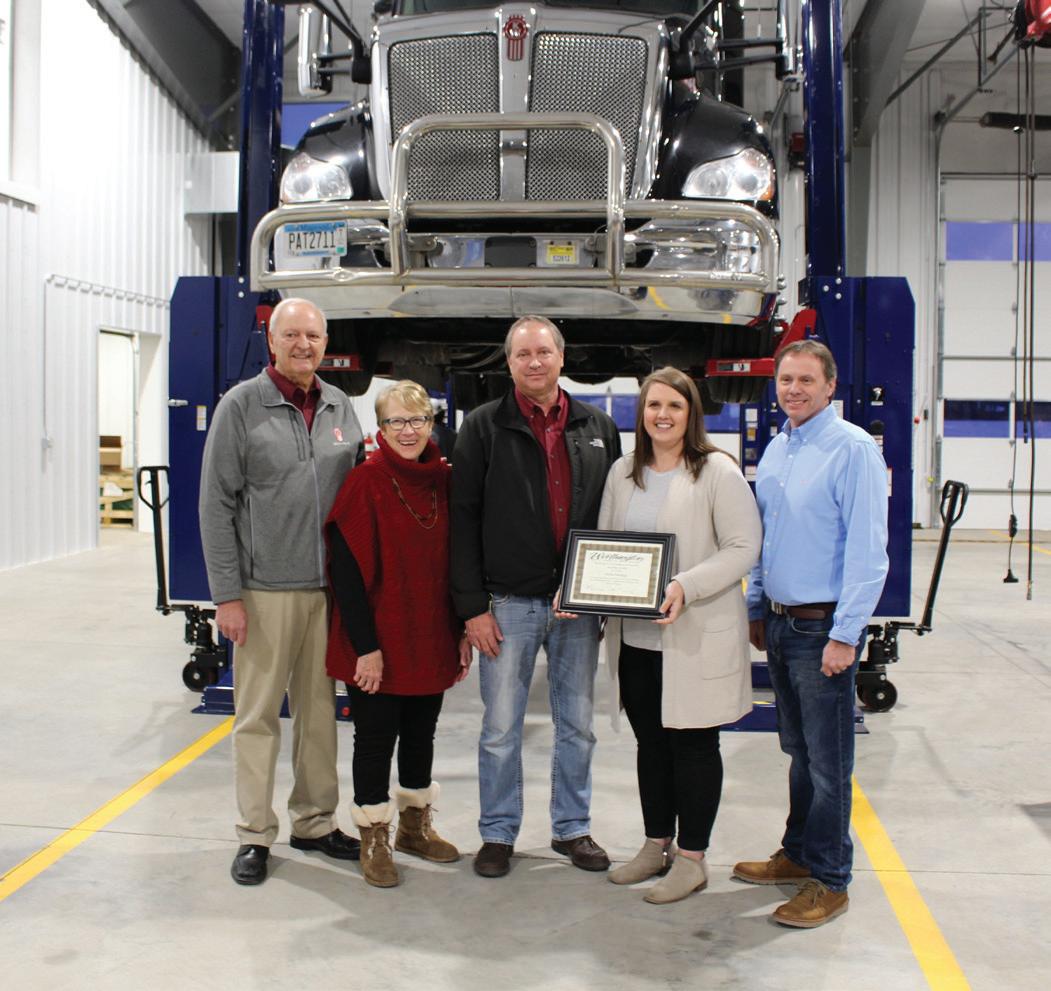
SPONSORED CONTENT Maximizing Truck Productivity in a World of Shortages
A significant number of market challenges are creating inefficiencies in supply chains and giving food shippers major headaches: a weak economy, rising inflation, volatile fuel prices, the driver shortage, and port congestion, to name a few. In particular, shortages in these areas are presenting significant challenges to those in the food industry: Labor Shortages. The Great Resignation has created a major vacuum in the workforce, and ultimately is creating volatile supply and demand in the food chain – from manufacturing and supply chain to logistics, warehousing and transportation. Truck and Railcar Shortages. Freight shipping delays, lower truck production, a severe shortage in truck drivers and available crews in rail yards are all factors creating a significant void in capacity. Ports Unable to Unload. North American ports are clogged with containerships as importers jockey for spots in ports in the United States and Canada – ultimately hitting deficits in all operations. Increasing Transportation and Fuel Costs. Historically approximately one-third of all supply chain costs involve transportation. A faltering global economy is exponentially increasing transportation-related costs.
The Opportunity: Unused Capacity in Trailers, Containers With these shortages in mind, it’s now critical that food shippers and their partners maximize the capacity and productivity of their trailers or containers – whether it directly involves their private fleets or equipment they’re using through their for-hire carriers. How big is the problem of unused capacity? For example, recent estimates typically place empty miles around 20 percent, but for the most familiar type of interstate freight – heavy trucks with box trailers or containers - empty miles are substantially higher, says Charles Kiolbasa, Chief Executive Officer of CCT Shipping Frames. “And while unused capacity in partially unfilled trailers or containers are not closely monitored, there’s clearly a significant opportunity to increase efficiencies and save on transportation costs if more concentrated efforts were placed on full space utilization,” says Kiolbasa. Because let’s face it: Unused capacity over-the-road, on rail, or over the ocean can lead to inefficiencies and higher costs – as well as more damage to products and materials in-transit due to extra shifting. Another opportunity to increase productivity is to proactively stage freight in the dock area to minimize dwell time, says Kiolbasa: “When you do this, you can ‘load and go’ and get the driver quickly on their way.” Kiolbasa recommends that shippers and their providers be more proactive and strategic in “building their shipments” and staging their freight. He says there are opportunities to accomplish this in several areas: • Engage the appropriate operations, sales and customer service teams to collaborate on creating efficient sales and fulfillment processes • Invest in the right order fulfillment and load planning software to effectively manage the entire order process • Lastly, invest in technologies and equipment that maximize your trailer and capacity. For example, CCT Shipping Frames manufactures a patented shipping frame that maximizes freight efficiencies in a trailer or container and helps to minimize damage while loading, unloading, and in-transit. “Companies involved in the food chain – whether they be food shippers, carriers or providers – must look at ways to maximize truck productivity in this world of shortages.” For more information, visit www.CCTShippingFrames.com or call 630-441-7046.

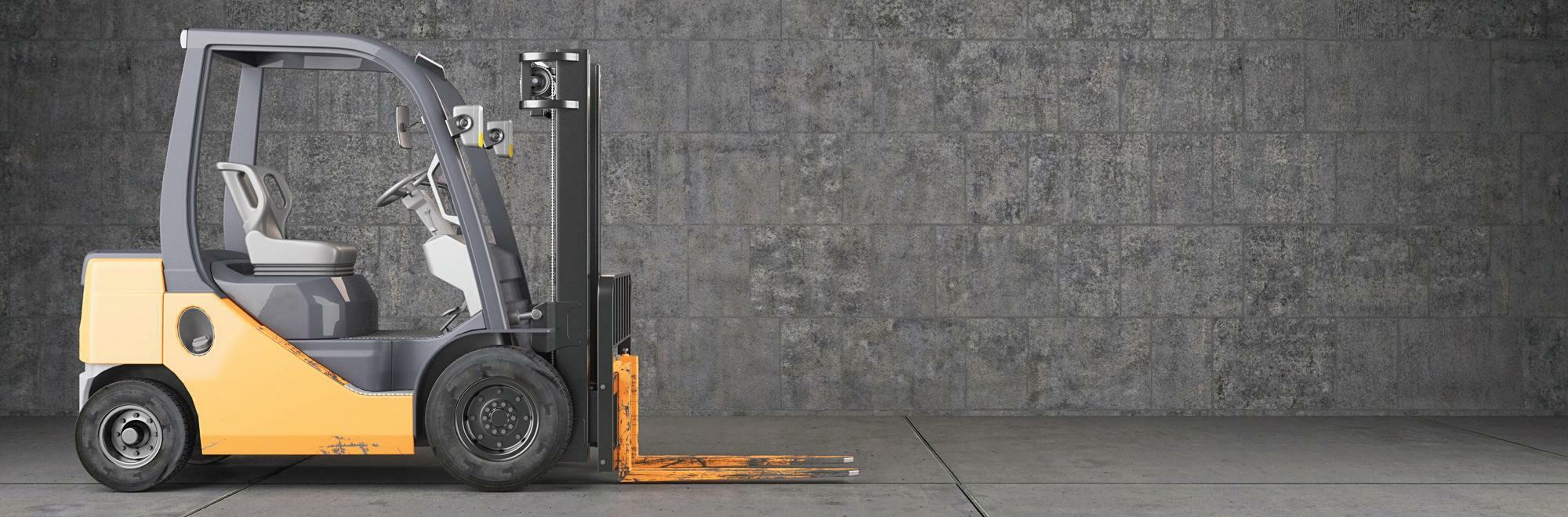
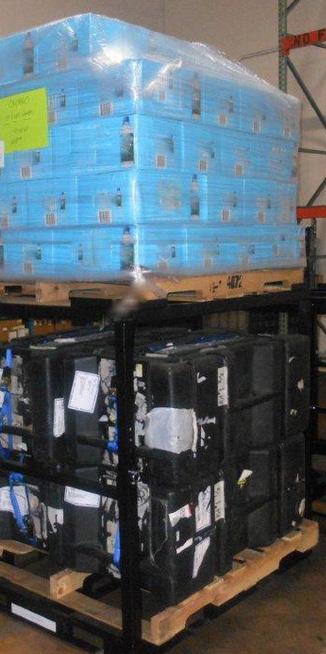
Stop the Squish.
Add capacity or temporary storage in your warehouses or DCs Maximize use of your trailers or containers and reduce damage risk
Increase equipment productivity and minimize product damage.
CCT’S Load Saver™ Shipping Frame allows you to stack and “cube out” your freight while protecting it from damage. Using a patented 2-deck frame design that’s sturdy and safe, this unique product can be customized to meet any shipping challenges you have. 4 4 4
Flexible and customized to individual challenges Purchase or rental options available Holds up to 4,000 lbs. (truck version) and 8,000 lbs. (rail version)
ShippingFrames.com | 630-441-7046
Food Shipper Supply Chain Visibility Report
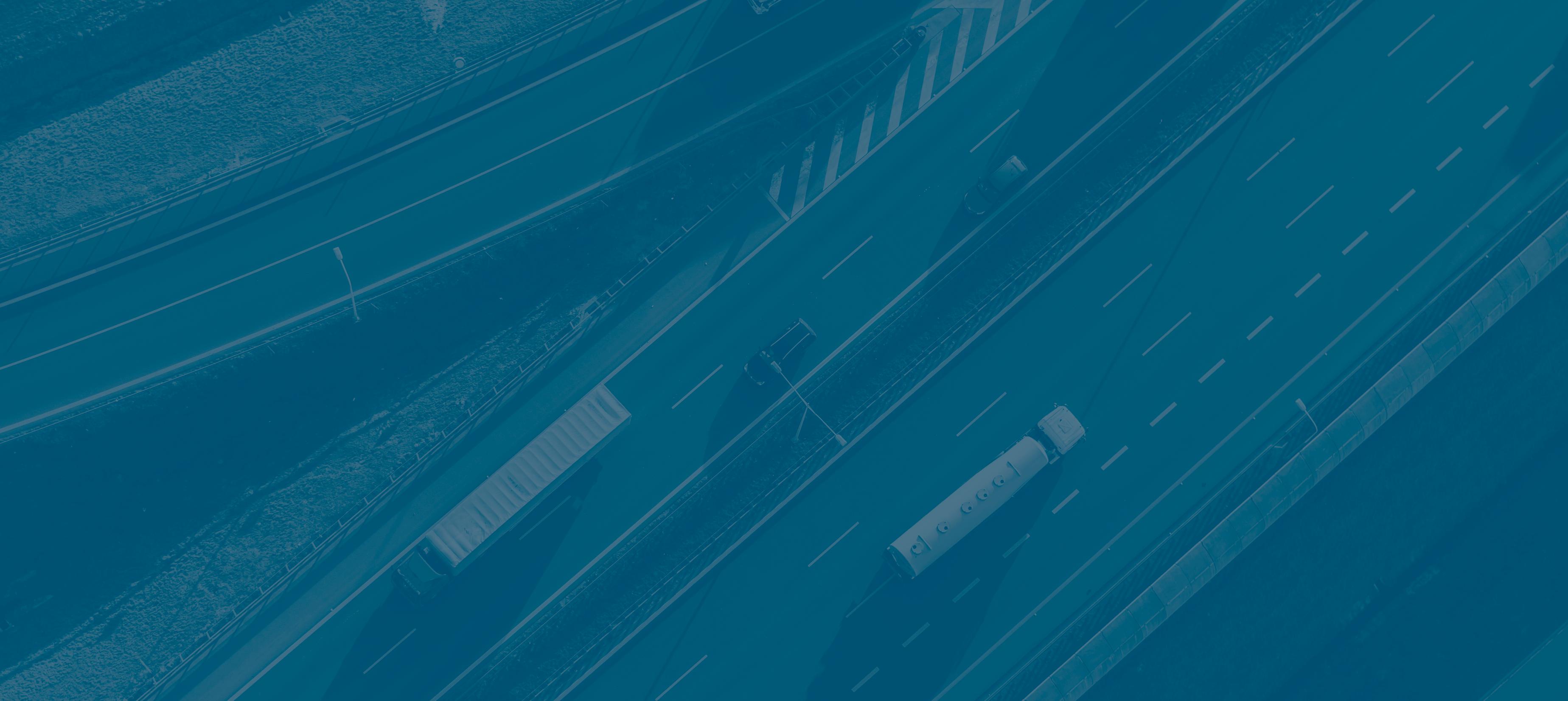
Actionable Insights from surveying more than 100 global supply chain professionals in the food industry
SPONSORED RESEARCH IN CONJUNCTION WITH FOOD SHIPPERS OF AMERICA BY:
More and more, food companies are seeking innovative ways to achieve end-to-end supply chain visibility. This enables them to track materials, good and products within the supply chain through a clear view of inventory and critical activities. Through food chain visibility, shippers can automate manual processes and access the information they need to make proactive decisions about their supply chain operations - improving efficiency and the customer experience. In addition, food chain visibility provides comprehensive insights on how your supply chain is functioning while ultimately reducing risk. Couple those insights with collections of user data and you can achieve a food chain that can be optimized to be as efficient as possible. FourKites recently teamed up with Food Shippers of America (FSA) to sponsor current research that sheds light on the most pressing challenges involving visibility of food shippers’ supply chains, opportunities to improve supply chain visibility, and ultimately best practices they have in place to achieve optimum visibility. FourKites is the world’s leading supply chain intelligence platform, delivering real-time visibility and execution for Fortune 500 companies and thirdparty logistics firms (3PLs) across 200 countries.
Key Trends in Food Chain Visibility
FourKites worked with FSA to deploy an online survey in June 2022 to invite participation by food manufacturers, retailers, distributors, 3PLs and freight brokers that control the transportation and distribution of materials and products in the supply chain. There were 118 participants in the survey, thus ensuring the research initiative is statistically valid. The survey qualified all participants to identify the type and size of company they represent, and to ensure they have responsibilities in supply chain, transportation, logistics and warehousing. The survey also asked critical questions to gain perspectives on their most pressing supply chain challenges, the most serious disruptors to their operations, the financial impact of product shortages, growth in e-commerce, the use of SKUs, and trends in customer loyalty. Participants were asked to identify up to three of their most pressing supply chain challenges they are currently facing. Primary challenges are Labor/Talent Management (49.4%), Transportation Capacity Issues (39.2%), Supply/Demand Planning and Disruptions (35.4%), Transportation Rate Issues (29.1%), and Warehousing Capacity Issues (15.2%).
Creating more visibility in your network can help to address challenges in labor and talent management by increasing productivity across your teams, drastically reducing inbound customer service calls and manual processes. Visibility can enable you to optimize planning and reduce inventory with critical real-time supplier data, while reducing your safety stock and improving your overall forecast accuracy. Participants also were asked to identify primary disruptors in the past three years, and these were their responses: COVID impact on labor (55.7%), over-the-road capacity (44.3%), Port Delays/Congestion (30.4%), and Changes in Consumer Behavior/Buying Patterns (21.5%). Food chain visibility can help to address labor challenges that have been exacerbated by the pandemic. In addition, for global food companies struggling with problems generated by port delays and congestion, they can benefit from ocean exception management paired with ocean visibility to ultimately lower transportation costs, reduce demurrage and detention fees, improve customer satisfaction, improve product availability, and generate less spoilage. Lastly, visibility enables food shippers to improve vendor relations and performance by collaborating in real-time with your suppliers and fulfillment teams, thus increasing your ability to react to changes in buyer behavior and purchasing patterns. Food chain visibility enables shippers to integrate their transportation, supply and warehouse management systems with order-level detail to ultimately break down silos and create new opportunities for supply chain optimization. Supply chain integration allows you to have a significant impact on avoiding product shortages, or a decline or miss in sales.
The Food Shipper Supply Chain Visibility Report also provide additional perspectives from food shippers, such as how they see grocery e-commerce changing in the coming months, to what degree they’re rationalizing SKUs, the state of customer loyalty, significant initiatives to reduce labor costs, and the impact that rising inflation and geopolitical uncertainty is having on food chains. To download a copy of the Food Shipper Supply Chain Visibility Report, visit www.foodshippers. org, click ‘Resources’ and go to ‘Whitepapers’.
100
80
60
40
20 BIGGEST CHALLENGES THE FOOD SHIPPING INDUSTRY FACES
0
Labor/Talent Management (49.4%) Transportation Capacity Issues (39.2%) Supply/Demand Planning and Disruptions (35.4%) Transportation Rate Issues (29.1%) Warehousing Capacity Issues (15.2%) 100
80
60
40 PRIMARY DISRUPTORS IN THE PAST 3 YEARS
COVID Impact on Labor (55.7%) Over-the-Road Capacity (44.3%) Port Delays/Congestion (30.4%) Changes in Consumer Behavior/ Buying Patterns (21.5%)
20
0
Technology Provides Visibility and Capacity
Food shippers are seeking ways to gain visibility into their supply chain to ultimately enhance their capacity. One freight brokerage offering efficient and innovative technology solutions to accomplish this goal is Edge Logistics. In fact, Edge Logistics has recently leveraged new technology for its top five shippers to enhance integration, participation, and performance management and visibility. “Capacity for customers allows SMB clients to access the carrier network that enterprise clients have been taking advantage of for some time,” says Will Kerr, President of Edge Logistics. “Most SMB shippers cannot access premium freight broker services because of the case costs involved for the broker. This leads the SMB shipper to a smaller broker who is more customer service and less performance focused. We have solved that problem for the SMB shipper, now they can have both.” In addition, Edge Logistics uses carrier scorecards as well as GPS visibility via API or online portal so that food shippers know exactly where their trucks are at all times and their anticipated delivery time, continues Kerr. “Our carrier onboarding enables us to vet every carrier on a variety of points while our GPS tracking gives food shippers full visibility every step of the carrier process.” For additional information, visit edgelogistics.com.
Will Kerr
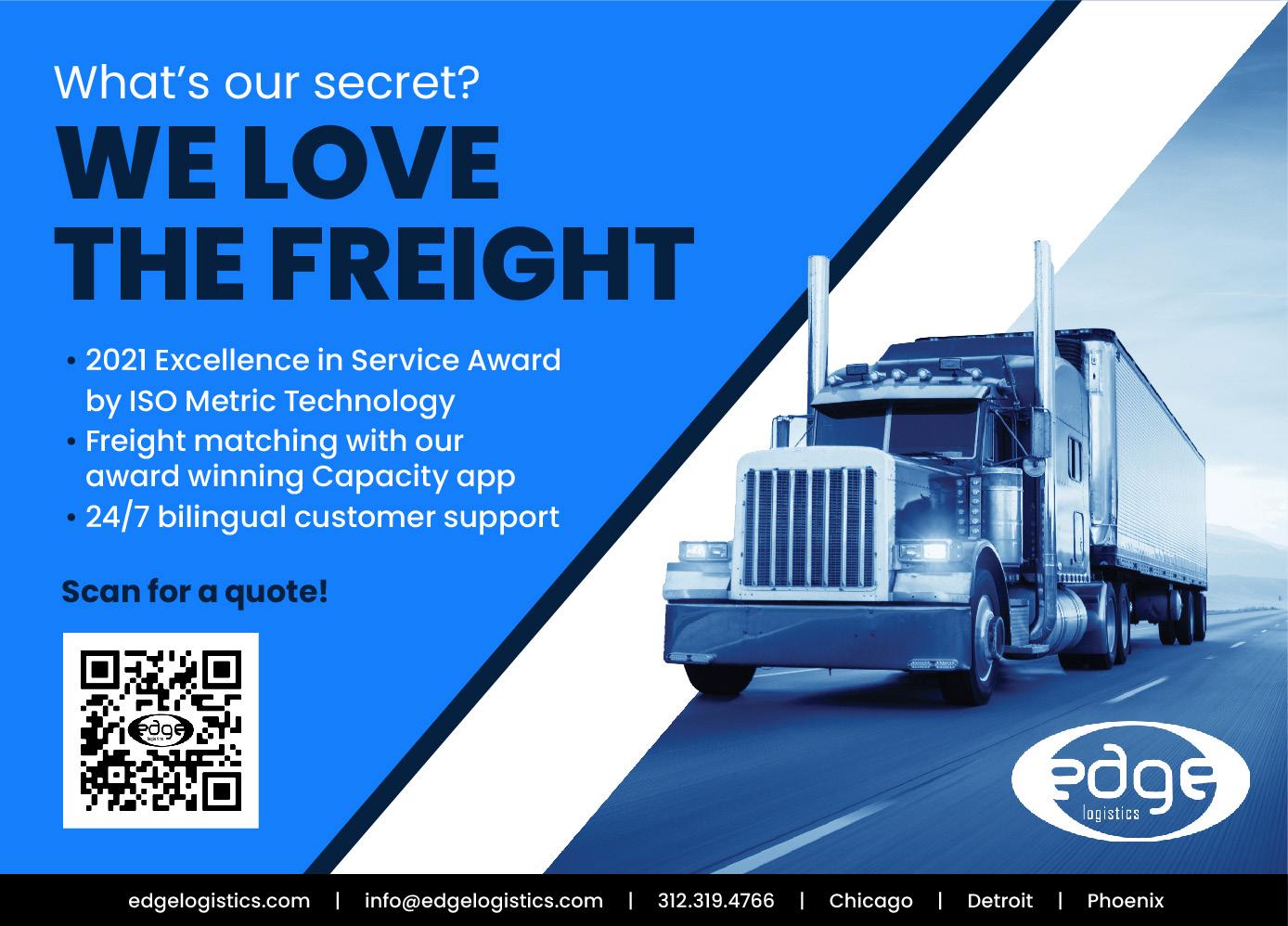
Relevant content where and when you need it.
Food Shippers of America gives you access to more market intelligence, best practices, and industry news on critical topics. You’ll find it all through four primary resources: • FoodShippers.org offers relevant, up-to-the-minute content. • Food Chain Digest leverages an editorial team with more than 100 years combined experience in transportation, logistics and supply chain. • Food For Thought features more relevant information, more often. • Social media channels provide comprehensive information designed specifically for and about food shippers. Make sure to follow us on LinkedIn (corporate page and discussion group), Facebook, Twitter, and Instagram!

Interested in advertising opportunities?
Download a 2022 Food Shippers Media Kit at FoodShippers.org or reach out to Cassidy Haley at cassidy@mindshare.bz or 952-442-8850 x215.
www.FoodShippers.org
Assembly Bill Five (AB5) is still upsetting independent contractors across the California trucking industry since its introduction in 2018. The restrictions it places on independent truck owner/operators has led several groups to protest against the law publicly and fight for their right to own their own businesses. What makes the AB test difficult for independent truck owner/operators to pass, what can be done to stay in compliance with AB5, and what’s on the horizon for independent trucking companies in California?
A Little Background The California Supreme Court issued an opinion known as the dynamics decision back in 2018, which eliminated the prior worker classification test and instituted the ABC test, according to Chris Shimoda, California Trucking Association (CTA) Senior Vice President of Government Affairs,The ABC test is a three-prong test with section B being the biggest hindrance, adding a significant challenge to owning an independent truck company in California. AB5 was introduced to the California Legislature in 2019 and was passed despite consistent pushback from the California Trucking Association and independent truck drivers. What makes the ABC test difficult?
Greg Feary, President and Managing Partner for Scopelitis Law Firm in Indiana, says AB5’s ABC test is “nearly impossible” to pass for a number of reasons.
“Part of the problem is that you have to, as the motor carrier, prove each of the three prongs,” he says. “If you don't prove any one of them, you lose and your contractor is deemed an employee.” Feary says the test needing to be met in totality is problem number one. The next issue is motor carriers having to prove that their contractor, who is an owner/operator with their own truck, is not in the same trade profession or occupation as the trucking company. “I would suspect in California that most California judges will be hard pressed to accept an argument that the truck driver is not in the usual course of business or in the same trade occupation or profession as the trucking company,” he said. “I think that the sticking combination of having to meet all three prongs, so that if you don't prove one you lose, and in particular that middle prong… I think that's where you find the test nearly impossible.”
What is the main goal behind AB5? Feary says the putative reason behind AB5 was to make sure all workers would receive all the employment benefits they deserved, though some may see it as a way to advance the cause of union groups to get more workers to join a union and pay dues. He says there are certain concepts of the ABC test that have applied to truck owner/operators in the past, but AB5 is what he calls “a fairly unique circumstance.”
“It’s somewhat of a ‘perfect storm’ of passing a law that potentially reduces the number of truck drivers in a state that needs every truck driver they can get. And even then, probably doesn't have enough,” he says.
Greg Feary
The Biggest Impact on Truck Drivers in California
Feary says AB5 causes an additional dip in the number of truck drivers and owner/operators across the state of California and beyond. “It's interstate trucking where there's substantial contact nexus with the state of California,” he says. “You've got…owner/operators who own their
WHAT IS CALIFORNIA AB5?
AB5 is California’s law that requires most industries to use the ABC Test to prove a worker is an independent contractor.
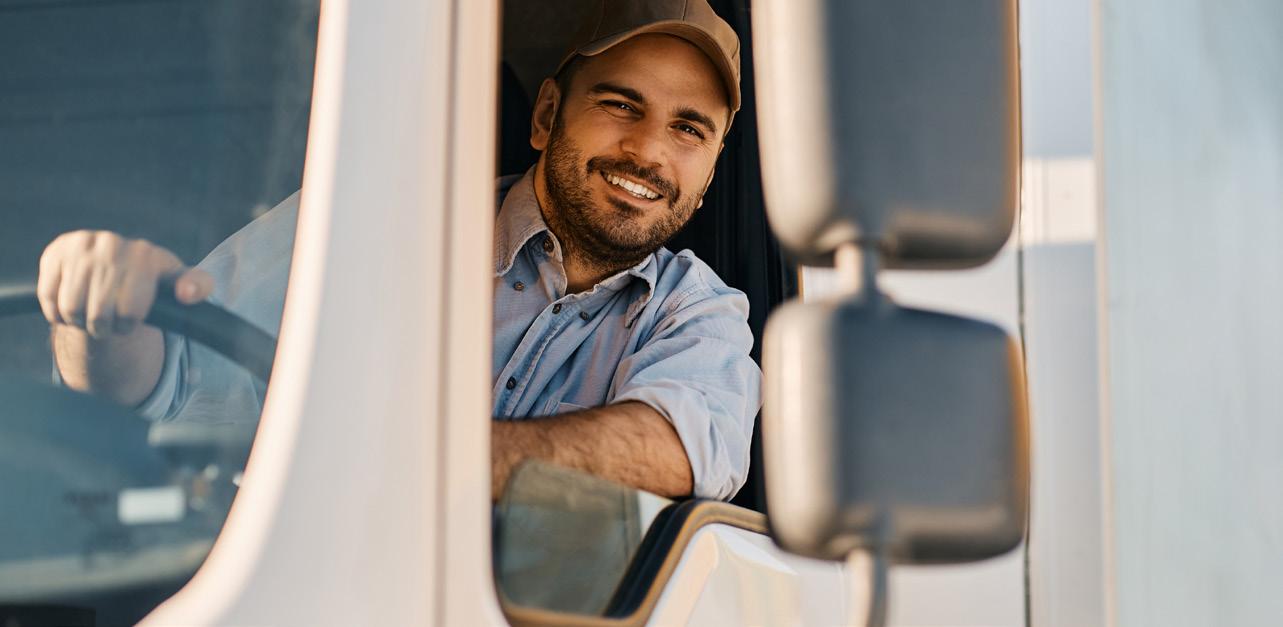
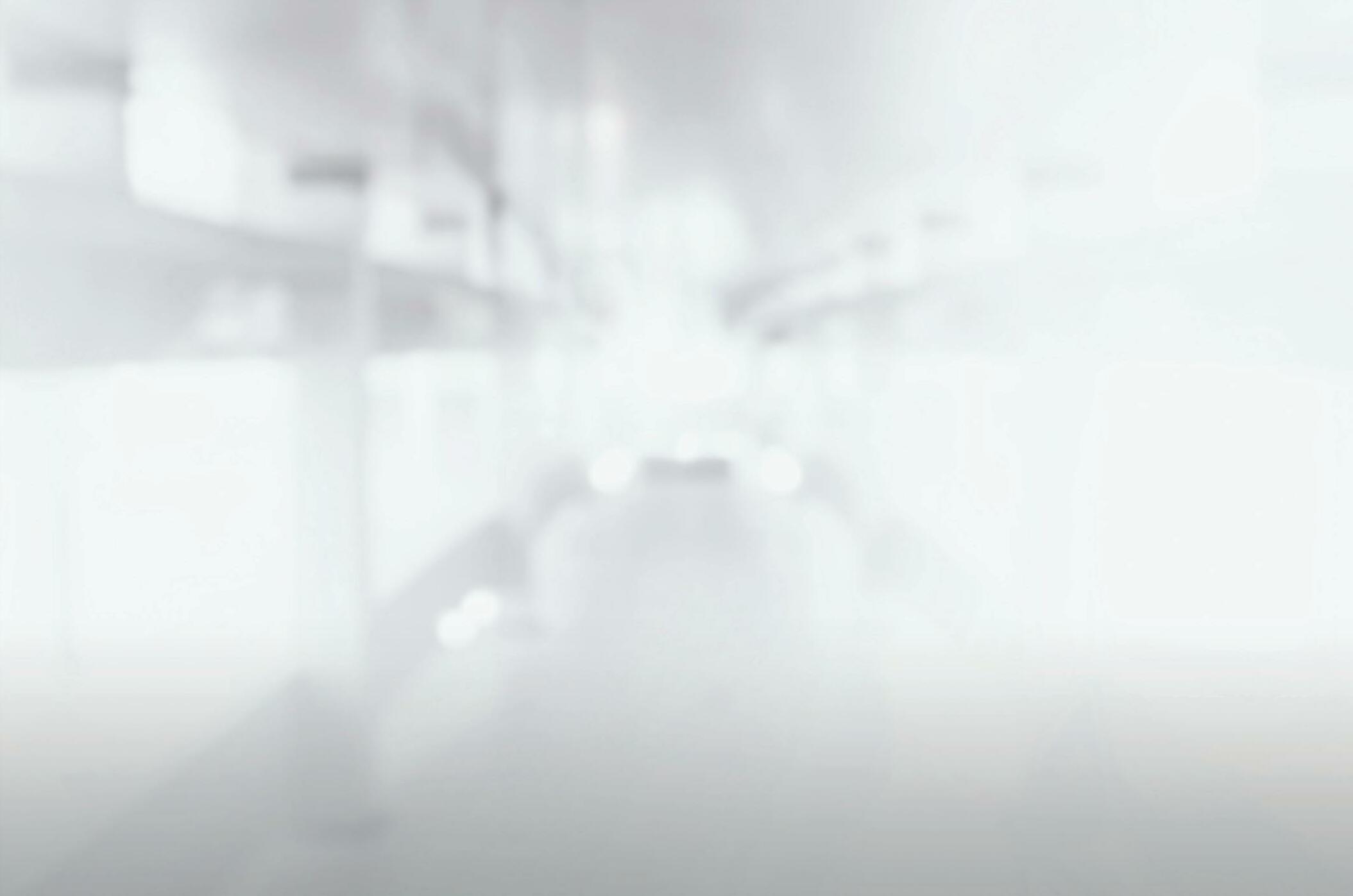
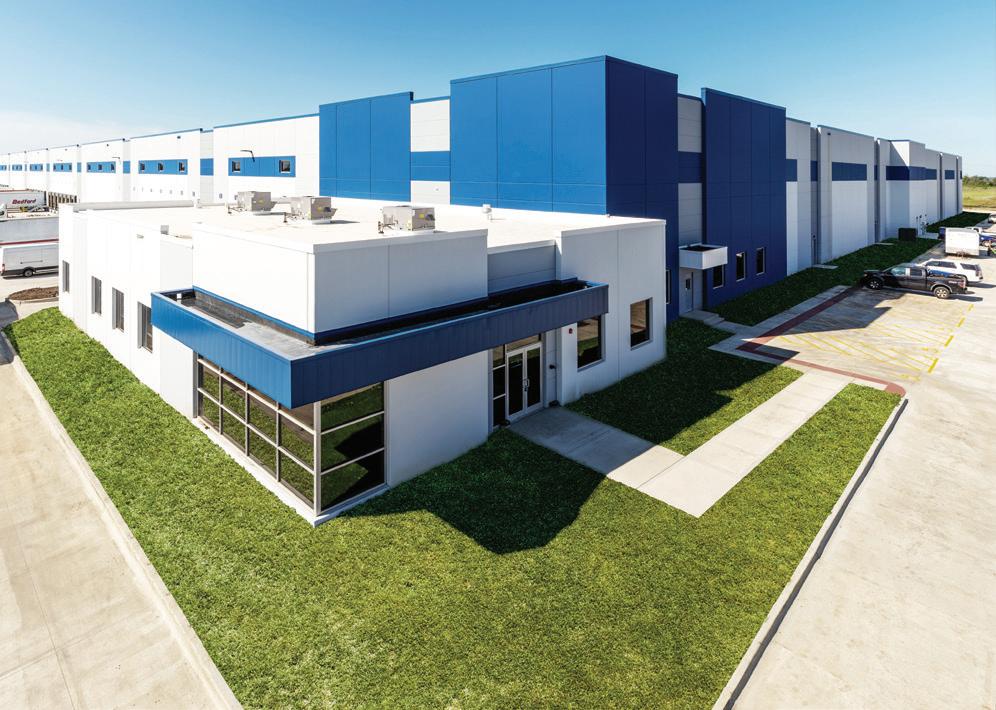
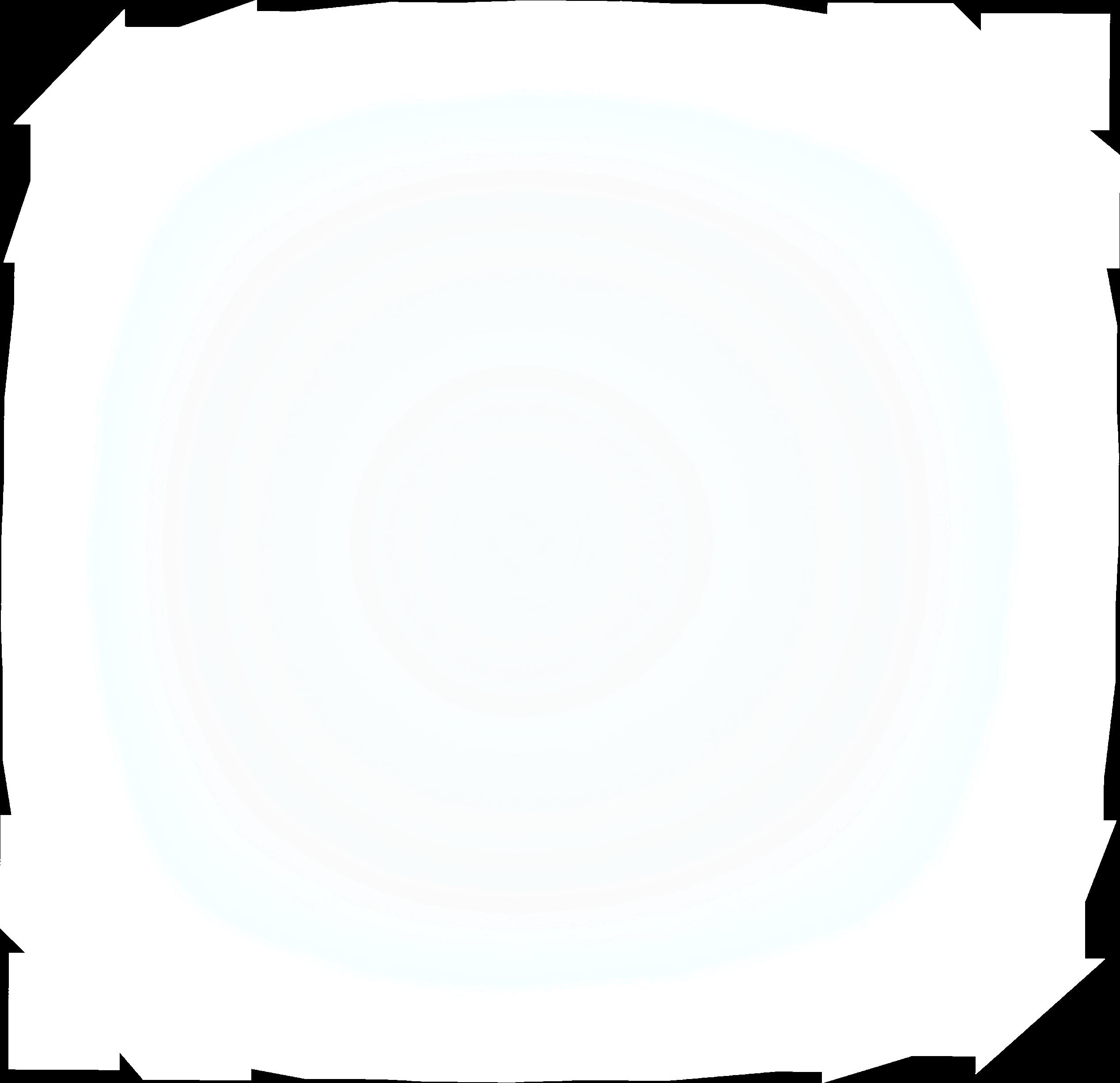
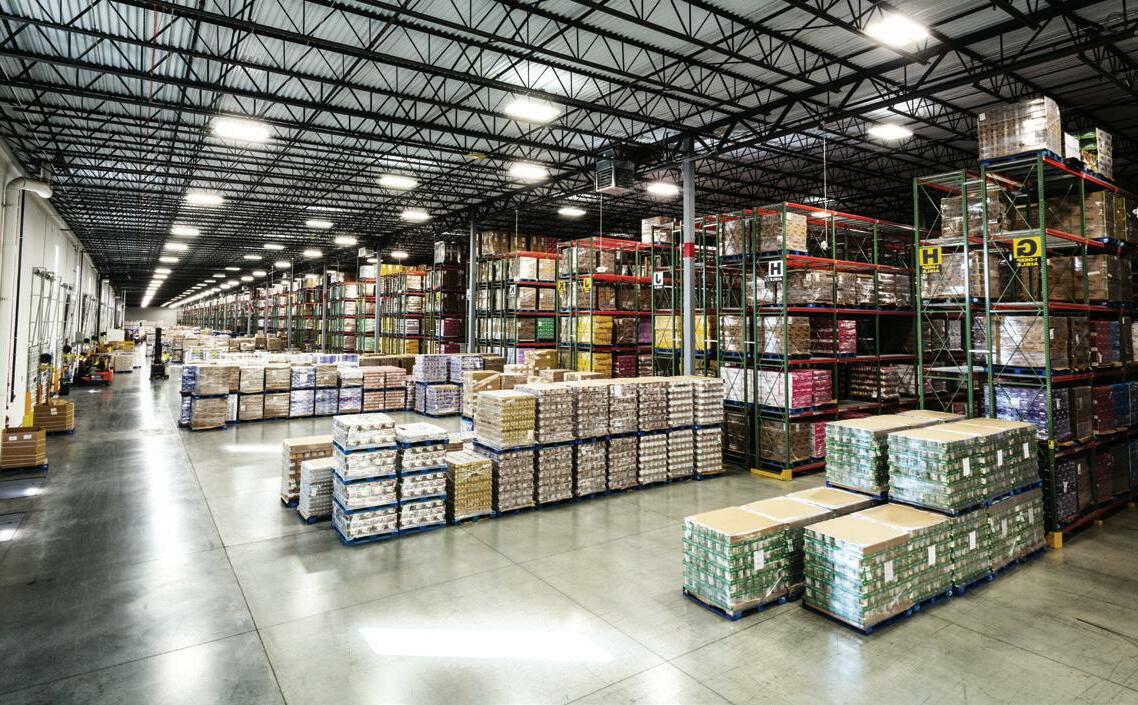
Combining Resources for Optimum Logistics Results
DTS TERMINALS BILLINGS, MT DENVER (AURORA), CO SALT LAKE CITY, UT
Our Network of Carriers, Cold Storage Facilities, and Logistics Coordinators are ready to work with all your Cold Chain Distribution needs.
• LTL Refrigerated, Chilled & Frozen • Nationwide Service • Single Point of Contact from Start to Finish – Ensures Excellent
Communication • Nationwide Network of Partner
Warehouses for Cross Dock &
Consolidation

www.dtslogistx.com 877-896-3460
• Tri Temp Reefers • Scheduled Routes to the U.S. &
Western Canada • Cross Dock, Redistribution,
Consolidation • Local Delivery Service to UT, CO, MT • Frozen, Chill, and Ambient Storage in
Billings, Denver (Aurora), and Salt Lake
City
www.dtsb.com 800-755-5855
• Celebrating Almost 40 Years in the
Transportation Industry • Nationwide/Canada LTL & TL Service • Chilled, Frozen, Dry & Multi-Temp
Available • Expedited Service / EDI Capability /
After Hours Contacts • Excellence in Third Party Logistics
www.freight-agency.com 800-676-6166
1640 Monad Road • Billings, Montana 59101-3200
own businesses, that maybe have an older truck. And maybe they're trying to decide whether to buy a new truck, reinvest in their business...go another three, four, or five years. And then this law is created and who they’ve been doing business with are saying, ‘Hey, we can't do business with you under the same model.’ So you're gonna have to go out and become your own motor carrier possibly…there's a lot more cost involved in what you're going to have to do.” On top of additional credentials and costs, some independent contractors that are close to retirement may choose to transition out of the industry early. Feary says AB5 is a tipping point for drivers that can lead them to move out of state.
Independent Contractors Staying in Compliance One way for an owner/operator to continue to run their own business is to obtain Federal Motor Carrier Authority, according to Feary. The process includes filing a lot of paperwork and studying compliance and safety regulations, which can seem daunting. He also says drivers should secure auto liability insurance as well. A $750,000 commercial trucking policy typically costs owner/operators about $20,000 per year. This could increase an owner/operator's business expenses by at least 20 percent.
The Latest Update with AB5 In August, the injunction on AB5 was lifted, allowing the law to be enforced in California against interstate trucking. Feary said the CTA will move forward at the Federal District Court in San Diego to seek another injunction. He says independent owner/operators should stay in communication with their motor carriers and gain an understanding of the carrier's plans on how to move forward.
LookingLooking forfor a a transportationtransportation providerprovider withwith overover 4040 yearsyears ofof experienceexperience providingproviding best-in-best-inclassclass service?service? ContactContact usus today!today!

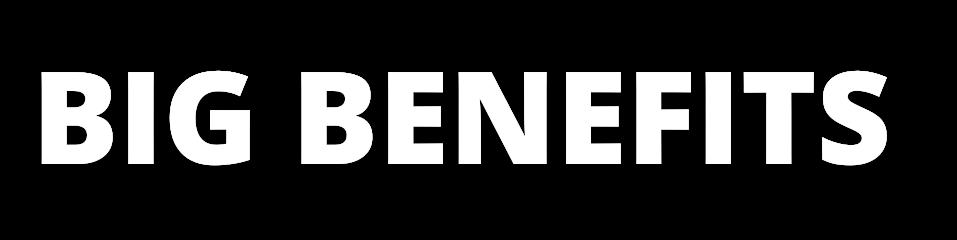

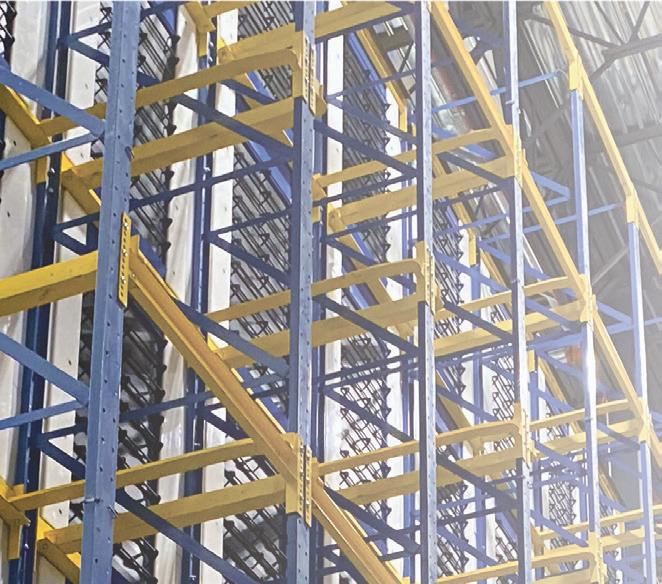
FSA Makes a Difference for Those in Need
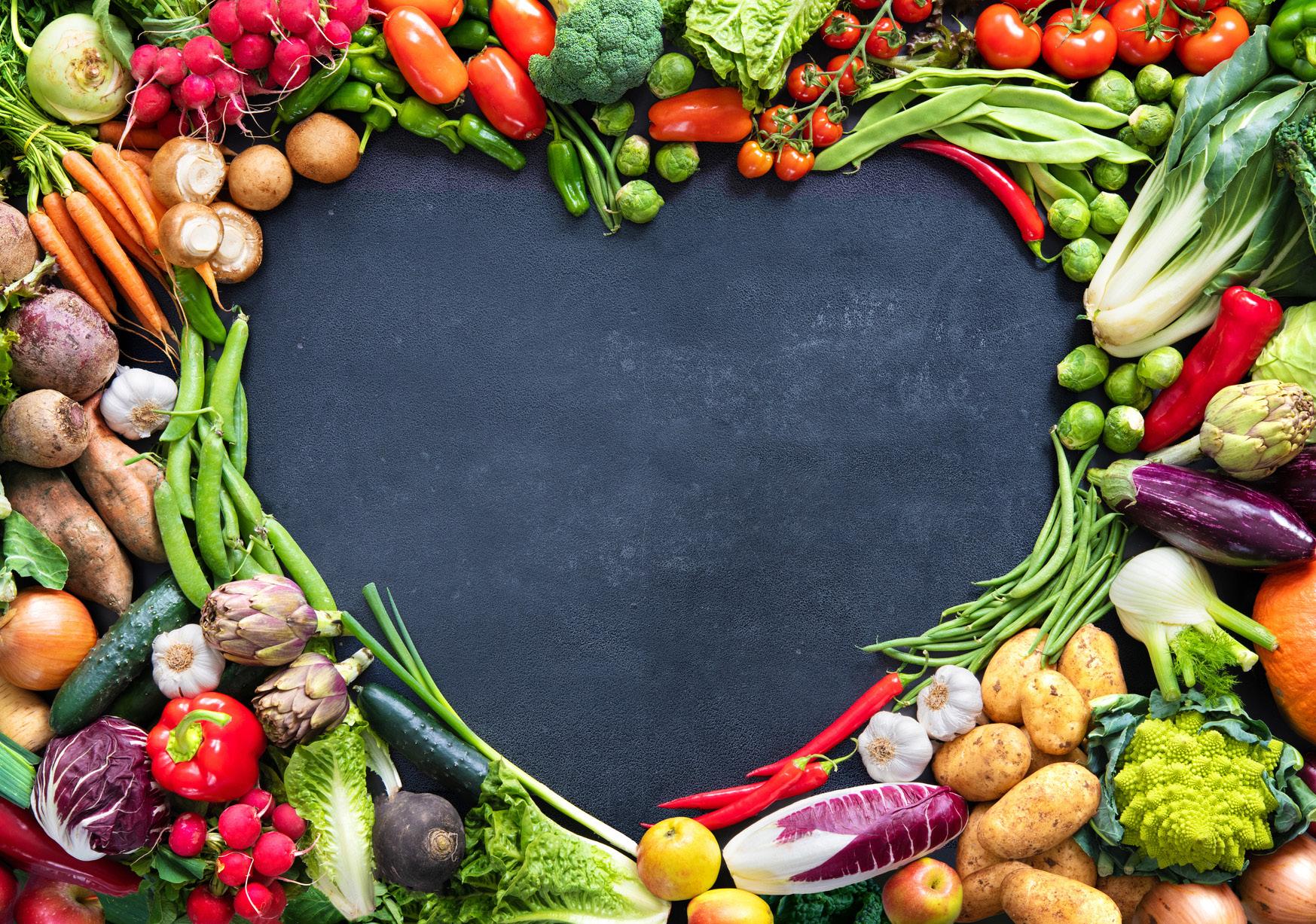
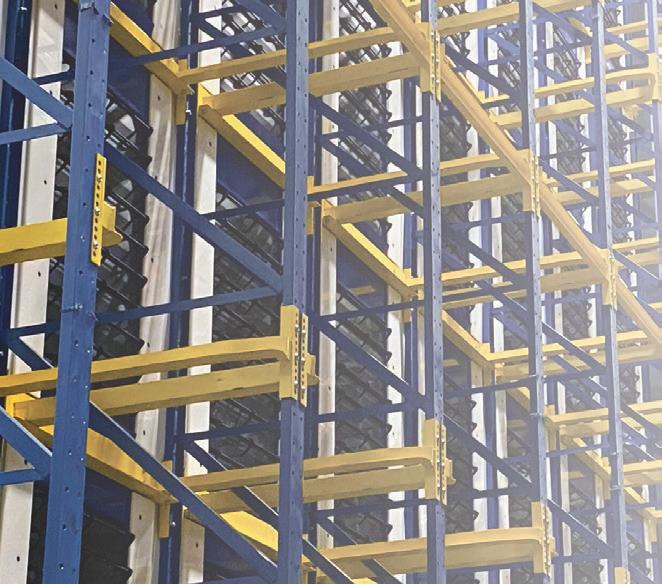
There are many recent world events that have placed extraordinary pressures on food chains. With all these pressures, Food Shippers of America (FSA) continues to support organizations that can have a significant impact on its members operations and success. In fact, in 2022 FSA has chosen to provide financial resources to the following organizations: American Logistics Aid Network: Logistics Compassion in Action This industry non-profit exists to provide supply chain assistance to disaster relief organizations and other non-profits. ALAN does this by bringing together the expertise and resources of the logistics industry with non-profit disaster relief organizations so that ALAN can help solve their most pressing supply chain challenges immediately after disasters strike. That way, help and op arrive sooner. Just as important, ALAN helps humanitarian organizations make every logistics dollar count. After all, studies show that up to 80 percent of their crisis spending goes to logistics. And of that, as much as 40 percent may be wasted simply because these organizations do not have access to the right supply chain equipment, knowledge or connections. In March, FSA renewed its ALAN Sustainer Sponsor status in 2022 –which continues a supportive relationship FSA has maintained with ALAN for more than a decade.
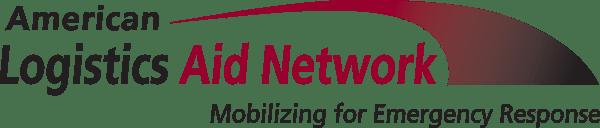
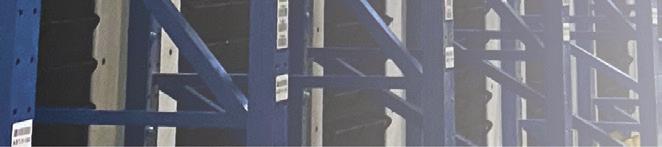
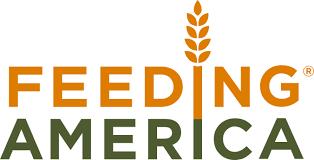
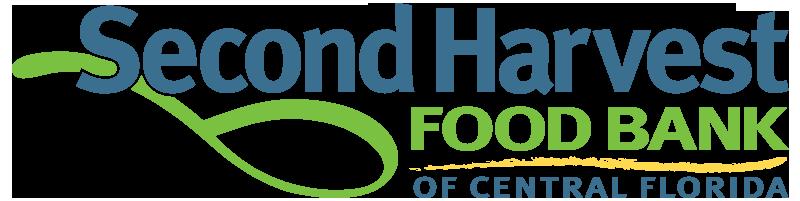
“In the past two years alone, ALAN has enabled the delivery and distribution of more than $10 million in relief supplies for hurricanes, floods, tornadoes, and the pandemic,” says ALAN Executive Director Kathy Fulton. “That’s only possible because of the support of organizations like Food Shippers of America, whose generous donation came at the start of a year already bustling with requests for disaster aid.”
For more information, visit alanaid.org.
Feeding America: Working Together to End Hunger
In a country that wastes billions of pounds of food each year, it’s almost shocking that anyone in America can go hungry. Yet every day there are millions of children and adults who do not get the meals they need to thrive. Feeding America is the largest domestic hunger-relief organization in the U.S. – and has a natural tie-in to the food industry. For this reason, in 2022 FSA has made a substantial financial commitment to support Feeding America. Thanks to the donation by FSA as well as thousands of other businesses, government organizations, and individual Americans, the Feeding America network of food banks, pantries and meal programs serve virtually every community in the THE FEEDING AMERICA NETWORK OF FOOD BANKS, PANTRIES AND MEAL PROGRAMS SERVE VIRTUALLY EVERY COMMUNITY IN THE UNITED STATES – 40 MILLION PEOPLE, INCLUDING 12 MILLION CHILDREN AND 7 MILLION SENIORS.
20,000+ QFR pallet positions installed and the qfr zone® is still the most efficient blast freezing solution ever!

• pallet fit™ door fits any pallet height • reduces labor • works with full, partial, or single layer pallets • no more need for plug pallets, zone can run with one or multiple empty pallet positions • increased airflow • more flexible • more efficient • more $aving$
9009 Coldwater Road Fort Wayne, IN 46825 (260) 490-3000 • www.tippmanngroup.com
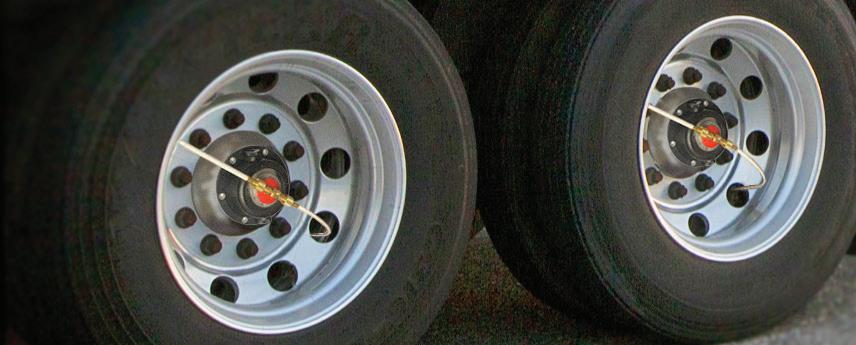
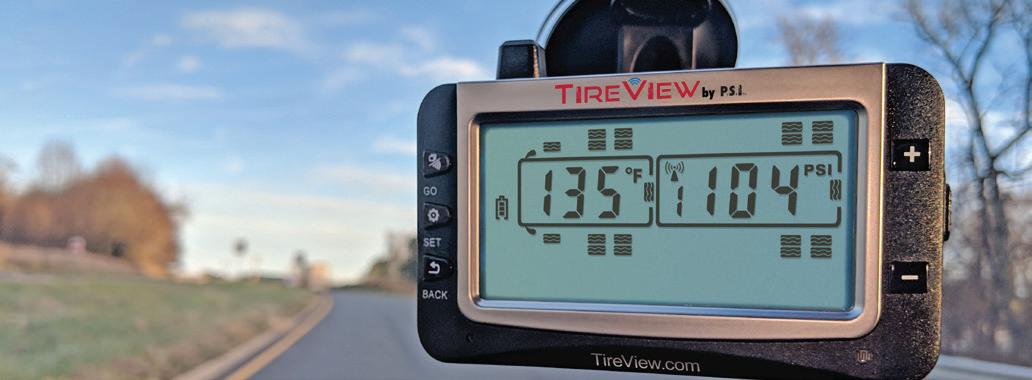
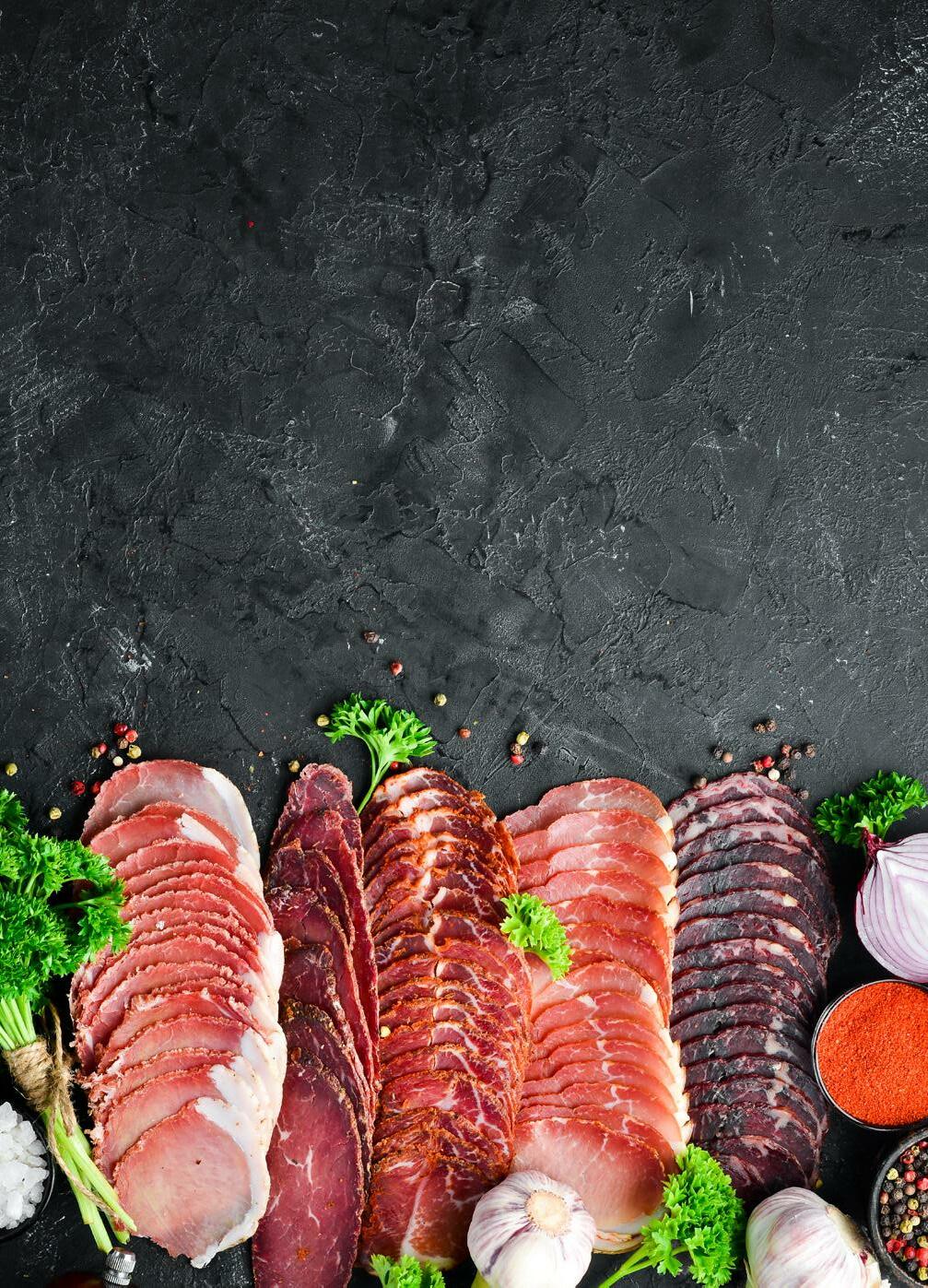
Open platform data analytics can integrate with your telematics provider.
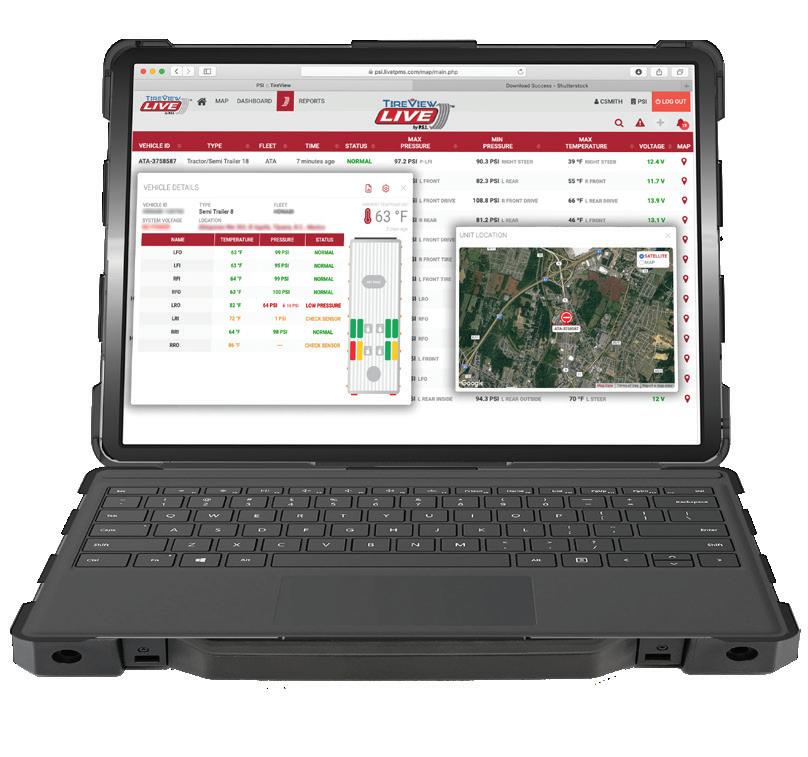
TIRE. INTELLIGENCE. DELIVERED.
The Global Leader in Tire Inflation SINCE 1993
(210) 222-1926 | www.PSItireinflation.com
© 2022 Pressure Systems International, Inc. A Clarience Technologies Company. Outstanding food logistics broker
FOOD GRADE REFRIGERATED | DRY TRUCKLOAD | NATIONAL NETWORK EXCEPTIONAL CUSTOMER SERVICE
FoodShippers Ad_PSI 2022 Edition 3-Rev1.indd 1 9/15/22 4:25 AM
Driven by Values
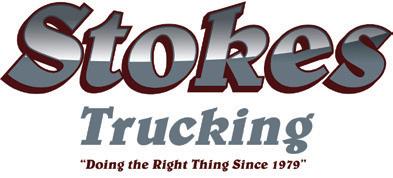
Safety, Sustainability, Driver Satisfaction, Relationships
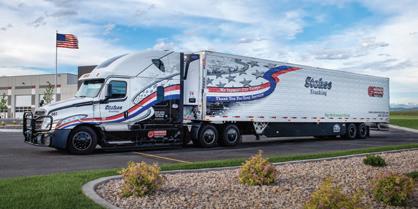
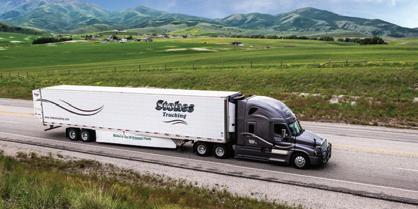

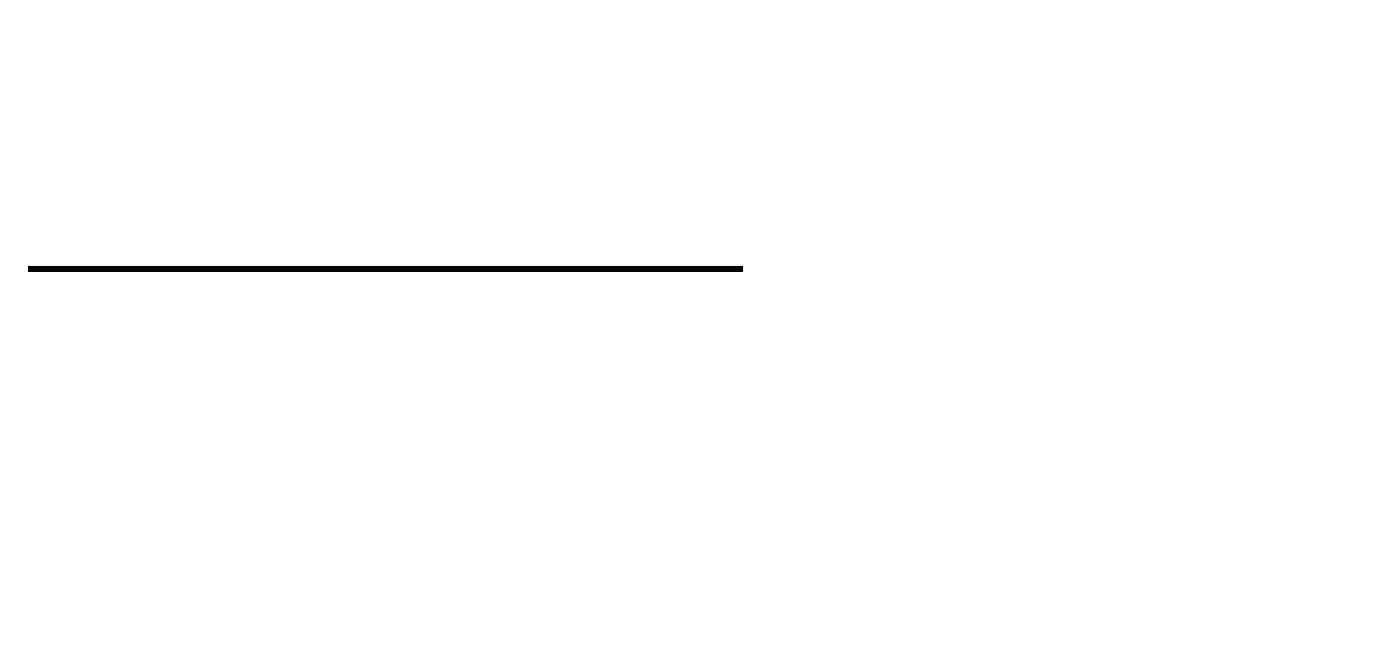

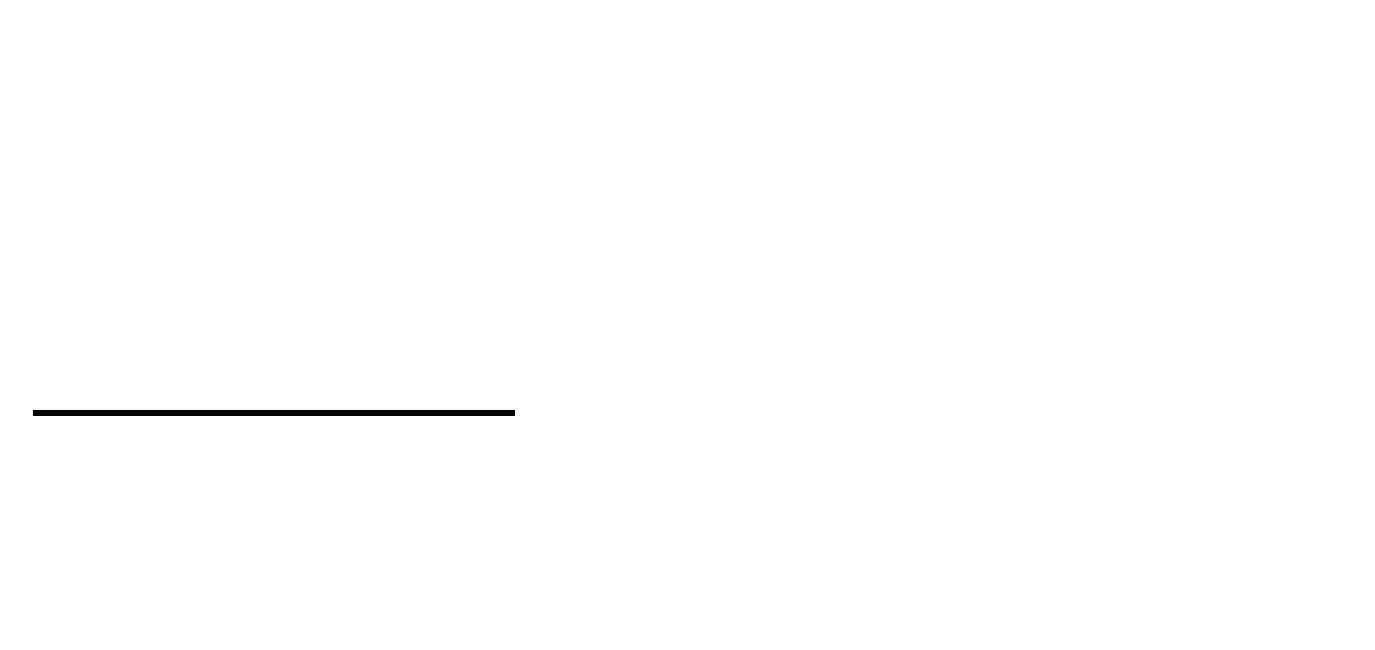
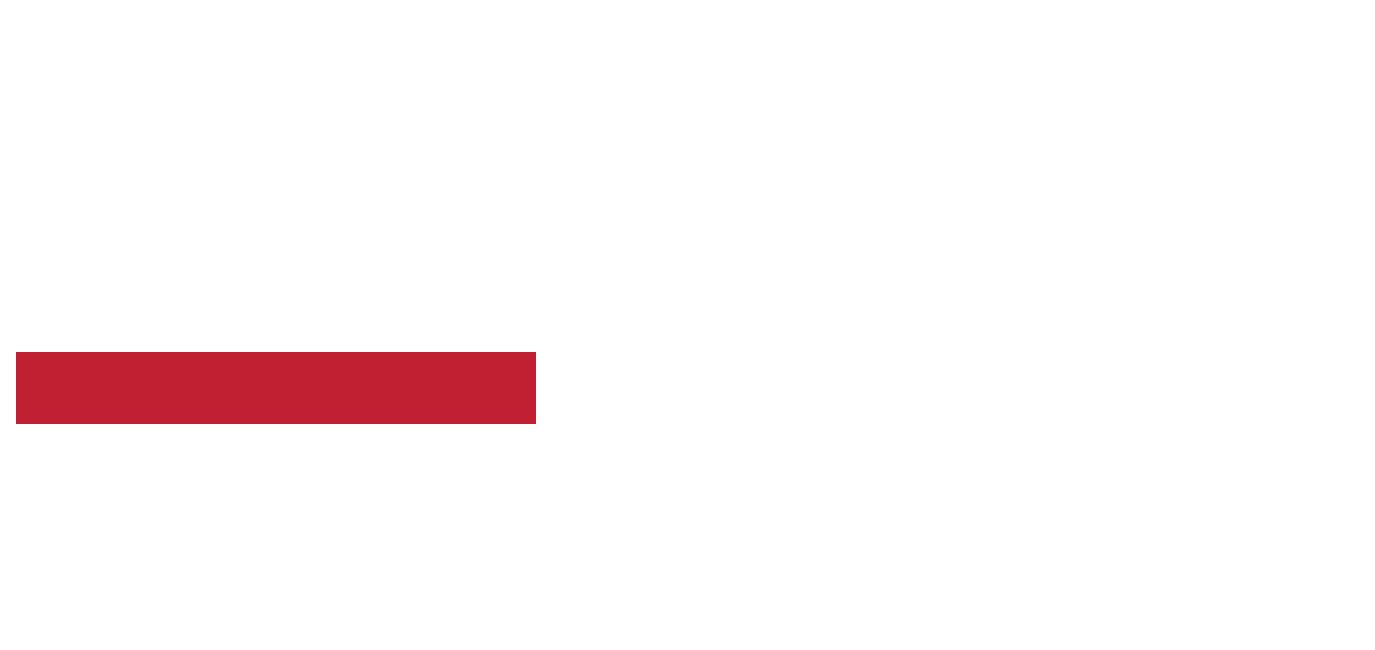
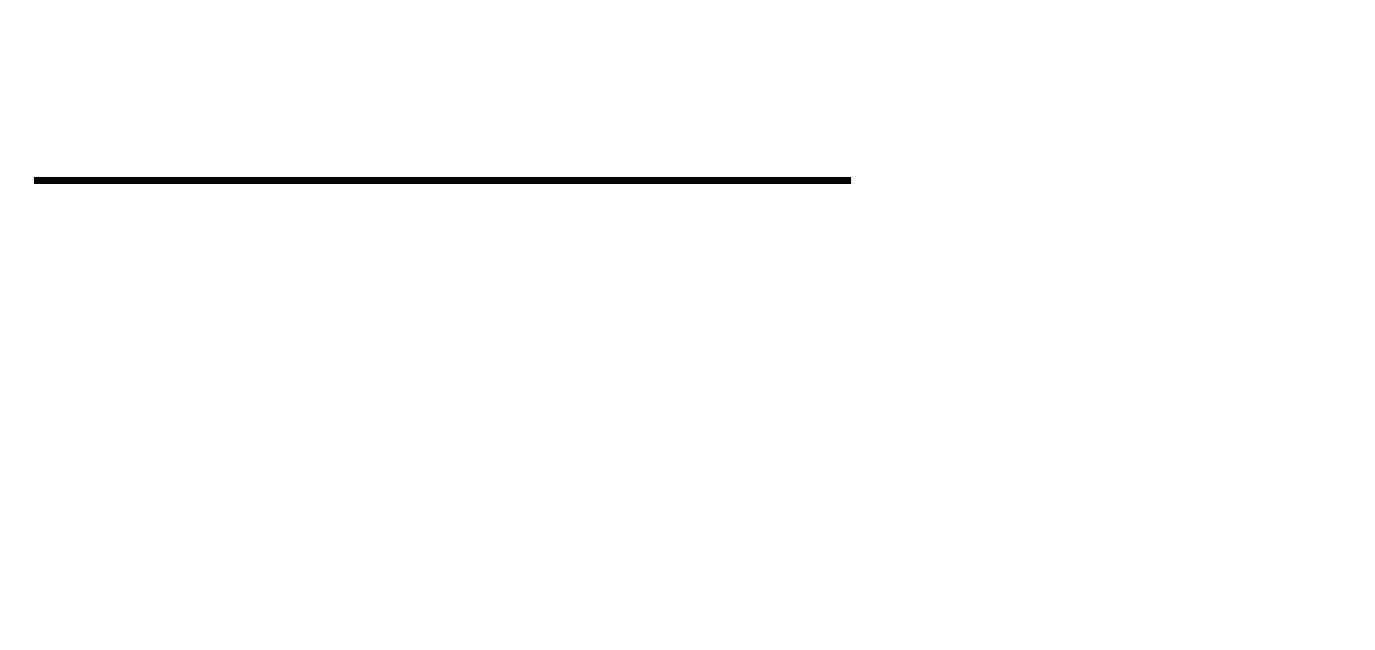
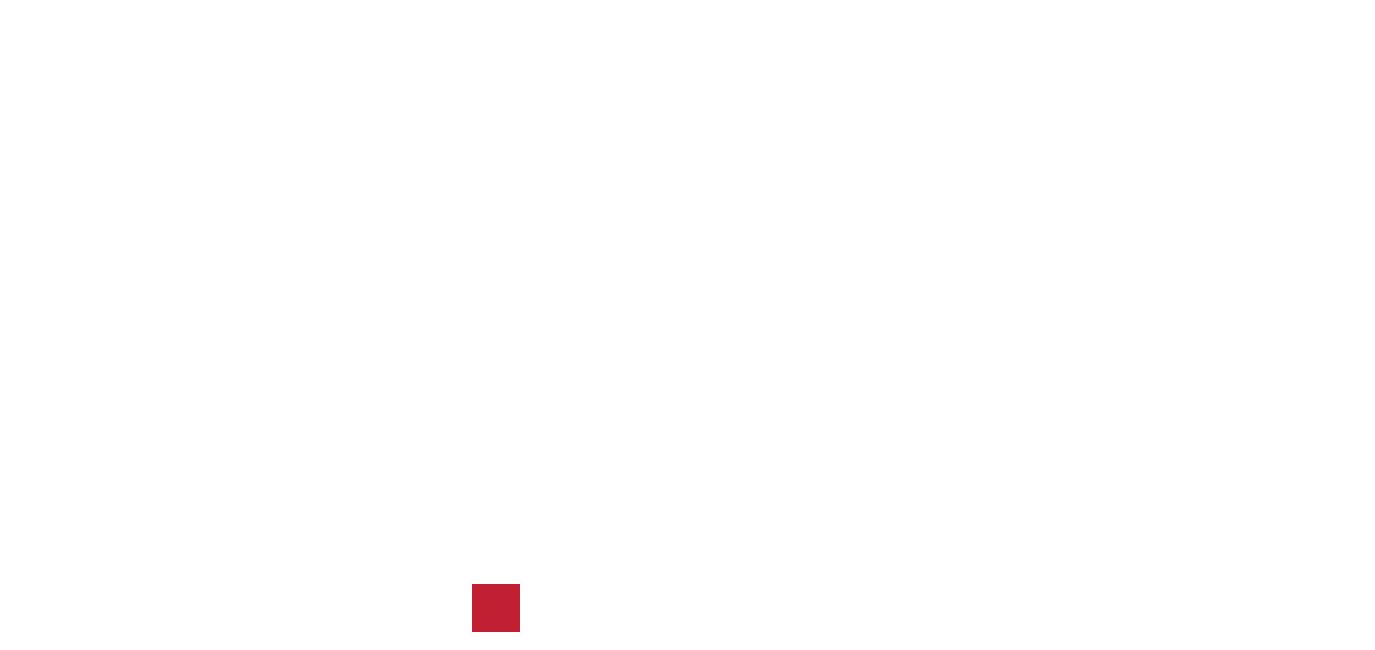
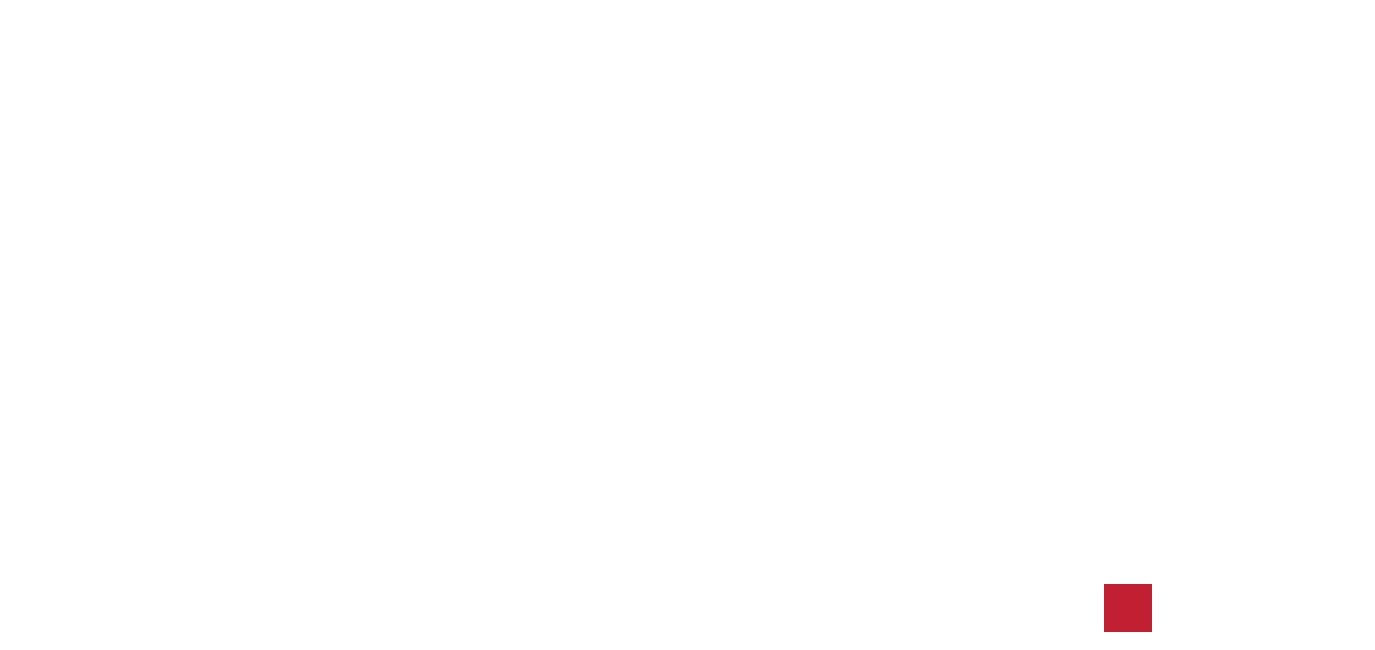
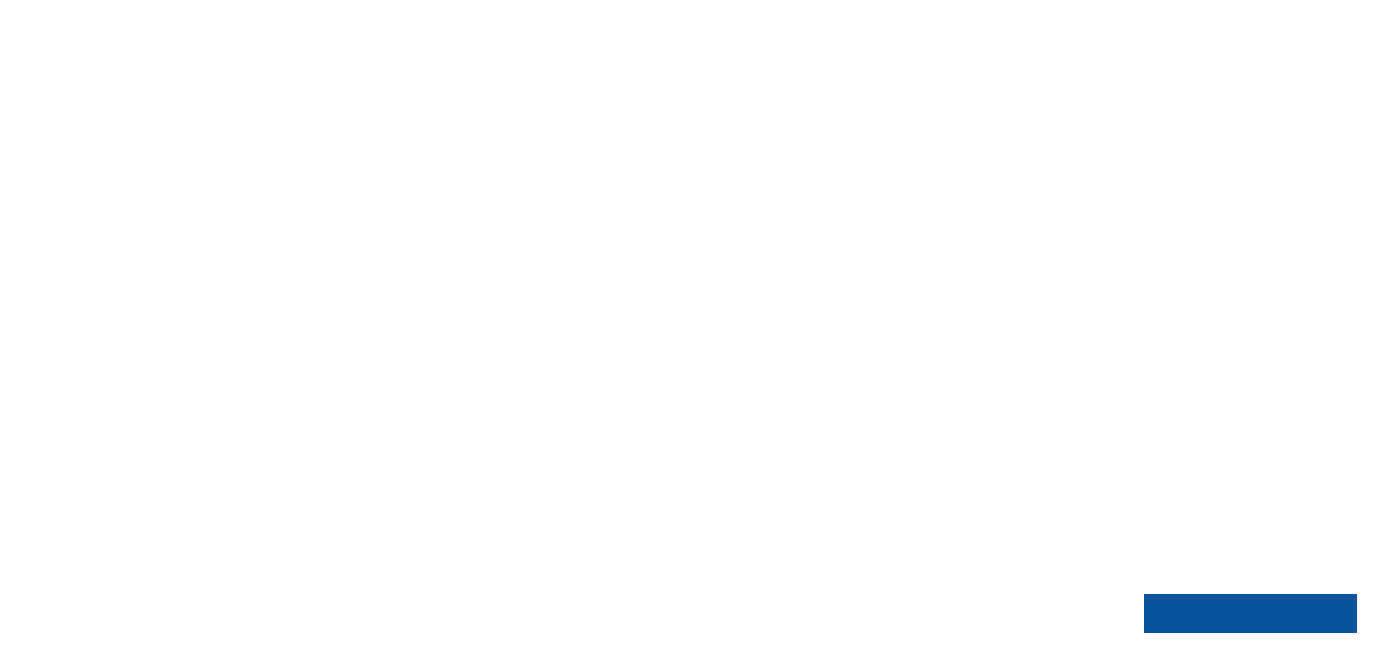
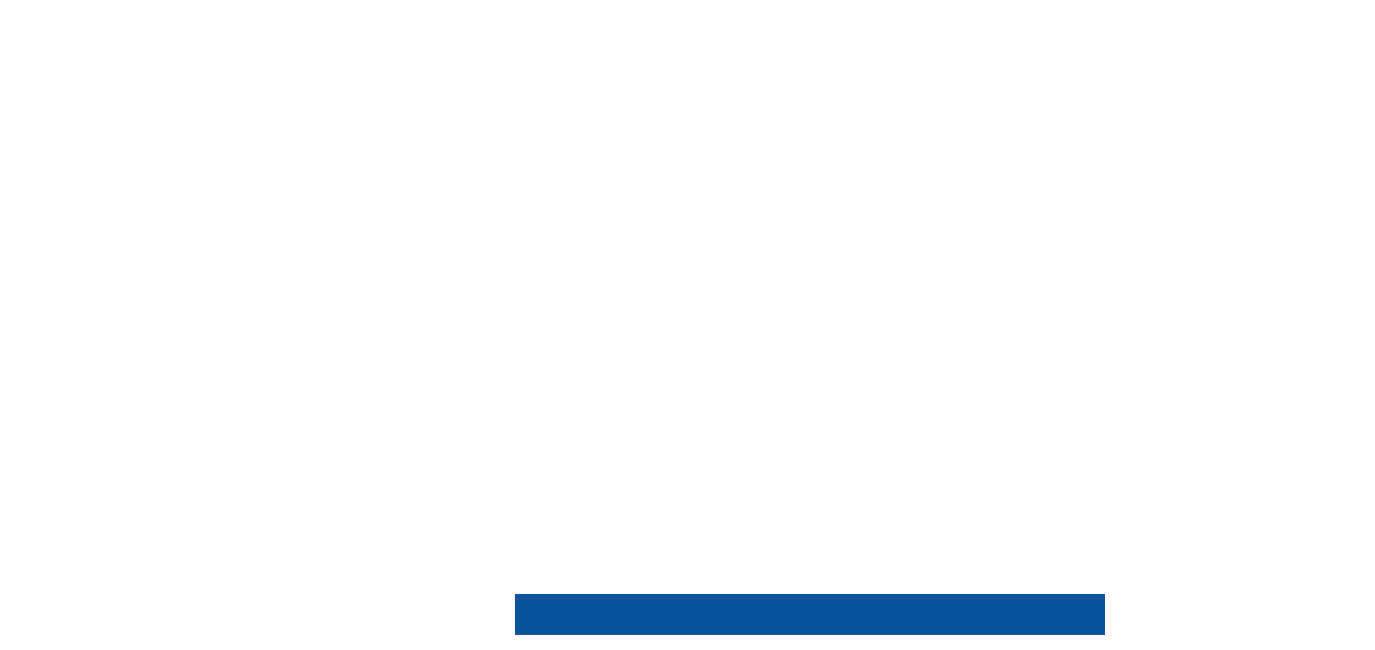

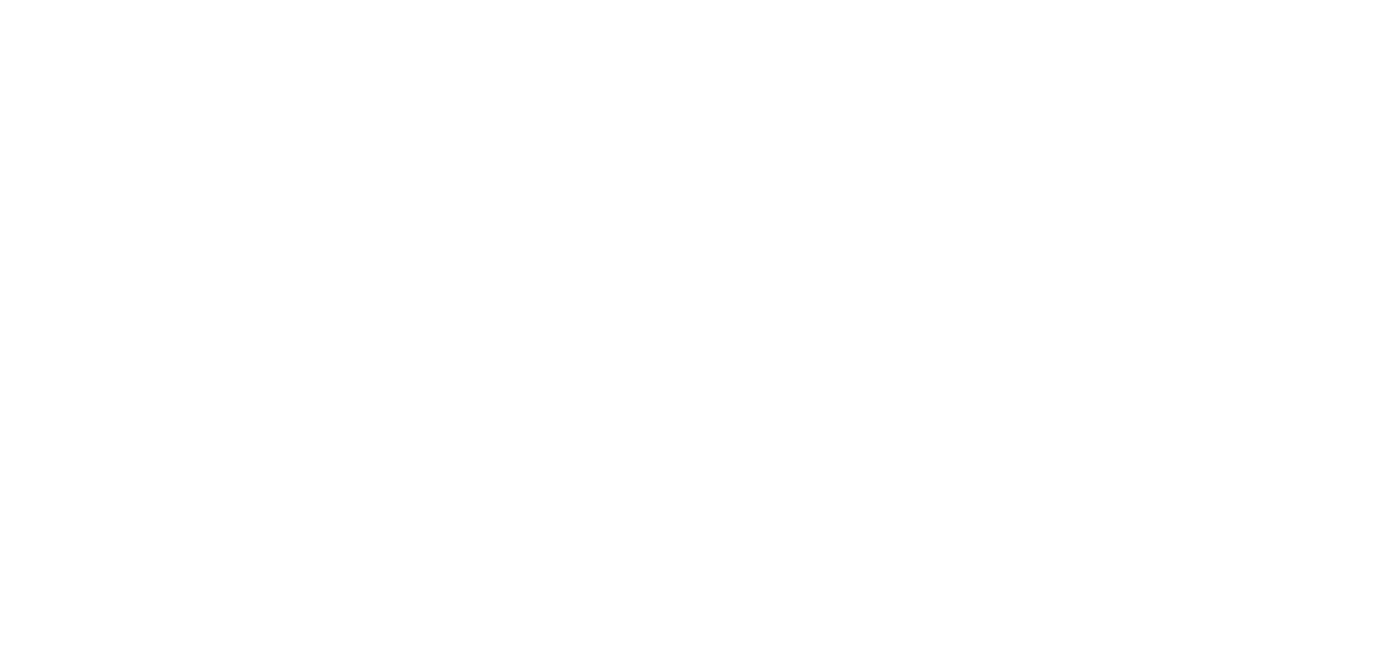



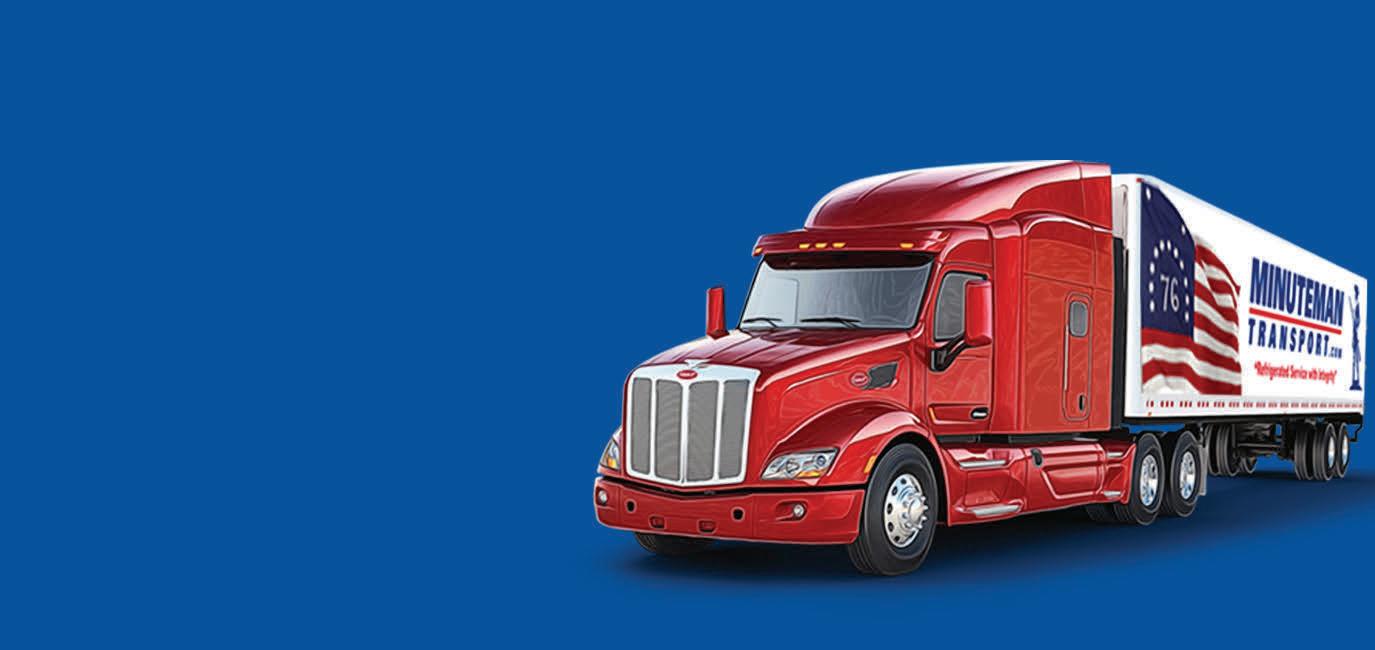
Services
Servicing Utah to the 11 Western States, Texas, and the Upper Midwest Asset and Logistics services Safe Veteran Drivers Among the cleanest, greenest fleets in the nation Continued yearly growth with existing customers
Awards
EPA Smartway Excellence award for Sustainability - 2019 Schreiber Foods Carrier of the year - 2017 Utah Trucking Association Grand Trophy - 2016 Heavy Duty Trucking Top 50 Greenest Fleets - 2013 Numerous safety awards from Great West Casualty over the last 30 years
www.stokestrucking.com | 800-722-1616
Mark Lawver | mark@stokestrucking.com | 435-799-8540 United States – 40 million people, including 12 million children and 7 million seniors. In fact, the Feeding America network has provided more than 6.6 billion meals, helping one in seven people facing hunger live more secure and stable lives.

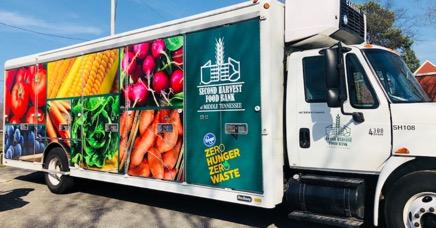
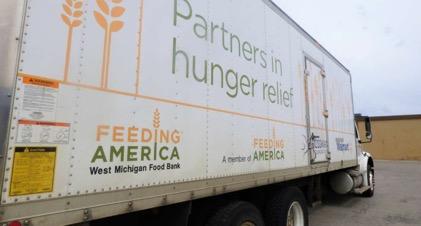
Second Harvest Food Bank: Making a Difference for Those in Need
Second Harvest Food Bank of Central Florida is a private, nonprofit organization that collects, stores and distributes donated food to more than 500 feeding partners in six counties in central Florida: Brevard, Lake, Orange, Oscola, Seminole and Volusia. This charity was chosen specifically because FSA hosted its Food Shippers Annual Conference in Orlando in February of this year, and wanted to contribute to the local area in which the conference was hosted.
FSA has made a financial donation in 2022 to Second Harvest Food Bank of Central Florida.
Last year, with the help of numerous donors like FSA, the food bank distributed enough food for 97 million meals to partner programs such as food pantries, soup kitchens, women’s shelters, senior centers, day care centers, and Kids Cafes. “Food Shippers of America has consistently contributed to worthwhile organizations such as ALAN, Feeding America, and Second Harvest,” says Paul Newbourne, Executive Director of FSA. “We feel it’s important for our organization to support non-profits and charities that have a direct and positive influence on the lives of others.”
MINUTEMAN TRANSPORT INC. MINUTEMAN TRANSPORT INC.
LTL REFRIGERATED TRANSPORTATION
DAILY SCHEDULE TO LOCAL DESTINATIONS. WEEKLY SCHEDULE TO ENTIRE AREA. SERVICING: CA, NV, AZ
WAREHOUSE SERVICES
100,000 SQUARE FT., CLIMATE CONTROLLED, SHORT/LONG TERM STORAGE
MINUTEMANTRANSPORT.COM SALES@MINUTEMANTRANSPORT.COM (626)534-2007
FSA Announces 2023 Annual Conference Line-Up
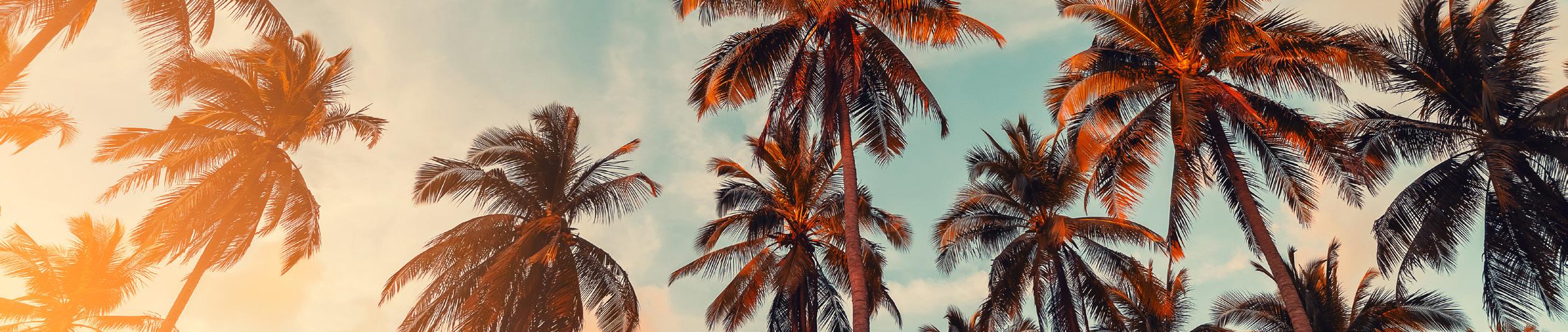
THE FOOD SHIPPERS OF AMERICA (FSA) 67TH ANNUAL CONFERENCE WILL TAKE PLACE MARCH 5-7, 2023, AT THE J.W. MARRIOTT DESERT SPRINGS IN PALM DESERT, CALIF.
In addition to ample opportunities to network with your peers and providers, this three-day event will feature nationally recognized professional speakers, academic scholars, and high-level executives within the food, beverage and logistics industry, including:
Keynote Speaker
Founder and CEO of sportwear company FUBU and star of ABC’s Shark Tank, Daymond John, will share his philosophy Daymond John and business practices that helped him achieve personal and professional success.
Diversity, Equity, and Inclusion in Supply Chain
Shelley Simpson, President at J.B. Hunt Transport, will highlight where the industry has been, where it is today, and where it needs to go to move forward in the areas of diversity, equity, and inclusion within the supply chain. Such initiatives can drive innovation, acceleration and growth in any business.
Innovation and Technology of the Future
Tracy Rosser, Executive Vice President, Operations at Transplace will talk about what is around the corner with data visibility, new Tracy Rosser
transparent platforms, connectivity, and integration technology that will drive supply chain networks into the future.
Traditional Versus Digital Brokerage Panel
Discussion on the “pros versus cons” on the virtues of traditional and digital brokerage, and highlighting similarities and differences to the approach. Shippers will gain perspectives on how to collaborate brokerage solutions that fit their food chain needs.
Seed to Sea and Everything Inbetween
Moderator Alyssa Correale, Senior Vice President Strategic Fleet Partnerships, Uber Freight along with panelists: Alyssa Correale Russell Leo, CEO, RLS Logistics; Joe Dagnese, CEO, Peco Pallet; Adam DeGroot, CEO, DeGroot Farms Beach; and Mario Cordero, Executive Director, Port of Long Beach. These industry leaders will provide insights as to how innovation, collaboration, and acceleration can help drive success in today’s supply chain.
Russell Leo Joe Dagnese
Adam DeGroot Mario Cordero
MARCH 5-7, 2023 PALM DESERT
Making Sense of an Uncertain Future
Chris Caplice, Executive Director for the MIT Center for Transportation & Logistics and Chief Scientist DAT Freight Chris Caplice and Analytics, will review available tools and techniques that can be used to better prepare organizations for a future that is ever changing and unpredictable.
Andrew Whitworth, NFL Player and Super Bowl Champion
Andrew Whitworth talks about his success in the NFL, being the oldest tackle in NFL history, the oldest offensive Andrew Whitworth lineman to win a super bowl, and how the principles that guided him to success can be applied to businesses and personal lives every day. Named the 2021 Walter Payton NFL Man of the Year, Whitworth also discusses the importance of giving back to the community. “With all the disruption and challenges going on in the supply chain these days, we developed the theme ‘Innovate. Collaborate. Accelerate.’ and it has hit home for many food shippers,” says 2023 FSA Conference Chair Mark Purdy, Senior Manager Dry National Transportation Strategy & Operations, General Mills. “We have developed a comprehensive agenda around this theme to ensure it’s as relevant as possible to our attendees.” - Mark Purdy, Conference Co-Chair, General Mills
The Food that Feeds America
Ethel “Stephanie” Stuckey, CEO of Stuckey’s Corp., highlights the turnaround success story of Stuckey’s, and Ethel Stuckey how to use innovate, collaborate, and accelerate concepts to win in the marketplace.
Annual Economic Update
Bob Costello, Chief Economist & Senior Vice President at the American Trucking Associations (ATA), returns to present current key economic data and its effects throughout the supply chain. New for the 2023 conference is an exclusive member only networking event on Sunday afternoon where FSA member shippers and receivers can meet to discuss the supply chain and logistics challenges that they are collectively facing in today’s dynamic market environment. For more information on the 67th Annual Conference, visit foodshippers.org. (Note: Agenda subject to change so check back to the website often).
Bob Costello
www.FoodShippers.org
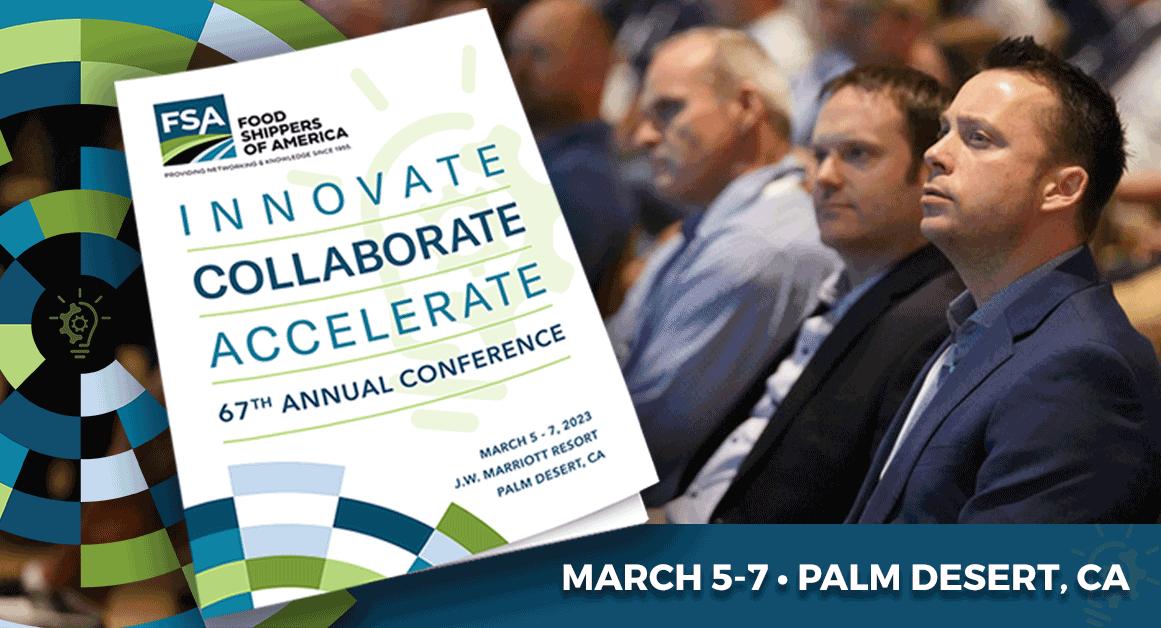

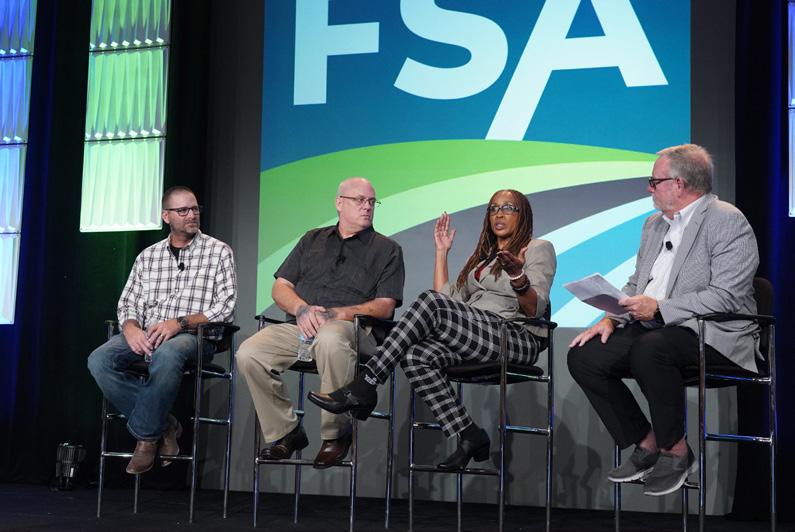
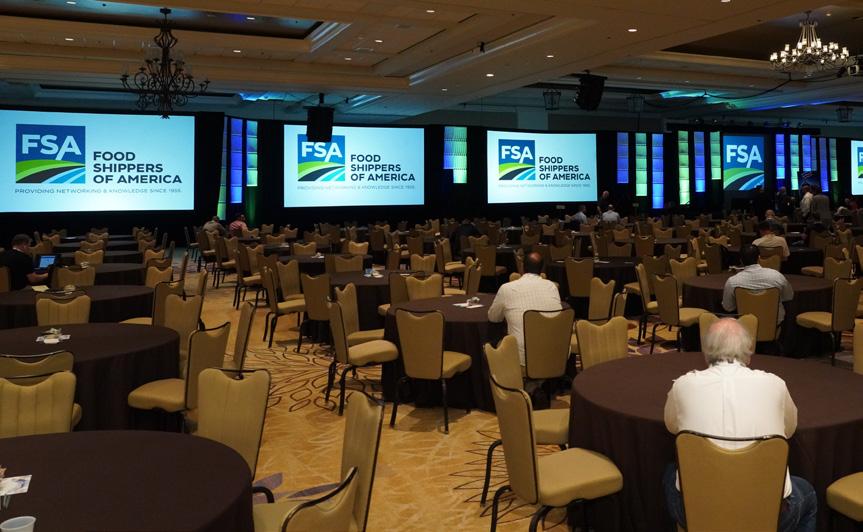
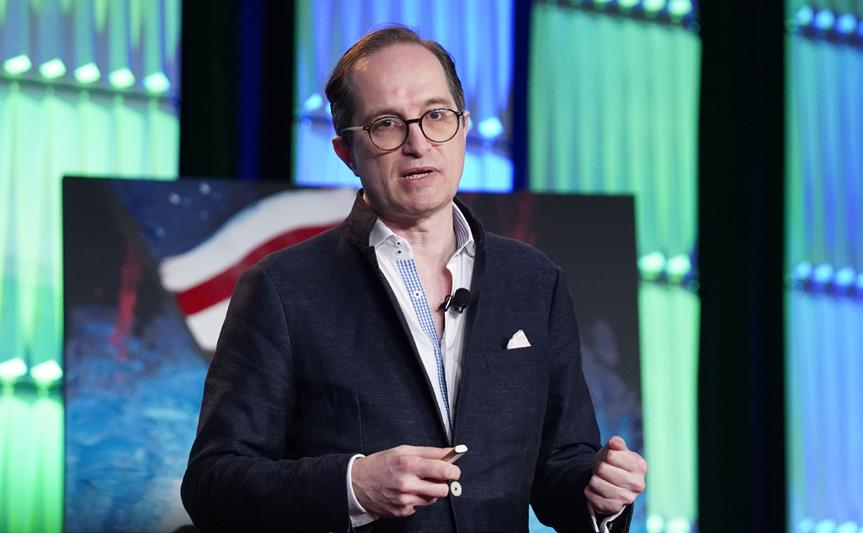
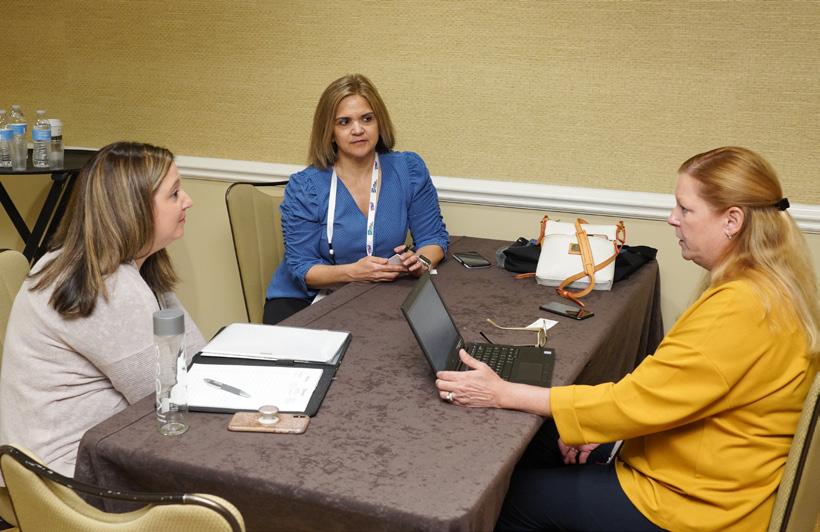