All things food supply chain.
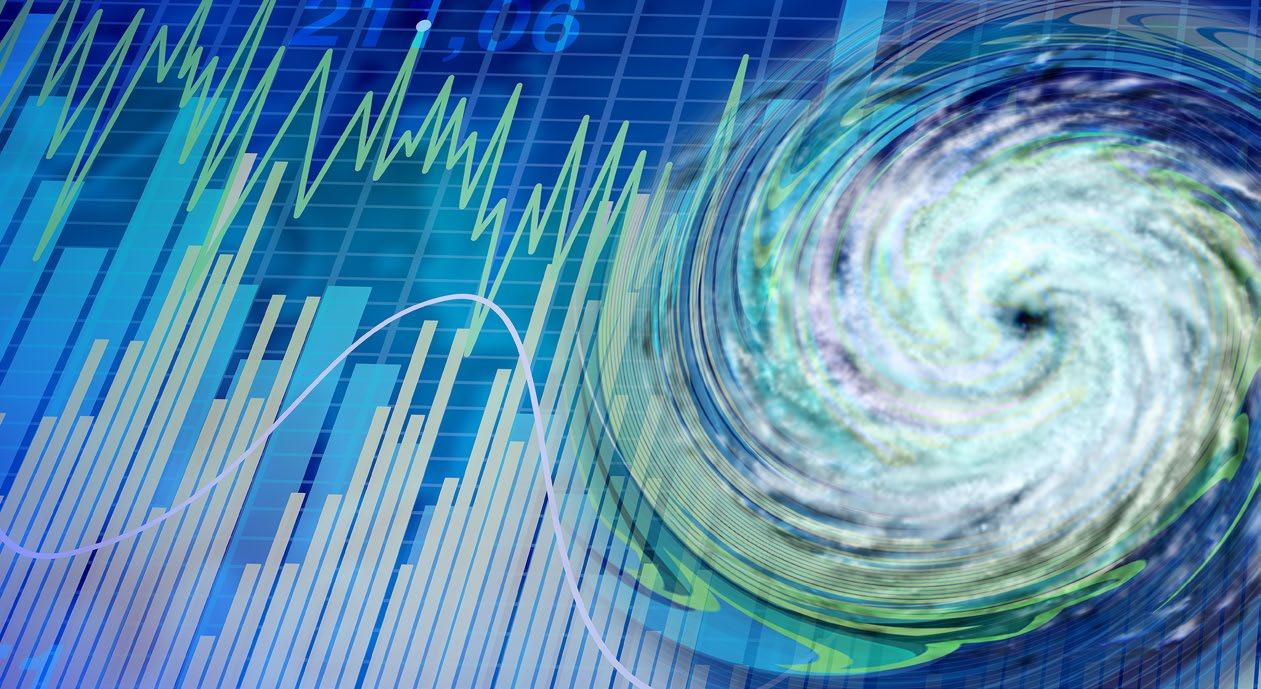
All things food supply chain.
Yields Improved Productivity Women Mean Business: Gender Diversity in the Supply Chain
► Target Asset Carrier of the Year 2023
► General Mills Gold Dry Carrier of the Year 2024
► Ecolab Breakthrough Carrier of the Year 2023
1200+ Power Units and 5000+ Trailers (Over 4:1 trailer ratio)
25% of total fleet is Hazmat Certified
• Specialized fleets for our customers’ unique or expedited needs
• Fleets dedicated regions and routes to service one-way lanes with efficiency
• 36% of total 2023 Legend miles were powered by biodiesel and renewable diesel
• EV fleet dedicated to servicing the Southern California area efficiency
Our goals in the Food and Retail markets are to provide services in all areas that meet the demands of our Customers.
Meet Aaron, logistics leader for Seneca Foods, a shelf-to-table food producer. Aaron manages customer orders by effectively balancing warehouse space and transportation demand, trusting Ruan to provide dedicated capacity, cost savings, and continuous improvement.
Meet Kelli, operations leader for Ruan, a dedicated third-party logistics provider. Kelli’s team of professional drivers enable Seneca Foods to succeed in a fast-paced commodity market, serving as the physical link between and an extension of their plants to ensure production stays on track.
Delivering farm fresh goodness made great. Together.
Freight transport is becoming more efficient, as well as both environmentally and socially responsible. Its future is bright. Why? Because SmartWay, a program marking 20 years of progress, continues to share with its Partners — over 4,000 companies and organizations — information about market-based incentives and technology solutions to help cut fuel costs and reduce emissions. Being a SmartWay Partner is free. If your company ships food and almost anything else, SmartWay has the roadmap to help you achieve greater freight sustainability.
Learn all the benefits of being a SmartWay Partner at epa.gov/smartway
SmartWay. Driving sustainable freight.
Published three times a year
Shippers of America
1144 East State Street, Suite -288A Geneva, IL 60134
847-302-1496
executivedirector@foodshippers.org www.foodshippers.org
Published by:
MindShare Strategies, Inc.
Ponte Vedra Beach, FL 32004 USA 952-442-8850 www.MindShare.bz
Billing Address: MindShare Strategies, Inc. P.O. Box 843 Springfield, TN 37172 USA
Group Editorial Director and Publisher: Brian Everett, ABC 952-442-8850 x201 brian@mindshare.bz
Production Editor: Courtney Bloom 952-442-8850 x212 courtney@mindshare.bz
Editorial Content This Edition: Faith Boone
Advertising Sales: Cassidy Mullins 952-442-8850 ext. 215 cassidy@mindshare.bz
Alec Stifter 952-442-8850 x218 alec@mindshare.bz
Design/Production Manager: Todd Pernsteiner 952-841-1111 todd@pernsteiner.com
Accounting/Administration/Circulation: Karen Everett 952-442-8850 x203 karen@mindshare.bz
Brian Everett, Publisher Senior Partner, MindShare Strategies 952-442-8850 x201 brian@mindshare.bz
As global food chains become increasingly complicated, food companies need the best talent who bring productivity and efficiencies, strong logistics partners that understand their needs and exceed expectations, and robust technology platforms that optimize visibility and streamline operations. This edition of Food Chain Digest covers many of these food chain connectivity issues that involve talent management, outsourcing and technology:
Connecting the talent you need. Food companies that deploy a strategic, systematic approach to sourcing, recruiting, developing, and retaining talent are the most successful. Key roles in modern supply chain management include purchasing, operations, logistics, resource management, and information workflow/systems.
As the industry becomes more digitized, automation in plants, fulfillment centers, procurement, production planning and maintenance is eliminating jobs – yet there’s still insufficient talent to meet demand. In this edition, you’ll find helpful content focused on talent management in the feature article Recruiting Young Supply Chain Talent starting on page 24 and Women Mean Business: Gender Diversity in the Supply Chain starting on page 28.
Connecting logistics partners to support your food chain. Selection and management of your key intermediaries, rail/intermodal providers, and ocean carriers/maritime players with specific core specialties can contribute to building and maintaining an effective,
productive supply chain. Yet, there are many forces playing into how these logistics players are succeeding (or not) in the marketplace today – and their performance is critical to yours’ as well.
For example, there has been significant turmoil in the trucking market over the last several months, with a sharp downturn in consumer demand which has left motor carriers with a lingering surplus of capacity, a relative dearth of freight demand, and a plunge in rates.
The 3PL sector faces significant challenges as well, such as low freight rates and excess capacity. This could lead to further consolidation among 3PLs, especially smaller players and those reliant on venture capital funding. In addition, as the market anticipates improved conditions there is an opportunity for larger players to invest in internal capabilities and for shippers to lock in favorable rates and improved productivity commitments.
In the rail industry, the largest Class I railroads experienced this last year a challenging financial environment, including rising operating ratios, a 2% decline in revenue last year compared to 2022, and an 11% decrease in operating income. These financial reversals have been driven primarily by intermodal volume decreases, service challenges, inflationary pressures, and escalated fuel and labor expenses.
Lastly, the warehousing/distribution sector has been defined by a pullback from extreme conditions caused by the pandemic. Persistent inventory levels are another factor building a floor for vacancy and pricing but an elongated
recession scenario could break that resistance. As companies look for ways to improve capacity in existing space, demand for new warehousing space has softened and subleasing has hit a decade high.
With this backdrop of market conditions, refer to the feature article The Power of Partnership starting on page 12 and the list of Top Food Chain Providers starting on page 16.
Connecting technology to your operations. There’s no question that rapidly emerging technologies and IoT is accelerating the pace of change in the food chain. For example, food companies are well aware of the growing threat of cyberattacks on their company and its supply chain. Supply chain disruptions have altered the cybersecurity threat landscape, resulting heightened business risks. In addition, the age of generative artificial intelligence (AI) continues to drive radical change across the food industry. Across end-to-end supply chain networks, CSCOs are capitalizing on this reinvention of the way people work, access data insights, and generating information.
Much of the cover story Strategies to Navigate Supply Chain Disruptions starting on page 6 addresses the importance of diversification of suppliers and partners and integrating technology for real-time visibility and data analytics.
There’s lots of information to consume in this edition. Get the most out of it and enjoy!
• Zone Skip to Minimize Handling & Reduce Lead Times
• Food, Beverage & Alcohol Handling & Transportation
• Retail Compliance
• Analytics Reporting & Continuous Improvement
• Local Dedicated Account Management & Customer Service
• Sustainability Initiatives & Emissions Reporting
Volatile market forces, labor disputes, and unpredictable weather events are having a negative impact on food companies’ supply chains today. So what can be done to anticipate these forces that can cause major food chain disruption?
There is a myriad of events, either natural or man-made, that can cause major disruptions in today’s supply chains. Think about events in recent months or years that have caused significant disruptions in food chains – ranging from the Covid pandemic’s impact on labor and changes in consumer behavior and buying patterns to geopolitical uncertainties like the Ukraine war that have impacted port delays/ congestion.
Of course, other things can have a significant impact on supply chains, such as economic factors like inflation, market factors such as over-the-road truck capacity, or government/labor disputes such as the recent issue involving Canadian
railroads and government, and the labor dispute that led to disruptions at ports on the gulf and East Coast. Unpredictable weather ranging from hurricanes like Helene to tornadoes and flooding also play a substantial role in destruction and supply chain disruption.
What are some of the biggest supply chain operations challenges that can exacerbate supply chain disruptions? According to the recent Food Shippers Guide to Supply Chain Digital Transformation, a research project that was deployed in the first quarter of 2024 on behalf of a content sponsor with Food Shippers of America (FSA), some of the biggest supply chain
challenges include freight market fluctuations/rising costs, global supply chain disruptions, supply chain management collaboration and effectiveness (see illustration on next page).
Food companies are addressing such predictable and unpredictable forces head-on. Businesses also are resetting their operations with digital capabilities and renew logistics operating models to help them increase operational efficiency, effectiveness, and resilience of their supply chains in order to make them more resilient to future disruptions.
Here are five strategies that food companies can deploy to navigate and mitigate disruptions in their food chains:
Diversification of suppliers and partnerships. Historically food companies sometimes have relied heavily on suppliers and strategic partnerships – which ultimately helped them to build up volumes of business so they could more effectively negotiate pricing and rates and streamline their operations through a small number of sources. This is no longer common practice for many food companies.
Relying on a small number of suppliers for crucial components or materials (or worse, a single supplier) can be extremely risky. Today, food companies are establishing relationships with multiple suppliers, located in different regions of their supply chain networks, which helps to distribute and mitigate any supply chain risks. In addition, building strong partnerships with suppliers and other stakeholders fosters
enhanced collaboration and open communication, which enables companies to quickly adapt to changes in customer demand or disruptions in their food chains. A diverse supplier base also provides a greater opportunity for negotiating power during times of scarcity.
For example, Agropur Ingredients Supply Chain manages the supply chain for Agropur Ingredients, a global leader in supplying ingredients to the food, beverage, and nutrition industries. Agropur Ingredients is part of the Agropur Dairy Cooperative, which is owned by 3,000 dairy farmers who process and market their milk. Agropur Ingredients has a Procurement and Supplier Relations team that manages business relationships with suppliers, and seeks suppliers who provide high quality goods, services, and solutions. Agropur
(Weighted Average Rank)
offers a free Supplier Portal (CSP) to help manage relationships and transactions with suppliers.
Real-time visibility and data analytics. Embracing technology that provides real-time visibility into the supply chain can be a gamechanger. Advanced data analytics tools can help companies monitor inventory levels, track shipments, predict demand fluctuations and identify potential bottlenecks. With accurate data, companies can make informed decisions
and respond promptly to any changes, minimizing the impact of disruptions and optimizing resource allocation.
“We’re now investing in technology with a particular focus on the cold chain,” says Layne Fletcher, Vice President of Logistics & Supply Chain with Golden West Food
Group. “Digital transformation initiatives can have a positive impact on risk management, efficiencies, and customer service –all areas we are highly focused on.”
Resilient logistics and transportation strategies. A comprehensive logistics and transportation strategy that is robust is vital for a nimble supply chain. Food companies can explore options like multi-modal transportation (road, rail, sea, air) to diversify their shipping routes and reduce dependence on a single mode of transportation. Collaborating with third-party logistics providers (3PLs) and truck brokers also can provide access to expertise and resources during times of crisis.
Other food companies are reinventing their supply chains to be more focused on a selfdistribution model to buck the decades-old trend to outsource and they are developing their own supply chain operations and infrastructure for maximum control. For example, ADUSA Supply Chain is a family of supply chain companies that together support one of the largest supply chains on the East Coast, serving the omnichannel grocery brands of Ahold Delhaize USA – Food Lion, Giant Food, The GIANT Company, Hannaford and Stop & Shop – through a self-distribution model. Included in this group are ADUSA Distribution and ADUSA Transportation, which provide supply chain operations for one of the largest omnichannel grocery retail groups in the United States through an integrated selfdistribution model.
Inventory management and demand forecasting. Maintaining excessively high inventory levels can tie up capital and increase storage costs, while too little inventory can lead to items running out of stock during disruptions. Finding the right balance is key.
When it comes to streamlining your transportation, outsourcing is in. Penske’s Dedicated Contract Carriage services help take care of all of your truck, driver and fl eet maintenance needs so you can keep your eye on the bigger picture for your business.
Advanced demand forecasting techniques, fueled by historical data and market trends, can provide insights into future demand patterns. By optimizing inventory levels based on accurate forecasts, companies can reduce the impact of supply chain disruptions and better manage their resources. By optimizing and effectively managing inventory levels based on accurate forecasts, food manufacturers, retailers and distributors can
significantly reduce the impact of supply chain disruptions and better manage their resources.
Food companies operating in today’s complex and interconnected global marketplace must recognize the inevitability of supply chain disruptions. By adopting a combination of strategies that encompass
supplier diversification, data-driven decision-making, effective inventory management, resilient logistics and robust risk management, food companies can position themselves to weather changes in the supply chain more effectively. The ability to adapt swiftly and make informed decisions during disruptions not only minimizes short-term disruptions but also enhances the company’s overall resilience and competitive advantage in the long run.
A brighter road ahead requires a change agent.
In this case, it’s cows.
Heavy- duty trucks cover a lot of miles. You can’t sacrifice performance for sustainability. Fortunately, when you fuel the new Cummins X15N engine with renewable natural gas (RNG), you don’t have to. The X15N boasts the same power, torque, and range as its diesel counterpart, while RNG reduces carbon emissions by up to 300%. With Clean Energy’s network of over 600 fueling stations nationwide, finding RNG along your route is easier than ever. Making the road ahead a very beautiful thing.
The Power of Partnership
HOW PROVIDER COLLABORATION YIELDS
IMPROVED LOGISTICS PRODUCTIVITY
The sector also is becoming more complex. GMI notes that the jump in online grocery shopping is boosting demand for efficient and reliable delivery of all food products. “This shift requires advanced logistics solutions, such as improved cold chain management and rapid fulfilment processes, to ensure timely and safe deliveries,” GMI states. Innovations in last-mile delivery and tracking technologies can enhance the customer experience and boost operational efficiency, GMI notes. They also add complexity.
Shipments to grocery distribution centers and stores also present challenges. Deliveries often need to occur within specific delivery windows and comply with service level agreements.
Succeeding in this competitive, complex environment requires solid collaborations between food shippers and logistics providers. Food companies that collaborate with their supply chain partners can cut inventory and costs, while improving performance and customer satisfaction, as these examples illustrate.
While less-than-truckload (LTL) shipments generally account for a small percentage of the volume moving into distributors’ warehouses, they’re often among the more difficult deliveries, says Ed Garner, Director of National Accounts with Old Dominion Freight Line (ODFL). One reason is that vendors often include multiple purchase orders on one LTL shipment, so the distributor has to separate the pallets by purchase order or product type. In addition, when multiple LTL providers try to schedule appointments, dock utilization becomes unwieldy and visibility to incoming deliveries is lessened.
For the past several decades, ODFL has provided a grocery consolidation solution that streamlines the LTL receiving process. In one option, the company will fill a trailer with goods from multiple vendors and bring the trailer to the distributor’s yard, at its convenience, Garner says. The distributor will send an alert when the trailer is empty, and ODFL will
swap it out with another load.
ODFL also can deliver products to a designated express door at a time scheduled by the customer.
“We’re in and out,” Garner says. In another option, ODFL will consolidate LTL shipments onto equipment the distributor has placed at ODFL’s local service center. At a scheduled time, the distributor’s driver will return to pull the loaded trailer to the distributor’s facility and leave an empty trailer to be filled.
The relationships ODFL has established with distributors enable it to understand and enhance their receiving, delivery, scheduling, and operational requirements. “Without a doubt, the improved efficiency, the seamless integration, and the reduction in total dwell time has made a significantly positive impact on our overall profitability,” says Clyde Coleman, Director of Logistics with Performance Food Group.
One reason partnerships have become critical is that determining on one’s own which digital offerings can deliver the most value can be tough, says Armon Shahpar, Senior Lead of Enterprise Partnerships at Uber Freight. “No one understands the ins and outs of the supply chain more than the people working in it every day,” he says, noting that logistics providers can help shippers determine the goals that best fit their businesses.
Uber Freight partnered with a global distilled beverages importer and distributor to evaluate its workflows and address warehousing inefficiencies. By working closely with the company’s leadership team and third-party logistics partner, Uber Freight leveraged its findings
to guide a new warehousing design. For example, they found that the facility’s ineffective use of warehouse space and slow stock replenishment process, as well as a misalignment of systems and labor, frequently delayed shipments.
Limitations in the warehouse management system (WMS) also contributed to inefficiencies in stock replenishment. Because completing large-scale improvements with a WMS could extend for years, Uber Freight recommended manual augmentations to shore up existing gaps until system updates could be completed.
Through the partnership, units per hour at the facility jumped by 47%,
Food and beverage distribution requires breakneck speed without compromising quality.
while staffing adjustments lowered overall equipment costs. Six months in, the company’s warehouse redesign had hit $10 million in annualized cost savings, or almost half of its original annual spending.
Through its charitable program, Moves that Matter, Total Quality Logistics (TQL) contributes its logistics expertise and covers the costs of transporting donated freight to nonprofits and communities in need, with an emphasis on food insecurity, says Kerry Byrne, President. In 2023, TQL moved 12.2 million pounds of donated goods through Moves That Matter. “It has been incredible to see how far the program has come,” he says.
Recently, TQL partnered with Whirlpool Corporation and
At Kenco, we consistently elevate industry standards by exceeding global benchmarks for food safety while achieving the highest BRC scores and AIB sanitation ratings. Our integrated logistics solutions allow food and beverage companies to keep grocery store shelves stocked and ensure the exceptional quality of your product is maintained through the supply chain to your consumers’ plate.
We want to be your trusted partner in food storage & distribution. Visit us online! KencoGroup.com
Kerry Byrne, TQL
HelloFresh as part of Whirlpool’s Feel Good Fridge program. TQL moves donated refrigerators on behalf of Whirlpool and food on behalf of HelloFresh to fill fridges at food pantries. Together, they’re impacting 13 cities, with Whirlpool Corp. providing 2000 refrigerators which TQL will transport and HelloFresh will help fill with wholesome, fresh ingredients.
“We launched Feel Good Fridge to fight food insecurity in a sustainable way, and collaborating with HelloFresh and TQL allows us to expand our impact in the communities that need it most,” says Pam Klyn, Whirlpool’s Executive Vice President of Corporate Relations and Sustainability.
Food shippers are looking for experienced logistics providers that are focused on service and compliance, Byrne says. “We have moved millions of loads of food over 27 years. Food shippers rely on TQL for procedures and programs that keep food safe while transporting or storing,” he says.
The Top Food Chain Providers program recognizes third-party logistics companies (3PLs), freight brokers, motor carriers, rail/intermodal and maritime companies (ocean carriers and port authorities) that effectively serve the food chain industry. In turn, food shippers use this list as a resource to become better aware of providers recognized for their quality service and capabilities.
How does the program work? Providers with more than U.S. $5 million in gross global sales complete the nomination form that adequately articulates how the company solves business problems for food shippers. The nomination includes an impressive achievement in the last 12-18 months and a recent example of how the company has helped a food shipper accomplish a business goal. Finalists are listed on the ballot of an industrywide vote, and only companies that generate a minimum number of industry votes are named to the list.
Congratulations to the 2024 Top Food Chain Providers!
Advanced Transportation Services, Inc.
Category: Freight Broker
Website: www.advancedtransportationservices.com
Services: Brokerage, Temperature-Control
Allen Lund Company, LLC
Category: Freight Broker
Website: www.allenlund.com
Services: Brokerage, Dry, Refrigerated, LTL, Flatbed
Arrive Logistics
Category: Freight Broker
Website: www.arrivelogistics.com
Services: LTL, Expedited, Dry Van, Temperature-Control, Dedicated Capacity, Flatbed, Intermodal
Bay & Bay Transportation
Category: Third-Party Logistics
Website: www.bayandbay.com
Services: Refrigerated Trucking, Dry Tank, Flatbed, Intermodal, Project Management
Covenant Logistics Group
Category: Motor Carrier
Website: www.covenantlogistics.com
Services: Expedited, Dedicated, Warehousing, Managed Freight Transportation
Echo Global Logistics
Category: Freight Broker
Website: www.echo.com
Services: Truckload, LTL, Intermodal, International Air, Ocean, Small Parcel
Giltner Logistics, Inc.
Category: Third-Party Logistics
Website: www.giltnerlogistics.com
Services: Truckload, LTL, Intermodal, Warehousing, Heavy Haul, International, Freight Management
GLT Logistics
Category: Third-Party Logistics
Website: www.goglt.com
Services: Truckload, LTL, Drayage, Rail, Heavy Haul, Expedited
Heyl Truck Lines
Category: Motor Carrier www.heyl.net
OTR, Long Haul, Regional, Dedicated, Logistics
Category: Third-Party Logistics www.kencogroup.com
Distribution and Fulfillment, Transportation Management, Material Handling, Warehouse Real Estate Management
Koch Companies
Category: Motor Carrier www.kochcompanies.com
Truckload, Dedicated, Flatbed, Specialized, Brokerage, Ocean, Air, Leasing
Kottke Trucking, Inc.
Category: Motor Carrier www.kottke-trucking.com
Services: Truckload, LTL, Cold Storage, Final Mile, Brokerage, Dedicated
Leonard’s Express
Category: Motor Carrier
Website: www.leonardsexpress.com
Services: Truckload, Intermodal, Refrigerated, Warehousing, Distribution, Cold Chain Solutions
Loadsmart
Category: Third-Party Logistics Website: www.loadsmart.com
Services: Managed Transportation and Consultancy, Freight Management Software, Freight Brokerage, Dock and Yard Solutions, Truck Management Software, Tailor Made Logistics Solutions
MoLo Solutions
Category: Third-Party Logistics Website: www.shipmolo.com
Services: Truckload, LTL/Partial, Flatbed, Dedicated Capacity, Expedited, Refrigerated, Dry Van, GPS Integration
Old Dominion Freight Lines
Category: Motor Carrier Website: www.odfl.com
Services: LTL, Expedited, Truckload Brokerage, Container Drayage
Penske Logistics
Category: Third-Party Provider Website: www.penske.com
Services: Transportation, Warehousing, Freight Management, Dry-Van Truckload
Plains Dedicated LLC
Category: Motor Carrier Website: www.plainsdedicated.com
Services: Truckload, LTL
RLS Logistics
Category: Warehousing Website: www.rlslogistics.com
Services: Cold Storage Warehousing, LTL, Brokerage, E-Commerce
Schneider
Category: Motor Carrier Website: www.schneider.com
Services: Logistics, Dedicated, Brokerage, Long-Haul, Regional, Expedited, International, Warehousing, Port Drayage, Power Only, Dry Van, Intermodal, Bulk, LTL, Refrigerated, Flatbed
Stokes Trucking LLC
Category: Motor Carrier Website: www.stokestrucking.com
Services: Dry, Refrigerated, Logistics
Total Quality Logistics
Category: Third-Party Logistics Website: www.tql.com
Services: FTL, LTL, Intermodal, Drayage, Air, Ocean, Drop Trailer, Oversize/Overweight, Partials, Warehousing, Customs Brokerage, Canada Services, Mexico CrossBorder, Hazmat
Uber Freight
Category: Third-Party Logistics
Website: www.uberfreight.com
Services: LTL, Technology
Werner Enterprises
Category: Motor Carrier Website: www.werner.com
Services: Dedicated, Truckload, Intermodal, Temperature-Control, Expedited, Logistics, CrossBorder, Final Mile
XTL Transport Inc
Category: Third-Party Logistics Website: www.xtl.com
Services: Warehousing, Distribution, Logistics, Intermodal, Dedicated, Temperature-Control
Where Efficiency Meets Legacy – Over 35 Years of Unmatched Integrity and Customer Loyalty.
Driving Excellence in Transportation & Logistics - Delivering Innovation, Reliability, and Success Nationwide.
For over 35 years, Genpro has delivered on our promises with cutting-edge logistics solutions. As a leading 3PL provider, we specialize in temperature-sensitive multi-pick and drop freight to optimize your networks. Whether you’re navigating last-minute shipments or expanding into new lanes, our 24/7 support guarantees reliable, seamless service. Let us drive your business forward—today, tomorrow, and into the future.
And front to back.
When it comes to attracting young professionals to careers in the supply chain, it seems that some food companies may need to pivot their goals to align better with the needs of the current talent pool. What are companies doing to identify those key players who are ready to step into their first career experience? Some companies are missing the mark by overemphasizing the “fun” aspects of a position rather than the work experience and skills young professionals will build over time, says Dr. Stephanie Thomas, an Associate Professor of Practice
of Supply Chain Management at the Sam M. Walton College of Business at the University of Arkansas.
Thomas shares from personal experience, citing how her son struggled with some of the “benefits” of his summer internship: “My son did a fully remote internship this summer. He liked the company, he liked the people, but he was sitting in his room for eight hours a day. He said it was not good for his mental health. He’s a ‘social butterfly’ and he needs some interaction. He said, ‘Next year when I’m looking at an internship, I’m going to prioritize fully face-
to-face and fully in-person because I need to see that side of it.’”
During conversations Thomas had with recent graduates at the Food Shippers Conference in February, she compiled some observations she learned from young professionals they say they’re look for when seeking out the next step in their career journey:
Ability to Make an Impact. Young professionals are drawn to the idea that their work in supply chain can help get important products and supplies to people who need them.
Collaborative and Problem-Solving Work. The cross-functional, team-oriented aspects of supply chain, as well as the need to make decisions with incomplete information, appeal to today’s creative problem-solvers.
Variety of Career Paths. The ability to explore different areas of supply chain like sourcing, manufacturing, distribution, and logistics allows young professionals to find the best fit for their interests.
Technological Innovation. Young, techsavvy professionals are eager to work on technological solutions to address supply chain challenges.
Thomas says a lack of confidence is one of the biggest culprits hindering young professionals from starting a supply chain career. She says getting students to believe in what they’re bringing to the table is a challenge in itself.
“A lot of times on a campus, faculty and other staff members are trying to encourage students to step outside their comfort zone,” says Thomas. “Go to the career fair, talk to a couple companies, see what happens. A lot of universities are great at offering mock interviews or resume reviews and stuff to help build that confidence to lessen some of those voices in their head.”
Thomas says companies interested in identifying and retaining top talent need to be transparent, open-minded about recruiting from a wider range of universities, and provide clear career development plans.
Thomas encourages companies to ask themselves: Where is the talent coming from?
“Companies go to a ranking like Gartner or US News and World Report and be like, ‘We’re only going to recruit from the Top Five.’ Well, guess what? You and everybody else at the table,” Thomas says. “You might find another university or program that maybe they’re not in the top five, but they’re a really good program and they have really engaged students that have had very good training with faculty who are really invested in them. You may be able to be a better fit with them.”
As young professionals enter the supply chain industry, they are looking for more than just a job—they seek purpose and impact.
“Supply chain careers have so much meaning,” notes Cam Fulton, Principal at Korn Ferry. Even entry-level roles offer opportunities to drive productivity and efficiency. Additionally, companies that emphasize their environmental, social, and governance (ESG) efforts are increasingly attractive to new talent.
“It’s important for people to feel like they’re doing work that matters,” says Angie Freeman, Chief Human Resources & ESG Officer at C.H. Robinson, highlighting the importance of aligning corporate values with personal purpose to attract top candidates.
“As a young professional in the supply chain industry, I appreciate that I get to collaborate and network with my cross functional partners. I’m able to see the full end to end process, which helps me understand how my day-to-day role impacts our overall business. As for employers, an attribute I look for in an employer is a culture driven community. Company culture leads to better development across employees both professionally and personally. When a company prioritizes and invests in their culture, it shows in the roles, responsibilities, and people.”
McKenzie Meehan, Business Category Lead, General Mills
“One of my favorite things about being in supply chain as a young professional is the amount of opportunity available and the ability to try out so many different roles within the industry. The most important attributes I look for in an employer are opportunities for career growth, leadership development, and the strength of their culture. It always stands out to me when a company has created a great culture and shows investment in their people.”
Megan Formwalt, Merchandising Logistics Manager, Sam’s
Club
PepsiCo products are enjoyed by consumers more than one billion times a day in more than 200 countries around the world. Through a sophisticated supply chain, PepsiCo generated more than U.S. $86 billion in net revenue in 2022, driven by a brand portfolio that includes Lay’s, Doritos, Cheetos, Gatorade, Pepsi-Cola, Mountain Dew, Quaker, and SodaStream. PepsiCo’s supply chain supports a product portfolio that includes a wide range of enjoyable foods and beverages, including many iconic brands that generate more than $1 billion each in estimated annual retail sales.
In addition, PepsiCo has made these commitments related to ERG:
The business of this mega food company is intrinsically tied to the health of the planet and the resilience of its food system - so investing in Environmental, Social and Governance (ESG) is essential, according to Gregg Roden, Executive Vice President and Chief Operations Officer: “We believe that operating in a more sustainable way will help build a resilient supply chain and food system.”
PepsiCo’s complex value chain begins with the sourcing of more than 30 agricultural crops and ingredients from the company’s farmers and suppliers around the world. These crops and ingredients are made into PepsiCo products at more than 1,000 manufacturing facilities, including 291 company-owned facilities. Products are packaged and moved across approximately 1.3 billion miles worldwide by a company-owned fleet — and even more than that through third-party logistics providers (3PLs). Once the product has been enjoyed, the packaging is generally either collected as waste or recycled for another use.
• Established a goal to achieve net-zero emissions across our value chain by 2040. By 2030, the company plans to reduce its greenhouse gas emissions (Scopes 1 and 2 by 75% and Scope 3 by 40%) against a 2015 baseline, doubling its previous climate goal.
• Introduce more sustainable packaging into the value chain and cut virgin plastic per serving by 50% across the company’s global food and beverage portfolio by 2030. This will be accomplished by scaling new business models that avoid or minimize single-use packaging materials to deliver 20% of all beverage servings sold through reusable models by 2030.
• Advance human rights and diversity, equity and inclusion for the company’s people, in its business partnerships and communities, thereby contributing to a better workplace and world. That means continuing to make progress against our women’s goals and promoting fair and safe working conditions, advancing respect for human rights everywhere the company operates, providing access to safe water and advancing food security.
Food companies may be wrestling with the “Great Breakup” (the trend of women leaving the work force in the past two years), yet the urgency for more gender diverse organizations has never been so apparent. A recent Women in Supply Chain Survey, conducted by Gartner, underscores four key findings.
First, there are more women in supply chain than ever. According to Gartner’s report, women account for 41% of the workforce in the supply chain industry, although the gender gap grows in leadership positions. The survey found that women hold only 15% of executive roles in the supply chain sector.
Second, women are noticeably more absent from the front line.
For many Chief Supply Chain Officers (CSCOs), frontline teams in manufacturing and logistics form the cultural heart of their supply chain organization. Yet in 2022, more than a third of employers reported attrition rates over 20% for frontline workers, compared to just 13% of employers reporting the same high attrition rates for desk-based workers. If CSCOs can hire and retain more women, this larger labor pool provides a major competitive advantage. In addition,
the employee value proposition food companies craft to attract and retain more women will be more attractive to everyone: Gen Z and the caregivers of all genders, to name two key demographics.
Third, mid-career attrition among women in supply chain positions remains a challenge. According to the survey, greater compensation is the top reason women leave the supply chain organization at all levels (particularly mid-career), while lack of career opportunities is the second largest reason. Gartner recommends partnering with HR to uncover pay inequities in your organization, develop a plan for bridging any gaps, and determine what information you are able to share publicly to improve pay transparency.
Lastly, organizations experiencing progress in gender diversity cite leadership inclusion, intentional recruiting and professional
Total Supply Chain Workforce Managers/ Supervisors
Senior Managers
Directors Vice Presidents
CSCOs/SVPs/ EVPs/CPOs
development for women. Approximately 70% of supply chain organizations have established gender diversity objectives and 17% rely on enterprise-wide DEI initiatives (a decrease from 29% in 2022).
There are a number of areas involving specific corporate initiatives that currently drive more gender diversity in the industry, according to the “Top Companies for Women to Work in Transportation recognition program,” which is deployed each year by Redefining the Road, the official magazine for the Women In Trucking Association. These areas range from creating a corporate culture that supports and encourages gender diversity, flexible programs and policies that accommodate family and life balance, competitive compensation, benefits, and continued professional development and training.
According to Jennifer Hedrick, CAE, President and CEO of the Women In Trucking Association, some emerging trends in these areas are:
• Strategic and intentional recruitment of women, which could include reshaping the interview process or removing gendered language from job descriptions
• Professional development programs focused on more inclusive leadership
• More active employee engagement among women and male allies, which could include investments in employee resource groups (ERGs). Advanced learning and professional development programs specifically designed for women.
For a long time, supply chain management was viewed as an outgrowth of blue-collar professions. As such, the majority of people in leadership roles were promoted from the shop floor. Men typically held most of the transportation and front-line warehouse positions and therefore were most likely to become leaders in the field. What’s more, educational opportunities were limited, making it even more challenging for women to climb the ranks of the supply chain industry — and even enter the field itself.
Companies in the consumer goods and retail supply chain spaces had only 25% of Vice President roles filled by women. Overcoming the significant gender gaps that exist in the supply chain industry will be critical for food business’ success and more agile supply chains.
• Our locations: Chambersburg, PA Greensburg, PA Pittsburgh, PA Davenport, IA
• Dry, Refrigerated, and Frozen Temperature Zones
• Asset based with refer and Dry vans
• Rail/Truck Cross Dock Services
• Rework and Packaging Services
• Import/Export containers from Eastern Ports
• Licensed for Alcohol Storage
• USDA Room
• Customs Bonded
The following are examples of companies that have intentionally and strategically incorporated diversity & inclusion strategies into their business:
ADUSA DISTRIBUTION AND TRANSPORTATION, the distribution and transportation companies of Ahold Delhaize USA, aspires to have 100% gender balance at all levels. These goals are achieved by creating balanced slates during hiring processes and succession planning to ensure diverse candidate pools. Transparent talent plans provide equal access to growth opportunities, and the company fosters mentorship and sponsorship programs to empower underrepresented associates to thrive and excel within the organization.
ALDI, one of the fastest-growing retailers serving millions of customers each month, fosters a culture of inclusivity for all employees and customers through an updated anti-harassment policy: “Equality. Respect. Responsibility.” This policy reinforces assurance that all ALDI stores, warehouses and offices are inclusive and respectful for everyone, and applies to all customers, employees, suppliers and all third-party partners.
CONSTELLATION BRANDS, an international producer and marketer of beer, wine and spirits, has built DE&I into its strategic business priorities, says Mike McGrew, Executive Vice President, CSR & Diversity Officer: “As a consumer-obsessed company, our mission is to build brands that people love. We’ll do that best when we, as a workforce, reflect the viewpoints, perspectives and values of consumers we serve. Our DE&I strategy helps drive a company-wide mindset that weaves diversity, equity and inclusion into everything we do, enabling us to build an inclusive work culture while staying ahead of today’s evolving consumer landscape. For us, DE&I is both the right thing to do and critical to building a strong, sustainable business that continues to succeed over the long-term.”
DOT FOODS, North America’s largest food industry redistributor, has created an employee resource group (ERG) called the Women’s Leadership Group. This ERG drives key changes in areas such as professional development, work-life balance, and hiring and retention strategies. In addition, the company’s employees undergo unconscious bias and micro-behaviors training to create awareness and affect change.
FERRARA CANDY CO., a global leader of sugar confections with an operational network of more than a dozen manufacturing, distribution, and R&D facilities in North America, also has created ERGs to help the company to achieve its business goals through diversity. This includes enhancing its corporate culture, fueling innovation, contributing to the organization’s strategy, and making a positive impact on its communities.
GIANT EAGLE, with nearly 36,000 individuals who work in its retail stores, pharmacies, warehouses and corporate offices, supports diverse and historically underrepresented suppliers while offering a broader selection of products and services for its customers. By actively seeking out partnerships with more diverse suppliers, the company leverages its buying power to invest in the growth and development of diverse businesses and therefore the economic well-being of the communities in which the company operates.
HORMEL FOODS, a global branded food company with more than $12 billion revenue across more than 80 countries, cultivates an environment filled with unique perspectives that drives innovation to create a better, more inclusive workplace. The food company has a long-standing reputation as one of the most successful food companies in the world and has received numerous honors and accolades in this area, and recently received a perfect score of 100 on the 2023 Corporate Equality Index.
LAND O’ LAKES, a farmer- and retailer-owned food and beverage cooperative, is committed to creating space for brave conversations, promoting inclusion, and fostering a culture of support and empowerment for all employees. The company supports the development of women, with sub-pillars to support women of color, field-based women, and developing men as female advocates.
MICHAEL FOODS, the largest processor of value-added eggs and producer of refrigerated potato products, has made a commitment to a diverse workplace culture. This is accomplished by rewarding diverse ideas and perspectives; building diverse high-performing teams; working processes that enable inclusivity such as roundtables, councils, special projects; and establishing and communicating diversity metrics.
RED CLASSIC, a wholly owned transportation and logistics subsidiary of Coca-Cola Consolidate, maintains a corporate culture supportive of gender diversity through flexible hours and work requirements, competitive compensation, quality benefits package (i.e., paid maternity leave), training, continued education and development support, career advancement opportunities, and well-maintained/safe equipment and facilities for professional truck drivers.
SCHREIBER FOODS, a leader in cream cheese, natural cheese, process cheese, beverages and yogurt, has laid out a roadmap to create a diverse workforce that understands and values D&I. Its strategic priorities focus on data analytics and reporting; DEI education and training; internal talent review and development; workforce recruitment; and employee and community engagement and belonging.
THE HERSHEY COMPANY, an industry-leading snacks company, ranked number three on DiversityInc’s Top 50 Companies for Diversity annual list in 2023. Hershey credits this recognition to prioritizing its workforce and community initiatives, proactively fostering an equitable environment for employees. Notable results from Hershey’s DEI initiatives include representation and leadership (its Board of Directors has 58% diverse representation and a global workforce with nearly 50% gender representation); recruitment and supplier diversity (fostering a workforce and supply chain which reflect its consumer base - by 2030, Hershey will quadruple its investments with diverse suppliers); and gender and pay equity.
UNILEVER, one of the world’s largest manufacturers that includes food products, achieves an equitable workforce through: policies and practices (by removing barriers and bias from all existing policies and practices which impact employees’ experience); the employee experience (by establishing leadership accountability for equipping and supporting employees to excel in their roles and contribute to the growth of the business); talent attraction, recruitment and selection; and in representation and retention (by seeking to make its workforce fundamentally representative of the populations in the geography in which they operate, and of their customer base).
Lansdale has helped us to grow our local business, with excellent shipping and delivery procedures.
The staff is knowledgable and accessible by email and by phone.
Our inventory of merchandise is maintained at the highest standards.
-- Importer and Distributor of Tomato Products
Located within the northeast Megalopolis that runs from Washington to Boston
-Rail Served Daily by CSX and PNR
-Diverse Material Handling Equipment
-AIB Certification
-ISO 9001:2018 and ISO 200005
-An Asset Based Corporation
- Five Locations between Allentown & Philadelphia
-WMS and RF Technology
-Licensed to Store and Transport Alcoholic Beverages
QUALITY OF LIFE THEMES DOMINATE ATRI’S 2023 LIST OF CRITICAL ISSUES IN TRUCKING
Rebecca Brewster, President, ATRI
Considering that 70.5% of food in the U.S. is transported by truck, any impact to trucking costs or capacity impacts food shippers, according to Rebecca Brewster, President and Chief Operating Officer for the American Transportation Research Institute (ATRI), who presented fresh insights from ATRI’s Critical Issues in the Trucking Industry 2023 report at FSA’s Annual Conference in March 2024. With prices high in grocery aisles, the driver shortages, and echoes of challenges created
by the pandemic, Brewster’s observations hit home for conference attendees.
Brewster led with three issues linked to quality of life to truckers—a major theme, she said, considering that America is short 60,000 to 80,000 professional drivers today. The number one issue for truck drivers in 2023 was driver compensation. Brewster pointed out ATRI’s recent Operational Costs of Trucking, or Ops Costs, report found that drivers’ wage cost per mile increased 15% in 2023.
The second biggest issue for drivers was the lack of available truck parking. “Every person in this
room knows where you’re going to put your head down tonight and you know you’re gunna be safe. That same luxury is not afforded to the men and women who deliver for us each and every day and that’s an issue we’ve got to change,” Brewster said.
Delays at customers’ facilities, were the fifth biggest issue among truck drivers. This is one problem food shippers have the power to change, and Brewster says it’s within their interest to do so. She cited research from 2019 that found reducing average dwell time of truckers improved driver turnover rates in almost all fleet sizes and sectors.
Quality of life issues like these influence the larger issue of the ongoing driver shortage — the number two issue for motor carriers. Brewster pointed out that trucking is doing a poor job attracting new recruits to replace aging trucker generations who are retiring. She stated that trucking has a lower percentage of workers in the 20-24
age group than construction, professional services, and U.S. industry as a whole.
Fleets are increasing driver wages and benefits to attract and retain drivers, with larger fleets paying the most. Brewster observed that while fleets with fewer than 26 trucks pay the least, they also have the lowest annual turnover, per ATRI
Offering a wide spectrum of services, PalletTrader’s core focus is to optimize cost and bring efficiency to your pallet management process.
Backed by the largest nationwide digital supplier network, PalletTrader is the premier choice to support all your pallet needs. To learn more check out pallettrader.com
research. The finding suggests food shippers that operate fleets don’t necessarily have to raise pay to attract and retain drivers who value a positive work environment and non-monetary perks.
Women represent an untapped pool of potential drivers for food fleets. Today, only 11.9% of truck drivers are female. Furthermore, ATRI’s analysis found that male truck drivers are 14% more likely to be involved in a crash than female drivers. Brewster wonders whether fleets with female drivers could leverage this fact to negotiate lower insurance premiums.
Insurance premiums were the number six top issue for motor carriers in 2023. Brewster said over the past 10 Years, ATRI has seen liability insurance premiums rise 40%. This cost is a major reason why in 2023 the cost to operate a truck passed $2 per mile for the first time, Brewster said.
Rising fuel prices, the number three issue for commercial drivers and number five issue for motor carriers, were another reason for the bump. Diesel prices increased 54% in 2023 according to ATRI’s Ops Costs report.
Rising fuel costs eventually get passed on to food shippers and ultimately to consumers. As food and beverage shippers look for
costs to cut to avoid making further hikes to product prices, interest in electric vehicles (EVs) is gaining speed. Zero-emission vehicles were the number seven top issue for motor carriers in ATRI’s study.
Brewster cautioned food shippers feeling the rush to plug into EV particularly for long hauls. The U.S. is a long way from being able to completely convert the American fleet to EV. She estimates that would require chargers at every one of the nation’s 313,000 parking spots at truck stops and rest stops as well as $35 million and 40% of the current electrical generation in the U.S.
Furthermore, Brewster pointed out that increasing the range that drivers can travel so they don’t have to stop frequently to recharge will be problematic. It will require additional battery weight, which will reduce the weight of cargo that can be hauled. In other words, shippers will need more EV trucks to haul the same amount of food.
Focusing on these and other critical issues in the trucking industry helps point the way to positive changes that control transportation costs and support the driver pool that supports food chains.
When it comes to supply chain issues facing food companies, cargo theft and food safety are among the top challenges. These two challenges become even more difficult to navigate when you layer in unpredictable supply chain disruptions, a growing list of regulations, and a deep shortage of qualified talent that limits the reliability and flexibility of supply chains.
The most common form of fraud is cargo theft, which saw a 600% increase between November 2022 and March 2023 according to a report by the Transportation Intermediaries Association. The National Insurance Crime Bureau reports that cargo theft amounts to $15 billion to $30 billion each year. Industry watchdog CargoNet reported nearly 700 thefts documented by shippers, in Q3 2023 – which is a 59% year-overyear increase from 2022.
However, these statistics don’t tell the whole story. While more conventional direct theft of freight throughout transit does occur, cargo theft through fraudulent activity has sharply risen in the past 18 months. One deceptive practice involves thieves who call food shippers to impersonate a legitimate carrier, book a load, then hire a different carrier that has no idea they’re participating in a fraud to pick up and drop off a shipment at a DC or warehouse, then retrieve the stolen load from that location.
Cargo theft hasn’t just been increasing over the last year, it has been evolving – and so must the defensive strategies that come from both food shippers and their
providers. Here are five effective strategies for avoiding cargo threats:
Share information openly. The vital first step in thwarting cargo thieves is knowing what kinds of threats are out there. And the only way this is possible is if shippers, carriers and providers across the supply chain are open with one another about what they’re facing.
Bruce Koele, President, Heyl Truck Lines
“We take pride in building strong relationships with our customers, whether they’re food shippers, 3PLs or truck brokers,” says Bruce Koele, President of Heyl Truck Lines, a family-owned trucking company that specializes in temperature-controlled and dry food shipments. Based in Akron, Iowa, Heyl Truck Lines operates a fleet of more than 500 trucks and 1,250-plus refrigerated trailers to haul freight across the United States and Canada. The 75-yearold company has facilities in Akron, IA; Estherville, IA; Sioux Falls, SD; Zephyrhills, FL; Edinburg, TX, and Okotoks, Alberta.
“Food shippers need to build confidence in who they’re working with,” continues Koele. “At Heyl, we ensure communication is current and updates remain fluid between customers, dispatchers, and drivers. We continually invest in technology to assist in keeping all parties current on all load information. By leveraging the technology, we can better protect the load at all levels.”
Vet and verify everyone you work with. A volatile provider landscape in freight in a marketplace with bad actors means you’re often going to see new faces behind the wheel and at the dispatcher desk. Get to know the individuals at your provider partners.
If you’re adding a new carrier or provider to your transportation network, find out as much as possible about them. Identify key decisionmakers and anyone within the team who will have access to your freight and shipment data. It also is important to research their safety history and CSA scores to ensure you will be working with carriers who have a reputable safety history.
Take cybersecurity seriously, for both technology and training. Just as freight thieves are evolving, so are the technologies put in place to identify and stop them. Ensure your organization is using the latest best practices for password security, identity verification (including multifactor authentication) and encryption.
Ensure your partners implement equipment safety protocol. Make sure your logistics partners have best practices that physically protect your freight on the docks and in-transit. “For example, we thoroughly train our professional drivers to make sure they doublecheck their cargo security seals on every shipment to make sure it matches the seal number on their bill of lading and is ultimately protected by locked security covers so all shipments are sealed and padlocked,” says Koele.
Heyl’s TMS system has a number of security features in place to protect shipper user information, including SSL encryption, offline protection, internal system message encryption, routine web server upgrades, cloud services security, and web portal user management.
For your own internal technology platforms, the technology you choose is only as effective as the teams who use it. Constantly reinforce best practices and update your employees and coworkers about any changing procedures or protocols through regular cybersecurity training.
The most common form of fraud is cargo theft
600% Increase between Nov 2022 and March 2023
$15-30 Billion cost of cargo theft each year
documented by shippers in Q3 2023 –a 59% increase from 2022
Food safety is a major concern for the food chain industry. Temperature-sensitive perishable food items can spoil without best practices and proper precautions, which could lead to foodborne illnesses. Grocery chains, foodservice distributors, restaurant chains, and meal kit businesses all come with varying degrees of risk – and prioritizing food safety is an essential but challenging task.
One of the most important practices that food companies should implement into their operations is to carefully understand what their providers are doing to ensure food safety remains a top priority for shipments they’re managing.
“At Heyl, we understand the importance of food safety to our customers, and the responsibility they have to their customers,” continues Koele. “We take great pride in our performance and understand we play a huge role to ensure that the food products on the shelves are safe for the consumer. We go to great lengths to ensure that product temperatures and chain of custody is maintained while the product is in our possession.”
Heyl utilizes state-of-the-art technology with both Thermo King and Carrier units to ensure the temperature of the product
is maintained within our customers’ requirements, says Koele. “In addition to our drivers monitoring the status of the load while in transit, our operations team has the capability to continually monitor temperature set points and confirm our reefers are functioning properly,” he continues. “We create internal systems according to each product or customer that are set to alert us if the temperature of a trailer starts to vary from the set point. In addition to temperature integrity, we also ensure the chain of custody is maintained while in our care! In addition to seal protection devices, we also require our drivers to utilize padlocks and high-quality tamper resistant seals for cross border movements into Canada.”
Leveraging technology is a critical step that shippers can take in ensuring food integrity – and their most trusted providers are an important facet of this. “We have trailer position and temperature tracking on all units (Thermo King units via TracKing and Carrier units via Carrier Lynx/Orbcomm Platform),” says Koele. “This data integrates into McLeod so that we always have it right in front of us. We also use real time email warnings to monitor and quickly react to any unit having an issue. This information helps us to monitor all loads on the road daily to ensure we have correct settings along with proper operation of the units - all tracked by the set point and return air information integrating into Mcleod via mobile comm connections.”
Heyl has proactively saved many food shipments with this technology. “For example, we have a driver get loaded on say a load of
bananas that we know should be set at 58 degrees,” explains Koele. “As soon as the driver sends in a depart shipper the data from that reefer integrates into McLeod. We’d immediately see if there was a wrong temperature setting on the trailer versus what it should be. Same deal with spot trailer facilities. We can monitor those loads as well along the same means.”
Every step outlined above needs to be implemented before the worst happens, not just in response to a theft that’s already occurred. And best practices and protocols should be consistently monitored and updated. Starting a Freight Security and/or Food Safety Steering Committee in your own organization is a great way to make this a habit.
Heyl Truck Lines provides high performance levels to help customers achieve high OTD percentage, says Bruce Koele, President: “We have dedicated customer service teams who work with customers focusing on their specific KPI’s and scorecards. This helps our customers avoid fines and retail chargebacks. Our CSR teams are long-tenured, experienced professionals who have worked with the same customers for decades. That deep knowledge of our customer, and what we’ve taken the time to learn about various retail fines and invoice deductions, has enabled Heyl to improve shipper scorecards and help the customer save money.”
Heyl is named a 2024 Top Food Chain Provider by Food Chain Digest. For more information, visit heyl.net.
Sponsored Content