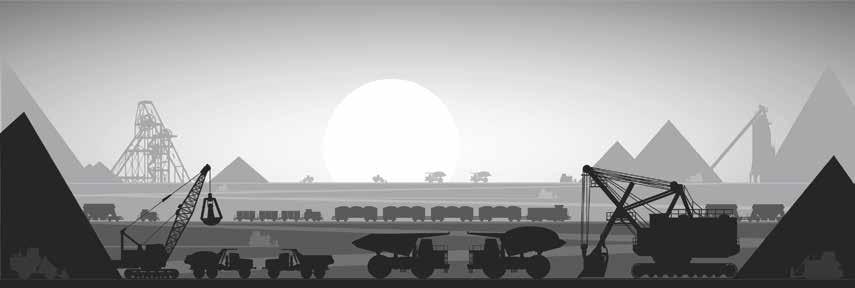
5 minute read
Return on Investment of Good Lubrication Management
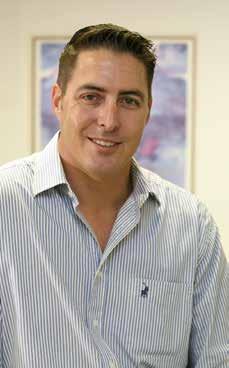
WearCheck’s Lubricant-enabled reliability (LER) solutions boost the lifespan of mining equipment.
Advertisement
Condition monitoring specialist company, WearCheck, appreciates the value of a world-class lubrication maintenance regime, which goes a long way towards keeping mechanical parts operating at their full capacity, for longer.
In line with the company’s ongoing innovation, WearCheck extends its services to offer expert advice on, and insights into, lubrication-related products and maintenance techniques that can go the extra mile towards keeping oil in an optimum state.
Solving machine lubrication issues
This advice is dispensed through WearCheck’s Lubrigard division, where a team of industrial lubrication specialists focuses on solving machine lubrication issues as part of WearCheck’s lubrication-enabled reliability (LER) offering. Some of the products featured in WearCheck’s Lubrigard brand include varnish removal systems, vacuum dehydrators and filtration systems for specific applications.
Lubrigard manager for WearCheck, Chris Hattingh, explains how good lubrication management can help to boost an operation’s return on investment in condition monitoring. ‘We arrange our LER services around FLAC - that is fuels, lubricants, air and coolants. In the mining industry, for example, some of the problematic commodities could be diesel, or oil and grease, or air, or coolant, where potential contamination is negatively affecting performance.
‘Our Lubrigard technicians are positioned to improve the reliability of these commodities and keep the mining machinery running optimally. We conduct a full FLAC audit, recommend standardisation techniques and help our customers to implement a road map to achieve lubrication best practice.
‘In any industrial operation, all assets have a particular risk rating, depending on factors ranging from operating conditions, component age, environmental issues and more. Using our FLAC systems, we can put controls in place to reduce the risk of that asset from high to low.
‘Moreover, the scientific oil analysis data enables us to implement systems to mitigate assets’ risks. Therefore, ongoing oil and other fluid analysis helps not only to diagnose the underlying problem, but also to track the effectiveness of remedial action that has been taken.
Chris Hattingh of WearCheck’s Lubrigard division, advises customers on the use of products and tips that can help keep fuel clean and enhance their condition monitoring programme. This service forms part of the company’s lubrication-enabled reliability (LER) offering.
Tried and tested LER techniques
Hattingh advises customers on lube management in many sectors, including mining. ‘In the dynamic and demanding world of mining, the reliability and performance of equipment are paramount to operational success. Mining operations involve heavy-duty machinery that operates in harsh conditions, subjecting them to extreme temperatures, dust, water, and heavy loads. To ensure smooth and efficient mining operations, maintaining the health of these machines is vital. A cutting-edge approach to achieving this is through tried and tested LER techniques.’
Understanding lubricant-enabled reliability
LER is a comprehensive approach to equipment maintenance that focuses on optimising the performance and lifespan of machinery through the proper management of lubricants and fluids. This methodology acknowledges the pivotal role that lubricants play in safeguarding the functionality of mining equipment. LER goes beyond traditional maintenance practices by integrating predictive and preventive strategies centred around lubrication.
The significance of FLAC
Hattingh explains that the company’s FLAC (fuels, lubricants, air and coolant) system is the answer to boosting reliability of mining equipment. ‘FLAC, WearCheck’s reliability improvement programme, focuses on one or all of the commodities we use in our equipment that, if not in an optimal state, will have negative mechanical impacts that will affect our clients’ business operations - either through production losses, reliability issues or expensive component replacement costs.’
FLAC is an essential element of any total fluid management (TFM) approach. In the mining sector, where downtime can lead to significant financial losses, TFM becomes a strategic asset. TFM is the broader framework within which lubricant-enabled reliability operates. It encompasses the entire lifecycle of fluids within mining machinery, from selection and application to monitoring and disposal. TFM involves careful consideration of additional factors such as contamination control, fluid analysis, and disposal practices.
Key Components of LER
• Lubricant selection: Choosing the right lubricant for each mining application is crucial. Different components of mining equipment, such as engines, transmissions, and hydraulic systems, have varying requirements. High-quality lubricants with appropriate viscosity and additives help reduce friction, wear, and heat generation, thereby enhancing equipment performance and longevity.
• Contamination control: Mining environments are notorious for their dust and debris, which can infiltrate lubricants and accelerate equipment wear. Implementing robust contamination control measures, such as effective filtration systems and regular fluid sampling, prevents abrasive particles from causing damage and extends the life of both fluids and machinery.

• Fluid analysis: Monitoring the condition of lubricants and fluids through regular analysis provides insights into equipment health. Fluid analysis involves measuring parameters like viscosity, acidity, and the presence of contaminants. By tracking changes over time, maintenance teams can identify potential issues before they lead to costly breakdowns.
• Predictive maintenance: The real value of LER lies in its ability to enable predictive maintenance. By analysing fluid data trends, WearCheck’s experienced diagnosticians can predict when components might fail and advise maintenance teams to schedule maintenance during planned downtime, minimising unscheduled interruptions to mining operations.
• Proactive measures: LER promotes a proactive approach to maintenance, focusing on preventing issues rather than reacting to them. Regular inspections, adherence to manufacturer guidelines, and scheduled fluid changes based on condition instead of fixed intervals contribute to sustained equipment reliability.
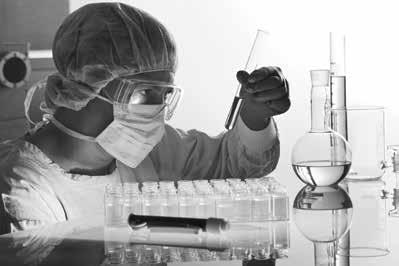
• Training and expertise: Successful implementation of an LER programme requires skilled personnel. Training maintenance teams in the intricacies of fluid management, analysis interpretation, and maintenance best practices is essential for the strategy’s effectiveness. WearCheck offers an extensive range of training courses aimed at all levels within an operation, from employees ‘at the coal face’ to senior management. Many of WearCheck’s courses earn delegates continuing professional development (CPD) points. Courses are run on site for clients around Africa or in scheduled venues. For more information on WearCheck’s training schedule, please visit https://www. wearcheck.co.za/training.html
Benefits of LER for mining operations
• Increased equipment lifespan: Implementing LER practices extends the operational life of mining equipment. Reduced friction and wear, as well as proactive maintenance, result in fewer equipment failures and replacements, leading to significant cost savings.
• Enhanced equipment performance: Proper lubrication leads to improved equipment efficiency and performance. Mining machinery can operate at optimal levels, delivering higher productivity and better operational output.
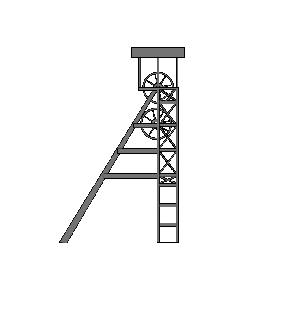
• Minimised downtime: Predictive maintenance based on fluid analysis allows for planned maintenance downtime, minimising unexpected breakdowns that can halt mining operations and lead to financial losses.
• Reduced maintenance costs: LER reduces maintenance costs associated with premature component failure. Regular fluid analysis and proactive maintenance prevent the need for extensive repairs or replacements. They also reduce the need for having to purchase expensive emergency spares.
• Environmental responsibility: TFM ensures proper disposal of used fluids, reducing the environmental impact of mining operations. It promotes responsible fluid usage and disposal, aligning with sustainability goals.
Sustaining success in a competitive landscape
Lubricant-enabled reliability has emerged as a game-changer in the mining industry. By recognising the pivotal role of lubricants and fluids in equipment health, mining operations can achieve increased reliability, improved performance, and reduced operational costs. As the mining sector continues to evolve, embracing these advanced maintenance practices can be the key to sustaining success in a competitive landscape.
WearCheck, Africa's leading condi�on monitoring company, is commi�ed to serving the mining industry with its range of sophis�cated analy�cal techniques.
Our specialist oil, coolant and fuel tes�ng programmes allow customers to reduce maintenance costs, avoid unexpected mechanical failures and ul�mately reduce unscheduled down�me.