

Let’s get automated
DEAR CUSTOMERS, our industry is changing rapidly, and automation is one of the most farreaching change drivers. Mining companies are embracing ever-higher levels of automation, and for good reason: it strengthens safety, machine utilization, and productivity and lowers energy consumption and total cost of ownership.
AUTOMATION GOES A LONG WAY toward protecting people. For example, customers can remove operators from dangerous areas by using Epiroc’s Rig Control System (RCS) and automated drilling, loading, and hauling. Our collision avoidance systems allow loaders and trucks to detect and avoid objects automatically. Our recently acquired company, Mernok Elektronik, further strengthens our position as the leading collision avoidance systems provider.
Another exciting new member of the Epiroc family is RCT, which provides mixedfleet automation and remote-control solutions, regardless of manufacturer or type of equipment. Many customers want to connect machines from different manufacturers and have these work together fully autonomously. We believe that automated mines will be the standard in the future.
ALMOST 10 000 OF OUR machines in operation are installed with RCS, making them automation-ready. We have enabled nearly 3 000 driverless machines, including a mixed fleet. About 500 Epiroc autonomous surface drill rigs have successfully drilled longer than the distance around the globe.
We want to support you in your entire production flow. For mining customers specifically, we want to create the mine of the future, fully automated from pit to port. We hope you will join us on this exciting journey.
On
my radar
Record acquisition
Our recent acquisition of Stanley Infrastructure is Epiroc’s largest ever. This will strengthen our presence in the excavator attachments and handheld hydraulic tools business.
Digital solutions
We are continuously launching digital solutions that allow customers to enhance their operations to become safer and more efficient.

Helena Hedblom Epiroc President and CEO
Epiroc
At a glance

Epiroc is a vital part of a sustainable society and is a global productivity partner for mining and construction customers. We develop and supply innovative and safe equipment and offer world-class service and other aftermarket support, as well as solutions for automation, digitalization and electrification. epiroc.com
With Epiroc as a dedicated partner, you get a passionate team that supports you in a sustainable, efficient and safe way. No challenge is too big for our curiosity and persistence when it comes to increasing your productivity, safety or sustainability. We lift your competitive advantage through our continuous drive to make good things better – from highperformance equipment and service excellence to building the mining and construction industries of tomorrow.
Epiroc Group – get to know us better
What we strive for Accelerate the transformation
The world needs metals and minerals for the energy transition. And we need cities that can cope with a growing population in a sustainable way. To succeed, we need to speed up the shift toward a more sustainable mining and construction industry. We at Epiroc accelerate this transformation.
Autonomous Pit Viper rig transforms drilling Triple boost for safe, sustainable and efficient mining
Fully autonomous drilling
Complete an entire drill pattern autonomously without an operator on board, increasing safety and productivity.
Automatic bit changer
Allow the operator to quickly change bits from a control room.
Control your whole fleet
With our digital solutions like Mobius for Drills, one operator can control and optimize an entire fleet.
Epiroc Group In numbers
22% higher productivity than conventional drilling. 80% reduction in bit change time with no manual handling. 70% increase in compliance to plan, meaning less waste and more efficiency.
Global presence Average employees
18 000+
More than 18 000 employees. Customers in around 150 countries. 151 years of experience.
Revenue in 2023: SEK 60.3 billion.
AUTOMATION
While we still need manual labor, automated solutions are surging forward. What challenges do we have to overcome?
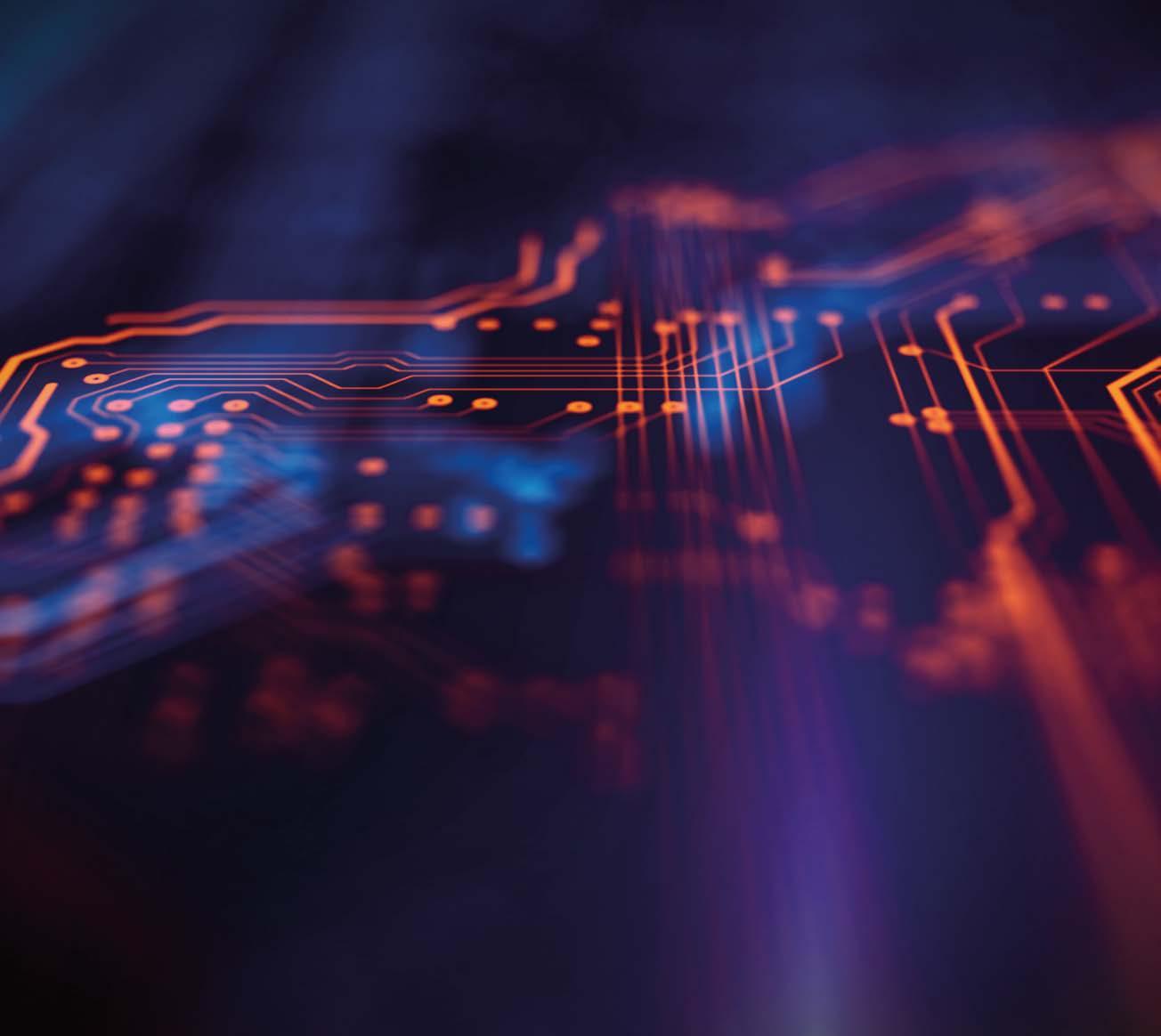
16
A scoop for space exploration
Japanese start-up ispace wants to accelerate space development. When the company needed a lightweight scoop for a lunar mission, getting in touch with Epiroc was a no-brainer.
WORKINGS
Clean air just in time
Ventilation in underground mines can be very costly. To avoid unnecessary energy consumption, Epiroc’s Meglab-produced Imagine solution can do wonders.
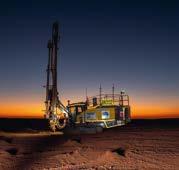
46
SUSTAINABILITY
Enabling women in mining
Finally, it’s possible for women to work underground as well as in open pit mines in India. To further diversity in mining, Epiroc India initiated a successful trainee program.
Autonomous operations are becoming increasingly important in the mining industry. A new version of Epiroc’s SmartROC D65 Autonomous drill rig, with great potential to improve productivity and increase safety, has been tested by Fortescue Ltd at the Iron Bridge mine in Australia.

The world’s largest mining event — MINExpo International, which takes place every three years — is returning this fall. The show is owned and produced by the National Mining Association, and this edition will be held September 24-26 at the Las Vegas Convention Center. www.minexpo.com

Autonomous future
At the Iron Bridge mine in Western Australia, the SmartROC D65 MKII
Autonomous is being tasked with drilling under various conditions.

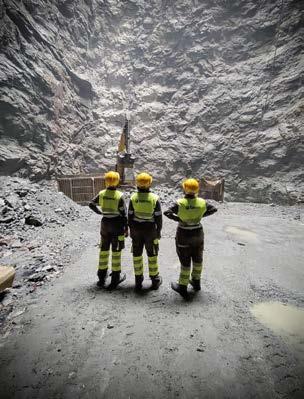
46

Selected highlights
06 EPIROC IN BRIEF
Keep tabs on what’s happening in the world of Epiroc.
14 FOLLOW-UP
SmartROC rigs transform operations for Explosia.
26 OUR CHALLENGE
The impact of mining had to be minimized for new neighbors of the Todaka Mine. SmartROC C50 made a big difference.
44 MY WORK
John Barbagallo, CEO at CR Mining, wants to help build confidence.
48 BLAST FROM THE PAST
Top-notch raiseboring equipment from Epiroc paved the way for Olympic travelers.
50 AROUND THE WORLD IN BRIEF
Assorted news from the mining industry.
Mining & Construction is published by Epiroc. The magazine focuses on the company’s know-how, products and methods used for mining and construction worldwide.
Address: Epiroc Rock Drills AB, SE-701 91 Örebro, Sweden
Web: epiroc.com
Phone: +46 (0)10 755 00 00
Publisher
Anna Dahlman Herrgård
Email: anna.dahlman. herrgard@epiroc.com
Editor Gustaf Höök
Email: gustaf@rubrik.se
Editorial Board
Anna Dahlman Herrgård, Ann-Sofie Andersson, Hanna Håll, Nurgül Atayer, Fredrik Ternström
Editorial Production & Art Direction/Layout
Rubrik AB, Masthamnsgatan 5, SE-413 29
Gothenburg, Sweden
Phone: +46 (0)31 719 06 00
Web: rubrik.se
Printed by Prinfo Welins, Sweden
Trademarks and reproduction of articles
All Epiroc product names (including but not limited to Pit Viper, Boomer, SmartROC, COP and Secoroc) are registered trademarks of one or more Epiroc companies. For questions regarding free reproduction of articles, photos or artwork in this magazine, please contact the editor or the publisher.
Safety first
Epiroc is committed to complying with or exceeding all global and local rules and regulations on personal safety. However, some photographs in this magazine may show circumstances that are beyond our control. All users of Epiroc equipment are urged to think safety first and always use proper Personal Protective Equipment (PPE) as required to minimize the risk of personal injury.
LENKA WAJGLOVA
EPIROC IN BRIEF
Epiroc BEVs support AF Ghella in tunneling project
The City of Oslo is building a new drinking water supply and distribution system. The construction of the tunneling network is being carried out by AF Ghella, a joint venture consisting of AF Gruppen (Norway) and Ghella (Italy). The City of Oslo has set strict contractual requirements for the use of zero-emission technology, and AF Ghella now operates several of Epiroc’s material handling BEVs, such as the Minetruck MT42 SG and the Scooptram ST14 SG loader, with Batteries as a Service.
“AF Ghella chose equipment from Epiroc for several reasons,” says Nils Ola Hoff, Project Director, AF Anlegg. “We have collaborated closely with Epiroc for many years and continue to do so, and AF Ghella is well-acquainted with both the organization and its products. Epiroc was able to deliver equipment in a short time, which was especially

important in this project. Apart from some small start-up challenges, the equipment has worked well, and we are very satisfied with both the equipment and support from Epiroc in Norway as well as Sweden.”
AFTER HAVING BEEN used exclusively up to now for mining operations, this is the first time Epiroc’s market-leading battery-electric machines are supporting a civil construction project.
“Epiroc’s battery-electric machines are being increasingly utilized in underground operations, generating significant benefits, including reduced emissions, lower noise, less heat and
vibration, and significantly increased productivity,” says Sarah Hoffman, Vice President Sales & Marketing, Epiroc Underground division. “We are proud that AF Ghella is using Epiroc equipment for such an important civil construction project in Oslo city. Together, we are accelerating the transformation toward more sustainable construction operations. This project showcases the enormous potential our battery-electric solutions have in civil infrastructure applications.”
The construction project began in 2022 and is scheduled to be completed in 2027. The project already used Epiroc Boomer face drilling rigs.
Battery-electric field-test with Capital
Limited
THE DEMAND FOR zero emission or low emissions is high, as the world is pushing for a transition from fossil-fueldriven equipment to sustainably powered rigs.. Epiroc has now partnered with leading mining services company Capital Lim-
ited to field-test the innovative SmartROC D65 BE, a batteryelectric surface drill rig for the mining and construction industry. The battery-electric version of the well-known SmartROC D65 rig will be tested in Capital Limited’s operations in 2024.
Epiroc launches new digital solutions for surface mining
WITH OVER 10 YEARS of experience and 40+ installations globally, Epiroc is now taking the safety technologies (previously called Mobilaris Mining Intelligence) to the surface mining market. The launch for surface mines
includes the new release for safe blasting, Blast Support. The offering entails a new release of Situational Awareness, which now features the capability for direct warning messages to people located in defined risk zones.
Construction of the tunneling network in Oslo began in 2022 and is scheduled for completion in 2027. The project already uses Epiroc Boomer face drilling rigs.
EPIROC
Gustaf Höök
Product news and innovation stories (choose country and click Newsroom): epiroc.com
Epiroc corporate press releases (click Media): epirocgroup.com
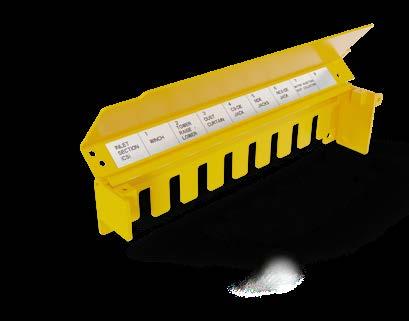
Spool valve guard enhancing safety
DEVELOPED FOR THE Pit Viper 270 series and Pit Viper 351 blast hole drill rigs, Epiroc has launched the Spool valve guard kit. The firstever global product developed by the Epiroc Innovation Station (an internal system for generating new ideas), it helps to lock out the 2, 7, 8, and 11 spool valve manual actuation points and reduces exposure to the risk of personnel working on the machine.
Epiroc surface drill rigs compatible with HVO100
EPIROC SURFACE DRILL RIGS are now verified compatible with HVO100, a hydrotreated vegetable oil that reduces greenhouse gas emissions from diesel engines. A diesel engine running on HVO100 produces up to 90% less harmful emissions, including greenhouse gases and particulates, when compared with an engine running on fossil-based diesel fuel.
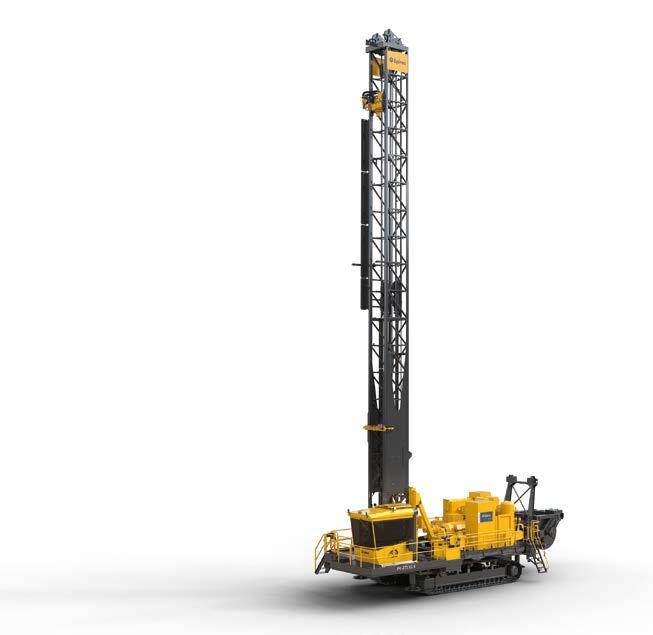
All three rigs are supported by a substantial 42-ton (80 000 lb.) bit load capacity that ensures reliable and effective drilling.
Epiroc has launched three all-new electric Pit Viper drills; Pit Viper 271 XC E (pictured), Pit Viper 275 XC E, and Pit Viper 291 E. Part of its Smart and Green Series, the electric-powered drills deliver the same groundbreaking performance with zero exhaust emissions, zero fuel consumption, and a lower carbon footprint. With this release, Epiroc now provides electric alternatives for each drill in the Pit Viper series.
AI and automation are linked in several ways. For instance, AI techniques can optimize and enhance automated systems.
How can Epiroc enable customers to employ AI?
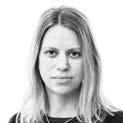
Kristin Nielsen Software Developer, Sweden
“We can create adaptive models that, when used in production, learn and adjust to the specific customer’s requests and needs. With user interfaces designed for the end user, everyone in the organization can be part of developing tailored functionality.”
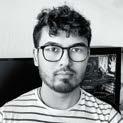
Edris Fatah Software Test Developer, Sweden
“From optimizing drilling patterns to predictive maintenance using machine learning, Epiroc enhances efficiency, safety, and sustainability in mining operations through AI-enabled solutions.”
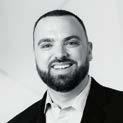
Zach Ellis Business Growth Manager, USA
“Epiroc enables miners to employ AI by providing rich data sets from our machines, allowing AI to perform analysis at speeds that humans cannot achieve on their own to make smarter decisions for a safer, more productive, and sustainable operation.”
FIGURE
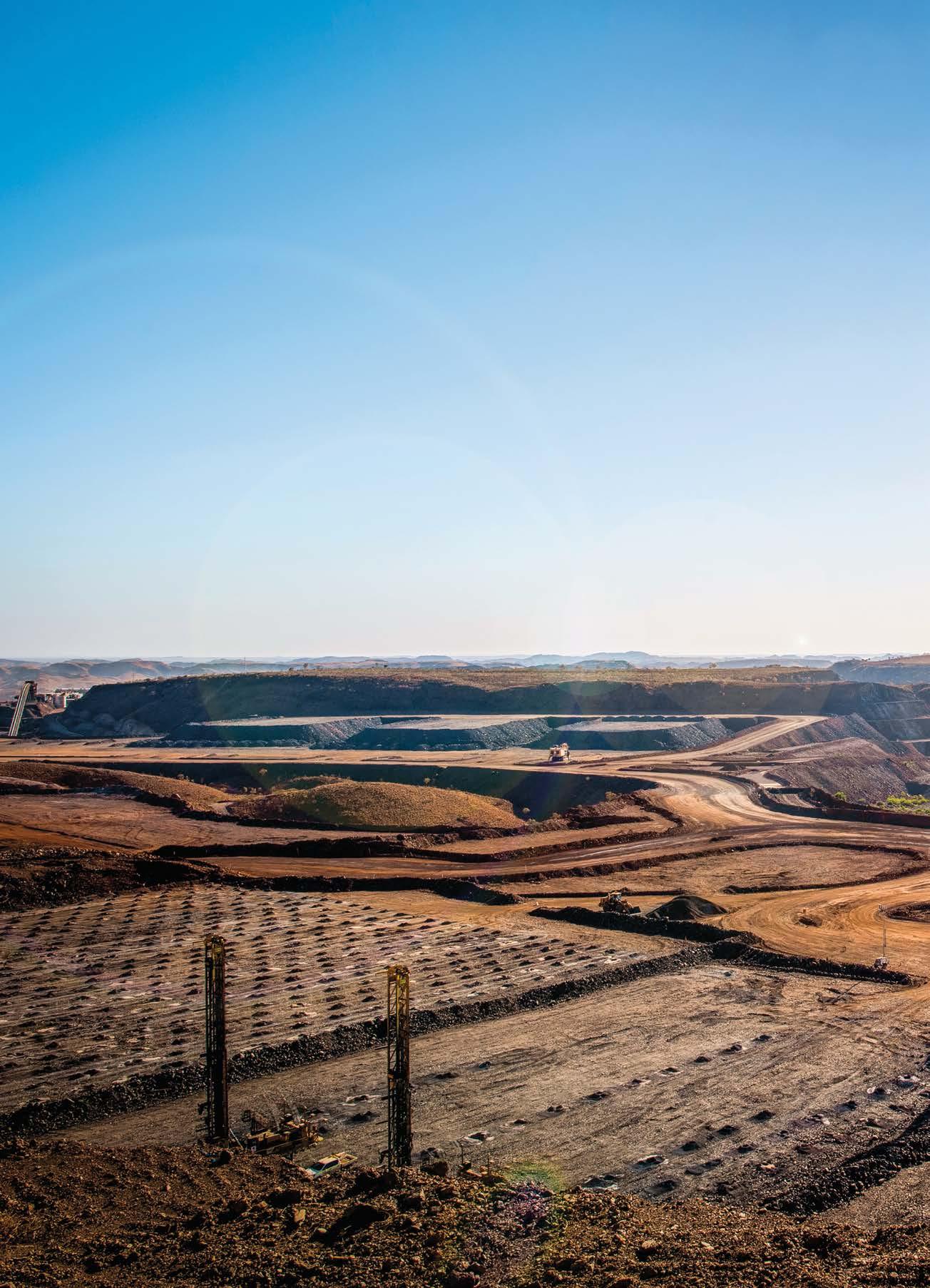
Partnership makes perfection
In the Australian Outback, Epiroc and Fortescue are working together to develop a drill rig that pushes the boundaries of autonomous mining.
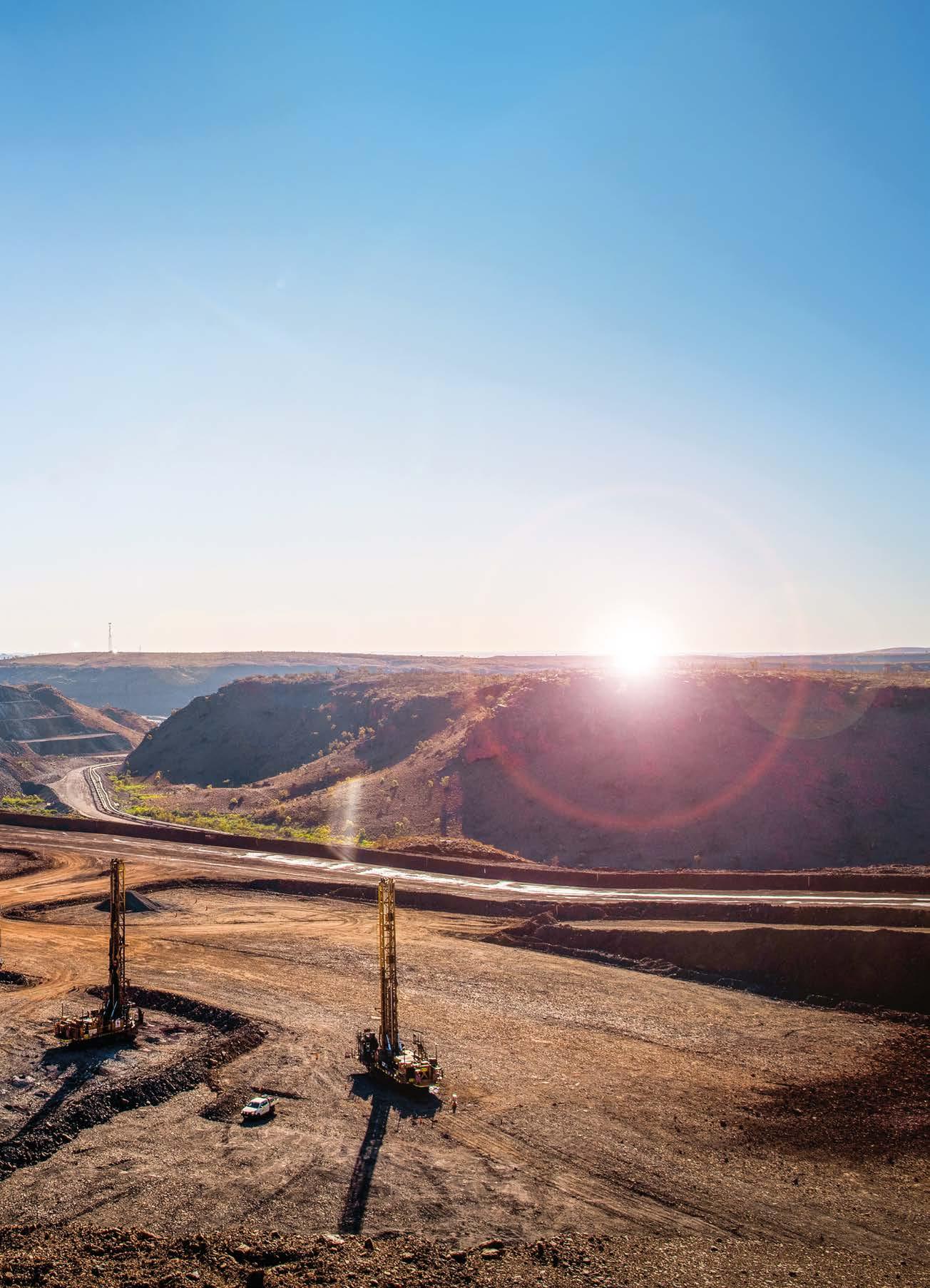
Pilbara is the ideal place to trial any equipment, autonomous or not, with summer temperatures here regularly eclipsing 45 degrees Celsius.
The
Matt Shea Bradley Kanaris
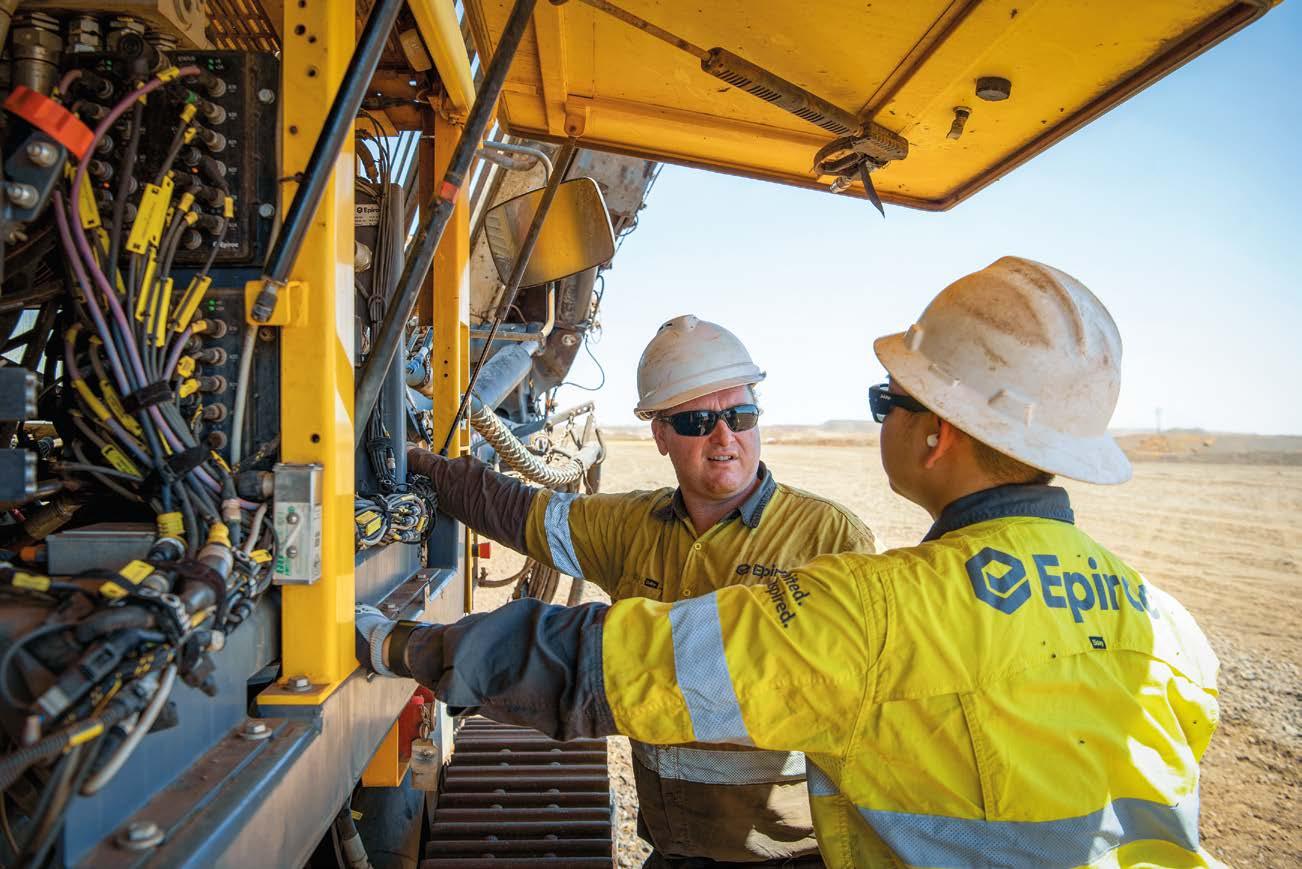
We’ve entered Nick Howlett’s sandpit. That’s what it feels like, anyway.
It’s deep in the Outback, 1 500 kilometers north of Perth. Take a 90-minute flight from the Western Australian capital, drive 20 minutes into the Iron Bridge mine, past its expansive camp, then past the mine’s operations center and towering crusher.
Wend your way further, climbing beyond the central pit, and there you’ll find an Epiroc SmartROC D65 surface drill working a drill pattern.
The rig finishes a hole, collects its pipes and trams to the next in the sequence. It could be a typical blast-drilling scene, but for one striking difference – there’s no operator in the cabin.
Five kilometers away, back down the
hill in the mine’s operations center, Howlett watches by video link as the SmartROC D65 drills another hole. And another. And then another. He smiles. Welcome to the future of autonomous mining.
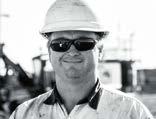
Iron Bridge is an ambitious joint venture mining project between Fortescue Metals Group subsidiary FMG Magnetite and Formosa Steel IB, the $US3.9 billion operation producing high-grade magnetite.
“It’s great to be working with Epiroc here at Iron Bridge and seeing the SmartROC D65 drill in action,” says Graham Howard, Director of Operations at Iron Bridge.
You can find an occasional shard of
magnetite sitting on the Martian-red earth. The beguiling black mineral is scorching hot under the 45-degree Celsius sun.
Those kinds of temperatures make this an ideal place to trial any equipment, autonomous or not. But Iron Bridge presents other opportunities to put this new test version of the SmartROC D65 Autonomous through its paces. The magnetite is buried in hard rock beneath meters of looser clay-like soil and then transitional earth, meaning the rig is drilling under various conditions.
“We want that,” says Howlett, an Epiroc Automation Specialist. “It’s how we develop and make a good product.”
Fortescue has a reputation for being a forward-thinking mining house.
An Automation Specialist, Epiroc’s Nick Howlett (left) is on the frontlines of the company’s cutting edge developments in autonomous mining.
Nick Howlett Automation Specialist, Epiroc
It has been pursuing autonomous solutions for well over a decade, making it a natural partner in the SmartROC D65 Autonomous program.
Epiroc and Fortescue entered a partnership in 2021 to trial this MKII version of Epiroc’s SmartROC D65 Autonomous. This project followed a 2018 SmartROC D65 Autonomous MKI pilot project in Canada. A successful test would provide Fortescue with an autonomous blast drill solution and Epiroc with vital test intel under realistic mining conditions.
“There’s no doubt autonomous is the way the industry’s going,” says Epiroc Australia General Manager and Managing Director Wayne Sterley. “And that speaks to the inherent productivity, efficiency and safety gains of autonomous solutions.”
An autonomous SmartROC D65 rig’s advantages aren’t down to pure speed but tend to accumulate over time via a clever use of autonomous subsystems and the high quality and consistency of the holes it produces.
“A manual operator could maybe beat us over an hour or so, but that’s not what it’s about,” Howlett says. “It’s about consistency. When the operator goes for a break, we drill. If there’s blasting nearby, we drill. And our shift changes tend to be shorter.
“We’ve spent a lot of time perfecting how the rig drills autonomously, including water control, how it starts a hole, and the tricky aspects of collaring. We’ve also tuned it for different types of ground, with five different settings. You set these different parameters, the operator selects one and the drill gets to work.”
The SmartROC D65 Autonomous has also had an edge in pre-split drilling. At Iron Bridge, operators drill up to 30 meters at an angle, meaning it’s relatively easy for unintended deviations in holes. The autonomous rig has been more precise in these scenarios, making for better drilling predictions and, in
Fortescue
Established in 2003, the Western Australian-based Fortescue Ltd. now ships more than 190 million metric tons of iron ore annually. It is one of the most cost-effective iron ore producers in the world.
Fortescue has been pursuing automation and autonomous solutions for well over a decade. In 2012, it introduced its first autonomous haulage truck and was the first company in the world to deploy an autonomous haulage system on a commercial scale.
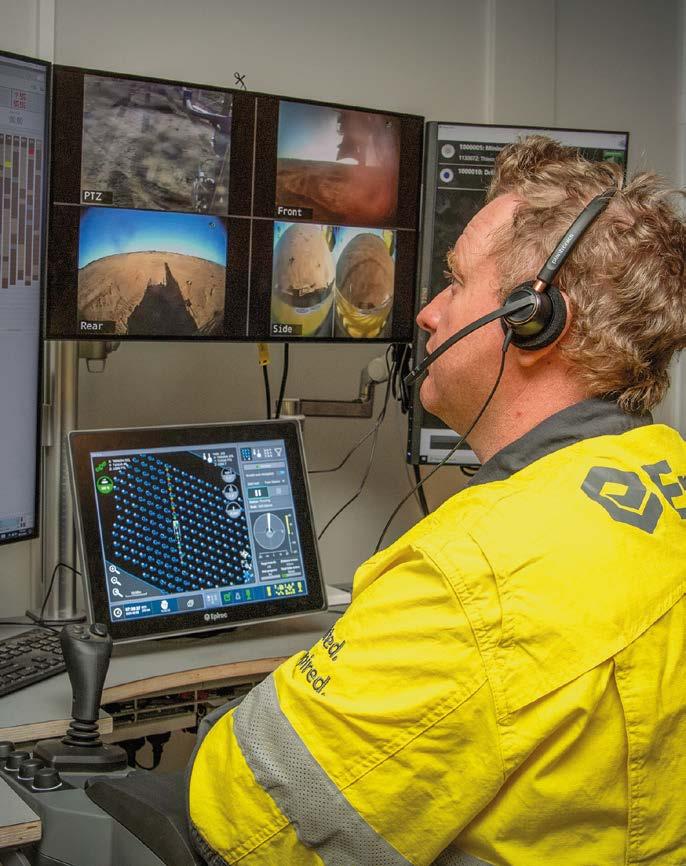

turn, easier drill plan adjustments.
Consistency also has positive impacts on equipment life cycles, with the SmartROC D65 MKII Autonomous rig’s autonomous algorithms utilizing components such as cylinders, feed chains, rotation heads, and rock drilling tools more optimally.
At its test site, the rig looks similar to a manually operated drill but features Lidar and cameras on the machine’s front, back and top. There are also automation mode (“safe-to-board”) lights for transitioning from remote to local operations. Surrounding traffic cones mark out the SmartROC D65 MKII Autonomous rig’s “geofence,” or perimeter of autonomous operations.
Still, the real magic happens at the tele remote station back at the Iron Bridge operations center. Howlett drives us down the hill to see it in action.
Nick Howlett operates the SmartROC D65 MKII Autonomous rig’s tele remote station inside Iron Bridge’s air-conditioned operations center.
Wayne Sterley General Manager and Managing Director, Epiroc Australia
“We have the opportunity to put people in a safer working environment, and help them be more productive and efficient”
Wayne Sterley General Manager
and Managing
Director, Epiroc Australia
Inside Iron Bridge’s air-conditioned nerve center is a hive of activity, with rows upon rows of personnel tapping away at workstations.
The SmartROC D65 MKII Autonomous rig’s tele remote station sits in a separate low-lit control room. It features two joysticks, a touch screen like that inside the rig, and three additional LCD screens that display critical operational information – hole and drill pattern progress, a video stream from the rig’s onboard camera system, and the drill’s technical state and alarms. And yet it just needs an internet connection and the station could be in Perth, where many Iron Bridge personnel live, or indeed anywhere in the world.
“Like any new tech, there’s been some skepticism,” Howlett says. “But [Fortescue] has begun to advertise for jobs
Epiroc and Fortescue
for autonomous operators and there’s been a lot of interest. One of the lads told me he sees it as an opportunity to see more of his family in Perth.”
“We have the opportunity to put people in a safer working environment, and help them be more productive and efficient,” Sterley adds. “By taking on this digital transformation, we’ll attract more talent into the industry.”
So, what’s next for the SmartROC D65 Autonomous program? After success at Iron Bridge, 2024 is about tackling autonomous contour mining at Fortescue’s nearby Solomon Hub.
“There’s a lot of knowledge about path planning and obstacle detection but not about tramming for contour operations,” Howlett says. “Those are wicked challenges. We’re looking forward to giving it a crack.”
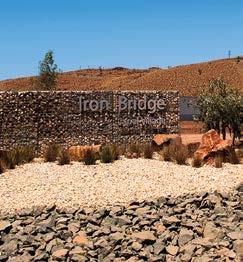
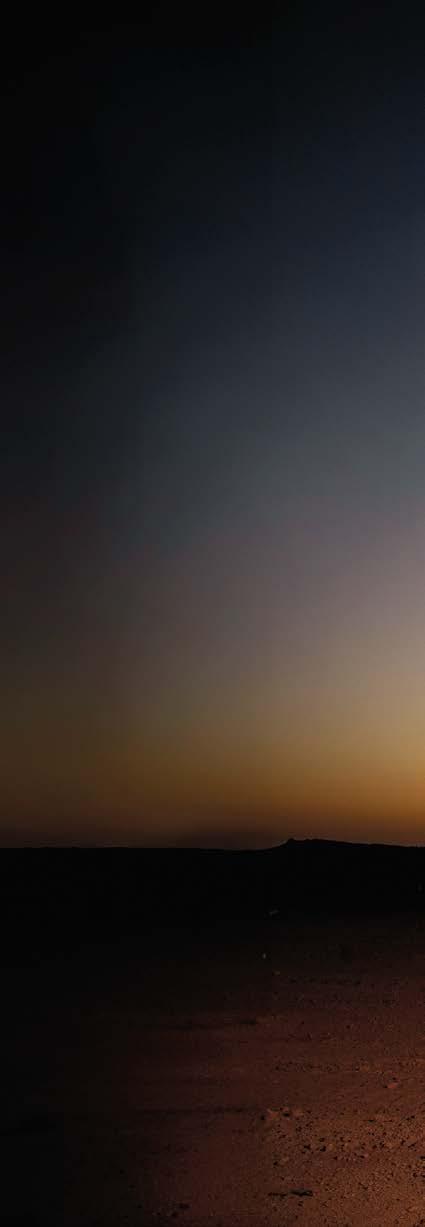
Located in the Pilbara in Western Australia, Iron Bridge is a joint venture between Fortescue Ltd subsidiary FMG Magnetite and Formosa Steel IB
The $US3.9 billion project produces high-grade magnetite, the high-ironcontent ore destined for Southeast Asia to help steelmakers reduce carbon emissions
Iron Bridge is part of a broader Fortescue strategy to raise the iron content of its product suite
Iron Bridge
Epiroc agreed to a partnership with Fortescue Ltd. in 2021 to use the SmartROC D65 MKII Autonomous on a Fortescue mine site for a trial period of at least 12 months. Iron Bridge Mine was selected as the best-fit site for the trial’s objectives. The trial began in 2022, and the rig hit production KPIs in May 2023.
Nick Howlett has been putting the Epiroc SmartROC D65 MKII Autonomous rig through its paces at Iron Bridge mine, 1 500 kilometers north of Perth.
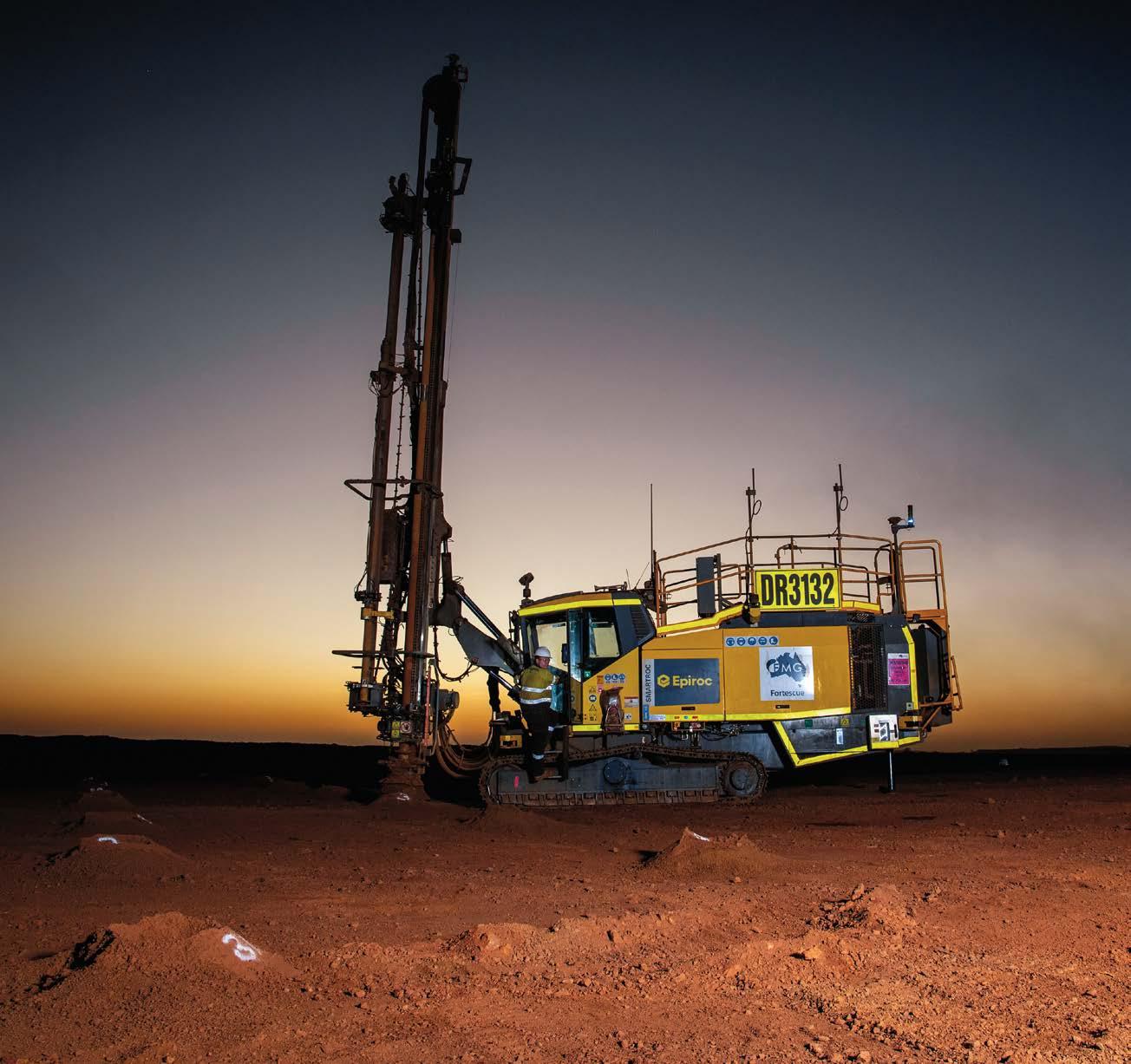
Five keys to success
Epiroc’s autonomous SmartROC D65 test program has benefited from having a willing partner like Fortescue. A successful test has provided Epiroc with valuable information under real-world mining conditions and Fortescue with a best-inclass autonomous solution.
The Australian Outback is a tough place to drill, and the SmartROC D65 MKII Autonomous has been tasked with drilling through different densities of earth and rock, making for ideal real-world test conditions.
Close collaboration onsite between the Iron Bridge and Epiroc teams has provided a continuous feedback flow. Thanks to direct communications with Epiroc’s programmers in Sweden, even minor software updates have been quickly delivered and applied.
Epiroc has been at the forefront of autonomous drilling since its first autonomous Pit Viper drill was released in 2014. It has made strategic agnostic autonomous acquisitions, giving it an edge when developing new products.
Success at Iron Bridge comes down to consistency with the SmartROC D65 MKII Autonomous capable of drilling during blasting and operator breaks. It has demonstrated a particular edge in production and pre-split drilling.
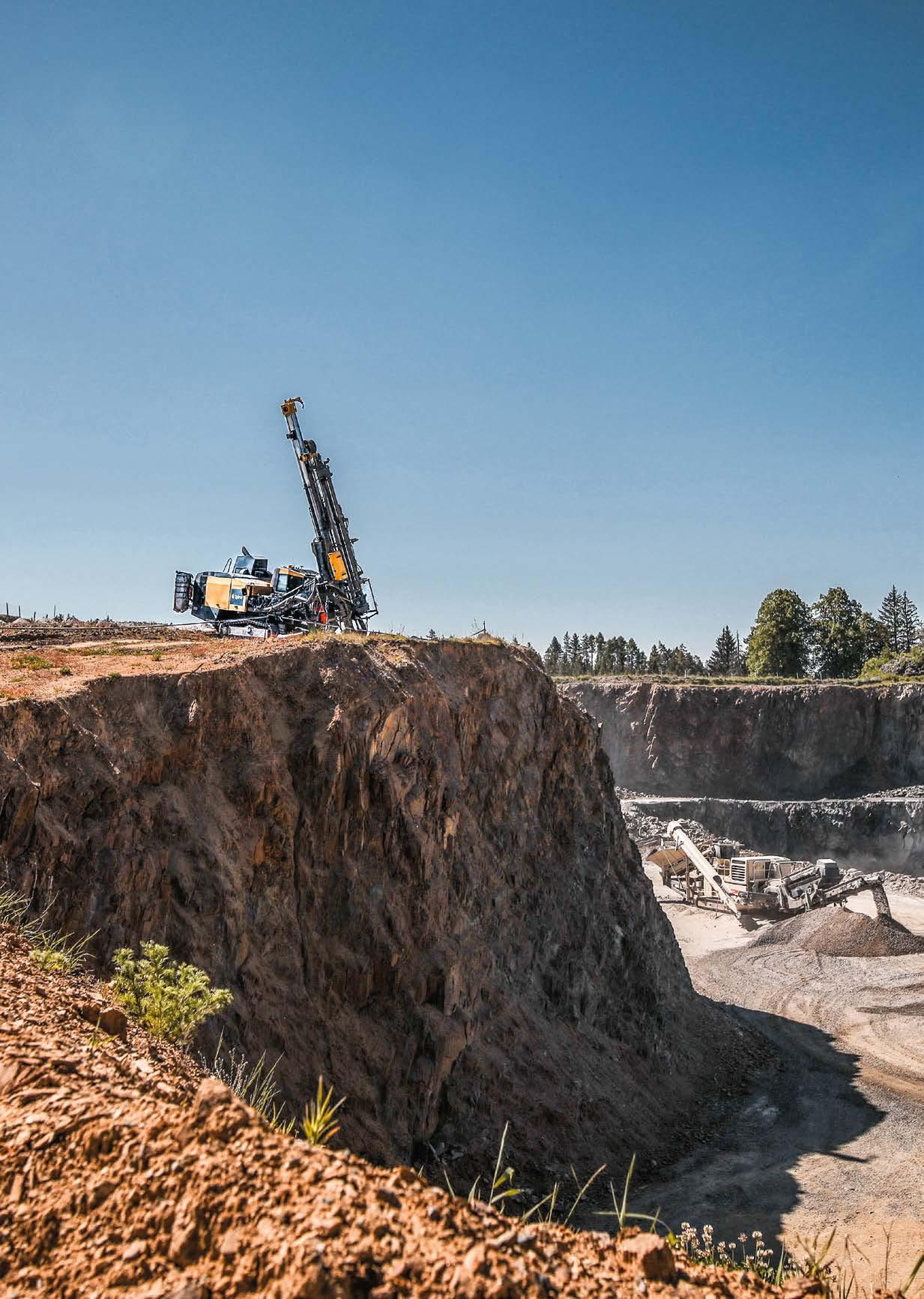
With the SmartROC D50, Explosia has significantly increased the number of meters drilled annually. Fuel consumption has dropped from 1.65 liters per drilled meter to 1.1 liters compared to the old rig.
FLEET TRANSFORMATION
For Explosia, an explosives and drilling company in the Czech Republic, renewing the fleet with SmartROC D50 and T40 drill rigs has brought higher productivity and lower fuel consumption.
THE FOSPOL DIVISION of Explosia provides drilling, blasting, secondary blasting, loading, and material collection in quarries throughout the Czech Republic. Until recently, the company’s machine fleet was aging, unproductive, and fraught with maintenance problems, with fuel consumption going through the roof. In 2020, however, Explosia started gradually replacing older drill rigs with brand-new SmartROC T40 and D50 machines from Epiroc. According to Přemysl Gromada, Head of the Drilling Group at Explosia, the effects on productivity, finances and emissions have been significant.
What difference does a rig like the SmartROC D50 you bought in 2021 make in your operations?
“It has made a huge contrast! The DTH – downthe-hole – drilling technique allows us to drill deeper. We can handle even hard rock like granite and better control the drilling process. It’s much more stable, and we get straighter holes. We get more meters drilled per year compared to the old rig, and fuel consumption has decreased from 1.65 liters per drilled meter to 1.1 liters. So, we get more done, using 33 percent less fuel. We had difficulty reaching our goals with the old machines, so the new rigs have improved everything.”
www.epiroc.com/smartroc-D50
You’re now working with HNS (Hole Navigation System), for example. Tell us a little about your experience.
“We can transfer our drill plans directly to the machine. The Hole Navigation System is an excellent application that saves a lot of time, work, and waste. We reach the right hole depths automatically and get more accurate results. Also, we do not have to exit the machine to measure results, which saves a lot of time. HNS will be very important in our work in the future.”
How has your staff handled the transition to more modern machines?
“It’s surprisingly easy to train people to use the new rigs, even without experience. I actually have a former postman and a former gardener working here now. We’ve built an outstanding team here.”
You have renewed your fleet with five rigs, including a few SmartROC T40 rigs. What is your experience with those?
“Compared to the old rigs, we have drilled almost double the distance per rig per year and nearly halved fuel consumption. With the new fleet, our total annual fuel savings are around 165 000 euros. That’s the equivalent of a new drill rig every three years. In addition, our emissions are much lower. Epiroc has greatly helped Explosia. I’m a very satisfied customer.”

Přemysl Gromada Head of Drilling Group, Explosia
CARLOS ESPEJEL
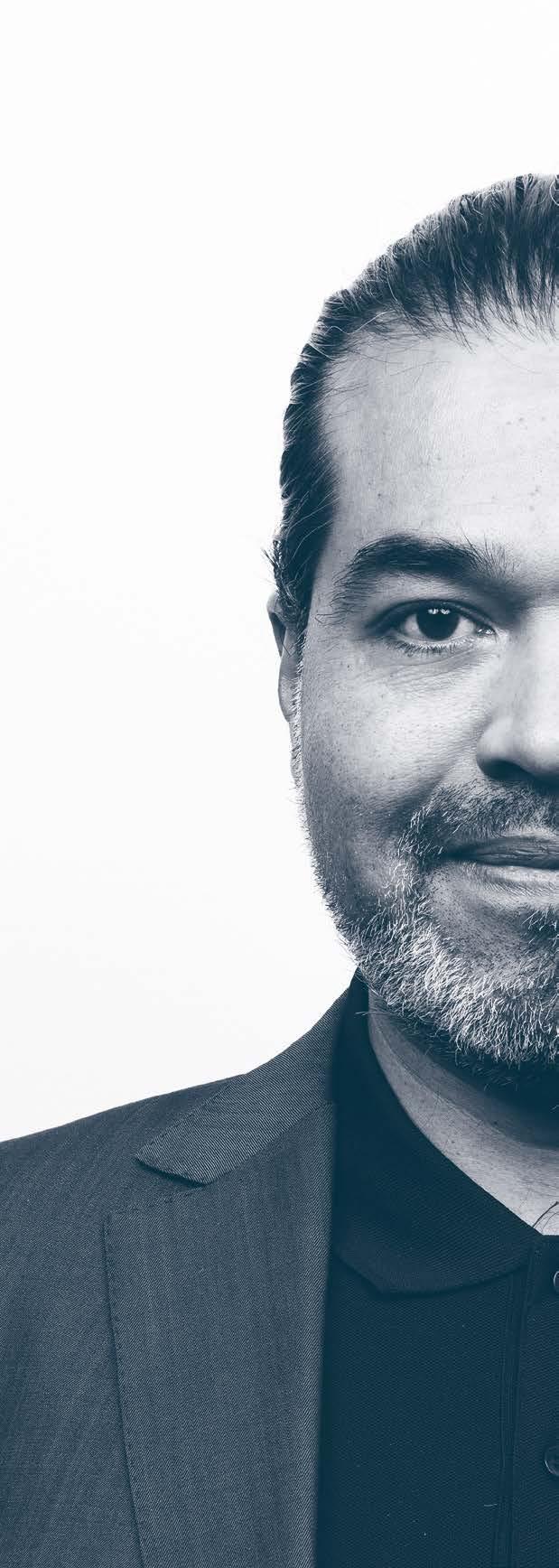
Joint mission to the
Expertise, trust and communication are the keys to a strong partnership
Outer space's resources remain untapped, offering unlimited potential. With focus firmly on the Moon, ispace is bringing Epiroc along for the ride.
mission Moon I
NTERNATIONAL LUNAR TRANSPORTATION and exploration company ispace – which has won two out of four of the world’s first Space resources collection contracts with NASA – and Epiroc have entered a long-term collaboration partnership. The companies will develop technologies and commercial services for NASA’s Lunar Resources Utilization and Lunar Construction initiatives.
The first joint activity between ispace and Epiroc revolves around ispace’s M2 mission, where ispace’s micro rover – equipped with Epiroc’s scoop, or regolith collection system – is scheduled to be operational on the Lunar surface after successful landing. The micro rover is to be delivered by ispace’s Resilience Lunar lander, which will be delivered by a rocket into space before it begins its journey to the Moon.
To succeed in sharing each other’s knowledge, the companies are building a relationship based on trust, understanding, and technical expertise. Miriam Bergvall, Global Manager of Acquisitions & Partnerships at Epiroc, and Carlos Espejel, Space Resources Utilization (SRU) Lead at ispace Europe, explain how this is made possible.
What sparked the partnership?
CARLOS ESPEJEL: “We’ve had our eyes on Epiroc for quite some time, having identified them as one of the best companies in drilling for the mining industry, underground extraction, and materials handling on Earth. In the long-term, these are activities and technologies that we are planning to perform and use on the Moon for resource exploration and eventual extraction.”
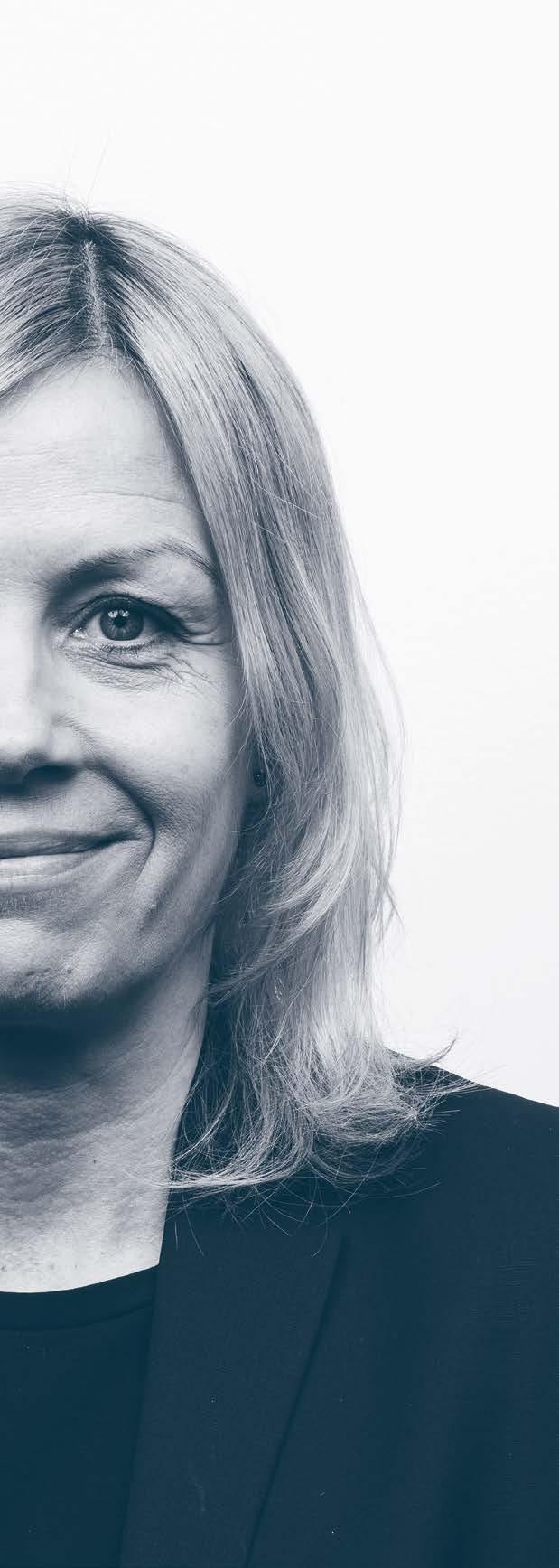
MIRIAM BERGVALL
Global Manager Acquisitions & Partnerships at Epiroc, based in Örebro, Sweden
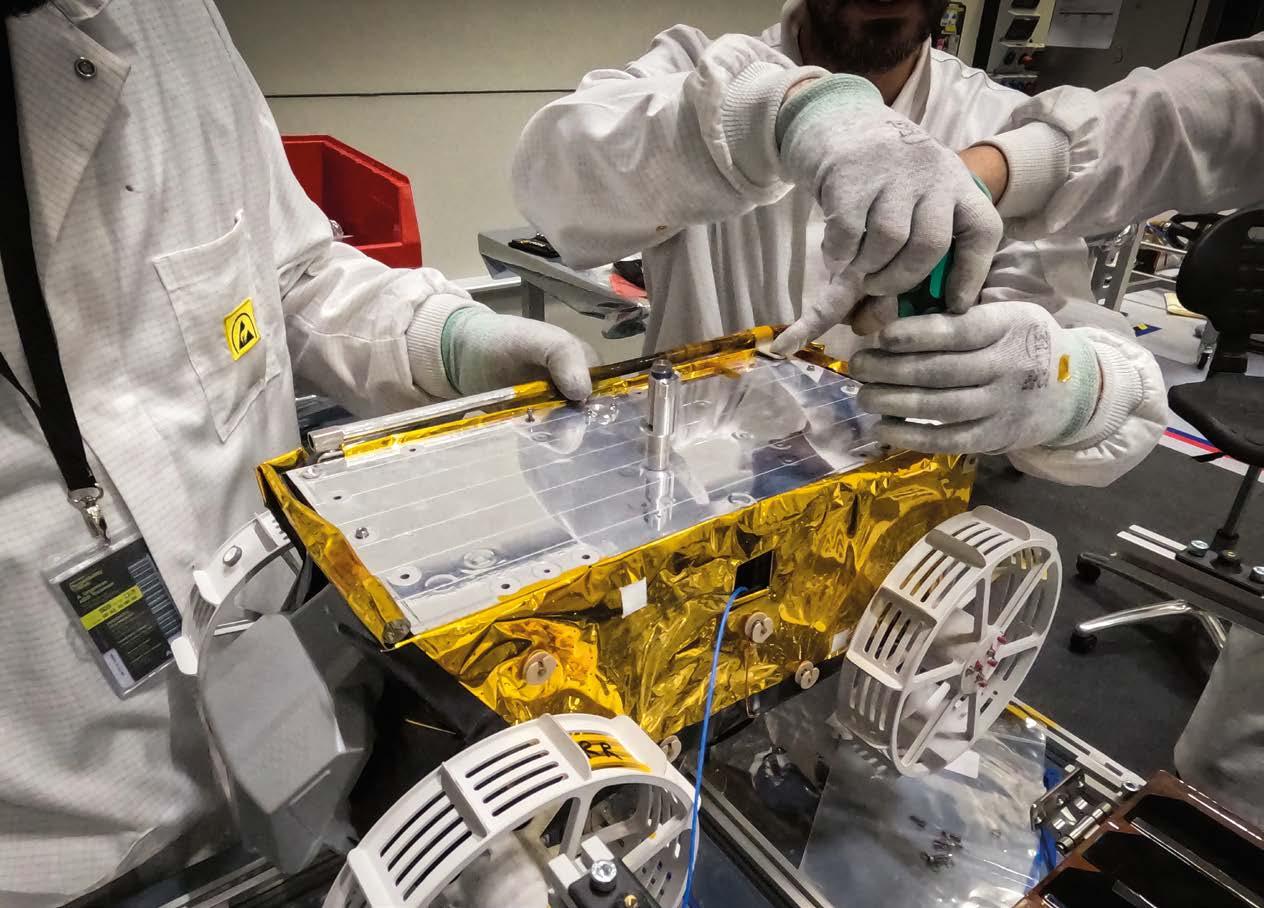
MIRIAM BERGVALL: “This opportunity represents Epiroc’s core values, which was the main reason for us entering a partnership with ispace. Their experience, knowledge, and NASA contracts also assured us they were the right partner to collaborate with. Initially, it sounded unreal, and it took some time to convince the organization that it was happening. Epiroc is going to the Moon!”
What are the similarities between working with equipment for underground conditions on Earth and conditions on the Moon?
CE: “There are a lot of similarities – but also new challenges. Firstly, temperatures on the Moon are extreme; near the equator, the temperature can range from 120 degrees Celsius to around –133. Similarly, underground operations can also face extreme temperatures. On the Lunar surface, there is an almost nonexistent atmosphere, which requires electrical systems, among others, similar to the ones used for underground mining. Also, there is no GPS signal underground, which, of course, is the case on the Moon as well.”
What have you learned from each other so far?
CE: “For instance, we were not completely aware of the stresses and forces involved on the Lunar rover when you operate a scoop – up, down, forward, and so on – as well as the visibility aspects of the operating camera used to operate the scoop remotely from Earth. Thanks to the support and requirements of Epiroc’s team, we redesigned an entire rover face, optimizing scoop and camera placement to match the tight field of view and volume requirements.”
MB: “Even though our equipment is often operated in harsh conditions, the Moon is different. On the Moon, it is extremely harsh, with extreme temperatures, high radiation levels, and a lack of atmosphere. Thanks to ispace, we have learned a lot about Moon conditions and how to develop a specialized product that can withstand this environment.”
The scoop will collect regolith from the surface of the Moon for historical NASA resource contracts. Can you elaborate a little on the design and development process?
CE: “We gave Epiroc strict requirements and restrictions regarding the scoop design and capabilities within the mechanical, thermal, and electrical domains. Very impressively, they achieved all requirements and more for the Lunar scoop.”
In Focus: ispace
Private Lunar exploration company with a vision to extend human presence on the Moon and support sustainable human life on Earth. The company’s next mission (M2) will launch as soon as Q4 2024 and be operational on the Moon in early 2025. Its task is to collect Lunar regolith for NASA’s historical Space Resources contracts.
www.ispace-inc.com More
• 300 employees
• Founded in 2010 in Tokyo, Japan, where the headquarters are based
• Additional offices in the US and Luxembourg
MB: “The right weight and size were crucial. Our project team did a great job designing and developing the scoop to be very light and small yet robust enough to endure the harsh environment. In addition to the scoop, we have also designed and developed the electronics and software to control it. Both design and coding have been kept simple to reduce risk. We only get one chance, so our solution has to be perfect.”
What’s the secret to the strong relationship between ispace and Epiroc?
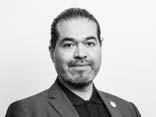

CE: “Firstly, our companies share similar working cultures and values, such as trust, respect, transparency, and proof by action. This made for a great match and was a deciding factor when developing the partnership. Miriam and I have meetings every second week, and the engineers even more often. We have high trust, communication, and space ambitions.”
MB: “I completely agree, Carlos. Both the technical and commercial teams have worked closely to accomplish this joint project. Despite not being in the same room as the ispace team for most of the time, our relationship has developed into a fruitful and long-term partnership.”
What’s your prediction on future space mining?
CE: “In the next twenty years, I can see us bringing larger or even full-size machines for exploration, mining and infrastructure on the Moon once larger landers are developed and Space X’s Starship is fully operational.”
MB: “Space mining in some form is going to happen, but some challenges need to be overcome first. Some examples are the cost of transporting mining equipment to the moon, establishing an infrastructure and maintaining the equipment with or without limited human support. It is an exciting journey, and I believe partnerships and consortiums between governmental, space, and commercial companies are crucial to making it happen.”
To find a solution for complex requirements on the Moon, expertise, vision, commitment and a perceptive mindset are required. Carlos Espejel (ispace) and Miriam Bergvall (Epiroc) share their advice on building a sustainable relationship.
Shared vision
Everyone involved needs to share the same vision, goals, and values to achieve this level of complex and meaningful projects.
Trust and transparency
Open and honest communication from both sides, where everything is on the table, and any issues can be handled quickly and flexibly with mutual understanding, respect and knowledge sharing.
Expertise and mature technology
Proven expertise (Moon and Earth) in engineering, commercial, and legal fields, coupled with cutting-edge technology, is a good foundation for a partnership.
www.epirocgroup.com/vision-and-beliefs More
Miriam Bergvall Global Manager Acquisitions & Partnerships, Epiroc
Carlos Espejel Space Resources Utilization Lead, ispace
The micro rover will be equipped with Epiroc’s Lunar scoop, which has an operating mass capacity of 300 grams. The scoop, manufactured with advanced materials, was 3D printed.
EPIROC IN BRIEF
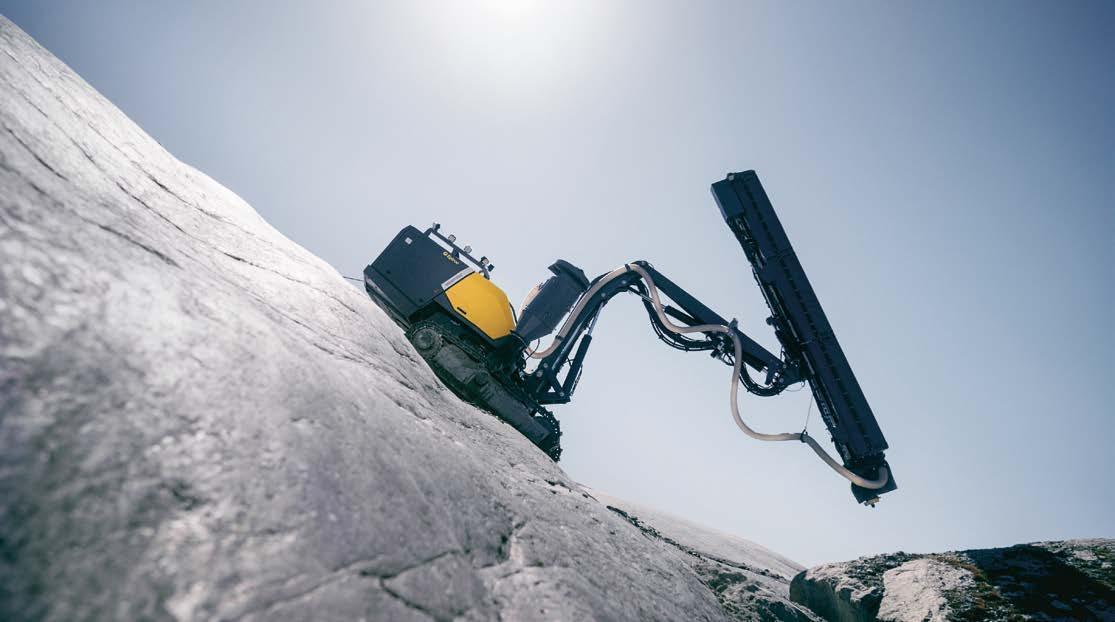
SmartROC T30 R is equipped with Epiroc’s Hole Navigation System (HNS), which reduces the amount of explosives and improves fuel efficiency – contributing to a reduced environmental footprint.
More meters per shift
EPIROC IS LAUNCHING SmartROC T30 R, a powerful surface radio remote drill rig built on the same flagship platform as the newly released SmartROC T25 R. The powerful model with 19 kW drilling power, developed for construction and quarrying, will provide operators with the highest technology and automation level in its segment, making everyday life easier
for the operator.
“Thanks to its drilling power, this rig can tackle big and demanding projects with ease. Compared to the versatile T25 R, with 14 kW, the T30 R can work in additional environments, helping to expand the options of this flagship platform,” says Marcus Leü, Global Product Manager at Epiroc.
SmartROC T30 R is equipped with
Epiroc wins large mining equipment order in Mexico
DUMAS CONTRACTING LTD., a leading full-service underground mining contractor providing services to mining companies throughout the Americas, has ordered a range of Epiroc machines for use at a new gold mine in Mexico. The order is valued at about SEK 195 million and includes rigs for face drilling, production drilling and rock reinforcement, as well as loaders
and mine trucks.
“We have several years of successful partnership with Dumas in Canada and the United States, and we are happy that we can now support them in Mexico so they can provide their mining clients with the best solutions possible to strengthen safety and productivity,” says Helena Hedblom, Epiroc’s President and CEO.

RCS hardware and software, facilitating onboard automation solutions. An automated rod handling system lets you add drill rods manually or automatically to reach the desired hole depth. The RCS also enables access to the Epiroc-developed Hole Navigation System (HNS), which ensures the highest quality of drilled holes and makes your operation a great deal safer and easier.
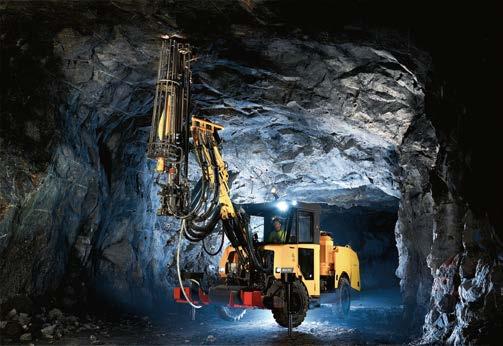
Marcus Leü Global Product Manager, Epiroc
Want to keep track of what’s happening in the mining and construction industry? Visit miningandconstruction.com for links to industry news and other interesting reading.
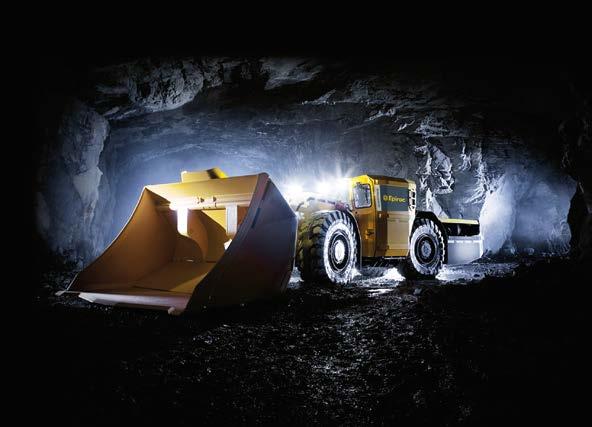
Epiroc wins large order in China
SHANDONG GOLD GROUP, one of China’s largest gold mining companies, has ordered a fleet of Epiroc mine trucks, loaders, and drill- and rock-reinforcement rigs to expand production at the Jiaojia, Xincheng, and Sanshandao gold mines.
Epiroc has supported the development of the Shandong Gold Group with various underground mining equipment since 1986.
“We have a long-standing and productive partnership with Shandong
Gold Group, and we are happy to continue supporting the company on its journey toward operations that are as safe and productive as possible,” says Helena Hedblom, Epiroc’s President and CEO.
The ordered equipment – valued at about MSEK 350 – includes the Minetruck MT2200 hauler, Scooptram ST1030 and Scooptram ST3.5 loaders, Boomer 282 face drilling rig, and Boltec S1K rock reinforcement rig.
EPIROC NEWS IN SHORT
01 02 03
Boom isolation kit launched
To advance safe productivity for customers, Epiroc has launched the Boom isolation kit for Boomer L1D, Boomer L2D, Boomer M1D, and Boomer M2D. The booms will be isolated during maintenance and service, ensuring no unexpected movement of the booms when operators enter the drilling area.
Epiroc + Stanley Infrastructure
Epiroc has acquired Stanley Infrastructure, a global manufacturer of excavator attachments and handheld hydraulic tools. The acquisition will strengthen Epiroc’s presence in the attachments business in infrastructure and construction, especially in the United States.
Majumder gets professorship
Epiroc’s Senior Principal Engineer, Dr. Ritwik Majumder, is set to take up an additional role as an Adjunct Associate Professor at Chalmers University of Technology. The collaboration between Epiroc and Chalmers will play an important role in Epiroc’s transition to an electric future.
Hello there! What’s happening online?

IN DECEMBER 2023, Epiroc launched a new platform for the online sales of spare parts and consumables. The service is targeted toward a select group of US customers, but over time, the scope of the platform and the number of markets and connected customers will expand.
What’s new in this solution?
“We have striven to bring the genuine Epiroc experience to the digital world. The site mimics and extends the capabilities of our customer centers. It is also highly customizable for the customer. For example, by entering the serial number of your machine you get immediate access to everything relevant.”
Why are you taking these steps?
“Customer experience is everything to us. It should be personalized, easier, faster, and more enjoyable. You are not simply buying a product –you buy our experience and partnership. A deeper and richer digital experience has been in demand, and we want to deliver the same worth and care digitally as we do in real life. We are stepping up our performance, with a warm touch.”
What’s next on the agenda?
“We will launch the full version in the US by the end of 2024, at which point we consolidate all the existing digital platforms into a single solution. In other words, customers will have a single point of entry into the full Epiroc experience. We also plan to extend this to other markets.”
The Epiroc Scooptram ST1030 loader is part of the order made by Shandong Gold Group.
Bianca Teti Digital Transformation Officer, Epiroc
Gustaf Höök & Christian Tarras Ericsson
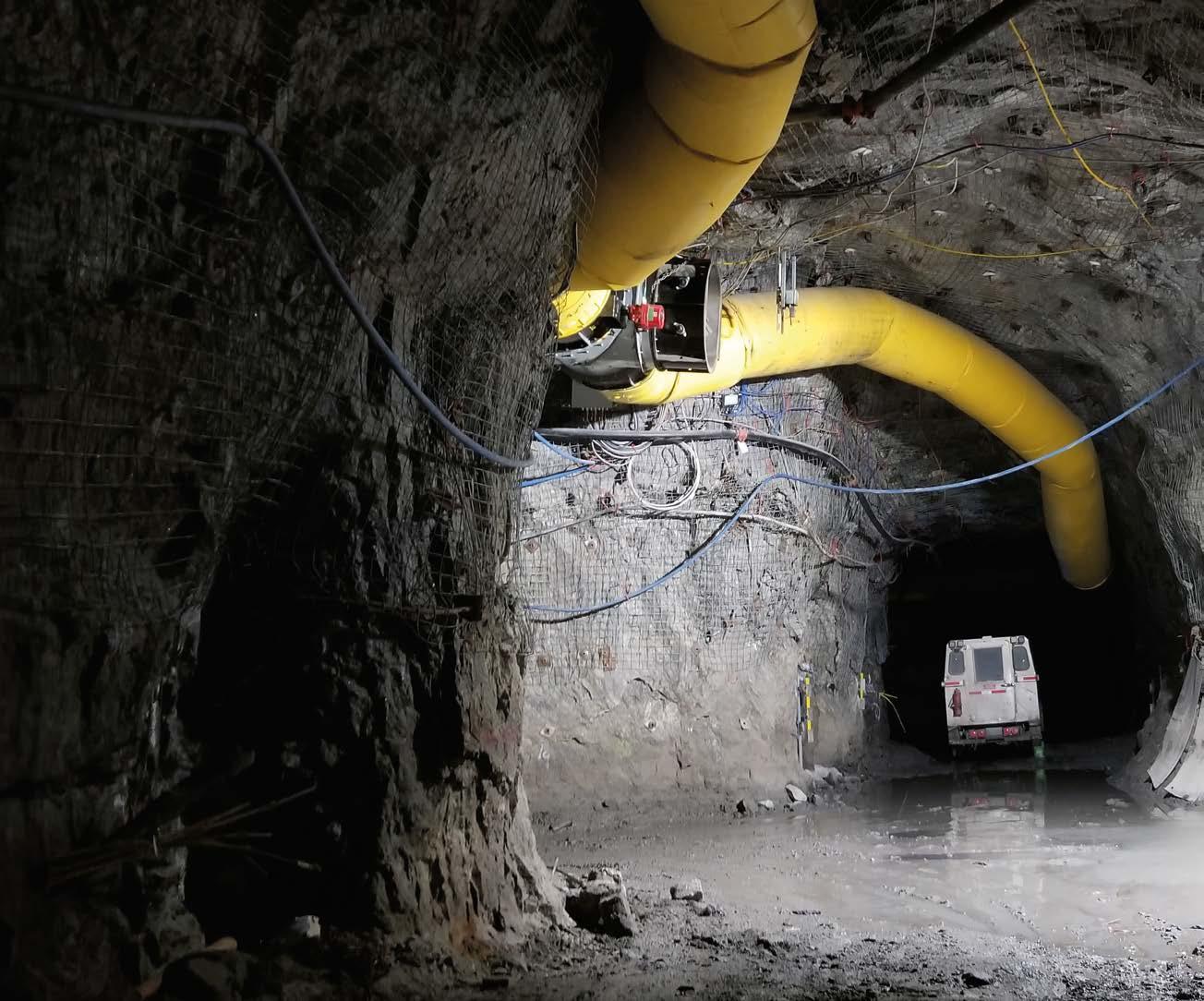
Epiroc’s revolutionary Ventilation on Demand technology is a game-changer in the mining industry. It significantly reduces energy consumption at the Borden gold mine in Canada by providing clean air precisely when needed.
A BREATH OF FRESH AIR
VENTILATION IS A vital service in underground mining.
Digging far into the Earth’s entrails, underground miners often encounter stale air or toxic gases that make life uncomfortable or impossible.
With the mechanization of mining in the last century, they have also faced potentially lethal fumes from their machines and vehicles.
A hundred years ago, coal miners took canaries underground to protect themselves from bad air. When the bird stopped singing – overcome by poisonous gases – the miners knew it was time to get out.
Thankfully, those days are long gone.
Modern underground mines are equipped with massive ventilation systems to ensure staff have a constant supply of clean air even when working hundreds of meters below the surface.
However, keeping the air flowing through a series of giant fans on the surface and each level is highly energy-intensive. The ventilation system is often the operation’s biggest electricity consumer.
As mining companies strive to cut costs to re-
main efficient and lower energy consumption to reduce their environmental footprint, any measure that can help to reduce that bill is welcome.
At its Borden mine in western Ontario, mining company Newmont has implemented a new automated Ventilation on Demand system – provided by Epiroc, through acquired company Meglab’s Imagine solution – which automatically adjusts the ventilation system’s operation as required.
“Historically, regardless of whether you have one truck or five trucks, you’re always pumping the maximum air underground, but it doesn’t have to be that way,” explains Mario Lachance, the Mine Superintendent at Borden mine, which has very high sustainability goals.
With Ventilation on Demand, air is pumped only to those areas as required in the volumes needed for the number of people and machines working there.
“If we are only working on the west sill, the automatic louvers will adjust to pump enough air just to the west sill and control the amount of air that is flowing to other sills,” explains Probel Varghese, a ventilation technician at Borden.
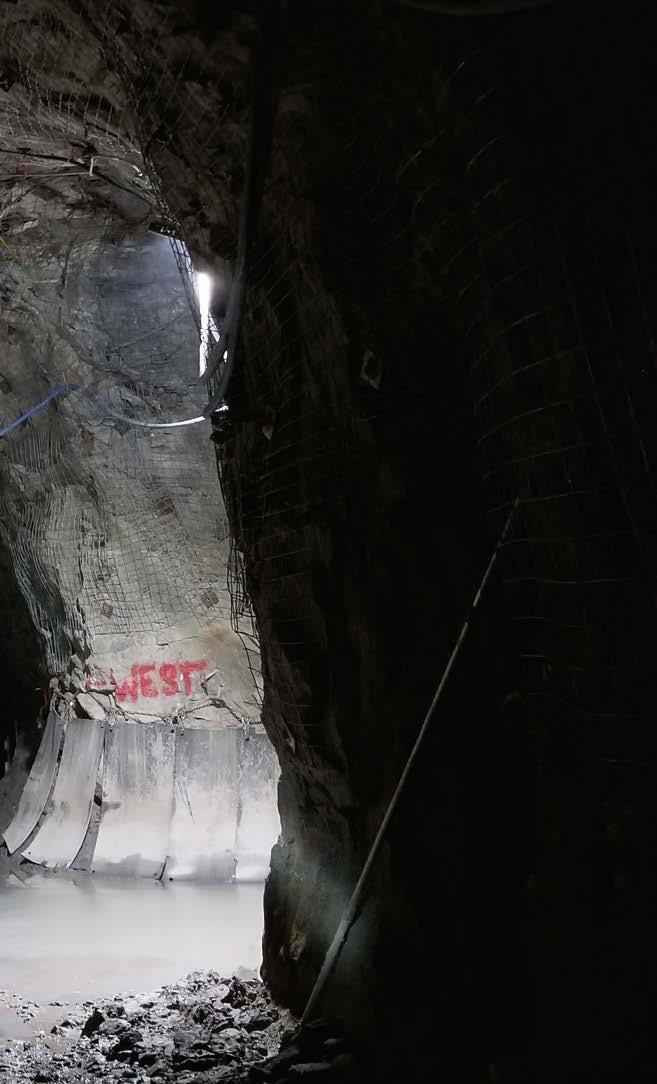
Given the importance of ventilation in the mine’s cost structure, the ventilation automation system has resulted in significant savings.
“By optimizing your electricity demand from a ventilation standpoint, it’s a big cost saver,” notes Lachance.
BUILT IN 2019, Borden is the latest addition to Newmont’s Porcupine complex of mines, which produced 7.9 million grams of gold in 2022. The deposit is located where mining has traditionally not taken place and near a lake popular with holidaymakers; the company was especially keen to minimize the mine’s environmental impact.
That has involved using many new technologies, including electric vehicles (which are quieter and cleaner) and burying large, noisy machinery, including air compressors.
“We just want to break that conception that mining is dirty, it’s dangerous, all that stuff,” explains Lachance.
LEARN MORE // Ventilation on Demand
One technology for a connected mine
Epiroc’s ventilation automation system evolves according to your needs, integrating data collected from a wide range of assets.
Tracking
The Imagine system allows operators and managers to track their KPIs in real-time to achieve their goals.
Ventilation automation
Each fan is linked to a terminal that can detect the presence of tags on workers and vehicles in a specific ventilation zone, adjusting airflow to their needs.
Proximity detection system
Gives the operator a rapid warning (visual and audio), signaling the presence and number of persons and/or vehicles around.
Mine evacuation
Orders an emergency evacuation of the mine via the miners’ lamps and monitors the progress of the mine rescue team.
Fleet management
Locates and manages all mobile equipment in the mine, showing its position, availability and status.
Tagboards and reports
Generates customized reports, as well as notifications and alerts.
However, Epiroc’s Ventilation on Demand technology has made a significant advance in automating the ventilation system, which is con- www.epiroc.com/sustainable-mining More
Newmont has implemented a new automated Ventilation on Demand system – which automatically adjusts the ventilation system’s operation as required – at its Borden mine in western Ontario.
Tom Azzopardi Patrick Gilbert
Fredrik Saarkoppel, Epiroc & Shutterstock
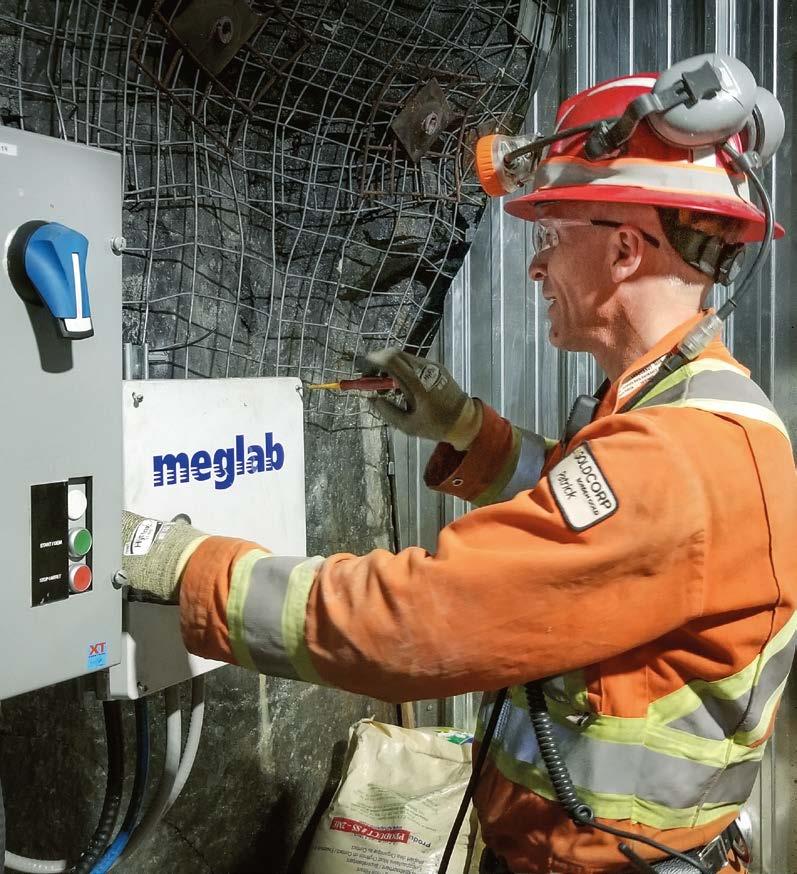
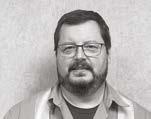
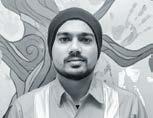
trolled by a computer that monitors the mine operation and calculates when and where fresh air is required.
Using a chip in each miner’s helmet lamp, equipment, and a series of anchor points throughout the mine, the system detects precisely how many people and vehicles are in each sector and automatically adjusts the airflow to meet their needs.
As workers move into a new sector, the software automatically switches on the right fans at the right level to ensure they have enough air.
As a result, the automated system has reduced the time mine staff need to dedicate to operating the ventilation system, freeing up workers to carry out other critical tasks.
Varghese notes that a traditional mine would require one worker to constantly monitor and adjust the ventilation system around the clock. At Borden, the mine’s dispatch can leave this in the hands of the automated system with minimal oversight.
Since installation, Epiroc staff have continued to work at Borden, supporting the extension of the ventilation system as the underground mine expands into new areas.
“Electrical engineering is clearly their forte and the support from the team has been very good. Seamless I would say,” comments Lachance.
Six success factors
Screen information is clockwise from the top left.
1. The operating status of each fan indicates air demand and distribution.
2. Fan start-up sequences can be easily set up according to requirements.
3. The system evolves as the mine grows.
4. Knowing the location of vehicles and their propulsion mode enables the supply of the right amount of air to a given area.
5. Another example of vehicle information, which leads to effective distribution of fresh air.
6. Real-time information from gas and airflow sensors ensures quality air for workers.
Newmont
Newmont is the world’s largest gold miner, operating over 20 mines in Africa, Australia, Latin America, the Caribbean, North America, and Papua New Guinea. Founded in Nevada in 1921 and listed on the New York Stock Exchange, it reached its current size after acquiring Canadian rival Goldcorp in 2019 for US $10 billion.
Workforce: 14 600 (2022)
Production: 170 million grams of gold, plus copper, silver, lead, and zinc (2022)
Market capitalization: US $38 billion (February 2024)
Mario Lachance Mine Superintendent, Borden
Electrician commissioning a new fan controller. The ventilation automation system has resulted in significant savings for Newmont, thanks to reduced energy consumption.
Probel Varghese Ventilation Technician, Borden
EMPOWERING AUTOMATION
The solution is dedicated to maximizing efficiency, ensuring safety, and optimizing resource utilization, from real-time monitoring to strategic decision-making.
Borden mine
The Borden mine is one of the group’s newest operations. Commissioned in 2019 by Goldcorp shortly before its takeover by Newmont, it is located near Chapleau, Ontario. The underground mine forms part of Newmont’s Porcupine complex, which produced 7.9 million grams of gold in 2022. Ore from the mine is transported by truck 180 kilometers to the Porcupine processing facility in Timmins.
Ventilation on Demand – three gains
Ensures good air quality for miners
Sends, in real-time, the right amount of fresh air to guarantee optimal work conditions.
Reduces energy consumption up to 50% Managing energy consumption decreases the mine footprint and offers substantial savings.
Maximum production in strategic locations
Maximizes production efficiency and safety in all active mining areas.
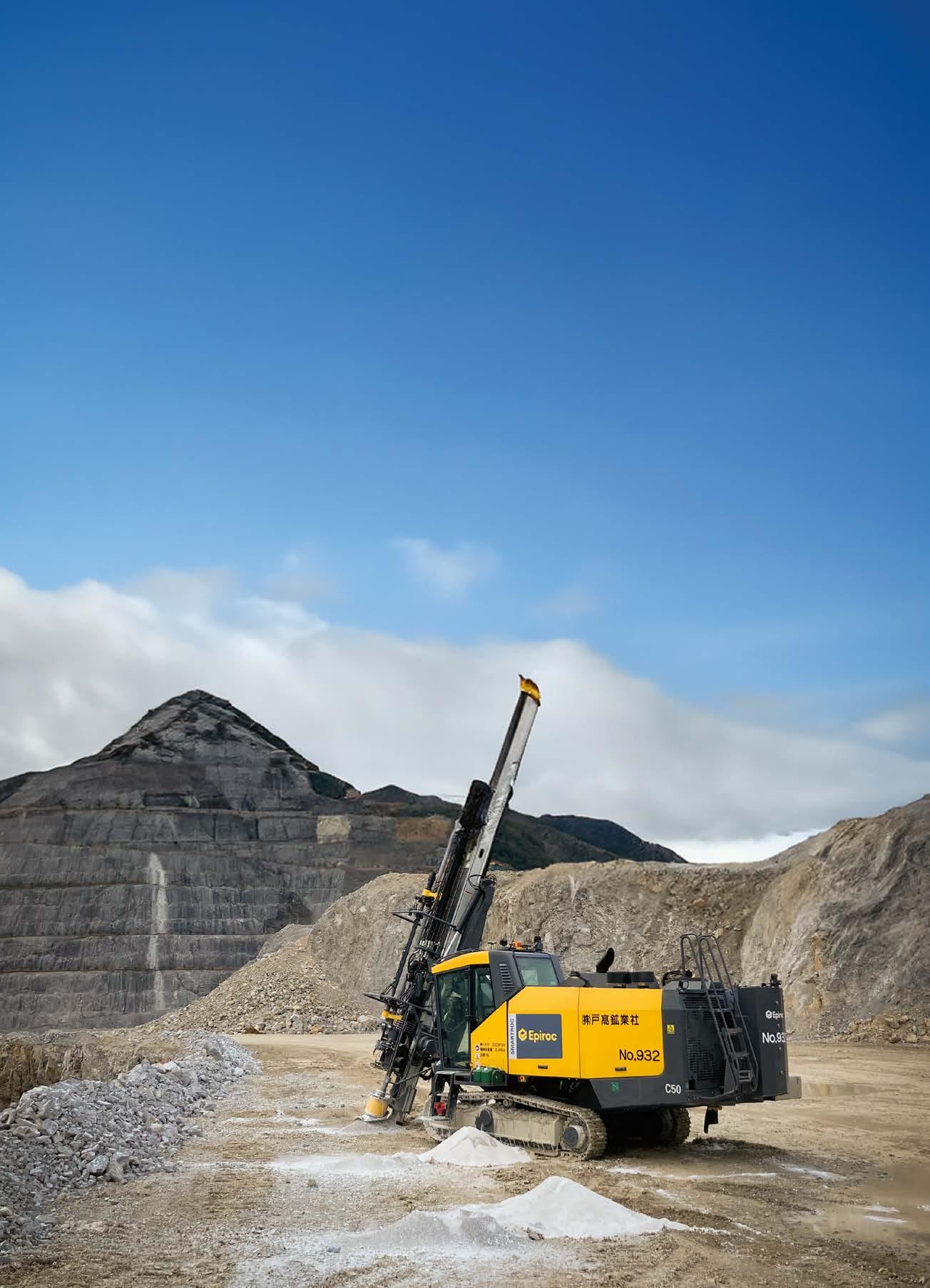
[ On Location ] Japan
QUIETERSMARTERAND
Out of respect for the nearby community, the Todaka Mine has reduced noise, vibrations and CO2 levels by upgrading to the SmartROC C50 with the COPROD system.
THE CHALLENGE 1
LOCATED IN the scenic Oita Prefecture – nestled on northern Kyushu, Japan’s third-largest island – the Todaka Mine is one of the biggest limestone mines in the country. It is operated by Todaka Mining Co., Ltd., a company that has been engaged in limestone mining since 1958 with the corporate philosophy “together with the local community.” Over the years, the expansion of the mine has gradually brought it closer to the surrounding communities.

“To conduct environmentally conscious operations considerate of nearby residential areas, it was necessary for Todaka Mining to minimize the generation of blasting noise, vibration, and CO2 emissions,” says Hidefumi Uchikura, Fukuoka Sales Branch Manager at Epiroc Japan, adding: “However, the drilling conditions at Todaka Mine present their own set of challenges. The presence of variable voids, clay, and water further complicates the mining process.”
THE SOLUTION 2
OVER THE COURSE of more than 40 years, Epiroc and Todaka Mining have built a strong partnership. To mitigate noise and vibration around the site, during the development of the Kono-Yato area, it was necessary to reduce the hole diameter without affecting production. Having first improved operations with the ROC F9CR drill rig, Todaka Mining selected the even better SmartROC C50.
“The SmartROC C50, along with the COPROD drill strings, was the perfect solution. By reducing the hole size from 165 millimeters to 127 millimeters, there was a significant decrease in noise levels and vibrations, and the machinery itself also operates at much
quieter levels, enhancing the work environment,” says Uchikura.
Epiroc’s COPROD rock drilling system combines excellent drilling speed of the tophammer with low fuel consumption, enhancing hole quality and straightness in down-the-hole drilling.
“In fact, the SmartROC C50 is currently one of the fastest, safest, and most efficient drill rigs on the market. The drilling cycle is fully automated, ensuring operational consistency and reducing dependence on operators,” says Uchikura.
Through joint consideration, Todaka Mining and Epiroc concluded that investing in this rig was wise, considering total ownership costs (TCO) and production costs of the final product.
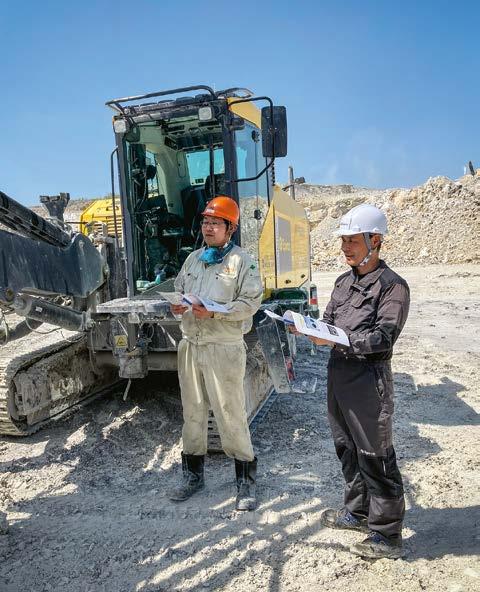
THE RESULT 3
SINCE INTRODUCING THE first SmartROC C50 in 2021, Todaka Mining added additional crawler drills of the same model in January 2021 and December 2023. These crawler drills are currently operating at full capacity in two shifts from early morning to late night. According to the client, production results have been very satisfying.
“Thanks to the SmartROC C50 and the crawler rigs, fuel consumption has been reduced from 38 liters (10 gallons) per hour to 20 liters (5 gallons) per hour. Also, because the SmartROC C50 reduces noise inside the operator’s cab, the operators’ work environment has improved,” says Uchikura, adding: “The SmartROC C50 is also very userfriendly for young operators, with joystick controls like gaming consoles. Thanks to this intuitive design, after one to two months, even beginners can operate the rig like experienced operators.”
www.epiroc.com/smartroc-c50
Hidefumi Uchikura Fukuoka Sales Branch Manager, Epiroc
Compared to competing products, the SmartROC C50 exhibits significant differences in radiated noise throughout the drilling process.
Maritha Arcos Hidefumi Uchikura (left) & Kazuyuki Sakimura (right)
ORIENTATION / ON SITE / PERSPECTIVE / SURVEY / SEVEN THINGS
AUTOMATION In Focus
Achieving autonomous processes takes a lot of old-fashioned labor. But new and improved technologies like artificial intelligence, big data and better connectivity certainly help. On the horizon, increased safety and productivity beckon. The automation train is rolling, and who knows where – if ever – it will stop.
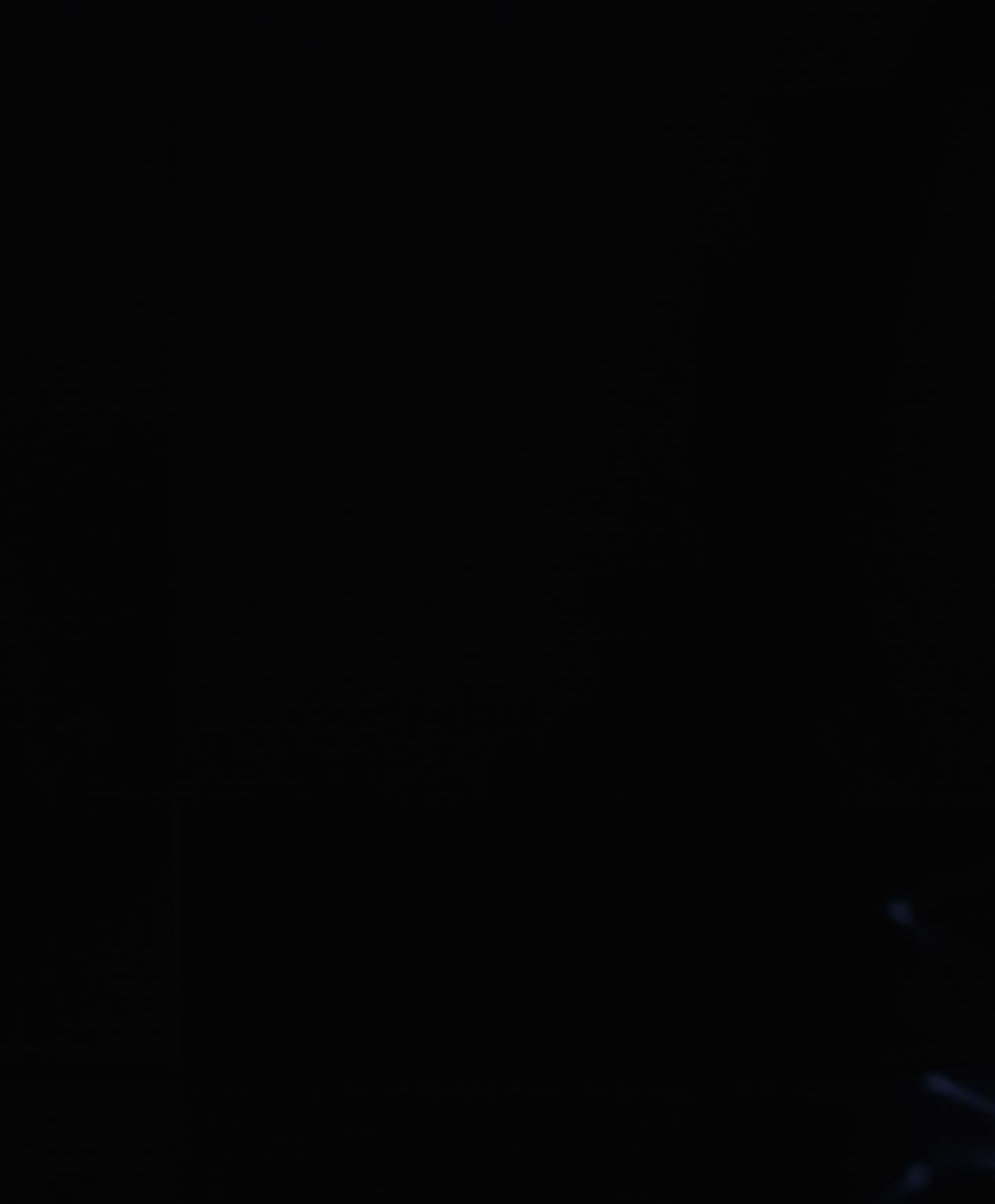
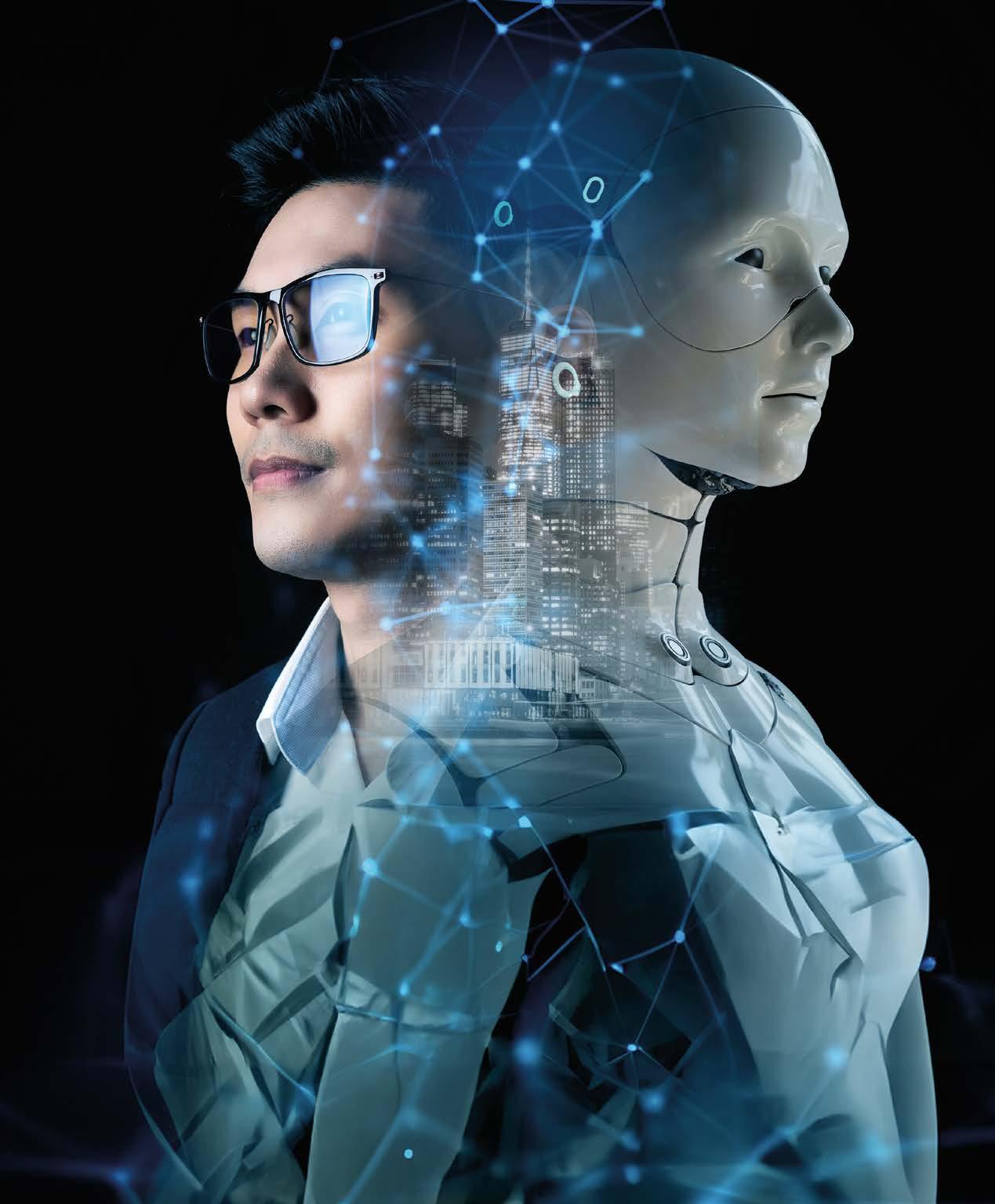
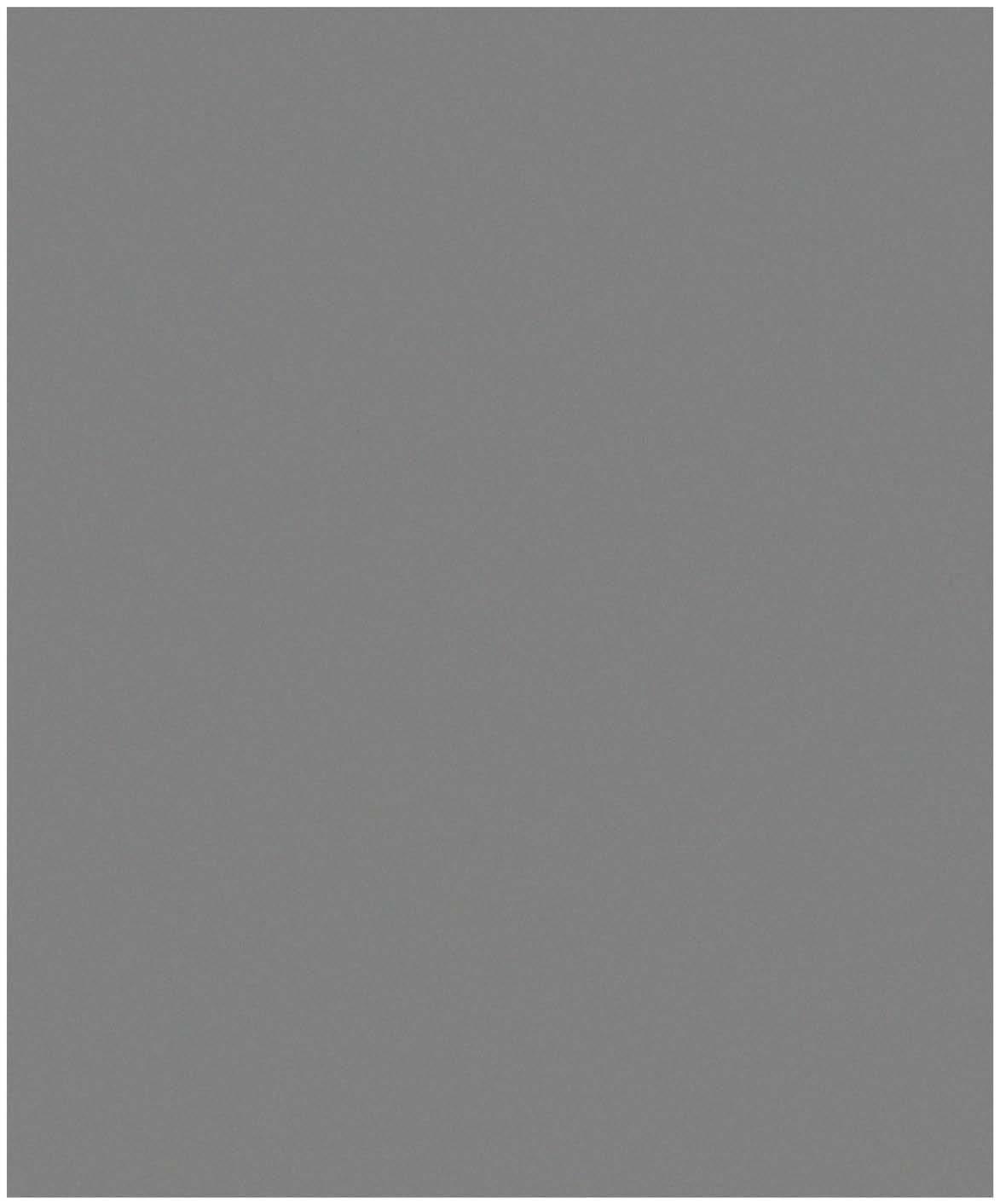
Automation is almost a passé concept — the word of the day is hyper-automation. What lies
Going all the way 28 32

Australian Epiroc company RCT is creating an automated pit-to-port concept, one solution at a time.
38 PERSPECTIVE Life-giving robots
Robot-assisted surgery has existed for decades, but incorporating machine learning and autonomy into procedures is fairly new. At Johns Hopkins, a robot that can suture intestines has been developed.
40
SURVEY The automated future
According to experts we have talked to, challenges ahead include human-AI interaction, energy efficiency, and integrating automation into existing systems. But there are ways to address the concerns.
41
SEVEN THINGS The other side
Automation brings blessings and progress, but the other side of the coin is removing the need for humans in certain job positions. Here is our take on jobs that the machines might take over.
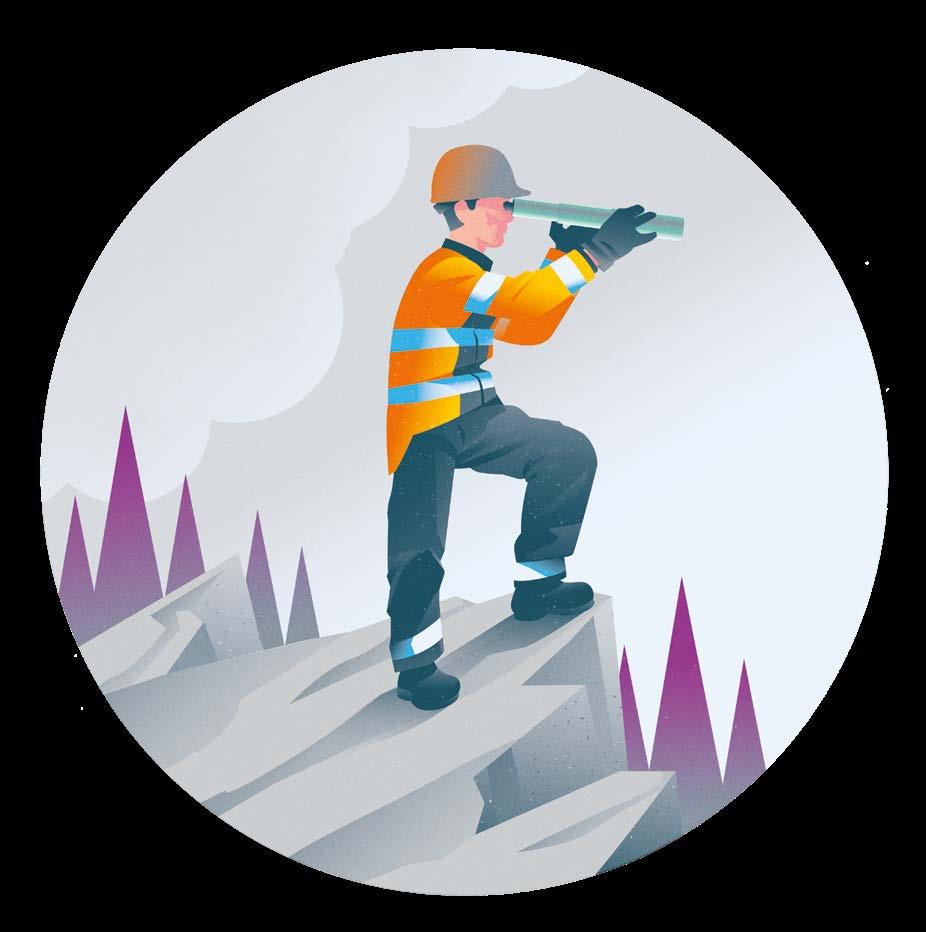
Artificial Intelligence, autonomous robots and automation processes that go further than ever before. Experts agree that the industry, thanks to technological innovations, will change fundamentally in the future. So, what’s next?
WHEN HENRY FORD in the early 1930s explained why he was earning money at the Edison Institute in Detroit, he said the Innovation Museum was a way to remind people of the importance of new inventions.
“If we’ve come so far, so fast, is it likely we would stop now?” wondered the car magnat.
In Ford’s factories, manufacturing had gradually evolved with the help of technical innovations since the early 1900s. So much so that in 1946, one of the employees, engineer D.S. Harder, began to use the word “automation” to describe what was happening on the floor.
Back then, he referred to advanced manufacturing plants and assembly lines; today the term describes rather how software-controlled machines perform automated work. But fundamentally, the meaning of automation is the same: using new technologies to create more efficient and productive processes.
“Automation has actually been around for thousands of years. Mechanical solutions that regulate water flow can be found early in history, and it is the same technology that lives on in today’s bathroom fixtures,” says Alf Isaksson at electrical equipment corporation ABB.
He has devoted his entire professional life to control technology and automation, first in academia, where he became a professor at KTH in Stockholm in 1999, then at ABB Corporate Research where he now holds the title of Research Fellow, which carries the highest level of research responsibility. He thanks his area of expertise for getting him to this point.

Research Fellow, ABB Corporate Research

“Control technology in a wide sense is the biggest research area we have, as it involves controlling most of what is ‘under the hood.’ And automation is a collective term where software, control and measurement technology coincide,” explains Alf Isaksson.
BUT EVEN THOUGH the desire to find automatic solutions goes back several hundred years, Alf Isaksson is the first to admit that much has happened since the days of mechanical water flow control. Especially in the last 10 years.
“From 1983, when ASEA released its control system ASEA Master, until 2013, it was in a sense evolution. Everything gradually improved, but not much actually happened to the gen-
eral structure of a control system. If you look at the digitalisation of the past 10 years, new technologies such as artificial intelligence and cloud computing have been introduced, and there is no reason to believe that the next 10 years will be less eventful.”
Maria Pia Fanti, Professor at the Polytechnic University of Bari, agrees. Since the early 1980s, she has been doing research in the field, and describes the development of artificial intelligence as “a revolution.” The buzz word of today is hyperautomation and the difference is dramatic, says Maria Pia Fanti:
“Traditional automation was based on system models created by engineers, allowing some manufacturing to take place via automation within the framework of the system. Now it is AI that develops the laws, based on the continuously collected data.”
Maria Pia Fanti believes that no industry will escape being swept up in this development, where AI and Robotic Process Automation (RPA) will become increasingly important.
“The automotive industry, the manufacturing industry and, not least, intelligent transport systems are leading the
Alf Isaksson
Maria Pia Fanti Professor, Polytechnic University of Bari

“The next step is to develop fully automated systems that handle the entire production chain”
Andrew Scott Co-Founder, Global Mining Guidelines Group
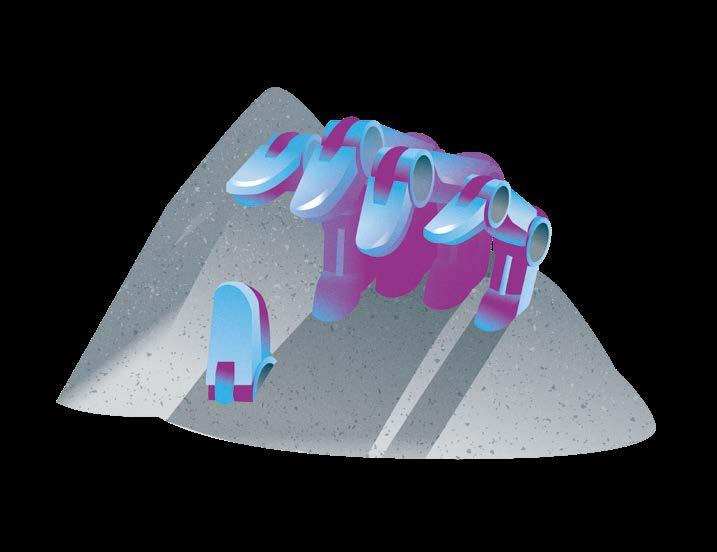
way today, but all industry will move in this direction in the future.”
SO WHAT DOES this mean for the mining industry? Andrew Scott, one of the founders of the Global Mining Guidelines Group (GMG) network, has followed the industry’s developments closely for decades and says there are still many steps to be taken.
“On a five-digit dial, where five is high automation, I would say the mining industry is a two. We’ve had automation for a long time, but we still see resistance in many areas, such as operators thinking they can do the job better than advanced systems,” says Andrew Scott.
Some things are already in place. But mainly in the areas of individu-
al machines and tools.
“The next step is to develop fully automated systems that handle the entire production chain,” says Andrew Scott.
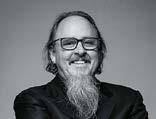
One challenge to moving forward is the fear of sharing competitive advantages. GMG is working to bridge this gap between the companies.
“More collaboration would speed up the process and benefit everyone. For the industry, the gains in efficiency and reduced costs are enormous,” says Andrew Scott.
At the same time, when talking about robots doing people’s jobs, and how cost-effective that would be, the
question inevitably arises: What happens to the jobs?
Experts agree: the lives of those working in industry will change, but that doesn’t mean they will be unemployed.
“I’m absolutely sure that humans can never be completely replaced by robots,” says Maria Pia Fanti.
Andrew Scott agrees and highlights the Amazon example. “Automating their warehouses led to an increase in the workforce. And in the mining industry, we see the same thing in places where automation has been used, for example transport and drilling,” says Andrew Scott.
In short, the way forward is through more technology. And that sounds like an echo from Henry Ford almost 100 years ago: After all these developments, why stay here?
HYPERAUTOMATION
New technology – new engineers
HYPERAUTOMATION FORCES universities to rethink. This is the opinion of Maria Pia Fanti, Professor at the Polytechnic University of Bari. Where in the past engineers needed to emphasize physics and mathematics, in the future they will need to learn more about computer science and software development, in order to stay relevant.
“Mechanical systems are constantly being replaced by software, and this places new demands on us in universities. Whereas in the past we needed to train people who could control those machines, in the future we need to train people who understand the AI systems to be able to work more with robots,” says Maria Pia Fanti.
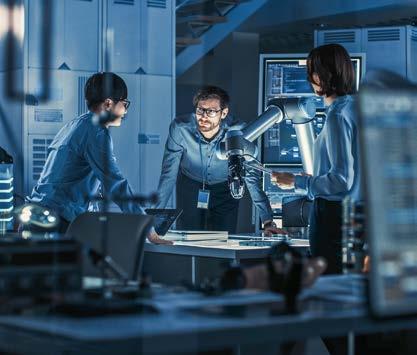
Andrew Scott Co-Founder, Global Mining Guidelines Group
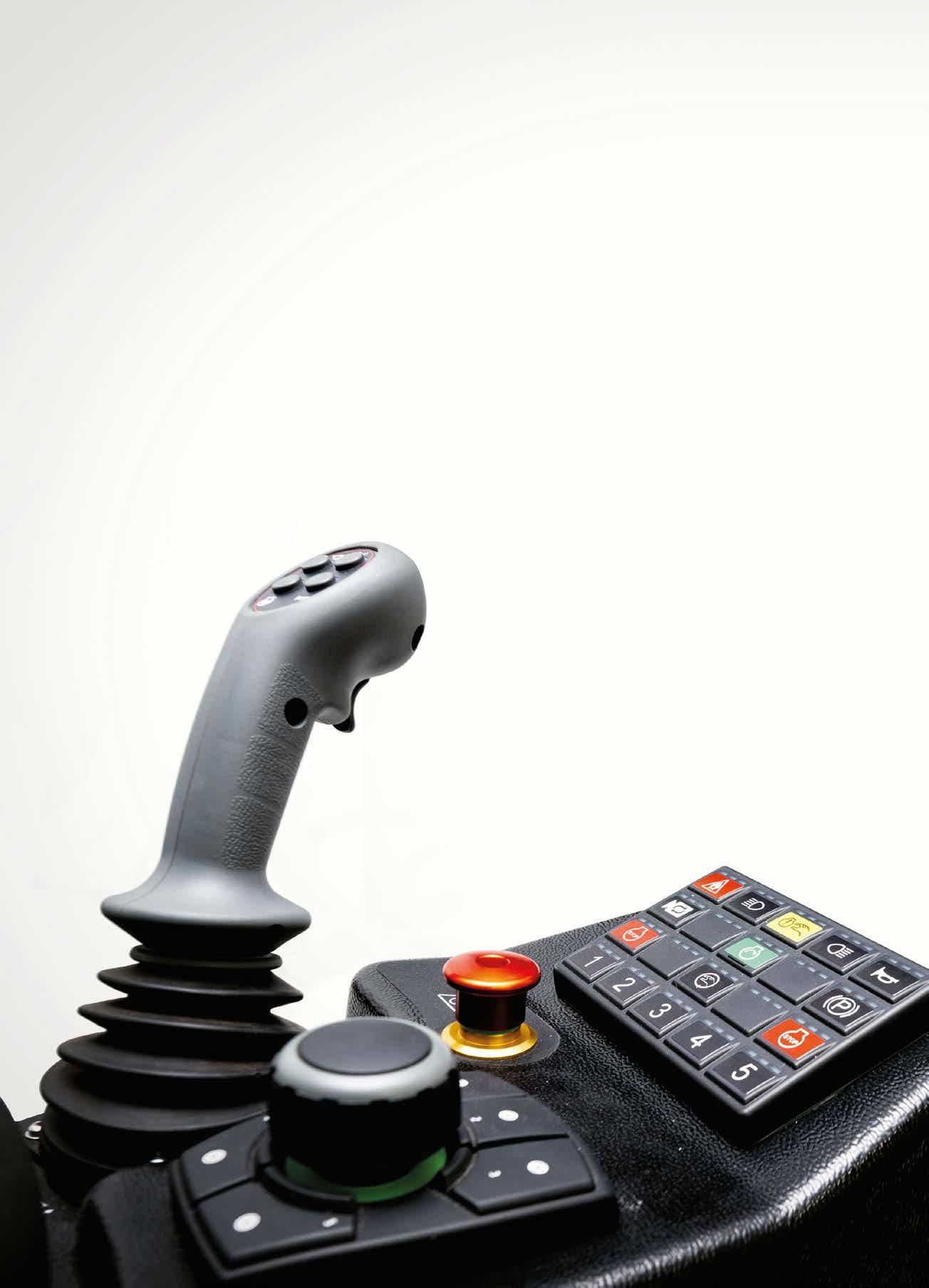
...
EVERYTHING IS UNDER CONTROL
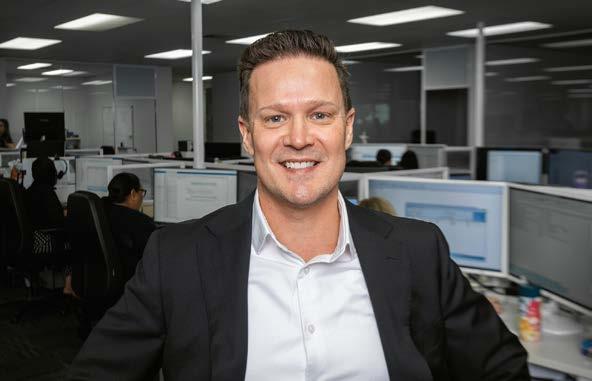
“I thought of us as a mining services company when I first got here. But the automation side is clearly dominant and where the market knows and loves us”

To become the go-to for scaleable agnostic mine solutions – that is what drove Epiroc’s acquisition of Australian company RCT in late 2022. Here is how they’re creating a pit-to-port automated future.
S RCT A MINING SERVICES COMPANY or a tech company? You begin to wonder as you explore its labyrinthine warehouse on the outskirts of Perth, in Western Australia.
This is a mining services company – a world-leading manufacturer of customized, scalable automated mine solutions.
But it’s also a tech company. Wander from workshop to workshop and you see lines of circuit boards, blinking computer terminals, and engineers prodding and testing. Just the smell of the place: it’s more server-room new than the metal and oil of a traditional workshop.
CEO Brett White explains that the company will soon look at moving to bigger premises, as if these ones might be cramped. They don’t feel that way. They feel clean, precise, organized.
“I think of RCT as a tech company,” White says. “But that’s evolved. I thought of us as a mining services company when I first got here. But the automation side is clearly dominant and where the market knows and loves us.”
The market loves RCT because automation is the future of mining. Its safety advantages have
long been clear, but so too now are its productivity benefits after rapid recent advances in technology.
“Safety, utilization and cost efficiencies,” says Epiroc President of Digital Solutions division Paul Bergström. “They’re the three aspects that, over the last 10 or 20 years, are getting more and more mature, and now allow us to consider fully automated solutions. And that, in turn, is creating more and more demand for automation.”
It explains Epiroc’s late 2022 acquisition of RCT, which followed a 2018 partial acquisition of ASI Mining, another industry leader in automation. Epiroc’s goal? To be the industry go-to for scaleable agnostic machine control solutions, allowing mine operators to run a mixed-fleet completely autonomously.
BACK IN 1972, Bob Muirhead wasn’t thinking about automating mines. He was thinking about saving equipment and lives.
Muirhead had started his career as an electrical apprentice in the mining town of Kalgoorlie, 600 kilometers east of Perth, and was confronted by the industry’s then laissez-faire approach to safety.
Brett White CEO, RCT [ On Location ] Australia
Matt Shea
Bradley Kanaris
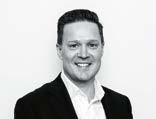
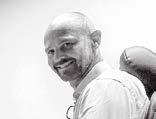
So he tinkered, created his own business, Muirhead Electrical, and came up with his first product: a fail-safe engine protection system.
“It would detect when something catastrophic was about to happen and shut the engine down,”
White says. “It’s called the Muirhead Engine Protection System. That’s what he’s famous for.”
MUIRHEAD WAS AN INVENTOR by nature and other products followed. Muirhead Electrical became Automotive Industrial Mining Supplies, which then became Remote Control Technologies, and finally RCT. Over that time, the focus slowly shifted from custom-made products to entire solutions and platforms, with remote technology and automation increasingly becoming the business’s focus. Australia was a natural leader in the domain, given its early shift towards tighter workplace health and safety legislation.
Muirhead remains an executive director at RCT.
“He’s the reason some people are still here after 40 years,” White says. “Bob has no airs and graces. People see that leadership and that passion, and follow him.”
It’s in part that culture that attracted Epiroc to RCT, and a key element that it wants to retain going forward.
“The values match very well,” Bergström says. “And we’re then adding value on top of that, bringing these new companies in. There are roughly
Q& A
1 300 people in Epiroc’s Digital Solutions division, and almost 1 200 of those are new members of that family.”
Still, what really attracted Epiroc was RCT’s tech and, after 50 years of designing custom solutions for companies across the globe, it’s enormously impressive.
RCT Head of Product Management Brendon Cullen shows a group of trainee operators through one of the company’s larger warehouses. Laid out on a series of tables is an autonomous kit ready to be packed and shipped to Red Lake, a gold mine in Canada, to be fitted to a 10-tonne Epiroc Scooptram underground loader. There’s a large central control box, control sticks, self-cleaning cameras, video screens, LIDAR arrays and meters of cabling, all decked out in RCT’s signature navy blue.
Elsewhere in the warehouse, there’s a light utility vehicle covered with lights, lasers and detection systems. It’s one of RCT’s test mules.
And in the corner is the main attraction: three brand-new Automation Centre cabins. Step inside and you find a tele-remote chair with two control sticks and two LCD monitors. These particular units are still being finished, but each features air-conditioning and space for a small fridge. They’re made of reinforced steel, so they can be placed in an underground mine when network conditions make more remote options unfeasible.

Epiroc to acquire the remaining share of autonomous solutions provider ASI Mining.
Q Can you provide some insight as to why Epiroc is fully acquiring ASI Mining?
A “Epiroc has been on an automation journey for many years now. In early 2018, Epiroc saw the potential in OEM agnostic autonomous haulage systems (AHS) and made an investment in ASI Mining to help the company grow and learn more about this product segment. After five years as a minority owner, we determined the time is right to take on the whole business.”
www.asimining.com
Q How will the complete acquisition of ASI Mining affect current customers?
A “First, I want to ensure current and future customers that our products, services, and support will continue uninterrupted. Epiroc has been the preferred distributor of ASI Mining technology for the last five years. As the distributor, Epiroc has managed the commercial agreements with the customers and has provided the boots on the ground to complete the retrofit instal-
lations. With ASI Mining, we also provide support for vehicle systems, office systems, and service spares. From a customer perspective, the changes will be positive as we increase resources in the business to better support ongoing projects and to develop key features for current and future projects.”
Q Can you explain how the acquisition will affect Epiroc and ASI Mining?
A “Epiroc’s ambition is to support the current ASI Mining business and grow the future AHS business. To accomplish this, ASI Mining will be quickly integrated into Epiroc, which will provide access to our state-ofthe-art facilities, systems, outstanding Research & Development capability and wide range of automation and digital technologies. Epiroc will invest in key areas to strengthen the ASI Mining offering and incorporate Epiroc technology into the current ASI Mining platform. Together we will accelerate the automation journey and bring much-needed OEM agnostic AHS solutions to the global Surface Mining community.”
Paul Bergström
President Digital Solutions division, Epiroc
Brett White CEO, RCT
Tim Ledbetter, Surface division Vice President for Automation R&D, Garland, TX

CEO Brett White sits in a teleremote chair in RCT's training room. This cutting edge equipment illustrates the maturity of the company's technology solutions.
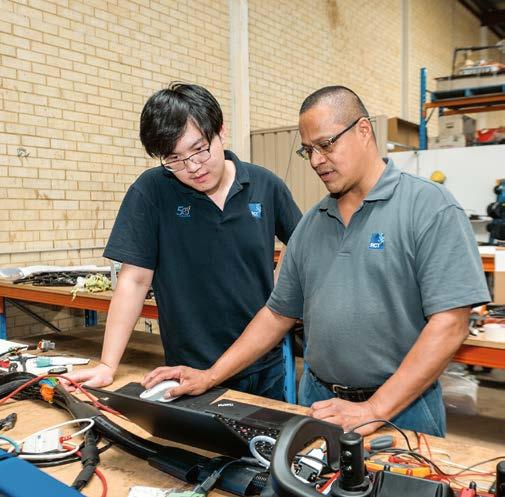
“We certainly have transformed into more of a tech company over the past decade,” Cullen says. “Before that, we were really focused on solving problems. Now, it’s more about creating platforms.”
“People are surprised when they visit us and see the extent of that technological focus because, despite being an international company, we weren’t on the radar of some of those tier-one companies. But they’re now seeing us as a productivity driver and an efficiency driver, so that’s changing.”
Also attracting attention from the majors is a more formalized auditing and consultancy process.
“There’s real value for the customer in a project plan that lays out the stages and timelines,” Cullen says. “[Project engineer] Kevin Winchester had a hand in getting those elements up and running.”
“I was brought in to say, ‘What is the engineering effort required to do these big projects? Is this of business benefit to RCT and the customer?’”
Winchester says. “Because sometimes the customer doesn’t know what they want. We might be able to give them 90% of what they want for a much better price point.”
“You’re sitting down and trying to give a customer a path to their aspirations in automation.”
BACK IN THE TRAINING ROOM, we get to see a couple of teleremote chairs in operation. Here, the maturity of RCT’s technology becomes apparent. On a large widescreen monitor, a loader moseys its way through an underground mine, its progress tracked by both front and rear-facing cameras. In the bottom right of the screen is a digital dash;
“People are surprised when they visit us and see the extent of that technological focus”
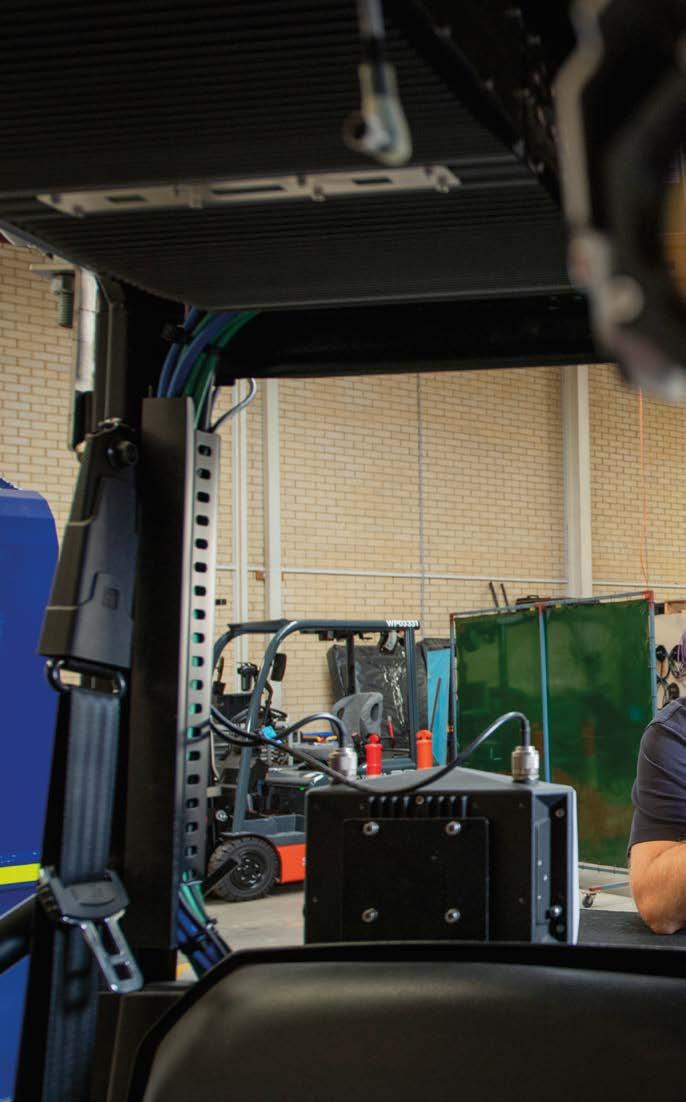
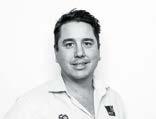
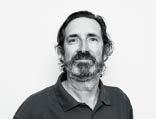
in the top right, a map; and in the middle of the screen, a digital overhead view of the loader and the mine walls, as its LIDAR system finds its way around the mine. It’s show-stopping stuff.
These underground systems are where RCT’s autonomous tech has traditionally had the most industry impact. With the acquisition of RCT, Epiroc is now servicing more than 990 teleremotecontrolled and autonomous underground loaders and trucks, and 810 automated underground drills, compared to about 340 teleremote production surface drills and 270 automated surface haul trucks – in part because of the inherent health and safety risks of underground mining, and in part because it’s easier for equipment to operate autonomously in a constrained environment. But expect that to change as Epiroc and RCT head toward 2030 and tackle more pit-to-port solutions.
“There’s a great understanding now that you
RCT's neatly kept, labyrinthine operations on the outskirts of Perth feel like a hybrid of a mining services company and a tech company.
Brendon Cullen Head of Product Management, RCT
Kevin Winchester Project Engineer, RCT
Brendon Cullen Head of Product Management, RCT

shouldn’t necessarily go straight for the ‘Star Wars’ approach and automate everything at once,” White says. “The change management required with that is enormous.”
“We’re scalable. And that’s why Epiroc acquired us. What we have is relevant to the global mining industries. So the environment is ripe for RCT to expand off the back of Epiroc’s footprint.”
“Epiroc now has a full agnostic automation layer,” Bergstrom adds. “Our competition says, ‘We’re not going there,’ and we’re saying, ‘We have to go there.’ Taking a stake in ASI was a move in that direction. With RCT joining us, it becomes real.”
“A fully automated mine, pit-to-port, by 2030, say. Why do it? Because of the safety, better utilization, and cost efficiencies. Is it a mixed fleet? Of course it’s a mixed fleet. And that, in a nutshell, is our strategy for the future.”
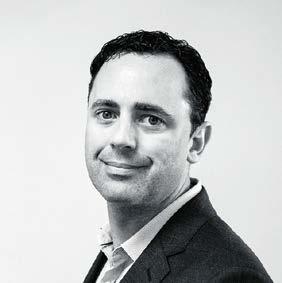
Derries Innovation and technology unit manager, Gold Fields
How do Epiroc’s solutions boost business?
How have you partnered with Epiroc at your gold mines?
“I’m responsible for the innovation, technology, and modernization strategy for the Australian region, which covers our four sites in Western Australia. We have an integrated mine operation center that we’ve developed at Granny Smith, currently our flagship technology mine, and we’ve partnered with Epiroc to use its Mobilaris situational awareness tracking system. We also partnered with Epiroc to develop an integration with their peer-to-peer collision avoidance system, and we’re going to pilot that at Granny Smith in mid-2024.”
What advantages does automation give you at Granny Smith?
“We’re able to remove people from the higher risk areas of the mine, especially underground. We’re also able to increase our productivity and efficiency. Underground, we have up to an hour and a half per day when the mines are evacuated for blasting, so we’re not able to operate our equipment. With the introduction of automation, we can make use of this down time by operating our equipment during shift change when there is no one in the mine.”
How important is it that this technology is agnostic and scalable?
“It is absolutely critical. As our mines get deeper and more challenging, we will need to integrate more of these kind of solutions into our existing operations to support our workers and increase the utilization and efficiency of our equipment.”
www.goldfields.com
Head of Product Management Brendon Cullen (right) inspects RCT's light utility test mule, which is adorned with lights, lasers and detection systems.
Rob
AUTONOMOUS ROBOTIC SURGERY
things to be
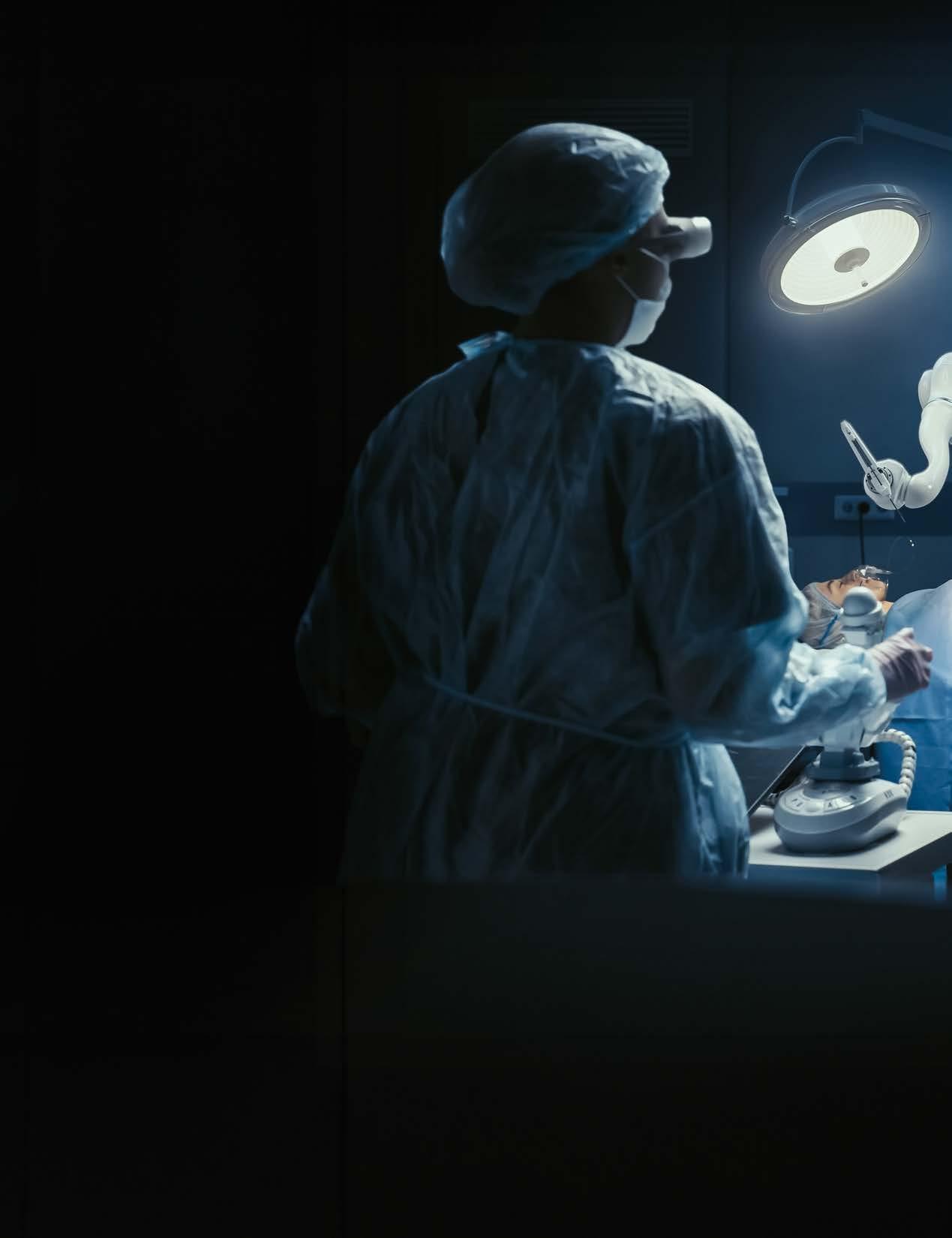
from other
and other
The operating STAR
Cutting edge technology
IN EARLY 2022, a significant step toward fully automated surgery was taken when a robot performed keyhole surgery on a pig’s soft tissue without a human’s guiding hand. The robotic surgeon, Smart Tissue Autonomous Robot (STAR), was designed and run by a team of researchers at Johns Hopkins University.
The surgery consisted of intestinal anastomosis, which connects two ends of an intestine. This procedure is performed more than a million times per year globally. This is one of the most challenging steps in gastrointestinal surgery, requiring repetitive motion and precision with high accuracy and consistency. Any misplaced stitch can result in leaks with potentially catastrophic consequences for the patient.
Robotic systems for surgery have been around for a while – at least since 1985, when a robot performed a brain biopsy. Until recently, though,
most, if not all, robotic systems required extensive human guidance. The difference with STAR is that it can plan, adapt, and execute a surgical plan in soft tissue with minimal human intervention, making it a world first in keyhole surgery.
A STRUCTURAL, light-based, three-dimensional endoscope and a machine learning-based tracking algorithm guide the robot. Human intervention is limited to appraising the surgical plan and manually applying near-infrared markers at strategic points to help orient the robot.
The results were encouraging; STAR performed the procedure on four animals, producing significantly better results than humans performing the same method. A key advantage of autonomous robotic surgery is improved consistency – unlike a human surgeon, a robot will never have a bad day but will give the same result every time.
There are always
learned
organizations
industries. Here’s a look at Smart Tissue Autonomous Robot (STAR), a robotic surgeon that’s taking us one step further toward fully automated surgery.
The future of surgery? Life science companies envision operating rooms where advanced robotics and autonomous solutions unite, increasing precision and efficiency in medical procedures.
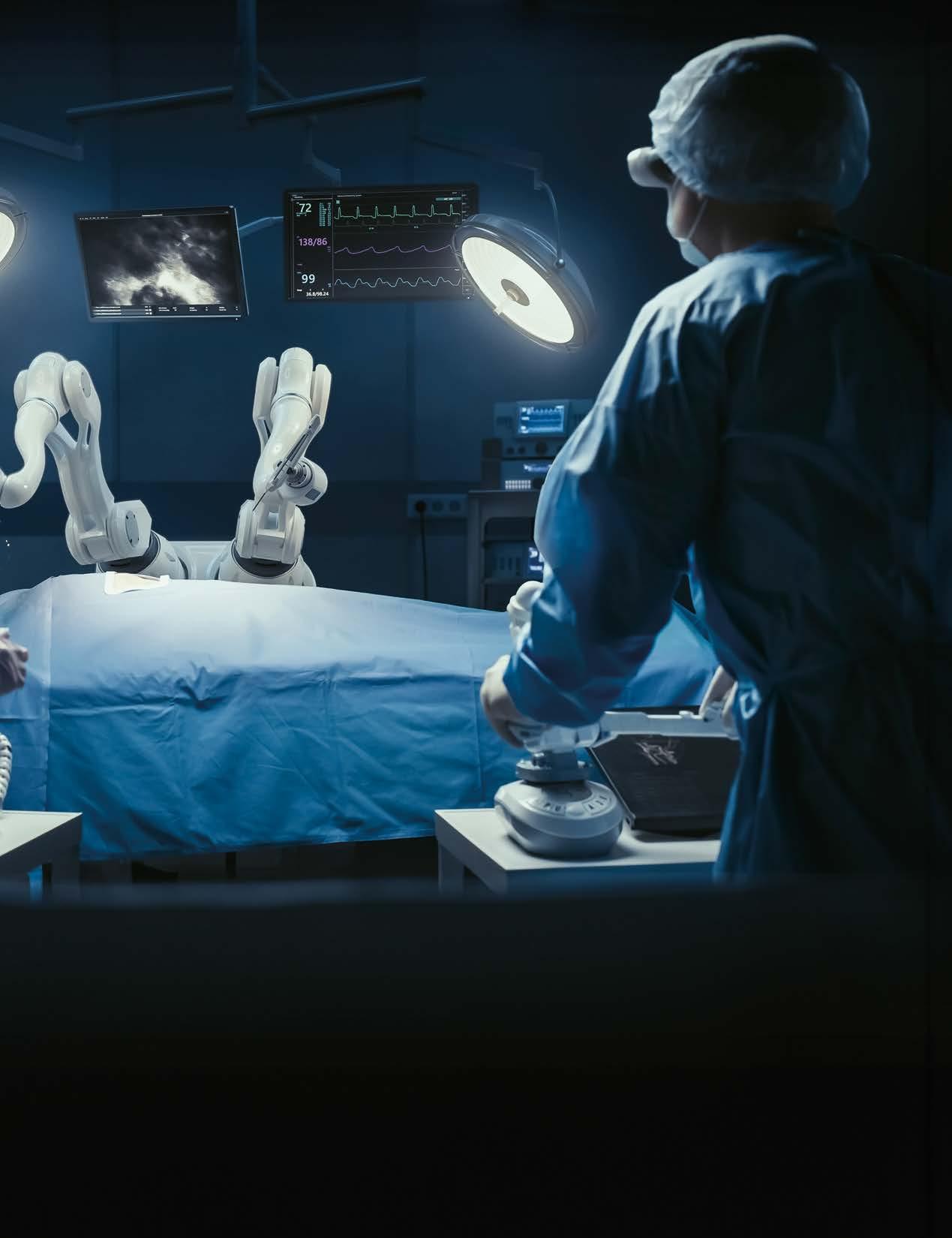
KEYHOLE SURGERY performed by humans requires a very high skill level and the need to operate at awkward angles. With robots, surgeons can perform more complex operations with less physical strain and better performance.
Assisted robotic surgery is already an established technology, and robots can be found in hospitals worldwide. The most prolific device, the Da Vinci, is a fourarmed robot capable of working in hardto-reach places that is used in at least 1.5 million operations per year. It has a 3D viewfinder hooked up to a camera on the robot, allowing the surgeon to magnify, grasp, cut and cauterize tissue inside. In Focus: Robotic surgery
robotsguide.com/robots/davinci
FORWARDING AUTOMATION
01 02
What are the main challenges in the transition toward automation?
How should those challenges be met?
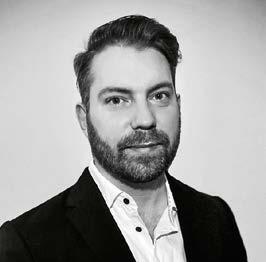
Andreas Hoffman
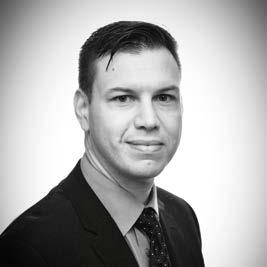
Philip Piatkiewicz

Qing-Shan Jia
01
“In today’s global mining industry, sustainability and traceability have become paramount concerns as stakeholders increasingly prioritize ethical practices and environmental responsibility. Such initiatives focus on reducing energy consumption, implementing efficient waste management practices, and ensuring the responsible sourcing of minerals with transparency throughout the supply chain.”
02
“In addressing the challenges, Rockwell Automation’s 9th State of Smart Manufacturing Report highlights that in the next three years, AI adoption will improve quality maintenance and risk reduction in manufacturing. Moreover, collaborative efforts among stakeholders, policymakers, and educational institutions are crucial in fostering sustainable solutions to mitigate the impact of these challenges.”
Account Manager Heavy Industries, Rockwell Automation, Sweden www.adr-association.eu
Secretary-General Adra (AI, Data and Robotics Association), Belgium
01
“In relation to the mining and construction sectors, there are numerous economic pressures to deploying automation and AI technologies, bringing both opportunities and challenges. Successful automation adoption must consider a holistic approach that balances technological advancements with practical realities. Integrating automation seamlessly into existing mining and construction operations is a complex task, with interoperability across existing infrastructure, legacy systems, and processes being critical.”
02
“Collaboration and transparent communication are key, as companies, workers, and regulators must work together to identify the right pathways to reap the benefits of increased efficiency and safety, as well as address concerns and involve them in decision-making.”
Professor,
Department of Automation, Tsinghua University, China
01
“The main challenge is human-AI interaction (HAI). This is not just natural language processing or audio, video, and even multi-modal communication, but more about knowing the objective in a task, knowing the strength and weakness of human and AI towards that objective, and designing an effective mechanism to coordinate the two. Secondly, how do we create sustainable AI for automation? Thirdly, how do we regulate the design, production, and utilization of AI in automation?”
02
“First, advance both general purpose as well as customized AI for automation. Second, improve energy efficiency of automation, especially the AI part. Beyond improving energy efficiency of AI in general, it is of significant interest to develop energyaware AI tools, and energy-flexible automation systems. Third, advance regulations on AI in automation.”
THE ROBOTS ARE COMING!
There is much speculation and fear about which jobs will be made obsolete by automation in the near future. Below are some scenarios.
Software Developers
Making yourself redundant is seldom a brilliant idea. Ironically enough, even the part of the workforce that has developed the software side of automation will have to relinquish many of their tasks to AI-based automated programming tools.
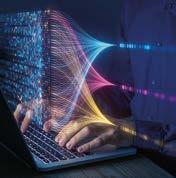
Factory Workers
As automation, machine learning and robotics become more advanced, many tasks traditionally performed by humans in factories are being automated, reducing the demand for human workers. The need for human supervision will persist for longer, though.
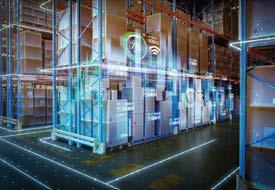

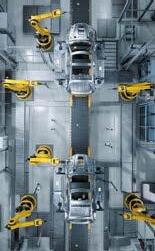
Retail Workers
Physical retail stores have long struggled with e-commerce. The latter has hitherto also depended on manual labor, but that will change with the increasing number of autonomous solutions for warehouses and shipping, like trucks and drones.
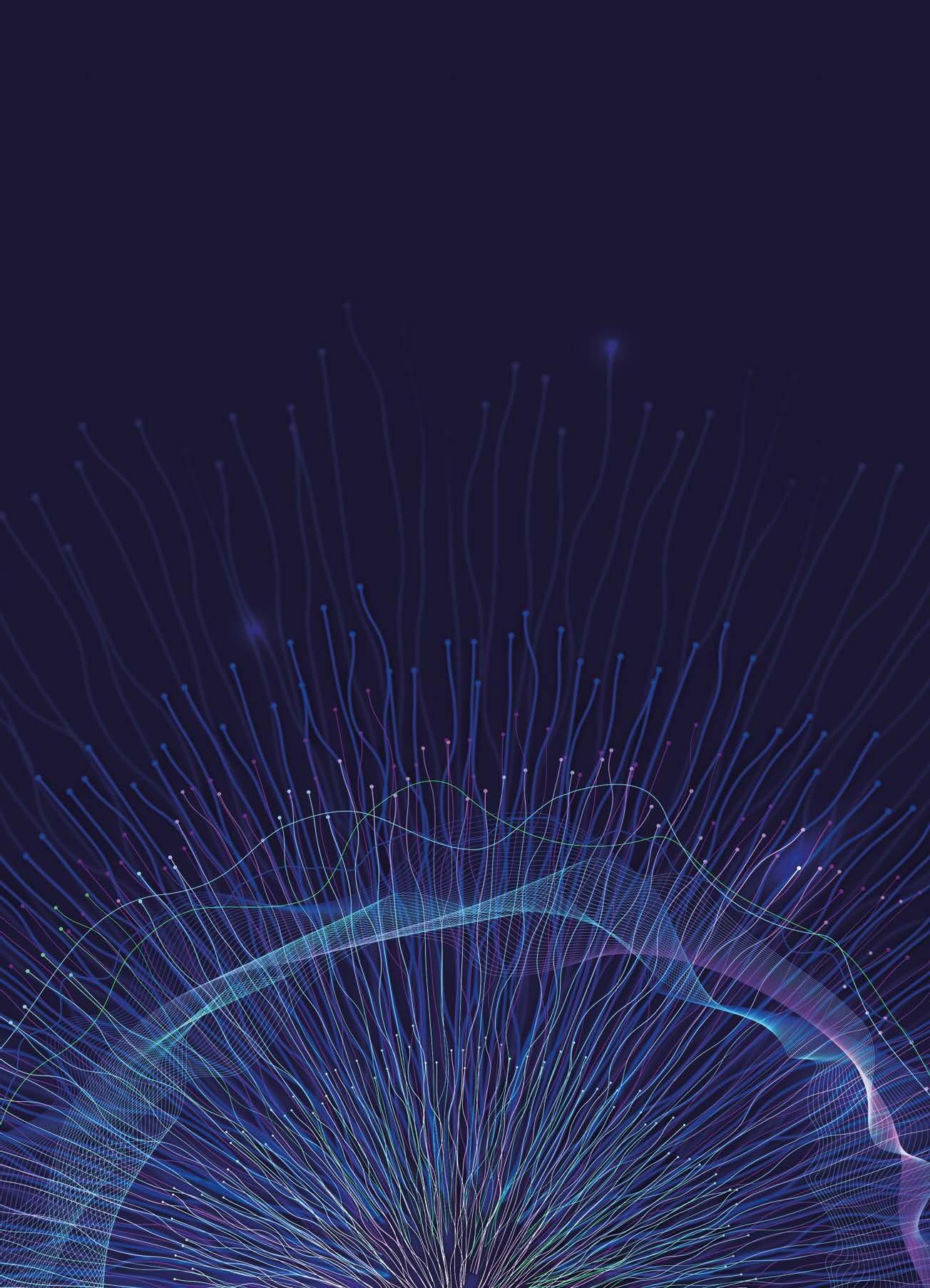
Telemarketers
Automated telephone calling systems have existed for a while. The increasing ability of AI chatbots to mimic human speech patterns, combined with huge strides in voice recognition algorithms, will gradually make it less attractive to employ human telemarketers.
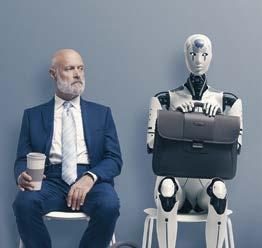
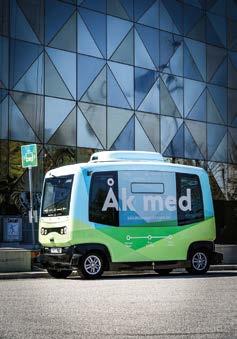
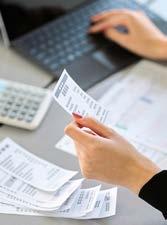
Psychologists
The present and coming generations of chatbots will only improve human interaction and will increasingly be combined with expert systems. This means that even people in highly specialized jobs, like psychologists, may be supplanted.
Bookkeepers
Transportation Workers
While autonomous vehicles have yet to make a major breakthrough in infrastructure, they surely will; self-driving cabs, trucks, trains, and other modes of transport will take over at some point when all the kinks of mixed traffic are resolved.
Automation software for bookkeeping and accounting tasks, such as organizing data feeds from sources like banks or expense systems, is already becoming more prevalent. This naturally reduces the need for manual bookkeepers and accounting clerks.
MY WORK: CEO CR MINING
“Business is about building confidence”

In February of 2023, Epiroc acquired Australian company CR Mining. John Barbagallo has been CEO since 2018, and brings over three decades of expertise and knowledge into the Epiroc family. Here is his story.
“Igrew up in an agrarian family in Northern Australia, and I was helping out on the farm by the time I was 10 years old. Early on, I was fascinated by machinery and farming processes, and how to improve future outcomes. I studied Chemical Engineering and acquired an MBA at the University of Queensland, and after graduation I worked in the mining extraction industry. In my career I’ve worked with process engineering, mineral concentration, aluminum smelting, supply of grinding media and managing facilities, in countries like Australia, New Zealand and the UK. In 2018, I was appointed CEO for CR Mining, providing mining bucket consumables for the mining industry.
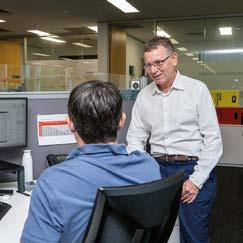
JOHN BARBAGALLO
Age: 58
Job: CEO, CR Mining
Powered by Epiroc
Joined the company: 2023
Best part of the job: “Making a difference for our customers, seeing people being successful and building their careers.”
During my 35 years in the business, I have been fortunate to experience everything from exploration, mining, extraction, concentration and supply of missioncritical consumables. I’ve continued to keep learning
on every job I’ve had, collecting experience and wisdom from great managers and mentors, and have strived to add value. I’ve thoroughly enjoyed the journey, every step of the way.
I THINK THAT business is about building confidence. I don’t think of challenges in those terms, I think of them as opportunities. To achieve sustainable success, I focus on these building blocks: building a diverse leadership team, respecting and valuing everyone’s contribution, creating a winning culture, and defining clear business strategies with excellent implementation routines. My advice is: don’t be afraid to stretch more outside your comfort zone.
Mining has an incredible future given the energy transition and the resulting demand for minerals and metals. As business leaders we need to be acutely aware of our responsibilities to successfully balance the social, environmental, community and economic requirements.”
Epiroc’s greatest asset is our employees. We take pride in offering them an outlet for their creativity in order to provide the best possible value to our customers.
Christian Tarras Ericsson
Bradley Kanaris
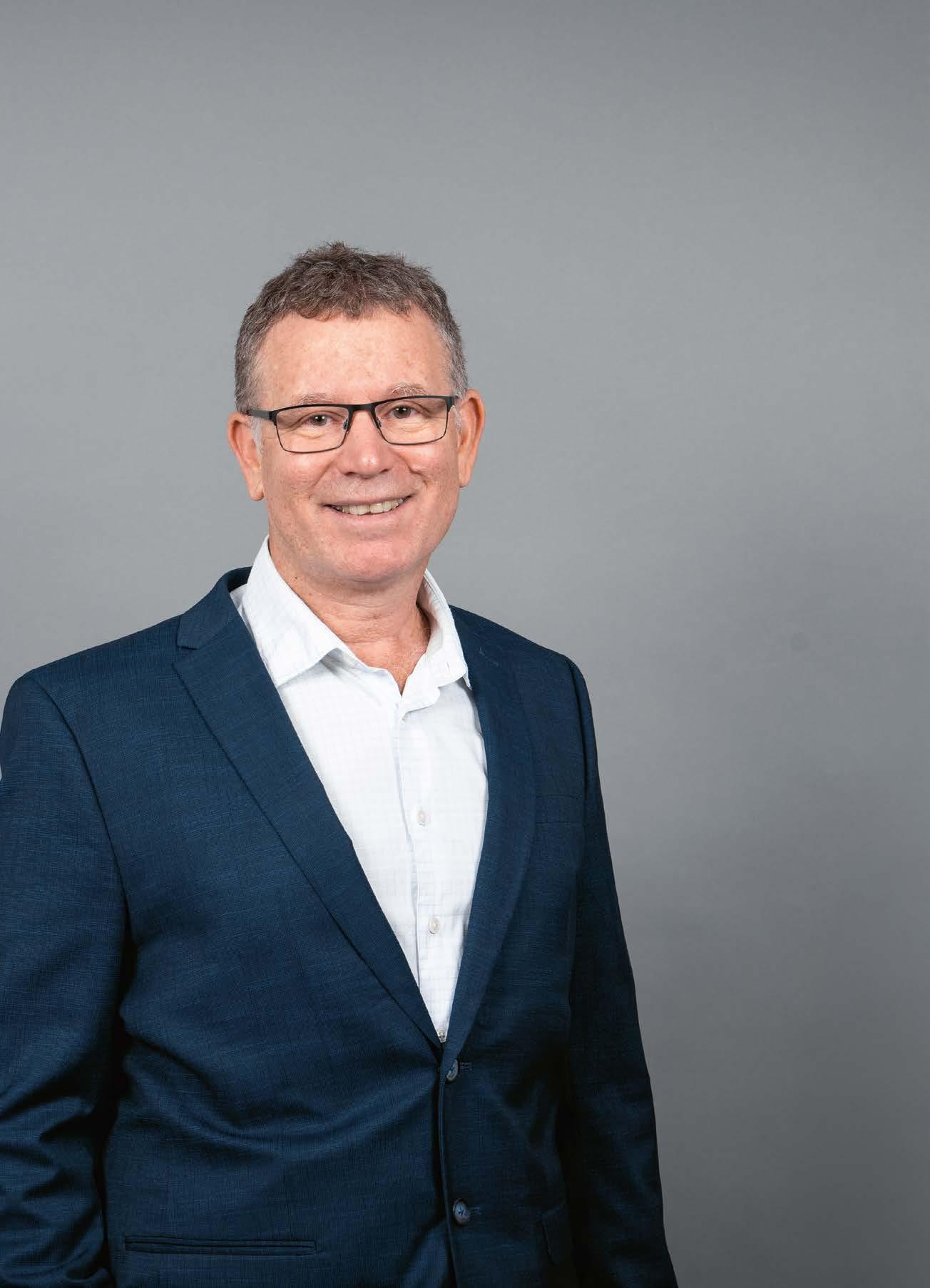
“If you have an inquisitive mind, you can learn from every job you have during your career. Every job is additive,” says John Barbagallo.
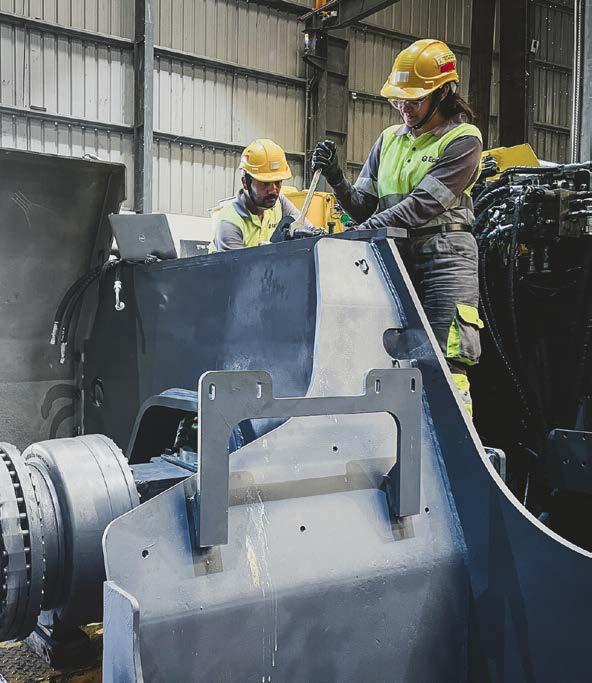
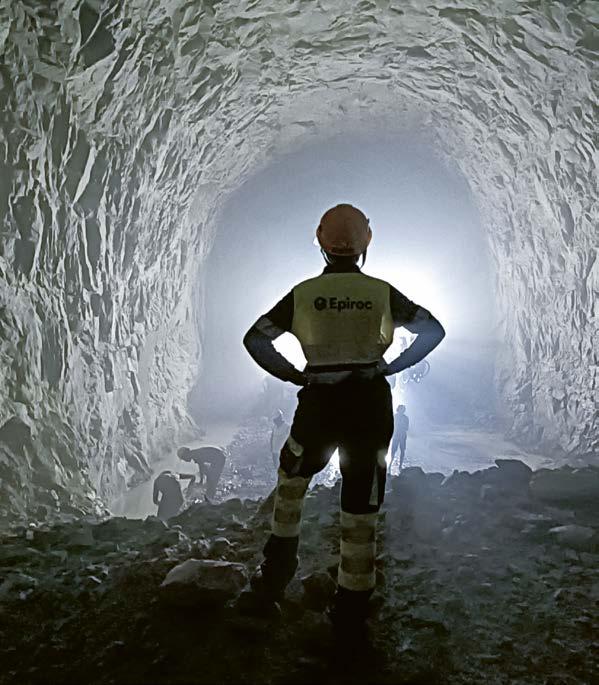
TRAINEE PROGRAM FOR DIVERSITY
Women of Mettle breaking new ground
Epiroc India launched the Women of Mettle program to enhance diversity, challenging the long-held belief that mining was too dangerous for women.
IN 2019, the Government of India updated its employment regulations to enable women to work in both underground and open pit mines, promoting gender inclusion and economic growth. Following this change, Epiroc India launched the Women of Mettle program, which focuses on encouraging and training female students for careers in the mining industry, ultimately integrating them as employees within the company.
“We aim to incorporate diverse perspectives and encourage young engineers to come forward. Regardless of gender or technical capabilities, what matters to us is the value and innovation each individual can contribute,”
says Dharmesh Mehta, HR Manager, Epiroc India.
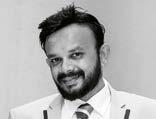
HR Manager, Epiroc India
Between 2020 and 2022, Epiroc India recruited two classes for the Women of Mettle program. 28 out of 35 trainees continued their careers at Epiroc in roles such as Sales Engineer, Marketing Analyst, or Service Engineer at customer mine sites. During 2024, Epiroc will continue to expand the talent pool in sales, marketing, and service.
“Over the course of a year, we are training these women in our organization and products. Service trainees learn the basics in a classroom before
getting practical experience in the factory. By the end of the year, they are ready to work at our customer sites,” says Dharmesh Mehta.
ONE OF THE EMPLOYEES is Alka Chinaliya, who, for the past two and a half years, has worked as an Epiroc Service Engineer at the Sindesar Khurd Mines, owned by Hindustan Zinc.
“I accepted this challenge because I wanted to show every girl out there that everything is possible. I’m working hard to change the mindset in India that women can’t work within mining,” says Chinaliya, continuing:
“Mining is an industry that still is very male-dominated, but I’ve noticed an improvement in acceptance compared to when I first started working in the mine.
Dharmesh Mehta
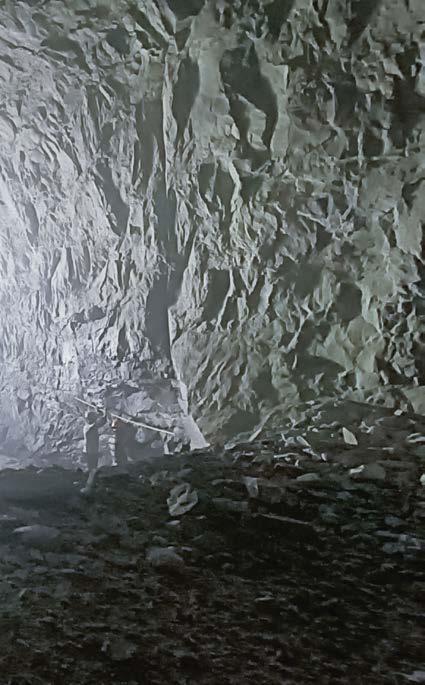
Women of Mettle participants included Service Engineer trainees. Of the program’s 35 trainees, 28 continued their careers at
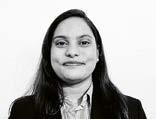
However, I believe there’s still room for progress towards greater inclusivity.”
Chinaliya became Epiroc’s first female First Aider, won the All India Mines Rescue competition, and received the Zinc Ratan Award 2022
“I have grown from questioning my abilities to confidently handling maintenance, operations, troubleshooting machinery and enhancing machine performance. Working with machinery has always been my dream, and now, I’m living that dream,” Chinaliya concludes.
Epiroc has selected nine relevant UN Sustainable Development Goals, connecting them to the company’s own goals. In each issue, we highlight one of them.









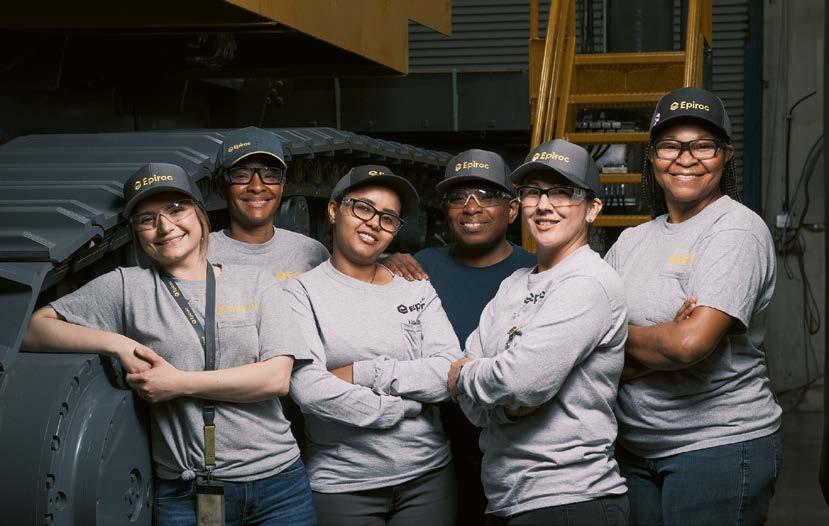
The inclusion recipe in action
The global Sustainable Development Goals (SDG) formulated by the UN guide our sustainability work. We take a closer look at how Epiroc approaches Goal 5.
IN SOCIETY AS A WHOLE, gender inequalities are still deeply rooted, making SDG 5 – Achieve gender equality and empower all women and girls – hugely important, both on an individual level and for the sake of general progress and the unlocking of potential. In the world of mining, Epiroc is dedicated to being a leading light.
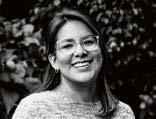
“Gender diversity is a big part of our commitment to ESG regulations, since it includes people. Epiroc is working to accelerate the transformation toward a more sustainable mining and construction industry, and for that to succeed we need everyone in the company to be on board for the journey,” says Lía Ascacibar Vargas, Global Inclusion and Diversity Booster.
Part of the company’s 2030 goals is to double the number of women in operational
roles, and targets supported by specific action plans have been set in each division. There are also mentorship programs for female employees, cooperation with external stakeholders, and Epiroc has also implemented the When life transforms policy, granting all employees 12 weeks of parental leave during the first year of parenthood.
“It’s great to see the impact the policy has created. We have also shared our experiences from the implementation with other companies who are interested in this type of change,” says Lía Ascacibar Vargas, concluding: “The parental leave policy is part of our inclusive culture, and for 2024, we really want to focus on reinforcing that. This work includes focusing on our strategic commitment as well as having hands-on activities; the inclusion recipe in action, if you will.”
Lía Ascacibar Vargas Global Inclusion and Diversity Booster, Epiroc
A diverse team – formed by engineers, electricians, and welders – assembles Pit Viper rigs at Epiroc’s production company in Garland, Texas.
Epiroc.
Alka Chinaliya Epiroc Service Engineer, Sindesar Khurd Mines
Gustaf Höök Dima Barulin
BLAST FROM THE PAST YEAR 2017

Portfolio:
Inje-Yangyang Tunnel
WITH THE 2018 Winter Olympics in PyeongChang on the horizon, South Korea had many challenges to meet. One of them was how to better connect Seoul, in the west, to Yangyang County on the east coast of the peninsula. A key element of the Seoul–Yangyang Expressway was the construction of the Inje-Yangyang Tunnel, situated in the northern province of Inje in the mountainous region of Kangwondo.
Construction began in 2009, and SungPoong Construction, South Korea’s leading company in ventilation and shaft applications, was awarded the contract to install the ventilation consisting of two shafts, 212 and 307 meters long, spaced four kilometers apart. For this job, SungPoong Construction used what was prob-
www.bit.ly/longestroadtunnels
ably the most sophisticated raise boring equipment in the world. It consisted of a Robbins 73RVF C medium-sized raise drill, a Secoroc Mini Super Base System (for modular reamer assembly), Secoroc Magnum cutters, and a 12¼ inch flanged stinger and a 12¼ inch pilot bit.
The equipment was clearly up to par, with Kiman Cho, Project Manager for SungPoong Construction, remarking: “I think the Magnum cutter is amazing. It has a three to four times longer service life than any cutter I have ever used before.”
The Inje-Yangyang Tunnel was opened in June 2017. Having employed 50 000 construction workers and at 10 965 meters, it was, and remains, the longest road tunnel in South Korea.
Innovative products and a wide array of customers: Epiroc is a new company with a long and rich history dating all the way back to 1873. In each issue of Mining & Construction, we look into the review mirror for a glimpse of the past.
Epiroc and Gustaf Höök Shutterstock
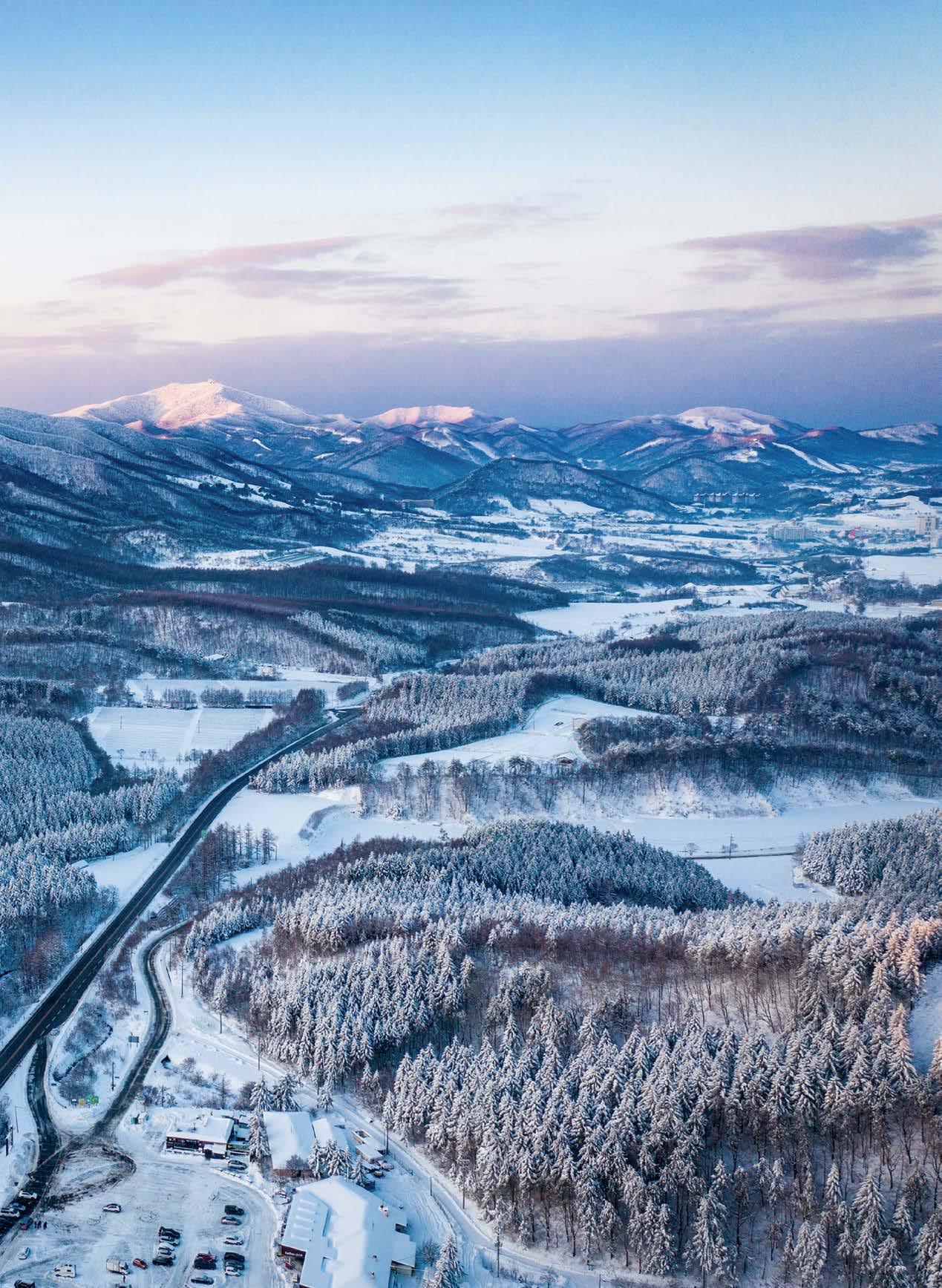
The Seoul–Yangyang Expressway, including the Inje-Yangyang Tunnel, dramatically reduced the time it takes to drive to PyeongChang from four hours to just 1.5 hours. This view is from the mountainous region close to PyeongChang.
AROUND THE WORLD IN BRIEF
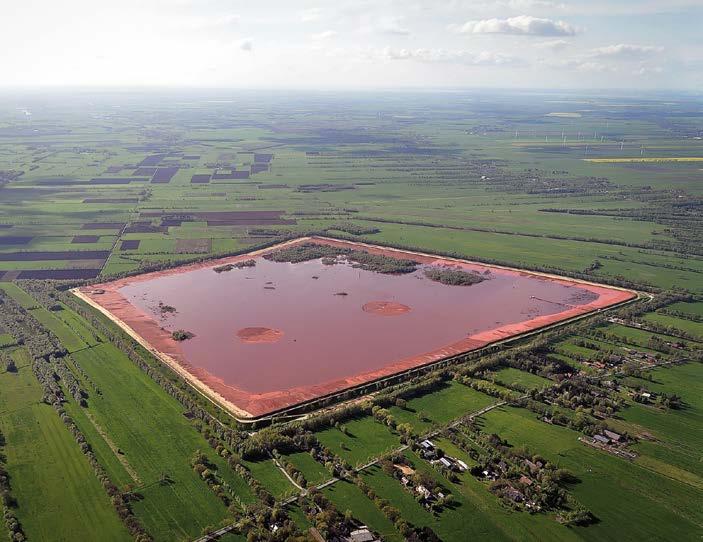
How to produce green steel from aluminum’s red mud
SCIENTISTS AT THE Max-Planck-Institut für Eisenforschung, a center for iron research, have shown how green steel can be manufactured from aluminum production waste relatively simply, mining.com reports. In a paper published in the journal Nature, the researchers point out that the feasibility of their technique relies on the fact that the production of aluminum generates millions of tons of toxic red mud every year.
Scientists could convert the iron oxide in red mud into iron using hydrogen plasma in an electric arc furnace similar to those used in the steel industry for decades. With this process, almost 700 million metric tons of CO2-free steel could be produced from the four billion tons of red mud that have accumulated worldwide to date – corresponding to a third of annual steel production worldwide.
IEA to launch security program for critical minerals
THE INTERNATIONAL ENERGY AGENCY (IEA) is launching a program to secure the supply of minerals critical to energy security as demand rises fast. At the same time, Reuters reports that manufacturing remains in the hands of a few key producers. “Currently, we are A, not able to keep up with the demand, and B, the ability to manufacture these critical minerals is concentrated in one single country or two,” IEA executive Fatih Birol (pictured) said in a speech.
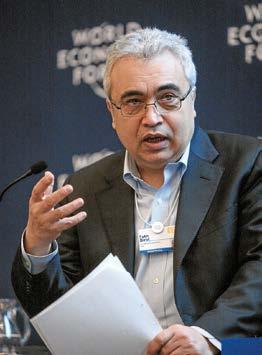
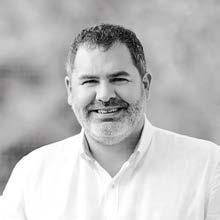
Vladimir Glasinovic Director Eleva Program, Chile
What does
The CCM-Eleva Alliance has presented the Workforce Study of Chilean largescale Mining 2023–2032. What are the key findings?
“The alliance is a collaborative effort between the Mining Council and Fundación Chile, and our research indicates a demand for more than 34 000 new skilled professionals within the next ten years. That’s a significant increase from estimations made two years ago. This surge is primarily attributed to the initiation of several new projects.”
What sort of profiles will be needed?
“The greatest demand is anticipated in the mechanical sector, encompassing both mechanical and electrical roles, with over 13 000 vacancies expected over the next decade. At this point, securing maintainers poses the greatest challenge for recruiters.”
How about women in mining?
“There has been a remarkable growth, with the number of women doubling in the past four years, from 8% to 18%. Notably, last year, one out of every two hires made by mining companies was a woman. This surge in female participation extends beyond operational and maintenance roles, with women now comprising 20% of managers, 19% of superintendents, and 14% of supervisors.”
www.bit.ly/chileanworkforce
Red mud near Stade, Germany. The global aluminum industry produces around 180 million metric tons of red mud annually.
RABOE
Pinpointed
1
AI-powered Zambian copper mine may become the world’s third-largest Mingomba, Zambia
Zambia may be home to the world’s third-largest copper mine after a startup backed by billionaire Bill Gates discovered vast metal deposits, according to Hakainde Hichilema, the country’s president, Bloomberg News reports. San Francisco Bay Areabased KoBold Metals, which uses artificial intelligence to explore materials key to the green-energy transition, said that its discovery at the Mingomba project far surpasses existing operations in top producer Chile by copper grade.
2
NASA delivers maps of minerals in dust-source areas Pasadena, USA
NASA’s EMIT mission (Earth Surface Mineral Dust Source Investigation), which scans broad areas that would be impossible for a geologist on the ground or instruments carried by aircraft to survey, has created the first comprehensive maps of the world’s mineral dust-source regions, providing precise locations of 10 key minerals based on how they reflect and absorb light. Understanding their abundance around the globe will help researchers predict future climate impacts.
Want to keep track of what’s happening in the mining and construction industry? Visit miningandconstruction.com for links to industry news and other interesting reading.
4
Rio Tinto gets $13 million to decarbonize iron ore processing Ottawa, Canada
The Government of Canada has awarded C$18.1 million from its Low Carbon Economy Fund to Rio Tinto to support the decarbonization of iron ore processing at the company’s operations in Labrador West. The funding will enable Rio Tinto to reduce the amount of heavy fuel oil consumed in
producing iron ore pellets and concentrate. The company will install an electric boiler to displace emissions from the usage of the heavy fuel oil boilers, as well as instrumentation and fuelefficient burners to reduce heavy fuel oil consumption from induration machines further.
3
Over a third of construction using “immersive tech” Newcastle upon Tyne, UK
The construction industry’s use of technology is growing, NBS’ 2023 Digital Construction Report reveals, having surveyed over 700 construction professionals, from architects/engineers and other consultants, contractors, clients, and suppliers, Construction Briefing Reports. For instance, 36% already use “immersive tech” such as AR, VR, and MR within building projects. However, despite this increase in usage, nearly half (47%) are concerned the industry is behind the times.
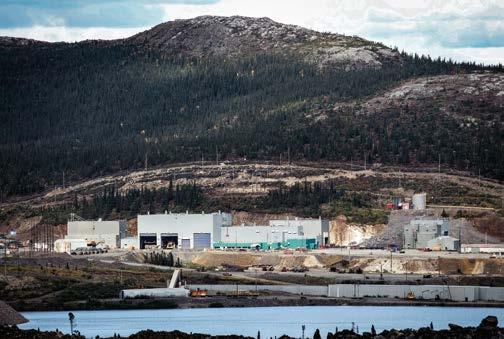
DML and DM45
Unlocking Drill Master automation
Increased safety and productivity in mining are important. The new Drill Master series, soon to be launched by Epiroc, supports these goals. Yara Hussein, Product Manager at Epiroc in Garland, Texas, has led the developing process.
What is the purpose of the new enhanced drill rig?
“The new Drill Master rigs integrate our rig control system, RCS, into the DML and DM45 models, extending advanced automation features to a broader customer base beyond rigs like the Pit Viper. With this offer, Epiroc expands its automated product range for platform drills, ensuring accessibility across all hole sizes.”
Could you describe the developing process?
“We started by thoroughly examining the market potential and engaging with numerous customers worldwide, strongly emphasizing their involvement. We explored their perspectives on automation, envisioning it as a scalable offering wherein they retain the autonomy to transition to higher levels at their discretion. We start with
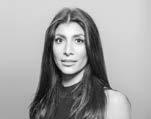
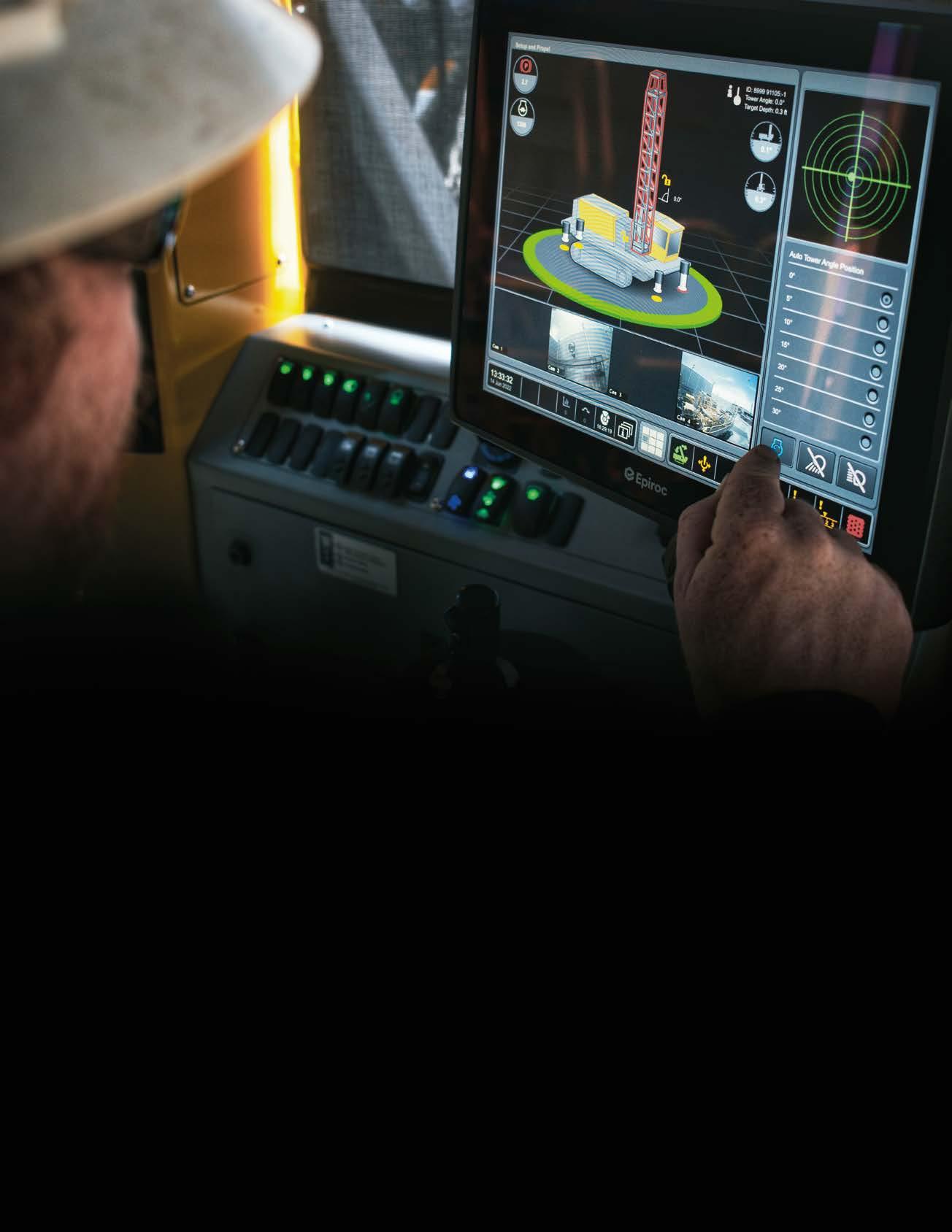
basic safety features and go up to fully automated rigs where operators do not need to be in the cab.”
So, what is the value for the customers?
“By integrating our proprietary rig control system, RCS, into the DML and DM45 models, these rigs offer enhanced efficiency, safety, and productivity. Previously limited to hole sizes ranging from 200 millimeters to 406 millimeters, these automation features have now been extended to smaller sizes with the addition of the 45s and Ls models equipped with RCS. With automation now available across a wider range of hole sizes, operators can streamline drilling operations while upholding stringent safety standards.”
DML and DM45 in brief:
Auto-Drilling Automated drilling depth and speed control for precise and consistent drilling operations.
Auto Leveling Automated rig leveling to ensure stability and accuracy during drilling.
Automatic Rod Handling Mechanized handling of drilling rods for seamless rod changes and improved efficiency.
Real-Time Monitoring Continuous monitoring of drilling parameters and rig performance for proactive maintenance and optimization.
Fault Detection Automatic detection and alerting of potential issues or malfunctions to minimize downtime and enhance operational reliability.
Yara Hussein Product Manager, Epiroc, USA